
3702
.pdfУДК 621.74
АНАЛИЗ ПРОЦЕССОВ ЗАТВЕРДЕВАНИЯ В ПРИБЫЛЬНОЙ И ПОДПРИБЫЛЬНЫХ ЧАСТЯХ СТАЛЬНОЙ КОРПУСНОЙ ОТЛИВКИ ПРИ ЛИТЬЕ В ПГФ ПОСРЕДСТВОМ CAD-СИСТЕМ
SOLIDWORKS И LVMFLOW
Т.И. Сушко, Т.В. Пашнева, А.А. Неровный
Военный учебно-научный центр Военно-воздушных сил «Военно-воздушная академия им. проф. Н.Е. Жуковского и Ю.А. Гагарина», Воронеж
tat120675@yandex.ru
В работе проводилось изучение температурно-фазовых полей в отливке на этапе затвердевания, моделирование процессов образования усадочных дефектов в металле и прогнозирование образования усадочных дефектов в зависимости от изменения технологических параметров при литье в песчано-глинистые формы посредством
CAD-систем SolidWorks и LVMFlow
Ключевые слова: отливка, литейные и усадочные дефекты, корпус запирающего винта, процесс затвердевания отливки
При добыче и транспортировке нефти и газа арматура трубопроводов испытывает воздействие агрессивных сред, углеводородов, давления и низких температур. В этих условиях к качеству металла должны предъявляться жесткие требования по прочности, герметичности, сопротивлению коррозии. Корпусные детали имеют в своей конструкции сопряжение тонких и толстых стенок и характеризуются высоким уровнем усадочных дефектов, в частности рыхлоты и пористости. Метод «проб и ошибок», часто применяемый на литейных предприятиях России при разработке технологии приводит к отрицательным результатам. При этом выявлению механизмов образования усадочных дефектов не уделяется должного внимания, хотя существует множество работ по видам дефектов и методов борьбы с ними [1], поэтому данная работа является актуальной. Устранение литейных дефектов невозможно без анализа влияющих на их образование факторов. Этими факторами (при литье в песчано-глинистые формы) могут быть состояние литейной формы, составы формовочных и стержневых смесей, конструкция отливки, марка выплавляемого сплава и условия его плавки, температура заливки металла и условия охлаждения отливки в форме. Для того, чтобы не нарушить производственный цикл необходимо оперативно выяснять причины образования литейных дефектов и вносить необходимые технологические коррективы. Современный подход к разработке технологического процесса получения качественных отливок основан на интенсивном использовании компьютерной техники и инновационных технологий. Для реализации такого подхода в работе использована система компьютерного моделирования литейных процессов LVMFlow, которая позволяет провести анализ влияния множества технологических факторов на качество литья за короткий промежуток времени и выявить некоторые механизмы их образования [2]. Цель данной работы – изучение темпе- ратурно-фазовых полей в отливке на этапе затвердевания, моделирование процессов образования усадочных дефектов в металле, установление закономерно-
120

стей образования пористости и рыхлоты посредством LVMFlow, разработка оптимальных способов борьбы с пористостью.
Для достижения данной цели поставлены следующие задачи: 1) построение в СAD-системе объемной 3D модели корпусной отливки способом литья в ПГФ; 2) построение сетки конечных разностей с применением LVMFlow; 3) изучение динамики развития затвердевания и выявление мест залегания дефектов усадочной природы посредством моделирования; 4) по результатам анализа разработать технологические рекомендации по совершенствованию технологии изготовления отливки и исключения выявленных усадочных дефектов.
Анализ протекания процессов затвердевания в прибыльной и подприбыльной частях, детали «корпус запирающего винта» (рис. 1), материал изготовления детали – 35ХМЛ ГОСТ 977-88, выпускается в серийном производстве в филиале ФГУП «ГКНПЦ им. М.В. Хруничева» и имеет массу 36 кг, осуществляли с применением системы LVMFlow. Отливку выбрали для исследований в связи с тем, что во время механической обработки проявляется брак в виде усадочной пористости. Формировалась 3D модель отливки вместе с ЛПС в SolidWorks 2013, 3Dмодели литниковой системы, прибылей и стержня. Затем они были конвертированы в необходимый формат LVM Flow (рис. 2). При моделировании процессов затвердевания отливки задавались следующие начальные условия: температура заливки – 1620 °С, в качестве формовочной и стержневой смеси использовалась жидкостекольная смесь ФС ПСС с начальной температурой 20 °С, формовка – ручная, в двух горизонтальных полуформах по разъему, расчет велся при размере ячейки 7,00 мм, граничные условия – излучение в среду с температурой 20 °С кроме верхней плоскости формы, вид литья – гравитационное (заливка из ковша или печи), время заливки расплава в форму – 12 с.
