
3433
.pdfТЕМА 2. ОБЩИЕ ВОПРОСЫ ПРОЕКТИРОВАНИЯ ДЕТАЛЕЙ И УЗЛОВ МАШИН
2.1. Виды нагрузок, действующих на деталь
При определении нагрузок, действующих на деталь механизма, следует учитывать все внешние нагрузки, воспринимаемые деталью, могут быть подразделены на две группы: нагрузки рабочего и нерабочего состояния. При этом нагрузки рабочего состояния подразделяются на нормальные и максимальные.
Кнормальным нагрузкам рабочего состояния относятся: основные нагрузки – собственный вес машины и номинальные рабочие нагрузки; дополнительные нагрузки – инерционные нагрузки, действующие в период пуска и торможения.
Кмаксимальным нагрузкам рабочего состояния относятся следующие: основные нагрузки – собственный вес машины и номинальные рабочие нагрузки; дополнительные нагрузки – инерционные нагрузки при экстренном торможении.
Кмаксимальным нагрузкам нерабочего состояния (когда ни один механизм или деталь машины не работает) относят: собственный вес узлов машины.
2.2. Классификация напряжений
Нагрузки на детали машин и напряжения в них, как известно, могут быть постоянными и переменными по времени.
Детали, подверженные постоянным напряжениям в чистом виде, в машинах почти не встречаются. Постоянная, неподвижная в пространстве нагрузка вызывает во вращающихся деталях (валах, осях, зубьях зубчатых колес) переменные напряжения. Однако некоторые детали работают с малоизменяющимися напряжениями, которые при расчете можно принимать за постоянные. К таким деталям могут быть отнесены детали с большими нагрузками от силы тяжести(в транспортных и подъемно-транспортных машинах), детали с большой начальной затяжкой (заклепки, часть крепежных винтов и пружин) и детали с малым общим числом плавных нагружений.
Переменные напряжения, прежде всего, характеризуются циклом изменения напряжений.
В деталях машин возникают следующие циклы изменения напряжений:
а) отнулевой цикл, в котором напряжения меняются от нуля до максимума(зубья зубчатых колес, работающих в одну сторону, штоки, толкатели и шатуны тихоходных механизмов, малонагруженные при обратном ходе и т.д.);
11
б) знакопеременный симметрический цикл, в котором напряжения меняются от отрицательного до такого же положительного значения (напряжения изгиба во вращающихся валах и осях);
в) ассиметричный, знакопостоянный (винты, пружины) или знакопеременный цикл.
Постоянные режимы характерны для центральных силовых и насосных станций и транспортных машин дальнего следования, переменных – для большинства машин – универсальных машин-орудий, транспортных машин и т.д.
Переменные режимы могут быть регулярными, т.е. с постоянными амплитудами и средними напряжениями, и не регулярными – с непостоянными амплитудами и средними напряжениями.
Нагрузки могут изменяться плавно или прикладываться внезапно (удары). Существенные ударные нагрузки действуют в машинах ударного действия и в транспортных машинах. Удары бывают связаны с работой механизмов (переключением зубчатых колес и кулачковых муфт на ходу, использований упоров и т.д.), с погрешностями изготовления и увеличенными зазорами в сопряжениях. Очень опасны удары при авариях. Основная характеристика сопротивления удару – ударная вязкость.
2.3.Основные критерии работоспособности
ирасчета деталей машин
Детали машин должны удовлетворять условию надежности, т.е. способности, сохраняя свои эксплуатационные показатели, выполнять заданные функции в течение заданного срока службы, и условию экономичности, т.е. иметь минимальную необходимую стоимость изготовления и эксплуатации.
Работоспособность и надежность деталей машин характеризуется определенными критериями. По одному или нескольким критериям ведут расчет, цель которого – определение размеров и материалов деталей машин. Часть критериев удовлетворяет заведомо и не требует проверки.
Важнейшие критерии: прочность, жесткость, износостойкость, теплостойкость, виброустойчивость.
Расчеты на прочность ведут по номинальным допускаемым напряжениям, по коэф. запаса прочности(запасам прочности) или по вероятности безотказной работы. Расчеты по номинальным напряжениям наиболее просты и удобны в качестве предварительных и для обобщения опыта конструирования путем накопления данных о напряжениях в хорошо зарекомендовавших себя конструкциях, работающих в сходных условиях. Наиболее полезны такие данные для машин массового выпуска (автомобилей) опыт эксплуатации которых велик.
