
3238
.pdfметалла. Были разработаны секционные щетки и щетки, в которых между секциями размещались ударные элементы в виде шайб, болтов, жгутов проволоки и т.д. При использовании таких инструментов на зачистных операциях формируется в основном обрабатываемый поверхностный слой. Недостатками механических щеток и иглофрез являются: недостаточная производительность, высокий износ инструментов, отсутствие стабильности получаемых технологических показателей, экологически неблагоприятные условия труда. Все это ограничило область применения механических щеток операциями безразмерной зачистки заготовок.
Использование механических щеток представляет интерес, однако им свойственны следующие недостатки:
1.Высокий износ и за счет этого высокая стоимость
2.Низкая производительность
3.Отсутствие разработанных технологий и инструментов с возможностью использования на черновых и чистовых операциях одновременно;
4.Невозможность их использования для размерной обработки. Анализ литературных данных и исследования, проведенные в
ВГТУ [1, 2, 3, 4] показывают, что на современном этапе развития техники возможно существенно уменьшить износ непрофилированного инструмента-щетки, значительно повысить производительность и улучшить качественные показатели обработки за счет наложения электрического поля на механическую обработку вращающейся металлической щеткой, то есть за счет комбинации электрической, механической энергии и анодного растворения обрабатываемого изделия в одном комбинированном процессе обработки непрофилированным электродом-щеткой.
Одним из способов обработки непрофилированным инструментом является получающая все большее распространение обработка непрофилированным электродом-щеткой с рабочей частью из консольно закрепленной проволоки. При таком способе обработки заготовка подвергается комбинированному воздействию эрозионной, химической и механической составляющих процесса. Их взаимное наложение позволяет осуществлять производительную обработку изделий из высокопрочных и твердых материалов при высоком качестве и точности обработки. Конструкция электрода-щетки проста,
80
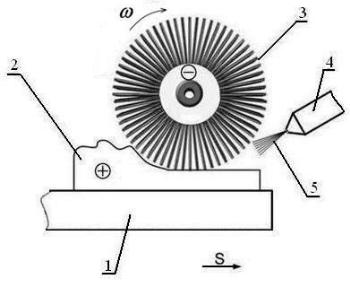
универсальна, недорога, а так же легко изготавливается. Она может использоваться для черновой обработки, к примеру, снятия заусенцев, удаления облоя и грата после литья, скругления острых кромок, зачистки наплавленных поверхностей. А так же для чистовой – подготовки изделийпод покрытия, удаления припуска, нанесения покрытий, отделочной и декоративной обработки. Так шероховатость поверхности сварных швов, обработанных электродом-щеткой составила до Ra 0,1 мкм. В зависимости от предъявленных к обрабатываемому изделию требований и его формы обработка может осуществляться дисковыми, чашечными, комбинированными щетками или щетками-кисточками как на специально спроектированных, так и на модернизированных универсальных металлорежущих станках, которые оснащаются источниками питания. На рис.12 представлена схема обработки непрофилированным электродом-щеткой [1].
Рис. 12. Схема обработки непрофилированным электродом-щеткой
На стол плоскошлифовального станка 1, модернизированного для комбинированной обработки электродом-щеткой, устанавливается заготовка 2. Электрод-щетка 3 вращается со скоростью ω. Заго-
81
товка с заданной подачей S перемещается к электроду-щетке. Обработка происходит в среде рабочей жидкости 5, подаваемой через сопло 4 в зону обработки. Использование непрофилированного элек- трода-щетки позволяет механизировать слесарно-зачистные операции, при этом устраняется неквалифицированный труд слесарей, работа которых связана с тяжелыми условиями труда (вибрации, шумы), значительно повышается производительность процесса обработки и качество обрабатываемых изделий. Недостатками комбинированного способа обработки непрофилированным электродомщеткой являются неполная изученность данного процесса обработки, вследствие чего наблюдается нестабильность выходных показателей, достигаемых при высоких окружных скоростях электрода-щетки, отсутствие методики расчета и моделирования универсального инструмента, невозможность обеспечить в едином технологическом процессе показателей чистового формообразования.
При обработке изделий электродом-щеткой можно скруглять острые кромки, удалять припуск, повышать пластичность и коррозионную стойкость изделий, улучшать качество поверхности для последующих покрытий.
