
3238
.pdfоблегчает вырывание частиц металла, способствуя тем самым интенсивному изнашиванию.
Следствием воздействия высокой температуры и давления, достигающего в очаге деформации 600 МПа, является тепловой износ поверхности валка, обусловленный адгезионным взаимодействием пластически деформированных микрообъемов пары трения. Локальные участки схватывания разрушаются на выходе из пятна контакта, результатом чего может являться вырывание частиц поверхности валка или налипание прокатываемого металла. Сочетание теплового износа с абразивным может способствовать возникновению на рабочей поверхности валка насечки, состоящей из впадин и выступов, которая представляет собой результат адгезии с последующим массопереносом на выходе из контакта «инструмент - металл» и абразивного изнашивания отслоившимися продуктами окисления [3].
Таким образом, весь комплекс явлений, приводящих к изменению геометрии рабочего слоя валков в процессе эксплуатации, можно свести по основным признакам к двум типам взаимодействия: механическому и физико-химическому.
Первый включает в себя абразивное истирание и образование трещин, второй - адгезионное взаимодействие и окисление.
Как правило, различные виды изнашивания взаимосвязаны и сопутствуют друг другу. Образование участков схватывания под действием адгезионных сил, например, усиливает пластическое течение и вынос частиц поверхности материала валка, окислительные процессы активируют возникновение и развитие трещин термической усталости.
Для прокатки труб на пильгерных станах применяются только валки с наплавленной рабочей частью калибра. Наплавке подвергаются валки как новые, так и ранее наплавлявшиеся, с износом рабочей поверхности в результате эксплуатации.
По существующей технологии валки, наплавляемые первый раз, предварительно обтачиваются по рабочему профилю на вальцетокарном станке на глубину 5-7 мм.
Перед повторной наплавкой валки также обрабатываются на вальцетокарном станке на глубину удаления грубых дефектов: трещин, вмятин, раковин.
120
Допускается наличие на поверхности валка мелких трещин разгара, шириной не более 1 мм и длиной до 20 мм.
Обязательно удаляются ржавчина, окисленный слой, масло, которые могут быть причиной образования пор в наплавленном слое (ржавчина и окисленный слой удаляются наждаком, газопламенной горелкой).
Для предотвращения преждевременного разрушения валков изза сквозных трещин, после 4-х наплавок наплавляемая поверхность валка обтачивается на вальцетокарном станке до полного снятия всего наплавленного слоя и частично основного металла на глубину удаления глубоко расположенных дефектов: трещин, раковин и др.
Перед установкой в наплавочный станок валок предварительно подогревают до температуры не менее 250 °С.
Нагрев непосредственно рабочего участка валка осуществляется переносной газовой горелкой в течение 3 часов или производится нагрев валков в камерной газовой печи термического участка при температуре печи 700 °С в течение 40-50 мин.
По литературным данным [2], при подогреве валков перед наплавкой до 280…3000С в процессе охлаждения возможно появление продольных и поперечных трещин. Предварительный подогрев до 350...3700С полностью исключит образование трещин.
По существующему опыту данная подготовка валков под наплавку является вполне достаточной. Однако допустимый размер остающихся после обточки трещин разгара может быть причиной возникновения в наплавленном металле пор. Причиной возникновения пор является наличие в трещинах масла и окалины.
Способ нагрева валков не имеет значения, если только обеспечен сквозной нагрев до нужной температуры. Подогрев осуществляется переносными горелками до нужной температуры.
Наиболее широко в металлургической промышленности используют автоматическую наплавку под флюсом одной проволокой (сплошной, порошковой) или лентой (холоднокатаной, порошковой, спеченной). Это достаточно универсальный способ, обеспечивающий хорошее формирование и высокое качество наплавленного металла. Легирование наплавленного металла при этом способе наплавки осуществляется, как правило, через электродный материал, легирующие флюсы применяют редко.
121
На механическом трубном заводе для наплавки пильгерных валков используется автоматическая электродуговая наплавка под флюсом проволокой сплошного сечения [2].
Эффективность эксплуатации наплавленных валков определяется, прежде всего, составом металла, обеспечивающим необходимые свойства рабочей поверхности.
На механическом заводе №13 по существующей технологии наплавка рабочей поверхности пильгерных валков производится высоколегированной проволокой Св30Х25Н16Г7 аустенитного класса по ГОСТ 2246-70. При восстановлении валков рабочей поверхности предварительно наплавляется подслой проволокой Св-08Х21Н10Г6 ГОСТ 2246-70 для лучшей свариваемости с основным металлом.