Рис. 1. Деталь «корпус запирающего винта»
Рис. 2. 3D модель отливки с ЛПС
121
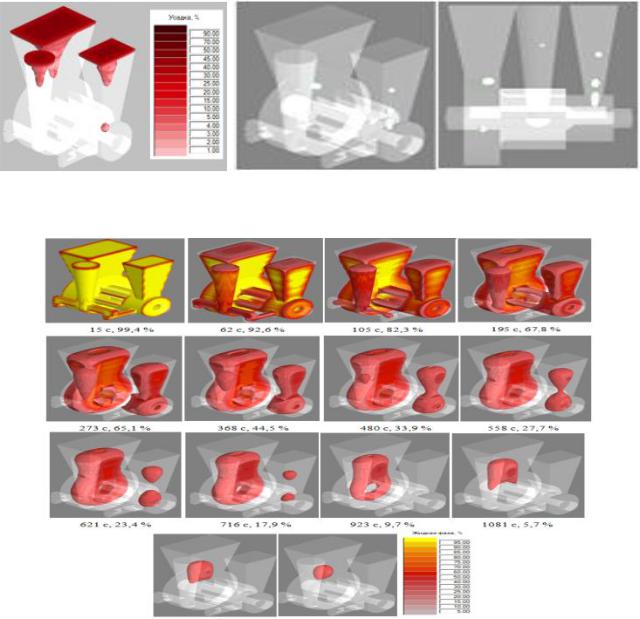
В конструкции отливки можно выделить один массивный пояс, в месте его сопряжения с основной стенкой наблюдается два тепловых узла и чтобы избежать возникновения усадочных дефектов необходимо установить прибыли. Моделирование процесса затвердевания подтверждает наличие тепловых узлов и визуализирует местоположение усадочных дефектов в отливке. В отливке проявляются недопустимые усадочные дефекты в виде закрытой и открытых усадочных раковин и микропористости, что подтверждает информацию о браке. Рассмотрим причины, влияющие на образование дефектов. Как видно из рис. 3, закрытая усадочная раковина располагается над стержнем, под прибылью. Значение усадки для данного расчетного узла достигает 35 %, что является недопустимым, так как в этом месте происходит соединение детали, и она испытывает напряжения (рис. 3). На рис. 4 показано развитие процесса затвердевания за определенные промежутки времени.
а) б)
Рис. 3. Распределение усадки (а) и пористости (б) в теле отливки
Рис. 4. Этапы затвердевания отливки, для каждого этапа приведено время затвердевания и количество жидкой фазы, %
122
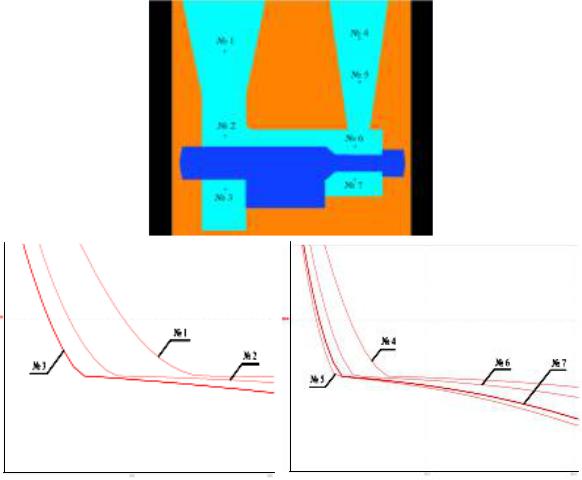
О характере развития процесса затвердевания металла в отливке (считается, что гидродинамические процессы к этому моменту полностью завершены) можно судить по цветовой шкале рис. 4.
Исходя из этого можно сделать вывод, что затвердевание развивается в соответствии с законом х=K 0,5. На основе анализа результатов численного моделирования процесса затвердевания и распределения жидкого металла в сечении отливки (где были установлены виртуальные температурные датчики) построены кинетические зависимости жидкого, двухфазного и твердого металла от времени в прибыли, отливке и на границе прибыль-отливка (рис. 5).