12
Расчеты по коэф. безопасности учитывают в явной форме отдельные факторы, влияющие на прочность: концентрацию напряжений, размеры, упрочнения, - а потому более точны.
Наиболее прогрессивным является расчет по вероятности безотказной работы, как по истинному и физически ясному критерию.
Жесткость, т.е. способность деталей сопротивляться изменению формы под действием сил, является наряду с прочностью, одним из важнейших критериев работоспособности машины. Во многих деталях машин напряжения намного ниже предельных, например, в станинах металлорежущих станков они составляют всего несколько МПа, и размеры таких деталей диктуются именно условиями жесткости.
Требования к жесткости деталей машин определяются:
1)условиями прочности детали – при недостаточном равновесии, а также при ударных нагрузках;
2)условиями работоспособности детали совместно с сопряженными деталями: например, жесткость валов определяет удовлетворительную работу подшипников, а также зубчатых, червячных и др. передач.;
3)условиями динамической устойчивости(отсутствием резонансных колебаний или недопустимых автоколебаний);
4)технологическими условиями (невозможностью высокотехнологичной обработки);
5)условиями удовлетворительной работы машин в целом (для машинорудий они сводятся к выпуску точных изделий).
Потеря деталями устойчивости характеризуется тем, что они, находясь под нагрузкой, после дополнительного деформирования на малую величину
впределах упругости не возвращаются в начальное состояние. Устойчивость является критерием, определяющем размеры: а) длинных и тонких деталей, работающих на сжатие;
б) тонких пластин, подвергнутых сжатию в плоскости пластины; в) оболочек, подверженных внешнему давлению; г) полых тонкостенных валов.
На продольный изгиб рассчитываются винты домкратов, штоки
цилиндров, пружины, работающие на сжатие.
Изнашивание – процесс разрушения и отделения материала с поверхности твердого тела и накопление его остаточной деформации или трения. Износ проявляется в постепенном изменении размеров и формы.
Износ – результат изнашивания. Износ вызывает резкое удорожание эксплуатации машин.
Износ ограничивает долговечность деталей по следующим критериям работоспособности машин:
а) по потере точности – приборы, измерительные инструменты, станки; б) по снижению КПД, увеличению утечек – цилиндр и поршень в
двигателях, насосах и т.д.;
13
в) по снижению прочности вследствие уменьшения сечений, неравномерного износа опор, увеличения динамических нагрузок – зубья зубчатых и червячных колес;
г) по возрастанию шума – передачи транспортных и других быстроходных машин;
д) по полному истиранию, которое делает деталь непригодной, - рабочие органы машин, тормозные колодки.
1.Механические - из которых основным является абразивное изнашивание.
2.Молекулярно-механическое изнашивание (изнашивание при схватывании). Схватывание происходит вследствие молекулярных сил при трении.
3.Коррозионно-механическое, при котором механическое изнашивание сопровождается химическим или электрическим взаимодействием материала со средой.
Теплостойкость. В результате нагрева могут возникать следующие вредные для работы машин явления:
1.Понижение несущей способности поверхности деталей из сталей при температурах выше 300…4000С и деталей из пластмасс при температурах выше 100…1500С. Это связано с понижением основных механических характеристик материалов.
Ползучесть, малая пластическая деформация при постоянной нагрузке, основной критерий работоспособности для отдельных деталей машин: лопаток и дисков турбин, элементов паровых котлов высокого давления.
2.Понижение защитной способности масляного слоя, разделяющего трущиеся детали машин, и, как следствие из этого, появление повышенного износа или заедание.
3.Изменение зазоров в подвижных соединениях вследствие обратимых температурных деформаций.
4.Изменение свойств, трущихся поверхностей, например снижение коэф. трения в тормозах.
5.Понижение точности машины вследствие обратимых температурных деформаций.
Виброустойчивость – способность конструкции работать в нужном диапазоне режимов без недопустимых колебаний. С повышением скоростей расчет на виброустойчивость становится актуальным.
