
3433
.pdfРАЗДЕЛ II. СОЕДИНЕНИЯ ДЕТАЛЕЙ МАШИН
ТЕМА 3. ЗАКЛЕПОЧНЫЕ СОЕДИНЕНИЯ
3.1. Классификация, область применения, достоинства и недостатки различных видов соединений
Под соединениями в машиностроении понимают узлы, образованные соединительными деталями (заклепками, винтами и др.) и прилегающими частями соединительных деталей (например, фланцами), форма которых обычно подчинена задаче соединения.
Соединения позволяют составить – собрать из отдельных деталей машину или агрегат.
Соединения по признаку разборки делят на неразъемные, которые нельзя разобрать без разрушения или повреждения (заклепочные, сварные), и разъемные, позволяющие повторную сборку и разборку (резьбовые, клиновые и др.).
Неразъемные соединения осуществляются силами молекулярномеханического сцепления (сварные, паяные, клеевые) или механическими средствами (клепаные, соединения с натягом, вальцованные).
Общей тенденцией развития соединений является приближение их к целым деталям и удовлетворение условию равнопрочности с соединенными элементами. Иначе материал соединяемых элементов не будет полностью использован. Соединения элементов сосудов и трубопроводов, содержащих жидкости или газы, должны удовлетворять условиям плотности (герметичности). Для этого контактирующие поверхности механических соединений должны быть сжаты давлением, существенно превышающим давление среды.
В связи с необходимостью сохранения точности под нагрузкой, соединения должны удовлетворять условию жесткости.
Достоинствами заклепочных соединений (по сравнению со сварными) является возможность соединения не свариваемых деталей, меньшие повреждения соединяемых элементов при разборках, меньшая концентрация напряжений из-за возможных смещений детали в соединении. Недостатками являются большая трудоемкость и больший расход металла, малая производительность и высокая стоимость.
Заклепочные соединения применяются в авиационных конструкциях, некоторых строительных конструкциях, приборостроении.
Соединение частей в одно целое при сварке получается за счет местного нагрева соединяемых частей до расплавленного или пластического состояния. Сваркой можно соединять как металлические, так и неметаллические детали.
Сварное соединение является самым совершенным из неразъемных соединений. Его преимуществами являются:
21
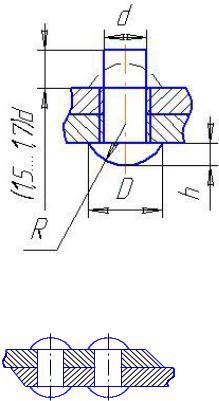
1)равнопрочность по отношению к соединяемым элементам;
2)экономия материала и уменьшение массы конструкции по сравнению с заклепочными соединениями;
3)высокая производительность и простота сварки.
Недостатками сварочных соединений являются появление температурных напряжений и концентрация их, а также возможность коробления при сваривании тонкостенных элементов.
3.2. Основные типы заклепок и заклепочных соединений. Область применения
Заклепочные соединения образуют постановкой заклепок в совмещенные отверстия соединяемых элементов и расклепкой с осаживанием стержня (рис.3.1,б). Заклепка (рис.3.1,а) представляет собой стержень круглого сечения с головками на концах, одну из которых, называемую закладной, выполняют на заготовке заранее, а вторую, называемую замыкающей, формируют при клепке.
а)
б)
Рис. 3.1. Заклепка с полукруглыми головками и простейшее заклепочное соединение
22
Заклепки стягивают соединяемые детали, в результате чего часть или вся внешняя продольная нагрузка на соединения передается силами трения на поверхности стыка.
Заклепочные соединения разделяют на:
1)силовые (иначе называемые прочными соединениями), используемые преимущественно в конструкциях машин, в строительных сооружениях;
2)силовые плотные (иначе называемые плотно-прочными соединениями), используемые в котлах и трубах, работающих под давлением.
Область практического применения заклепочных соединений ограничивается следующими случаями:
1)Соединения, в которых нагрев при сварке недопустим из-за опасности отпуска термообработанных деталей или коробления, окончательно обработанных точных деталей;
2)Соединения несвариваемых материалов;
3)Соединения в самолетах, например, в только одном современном пассажирском самолете применяют до 2,5 млн. заклепок;
4)Соединения в автомобилестроении, для рам грузовых машин. Заклепки изготовляются из сталей (Ст.2, Ст.3, 10, 15), латуни, меди,
алюминия. Клепку стальными заклепками диаметром 8…10 мм, а также заклепками из латуни, меди и легких сплавов всех диаметров производят холодным способом, а остальных – горячим способом.