Рис. 5. Изменение доли жидкого, двухфазного и твердого металла в отливке
Анализируя графики для датчиков № 1, 2, 4, видно, что металл в точке 3, соответствующей месту под стержнем затвердевает быстрее, чем в точках 1 и 2, а расплав в точке 1, находящейся в прибыли затвердевает наиболее медленно. Таким образом, для данного теплового узла соблюдается принцип направленного затвердевания, то есть затвердевание происходит снизу вверх, что соответствует условию получения плотной структуры. Из анализа кривых охлаждения для точек 4, 5, 6 и 7 (рис. 5) можно сделать вывод об отсутствии направленности затвердевания в данном термическом узле снизу вверх из-за того, что металл в точке 5 остывает намного интенсивнее, чем во всем остальных точках рассматриваемого узла (точки 4, 6 и 7). Следствием такого распределения тем-
123
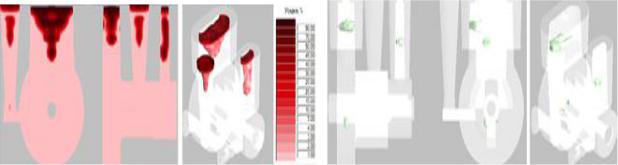
ператур является разрыв питания в подприбыльной области во время затвердевания расплава, то есть металл в нижней части прибыли затвердевает быстрее, чем под прибылью и в ее верхней части. В результате прекращения питания на одном из этапов затвердевания под прибылью образуется закрытая усадочная раковина. Таким образом, установлено, что возможной причиной образования усадочных дефектов в отливке является нарушение принципа направленного затвердевания из-за преждевременного затвердевания металла в прибыли и нарушения питания отливки. Ставилась задача – установить влияние (на уровне прогноза) ширины двухфазной зоны затвердевающего металла на образование пористости. Для ее решения использовали модель предложенную Тихомировым М.Д., предполагающую наличие в интервале затвердевания трех критических точек, соответствующих доле : жидкого металла в начале линейной усадки Kв, при прекращении гравитационного течения Kп и при полном перекрытии междендридных каналов Kн. В программе LVMFlow им соответствует «порог текучести» и «порог протекания». Было проведено численное моделирование затвердевания металла в двухфазной зоне по двум вариантам, 1 – порог текучести 70, протекания 30, 2 – порог текучести 70, порог протекания до 70, что позволило оценить глубину усадочной раковины и величину усадки в трех точках по оси прибыли. Глубина раковины, проникающей в тело отливки, уменьшается при переходе от порога протекания 30 до 70, что связано с сужением в двухфазном металле зоны между порогом протекания и порогом текучести до нуля. Это доказывает, что усадочная раковина и микропористость образуется в области жидко-твердого металла и в области твердо-жидкого. При этом увеличивается область вероятного образования микропористости, т.е. в интервале солидусликвидус. Уменьшение размеров раковины сопровождается увеличением размеров пористости, полностью от которой можно избавиться только при замене смеси, например с ЖСС на хромомагнезитовую, а избавиться от усадочных дефектов можно вследствие применения другой схемы питания отливки, например в случае экзотермического обогрева (рис. 6 (а, б), таблица).
а) б)
Рис. 6. Распределение усадки и пористости в отливке (а), усадка в теле отливки отсутствует, пористость минимальна (б)
Таким образом, получен результат изменения базовой технологии, позволивший получить бездефектную отливку, а также значительно повысить технологический выход годного с 55,6% до 73,6 %.
124
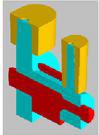
Система питания |
Глубина |
|
Распределение дефектов |
|||
(Прибыль |
залегания |
|
|
|
|
|
|
|
Раковина, |
Рыхлота, |
Порис- |
||
с экотермиком) |
дефекта, мм |
|
|
% |
% |
тость, % |
|
--- |
прибыль |
|
74 |
23 |
3 |
|
|
|
|
|
|
|
|
|
Отливка- |
|
– |
– |
– |
|
|
прибыль |
|
|||
|
|
|
|
|
|
|
|
|
|
|
|
|
|
Литература
1.Воронин Ю.Ф. Атлас литейных дефектов. Черные сплавы / Ю.Ф. Воронин, В.А. Камаев. – М.: Машиностроение – 1, – 2005. – 328 с.
2.Сушко Т.И. Исследование влияния технологических факторов на получение качественных отливок с экзотермическим обогревом посредством CKM LVM Flow / И.Н. Петров, И.Г Руднева, Т.В. Пашнева// Материалы IX Междунар. конф. “Achievement of high school-2013” 17-25 November 2013, т. 44, “Технологии”, София, “Бял Град-БГ”, ООД 2013, с. 12-17.
