
3433
.pdf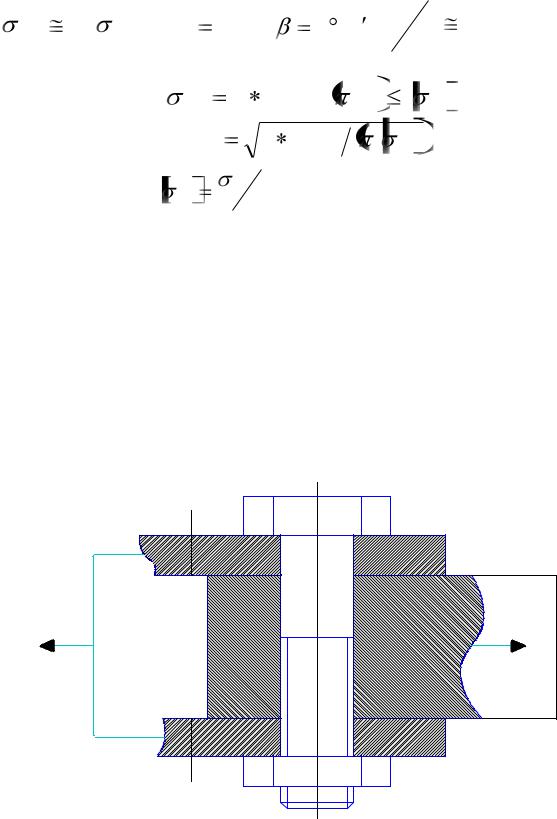
|
Для |
стандартных |
метрических |
резьб |
приближенно |
принимают: |
||||||
|
1,3 |
(при |
f |
0,15 , |
2 30 , |
d2 |
d p |
1,1); |
|
|||
экв |
|
|
||||||||||
|
|
|
|
|
|
|
|
|
|
|
|
|
при этом расчетная формула упрощается: |
|
|
|
|
|
|||||||
|
|
|
|
экв |
4 |
1,3FЗ / |
d12 |
|
P |
; |
|
|
|
|
|
|
d1 |
4 |
1,3F3 |
p |
|
|
|
||
|
|
|
|
P |
T n |
|
|
|
|
(7.23) |
|
|
здесь n – коэффициент запаса при неконтролируемой затяжке; |
|
|||||||||||
n = 1,2…1,5 при контролируемой затяжке. |
|
|
|
|
|
|||||||
|
Случай 3. Болтовое соединение нагружено силами, сдвигающими |
|||||||||||
детали в стыке. Условием надежности является отсутствие сдвига деталей. |
||||||||||||
|
Соединение можно выполнить двумя способами – без зазора и с |
|||||||||||
зазором. |
|
|
|
|
|
|
|
|
|
|
|
|
|
|
|
|
|
а) Соединение без зазора |
|
|
|||||
|
Соединение без зазора обеспечивает напряженную посадку болта в |
|||||||||||
отверстие. Силы трения в стыке не учитывают, поэтому затяжка болта |
||||||||||||
необязательна. |
|
|
|
|
|
|
|
|
|
|
||
|
|
|
|
h1 |
|
|
|
|
|
|
|
|
|
F |
|
|
|
|
|
|
|
|
|
F |
h2 |
|
|
|
|
|
|
|
|
|
|
|
|
|
|
|
|
|
h3 |
|
|
|
|
|
|
|
|
|
|
Рис. 7.7. Схема установки болта в отверстие без зазора |
61
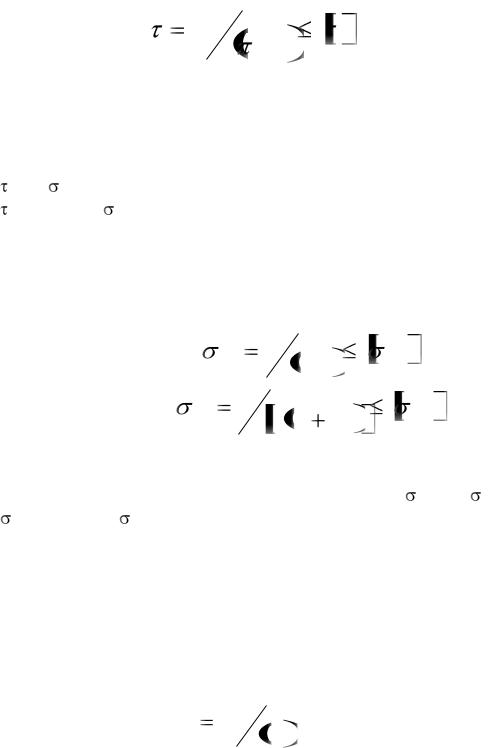
Длина части болта без резьбы должна быть меньше суммы толщин соединяемых деталей на 2-3 мм. Стержень болта рассчитывают по напряжениям среза и смятия. Условие прочности по напряжениям среза имеет вид:
4F |
|
d 2i |
(7.24) |
где i=z-1 – число плоскостей среза(стыка); z – число соединяемых деталей; d
– диаметр стержня болта, равный наружному диаметру резьбы или больше его.
