
3728
.pdfIssue № 4 (40), 2018 |
ISSN 2542-0526 |
2.Babkov V. F. [Stresses in ground bases of road pavement]. Trudy DorNII [Proc. of DorNII], 1941, vol. 5, pp. 99––196.
3.Balovnev V. I. Modelirovanie protsessov vzaimodeystviya so sredoy rabochikh organov dorozhnostroitel'nykh mashin [Modeling of processes of interaction with the environment of working bodies of roadbuilding machines]. Moscow, Vysshaya Shkola Publ., 1981. 335 p.
4.Belousov L. I. Issledovanie dorozhnykh katkov v svyazi s neobkhodimost'yu polucheniya vy-sokoy rovnosti dorozhnykh pokrytiy. Avtoref. diss. kand. tekhn. nauk [Investigation of road rollers in connection with the need to obtain high evenness of road surfaces. Abstract of diss.]. Leningrad, 1974. 22 p.
5.Varganov S. A. Issledovanie vibratsionnykh katkov dlya uplot¬neniya asfal'tobetonnykh smesey i obosnovanie vybora ikh ra¬bochikh parametrov. Avtoref. diss. kand. tekhn. nauk [Investigation of vibration rollers for compaction of asphalt concrete mixtures and rationale for the choice of their operating parameters. Abstract of diss.]. Moscow, 1960. 15 p.
6.Vyalov S. S. Reologicheskie osnovy mekhaniki gruntov [Rheological fundamentals of soil mechanics]. Moscow, Vysshaya shkola Publ., 1978. 447 p.
7.Kharkhuta N. Ya., Kapustin M. I., Semenov V. P., Eventov I. M. Dorozhnye mashiny. Teoriya, konstruktsiya i raschet [Road machine. Theory, design and calculation]. Leningrad, Mashinostroenie Publ., 1976. 472 p.
8.Zubkov A. F. Issledovanie parametrov vibratsionnykh katkov pri uplotnenii asfal'to-betonnykh pokrytiy. Avtoref. diss. kand. tekhn. nauk [Investigation of parameters of vibration rollers during compaction of asphalt concrete coatings. Abstract of diss.]. Leningrad, 1974. 16 p.
9.Ishlinskiy A. Yu., Kondrat'eva A. S. [About rolling of rigid and pneumatic wheels on deformable soil]. Trudy soveshchaniya po prokhodimosti kolesnykh i gusenichnykh mashin po tseline i gruntovym dorogam [Proc, of the meetingonthepatencyofwheeledandtrackedvehiclesonvirginsoilanddirtroads].Moscow,ANSSSRPubl.,1950.
10.Kaluzhskiy Ya. A., Batrakov O. T. Uplotnenie zemlyanogo polotna i dorozhnykh odezhd [Compaction of roadbed and pavement]. Moscow, Transport Publ., 1971. 160 p.
11.Kovalenko Yu. Ya. Issledovanie samokhodnykh vibratsionnykh katkov dlya uplotneniya as-fal'tobetonnykh smesey. Avtoref. diss. kand. tekhn. nauk [Study of self-propelled vibration rollers for compaction of asphalt concrete mixtures. Abstract of diss.]. Leningrad, 1979. 23 p.
12.KoltunovM.A.Polzuchest' i relaksatsiya [Creepandrelaxation].Moscow,VysshayashkolaPubl.,1976.278p.
13.Kustarev G. V. Analiz issledovaniy v oblasti uplotneniya dorozhno-stroitel'nykh materialov [Analysis of research in the field of compaction of road construction materials]. Moscow, Elektronnoe izdanie SDM –– Stroitel'nye i dorozhnye mashiny i tekhnika, kafedra SDM MADI, PO «Stroytekhnika», 2008. 32 p.
14.Nosov S. V., Goncharova M. A. Metodologiya sovershenstvovaniya tekhnologiy uplotneniya dorozhnostroitel'nykh materialov [Methodology of improvement of technologies of compaction of road-building materials]. Lipetsk, LGTU Publ., 2015. 166 p.
15.Nosov S. V. Vybor funktsii vliyaniya pri issledovanii reologicheskikh svoystv opor-nogo osnovaniya [Choice of the influence function in the study of rheological properties of the support base]. Traktory i sel'skokhozyaystvennye mashiny, 2006, no. 10, pp. 19––21.