AN ANALYSIS OF DURING SOLIDIFICATION
IN PROFITABILITYAND PODPRIBYLNYH PARTS STEEL FRAME CASTING AT CASTING INTO SANDY CLAY MOLDS
BY CAD SYSTEMS SOLIDWORKS AND LVMFLOW
T.I. Sushko, T.V. Pashneva, A.A. Nerovny
Military Educational and Scientific Center of the Air Force “N.E. Zhukovsky and Y.A. Gagarin Air Force Academy”, Voronezh
The work was carried out to study the temperature-field phase in the cast at the stage of solidification modeling of shrinkage defects in the metal and shrinkage defects prediction based on changes in the technological parameters during casting in sand-clay molds by CAD systems SolidWorks and LVMFlow
Keywords: casting, casting and shrinkage defects, the body of the locking screw, solidification process
125
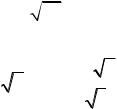
УДК 5.19.1
МОДЕЛИРОВАНИЕ ПЛОТНОУПАКОВАННЫХ ГЕОМЕТРИЧЕСКИХ ОБЪЕКТОВ ДЛЯ ПОСТРОЕНИЯ СТРУКТУРЫ НЕУПОРЯДОЧЕННОГО ВЕЩЕСТВА
Б.М. Даринский1, Д.С.Сайко2, Т.В.Пашнева3, И.А. Стативко3
1Воронежский государственный университет
2Воронежская государственная технологическая академия 3ВУНЦ ВВС «Военно-воздушная академия им. проф. Н.Е. Жуковского
и Ю.А. Гагарина», Воронеж tat120675@yandex.ru
В данной работе рассмотрены алгоритмы построения неупорядоченной структуры вещества. Предложена модель базисных полиэдров, в которых атомная структура стекол представлена в виде многогранников, составленных из базисного набора элементарных полиэдров. Введено понятие симплекcов. Предложена модель строения многоатомного кластера (многогранника)
Ключевые слова: тетраэдр, плотноупакованная геометрическая структура, базис, структура однокомпонентной жидкости, полиэдры
Одна из известных проблем математики – задача о наиболее плотной упаковке равных шаров [1].
Наиболее плотная упаковка на плоскости – это гексагональная решетка, так как правильный треугольник – двумерный симплекс – имеет угол при вершине, соразмерный 2 . В случае трех измерений симплексом является правильный тетраэдр. Телесный угол при вершине тетраэдра несоизмерим с 4 , поэтому в трехмерном пространстве отсутствует плотная упаковка, составленная из правильных тетраэдров. Наиболее плотная из известных трехмерных упаковок шаров имеет кристаллическую гранецентрированную кубическую структуру. Плотность ГЦК структуры (отношение объема шара к объему, приходящемуся на этот шар в структуре) равна [1]: 18 0.7405. В то же время тетраэдра аналогичная величина составляет
V |
|
|
|
2 |
|
|
||
|
|
|
||||||
шар.сегм. |
4 |
2arctg |
|
|
|
0.779636. |
(1) |
|
|
|
|
|
|||||
Vтетраэдра |
|
|
3 |
3 5 |
|
|
||
|
|
|
|
Это позволяет предположить, что существуют более плотные, чем ГЦК структуры в трехмерном пространстве, и эти структуры должны быть непериодическими и содержать тетраэдры в качестве основной компоненты. Алгоритмам построения плотноупакованных геометрических объектов такого типа посвящена данная статья.
Ранее авторами была предложена модель базисных полиэдров [2, 3], в которой атомная структура однокомпонентных жидкостей (стекол) представлялась в виде многогранников, составленных из некоторого базисного набора элементарных полиэдров.
126
Процесс образования некристаллической структуры регулируется механизмом Бенетта: каждый последующий атом присоединяется к трем другим, расположенным подходящим образом в пространстве. Атомные кластеры (полиэдры), организованные по указанному правилу, имеют число связей g, определяемое выражением
g 3 n 2 , |
(2) |
где n – число атомов в кластере. Данная формула справедлива при n 3. Все ранее известные фигуры (полиэдры Бернала) также подчиняются формуле (1). Был произведен последовательный перебор всех полиэдров с числом вершин (атомов) n 14. Было выяснено, что, по крайней мере в указанных рамках, строение плотноупакованного атомного кластера в модели твердых сфер определяется набором из девяти полиэдров. Пять из них, названные базисными, могут присутствовать самостоятельно в аморфной структуре конденсированного состояния однокомпонентного вещества.
При моделировании структуры многогранники могут быть построены из базисных путем примыкания нескольких полиэдров друг к другу. Сформулированы также операции необходимые для построения составных многогранников
сбольшим числом вершин, удовлетворяющих формуле (1).
