
3433
.pdf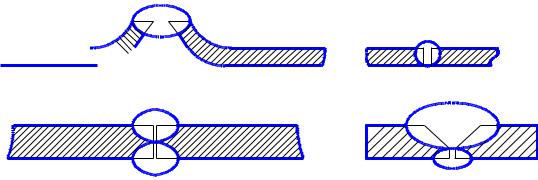
Соединение деталей с помощью контактной электросварки происходит за счет разогрева стыка теплом, выделяющимся при прохождении тока через место контакта соединяемых деталей при одновременном действии силы, сжимающей их. Чаще всего применяется точечная, стыковая, роликовая и коротко импульсная сварка.
При газовой сварке оплавление элементов деталей и прутка присадочного материала происходит в струе газового пламени. Такая сварка применяется при соединении деталей из металлов или сплавов с различными температурами плавления, а также пластмассовых деталей.
Достоинства газовой сварки являются возможность сваривать неметаллические материалы и независимость от источников электроэнергии.
Недостатки: возможность значительного коробления деталей, ограничение толщины свариваемых деталей (не более 30-40 мм), более низкая прочность швов чем при дуговой сварке.
При электродуговой сварке, в зависимости от расположения свариваемых деталей (рис.4.1), различают соединения стыковое, нахлесточное, впритык или тавровое, угловое.
При стыковых соединениях (рис.4.2.) используют стыковые швы с отбортовкой кромок, односторонние и двусторонние, без скоса и со скосом кромок.
а
б
в |
г |
Рис. 4.2. Типы соединений встык:
а) с отбортовкой кромок; б) без скоса односторонний; в) без скоса двусторонний; г) со скосом двусторонний
Востальных упомянутых видах соединений швы имеют форму валиков
иназываются валиковыми или чаще угловыми швами, которые также применяются без скоса (рис.4.1,б,г) и со скосом кромок (рис.4.1,в) и бывают односторонними (рис.4.1,г) и двусторонними (рис.4.1,в). Условное изображение и обозначение швов сварочных соединений стандартизировано
(ГОСТ 2.312-72).
Вшвах с отбортовкой и без разделки кромок при больших толщинах соединяемых деталей, расплавлением (провар) металла по всему соединению, особенно при ручной сварке, не обеспечивается. Поэтому в
31
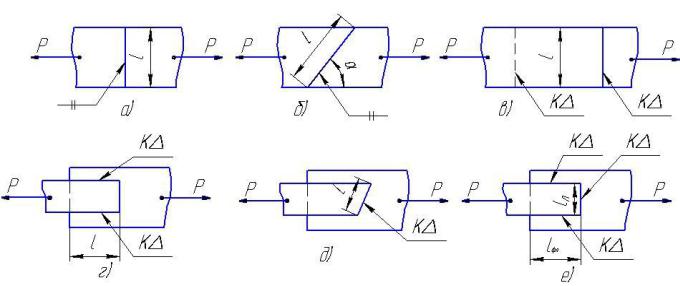
стыковых соединениях, выполняемых ручной сваркой, швы без разделки кромок применяют при сваривании углеродистой стали толщиной 1…6 мм при одностороннем шве и 3…8 мм – при двустороннем, а при автоматической или полуавтоматической сварке под слоем флюса - соответственно толщиной 2…5 мм и 2…20 мм. Выполнение скосов кромок позволяет увеличить толщину свариваемого металла. Конструктивные элементы подготовки кромок и размеры швов при сваривании листов из углеродистых и низколегированных сталей приведены в ГОСТ 5264-80 (для ручной сварки) и ГОСТ 8713-79 (для автоматической и полуавтоматической сварки под слоем флюса).
В зависимости от расположения шва относительно линии действия силы соединения встык, различают прямые и косые швы (рис.4.3,а,б); при соединениях внахлестку – лобовые, фланговые, комбинированные и косые швы (рис.4.3,в,г,д,е).
Для предупреждения возникновения повышенных изгибных напряжений лобовые швы рекомендуется располагать с двух сторон. При этом длина перекрытия соединяемых элементов не должна быть меньше 4S. Длина лобовых и косых швов не ограничивается; длина фланговых швов не должна превышать 50…60 К (К – длина катета углового шва).