16.Nosov S. V. Matematicheskoe modelirovanie dinamiki nazemnykh transportno-tekhnologicheskikh sredstv pri vzaimodeystvii s deformiruemym opornym osnovaniem [Mathematical modeling of the dynamics of ground transportation and technological means in interaction with the deformable support base]. Lipetsk, Izd-vo Lipetskogo gosudarstvennogo tekhnicheskogo universiteta, 2016. 164 p.
71

Russian Journal of Building Construction and Architecture
17.Nosov S. V., Nosov V. V. Dinamicheskaya model' vibratsionnogo katka s vakuumnym ust-roystvom [A dynamic model of the compactor with the vacuum device]. Izvestiya vuzov. Stroitel'stvo i arkhitektura. Novosibirsk, 1991, no. 7, pp. 101––107.
18.Nosov S. V., Nosov V. V. K voprosu po opredeleniyu modulya deformatsii uplotnyaemykh sloev dorozhnostroitel'nykh materialov [On the question of determining the deformation modulus of compacted layers of roadbuilding materials]. Izvestiya vuzov. Stroitel'stvo. Novosibirsk, 1991, no. 10, pp. 104––108.
19.Nosov S. V. Mobil'nye energeticheskie sredstva: vybor parametrov i rezhimov raboty cherez reologicheskie svoystva opornogo osnovaniya [Mobile power facilities: selection of parameters and operating modes through rheological properties of the support base]. Lipetsk, LGTU Publ., 2006. 228 p.
20.Nosov S. V., Peregudov N. E. Matematicheskaya model' vzaimodeystviya gusenichnogo dvi-zhitelya s opornym osnovaniem [Mathematical model of the interaction of crawler engine with its support base]. Traktory i sel'skokhozyaystvennye mashiny, 2006, no. 11, pp. 29––33.
21.Nosov S. V. Razrabotka tekhnologiy uplotneniya dorozhnykh asfal'tobetonnykh smesey i gruntov na osnove razvitiya ikh reologii. Diss. kand. tekhn. nauk [Development of technologies for compaction of road asphalt concrete mixtures and soils based on the development of their rheology. Cand. eng. sci. diss.]. Voronezh, 2013. 366 p.
22.Pershin M. N., Kulizhnikov A. M., Radov V. P. Dorozhnoe gruntovedenie [Road soil science]. SaintPetersburg, SPbGASU Publ., 1998. 153 p.
23.Sidenko V. M., Batrakov O. T., Leushin A. I. Tekhnologiya stroitel'stva avtomobil'nykh dorog. Ch. 1: Tekhnologiya stroi-tel'stva zemlyanogo [Technology of road construction. Part 1: technology of construction of the roadbed]. Kiev, Vishcha shkola Publ., 1970. 236 p.
24.Kharkhuta N. Ya. [Problems of the theory of compaction of road surfaces]. Trudy SoyuzdorNII «Uplotnenie zemlyanogo polotna i dorozhnykh odezhd» [Proceedings of the Union “Compaction of roadbed and pavement”]. Moscow, 1980. pp. 64––71.
25.Kharkhuta N. Ya. Mashiny dlya uplotneniya gruntov [Soil compaction machines]. Moscow-Leningrad, Mashinostroenie Publ., 1973. 176 p.
26.Kharkhuta N. Ya., Vasil'ev Yu.M. Prochnost', ustoychivost' i uplotnenie gruntov zemlyanogo polotna avtomobil'nykh dorog [Strength, stability and compaction of roadbed soils]. Moscow, Transport Publ., 1975. 286 p.
27.Angst Ch. Der Einflu der Vtrdichtung auf die mechanischen Eigen-Schaften bituminöser Schichten. Bitumen 2, 1982, pp. 75––84.
28.Compactors for road making materials. Technology steers market towards end resultstandard. "Contract J.", 1985, 328, no. 5534, pp. 25––28, 30, 34, 35, 37.
29.Development of machines for compacting soil and pavement. A decade of developments. "Constr. Plant and Equip", 1979, 7, no. 5, pp. 29––30.
30.Forssblad Lanz. Vibrorollers operation test. Vibratory compaction of asphalt pavements-experimences from different ports of the world. «Project», 1979, 18 Sept, 25––28.
31.Nosov S., Kuzmichev V., Repin S., Maksimov S Methodology of Ensuring Road Traffic Safety with Respect to Road-Building Materials Compaction Efficiency Factor. Transportation Research Procedia Vol. "12th International Conference "Organization and Traffic Safety Management in Large Cities", SPbOTSIC 2016" 2017, pp. 450––454.
