
2890
.pdfлокализованным сдвигом в периферийных от центральной трещины областях. Разрушение образцов только после термообработки давало чаще всего излом в виде ―чашка-конус‖, что соответствует условиям распространения трещины за счет слияния с трещинами периферийной зоне. Причем этот эффект тем более явно виден, чем ниже значение Sк.
Таким образом созданием определенного структурного состояния путем конкретной предварительной обработки стали 12Х18Н10 можно заметным образом влиять не только на характер развития пластической деформации, но и повышать параметры конструктивной прочности, такие, как надежность и циклическая стабильность.
Специалистам в области ОМД рекомендуется учитывать приведенные в работе результаты при разработке операций получения изделий из стали 12Х18Н10 глубокой вытяжкой,
штамповкой, волочением. |
|
Получено: |
Воронежский государственный |
14.09.2003 |
технический университет |
УДК 621.78 |
|
КОНСТРУКТОРСКО-ТЕХНОЛОГИЧЕСКАЯ ОТРАБОТКА УПЛОТНЕНИЙ РАЗЪЕМНЫХ НЕПОДВИЖНЫХ СОЕДИНЕНИЙ
Лебедев В.Ф., СинюковТ.У., Скачилов В.Н., к.т.н.
Многие соединения топливных и газовых магистралей двигателей выполняются неразъемными, но из условии проведения разборки, замены узлов при техобслуживании и проверке требуется использование разъемных неподвижных соединении с соответствующими уплотнениями.
Внастоящей статье представлены пути разработки конструкции уплотнения неподвижного соединения, имеющего минимальный вес и незначительную утечку рабочего тела при высоких давлениях.
Встатье рассматриваются особенности конструкции уплотнения,
способы его изготовления и этапы отработки.
Разработка новых надежных уплотнений для криогенных и высоко температурных сред для разъемных неподвижных соединений, имеющих малый вес, с возможными
73
раскрытиями стыков от воздействия давления, температур, виброперегрузок с допустимыми нормами утечек рабочего тела до 10-8 кг/с, на давления до 800 кг/см2 требует комплексного подхода решения проблем по их созданию.
Проблемы создания упругих, самоуплотняющихся от давления уплотнений с наружным диаметром до 600 мм для разъемных соединений двигателя и агрегатов подачи решались совместно со специалистами смежных предприятий, НИИ и учебных заведений по следующим направлениям:
-выбор конструкции и материалов; -проведение расчетно-исследовательских работ; -отработка технологии изготовления;
-разработка установок с максимально -возможной имитацией условий эксплуатации и конструкции разъемных соединений;
-проведение экспериментальной отработки в имитаторах;
-подтверждение эксплуатационных характеристик уплотнений на двигателе. Для ЖРД, созданных в КБХА были разработаны упругие самоуплотняющиеся от давления металлические прокладки с уплотнительными кромками покрытыми пластически деформируемым материалом.
Упругость прокладок обеспечивается их профилем и соответственно выбранным материалом.
По характерным особенностям конструкции прокладки подразделяются на:
а) радиального типа, конические с углом наклона 50°60° из стали 12Х18Н10Т -ВД с покрытием МЗ;
б) осевого типа:
-К- и П- образного профилей, из сталей марок 07X16Н6, ХН43БМТЮ с фторопластовым покрытием ФЗ толщиной 0,060,1 мм и М60Ср21 для К-образного профиля;
-Ω -профиля из стали 36НХТЮ с покрытием M60Kg 9-21. Размеры поперечного сечения прокладок выбраны
минимально возможными, прокладки размещаются в канавках фланцев, что, с точки зрения уменьшения габаритов соединения, является наиболее предпочтительными.
74
Уплотнительные прокладки не оказывают влияния на размер фланцев. Наружный диаметр фланцев определяется диаметром окружности под болты. Размеры прокладок и элементов соединения регламентируются работами [1], [2].
Применение упругих прокладок снижает нагрузки на болты, что позволяет применить болты с меньшим диаметром и в целом уменьшить вес элементов разъемного соединения.
Толщина лапок , К- образного профиля прокладок, поперечное сечение и угол наклона прокладки конической формы выбраны так, чтобы обеспечить нагрузку на уплотнительные пояски по окружности после установки прокладки, составляющую 3050 кгс/см и 100170 кгс/см, соответственно. Такая нагрузка создает давление на месте контакта рабочего пояска уплотнения и поверхности гнезда достаточное для того, чтобы вызвать затекание покрытия в микронеровности на поверхностях гнезд.
