
3238
.pdf
Рис. 2. Общий случай динамической неуравновешенности
Балансировку всех роторов, изготавливаемых для турбонасосных агрегатов ракетно-космической техники, проводят согласно общим требования к динамической балансировке:
1.1Значения остаточных дисбалансов ротора определять прямым измерением (в некоторых случаях измерение значений остаточных дисбалансов методом обхода контрольным грузом).
1.2При балансировке на зарезонансных станках со стробоскопом для каждого типоразмера роторов агрегатов подачи следует изготавливать тарировочный ротор, на который предприятием – изготовителем оформляется технологический паспорт.
1.3Балансировочная оснастка и станок должны обеспечивать при балансировке ротора воспроизводимость показаний индикатора значений дисбаланса.
1.4Способы базирования роторов в опорах балансировочного станка следует выбирать, руководствуясь следующим справочными данными, представленными в таблице 1 (большое число знаков «+»
40
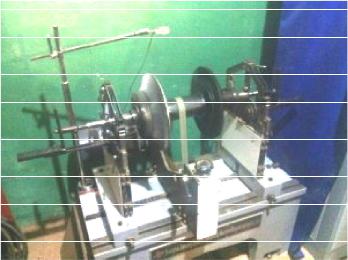
соответствует предпочтительному применению данного способа базирования, знак «-» - применять не рекомендуется).
Рис. 3. Динамическая балансировка пакета лопаточных деталей на оправке
1.5Балансировку роторов проводить на технологических подшипниках, точность изготовления которых должна быть не ниже пятого класса, а величина радиального зазора не должна превышать верхней границы 7 группы стандартных зазоров. Перед балансировкой ротора ввести в подшипник 0,2-0,5 г жидкой смазки и так же добавлять ее вовремя балансировки. Предохранять подшипники от попадания в них частиц абразива или металлической стружки при съеме материала. Проводить периодический контроль по внутреннему диаметру и радиальному зазору на соответствие технологической документации не реже 1 раза в 3 месяца. Внешний вид, плавность вращения (без заеданий – проверяется в вертикальном положении оси вращения) подшипника проверять перед каждой сборкой ротора на балансировку.
1.6Балансировку консольных роторов на станках, не предназначенных для их балансировки, следует проводить в балансировочных рамках, которые должны обладать достаточной жесткостью и
41
минимальной массой. Опорные поверхности рамок и посадочные места под подшипники выполнять с полем допуска h6, Н7, параметром шероховатости Ra от 0,8 до 0,4 мкм, допуском соосности относительно общей оси опорных поверхностей 0,015 мм в радиусном выражении.
Опоры для балансировки роторов
Объект |
|
Цилинд- |
Опоры |
Роли- |
Косо- |
Призматиче- |
баланси- |
|
рические |
скольже- |
ковые |
валко- |
ские вкла- |
ровки |
|
вклады- |
ния |
опоры |
вые |
дыши |
|
|
ши |
|
|
опоры |
|
Роторы |
|
|
|
|
|
|
баланси- |
|
+ |
+++ |
++ |
++ |
++ |
ровочные |
|
|
|
|
|
|
Детали |
и |
|
|
|
|
|
сборочные |
- |
++ |
+ |
- |
- |
|
единицы |
|
|
|
|
|
|
на оправке |
|
|
|
|
|
|
Детали |
и |
|
|
|
|
|
сборочные |
|
|
|
|
|
|
единицы |
с |
+ |
+++ |
++ |
+ |
+ |
собствен- |
|
|||||
ными цап- |
|
|
|
|
|
|
фами |
|
|
|
|
|
|
1.7Участок балансировки должен быть изолирован от оборудования, оказывающего постороннее влияние на показания индикатора дисбаланса балансировочного станка.
1.8Ротор должен поступать на участок балансировки чистыми, без видимых невооруженным глазом следов загрязнений (масляных пятен, пыли, стружки и т.п.). После балансировки поверхности ротора в местах съема металла следует протереть салфеткой, смоченной в бензине, и просушить сжатым воздухом.