Рис. 4.3. Виды швов по их ориентации относительно линии действия силы
32
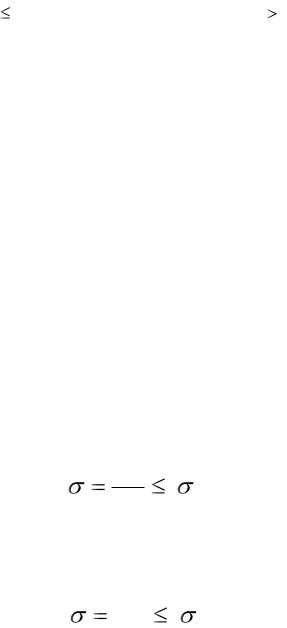
Разделка кромок в соединениях с большими толщинами (до 16 мм), выполненных газовой сваркой, примерно такая же, как при ручной электродуговой сварке. В качестве присадочного материала применяется проволока Св-08 и Св-08А по ГОСТ 2246-70.
Для стыковых соединений контактной сваркой необходимо, чтобы сечения свариваемых деталей в листе соединения совпадали по форме. При точечной сварке внахлестку качество соединения зависит от количества свариваемых деталей, которое не должно превышать четырех (при сварке двух деталей качество наилучшее), и от взаимного расположения сварочных точек в шве. Не рекомендуется соединение деталей точечной сваркой с разницей толщины их в три раза и более. Диаметр d точки назначается в зависимости от наименьшей толщины свариваемой детали; для стальных деталей при S 1,5…3 мм, d=1,2S+4 мм, при S 3 мм, d=1,55+5 мм. Обычно расстояние (шаг) между центрами точек при соединении двух или трех деталей e=3d и e=4d соответственно. Расстояние от оси точки до кромки в направлении действия нагрузки e1=2d при соединении двух и e1=3d при соединении трех деталей.
4.2. Расчеты на прочность сварных швов при постоянных нагрузках
Сварное соединение должно быть по возможности равнопрочные с основным металлом конструкций.
Влисте шва сварных конструкций могут возникать напряжения двух родов – рабочие и связывающие.
К первым относятся напряжения в соединениях, разрушение которых приводит к выходу конструкции из строя; ко вторым – напряжения, возникающие в наплавках при их совместной работе с основным металлом, в большинстве случаев они не опасны для прочности конструкции и в расчетах не учитываются.
Всоединениях в стык (рис.4.1, а), условие прочности шва длинной l (рис.4.3,а), при работе на растяжение:
P
S [ p '] (4.1)
при работе на сжатие:
P |
[ сж |
'] |
|
|
|
(4.2) |
|||
S |
||||
|
|
|
33
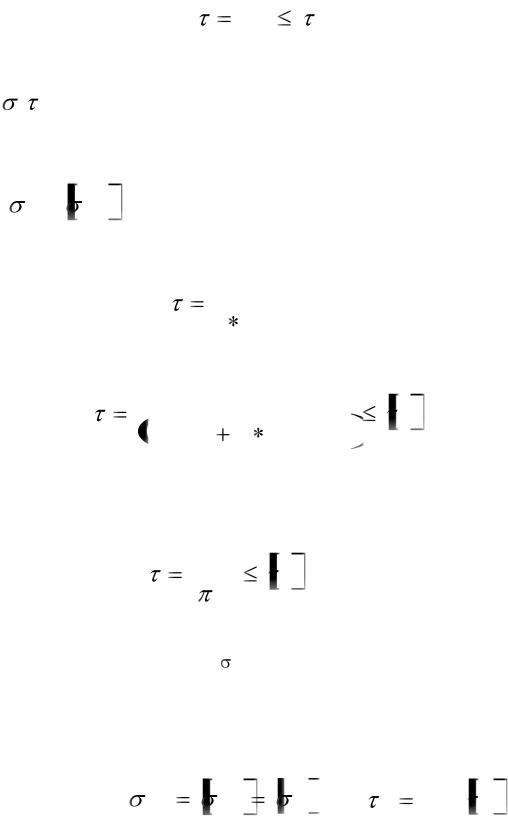
Если шов расположен под углом (обычно 450) к направлению усилия (рис.4.3,б), то его прочность условно определяется по формуле:
P |
[ '] |
|
|
|
(4.3) |
||
S |
|||
|
|||
|
|
Вприведенных зависимостях:
,- нормальное и касательное напряжения в материале шва;
P – действующее усилие;
S – толщина соединяемых элементов; l – длина шва;
[ p '], |
/ |
сж - допускаемое нормальное напряжение материала шва; |
Для соединений внахлестку в лобовых (рис.4.3,в) и фланговых швах
(рис.4.3,г):
P
2 0,7Kl |
(4.4) |
|
В комбинированных швах на основании принципа независимости действия сил:
P |
/ |
|
|
|
|
0,7KlЛ 2 |
(4.5) |
|
0,7KlфЛ |
В тавровых соединениях при угловых швах (рис.4.1,в) прочность определяется по формуле(4.4). Угловые соединения чаще всего применяются в связывающих элементах и на прочность не рассчитываются.