Выбор оптимальной степени деформации уплотнения, определение удельных давлений по уплотнительным пояскам и правильность выбора типа покрытия проводится на основании исследований упругих характеристик уплотнений (рис. 1), с оценкой величины деформации в зависимости от нагрузки.
Уплотнения конические, , К - образного профиля сечения изготавливаются точением на станках с ЧПУ из заготовок - прутков, поковок; Ω-профиля диаметром 400-600мм изготавливаются из ленты 36НХТЮ в штампах, с разжимными пуансонами (рис. 2, 3).
Определенную сложность при отработке технологии [3] имелись при получении диаметров 400-600 мм с отклонением 0,4 мм, неплоскостности в пределах 0,02, непараллельности 0,05 мм торцов уплотнения и выполнения сопряженных радиусов скруглений на уплотнительной кромке.
Экспериментальная отработка проводилась с целью проверки эксплуатационных характеристик уплотнений. Проверяемые параметры включали - утечку, температуру, давление, цикличность, вибрации.
75
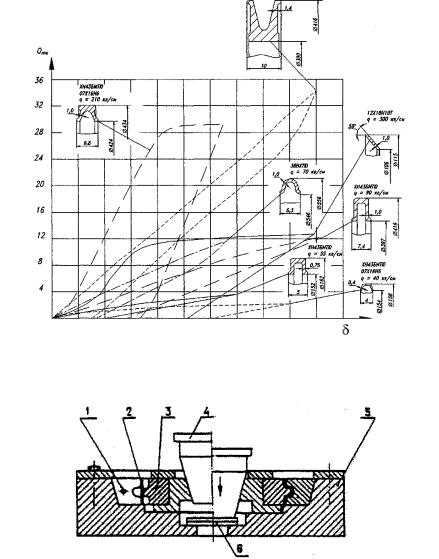
БрБ2 q=260 кг/см
0,1 |
0,2 |
0,3 |
0,4 |
0,5 |
0,6 |
0,7 |
0,8 |
0,9 1,0 |
мм |
Рис.1. Характеристики упругости прокладок
Рис. 2. Схема штампа с разжимными пуансонами для формообразования профиля 1 - полукольца; 2 - заготовка; 3 - разжимные пуансоны; 4 - пуансоны вертикального хода; 5 - бандаж; 6 – кольца
76
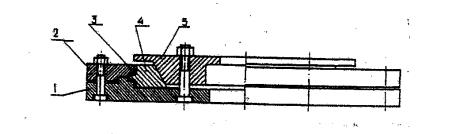
Рис. 3. Схема приспособления для термообработки 1 - основание; 2 — кольцо; 3 - уплотнительное кольцо; 4 - разжимные секторы; 5 - разжимной конус
Низкотемпературные условия моделировались пропусканием жидкого азота, водорода через испытательную установку или погружением в емкость с азотом. Высокотемпературные условия достигались размещением внешних нагревательных элементов вокруг установки или размещением самой установки в печи.
В установку подавался под давлением один из компонентов: гелий, азот или оксид.
Утечка измерялась методом «щупа», накопления, мундштука. При проверке двигателя утечка через каждое соединение в
магистралях не должна была превышать допустимую утечку гелия равную 132 мм3 Па/с (1·10–З л мкм рт.ст./с) при давлении ВГС 1,6 МПа (16 кгс/см2 ).
В испытательных установках, имитирующих конструкцию разъемных соединений и рабочие условия в двигателе, было испытано более 250 образцов уплотнений, диаметром от 20 до
600мм [4].
Результаты комплексных исследований показали, что конструкция упругих уплотнений для разъемных соединений удовлетворяет эксплуатационным требованиям и их работоспособность подтверждена при работе двигателей.
При разработке уплотнений и для сравнения технического уровня была использована информация [5] по созданию уплотнений для неподвижных соединений в криогенных системах космических летательных аппаратов США.
Из сравнения параметров двигателя РД0120 и SSME выявлено, что упругие уплотнительные прокладки по конструктивному
77
исполнению, обеспечению степени герметичности находятся на уровне уплотнений, применяемых на SSME и обеспечивают работоспособность разъемных неподвижных соединений в магистралях при давлениях больших на ~10%, и диаметрах больших на 25-30%.
Разработанные упругие самоуплотняющиеся от давления малогабаритные в поперечном сечении уплотнения для разъемных соединений позволяют проводить разборку, замену узлов, многократно их использовать и сокращают сроки доработки и доводки двигателей.