Рабочий слой, наплавленный проволокой Св-30Х25Н16Г7, относится к жаростойким сталям. По диаграмме Шеффлера состав слоя– аустенит.
Отличительной особенностью хромоникелевых аустенитных сплавов является прочность и вязкость, высокая стойкость против коррозии, окалиностойкость и жаропрочность. Твёрдость наплавленного слоя после наплавки составляет 220-230 НВ, после эксплуатации твёрдость повышается в результате наклёпа до 270 НВ.
Аустенит хромоникелевых сталей (не содержащих других примесей) не вполне стабилен: при нагреве до «критических» температур (от 450 до 850°) по границам кристаллов выделяются сложные карбиды хрома и железа. Эти карбиды уменьшают проскальзывание зёрен при ползучести, что положительно сказывается на эксплуатационные свойства наплавленного металла.
В основном хром используется для увеличения коррозионной стойкости сталей, а поскольку коррозионная стойкость при эксплуатации пильгерных валков не лимитируется, то присутствие в наплавленном металле хрома не обязательно.
При наплавке пильгерных валков применяется флюс марки АН-20 ГОСТ 9087-81 с температурой плавления 1100 0С, величиной зерна от 0,33 до 3 мм.
Флюс АН-20 предназначен для автоматической дуговой наплавки и сварки высоколегированных сталей.
Сварочно-технологические свойства: устойчивость дуги удовлетворительная, разрывная длина дуги до 7мм; формирование шва
122
хорошее, без особенностей; склонность металла шва к образованию пор и трещин низкая; отделимость шлаковой корки хорошая.
Флюс АН-20 обеспечивает высокую стабильность дуги, хорошее формирование наплавленного металла, хорошую отделимость шлаковой корки, что полностью соответствует требованиям получения качественного наплавленного слоя.
Качество формирования наплавленного металла, его химический состав и структура зависят от режимов наплавки. Основными факторами, определяющими режим наплавки, являются: сила тока, напряжение дуги, скорость перемещения дуги, вылет электрода, шаг наплавки и смещение с зенита.
При наплавочных работах производительность процесса определяется не скоростью перемещения дуги, как при сварочных работах, а количеством металла, наплавляемого в единицу времени. Поэтому при наплавке применяются технологические приемы и способы, позволяющие увеличить количество наплавляемого металла. Поскольку наплавке подвергаются изделия повышенной твердости (с высоким содержанием углерода и легирующих элементов), желательно, чтобы проплавление основного металла было минимальным.
Режимы наплавки пильгерных валков приведены в таблице.
Режимы наплавки пильгерных валков по технологии, применяемой на механическом заводе №13[3]
Параметры режима наплавки |
Параметры |
|
режима |
||
|
||
Диаметр сварочной проволоки, мм |
4,0 |
|
Напряжение дуги, В |
32-34 |
|
Сила тока дуги, А |
550-600 |
|
Скорость подачи наплавочной проволоки, м/ч |
86,7 |
|
Вылет электрода, мм. |
20-35 |
|
Шаг наплавки, мм. |
6-8 |
|
Скорость наплавки, м/ч |
56 |
Ток дуги при наплавке аппаратом с постоянной скоростью подачи проволоки определяется скоростью подачи. Чем больше ток,
123
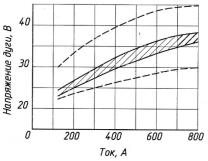
тем больше производительность наплавки, поэтому увеличение тока приводит к увеличению глубины проплавления, что нежелательно.
Напряжение дуги при данном токе определяет форму наплавленного валика. Повышение напряжения увеличивает ширину и уменьшает высоту валика. Желательно минимальное напряжение дуги, однако оно должно быть согласовано с током: при слишком малом напряжении получается узкий, высокий наплавленный валик, с уродливыми очертаниями сечения, при слишком большом - плавится очень много флюса и возможно его стекание.
Рис. 2. Напряжение дуги в зависимости от тока при наплавке под флюсом [4]
Заштрихованная область (рис. 2) – оптимальный диапазон, пунктиром показаны пределы напряжения применяемого в отдельных случаях.
Согласно вышесказанному, напряжение и ток дуги при наплавке пильгерных валков находятся в области оптимальных значений.