1.9Рабочее место съема металла с поверхностей ротора должно быть отделено от участка балансировки и оборудовано вытяжной вентиляцией.
42
1.10 Относительная влажность воздуха в балансировочном помещении должна быть не выше 70%, температура воздуха не ниже 15 ͦС и не выше 30 ͦС.
Для решения на протяжении уже нескольких десятков лет разрабатываются и совершенствуются методы и балансировочное оборудование [4, 5], которые однозначно предусматривают снятие излишков металла в местах повышенной концентрации эксплуатационных экстремальных нагружений. Для повышения усталостной прочности таких участков нами был получен опыт местного упрочнения нарушенных балансировщиками поверхностей микрошариками с положительным результатом [6]. В нашем случае комбинированная обработка образцов до и после осаждения никеля толщиной 30...50 мкм, проводилась на установках эжекторного типа с наложением тока низкого напряжения (рис. 4) при соблюдении следующих режимов:
расстояние от оси сопла между его срезом и поверхностью образца L=50 5 мм на диаметре вращения Dв=100 мм;
время обработки каждого участка поверхности – 60 с;
угол соударения потока микрошариков с поверхностью
=60 5 ;
диаметр сопла – 10 мм;
скорость вращения шпинделя установки nвр=20–60 мин-1;
давление сжатого воздуха в струйном аппарате – 0,2–0,4
МПа;
напряжение 2-10 В;
расход газожидкостной слабопроводящей среды – 2 м3/мин. Газожидкостная слабопроводящая среда состояла из воздуха и
распыленной до капельной фракции технической воды, являющейся слабым проводником. Эффект от воздействия токов низкого напряжения заключался в том, что если принять в качестве исходной информации высоту микронеровностей до обработки (RZ0), а ограничительными условиями – время действия тока, то процесс съема неровностей за единичное соударение принимает вид (рис. 4)
43
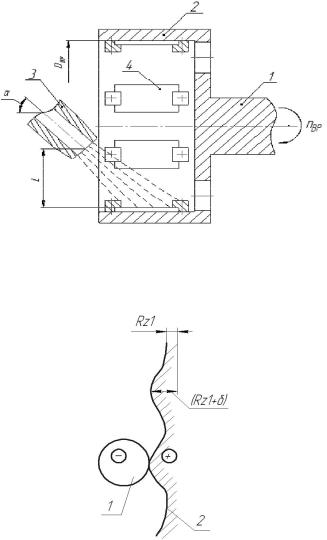
Рис. 3. Схема проведения эксперимента по струйной обработке образцов:
1 – шпиндель установки, 2 – экспериментальная оснастка, 3
– сопло, 4 – образец плоский
Рис. 4. Схема формирования микрогеометрии в полости канала: 1 – гранула-катод; 2 – анод-заготовка;
RZ1 – глубина микрорастравливаний неупрочненного участка заготовки; (RZ1+δ) – микропогрешность и микроуглубление.
44
(RZ1+δ) = RZ0 – ( / )· ·jср к,
где – электрохимический эквивалент материала заготовки;– удельная плотность материала заготовки;
jср – средняя плотность тока;
к – длительность контакта ( к =0,1–0,3 мкс);– коэффициент выхода по току.
Ток (J) в зоне контакта может достигать 10А, площадь контактного действия гранулы составляет 0,1–0,3 мм2. Тогда средняя плотность тока
jср = 0,5J/F.
Экспериментальные исследования показали, что время обработки с целью получения требуемой шероховатости составляет доли минуты, что на порядок ниже по сравнению с параметром, показанным при виброударном осаживании микронеровностей.
Достижимое изменение шероховатости в этом случаеRz max=RZ0–(RZ1+δ) зависит от скорости анодного растворения, которая в момент удара резко увеличивается из-за повышения удельной проводимости в месте соударения в 2-3 раза. При этом создается сглаженный микрорельеф без концентраторов микротрещин и микровыступов, а микрошарики формируют стабильную шероховатость, определяемую их размерами и механическими свойствами с учетом сплошности перекрытия не менее 95% (для высокопрочных никелевых сплавов Rz ср =2,5-3,2 мкм).