|
Допускаемые напряжения на срез определяют из соотношений: |
[ |
]=0,4 Т – при действии статических нагрузок; |
[ |
]=(0,2…0,3) Т – при действии переменных нагрузок(динамика). |
Расчет на смятие выполняют по условным напряжениям. Условно принимают напряжения смятия равномерно распределенным по диаметральному сечению рассматриваемого участка стержня. Тогда условия прочности по напряжениям смятия можно записать в виде(соответственно для средней и крайних деталей):
|
|
F |
|
|
см |
dh2 |
см |
|
|
||
|
|
F |
h3 |
|
|
d h1 |
|
см |
|
|
см |
Эти формулы справедливы и для болта и для соединяемых деталей. При этом допускаемые напряжения на смятие [ см]=0,8 т – для стали и
[ см]=(0,4…0,5) В – для чугуна.
б) Соединения с зазором
Внешняя нагрузка уравновешивается силами трения, возникающими в плоскости стыка деталей 1, 2, 3 вследствие прижатия деталей одна к одной под действием усилия затяжки болта.
Из условия равновесия одной из деталей в стыке F=iFтр=iFзf, или расчетную зависимость:
F3 |
KF |
(7.25) |
|
if |
|||
|
где Fтр – сила трения;
f – коэффициент запаса от сдвига (к=1,3…1,5 – при статической нагрузке; к=1,8…2,0 – при переменной нагрузке).
Прочность болта оценивается по эквивалентной нагрузке.
62
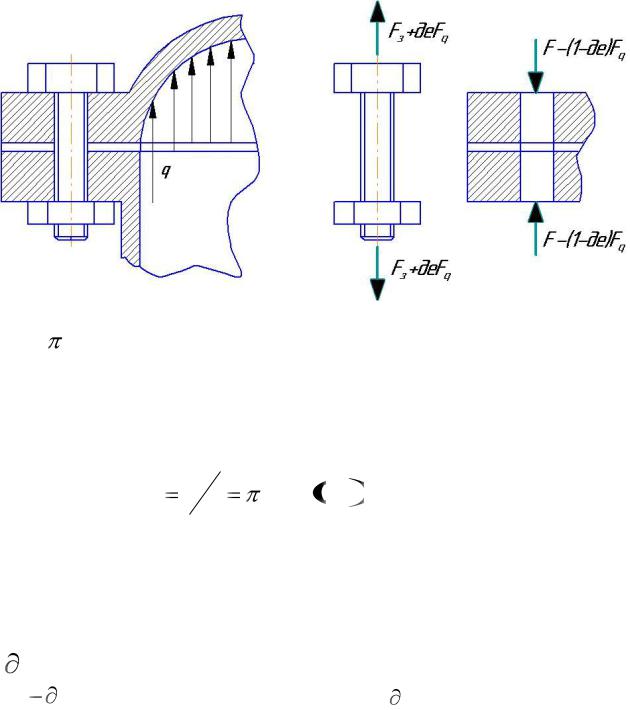
Cлучай 4. Болт затянут, внешняя нагрузка раскрывает стык деталей. Например, фланцевое соединение труб и ассиметричных конструкций
типа оболочек, крепления крышек резервуаров под давлением. После затяжки болтов соединяемые детали находятся под действием сжимающей силы Fз (на участке действия одного болта) а болт растянут такой же осевой силой Fз. При помощи жидкости или газа в резервуаре внутреннее давление увеличивается и на соединяемые детали действует дополнительная нагрузка Q, которая пытается разъединить детали (раскрыть стык).