В соединениях в нахлестку с точечной сваркой напряжение в точке:
4P /
i d |
2 |
(4.6) |
|
|
Допускаемые напряжения в сварных швах конструкций в зависимости от качества выполнения шва и способа сварки выбирают как часть допускаемого напряжения [ р] для основного металла.
Так, в швах соединений из малоуглеродистой и среднеуглеродистых конструкционных сталей, выполненных полуавтоматической и автоматической сваркой под слоем флюса, в среде защитного газа, а также вручную электродами типа Э42А и Э50А (ГОСТ 9467-75) при растяжении и сжатии:
[ p '] |
/ |
p , при [ '] 0,65 p . |
сж |
34

Для соединений, сваренных электродами обычного качества, например Э42 и Э50:
[ p '] 0,9 p , [ сж '] p , [ '] 0,6 p .
Для соединений с контактной точечной сваркой: [ '] 0,5 p .
35
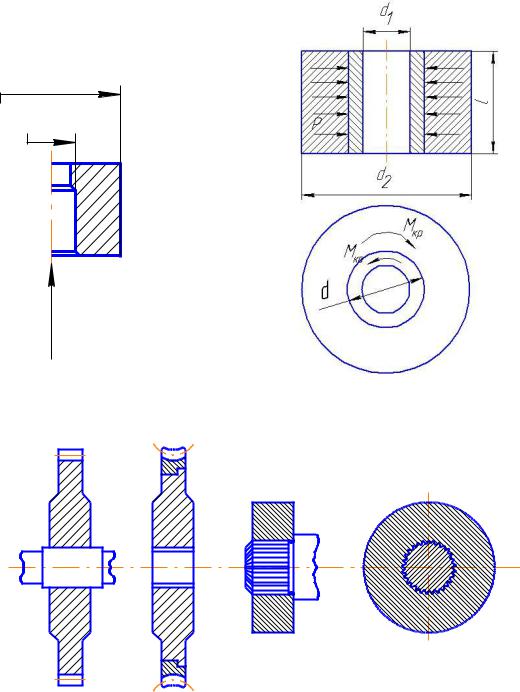
ТЕМА 5. СОЕДИНЕНИЯ С НАТЯГОМ, КЛЕММОВЫЕ СОЕДИНЕНИЯ
5.1. Расчет соединений с гарантированным натягом
Назначение. Соединения этого типа обеспечивают неподвижное скрепление деталей за счет сил трения, возникающих между охватываемой и охватывающей поверхностями при сборке деталей по посадке с натягом
(рис.5.1,а)
d2 |
d1 |
P |
а) |
б) |
Рис. 5.1. Соединения с натягом
Рис. 5.2. Соединения запрессовкой
36
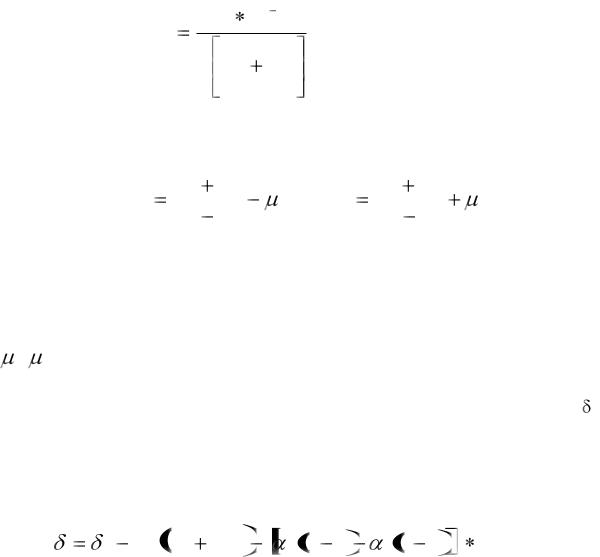
Такой способ соединения применяют для сборки деталей, нагруженных значительными усилиями или подверженных вибраций и ударов: при соединении зубчатых колес с валами (рис.5.2,а) или бандажей червячных колес со ступицей (рис.5.2,б). Кроме гладких, в соединениях с натягом применяют накатанные детали. Надежность соединения при этом обеспечивается за счет вдавливания зубцов накатки в цилиндрическую поверхность сопряженной детали (рис.5.2,в).
