
2890
.pdf
Для уточнения полученного |
значения |
0 |
принимаем z1 |
за |
||||||
1 |
||||||||||
начальное приближение ( z |
z 0 ) и, воспользовавшись формулами |
|||||||||
|
|
1 |
1 |
|
|
|
|
|
|
|
(13) и (14), глава IV /1/, вычисляем z 1 по формуле: |
|
|
||||||||
|
|
|
|
1 |
|
|
|
|
|
|
|
|
(0) |
|
|
0,59691 |
|
|
|||
z (1) |
z 0 |
1 |
0,68834 |
0,68631, |
|
|||||
|
|
|
|
|
||||||
|
|
|
|
|
|
|||||
1 |
1 |
2(n 3) |
|
|
|
294 |
|
|
|
|
|
|
|
|
|
|
|
|
|
||
|
|
2z(1) |
1,37262, |
|
|
|
|
|
||
|
|
|
1 |
|
|
|
|
|
|
|
|
(1) е1,37262 |
1 |
0,59561. |
||
1 |
1 |
е1,37262 |
1 |
||
|
|||||
|
|
|
Исправленное значение мало отличается от 0,59691. Аналогично вычислим исходное приближение для верхнего
доверительного предела:
z2 arg thr |
(1 |
|
|
) |
0,85 |
|
|
1,960 |
|
1,01166, |
|||
|
|
|
|
|
|
|
|
|
|
||||
|
|
|
|
|
|
|
|
|
|||||
|
|
|
|
|
|
|
|
||||||
|
|
n |
3 |
|
|
12,12435 |
|
||||||
|
|
|
2z2 |
|
2,02332, |
|
|
|
|||||
|
2 |
|
е |
2,02332 |
1 |
|
0,76645. |
|
|||||
2 |
0 |
|
|
|
|
|
|
|
|
|
|||
|
е |
2,02332 |
1 |
|
|
||||||||
|
|
|
|
|
|||||||||
|
|
|
|
|
|
|
|
||||||
Для уточнения полученного значения |
2 принимаем z2 за |
||||||||||||
|
|
|
|
|
|
|
|
|
|
|
0 |
|
|
начальное приближение |
z2 |
z20 и, воспользовавшись формулами |
|||||||||||
(13) и (14), глава IV /1/, вычислим z2(1) по формуле: |
|
13
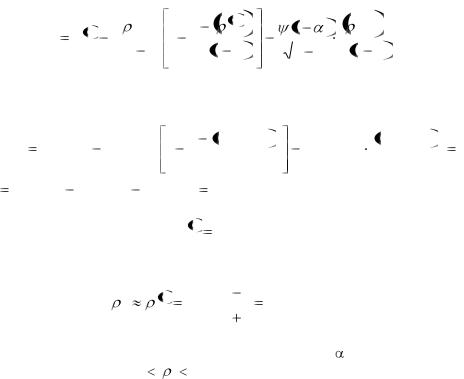
|
|
(0) |
|
3 |
0 |
2 |
1 |
(0) |
2 |
|
||||
z(1) |
z 0 |
2 |
1 |
2 |
|
|
|
2 |
|
, (11) |
||||
|
|
|
|
|
|
|
|
|||||||
|
|
|
|
|
|
|
|
|
|
|||||
2 |
2 |
2(n 3) |
|
|
4 n 3 |
|
|
|
n 3 4 n 3 |
|||||
|
|
|
|
|
|
|
По этой формуле в нашем случае получим:
z2(1) |
1,01166 |
0,76645 |
1 |
3 |
0,76645 2 |
1,960 |
|
0,76645 2 |
||||
|
|
|
|
|
|
|
|
|
||||
294 |
|
|
588 |
12,12435 |
588 |
|||||||
|
|
|
|
|
|
|||||||
1,01166 |
0,00260 |
0,00016 |
1,00890 |
|
|
|
|
|||||
|
|
|
|
|
|
2z21 |
2,0178 |
|
|
|
|
|
1 |
е2,0178 |
1 |
0,76531. |
|
2 |
2 |
е2,0178 |
1 |
||
|
|||||
|
|
|
|||
Следовательно, с коэффициентом доверия 1 - 2 = 0,95 можно |
|||||
заключить, что 0,59691 |
|
0,76531. |
|
|
таким образом, для уровня значимости = 0,025 в такой интервал с вероятностью 95 % попадет значение коэффициента корреляции той генеральной совокупности, из которой взята выборка.
Проведенные исследования и полученные результаты прямо указывает на наличие тесной корреляционной зависимости параметров L и B и дает основание предполагать о наличии корреляционной зависимости между длиной и шириной и высотой алмазного зерна. Вычисленное значение коэффициента корреляции может быть использовано для установления предельных размеров зерен по фракциям и по зернистости в целом, а также для проведения количественной оценки формы зерна.