Заклепочное соединения осуществляется либо с помощью специальных деталей – заклепок (рис.3.2,а,в), либо с помощью цапф, предусматриваемых на соединяемых деталях (рис.3.2,б,г), которые могут выполняться сплошными или пустотелыми, называемыми пистонами (рис.3.2,б). Одна из головок заклепки называется закладкой, а другая, которая образуется в процессе клепки, - замыкающей. Соединяемые детали при этом сильно сжимаются.
23
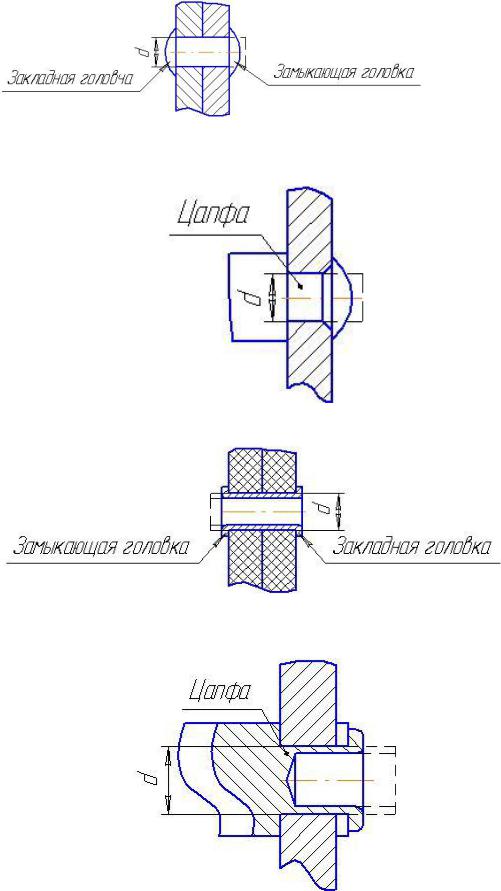
а)
б)
в)
г)
Рис. 3.2. Заклепочные соединения
24
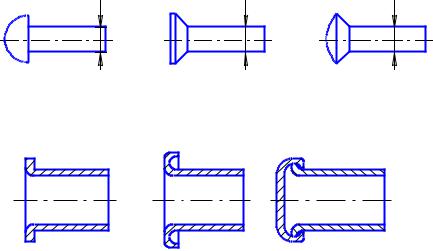
Форма и размеры заклепок стандартизированы. Некоторые типы заклепок и пистонов приведены на рис.3.3:
а) с полукруглой закладной головкой(ГОСТ 10299-80); б) потайной головкой (ГОСТ 10300-80); в) полупотайной головкой (ГОСТ 10301-80); г) точечная пустотелая; д) штампованная пустотелая;
е) штампованная, пустотелая с закрытой головкой.
d |
d |
d |
а) |
б) |
в) |
г) |
д) |
е) |
Рис. 3.3. Типы заклепок
Различают три основных типа заклепочных соединений: в нахлестку (рис.3.4,а), с одной (рис.3.4,б) и двумя (рис.3.4,в) накладками; однорядные, двухрядные (рис.3.4,г) и т.д. Конструкция шва выбирается в зависимости от условий работы и формы соединяемых деталей (листы, профильный материал). При конструировании швов следует стремиться к обеспечению симметричного расположения плоскостей срезывания относительно действующей силы Р (рис.3.4,в), так как в противном случае (рис.3.4,б) стержень заклепки подвергается изгибу и появляются усилия, стремящиеся оторвать головки заклепок.
