
Учебная практика
.pdf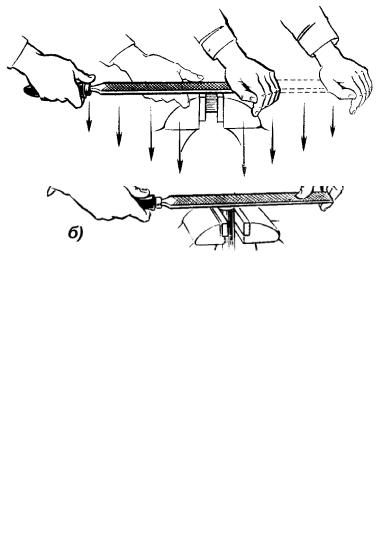
его положения. Во время движения напильник должен оставаться в горизонтальном положении, чтобы опиливаемая поверхность не имела неровностей.
Рис. 1.14. Приемы опиливания:
а – крупным напильником; б – мелким напильником
Правильное распределение вертикальных усилий на напильник в правой и левой руках является одним из существенных моментов опиливания и называется балансированием (рис. 1.15).
Рис. 1.15. Распределение усилий на напильник в процессе опиливания
Опиливание широких плоскостей может осуществляться продольным, поперечным или перекрестным штрихом (рис. 1.16). Опиливание продольным штрихом начинается с левого края поверхности. При движении назад напильник передвигается вправо примерно на 1/3 его ширины. После первого прохода опиливание повторяется справа налево.
При обработке поперечным штрихом во время рабочего хода напильник одновременно смещается вправо или влево на величину, примерно равную его ширине. Наиболее производительным и точным опиливанием широких плоскостей является перекрестное, при котором поверхность сначала опиливается справа налево, а затем слева направо.
21

При опиливании цилиндрических (криволинейных) поверхностей заготовку зажимают в тиски горизонтально или вертикально и обрабатывают колебательными движениями напильника.
Рис. 1.16. Опиливание широких плоскостей:
а – продольным штрихом; б – поперечным штрихом; в – перекрестным штрихом
Вогнутые криволинейные поверхности, а также отверстия и пазы в заготовках опиливают круглыми или полукруглыми напильниками, при этом напильник движется горизонтально и одновременно поворачивается вокруг своей оси. При опиливании таких поверхностей радиус кривизны напильника должен быть всегда меньше радиуса кривизны обрабатываемой поверхности.
Контроль опиленной поверхности осуществляется по размерам и по форме. Контроль по размерам осуществляется при помощи кронциркуля, нутромера с масштабной линейкой, штангенциркуля. Контроль формы осуществляется при помощи угольника, лекальной линейки, специальных шаблонов и проверочной плиты.
При опиливании плоских тонких заготовок применяют раздвижные закаленные стальные рамки, состоящие из двух планок, между которыми зажимается тонколистовая заготовка. Сама рамка с заготовкой зажимается в тиски. Обработка ведется до касания напильником верхней плоскости рамки, что позволяет обходиться без контроля правильности опиливания мерительным инструментом.
ОБРАБОТКА ОТВЕРСТИЙ
22

Сверлением называется технологическая операция получения сквозного или глухого отверстия в сплошном материале.
Сверление осуществляется сверлами на сверлильных, токарных и других станках, а также дрелями. В зависимости от конструкции различают винтовые или спиральные сверла, центровые, перовые и другие. Спиральное сверло (рис. 1.17) состоит из рабочей части и хвостовика, которым закрепляется в шпинделе станка. Хвостовики изготовляют коническими и цилиндрическими. Конический хвостовик удерживает сверло от проворачивания в шпинделе благодаря трению между конусом хвостовика и стенками конического отверстия шпинделя.
Рис. 1.17. Спиральное |
Рис. 1.18. Приспособления для зажима сверла: |
сверло и его части: |
а – трехкулачковый патрон; |
1 – лапка; 2 – хвостик; |
б – переходная конусная втулка |
3 – шейка; 4 – канавка |
|
Сверло с цилиндрическим хвостовиком предварительно закрепляется в специальном патроне (рис. 1.18, а). В том случае, когда конус сверла меньше конуса в шпинделе станка, применяются конусные переходные втулки (рис. 1.18, б). Лапка – концевая часть сверла – служит упором при выбивании сверла из шпинделя станка. При сверлении обрабатываемую деталь закрепляют неподвижно, а сверху сообщают два совместных движения (рис. 1.17): вращательное (по стрелке I) и поступательное, направленное вдоль оси сверла (по стрелке II). Вра-
23