Рис. 7.8. Резьбовое соединение с затянутым болтом
Q D12 q / 4 , где D1 – внутренний диаметр соединяемых деталей.
где q – давление жидкости или газа внутри резервуара.
Таким образом, на участке действия одного болта помимо силы Fз возникает сила F, по направлению совпадающая с Fз:
F |
Q |
D2 q / 4Z |
(7.26) |
|
Z |
1 |
где z – число болтов.
При нормальной работе соединения должно выполняться условие нераскрытия стыка (сила, сжимающая детали в стыке, должна быть всегда больше нуля). В этом случае часть нагрузки от внешнего давления, равная
eF , дополнительно нагружает болт, а |
остальная часть, равная |
( (1 e)F ), идет на разгрузку стыка; здесь |
e - коэффициент внешней |
нагрузке, который соответствует приходящейся на болт доле внешней нагрузки F. В соответствии с условием нераскрытия стыка(сохранения плотности стыка) можно выразить усилие затяжки через внешнюю нагрузку:
63
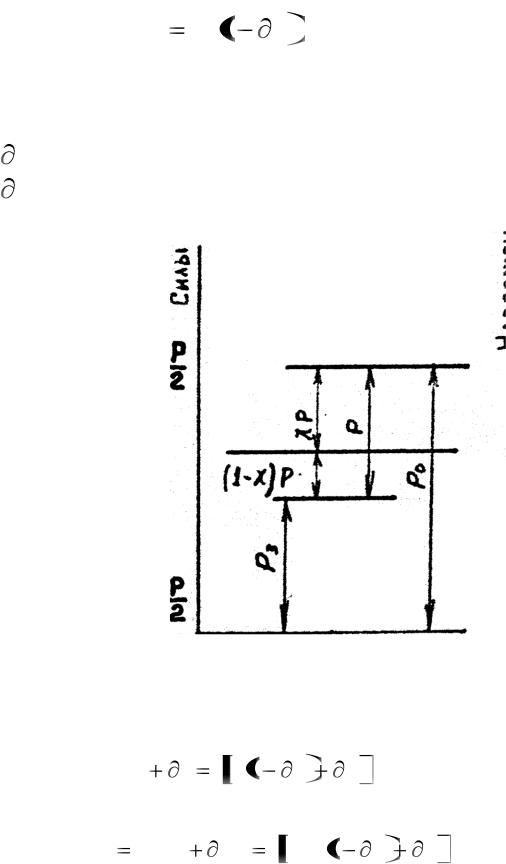
F3 K 1 e F |
(7.27) |
где К – коэффициент затяжки или коэффициент запаса по затяжке (К=1,25…2,00 – при статической внешней нагрузке, К=2…4 – при динамической – переменной – внешней нагрузке;
e = 0,2…0,3 – при жестких фланцах
e = 0,5…0,7 и до 0,9 – при податливых фланцах.
Рис. 7.9. Участок действия сил
Осевая растягивающая сила, действующая на затянутый болт после приложения внешней нагрузки:
F3 |
e |
K 1 |
e |
e F |
(7.28) |
|
Расчетную растягивающую нагрузку Fр |
можно определить с учетом |
|||||
крутящего момента при затяжке: |
|
|
|
|
||
FP 1,3F3 |
eF |
1,3K 1 |
e |
e F |
(7.29) |
По Fр можно определить необходимый внутренний диаметр болта с использованием уравнения (2).
64
РАЗДЕЛ III. ОСНОВНЫЕ ТИПЫ ПЕРЕДАЧ
ТЕМА 8. МЕХАНИЧЕСКИЙ ПРИВОД И ОСНОВНЫЕ ТИПЫ ПЕРЕДАЧ
8.1. Общие сведения
Механическими передачами или просто передачами называют механизмы, служащие для передачи механической энергии на расстояние, как правило, с преобразованием скоростей и моментов, иногда с преобразованием видов(например, вращательное в поступательное) и законов движения.