В машинах основное распространение имеют:
1.Вынужденные колебания, вызываемые внешними периодическими силами (неуравновешенностью вращающихся деталей, погрешностями изготовления, переменными силами в поршневых машинах и т.д.).
2.Автоколебания или самовозбуждающиеся колебания, т.е. колебания
вкоторых возмущающие силы вызываются самими колебаниями, например фрикционные автоколебания, вызываемые падением силы трения с ростом скорости и др. факторами.
14
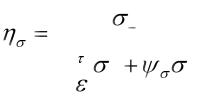
Шум в первую очередь связан с погрешностями изготовления деталей
– ошибками шага и профиля зубьев, волнистостью дорожек качения подшипников.
Надежность – свойство объекта выполнять в течение заданного времени или заданной наработки свои функции, сохраняя в заданных пределах эксплуатационные показатели.
Безотказность – свойство сохранять работоспособное состояние в течение заданной наработки без вынужденных перерывов.
Долговечность – свойство изделия сохранять работоспособное состояние до предельного состояния с необходимыми перерывами для технического обслуживания и ремонта.
Ремонтопригодность – приспособленность изделия к предупреждению, обнаружению и устранению отказов и неисправностей путем проведения технического обслуживания и ремонтов.
Сохраняемость – свойство изделия сохранять безотказность, долговечность и ремонтопригодность после и в течение установленного срока хранения и транспортирования.
Отказы бывают полные и частичные.
2.4. Выбор запаса прочности и допускаемых напряжений при статических и переменных нагрузках
Расчеты на прочность при постоянных пластичных материалов производят согласно пластических деформаций, т.е. обеспечивают
напряжениях деталей из из условию отсутствия общих требуемый коэф. запаса по
отношению к пределу текучести материала (σТ, σS).
Расчет на прочность при постоянных напряжениях, равномерном напряженном состоянии и хрупком состоянии материала производят по
заданному коэф. запаса относительно временного сопротивления (σв). Расчет на прочность деталей машин при регулярных переменных
напряжениях обеспечивает требуемый запас прочности по отношению к пределу выносливости.
При одноосном растяжении-сжатии или изгибе запас прочности определяется по формуле:
|
|
|
1 |
|
|
K |
|
(2.1) |
|
|
B |
a |
m |
|
|
|
|
|
15
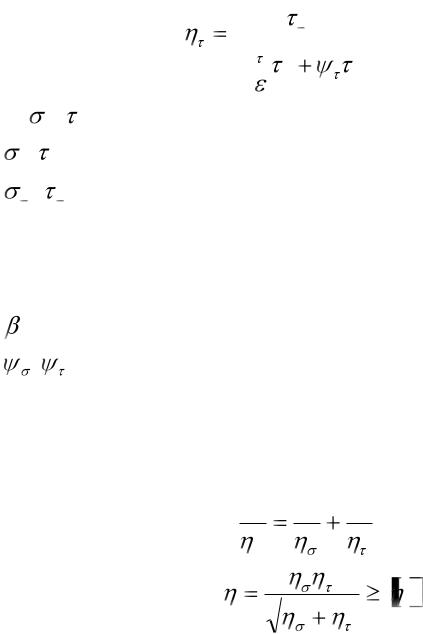
при кручении:
|
|
|
|
|
|
1 |
|
|
|
|
|
K |
|
(2.2) |
|
|
|
|
|
B |
a |
m |
|
|
|
|
|
|
|
|
|
где |
m , |
m - среднее напряжение циклов при изгибе и кручении |
|||||
a , |
a |
- амплитуда напряжений |
|
|
|
||
1, |
1 - пределы выносливости |
материала при знакопеременном |
симметрическом цикле;
K, K
- общий коэф. снижения пределов выносливости деталей при изгибе
и кручении, учитывающий концентрацию напряжений, размер деталей и упрочнения.
- коэф. упрочнения, вводимый для валов с поверхностным упрочнением;
, |
- коэф., характеризующие чувствительность материала к |
асимметрии цикла.
Е - масштаб фактор, учитывающий влияние размеров сечения вала (принимаемый по табл.).
Общий коэф. запаса прочности при совместном действии растяжениясжатия и кручения:
1 1 1
2 |
2 |
2 , |
откуда |
2 |
2 |
(2.3) |
Коэф. запаса прежде всего зависит от материала, по отношению к которому выбирается запас прочности.