Скорость перемещения дуги при наплавке, в отличие от сварки, не определяет производительности процесса, но влияет на распределение металла по наплавляемой поверхности. Однако слишком малая скорость наплавки нарушает формирование: образуются подвороты, ванна растекается не равномерно.
Линейная скорость наплавки обычно выбирается в пределах от 20 до 40 м/ч. Следует учитывать, что пильгерный валок имеет переменное сечение, в результате чего при постоянном значении скоро-
124
сти вращения шпинделя наплавочного станка линейная скорость по длине наплавляемого валика будет переменной.
Оптимальная величина вылета зависит от физических свойств проволоки и от диаметра. Учитывая, что сварочная проволока Св30Х25Н16Г7 относится к аустенитной нержавеющей стали и имеет относительно высокое электрическое сопротивление оптимальный вылет не должен превышать 30мм.
Смещение электрода с зенита навстречу направлению вращения позволяет в определенных пределах предупредить стекание жидкого металла.
В зависимости от длины ванны величина смещения должна составлять от 15 до 40мм. Смещение с зенита корректируют в процессе наплавки с таким расчетом, чтобы не происходило ссыпания флюса и затекания шлака перед началом дуги.
Шаг наплавки определяет гладкость наплавленной поверхности и долю основного металла в составе металла наплавки. Слишком большой шаг наплавки может вызвать неровности и чрезмерное разбавление основным металлом, слишком малый шаг – дефекты в виде подворотов и непроваров.
Для получения качественного слоя шаг наплавки должен составлять примерно от 0,4 до 0,75 ширины наплавленного валика.
Режим наплавки должен выбираться с таким расчётом, чтобы, несмотря на переменную скорость по длине наплавленного валика, получить на всех участках хорошее формирование и свести к минимуму припуск на обработку.
Литература
1.Сафонов Е.Н. Новые материалы и технологические процессы для продления ресурса прокатных валков – Нижний Тагил, 2005.
–212с.
2.Гусев В.П. Исследование и разработка технологии наплавки деталей экономнолегированным сплавом стойким в условиях термоциклического воздействия: Дис. к.т.н. Свердловск, 2008 – 132с.
3.Бирман С.Р. – Экономнолегированные мартенситностареющие стали. – М.: Металлургия, 2001г – 208с.
125
4.Толстых Л.Г., Фурман Е.Л. – Наплавочные материалы и технология наплавки. – Екатеринбург: ООО «Издательство УМЦ УПИ»
2004. – 100с.
5.Сварка и свариваемые материалы. Справочник . Т.1. Под ред. В.Н. Волченко. М.: Металлургия, 2006, 527с.
Воронежский государственный технический университет
УДК 621.9(075.8)
А.В. Перова, Е.Ю. Марышева
ОПТИМИЗАЦИЯПРОЦЕССОВВМАШИНОСТРОЕНИИ СИСПОЛЬЗОВАНИЕМ ГЕНЕТИЧЕСКИХМОДЕЛЕЙРЕШЕНИЯ
Ключевые слова: генетический алгоритм, нелинейные модели, целевая функция
Рассматриваются основные преимущества использования генетического алгоритма решения при оптимизации процессов машиностроительного производства, описываемых нелинейными математическими моделями
Для описания, исследования и оптимизации процессов в машиностроении, возникающих в непредсказуемых рыночных отношениях используются нелинейные модели, например при инвестициях в машиностроительное производство, задачах планирования производства при ограниченных ресурсах, прогнозировании поломки и ремонта оборудования, качества выпускаемой продукции, и т.п. Кроме того, во многих существующих табличных моделях широко используются негладкие функции Excel. Наличие существенно нелинейных и негладких функций, имеющих несколько локальных оптимумов обычно означает, что у данной модели отсутствуют свойства вогнутости или выпуклости, необходимые средству Поиск решения, чтобы оптимизировать задачу нелинейного программирования и найти глобальный оптимум. На практике наличие в табличной модели негладких функций может помешать средству Поиск решения найти даже локальный оптимум, поскольку его методы выбора направления поиска зависят от гладкости целевой функции.
126

Например, процесс описан моделью с двумя переменными решения, в которой требуется максимизировать целевую функцию прибыли Y. График целевой функций, которая является произведением двух негладких нелинейных функций от двух переменных XI и Х2 показан на рисунке.