32.Nosov S. V. Determination of Rational Contact Pressure Under a Roller When Compacting Asphalt Concrete Mixes. Russian Journal of Building Construction and Architecture, 2017, no. 2 (34), pp. 45––53.
72

Issue № 4 (40), 2018 |
ISSN 2542-0526 |
UDC 625.7/.8 : 621.78
V. P. Podol'skii1, M. X. Al-Addess2,S. V. Nosov3
TECHNOLOGY OF REPAIR WORKS
WITH USE OF EMULSION-MINERAL MATERIALS AND EMULSIONS
Voronezh State Technical University
Russia, Voronezh
1D. Sc. in Engineering, Prof., Head of the Dept. of Construction and Operation of Highways, tel.: +7-980-555-02-85, e-mail: ecodor@bk.ru
2PhD student of the Dept. of Construction and Operation of Highways, tel.: +7-951-864-83-91, e-mail: aladdess@yandex.ru
Lipetsk State Technical University
Russia, Lipetsk
3D. Sc. in Engineering, Prof. of the Dept. of Building Materials Science and Road Technologies, tel.: 8-903-699-3180, e-mail: nosovsegej@mail.ru
Statement of the problem. In recent years, thin surface pavement layers have been very important for providing the required roughness and protect the upper layers from negative natural effects and operational factors. These layers are commonly made of emulsion-mineral mixtures using recycling machines.
Results. According to the goals of recycling and a type of a machine, which is used to distribute a bitumen binder, machines might vary considerably. During the reconstruction of the Najaf-Karbala road in the Republic of Iraq asphalt granulate milled from a pavement surface for the preparation of the asphalt-gravel concrete mixture was used.
Conclusions. During the study an analytical method of identifying the amount of new road metal was suggested depending on the residual bitumen in the asphalt granulate. Another use of the asphalt granulate with a complex addition of cement and bitumen emulsion saves energy and material resources and can be used for the installation of the lower pavement layer. An increase in the strength of the emulsion mineral mixtures with the addition of fiber fillers allows one to obtain dispersed reinforced materials with high crack resistance at high temperatures and deformation stability.
Keywords: cation-active emulsion, recycler, recycling, asphalt-granulate, granulate, recycled materials, wear and tear layer.
Introduction. Recently there have been a lot of thin wear-and-tear layers to provide a required level of roughness and protect surfaces from the negative impact of natural and operational factors. They are commonly designed using emulsion and mineral mixes.
© Podol'skiiV. P., Al-Adddess M. X.,NosovS. V., 2018
73

Russian Journal of Building Construction and Architecture
According to the recycling technology, the transportational and operational properties of the upper layers of road surfaces. Lower construction layers are protected from corrosion and moisture and there is a wear-and-tear resistance layer on the surface. A new skeleton material, i.e. a cation-active emulsion, as well as cement is introduced according to a recipe of choice. The major advantages of these layers are as follows:
––A high elasticity and increase in the dynamic load resistance due to polymer modifiers [1];
––a high cohesion coefficient;
––temperature resistance;
––active adhesion to a surface;
––no emission of stone material;
––a low energy capacity of a production process;
––a low environmental impact;
––durability of a layer (3—5 years);
––a low noise level in a surfacing;
––a small weight of a surfacing and a high water resistance;
––aesthetics of an even surface of a surfacing;
––no need to relay a curbing enclosure.
1. The recycling technology using emulsion and mineral materials. An alternative method is cold recycling for part of production. Throughtout its history recyclers started being produced as specialized machinery in place of modified road cutters and soil stabilizers. They are employed particularly for recycling road surfacing materials in large depth in one go and are thus large-sized superpower caterpillar or wheeled machinery.