Коэф. запаса при постоянных напряжениях для пластических материалов выбирается минимальным, т.е. равным 1,3…1,5, т.к. пластические деформации малы при кратковременных перегрузках, что не вызывает выхода детали из строя.
Коэф. запаса по пределу выносливости выбирается порядка 1,5…2,5. Это связано с тем, что единичные перегрузки не приводят к разрушению. При контактных нагружениях, коэф. запаса можно выбирать равным 1,1…1,3, т.к. возможные повреждения имеют местный характер.
Одним из наиболее общих условиях конструирования машин является условие равнопрочности. Конструирование машины с измененными
16
запасами несущей способности, которые все равно не могут быть реализованы в связи с выходом конструкции из строя из-за разрушения или повреждения других элементов.
2.5. Перспективы методов расчета при конструировании деталей машин
Конструирование – это творческий процесс создания машин в документах (главным образом в чертежах) на основе теоретических расчетов, конструкторского, технологического и эксплуатационного опыта и экспериментов.
На основных этапах конструирования машин разрабатывают следующую технологическую документацию:
1.Техническое задание на проект или техническое предложение. Эти документы содержат паспортные параметры машины и решение общих принципиальных вопросов схемы машины.
2.Эскизный проект, включающий в себя эскизную проработку общих видов основных узлов.
3.Технический проект, содержащий отработанные общие виды машины и ее узлов, готовых к деталировке.
4.Рабочий проект, представляющий собой комплекс общих видов, рабочих чертежей деталей, спецификаций и др. документов, достаточных для изготовления машины.
Техническая эстетика необходима при конструировании.
Для предварительного определения размеров деталей применяют упрощенные условные расчеты по номинальным напряжениям, позволяющие в удобной форме обобщать опыт конструктора.
При окончательных расчетах используют критерии работоспособности
инадежности.
Применение ЭВМ переводит расчеты деталей машин на новый уровень, обеспечивая возможность оптимизации расчетной конструкции, многократного уменьшения трудоемкости выполнения расчетов, которые раньше были невозможны. На ЭВМ проводят расчеты деталей машин общемашиностроительного применения по единым программам, сложные расчеты, составление расчетных таблиц и т.д.
Система автоматизации проектирования (САПР) предусматривает оптимизацию конструкций и выдачу результатов на графопостроитель или дисплей.
Цели САПР – в повышении качества продукции, уменьшение трудоемкости и сокращении сроков проектирования в связи с повышением сложности объектов.
Оптимальные параметры машины выбираются по многочисленным экономическим и социальным критериям, часто противоречивым: наименьшая масса, габариты и стоимость, набольшее КПД и надежность.
17
Инженерная оптимизация конкретного изделия начинается с
постановки задачи, которая включает:
-определение критериев, характеризующих качество изделия;
-выявление независимых переменных параметров, влияющих на критерии качества;
-разработку математической модели, отражающей взаимосвязь между параметрами и критериями качества.
2.6. Пути снижения металлоемкости при конструировании деталей машин
1.Выбор оптимальной схемы машины или узла.
2.Уточнение расчетов и снижение коэф. безопасности.
3.Выбор оптимальных типов деталей и конструктивных исполнений (переход от клепанных к сварным экономит 15-20% материала).
4.Выбор оптимальных параметров деталей и агрегатов(расчетных скоростей, основных конструктивных соотношений, повышая частоту вращения вала, при той же мощности, можно уменьшить массу вала).
6.Снижение массы заготовок, приближение форм деталей к формам наиболее простых и дешевых заготовок в виде труб, профильного проката, чисто тянутого материала и т.д.
2.7. Роль машин в производительности труда
Во всех отраслях народного хозяйства производственные процессы осуществляются машинами или аппаратами с машинными средствами механизации. Поэтому уровень народного хозяйства в большей степени определяется уровнем машиностроения.
Современные машины многократно повышают производительность физического и умственного труда человека.
В настоящее время достигнутая мощность энергетических машин – турбин и электрических генераторов – превзошло миллионный рубеж.
Современные мощные вычислительные машины делают миллионы и сотни миллионов операций в секунду.