Литература:
1. Большев Л.Н., Смирнов Н.В. Таблицы математической статистики, 3-е изд., - М.: Наука, 1983. - 416 с.
14

Получено: |
Воронежский государственный |
15.12.2003 |
технический университет |
УДК 621.9.01
ОПРЕДЕЛЕНИЕ ОПТИМАЛЬНОЙ СКОРОСТИ РЕЗАНИЯ
Э. М. Янцов, Т. Э. Янцова
В условиях перехода экономики к рыночным отношениям для малых и средних предприятий машиностроительных отраслей одной из важных задач является эффективное использование металлорежущих станков. Его характеризует ряд показателей: расход инструмента, энергетические затраты, цеховая себестоимость, показатели нормирования труда и другие. В связи с этим рассмотрим методики определения режимов резания, под которыми понимается совокупность числовых значений: глубины резания, подачи, скорости резания, геометрических параметров и стойкости режущей части инструментов, а также силы резания, мощности и других параметров рабочего процесса резания. Режимные параметры взаимосвязаны и изменение одного из них ведет к изменению других. Расчет скорости резания при назначении режимов резания, когда уже назначены глубина резания t и скорость подачи s, производится по эмпирической формуле:
V |
cv |
Kv . |
|
T mt xs y |
|||
|
|
Значения коэффициента сv и показателей степеней, также как и период стойкости инструмента Т, выбираются из таблиц. Скорость резания, рассчитываемая по формуле
V VT Kv ,
может выбираться и по таблицам соответствующих нормативов. Как в первом, так и во втором случае, Kv – это произведение ряда
15
коэффициентов, учитывающих конкретные факторы обработки, отличные от табличных.
Значение периода стойкости T выбирается, как правило, произвольно в интервале от 15 до 120 мин.
Недостатком подобного определения скорости резания является то, что для конкретной пары материалов заготовка – режущий инструмент эта скорость является величиной случайной и, в большинстве случаев, не оптимальной.
Доктором техн. наук проф. А. Д. Макаровым был открыт закон (положение) постоянства оптимальной температуры резания, из которого можно сделать следующие выводы.
Для инструментов с любой комбинацией геометрических параметров режущей части точкам максимума кривых, характеризующих зависимость интенсивности износа от скорости резания, соответствует одна и та же оптимальная температура резания, хотя уровень оптимальных скоростей резания при этом может колебаться.
Каждому значению подачи соответствует определенная скорость резания Vо, на которой достигается максимальная размерная стойкость инструмента. Она выше скорости резания Vм, соответствующей максимальному периоду общей стойкости, или минимуму скорости размерного износа инструмента.
Снижение скорости резания до значений ниже оптимальной Vо, уменьшает размерную стойкость инструмента и точность отработки, хотя период общей стойкости Т, в отдельных случаях, при этом может быть выше значения оптимального периода стойкости То, наблюдаемого при работе на оптимальной скорости резания Vо. Другими словами, если поддерживать постоянную температуру в зоне резания, определенной для данной пары материалов деталь – режущий инструмент, то различным сочетаниям значений подач и скоростей будут соответствовать различные периоды стойкости при минимальных значениях интенсивности износа инструмента.
Современная техническая литература и нормативы по режимам резания часто ориентируют на более высокие значения периода стойкости T и, тем самым, занижают скорости резания, уменьшая производительность обработки.
Значения скоростей резания не соответствуют значениям скоростей подач, необходимых для поддержания оптимальной
16

температуры в зоне резания. Таким образом нахождение оптимальной скорости резания, а также взаимосвязи между оптимальной скоростью резания и подачей, между оптимальным износом и подачей с помощью параметрических уравнений
V |
c1 |
; h |
с2 |
, |
|
|
|||
o |
s x1 |
оп |
sx2 |
|
|
|
является важной задачей для получения максимальной размерной стойкости инструмента при резании. Следовательно, подобный расчет скорости резания в отличие от принятых, с учетом вышеизложенного, заключается в определении оптимального периода стойкости инструмента To, связанной с величиной подачи оптимальной скорости Vо при характерной для данной пары деталь – инструмент температурой резания.
Такой способ расчета скорости резания позволяет повысить производительность труда за счет сокращения машинного времени, увеличения суммарной стойкости инструмента, количества переустановок инструмента и, тем самым, улучшить техникоэкономические показатели производства.
Получено: |
Воронежский государственный |
20.12.2003 |
технический университет |
УДК 621.9.06. |
|
ЭКОНОМИЧНОСТЬ ОБРАБОТКИ ДЕТАЛЕЙ НА ТОКАРНЫХ СТАНКАХ РАЗЛИЧНЫХ ТИПОВ
Э. М. Янцов, Т. Э. Янцова
При выборе типов токарных станков для обработки сравнительно несложных деталей при величине партий от 1 до 1000 шт. необходим сравнительный расчет стоимости изготовления единицы продукции на каждом из типов станков. При одинаковых технических характеристиках токарные станки имеют различные системы управления и, следовательно, требуют различных расходов на подготовку производства деталей, стоимость обработки единицы продукции или единицы времени работы станка.