Вкачестве исходного набора следует рассматривать такой, в котором выполняются условия:
1. Все полиэдры должны иметь только треугольные грани. Если хотя бы одна грань не треугольная, то следующий добавляемый атом образует более чем три связи. Поэтому такой многогранник будет являться составной частью полиэдра, вошедшего в классификацию. Как следствие, все полиэдры, входящие в базисный набор, подчиняются соотношениям
F 2 V 2 , |
E 3 V 2 , |
(3) |
где F – число граней полиэдра, E – число ребер, V – число вершин.
2.Все базисные полиэдры должны быть выпуклыми, то есть отрезок, соединяющий две любые вершины полиэдра, не должен пересекать его грани.
3.Число связей, приходящееся на одну вершину полиэдра, не должно превосходить пяти.
С учетом сказанного, при построении базисных полиэдров следует рассматривать только вершины инцидентные 3, 4 и 5 ребрам. Обозначив числа таких вершин в полиэдре соответственно V3, V4, V5 , запишем систему уравнений:
3V3 4V4 5V5 2E 6 V 2 ; |
V3 V4 V5 V . |
(4) |
С учетом того, что V3 0 только для фигур, составленных из тетраэдров, для фигур с числом вершин n 5 система имеет решение (при дополнительном условии V3 0)
127

V |
12 V5 |
. |
(5) |
|
|||
4 |
2 |
|
|
|
|
|
Таким образом, число вершин выпуклого полиэдра не может превосходить число 12. Совокупность таких полиэдров перечислена в таблице.
Выпуклые полиэдры
V |
V4 |
V5 |
E |
F |
Полиэдр |
4 |
0 |
0 |
6 |
4 |
|
|
|
|
|
|
|
5 |
0 |
0 |
9 |
6 |
|
|
|
|
|
|
|
6 |
6 |
0 |
12 |
8 |
|
|
|
|
|
|
|
7 |
5 |
2 |
15 |
10 |
|
|
|
|
|
|
|
8 |
4 |
4 |
18 |
12 |
|
|
|
|
|
|
|
9 |
3 |
6 |
21 |
14 |
|
|
|
|
|
|
|
10 |
2 |
8 |
24 |
16 |
|
|
|
|
|
|
|
11 |
1 |
10 |
27 |
18 |
нет |
12 |
0 |
12 |
30 |
20 |
|
|
|
|
|
|
|
128
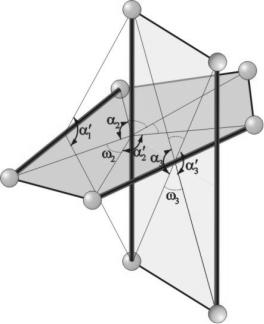
Исследование неупорядоченной геометрической структуры начнем с определения симплексов. В качестве симплексов выберем фигуры, составленные из тетраэдров (не обязательно правильных). Рассмотрим контакт двух бипирамид – пятиугольной и четырехугольной – изображенный на рис. 1.
Представленная на рисунке фигура содержит отрезки единичной длины и «растянутые» отрезки. Геометрическая структура определяется последовательностью выделенных (растянутых) отрезков, соединяющих вершины фигуры. На рисунке не показаны боковые ребра бипирамид, а только те, что лежат в плоскости симметрии. Выделены растянутые ребра – на них опираются углы, обозначенные символом α. Там, где длина ребер равна 1, используется символ ω для обозначения опирающегося на это ребро двугранного угла. Вершины бипирамиды, не лежащие в плоскости симметрии, равноудалены от нее и от вершин, лежащих в указанной плоскости.
Рис. 1. Двугранные углы в плоскостях оснований бипирамид
Построение фигуры начинается с выделенного отрезка с левой стороны (см. рис. 1). Этот отрезок является ребром основания пятиугольной бипирамиды; 1 – двугранный угол при этом ребре, опирающийся на вертикальную ось бипирамиды. В плоскости основания бипирамиды лежат углы 2, 2, 2 . Угол2 порождает следующее растянутое ребро, которое перпендикулярно плоскости симметрии следующей бипирамиды. Плоскости симметрии бипирамид выделены цветом. Число возможных положений растянутых ребер на единицу меньше, чем число ребер основания бипирамиды.
Модель строения многоатомного кластера (многогранника) предполагает последовательность растянутых ребер, выстраивающихся в цепочку. В рамках модели запрещены «ветвящиеся» многогранники, предложенный способ описания контакта предназначен для перечисления плотноупакованных линейных структур. Грани такой структуры – правильные треугольники. Следовательно,
129