Литература
1.Сухочев Г.А. Управление качеством изделий, работающих
вэкстремальных условиях при нестационарных воздействиях / Г.А. Сухочев. – Воронеж: ВГУ, 2003. – 287 с.
2.Проблемы прочности элементов конструкции ЖРД / Е. Б. Заметаев, Ю. М. Мисевич, Л. И. Поляков и др. // Научнотехнический юбилейный сборник КБ химавтоматики. – Воронеж:
ИПФ «Воронеж», 2001. – С. 528–531.
3Моисеев, В. А. Технология производства жидкостных ракетных двигателей. / В. А. Моисеев, В. А. Тарасов, В. А. Колмыков и др.
– М.: Изд-во МГТУ им. Н.Э. Баумана, 2008. – 381 с.
45
4.Уравновешивание роторов и механизмов: [Сб. статей] / Под ред. В.А. Щепетильникова. – М.: Машиностроение, 1978. – 320 с.
5.Сокольников В.Н. Технологические вопросы обеспечения качества динамической балансировки роторов / В.Н. Сокольников, Г.А. Сухочев, С.Н. Коденцев // Проблемы и перспективы развития машиностроения: сб. науч. тр. междун. науч.-техн. конф., посвящённой 60-летию Липецкого государственного технического универси- те-та: Липецк, 17-18 ноября 2016 г. - Том. 1, Часть 1. – С. 238-244.
6.Сухочев Г.А. Технологическое обеспечение качества лопаточных деталей с использованием наукоемких нетрадиционных методов обработки / Г.А. Сухочев, А.В. Капустин, Е.Г. Смольянникова, Д.М. Небольсин // Насосы. Турбины. Системы, – Воронеж: ООО
ИПЦ «Научная книга», 2011. – №1. – С.34–42
Воронежский государственный технический университет
УДК 621.9(075.8)
Р.В. Хрюкин, Е.В. Смоленцев
ПРИМЕНЕНИЕ АДДИТИВНЫХ ТЕХНОЛОГИЙ ПРИ ИЗГОТОВЛЕНИИ «СМЕСИТЕЛЬНОЙ ГОЛОВКИ» ЖИДКОСТНОГО РАКЕТНОГО ДВИГАТЕЛЯ
Ключевые слова: ракетный двигатель, аддитивные технологии, 3D - печать, селективное лазерное спекание, смесительная головка, форсунки
В работе рассмотрен метод получения «смесительной головки» жидкостного ракетного двигателя при помощи аддитивных технологий методом «селективного лазерного спекания»
Аддитивные технологии являются перспективными технологиями для производства изделий в различных областях машиностроения, самолетостроения и ракетостроения. Аддитивные технологии – это принципиально новые методы в производстве различного рода изделий.
Аддитивные технологии позволяют:
– изготавливать детали из композиционного материала;
46
–воспроизводить форму изделия по компьютерной модели, уменьшая потери материала при механической обработке;
–изменять состав материала во время нанесения согласно функциональной особенности поверхностной и внутренней части детали;
–получать материалы со свойствами, характерными только для лазерной обработки [1].
Аддитивные технологии
Аддитивные технологии – это применение 3D - печати в промышленности, что означает изготовление изделия путем добавления.
Суть аддитивного производства в сложении, в способе создания деталей различной сложности, путем нанесения используемого материала последовательно, слой за слоем, при этом расходуется материал столько, сколько необходимо для построения.
Спомощью программное обеспечение компьютерная модель делится на слои одинаковой толщины, после чего 3D - принтер создаёт изделие, путём последовательного нанесения одного слоя за другим.
Аддитивные технологии отличаются друг от друга выбором материалов и способа их нанесения, однако во всех случаях создание модели основывается на послойном наращивании. Можно сказать, что аддитивное производство это еще один способ изготовления деталей из разных материалов, не уступая традиционным механическим методам.