17

Можно ориентировочно подсчитать стоимость изготовления единицы продукции С для любого типа станка по формуле
|
Ср |
|
C |
|
С С |
|
|
k |
, |
|
|
|||
е |
k n |
|
n |
|
|
|
где Се – стоимость обработки единицы продукции; Ср – расходы на подготовку производства, отнесенные к единице продукции; Сk – расходы на повторное заключение договора на изготовление; k – число заказов; n – величина партии деталей.
При обработке деталей малыми и средними партиями, как правило, применяется одностаночное обслуживание. При статической оценке составляющих статей расходов можно проследить следующую картину. Большую стоимость обработки единицы продукции имеют универсальные токарные станки, далее токарно-револьверные с ручным управлением, за ними токарные станки с ЧПУ и замыкают этот ряд токарные автоматы с программным управлением (ПУ). Но если сравнить сумму расходов Ср + Сk, или С, то получим следующую очередность: универсальные токарные станки, токарные станки с ЧПУ, токарно-револьверные станки с ручным управлением и токарные автоматы с ПУ. Анализ зависимостей k f (n) для различных типов станков показал
следующее. Кривые изменения пересекаются между собой. Точки пересечения кривых указывают границы экономичных областей использования токарных станков различных типов. Так при единичном производстве деталей или партии до 7 шт. экономически выгодно использование универсальных токарных станков, до 90 шт. целесообразно использовать токарные станки с ЧПУ, при больших партиях – токарные автоматы с ПУ. Примечательно то, что стоимость изготовления деталей на токарно-револьверных станках с ручным управлением больше стоимости изготовления на станках с ЧПУ и ПУ. Только при количестве свыше 60 шт. в партии стоимость обработки становится меньше, чем при изготовлении на универсальном токарном станке. Это еще раз подтверждает высокую эффективность применения станков с ЧПУ в мелкосерийном и серийном производствах и это связано с расходами на подготовку производства. При обработке деталей на станках с ЧПУ эти расходы оказываются меньше, чем при обработке на токарно-револьверных станках с ручным управлением. Эта
18
тенденция сохраняется и при обработке деталей более сложного профиля.
Если время обработки на станке с ПУ приблизительно на 20 % больше времени обработки на станке с кулачковым управлением, то большие партии деталей можно обрабатывать на токарно-револьверных станках. Такое ориентировочное значение разности в машинном времени получается из сопоставления расходов на приобретение этих станков. При этом не учитывались меньшие расходы на перенастройку станка с ПУ с расходами на перенастройку станков с кулачковым управлением, а также расходы на смену инструмента. Токарные автоматы с ПУ имеют более высокий съем металла в единицу времени и постоянное для цикла обработки детали вспомогательное время для любого штучного времени по сравнению с токарно-револьверными станками с ручным управлением. Таким образом, для экономически оправданного применения токарно-револьверных станков с ручным управлением необходима их модернизация.
При обработке деталей партиями до 1000 шт. можно определить эффективность использования разных типов токарных станков. Что касается токарно-револьверных станков с ручным управлением, то их применение в современном производстве, даже на малых предприятиях, малоэффективно.
Получено: |
Воронежский государственный |
20.12.2003 г. |
технический университет |
УДК 681.2 |
|
УНИВЕРСАЛЬНЫЙ ПРОГРАММНЫЙ ИНТЕРФЕЙС, ПРЕДНАЗНАЧЕННЫЙ ДЛЯ ИНТЕГРАЦИИ МЕТАЛЛОРЕЖУЩЕГО ОБОРУДОВАНИЯ С АСУП
Старов В.Н., Муранов В.А
Разработка и внедрение в производство новых конструкций машин, механизмов и приспособлений, соответствующих современному уровню развития науки и техники, возможны при наличии высокопроизводительного станочного парка с
19
автоматизированными системами управления на базе станков с числовым программным управлением (ЧПУ). Для эффективного функционирования такого оборудования необходимо точно и однозначно описывать технологические операции и их параметры, что производится с помощью специальных языков ЧПУ. Их конкретная реализация зависит от реальных возможностей оборудования и СЧПУ. Практика показывает, что существует множество языков, но для корректного управления данными технологических процессов, например, внутри предприятия нам необходимо прийти к единому описанию технологических операций и техпроцесса в целом по отрасли. Идеально – по стране.