Литература:
1.ГОСТ 19749-84-ГОСТ 19755-84. "Соединения неподвижные разъемные пневмогидросистем".
2.СТП 256-92-2000. "Соединения неподвижные разъемные с уплотнительной прокладкой манжетного типа". КБХА, 2000.
3.Разработка технологии изготовления уплотнительных элементов манжетного типа из ленты сплава 36НХТЮ. Технический отчет № 131-83-320. КБХА, 1983.
4.Завершение работ по АДИ уплотнений неподвижных разъемных соединений двигателя РД0120 в имитаторах. Техническая справка № К-01А-54-85, КБХА, 1985.
5.Даниэльс К.М. Разработка уплотнений неподвижных соединений агрегатов с малой массой на давление 75,84 МПа (770 Бар) и криогенные температуры. Технический перевод № 2246.УДК 62-762, 1982
Получено: |
Воронежский государственный |
14.09.2003 |
технический университет |
УДК 532.0 (083) |
|
ХИМИЧЕСКАЯ, МЕХАНИЧЕСКАЯ И РАДИАЦИОННАЯ СТОЙКОСТЬ МИНЕРАЛЬНЫХ МАСЕЛ.
Л.А. Иванов, Пачевская Г.Н., Эктов В.Н. (гр. АО-991)
В процессе эксплуатации минеральные масла и их смеси теряют физико-механические, смазывающие и другие свойства,
78
вследствие чего может быть нарушен режим работы питаемых гидроагрегатов. Такое ухудшение качества масел происходит в основном вследствие механического и химического воздействия на них различных факторов, основными из которых являются окисление жидкости вследствие контакта с воздухом и еѐ деформация в условиях работы под высоким давлением.
Важным качеством, характеризующим масла и их смеси, является химическая стабильность, или стойкость к окислению, в результате которого происходит выпадение из масел отложений в виде смол, а также понижение вязкости масла. При окислении на рабочих поверхностях подвижных элементов образуется тонкий твердый налет, который при перемещениях деталей разрушающе действует на резиновые уплотнения.
Практика показывает, что интенсивность окисления масла повышается с увеличением температуры на поверхности его контакта с воздухом. Например, при повышении температуры на 10 0С интенсивность окисления масла практически удваивается. В связи с этим необходимо стремиться к окислению или к уменьшению даже локального повышения температуры масла, которое может произойти за счет тепла, выделяемого при сжатии нерастворенных в масле пузырьков воздуха, а также тепла, выделяемого при трении скользящих пар гидроагрегатов и при дросселировании, вытекающего через их конструктивные зазоры. Для уменьшения окисления масла максимальная его температура не должна превышать 80 0С.
Помимо температуры, катализатором в процессе окисления масла являются механические частицы загрязнения.
Окислению способствует наличие в рабочей жидкости гидросистем воды и в первую очередь вследствии того, что в воде растворяются кислоты и щелочи, всегда присутствующие в гидросистемах.
Процесс окисления происходит особенно активно в масляном резервуаре системы, где в результате движения масла и пенообразования создаются условия для тесного контакта жидкости и кислорода воздуха. Для устранения этого явления применяют системы закрытого типа с герметичным резервуаромкомпенсатором.
Процесс разложения рабочей жидкости ускоряется при наличии омываемых жидкостью кадмированных и оцинкованных
79
деталей, что особенно заметно при высоких температурах (150 0С и выше). Поэтому кадмирование и цинкование деталей, контактирующих с рабочей жидкостью, не допускается.
Опыт показывает, что детали из алюминиевых сплавов целесообразно подвергать хромовокислому или сернокислому анодированию.
Стальные детали, работающие в жидкости, целесообразно подвергать воронению, а детали, поверхности которых соприкасаются с воздухом, изготавливать из нержавеющей стали. Надежная защита от коррозии достигается также применением химического никелирования. В целях устранения образования очагов коррозии не рекомендуется касаться обработанных поверхностей незащищенными пальцами рук.
Процесс окисления масел можно замедлить с помощью специальных присадок.
Вязкость большинства минеральных масел при длительной работе в условиях высоких давлений, особенно при дросселировании жидкости с большим перепадом давления и при смазке под давлением трущихся пар с высокой удельной нагрузкой, может значительно понизиться (примерно до 50% первоначального значения).