Основные причины применения передач в машинах следующие:
1.Требуемые скорости движения рабочих органов машины, как правило, не совпадают с оптимальными скоростями двигателя, обычно ниже,
атихоходные двигатели для больших моментов очень громоздки и дороги.
2.Для большинства технологических и транспортных машин необходима возможность регулирования скорости и периодическая работа с большими моментами (при малых скоростях); между тем регулирование скорости двигателя не всегда возможно и экономично.
3.Двигатели обычно выполняют для равномерного вращательного движения, а в машинах часто оказывается необходимым поступательное движение с заданным законом изменения скорости.
4.Двигатели не всегда могут быть непосредственно соединены с исполнительными механизмами из-за требований к габаритам машины, условий ТБ, удобства обслуживания.
Передачи по принципу работы разделяют:
1.Передачи зацеплением с непосредственным контактом (зубчатые, червячные и винт-гайка) и с гибкой связью (цепные).
2. Передачи трением с непосредственным контактом тел качения (фрикционные) и с гибкой связью (ременные).
Наряду с механическими передачами трением и зацеплением широко применяют гидравлические, пневматические и электрические передачи.
Основные характеристики передач: передаточное отношение, передаваемый момент, быстроходность и КПД.
65
ТЕМА 9. ПЕРЕДАЧА ВИНТ-ГАЙКА
9.1. Общие сведения
Передача винт-гайка предназначена для преобразования вращательного движения в поступательное. Особенностью винтовых механизмов является плавность и точность хода, что обеспечило им широкое применение в машиностроении и приборостроении. С помощью винтовых механизмов можно создать большие усилия при малых перемещениях (прессы, домкраты и т.д.).
Достоинствами винтовых механизмов являются: простота конструкции, большое передаточное отношение, возможность получить самотормозящую передачу.
Недостатки - наличие больших потерь на трение в винтовой паре, что приводит к быстрому износу и низкому КПД.
В зависимости от характера относительного движения винта и гайки различают пять типов винтовых механизмов (рис.9.1):
а) винт 1 вращается, а гайка 2 движется поступательно (применяется для установочного движения);
б) винт 1 вращается и движется поступательно, а гайка 3 неподвижна (измерительные и окулярные микрометры, зажимы, прессы и т.п.);
в) гайка 2 вращается, а винт 1 движется поступательно (применяется для установочного движения);
г) гайка 2 вращается и движется поступательно, а винт 1 неподвижен (применяется для грубых установочных механизмов);
д) винт 1 вращается и движется поступательно относительно стойки (как по схеме б), а гайка 2 движется поступательно (применяется для достижения малых точных перемещений вследствие малой разности ходов t13
и t21).
9.2. Примеры конструкции деталей с резьбой
Винты. Винт представляет собой цилиндр, на части которого нарезана резьба. Для силовых механизмов применяются (рис.9.2):
а) треугольная; б) трапецеидальная; в) упорная;
г) прямоугольная резьба (редко).
Широко распространена трапецеидальная резьба, она технологична и прочна.