Понятие технологического процесса является ключевым при разработке автоматизированной системы технологической подготовки производства (АСТПП). Эффективность деятельности машиностроительного предприятия во многом определяется совершенством реализации и управления технологическим процессом. Следовательно, для того, чтобы построить качественную АСТПП, нам необходимо формализовать технологический процесс, приведя его к определѐнной форме. В этом виде техпроцессы могут быть сохранены в базе данных предприятия для дальнейшей модификации или использования.
Для того, чтобы тот или иной техпроцесс был реализован на конкретном станочном оборудовании, необходимо перевести его на язык соответствующего ЧПУ. При этом моделируемый программный интерфейс должен состоять из следующих подсистем.
1.Автоматизированной визуальной системы разработки техпроцессов
2.Системы анализа техпроцессов и выбора подходящего оборудования из имеющегося в наличии
3.Трансляторов полученных формализованных техпроцессов для конкретных реализаций ЧПУ
Укажем некоторые особенности, которые следует учитывать при создании объектов АСТПП. Например, выберем процесс механообработки, при этом примем следующее допущение: проектируемый нами интерфейс обслуживает только механическую обработку заготовок, полученных литьѐм и другими способами, и, возможно, подвергшихся термообработке различными методами. Процесс сборки также не берѐтся в расчѐт. Таким образом, в поле
20
внимания отсутствуют составные детали, полученные сваркой, пайкой и т.п.
В базовых технологических операциях и выделим ряд параметров, однозначно описывающих каждую типовую операцию резания. Также выявим их описательные различия с точки зрения физико-механических явлений и требований к состоянию полученной эксплуатационной поверхности. Выберем требуемые средства, необходимые для поддержки системы контроля качества. Для описания в конкретном примере мы выбрали следующие операции: точение, строгание, долбление, сверление, рассверливание, зенкерование, развѐртывание, фрезерование, разрезание, резьбонарезание, протягивание, шлифование, при этом, например, для операций сверления, рассверливания, зенкерования и развѐртывания (ввиду их сходства) мы получили следующее единое формализованное описание. Результирующая объѐмная фигура V - цилиндр с диаметром D прямой или скошенный в зависимости от угла α входа инструмента. Инструмент – сверло, зенкер, развѐртка (в формализованном виде представлены кодом). Параметры качества – погрешности объѐмной фигуры резания ΔD и угла Δα. Элементы режима резания: глубина резания t, подача s, скорость резания v, крутящий момент M, мощность резания N. Эти параметры наряду с типом операции заносятся в формализованное описание техпроцесса. Операции резания предшествует операция позиционирования, которая также должна быть формализована и записана в описание техпроцесса, и так далее.
Таким образом, построили схему формализации некоторого множества технологических операций. Разработали программную систему визуального проектирования техпроцессов, с помощью которой в виде схем нотации STEP возможно наглядно построить техпроцесс как совокупность конкретных технологических операций.
Следующая часть программного интерфейса «компьютер – ЧПУ станков» – это система принятия решений, подбирающая и рекомендующая конкретное оборудование для того или иного техпроцесса. Она взвешивает множество факторов и выбирает то рациональное оборудование и маршрут выполнения конкретного техпроцесса, при котором ТП наиболее эффективен как по экономическим так и по технологическим соображениям.
21
Завершающей частью интерфейса является транслятор, способный «перевести» техпроцесс с формализованного языка на язык конкретного ЧПУ. При этом для каждого типового ЧПУ пишется отдельный транслятор. Система принятия решений управляет работой транслятора.
Предложенный программный интерфейс позволяет интегрировать ЧПУ металлорежущего оборудования в систему управления предприятием, предоставляя также широкие возможности для проектирования типовых техпроцессов, не привязанных к конкретному виду ЧПУ и оборудованию.
Получено |
Воронежский государственный |
12.12.2003 |
технический университет |
УДК 621.78 |
|
ИССЛЕДОВАНИЕ КИНЕТИКИ СТАРЕНИЯ ЖАРОПРОЧНЫХ СПЛАВОВ
А.Н. Осинцев, В.И. Корнеев
В авиастроении, химии, энергетике и целом ряде других областей современной техники жаропрочные сплавы типа нихром с добавками титана и алюминия прочно вошли в число основных конструкционных материалов при изготовлении наиболее ответственных деталей, работающих при высоких температурах.
Углубление представлений об особенностях природы тонких кристаллоструктурных превращений, протекающих в этой группе сплавов в процессе термической обработки и в условиях длительной эксплуатации, чрезвычайно важно для развития теории жаропрочности, базируясь на которой возможно дальнейшее увеличение долговечности и эксплуатационной надежности деталей машин путем совершенствования сплавов, уточнения конструктивных расчетов и разработки наиболее рациональных технологических процессов.
Неослабевающий уже более 50 лет практический интерес к жаропрочным сплавам на основе никеля обусловил появление значительного количества теоретических и экспериментальных
22