For cold recycling a set of machines with particular functions is used. In the start period a special machine distributes a bit of a binder or a mineral mix with a binder of a surface. A digital control system manages the geometric parameters of the layer followed by two machines, the first one with water and the second one with bitumen. A powerful cutter-rotor drum grinds an asphalt surfacing into small fragments. Preliminarily put onto a road surface, a mix of a binder is mixed with an asphalt concrete crumb and is moisturized with sprays fit in the first sector of a mixing chamber. The bitumen emulsion from the second machine is supplied with a special setup and sprayed from the second ramp. In order to activate the cut material of the road surfacing, the recycling equipment has been modernized to increase the number of rotations of the drum from 16 to 240 m/seс. In the upper area of the mixing chamber there is an activator that is a smaller cutting drum with a linear rate of the activator teeth of
74
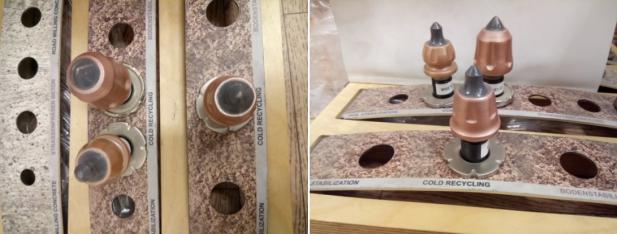
Issue № 4 (40), 2018 |
ISSN 2542-0526 |
50 m/seс (Fig. 1). Some of the material ground with the teeth of the cutting drum comes in contact with the activator teeth moving towards it and receives an extra impulse and some particles hit the chamber walls and are thrown back to the activator. In this case the particles hit the activator, one another and the walls of the cutting drum chamber for multiple times. Due to counter-acceleration of the particles, activation takes place at the rates of 290 m/sec [10, 11].
Fig. 1. Teeth of a cutting drum
Depending on the purposes of recycling and type of a used binder, a set of employed machines might vary considerably. In each case a recycler is a leading machine and skids or pushes the machines chained with it on its own.
If a bitumen emulsion or foamed bitumen is used in a combination with a cement water suspension, the same group of machines is employed. A bitumen mobile tank is pushed prior to setting up a cement water suspension. If cement is used as a powder (it is evenly distributed along the road surface), the mobile tank with water is pushed in front of the recycler. If the recycler has a caterpillar undercarriage and is fitted with a compacting operating body, a surface profiling grader is not used.
The use of recyclers in road works provides restoration of worn-out road surfaces at a minimum cost hence production of a new mix is becoming common. Growing intensity of a flow and more vehicles causes degradation of roads that might be more costly to maintain than to build new ones. Therefore it is cold recycling that is increasingly popular around the world. Particularly, it was employed for the reconstruction of the Najaf-Karbala road (Fig. 2) using an asphalt granulate and a complex binder.
75
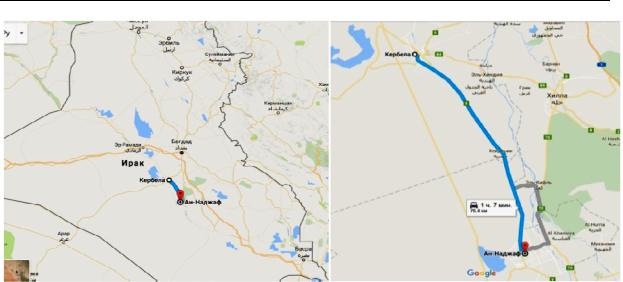
Russian Journal of Building Construction and Architecture
Fig. 2. Geographic scheme
The Najaf-Karbala road is in the South-West of Iraq and has a strategic purpose since in every city crossed by the road there are religious sanctuaries and an airport in Najaf. The main parameters of a transverse profile of roads is presented in Tables 1 and 2.
|
Таble 1 |
|
|
Length |
80 km |
|
|
Number of traffic lanes |
4 |
|
|
Width of traffic lanes, m |
3.75 m |
|
|
Width of a traffic lane, m |
2×7.5 |
|
|
Width of curbs, m |
3 м |
|
|
Smallest width of a reinforced lane of a curb, m |
0.75 m |
|
|
Smallest width of a traffic lane between different traffic directions, m |
10 m |
|
|
Smallest width of a reinforced lane at a traffic lane, m |
< 1 m |
|
|
|
Таble 2 |
|
|
Traffic intensity, reduced to units/day |
Number of days in a year |
|
|
1000—5000 |
52 |
|
|
5000—1000 |
3 |
|
|
12000—18000 |
2 |
|
|
80000—125000 |
10 |
|
|
76
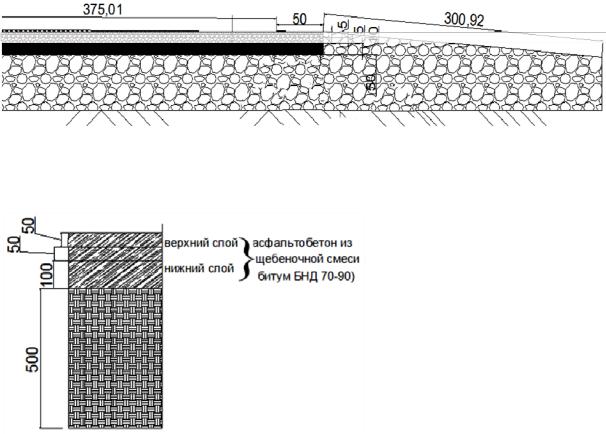
Issue № 4 (40), 2018 |
ISSN 2542-0526 |
The traffic intensity category of the Najaf-Karbala is I-b. In order to develop the road, two lanes should be added, reinforced using emulsion-mineral materials as well as covered with a protective layer (a wear-and-tear layer) with the thickness of 3 cm [4, 11, 17].