Электрод-щетка универсальна, проста в изготовлении, применение ее экологически безопасно. Рассмотренный в работах способ обработки непрофилированным электродом-щеткой совмещает в себе тепловое, механическое воздействие металлических проволок на обрабатываемую поверхность и анодное растворение металла заготовки, что позволяет производить обработку с высокой производительностью.
Обработку электродом-щеткой, по воздействию на изделие, можно условно разделить на пять этапов [1] (рис.13).
На первом этапе, при приближении проволоки к заготовке и достижении зазора Sа, съем металла происходит под действием электрохимической обработки. На втором этапе, при уменьшении зазора до Su, на заготовку начинает воздействовать и электроэрозионная обработка, расплавляя металл импульсами тока. На входе и выходе рабочей части электрода-щетки в зону обработки условия схожи, поэтому процессы на первом и пятом, втором и четвертом этапах будут происходить одни и те же. На третьем этапе обработки проволока пучков касается обрабатываемой поверхности с заданной величи-
82
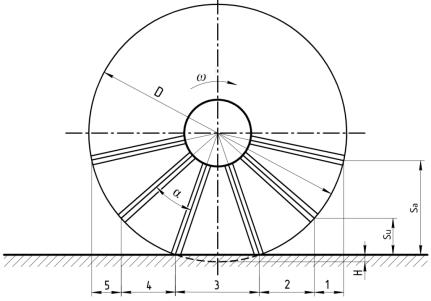
ной по длине проволоки. В результате начинается процесс электроконтактной обработки.
Рис. 13. Схема обработки электродом-щеткой
В процессе обработки проволока пучков электрода-щетки оказывает механическое воздействие на обрабатываемую поверхность, сглаживая неровности и удаляя продукты эрозионного и электроконтактного процессов, окислые пленки из зоны обработки. В наиболее общем случае обработки электродом-щеткой на величину съема металла и качество формируемого поверхностного слоя оказывают влияние основные процессы: электрохимический, тепловой и механический.
Производительность комбинированного удаления припуска щетками с наложением электрического поля значительно превосходит производительность обработки механическими щетками. При этом достигается высокое качество обработанной поверхности, шероховатость составляет до Ra 0,1 мкм. Установлено, что скорость продольной подачи непрофилированного инструмента-щетки из
83
бронзовой проволоки БрОФ 6,5-1 с диаметром 0,2 мм достигает 75200 мм/мин при глубине обработки до 3 мм и шероховатости до
Ra1,25-2,5 мкм.
Обработка непрофилированным электродом-щеткой происходит в жидкой рабочей среде, которая подбирается с учетом особенностей комбинированного процесса обработки. Однако, при обработке электродом-щеткой имеются требования, которые трудно совместить: для анодного растворения припуска применяется токопроводящая рабочая среда [4], для электроэрозионного съема материала необходима диэлектрическая жидкость [4]. При комбинированной обработке необходимо чтобы рабочая среда обладала свойствами электролита. При этом учитывается, что увеличение проводимости рабочей жидкости повышает производительность процесса обработки. Но в этом случае снижается точность. Для получения высокой геометрической точности обрабатываемой поверхности используются рабочие жидкости ограниченной проводимости или диэлектрики. Для этой цели используют: водные растворы нейтральных солей Na2CO3 и NaNO3 c добавками диэлектрика, например, масла индустриального «И-20».
При выборе материала для изготовления непрофилированного электрода-щетки необходимо учитывать следующее:
1. Электрод-щетка должна быть изготовлена из электропроводящего материала с малым удельным сопротивлением.
2.Поверхность рабочих элементов электрода-щетки должна быть коррозионно-стойкой к воздействию рабочих жидкостей.
3.При выборе проволоки учитывается ее способность выдерживать значительные упругие деформации без разрушения.
4.Материал должен быть недефицитен, хорошо обрабатываться.
5.Рабочие элементы электрода-щетки не должны иметь большого износа.
Сучетом предъявляемых требований для изготовления непрофилированного электрода-щетки применяются следующие материалы: 12Х18Н10Т, Медь М1, Латунь Л80, Бронза БрКМц3-1,Ст. 65Г и другие.
