
3238
.pdf
Рис. 1. Дисковые щетки с рабочей частью из проволоки свитой в жгуты
Проволочные жгуты имеют большую гибкость и длину. Диаметр таких щеток от 75 до 250 мм. Используются они на высоких скоростях с ручным механизированным инструментом: пневматическим и электрическим, имеющим скорости вращения 4200-15000 об/мин., что соответствует окружной скорости 50-60 м/с. Соединение нескольких тонкодисковых щеток в одну позволяет получить щетку с широкой рабочей поверхностью до 60 мм.
По данным хорошо зарекомендовали себя в работе дисковые щетки с резиновыми ступицами (рис.2). В таких щетках часть проволоки, или по всей длине, заполнена вулканизированной резиной, что значительно повышает жесткость проволок. Щетки с резиновыми ступицами характеризуются высокой износостойкостью, хорошо сохраняют приданную им форму на весь период стойкости, безопасны в работе, т.к. исключены случаи излома и вылета проволок рабочей части.
При обработке неметаллов: пластмасс, дерева используются дисковые щетки с естественной или принудительной вентиляцией (рис.3). При непрерывном цикле работы особенно у щеток с неметаллической рабочей частью и шириной 75 мм и более необходимо наличие вентиляции.
70
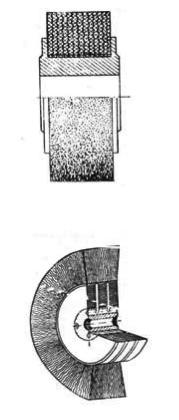
Рис. 2. Дисковая щетка с резиновой ступицей
Рис. 3. Дисковая щетка с вентиляционной системой
Вентиляционные отверстия в ступице способствуют охлаждению щетки и снижают или устраняют перегрев щеток, увеличивая их долговечность.
Дисковые механические щетки широко используются на чистовых и финишных операциях: полирования, глянцевания, удаления небольшой окалины, цвета побежалости, при этом обычно в зону контакта проволок щетки и обрабатываемой поверхности подают полировальные пасты и абразивные составы. На таких операциях используют щетки изготовленные из неметаллических материалов: капрон, щетина, фибра, корд. При обработке изделий сложного гео-
71
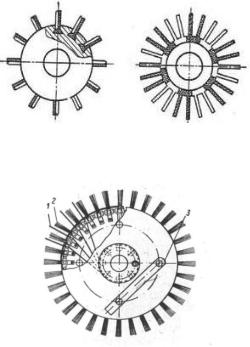
метрического профиля из специальных сталей применяют щетки, шаржируемые алмазной крошкой, размером 4-48 мкм с концентрацией по объему до 15-50% (рис.4) или абразивную дисковую щетку показанную на рис.5. Режущими элементами в щетке такой конструкции являются абразивные ленты - 1.
Рис. 4. Щетки с рабочими элементами из синтетического материала
Рис. 5. Дисковая щетка с рабочей частью из ворса и абразивных лент
Ленты представляют собой полосы шириной 7-10 мм и при работе опираются на упругие секции из ворса 2, которые крепятся по диаметру щетки из расчета одна секция на 1 ленту. В процессе обработки с помощью рычага 3 варьируется длина абразивных лент. Конструкция щетки позволяет проводить быструю смену абразивных лент. Используются такие щетки на чистовых и отделочных операциях при обработке различных деталей. Так, абразивно-полимерные
72
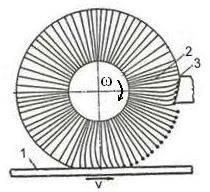
щетки фирмы OSBORN, применяются на операциях скругления острых кромок деталей газотурбинных двигателей. Щетки состоят из нитей стабилизированного нейлона с включениями абразивных зерен карбида кремния.
Механические щетки часто применяются для декоративной отделки цветных металлов и сплавов, шлифования, полирования деталей из пластмасс, дерева, стекла, снятия изоляции с проводов, зачистки изделий армированных резиной, для упрочнения с одновременным нанесением покрытия. Способ нанесения покрытия (рис.6) заключается в том, что подготовленная для обработки поверхность 1 перемещается со скоростью V. Перед ней установлен материал наносимого покрытия 3 в твердом состоянии. Перенос материала на обрабатываемую поверхность осуществляется упругой механической щеткой 2. При вращении щетки, за счет удара и трения скольжения ее проволок, происходит разогрев наносимого металла и обрабатываемой поверхности. Разогретый металл переносится проволоками в виде капель на обрабатываемую поверхность, где за счет высокой температуры, механического воздействия и химических реакций происходит сцепление материала наносимого покрытия и обрабатываемой поверхности. Способ нанесения покрытия механической щеткой позволяет получить упрочненную поверхность сердечника при производстве сталеалюминиевой проволоки. Ее использование позволит сократить обрывы на линиях связи и электропередач в 1,5 раза.