Расчет. При сборке деталей с натягом сопрягающиеся поверхности оказываются нагруженными давлением Р (рис.5.1,б), величина которого в МПа может быть подсчитана по формуле (применима только при упругих деформациях):
Р 10 3
|
d |
|
c1 |
|
c2 |
|
|
(5.1) |
|
||
|
|
E1 |
|
E2 |
|
|
|
|
|
||
где коэффициенты: |
|
|
|
|
|
|
|
|
|
|
|
|
d 2 |
d 2 |
|
|
|
d 2 |
d 2 |
|
|||
c1 |
|
1 |
|
|
|
c2 |
|
2 |
|
|
|
d 2 |
d 2 |
1 |
d 2 |
d 2 |
1 |
||||||
|
|
1 |
|
|
|
|
2 |
|
|
|
d- номинальный посадочный диаметр сопрягающихся поверхностей, мм;
d1 – диаметр отверстия охватываемой детали (для сплошного вала d1 =0), мм; d2 – наружный диаметр охватывающей детали, мм;
б – расчетный натяг, в мкм;
1, 2 , E1, E2 - модули упругости, МПа, и коэффициенты Пуассона материалов охватывающей и охватываемой деталей.
При проектировании соединения деталей расчетный натяг т с поправками, учитывающими уменьшение его вследствие обмятии микронеровностей поверхностей RZ1 и RZ2 в месте сопряжения, различия рабочих температур t1, t2 деталей и коэффициентов линейного расширения d1, d2 материалов сопрягаемых деталей:
T |
1,2 RZ |
RZ |
2 |
2 t2 t |
1 t1 t d 103 |
(5.2) |
|
1 |
|
|
|
где t – температура в сборочном помещении;
RZ2, RZ1 – высота неровностей профиля шероховатости (ГОСТ 2789-73) сопрягаемых поверхностей.
Наибольший крутящий момент, которым может быть нагружено соединение:
37
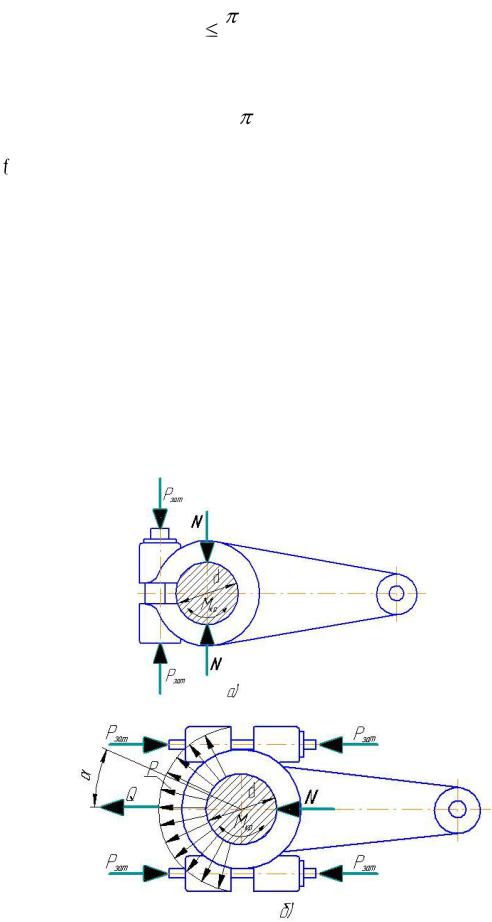
T |
|
d 2lpf |
(5.3) |
|
2 |
||||
|
|
|||
|
|
|
наибольшая осевая сдвигающая сила:
P dlpf (5.4)
где - коэффициент трения.