Конструкции проволочных электродов-щеток, применяемые при обработке, разнообразны. Их выбор зависит от геометрической формы обрабатываемого изделия, назначения технологической опе-
84
рации, выходных показателей. Применяемые при обработке типы электродов-щеток и их назначение представлены в таблице.
Типы и назначение электродов-щеток |
|
Тип |
Область использования |
Дисковая |
Для черновой и чистовой обработки загото- |
|
вок, снятия заусенцев, скругления острых |
|
кромок, зачистки сварных, паяных соедине- |
|
ний, электроэрозионного нанесения покры- |
|
тий, правки абразивного инструмента |
Торцовая, |
Для удаления заусенцев, зачистки и полиров- |
Чашечная |
ки пазов, торцов, углублений, полировки ка- |
|
налов прямоугольного и сферического сече- |
|
ний |
Цилиндрическая |
Для зачистки крупногабаритных деталей, из- |
|
делий металлургического передела: слябов, |
|
блюмов |
Кисточка |
Для обработки внутренних отверстий малого |
|
диаметра, пресекающихся каналов корпусов, |
|
деталей гидропневмоавтоматики |
Комбинированная |
Для одновременной обработки трех и более |
|
поверхностей: снятия заусенцев, зачистки и |
|
полировки |
Секционная |
Для черновой и чистовой обработки, доводки |
|
и полировки деталей из цветных сплавов и |
|
других материалов |
Заключение В результате проведенных исследований [1] была определена
область применения комбинированной обработки непрофилированным электродом-щеткой, уточнены технические возможности исследуемого метода. Электроды-щетки имеют разнообразную форму, универсальны, недороги в изготовлении. Область использования электродов-щеток очень широка: они могут применяться при обработки мест переходов, скругления острых кромок, снятия заусенцев, наплывов металла, удаления грата для черновой и чистовой обработки изделий со сложной формой из токопроводящих материалов. В
85
результате мы получаем возможность проведения высокопроизводительной обработки изделий, в том числе со сложной геометрической формой, исключить ручной, малопроизводительный труд слесарей, получить изделия с заданными технологическими характеристиками и качеством. Вследствие чего можно сделать вывод, что обработка электродом-щеткой является перспективным методом и необходимы его дальнейшие исследования.
Литература
1.Кириллов О.Н. Технология комбинированной обработки непрофилированным электродом: монография / О.Н. Кириллов. Воронеж: ГОУВПО «Воронежский государственный технический универ-
ситет», 2010. 254 с.
2.Перепичка Е.В. Очистно – упрочняющая обработка изделий щетками. М.: Машиностроение, 1989. 136 с.
3.Серебренник Ю.Б. Обработка деталей вращающимися металлическими щетками. Пермь: ЦБТИ Пермского совнархоза, 1960. 59 с.
4.Справочник по электрохимическим и электрофизическим методам обработки / Под общ. ред. Волосатова В.А. Л.: Машино-
строение, 1988. 719 с.
Воронежский государственный технический университет
УДК 621.9(075.8)
А.В. Перова, А.А. Санков
АНАЛИЗ И ОЦЕНКА СЕБЕСТОИМОСТИ МЕХАНИЧЕСКОЙ ОБРАБОТКИ МАТЕРИАЛОВ ОТ СТОЙКОСТИ ИНСТРУМЕНТА
Ключевые слова: режимы обработки, стойкость инструмента, оптимизация
Рассматриваются основные критерии стойкости инструмента, влияющие на себестоимость обработки деталей
Основная цель применения методов оптимизации при
86
использовании методов механической обработки - это установление численных значений элементов режимов обработки, которые позволили бы наиболее производительно, с наименьшими затратами осуществлять обработку детали. На производстве в подавляющем большинстве случаев решается две из трех традиционных задач, возникающих в реальных производственных условиях:
1)Определить режимы, которые обеспечивают себестоимость обработки, при этом на производительность процесса не наложены ограничения;
2)Найти режимы, которые обесп6ечивают максимальную производительность, а себестоимость производства детали выбрана без ограничений;
3)Найти режимы обработки, при которых себестоимость процесса минимальна, а производительность задана заранее.