щательное движение сверла называется главным, а поступательное – движением подачи.
Сверление применяют, когда необходимо получить отверстия невысокой степени точности и невысокого класса шероховатости, например, под крепежные болты и шпильки, а также под нарезание резьбы, развертывание и зенкерование. Если отверстие в детали несквозное, то операция называется засверливанием, а увеличение диаметра отверстия – рассверливанием, или зенкерованием.
В процессе сверления происходит стачивание режущих кромок сверла, и оно становится неработоспособным. Для восстановления режущих свойств сверла его затачивают. Полученный в результате заточки угол при вершине сверла проверяют специальными шаблонами (рис. 1.19). Величина этого угла выбирается в зависимости от обрабатываемого материала (табл. 1.1).
Рис. 1.19. Проверка сверла при заточке по шаблону:
а– шаблон; б – измерение длины режущей кромки;
в– измерение угла при вершине; г – измерение угла заострения; д – измерение
угла наклона поперечной кромки
Таблица 1.1 Зависимость угла при вершине от обрабатываемого материала
Обрабатываемый материал |
Угол при вершине, град |
Сталь и чугун средней твердости |
116…118 |
Сталь закаленная, медь |
125 |
Латунь, бронза, алюминий, баббит |
130…140 |
Силумин |
90…100 |
Эбонит, целлулоид |
85…90 |
Хрупкие материалы (мрамор и др.) |
80 |
Пластмасса |
50…60 |
24

Для уменьшения трения сверло имеет обратную конусность: его диаметр уменьшается по направлению к хвостовику на 0,03...0,12 мм на каждые 100 мм длины.
Свёрла изготовляют из сталей марок Р9, Р18, Р9К10, Р6М5, Р18К5Ф2, У12А, оснащают пластинками из твердых сплавов и композиционных материалов.
При сверлении отверстий диаметр сверла выбирают в зависимости от диаметра крепёжной детали – болта или шпильки (табл. 1.2).
Таблица 1.2 Диаметр сверла при получении отверстия для крепежной детали
Диаметр сверла, мм |
2,4 |
3,5 |
5 |
6 |
7 |
9 |
11 |
13 |
15 |
17 |
20 |
22 |
Диаметр крепежной |
2 |
3 |
4 |
5 |
6 |
8 |
10 |
12 |
14 |
16 |
18 |
20 |
детали, мм |
|
|
|
|
|
|
|
|
|
|
|
|
Зенкование – это операция обработки цилиндрических или конических углублений и фасок просверленных отверстий под головки болтов, винтов и заклёпок (рис 1.20, а). Режущим инструментом является зенковка. По форме режущей части зенковки делятся на цилиндрические, конические и торцовые (цековки). Все они состоят из рабочей части и хвостовика.
Рис. 1.20. Способы обработки отверстий:
а − зенкование; б −зенкерование; в − развёртывание
Рабочая часть цилиндрической зенковки имеет от 4 до 8 торцовых зубьев и направляющую цапфу, которая входит в просверленное отверстие, что обеспечивает совпадение оси отверстия и образованного зенковкой цилиндрического углубления.
25
На конической зенковке рабочая часть имеет конус при вершине. Наибольшее распространение получили конические зенковки с углом конуса 30, 60, 90 и 120°.
Цекование производится торцовыми зенковками для зачистки торцовых поверхностей, обработки бобышек под шайбы, упорные кольца, гайки. Для изготовления зенковок используется сталь марок Р9, Р18.
Зенкерование – процесс обработки цилиндрических и конических необработанных отверстий с целью увеличения диаметра, улучшения качества их поверхности, повышения точности (уменьшения конусности, овальности, разбивки). Зенкерование выполняется на сверлильных станках зенкерами (рис. 1.20, б), которые по внешнему виду напоминают сверло и состоят из тех же основных элементов, но имеют большее количество режущих кромок (3–4) и спиральных канавок.
Зенкеры изготовляют из стали марок Р9, Р18, 9ХС, У12А двух типов: цельные диаметром 10…40 мм с длиной рабочей части 80…200 мм и насадные диаметром 32…80 мм с длиной 10…18 мм.
Отверстия, которые после сверления необходимо обрабатывать зенкером, должны иметь меньший диаметр по сравнению с диаметром окончательно обработанного отверстия (табл. 1.3).
Таблица 1.3
Диаметр зенкера с учетом припуска
Диаметр |
10…24 |
25…35 |
36…42 |
46…55 |
56…65 |
66…75 |
|
зенкера, мм |
|
|
|
|
|
|
|
Припуск под |
1 |
1,5 |
2 |
2,5 |
3 |
3,5 |
|
зенкерование, мм |
|||||||
|
|
|
|
|
|
Развёртывание – обработка отверстий после сверления, зенкерования или расточки для придания им требуемой высокой точности и шероховатости (рис. 1.20, в).
Основным инструментом является развёртка, которая состоит из рабочей части, шейки и хвостовика. В зависимости от формы обрабатываемого отверстия применяют цилиндрические и конические развёртки с 6…12 зубьями. По конструкции развёртки подразделяют на цельные, регулируемые и со вставными зубьями, а по способу применения на ручные и машинные.
При развертывании отверстий вручную применяют развертку с неравномерным распределением зубьев по окружности, что способствует получению менее шероховатой поверхности. Машинные развертки имеют чётное количество равномерно распределенных зубьев. Чем
26