66
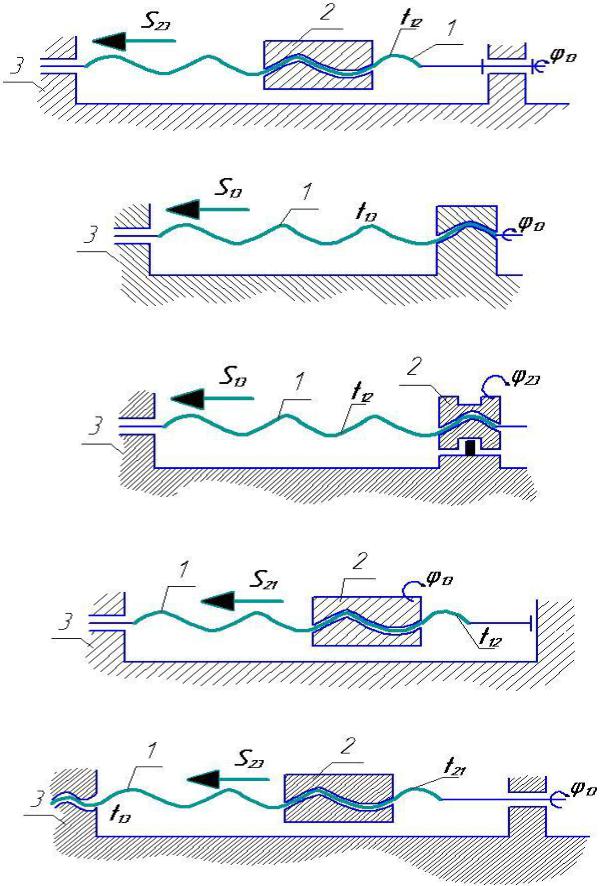
а)
б)
в)
г)
д)
Рис. 9.1. Основные типы винтовых механизмов
67
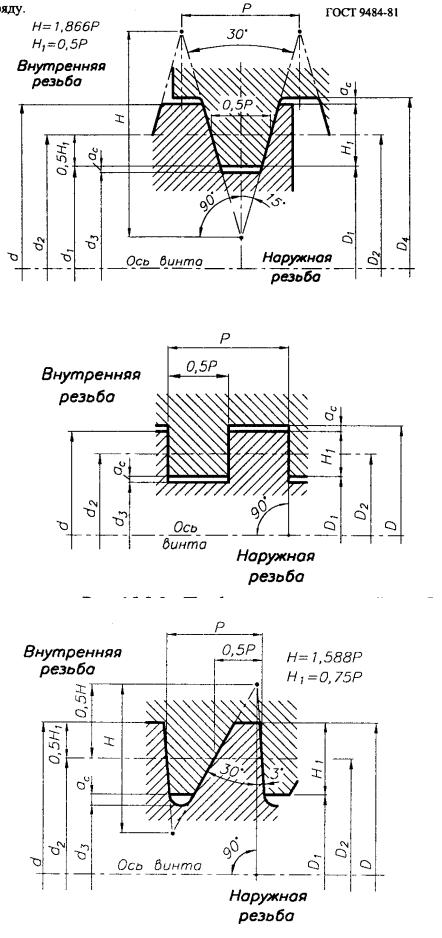
Рис. 9.2. Основные типы резьб
68
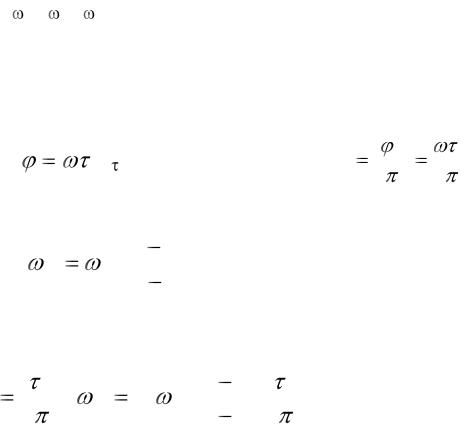
Ходовые винты обычно изготавливаются из сталей 45 и 50. При необходимости получения высокой твердости винтов, применяются стали 40Х, У10, ХГ, ХВГ, 65Г, которые подвергаются термической обработке. Для антикоррозиционной стойкости винты приборов полируют и проводят оксидно-гальваническую отделку (хромирование, кадмирование, цинкование и д.р.).
Гайки. Представляют собой втулку или корпус с резьбой в отверстии и опорными поверхностями, предохраняющие ее от смещения и проворачивания. В механизмах, где предъявляются требования компенсации износа с целью уменьшения мертвого хода (зазора между винтом и гайкой), применяют разрезные гайки, снабженные специальными приспособлениями обеспечивающими радиальную либо осевую выборку зазора(стяжной винт или пружина).
С целью уменьшения потерь на трение гайки изготовляются из оловянистых бронз БрОФЖ10-1, БрОЦС6-6-3, а также антифрикционного чугуна или латуни марок ЧС, Л60-62, пластмасс и др. С этой же целью применяются механизмы с трением качения. Контакт винта с гайкой осуществляется посредством шариков.