Первую задачу можно решить, если в качестве критерия оптимизации выбрана переменная составляющая себестоимость обработки детали на операции:
C t0 (Cp |
Cст ) |
t |
см (Cp Cст ) |
|
C |
и |
, |
(1) |
|
Q |
|
|
|||||
|
|
|
|
Q |
|
где tо - машинное (основное) время на операцию, мин; Cр - минутная заработная плата рабочего, руб.;
Cст - затраты на эксплуатацию станка в течение 1 мин, руб.; Cр + Cст = E = 4,4 руб - стоимость станкоминуты;
tсм - время на смену затупившегося инструмента и его наладку за период стойкости, мин;
Q - количество обработанных деталей за период стойкости, шт; Cи - стоимость эксплуатации инструмента за период стойкости,
руб.
При осаждении покрытия методом ГКО использованы следующие технические обозначения: n - частота вращения шпинделя, об/мин; S – продольное перемещение инструмента вдоль оси детали за один оборот шпинделя установки, мм/об; t – глубина резания; h – толщина срезаемого слоя, мм; L - длина участка, подлежащего обработке.
Основное время обработки tо, мин можно выразить через период стойкости. Для токарной обработки:
87

t |
|
|
Lh |
, |
(2) |
|
0 |
|
nSt |
|
где частота вращения шпинделя станка n, об/мин может быть определена как
n |
1000V |
(3) |
|
D |
|||
|
|
где V - скорость перемещения инструмента относительно поверхности детали, м/мин;
D - диаметр обрабатываемой детали, мм.
Скорость резания V м/мин является функцией стойкости инструмента. Для метода токарной обработки ее можно записать в виде:
V |
CvK |
, |
(4) |
|
TmtxSy |
||||
|
|
|
где Cv, m, x, y - коэффициент и показатели степени, зависящие от типа наносимого покрытия и вида применяемого инструмента.
K - коэффициент, зависящий от многих факторов t - глубина резания, мм;
S - продольное перемещение инструмента вдоль оси детали за один оборот шпинделя установки, мм/об;
T - стойкость инструмента, мин.
Таким образом, выражение (2) можно представить в виде:
t |
|
|
L h D |
|
L h D |
|
|
|
|
0 |
|
|
Cv K |
|
|
||||
|
|
S t 1000 V |
S t 1000 ( |
) |
|
|
|||
|
|
|
|
|
Tm tx S y |
|
(5) |
||
|
|
|
|
|
|
, |
L h D tx S y T m A Tm
1000 S t Cv K
где А - коэффициент, равный
L h D tx Sy
1000 S t Cv K
Количество обработанных деталей Q, шт. за период стойкости так же можно выразить через стойкость инструмента Т:
Q |
T |
|
T |
|
1 |
(6) |
|
ATm |
ATm 1 |
||||
|
t0 |
|
|
88

Используя выражение (5) и (6) выражение (1) можно представить в виде:
C ATm E |
tсм |
|
E |
|
Cи |
ATm E t |
см EATm 1 Cи ATm 1 |
||
|
|
|
|
||||||
|
1 |
|
|
|
1 |
|
|
|
|
|
|
ATm 1 |
|
|
|
ATm 1 |
|
ATm T m 1 (tсм E Cи )A
Для определения стойкости инструмента, при которой наблюдается наименьшая себестоимость обработки необходимо решить уравнение:
C mAETm 1 (m 1)A(tсмE Cи )Tm 2 0 |
(7) |
Для определения стойкости инструмента, обеспечивающего минимальную себестоимость обработки необходимо определить исходные параметры для расчета:
Tсм = 10 мин;
Cи = 50 р. ;
L = 105 мм, по чертежу детали;
h = 0,4 мм по техническим условиям обработки;
s= 5 мм/об по техническим условиям обработки;
t= 0,002 мм;
m = 0,6;
E = 6,5 /по данным ООО «Миком»/;
Подставляя цифровые данные в формулу, определяем коэффициент А
A 105 0.4 3.14 60 0.0020.2 5.00.35 1.14 1000 5.0 0.002 340 1
Себестоимость обработки в зависимости от стойкости инструмента с учетом технологических параметров обработки связана выражением
C 1.14T0.6 131.1T 0.4 (8)
Графически этот материал можно представить в виде двумерного графика, как показано на рисунке.
Для определения стойкости инструмента, при которой наблюдается наименьшая себестоимость обработки необходимо решить уравнение (7), которое, учитывая технологические параметры обработки, принимает вид
89