Машины настолько прочно вошли в жизнь нашего общества, что трудно найти такой предмет или продукт потребления, который был бы изготовлен и доставлен к месту потребления без помощи машин.
Важнейшим достижением и показателем уровня машиностроения и приборостроения является автоматизация, в частности комплексная автоматизация производственных процессов в народном хозяйстве, охватывающая автоматизацию крупного производства штучных изделий и в настоящее время распространяемую на принципиально более сложную автоматизацию производства. Расширяется применение материало-, трудо- и
18
энергосберегающей технологии, станков с программным управлением и многоцелевых, гибких производственных систем. Во все области машиностроения бурно внедряется микропроцессорная техника.
Машиностроение является приоритетной областью народного хозяйства.
2.8. Основные методы упрочнения поверхностей деталей машин
Механические характеристики не упрочненных металлических материалов далеки от требований современного машиностроения.
Большинство деталей машин подвержено изгибу и кручению, при которых напряжения растут по направлению к поверхности, на поверхности концентрируются напряжения, вызванные формой и шероховатостью поверхности, контактные напряжения, происходит изнашивание и зарождение трещин.
Поэтому широко применяется поверхностное упрочнение. Упрочняется поверхностный слой, создаются в нем остаточные сжимающие напряжения, которые вычитаются из опасных растягивающих напряжений от внешней нагрузки. Поверхностные упрочнения цементацией и закалкой повышают по сравнению с объемной закалкой до такой же твердости, сопротивление усталости на 30…40% и больше.
Применяются поверхностные упрочнения следующих видов:
1)механические – обкатка роликами, обдувка дробью и т.д.
2)термические – закалка с нагревом токами высокой частоты и кислородно-ацетиленовым пламенем;
3)химико-термические – цементация и нитро цементация с закалкой, азотированием.
4)термомеханические;
5)концентрированными потоками энергии.
Механические упрочнения характеризуются малой трудоемкостью, возможностью обработки в механическом цеху, отсутствии окалины.
Повышение усталостного сопротивления на гладких участках на 20…40%, для деталей типичных для машиностроения форм – на 80…100%, при особо редкой концентрации напряжений – до трех раз.
Обкатка роликами удобна для тел вращения и осуществляется на токарных станках (валы для железнодорожного транспорта).
Дробеструйный наклеп осуществляется на дробометных машинах роторного или пневматического типа, позволяет упрочнять детали сложной формы. В связи с необходимостью спец. оборудования имеет применение в массовом и серийном производствах.
Применяются механические упрочнения: чеканкой, ротационно-
ударное шариками, гидробеструйное, ультразвуковое через сферический инструмент или шарик, взрывом бризантных веществ.
19
Упрочнение лазерными, электронными или ионными лучами и струей плазмы обеспечивает высокую интенсивность процесса, геометрическую точность зоны нагрева, а следовательно минимальное коробление деталей.
Очень эффективен способ для низкоуглеродистых сталей, вызывает перекристаллизацию и эффект, аналогичный термомеханической обработке. Ионная имплантация – это внедрение ионов химических элементов бомбардировкой поверхности пучками соответствующих ускоренных в вакууме ионов. Она обеспечивает повышение микротвердости и выносливости в несколько раз.
Покрытия – это слои из требуемого материала, наносимые на покрываемую поверхность наплавкой или напылением(металлизацией). Покрытия применяют для повышения износостойкости и жаростойкости. Наплавляемые материалы – твердые сплавы, антифрикционные материалы.
Наносят на ремонтируемые и новые детали.
2.9. Основные пути повышения КПД машины
КПД машины складываются из КПД отдельных частей машины: вращающихся валов, механических и зубчатых передач, ременных передач и др.
Потери мощности в зубчатых передачах в основном складываются из потерь:
а) на трение в зацеплении; б) на разбрызгивание масла; в) в подшипниках.
В особо быстроходных передачах могут быть значительные вентиляционные потери.
Потери в зацеплении вызываются силами трения между зубьями. Силы трения в режиме полужидкостной смазки растут с увеличением шероховатости поверхности, с уменьшением вязкости масла и с уменьшением скорости.
КПД ременных передач, фрикционных передач будут рассмотрены при изучении соответствующих разделов.
20