25
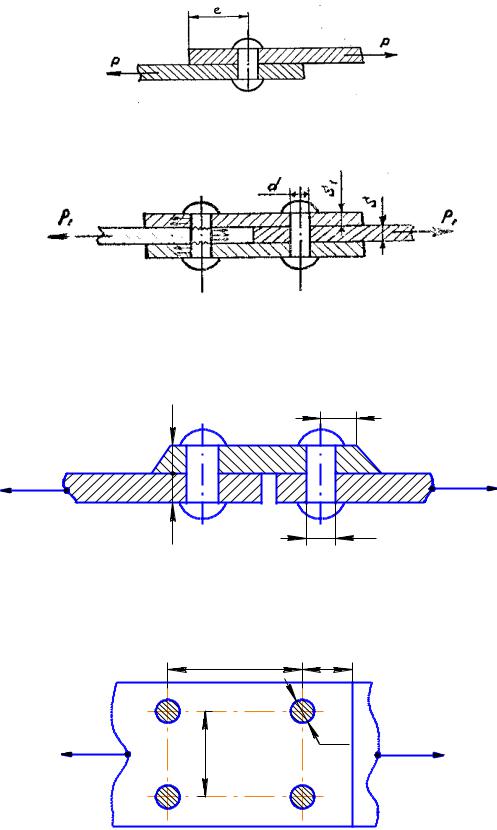
а)
|
б) |
|
S |
l |
|
|
|
|
P |
|
P |
S |
|
d |
|
|
|
|
в) |
|
m |
l |
|
P |
d |
P |
|
||
t |
|
|
г)
Рис 3.4. Типы заклепочных соединений
26
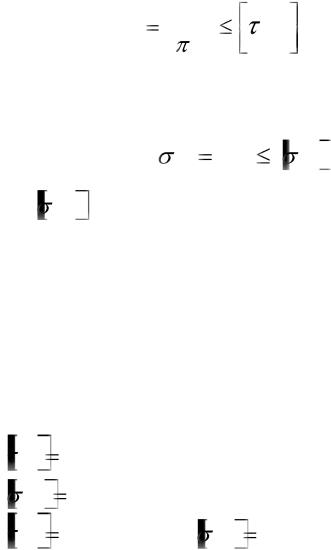
3.3. Расчет на прочность силовых заклепочных соединений
Заклепки в соединении, находящимся под действием продольных сил, рассчитываются на срез и проверяются на смятие (в плотных соединениях проверка на смятие не проводится, т.к. вся внешняя нагрузка воспринимается силами трения), хотя вначале нагрузка передается силами трения, затем в работе участвует тело заклепки, подвергаясь изгибу, смятию и сдвигу. Условность расчета учитывается соответствующим выбором допустимого напряжения на срез. Расчетная формула имеет вид:
τ |
4Р1 |
ср |
|
||
i d |
2 |
(3.1) |
|||
|
|||||
|
|
|
При проверочном расчете боковой поверхности заклепки на смятие:
|
P |
|
|
|
1 |
|
|
см |
Sd |
см |
(3.2) |
|
|
|
где см - допускаемое напряжение смятия; S – толщина соединяемой детали;
Диаметр заклепки d обычно выбирается в зависимости от толщины склепываемых деталей: d=s+1мм. После определения допускаемого усилия из формулы (3.1.) определяют необходимое число заклепок, как отношение полного усилия в соединении к допускаемому на одну заклепку.
Величины допускаемых напряжений при статических нагрузках назначаются в зависимости от материала заклепок и способа обработки отверстий: при сверленных отверстий для заклепок из Ст.0, Ст.2 и Ст3:
сp |
140МПа , |
см |
280...320МПа при продавленных поверхностях |
сp |
100МПа и см 240...280МПа |
27
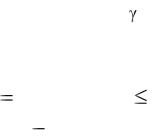
При действии переменных нагрузок, допускаемые напряжения понижаются умножением на коэффициент , значение которого зависит от характера изменения усилий на заклепки. Для соединений деталей из малоуглеродистой стали:
|
|
|
|
γ |
1 |
|
|
1 |
|
||
|
|
|
|
|
|
|
|
|
|
||
|
|
|
|
|
|
|
P |
|
(3.3) |
||
|
|
|
|
|
|
|
|
|
|
||
|
|
|
|
|
1 0.3 |
|
min |
|
|
|
|
|
1 |
|
|
|
|
Pmax |
|
|
|
||
|
|
|
|
|
|
|
|
|
|
||
γ |
|
|
|
|
|
|
|
|
|
|
|
|
P |
|
|
|
|
|
|
|
|
|
|
|
|
- |
отношение минимальной и |
максимальной, |
по абсолютной |
||||||
|
1 0.3 |
min |
|
|
|
|
|
|
|
|
|
|
|
Pmax |
|
величине силам, взятым со своими знаками |
|
||||||
|
|
|
|
|
|
|
|
|
|
|
Остальные параметры заклепочного соединения (рис.3.4,г) выбирают в зависимости от диаметра заклепки:
l = (1,5…2,0)d; m = (2…3)d; t = (3…4)d.