9.3. Расчет передачи винт-гайка
Кинематический расчет. В трехзвенном винтовом механизме (рис.9.1,д) угловая скорость ведомого звена (гайки 2) на основании теоремы о сложении скоростей:
23= 13+ |
21 |
(9.1) |
|
|
|
|
а осевое перемещение относительно стойки: |
|
|
|
|
|
|
S23=S13+S21 |
|
(9.2) |
|
|
|
|
Так как перемещение винта S вдоль оси при ходе резьбы t связано с |
||||||
углом поворота |
( - время, с) выражением |
S |
|
t |
|
t , то |
|
2 |
|||||
|
|
2 |
|
|
после совместного решения уравнений(9.1) и (9.2) получим:
t13 t21
23 |
13 |
t23 |
|
(9.3) |
|
|
t21 |
и
S23 |
|
t23 23 |
t23 13 |
t13 |
t21 |
|
|
|
2 |
t23 |
t21 2 |
(9.4) |
|||||
|
|
|
|
69
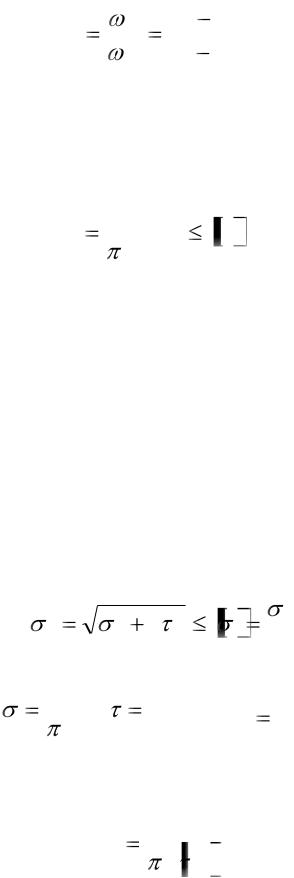
Передаточное отношение:
13 |
|
t23 |
t21 |
||
U12 |
|
|
|
|
|
|
|
t13 |
(9.5) |
||
23 |
|
t21 |
Расчет на износ. Винтовые механизмы с трением скольжения чаще всего выходят из строя из-за повышенного износа резьбы. Износостойкость винтовой пары обеспечивают выбором соответствующих материалов винта и гайки, а так же допустимого давления на резьбе:
P |
PS |
p |
|
|
|
(9.6) |
|||
d2hHr |
||||
|
|
|||
|
|
|
где Р – осевое усилие, действующее на винт; d2 – средний диаметр резьбы;
S – шаг резьбы;
h – рабочая высота профиля резьбы; Hг – высота гайки.
Допустимое давление выбирают в зависимости от материалов винтовой пары: сталь закаленная бронза или сталь[р]=12МПа, сталь незакаленная бронза, сталь или чугун[р]=9; 7 или 5МПа соответственно.
Давления в винтовых парах, применяемых для точных перемещений, применяются в 2-3 раза меньшими.
Расчет на прочность. Поломки винтов встречаются редко, и поэтому расчет на прочность проводится только для сильно нагруженных винтов. При работе винта с внутренним диаметром d1 на кручение и растяжение приведенное напряжение определяют по выражению:
|
2 |
4 |
2 |
|
T |
|
|
|
|
n |
|
|
n |
(9.7) |
|||
|
|
|
|
|||||
|
|
|
|
|
|
|
||
|
4P |
|
T |
|
|
|
||
|
|
|
|
|
и n |
3...5 |
|
|
Где |
2 , |
|
3 |
|
||||
|
d1 |
0,2d1 |
|
|
|
Крутящий момент Т определяется по формулам приведенным при расчете резьбовых соединений, в зависимости от типа резьбы.
Из расчета на срез определяется необходимая высота гайки:
Hr |
|
PS |
|
|
|
|
(9.8) |
||
d |
ср / 2 |
|||
|
||||
|
|
где d – наружный диаметр резьбы;
70