больше зубьев, тем менее шероховатой получается обрабатываемая поверхность.
Цилиндрические и конические развёртки изготовляют из стали марок Р9, 9ХС комплектно. В комплекте из трех развёрток первая − черновая, вторая − переходная, третья − чистовая.
Толщина слоя металла, снимаемого развёрткой, зависит от диаметра отверстия (табл. 1.4).
|
|
|
|
|
Таблица 1.4 |
|
Припуск на диаметр при развертывании |
|
|
||||
|
|
6…18 |
|
|
|
|
Диаметр отверстия, мм |
3…6 |
18…30 |
|
30…50 |
||
Припуск на диаметр, мм |
0,2 |
0,3 |
0,4 |
|
0,5 |
|
НАРЕЗАНИЕ РЕЗЬБЫ
Нарезанием резьбы называется образование резьбы снятием стружки (а также пластическим деформированием) на наружных или внутренних поверхностях заготовок деталей.
Резьба характеризуется профилем, шагом и диаметром. В зависимости от конфигурации профиля резьба бывает треугольной, трапецеидальной, прямоугольной и круглой.
По направлению движения винтовой линии резьба бывает правой и левой. В судостроении применяют в основном правую резьбу. Кроме того, резьбы бывают одно и многозаходными. Однозаходные имеют малые углы подъема винтовой линии и применяются для надежного крепления деталей. В судостроении применяют три системы резьб: метрическую, дюймовую и трубную.
Резьбу на деталях получают нарезанием на резьбонарезных, сверлильных и токарных станках, накатыванием или вручную при помощи метчиков, служащих для нарезания внутренней резьбы (рис. 1.21), и плашек, используемых для нарезания наружной резьбы (рис. 1.22).
Метчики делятся на ручные и машинные, изготавливаемые из инструментальной стали марок У8, У12, 9ХС. Для нарезания внутренней резьбы вручную требуется большое усилие. Для облегчения работы и для получения более чистой резьбы ручные метчики выпускаются комплектно: черновой, средний и чистовой, причем на метчиках соответственно наносят 1, 2 и 3 кольца для их различия.
Для уменьшения нагревания метчика и для получения более чистой резьбы необходимо применять смазочно-охлаждающие жидкости, выбираемые в зависимости от материала детали.
27

а)
г)
д)
б)
в) |
е) |
Рис. 1.21. Инструмент для нарезания внутренней резьбы:
а– метчик и его части; б – цилиндрические метчики; в – конический метчик;
г– гаечный метчик; д – плашечный метчик; е – маточный метчик
Наружную резьбу нарезают с помощью плашек (лерок). Плашки бывают круглые (цельные и разрезные) и призматические (раздвижные). Цельными плашками можно нарезать резьбу только одного диаметра, а разрезными можно регулировать диаметр резьбы, нарезаемой в небольших пределах.
Нарезание резьбы производят за один проход. Призматические плашки состоят из двух половинок, благодаря чему полный профиль резьбы можно нарезать за несколько проходов.
До нарезания резьбы в деталях сверлят отверстия диаметром несколько меньше, чем диаметр будущей резьбы.
Диаметр сверла выбирают по табличным данным (табл. 1.5) или
вычисляют по формулам: |
|
|
Dсв = dр − S, мм |
или |
d = D − 1,5 t, мм, |
28 |
|
|