The first protective layer can be made of an emulsion-mineral mix with the fraction 5—10 or the slurry seal technology. The next layer with the surfacing thickness of 5 сm can be designed based on the technology shown in Fig. 3.
Fig 3. Detail of a transverse profile of a road
Upper layer |
|
Asphalt concrete |
|
|
from a limestone mix |
Lower layer |
|
bitum BND 70-90 |
Limestone and sand mix
Fig. 4. Construction layer of an old traffic lane
Following the cutting of the layer of the asphalt concrete surfacing using the recycler (RM-300) or a road milling machine (WIRTGEN-2000), an asphalt concrete granulate is formed. Using thr asphalt concrete granulate with a mineral binder, bitumen emulsion or bitumen emulsion in combination with cement or, if necessary, new skeleton material (mainly limestone), an asphalt granule concrete mix is formed. After it is distributed and compacted in a construction layer, it is turned into a composite (Fig. 5) [1, 10, 11].
The first type (Fig. 5А) of the asphalt granular concrete mix can be prepared using the method of mixing “on site”, the second type (Fig. 5B) of a new traffic lane from the asphalt granular concrete mix can be made on a stationary setup.
77
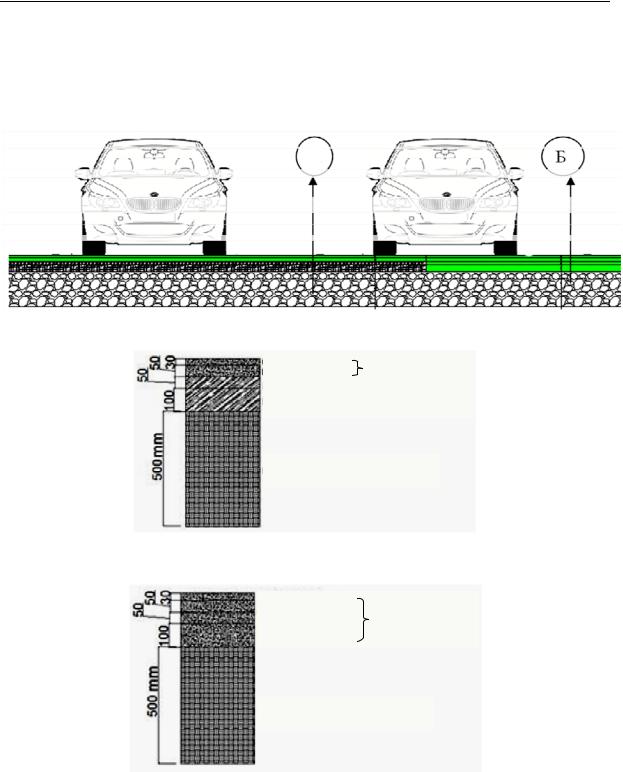
Russian Journal of Building Construction and Architecture
Based on the experiments at a road laboratory of Voronezh State Technical University, an anamnestic method of determing the number of added materials when an asphalt granulate is used is suggested.