Потеря вязкости особенно сильно проявляется в масляных смесях, содержащих повышение вязкости добавки, состоящие из длинных углеводородных цепочек. Эти цепочки при длительной деформации, в частности, при многократном продавливании жидкости под высоким давлением через малые зазоры, могут разрушаться, что аналогично постепенному «размалыванию» загустителя.
В некоторых случаях применения гидроагрегатов минеральные масла подвергаются воздействию ядерных излучений, в этом случае к рабочим жидкостям предъявляются дополнительные требования радиационной стойкости.
Радиационное воздействие проявляется в первую очередь в изменении вязкости масел, которое при определенных условиях может быть значительным. Например, изменение (в процентах) кинематической вязкости при 38 0С минерального масла под действием облучения нейтронами порядка 10 8 рад достигает 300400 %.
80
Под действием облучения происходит также понижение (примерно в 2 раза) температуры вспышки, повышение (в 10 раз) испаряемости, повышение (в 2,5 раза) кислотного числа, понижение (в 3-4 раза по потере веса металлических деталей) антикоррозийных свойств жидкости.
Получено: |
Воронежский государственный |
11.12.03 |
технический университет |
УДК 532.0 (083) |
|
ПРЕДОТВРАЩЕНИЕ КАВИТАЦИИ ЖИДКОСТИ В ГИДРОСИСТЕМАХ
Л.А. Иванов, Пачевская Г.Н., Эктов В.Н. (гр. АО-991)
Кавитацией называется локальное выделение паров (вскипание) жидкости с последующей конденсацией выделившихся воздушных пузырьков, сопровождающейся местными гидравлическими ударами.
Кавитация наступает при понижении давления в какой-либо точке потока жидкости до величины ниже давления насыщенных ее паров при данной температуре, в результате чего жидкость вскипает (происходит ее разрыв), выделившиеся пузырьки пара увлекаются потоком и переносятся в область более высокого давления, где воздушные пузырьки конденсируются. Так как процесс конденсации парового пузырька (каверны) происходит практически мгновенно, частицы жидкости, заполняющие его полость, перемещаются к его центру с большой нарастающей скоростью. В результате кинетическая энергия соударяющихся частиц жидкости вызывает в момент завершения конденсации (смыкание пузырьков) местные гидравлические удары, сопровождающиеся резкими повышениями в центрах конденсации давления и температуры.
Если ликвидация (конденсация) кавитационных пузырьков будет происходить у стенки канала, то она будет подвергаться непрерывным гидравлическим ударом со стороны быстродвижущихся частиц жидкости. В результате при длительной кавитации под воздействием указанных гидравлических ударов и одновременном воздействии высокой температуры, развивающейся
81
вцентрах конденсации, происходит поверхностное разрушение (эрозия) металлических элементов.
Указанные ударные действия частиц жидкости дополняются химическим воздействием на металл обогащенного кислородом воздуха, выделяющегося из жидкости, а также процессами электролитического характера.
Кавитация может возникнуть в трубопроводах, насосах, а также во всех устройствах, где поток подвергается сужениям с последующим расширением, например, в кранах, клапанах, вентилях, диафрагмах и др.
При кавитации жидкости в трубопроводе могут образоваться воздушные пробки, в результате чего нарушается неразрывность потока и уменьшается пропускная способность трубопровода.
Разрыву потока жидкости способствует воздух (газ), находящийся в ней в нерастворенном состоянии (механическая смесь). В такое состояние частично переходит и воздух, растворенный в жидкости, который при понижении давления выделяется из раствора.
Особенно разрушительное действие оказывает кавитация жидкости на насосы, в которых она наступает тогда, когда жидкость
впроцессе всасывания отрывается по тем или иным причинам от рабочего элемента насоса: поршня, лопасти, зубьев и т.п. Такое явление, в частности, наступает, если давление на входе во всасывающую камеру насоса окажется недостаточным для того, чтобы обеспечить неразрывность потока жидкости в процессе изменения скорости ее движения в соответствии со скоростью движения всасывающего элемента.
Предельно допустимым с этой точки зрения числом оборотов насоса является такое число, при котором абсолютное давление жидкости на входе в насос будет способно преодолеть сумму потерь
внем. В случае шестеренного и лопастного насосов к
рассмотренным внутренним потерям на всасывании насоса добавляются потери, обусловленные центробежной силой.
С появлением кавитации производительность насоса понижается, возникает характерный шум, происходит эмульсирование жидкости, наблюдаются резкие частотные колебания давления в нагнетательной линии и ударные нагрузки на элементы насоса, вызывающие преждевременный выход его из строя.
82