При построении графика целевой функции Y для значений XI и Х2 в диапазоне от 1 до 5 использовались значения этой функции, подсчитанные в таблице подстановки с двумя входами. Приведенный график подтверждает невогнутость функции Y. Как показано на рисунке, существует множество локальных оптимумов, которые из них с довольно плоскими вершинами, а другие с очень острыми вершинами. С помощью средства Поиск решения табличного процессора Excel мы не можем получить глобальный оптимум, находящийся приблизительно в точке XI = 1,42, Х2 = 1,41 со значением целевой
22,28.
При первом запуске средства Поиск решения обеим переменным XI и Х2 было присвоено начальное значение 3,3. Поиск решения нашел локальный оптимум, расположенный далеко от глобального.
127
При повторном запуске средства Поиск решения переменным XI и Х2 было присвоено начальное значение 1, начальная точка находилась вблизи от глобального оптимума, но Поиск решения вновь не нашел его. В этой простой модели можно отследить получаемые решения и сравнить их с известным глобальным максимумом, в более сложных моделях нелинейного программирования со многими переменными и ограничениями практически невозможно представить форму графика целевой функции, поэтому весьма вероятно будет принято "оптимальное" решение, которое может быть как угодно далеко от глобального оптимального решения.
Поэтому необходимо использование более устойчивых алгоритмов решения задач нелинейного программирования с негладкими функциями, имеющими несколько оптимумов. При этом необходимо найти способ выбора хороших начальных значений переменных, оценки промежуточных решений и их использования для нахождения лучших значений переменных, не полагаясь на методы, основанные на дифференцировании, которое часто невозможно выполнить вследствие негладкости функций. Для решения подобных задач возможно использование генетического алгоритма или метода направленного случайного поиска [1]. Работаалгоритма основана на следующих свойствах:
1.Алгоритм использует случайно выбираемые начальные точки. Таким образом это недетерминированный метод.
2.В большинстве методов оптимизации хранится только наилучшее решение, найденное в процессе поиска, в генетическом алгоритме хранится большое количество промежуточных результатов, называемое популяцией возможных решений, не все из которых являются хорошими решениями. Данная популяция используется для создания новых начальных точек, не обязательно в окрестности текущего наилучшего решения, что помогает алгоритму избегать остановки в локальном оптимуме.
3.Аналогично генным мутациям в биологии алгоритм время от времени производит случайные изменения в одном или нескольких членах популяции для создания новых потенциальных начальных точек -"потомков", которые могут находиться далеко от остальных членов данной популяции.
4.Элементы существующих в популяции решений комбинируются друг с другом с помощью операции, напоминающей скрещива-
128
ние цепочек ДНК, чтобы создать новое потенциальное решение, обладающее чертами каждого из родительских решений.
5.Любые нарушения ограничений новым решением приводят к вычитанию (в модели максимизации) из значения целевой функции для данного решения или прибавлению к нему (в модели минимизации) "штрафа", сумма которого отражает степень нарушения ограничений. Это измененное значение целевой функции становится мерой "пригодности" данного решения.
6.Аналогично естественному отбору начальные точкипотомки, которые не улучшают значения целевой функции и не помогают получить новые начальные точки, в конечном счете удаляются из популяции как "непригодные".
В генетическом алгоритме решение задачи представляется в виде генома. Алгоритм работает с выборкой, содержащей десятки или даже сотни допустимых решений. Из этой выборки решений генетический алгоритм создает с помощью операций мутации и скрещивания новые решения, чтобы получить набор значений на "звание" наилучшего решения. В ходе скрещивания комбинируют две выборки решений, чтобы получить новую. Идея скрещивания состоит в том, что новая выборка может быть лучше обеих предыдущих, если взять лучшие характеристики каждой из них. В отличии от скрещивания, операция мутации привносит некий элемент случайности новые значения. Ее задача заключается в том, чтобы помочь программе найти такие решения, которые невозможно получить путем скрещивания. Решения с низким значением выигрыша ("плохим" значением целевой функции) сохраняются, поскольку они могут произвести в следующих вариантах с высоким выигрышем (лучшим значением целевой функции). Если этого не происходит, эти значения в конечном счете удаляются из выборки решений. Согласно принципу выживания наиболее "приспособленных" значений, генетические алгоритмы - это алгоритмы поиска, использующие структурированный обмен информацией (скрещивание) и рандомизацию (мутации) для формирования процедуры поиска, обладающей свойствами природных процессов: в каждом поколении создается новый набор решений, созданных из наиболее подходящих экземпляров предыдущего поколения. Генетический алгоритм не является просто случайным движением по пространству возможных решений - это неэффективно. Напротив, данный
129