5.2. Клеммовые соединения
Назначение. Клеммовое соединения предназначено для закрепления деталей на валах, круглых стержнях, колоннах; оно может передавать крутящий момент и осевую силу. Охватывающая деталь удерживается на охватываемой за счет сил трения, возникающих на сопрягающихся поверхностях.
Применяются два основных типа клеммовых соединений (рис.5.3): со ступицей, имеющей прорезь (а), и с разъемной ступицей (б). Преимущество клеммового соединения заключается в возможности регулировки взаимного расположения деталей, простоте сборки и разборки, недостаток – относительно большие габариты.
Рис. 5.3. Клеммовые соединения.
38

Расчет. Если с каждой стороны клеммы с разъемной ступицей установлено Z болтов (рис.5.3,б) и сила затяжки каждого из них Рзат, то сила давления со стороны клеммы на вал равна 2РзатZ. Считая, что давления по окружности распределяются по косинусоидальному закону р=р0cos , из условия равновесия клеммы длинною l и равномерном распределении р; 2 равнодействующая давления со стороны каждой полуступицы:
2
Q 2Pзат Z 2
0
p |
d |
l cos d |
pdl |
|
|
(5.5) |
|||
2 |
|
|
||
|
|
|
А суммарная, нормальная к поверхности вала сила N от каждой полуступицы, способная передавать сдвигающую силу N ( - коэффициент трения):
N |
dlp |
|
Q |
|
|
|
|
|
(5.6) |
||
2 |
2 |
||||
|
|||||
|
|
oткуда:
Pзат |
Q |
|
N |
|
|
|
|
(5.7) |
|
2Z |
|
Z |
||
|
|
|
Условие передачи соединением момента Т с коэффициентом запаса n имеет вид:
2Nf |
d |
nT или N |
nT |
|
|
|
|
|
fd |
|
(5.8) |
||||
2 |
|
|
|
||||
Условие передачи соединением осевой силы Fа, равномерно |
|||||||
распределенной между двумя полуступицами: |
|
||||||
2Nf |
nFa или |
N |
nFa |
(5.9) |
|||
2 f |
|||||||
|
|
|
|
|
|
39
ТЕМА 6. ШПОНОЧНЫЕ, ШТИФТОВЫЕ
ИШЛИЦЕВЫЕ СОЕДИНЕНИЯ
6.1.Типы шпонок. Расчетные зависимости
Назначение. Шпоночные соединения осуществляются с помощью специальной детали – шпонки, закладываемой в пазы соединяемых деталей. Оно обеспечивает неподвижное скрепление соединяемых деталей и служит для передачи крутящего момента. В том случае, когда необходимо обеспечить возможность относительного смещения деталей в осевом направлении, применяют соединения со скользящей шпонкой.
Достоинства и недостатки. Достоинствами шпоночных соединений являются простота и надежность конструкции, удобство сборки и разборки, невысокая стоимость. К недостаткам следует отнести ослабление сопрягаемых деталей из-за уменьшения их сечения пазами и концентрации напряжений, а также сложность обеспечения концентричной посадки сопрягаемых деталей.
Типы шпонок. Различают следующие типы шпонок, наиболее часто употребляемых в машиностроении и приборостроении (рис.6.1): а – клиновая врезная (ГОСТ 24068-80) создает напряженное состояние по широким граням шпонки и передает крутящий момент за счет сил трения на них; б – призматическая обыкновенная со скругленными торцами (ГОСТ 23360-78), воспринимает давление боковыми узкими гранями; в – призматическая направляющая врезная с креплением на валу (ГОСТ 8790-79), допускает перемещение сопряженной детали вдоль оси вала; г – сегментная (ГОСТ 24071-80) работает подобно призматической обыкновенной; д – круглая цилиндрическая и коническая (не стандартизированы).
40