В настоящее время известны несколько технологий 3D-печати такие как:
1) Быстрое прототипирование;
2) Лазерная стереолитография (SLA);
3) Селективное лазерное спекание.
В данной работе будет рассмотрен метод селективного лазерного спекания.
Селективное лазерное спекание
В основе метода лежит использование лазерных излучателей высокой мощности для частичного спекания, материала в единое целое.
Как и другие технологии 3D - печати, лазерное спекание создает модели послойно. При лазерном спекании на модель наносится
47
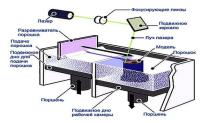
слой порошка, в котором с помощью лазера при высоких температурах частично расплавляя порошок в местах касания луча, спекая частицы между собой и с предыдущим слоем вычерчивается новый контур. В данном случае модель находится в неизрасходованном материале до окончания печати. Технология метода «селективного лазерного спекания», представлена на рис. 1.
Рис. 1. Технология (СЛС)
Как видно из рис. 1, лазерное излучение с помощью системы зеркал переносится в зону построения, где по мере формирования слоя платформа построения опускается и начинается формирование нового слоя порошка, который подается выдвижением платформы подачи материала и выравнивается в ровный слой роликом.
Смесительная головка жидкостного ракетного двигателя
Смесительная головка камеры жидкостного ракетного двигателя, включающая наружное, среднее и внутреннее (огневое) днища, соединенные между собой двухкомпонентными, однокомпонентными форсунками, пайкой и сваркой. Двухкомпонентные форсунки расположены по нескольким концентрическим окружностям, при этом несколько двухкомпонентных форсунок выступает из огневого днища, образуя анти пульсационные перегородки в виде кольца с шестью расходящимися лучами, деля поперечную площадь камеры сгорания на семь равнозначных полостей.
Также установлены однокомпонентные форсунки выступающие из огневого днища, кроме этого форсунки анти пульсационных перегородок выступают в огневую полость камеры. Концы форсунок соединены между собой припоем или сварным швом. Выступающие форсунки предотвращают развитие колебаний в камере. Модель смесительной головки представлена на рис. 2.
48
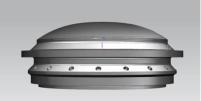
Рис. 2. Смесительная головка
По внутренним трубкам поступает жидкий кислород, а по наружным – отработанный на турбине турбонасосного агрегата (ТНА) генераторный газ с избытком водорода. Через поры днищ «чистый» водород с низкой температурой (около 300 К) из полости между огневой и средней днищ под давлением проникает, с одной стороны, в камеру сгорания, а с другой в полость между средним и наружным днищами с горячим генераторным газом. В результате обеспечивается охлаждение обоих днищ корпусов выступающих форсунок.
Изготовление смесительной головки методом (СЛС)
Данный метод позволит упростить изготовление смесительной головки совместно с форсунками, избежать сложности изготовления каналов охлаждения форсунок исключив из конструкции пайку. Позволит уменьшить маршрут изготовления и контроль изделия.
Для технологии послойного лазерного сплавления был выдран металлический порошок ЖС6К. Химический состав ЖС6К представлен в таблице.
С |
Cr |
Al |
W |
Mo |
Ti |
Co |
B |
Mn |
Fe |
S |
P |
0,13 |
9,5 |
5,0 |
4,5 |
3,5 |
2,5 |
4 |
0,02 |
0,4 |
2 |
0, 1 |
0, 1 |
|
|
|
|
|
|
|
|
|
|
|
|
Для изготовления смесительной головки ЖРД, методом «селективного лазерного спекания» используется металлический порошок ЖС6К с гранулометрическим составом 10 – 40. Диаметр луча 50
– 100 мкм.
Процесс 3D - печати начинается с разработки виртуального образа будущего объекта в CAD - программе («SiemensNX»,
49