Рис. 6. Нанесение покрытий механической щеткой
73

Для обработки больших поверхностей применяют валковые (цилиндрические) щетки длиной 50-1500 мм и наружным диаметром 50-1000 мм.Валковые (цилиндрические) щетки по плотности набивки подразделяются на щетки с большой, средней, малой плотностью набивки. Они могут изготавливаться из гофрированной или прямой проволоки или неметаллических материалов, с металлическим или деревянным сердечником.Рабочая часть может быть сплошной, а может располагаться по спирали или винтовой линии. Валковые (цилиндрические) щетки работают с большими скоростями, до 50 м/с.
Для обработки деталей на бесцентровых щеточнополировальных станках применяются кольцевые щетки (рис.7). Их изготавливают с большим наружным диаметром 450-500 мм, имея небольшой вылет рабочей части.
Рис. 7. Кольцевые щетки
Такие щетки характеризуются большой жесткостью, что позволяет использовать их для отделочных операций без предварительной обработки заготовок. Область использования кольцевых щеток ограничена необходимостью прямолинейного контакта с заготовкой.
Торцовые или чашечные щетки получили наибольшее распространение после дисковых. Они могут быть изготовлены из проволоки свитой в жгуты, такие щетки обладают большой жесткостью и режущими свойствами. Их используют с большими скоростями Vокр = 30-40 м/с в ручных переносных механизированных инструментах на судостроительных, вагоностроительных и других металлообрабатывающих предприятиях. Торцовые щетки могут изготавливаться из гофрированной или собранной в пучки проволоки или неметалличе-
74
ских материалов. Такие щетки используются для легких отделочных работ и полирования. Наружные диаметры торцовых щеток обычно не превышают 150-180 мм. Для обработки внутренних поверхностей изделий используются концевые щетки, хорошие результаты показывают миниатюрные щетки фирмы OsbornSchmitzLudwig (ФРГ). Концевые щетки, как правило, используются с ручным механизированным инструментом или на сверлильных станках. Обработка такими щетками осуществляется на больших скоростях до 12000 об/мин. Концевыми щетками эффективно удаляют заусенцы, скругляют острые кромки и углы, очищают и полируют поверхности в труднодоступных местах изделий. Изготавливают их чаще всего из гофрированной проволоки. Форма концевых щеток весьма разнообразна и зависит от назначения. Дисковые концевые щетки используют для очистки и отделки боковых поверхностей отверстий, каналов, труб. Их изготавливают диаметром 15-75 мм. Для одновременной обработки боковых стенок и дна в глухих отверстиях и пазах применяют щетки, рабочей частью в которых является торец и боковая поверхность щетки. Концевые щетки с рабочей частью, закрепленной с двух сторон применяют для обработки фасонных полузакрытых отверстий, каналов. Щетки такой конструкции воздействуют на обрабатываемый участок своей боковой поверхностью, режущие свойства таких щеток очень малы. Угловые концевые щетки предназначены для обработки внутренних фасонных поверхностей и углов. Торцовые концевые щетки применяют для обработки глухих отверстий, пазов, труднодоступных участков изделий. Рабочая часть таких щеток располагается прямо или имеет наклон в сторону вращения. Для обработки внутренних резьбовых поверхностей, удаления приставшей стружки, мелких заусенцев, следов инструмента, очистки просверленных отверстий, чистовой обработки мест переходов используют концевые щетки с радиально расположенным ворсом. Наружный диаметр таких щеток обычно не превышает 50 мм. Применяют их на сверлильных станках или с ручным механизированным инструментом. Окружные скорости обычно 10-15 м/с.
Большое внимание применению щеток для зачистки поверхностей уделяет проф. Таказава (Япония). В своих работах он исследует удаление заусенцев с корпусов приборов из стали и цветных металлов.
75
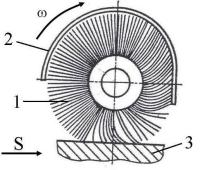
Съем металла с заготовки происходит за счет механического воздействия проволок на деталь. Для того, чтобы повысить энергию удара проволоки и тем самым увеличить производительность процесса, щетки стали делать секционными. При этом авторы придают решающую роль в формировании поверхностного слоя ударному воздействию проволок. Однако, в работе автор отрицает ударное воздействие в обычных щетках, считая, что при контакте с обрабатываемой поверхностью проволоки образуют на границе зоны обработки густую «подушку», амортизирующую удары вновь набегающих проволок. Происходит падение скорости проволоки до минимальных значений еще до контакта с микронеровностями обрабатываемой поверхности и основным фактором механического воздействия щетки на заготовку является сглаживающее скольжение деформированных проволок. Такая схема характерна при обработке щетками с большой плотностью набивки и при большом прижиме к заготовке. Для повышения энергии удара проволок разработаны вращающиеся щетки с отражателями (рис.8).
Рис. 8. Щетка с отражателем
Проволоки 1 в таких щетках за счет упругой деформации при контакте с отражателем 2 приобретают дополнительную энергию для обработки поверхности изделия 3. Недостатком таких щеток является повышенный износ проволок за счет дополнительного трения по отражателю и повышенное усталостное изнашивание.