a) |
b) |
|
|
Wear-and-tear layer
Upper layer Asphalt granulate
Lower layer (Asphalt granulate from a limestone mix, bitumen BND 60-90)
A limestone and sand mix
a)
Wear-and-tear layer
Upper layer
Lower layer |
Asphalt granulate |
Lower layer |
|
A limestone and sand mix
b)
Fig. 5. The road following the reconstruction:
a)construction layers of the old traffic lane following the repairs adding a wear-and-tear layer;
b)construction layers of the new traffic lane based on the emulsion mineral mix
78

Issue № 4 (40), 2018 |
ISSN 2542-0526 |
The calculation of the amount of a new limestone in the asphalt granular concrete mix depends on the proportion of bitumen in the asphalt granulate (Table 3—4) [8]:
М Z N; |
(1) |
|||
X 7 Er ; |
(2) |
|||
M |
X |
100 %. |
(3) |
|
|
||||
|
Z |
|
|
|
Мr ≤ М: |
|
|
|
|
P M G S Er ; |
(4) |
|||
Mr M P; |
(5) |
|||
Gr G P. |
(6) |
|||
|
|
|
Таble 3 |
|
|
|
|
|
|
Маterial |
|
|
Percentage |
|
|
|
|
|
|
Cation-active bitumen emulsion |
|
|
4 |
|
|
|
|
|
|
Cement |
|
|
5 |
|
|
|
|
|
|
Mineral material |
|
|
91 |
|
|
|
|
|
|
Water |
|
|
5—15 |
|
|
|
|
|
|
The composition of the mix is as follows: |
|
|
|
|
W Er |
S Gr Mr . |
(7) |
E.g., the percentage of a new limestone needs to be found if there is 4% of emulsion in the mix and 4 % of bitumen in the asphalt granulate.
The solution is as follows:
Х7 Еr 7 4 3 %;
Мxz 34 0.75 100 75 %;
the percentage of the new limestone is
G 100 М 100 75 25 %;
the composition of the mix: P = (100) – 5 − 4 = 91 %, Mr = 75 × 91 = 68.25 %, Gr = 25 × 91 = 22.77 % is the new limestone; the total volume of a surfacing = 8000×1.8= 14400 m3.
79
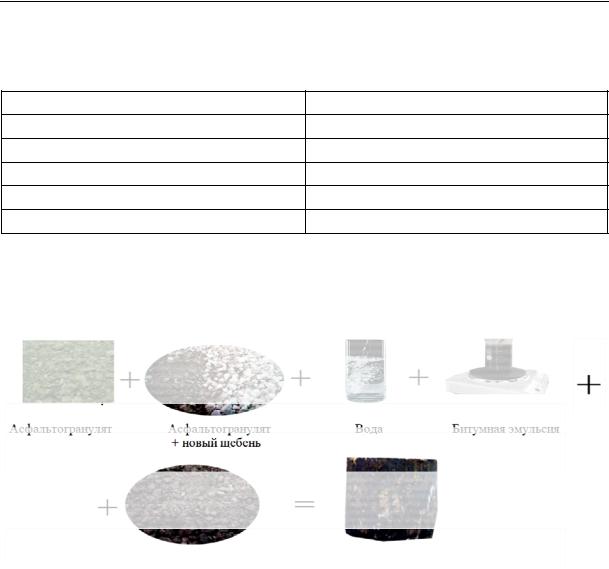
Russian Journal of Building Construction and Architecture
Таble 4
Amount of the materials for recycling 80 km of a roadway
Маterial |
Amount |
Cation-active bitumen emulsion, m3 |
576 |
Cement, tons |
966 |
New limestone, m3 |
2860 |
Asphalt granulate, m3 |
10272 |
Water, m3 |
1440—2000 |
2. Use of cation-active bitumen emulsions with additives. A technological process of preparing emulsion mineral materials using asphalt concrete waste and granulate is given in Fig. 6.
Asphalt granulate |
|
Asphalt granulate + |
|
Water |
|
Bitumen emulsion |
|
|
+ new limestone |
|
|
|
|
|
|
|
|
|
||
|
|
|
|
|
|
|
Emulsion mineral mix
Fig. 6. Scheme of a construction layer from recycled materials with a bitumen emulsion
Regeneration of old asphalt concrete at an asphalt concrete plant allows the material milled from the road. Regeneration should be introduced to obtain a mix with specified properties of an additive of stone materials, bitumen and plastifiers and added to a road surfacing in parts of a road with corresponding traffic intensity. Recurrent use of the materials enables one to save economic and material resources for laying construction layers of road surfacing.
The main stage proceeding the recycling of old asphalt concrete is selecting a recipe for a regenerated mix.
During recycling asphalt concrete waste from limestone or sandy mixes supplied from a road and stored separately in accordance with the types and piles. It is used as pieces with no additional mineral inclusions of over 3 % (according to the mass) of sandy and sabulous impurities and no more than 0.5 % (according to the mass) of clay impurities.
80