Заклепочные соединения приборов обычно не рассчитывают на прочность, а выбирают из конструктивных соображений: в зависимости от суммарной толщины склепываемых деталей S (в пределах S=2…10мм) диаметр заклепки d=0,5*S+1 мм.
28
ТЕМА 4. СВАРНЫЕ СОЕДИНЕНИЯ
4.1. Основные типы сварочных соединений
Сварные соединения – это неразъемные соединения, основанные на использовании сил молекулярного сцепления и получаемые путем местного нагрева деталей до расплавленного состояния (сварка плавлением, электродуговая, электрошлаковая и д.р.) или до тестообразного состояния, но с применением механической силы (контактная сварка).
Сварные соединения являются наиболее совершенными неразъемными соединениями, т.к. лучше других приближают составные детали к целым и позволяют изготовлять детали неограниченных размеров. Прочность статических соединений при статических и ударных нагрузках доведена до прочности деталей из целого материала. Освоена сварка всех конструкционных сталей, включая высоколегированные, цветных сплавов и пластмасс.
Существует несколько наиболее распространенных способов сварки: электродуговая, электрошлаковая, контактная и газовая.
При электродуговой сварке под действием тепла, выделяемого электрической дугой, оплавляются соединяемые элементы, и оплавленный металл вместе с металлом электрода, обмотанным защитным покрытием или под слоем флюса, образует прочный шов. Этим способом свариваются конструкционные материалы любых марок, титан, чугун, аллюминивые и медные сплавы. Сварка может выполняться с помощью сварочных автоматов и полуавтоматов или вручную. В первом случае обеспечивается более высокое качество шва, большая производительность и экономичность процесса, особенно в серийном производстве. Ручная дуговая сварка используется, когда по условиям производства, когда применения автоматических и полуавтоматических способов невозможно.
Электродуговая сварка в среде защитного газа (аргона или гелия) применяется при сваривании высоколегированных сталей, алюминиевых, магниевых сплавов, меди, молибдена и др. металлов и сплавов. Разновидностью электродуговой сварки в среде защитного газа является атомно-водородная сварка, применяемая при сваривании алюминия, низколегированных конструкционных и хромоникелевых нержавеющих сталей. В процессе сварки водород сгорает, и факел его пламени надежно защищает сварочную ванну от воздействия кислорода воздуха.
Электрошлаковая сварка позволяет сваривать металл практически неограниченной толщины. Нагревание металла осуществляется за счет тепла, выделяющегося при прохождении тока через электропроводящую шлаковую ванну, от электродов к соединяемым частям детали.
29
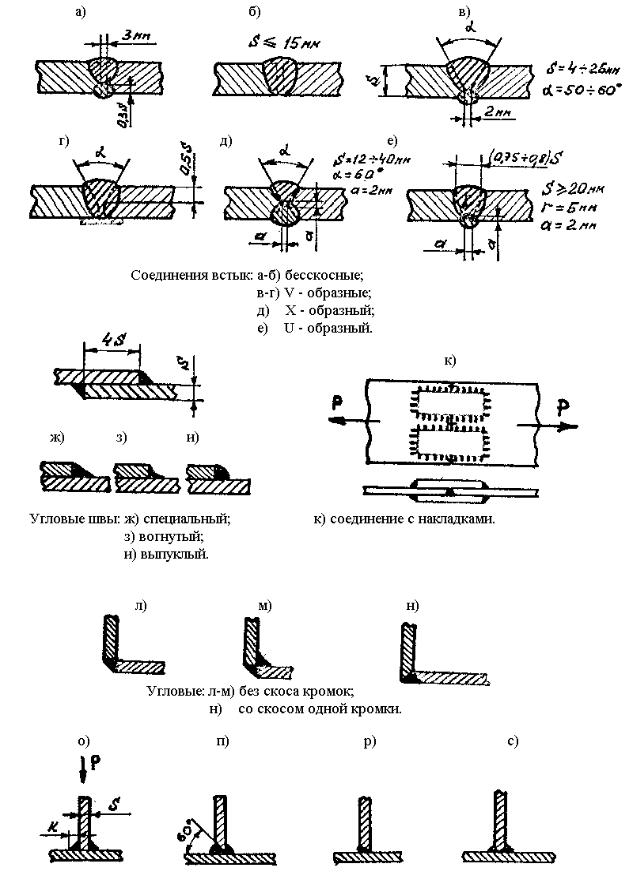
Рис. 4.1. Виды сварных соединений
30