Под руководством проф. Д.Д. Папшева были разработаны, теоретически и практически исследованы секционные щетки, в которых рабочие элементы 1 расположены секциями по окружности и закре-
76
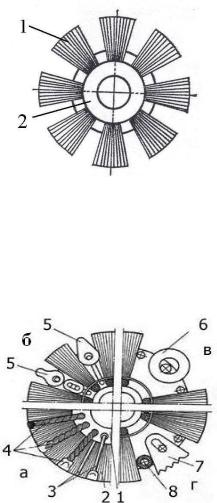
плены на ступице щетки 2. Такая конструкция щетки позволяет увеличить энергию удара проволок на линии атаки (рис. 9).
Рис. 9. Секционная щетка
Количество секций в щетке зависит от режимов обработки: прижима к заготовке, скорости вращения, материала элементов рабочей части.
Представляет интерес применение вращающихся металлических щеток с ударными элементами [2]. Схема металлической щетки с ударными элементами представлена на рис. 10.
Рис. 10. Схема металлической щетки с ударными элементами
Для повышения эффективности обработки между проволочными элементами щетки в чередующемся порядке расположены ударные. В корпусе щетки 1 закреплены проволоки 2 являющиеся
77
зачистными элементами и ударные элементы 3, 4, 5, 6, 7. Ударные элементы в виде переплетенных проволок, прядей троса, пластин, шайб, дисков, устанавливаются секционно по периметру щетки. Ударные элементы могут быть отделены от зачистных пальцами 8. В процессе контакта ударных элементов с обрабатываемой поверхностью, в результате удара происходит разрушение прокатной окалины, ржавчины, которые затем удаляются зачистными элементами – проволоками щетки. При этом поверхностный слой заготовки упрочняется.
Недостатком щеток с ударными элементами является их невысокая производительность, низкое качество поверхности, большой износ проволок и особенно ударных элементов, невозможность обработки поверхностей с наплывами металла после литья, сплошными заусенцами.
Заслуживает внимания устройство для поверхностной отде- лочно-упрочняющей обработки деталей, разработанное и запатентованное Бабичевым А.П. – шарнирно-стержневой упрочнитель (ШСУ). В основе создания многоконтактного виброударного инструмента лежит попытка объединить технологические возможности вибрационной обработки (гибкость среды) и высокую интенсивность воздействия свойственную таким методам обработки как чеканка. ШСУ можно осуществлять упрочняющую обработку ограниченных, локальных участков поверхностей изделий сложной геометрической формы.
В машиностроении нашли применение металлические щетки с большой жесткостью – иглофрезы (рис.11). Иглофрезы отличаются от обычных металлических щеток большой плотностью рабочей части, заполнение проволоками объема рабочей зоны находится в диапазоне 50-85 % от общего объема. Проволоки иглофрез при работе представляют собой полужесткие микрорезцы.
Усилие прижатия иглофрезы к обрабатываемой поверхности составляет в зависимости от вида работ 60-250 кг при окружных скоростях 2-5 м/с. Иглофрезы по сравнению с металлическими щетками имеют большую долговечность и производительность. Применяются они на тех же работах, что и механические щетки, но в отличие от них, могут использоваться не только на операциях зачистки, но и при резании материалов.
78
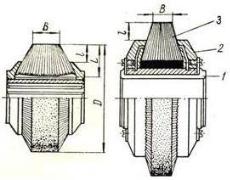
аб
Рис. 11. Иглофрезы: а) без корпуса, б) с корпусом
При удалении твердой горячекатаной окалины сталей обеспечивается шероховатость обработанной поверхности от 1 до 8 класса. По конструкции иглофрезы бывают бескорпусные рис 11а и с корпусом рис. 11б. Корпусная иглофреза имеет втулку корпуса 1, в которую вставляется обойма с проволокой 3, удерживаемая рифлеными торцами фланцев 2. При износе проволок обойма легко заменяется. Ширина иглофрезы В составляет несколько сантиметров, проволоки рабочей части выступают на небольшую величину l , чтобы сохранить жесткость иглофрезы. Применение иглофрез позволяет несколько повысить производительность зачистки ржавчины, окалины, удаления заусенцев по сравнению с механическими щетками, однако она остается недостаточно высокой, иглофрезы сильно изнашиваются, особенно на операциях резания, качество обработанной поверхности невысокое. При обработке механическими щетками съем металла с заготовки происходит за счет механического: ударного и сглаживающего воздействия проволок на заготовку. Управление процессом обработки механическими щетками сводилось к увеличению жесткости пучков за счет изменения диаметра и физикомеханических свойств материала проволок. Увеличение жесткости и твердости проволок в пучках щетки привело к созданию жестких металлических щеток-иглофрез с режущими рабочими элементами в виде закаленных острых кромок, которые могут обеспечить при определенных условиях съем значительных, до 4 мм за проход, слоев
79