где Dсв − диаметр сверла, мм; dр − диаметр резьбы, мм; S − шаг резьбы, мм; d − диаметр отверстия под резьбу, мм; D − наружный диаметр резьбы, мм; t − глубина резьбы, мм.
а) |
б) |
в) |
г) |
Рис. 1.22. Инструмент для нарезания наружной резьбы:
а– цельная плашка; б – разрезная плашка и ее части;
в– резьбонакатная плашка; г – раздвижная плашка
|
|
|
|
|
|
Таблица 1.5 |
|
|
Диаметры свёрл, применяемых для получения |
||||||
|
|
резьбовых отверстий |
|
|
|
||
Диаметр |
Диаметр сверла, мм |
Диаметр |
|
Диаметр сверла, мм |
|||
резьбы, |
Чугун, |
Сталь, |
резьбы, |
|
Чугун, |
|
Сталь, |
мм |
бронза |
латунь |
мм |
|
бронза |
|
латунь |
М 2 |
1,5 |
1,5 |
М 14 |
|
11,7 |
|
11,8 |
М 4 |
3,4 |
3,5 |
М 16 |
|
13,8 |
|
13,9 |
М 5 |
4,1 |
4,2 |
М 18 |
|
15,1 |
|
15,3 |
М 6 |
4,9. |
5,0 |
М 20 |
|
17,1 |
|
17,3 |
М 8 |
6,6 |
6,7 |
М 22 |
|
19,1 |
|
19,3 |
М 10 |
8,3 |
8,4 |
М 24 |
|
20,5 |
|
20,7 |
М 12 |
10,0 |
10,1 |
|
|
|
|
|
Диаметр нарезанной резьбы измеряют штангенциркулем. Для определения шага резьбы применяют резьбомер. Для комплексной про-
29
верки резьбы применяют комплект резьбовых калибров, состоящий из проходного и непроходного калибров.
Диаметр стержня для нарезания резьбы определяют по табл.1.6.
|
|
|
|
Таблица 1.6 |
|
Диаметр стержня для нарезания резьбы |
|||
|
|
|
|
|
Диаметр резьбы, |
|
Шаг резьбы, |
Диаметр стержня, мм |
|
мм |
|
мм |
наименьший |
наибольший |
М 6 |
|
1,0 |
5,8 |
5,8 |
М 8 |
|
1,25 |
7,8 |
7,9 |
М 10 |
|
1,50 |
9,75 |
9,85 |
М 12 |
|
1,75 |
11,76 |
11,88 |
М 14 |
|
2,0 |
13,7 |
13,82 |
М 16 |
|
2,0 |
15,7 |
15,82 |
М 18 |
|
2,5 |
17,7 |
17,82 |
М 20 |
|
2,5 |
19,72 |
19,86 |
М 22 |
|
2,5 |
21,72 |
21,86 |
ШАБРЕНИЕ И ПРИТИРКА
Шабрением называется операция по обработке незакаленных поверхностей путем снятия тонкого слоя металла с помощью шаберов
(рис. 1.23).
Это окончательная обработка точных поверхностей (направляющих станин станков, контрольных плит, подшипников скольжения и др.) для обеспечения плотного сопряжения.
Шаберы изготовляют из сталей марок У10 и У12А, режущие концы их закаливают без отпуска до твердости HRC 56…64. Шаберы подразделяются: по конструкции (цельные и со вставными пластинками), по числу режущих концов (односторонние и двусторонние), по форме режущей части (плоские, трёх-, четырёхгранные и фасонные).
Процесс подготовки и шабрение осуществляют в определенной последовательности. Поверхности детали очищают и протирают.
На поверочную плиту наносят тонкий слой краски (сажу, лазурь и другие, смешанные с машинным маслом) и осторожно накладывают деталь обрабатываемой поверхностью на плиту. Затем деталь передвигают круговыми движениями по плите и осторожно снимают. На обрабатываемой поверхности наиболее выступающие места слабо окрашиваются. В процессе шабрения с окрашенных мест постепенно соскабливают металл, передвигая шабер с легким нажимом вперед, каж-
30