
2890
.pdf
работ, посвященных изучению фазовых и структурных превращений и их взаимосвязи с прочностными характеристиками.
Несмотря на обширность имеющихся экспериментальных данных многие детали кинетики кристаллоструктурных превращений, сопровождающих распад пересыщенного твердого раствора, изучены недостаточно. Данные ряда работ не согласуются между собой. Возникают серьезные затруднения при попытках объяснения природы упрочнения и разупрочнения, связанных, согласно представлениям, развиваемым школой академика Г. В. Курдюмова, с изменениями тонкой структурной неоднородности.
Это обусловлено, прежде всего, чрезвычайной сложностью механизма распада пересыщенного твердого раствора. Здесь, повидимому, весьма незначительные изменения тонкой структурной неоднородности, возникающей в матрице еще на самых начальных стадиях выделения частиц второй фазы и одновременно предопределяющей прочностные характеристики сплава, часто лежат за пределами чувствительности экспериментальных методик.
Известно, что распад пересыщенного твердого раствора в сплавах на основе никеля связан с образованием так называемой моделированной структуры некоторого количества фазы выделения в виде частичек субмикроскопических размеров.
Для получения рентгенограммы с достаточно четкими интерференционным отражениями от решетки фазы выделения, ее предварительно электролитически выделяют в чистом виде, поскольку слабые отражения от решетки '-фазы на рентгенограммах с монолитных поликристаллических образцов обычно завуалированы флуктуациями фона. То же самое происходит с сателлитными отражениями от модулированной структуры, надежное выявление которых считается практически возможным только при исследовании монокристальных образцов.
Трудность приготовления и термической обработки монокристальных образцов, а так же сравнительно высокая трудоемкость их последующего рентгенографирования служат нередко препятствием для более детального исследования, анализ результатов которого возможен не по отрывочным данным, где порой весьма затруднительно выявить ошибки опыта, а по кинетическим кривым. Кроме того, рентгенографическое изучение стареющих сплавов значительно затруднено из-за их грубо-зернистости.
23

Все это приводит к необходимости дальнейшего совершенствования экспериментальных методик, разработки новых камер, приспособленных для экспрессного рентгенографирования плоских грубозернистых поликристаллических образцов с высокой степенью постоянства геометрии съемки в условиях серийного проведения опытов, а также расширения возможностей и повышения производительности фотометрирующей аппаратуры.
На основании изучения начальных стадий распада пересыщенного твердого раствора в ряде сплавов на основе никеля и меди установлено образование модулированной структуры, где период решетки в областях субмикроскопических размеров изменяется с некоторой статистической периодичностью.
Геометрически подобные структуры принято характеризовать периодом модуляции, определяемым по величине угла между сателлитным и основным отражениями с помощью формул Даниэля
—Липсона или Вильсона.
Всплавах никель-хром-титан-алюминий на начальных стадиях старения также обнаружена модулированная структура. Возникновение этой структурной неоднородности и возможные ее изменения в процессе образования и роста частиц фазы выделения, вероятно, сказываются на прочностных характеристиках сплава. Однако отсутствие сведений о характере изменений модулированной структуры в зависимости от температуры и длительности старения исключает возможность установить, хотя бы качественно, степень ее влияния на упрочение сплава.
Исследованиями Ю. А. Багаряцкого и Ю. Д. Тяпкина, М. В. Приданцева и Л. Н. Зиминой установлено, что в сплавах на основе
никеля, где равновесной фазой выделения является -фаза, как и в сплавах с фазой выделения, изоморфной матрице, распад пересыщенного твердого раствора начинается образованием субмикроскопических областей с упорядоченной структурой по типу Ni3Al . На их базе затем образуются частички '-фазы.
В сплавах никель-титан, никель-хром-титан и никель-хром- титан-алюминий распад пересыщенного твердого раствора осуществляется в две стадии. Сначала выделяется метастабильная фаза, близкая по химическому составу к интерметаллиду Ni3Ti , в котором часть атомов титана замещена атомами алюминия. На более поздних стадиях распада она перерождается в стабильную -фазу с гексагональной решеткой. Ведущим процессом при фазовом
24

переходе '→ предполагается диффузионное перемещение атомов.
С другой стороны, известно, что в процессе длительного старения сплавов типа нихром с добавками титана и алюминия возможна коагуляция частиц фазы выделения. Коагуляцию частиц '-фазы даже принято считать ответственной за разупрочнение сплавов, поскольку она нарушает тот оптимум структурной неоднородности, благодаря которому элементарные акты пластической деформации в кристаллах твердого раствора воз-
никали и затухали на минимально коротких расстояниях.
Отсюда можно предполагать, что превращение метастабильной фазы в стабильную органически связано с процессом коагуляции частиц начинается он образованием частиц метастабильной фазы изоморфной матрице, которая затем на более поздних стадиях старения превращается в стабильную -фазу.
Получено: 15.12.2003 |
Воронежский государственный |
|
технический университет |
УДК 621.7.011 |
|
МАТЕМАТИЧЕСКОЕ МОДЕЛИРОВАНИЕ ШЕРОХОВАТОСТИ ПОВЕРХНОСТИ ЗАГОТОВКИ,
ОБРАБОТАННОЙ ДЕФОРМИРУЮЩИМ ПРОТЯГИВАНИЕМ
Е.А. Балаганская
Представлена математическая модель для определения шероховатости поверхностного слоя при многоцикловом деформирующем протягивании трубных заготовок.
Теоретическое решение такой задачи как расчет Rz в
зависимости от параметров технологического процесса – является весьма сложным и, прежде всего, из-за большого числа влияющих факторов и сложности явлений в зоне контакта инструмента с заготовкой. Из опробованных теоретических решений можно отметить модели представленные в работах /1, 3, 4, 8/. Все они не учитывают упрочнение микровыступов.
25
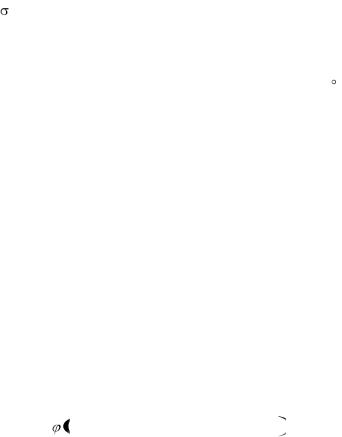
Эксперименты и существующий теоретический анализ показывают, что форма микрорельефа поверхности изделия зависит не только от ―текущего‖ значения параметров контактного взаимодействия, но и от всей предыдущей истории процесса воздействия инструмента на поверхность заготовки.
Анализ истории контактного взаимодействия инструмента с заготовкой позволяет выделить доминирующий обобщающий фактор, непосредственно влияющий на процесс формирования микрорельефа обработанной поверхности – работу сил трения Aтр .
Другой фактор известен – это или фактическое контактное
напряжение |
n , или осредненная по всей номинальной контактной |
|
поверхности |
величина - контактное давление |
q . Скорость |
деформирующего протягивания небольшая (менее 0,1 м/с), поэтому условия протекания данного процесса от нее практически не зависят. Температура в контактной зоне невысокая, не более 100 , и процесс деформирования происходит в холодных условиях /7/.
Но даже для таких стабильных условий деформирующего протягивания построить чисто теоретическую модель для расчета Rz обработанной поверхности невозможно из-за сложности
комплекса явлений контактного трения. Как показывает опыт исследования таких многофакторных явлений в физике и механике, наилучшие результаты в этом случае дают методы теории размерностей и подобия /5/. С их помощью на основании выявленных основных влияющих факторов анализируются экспериментальные данные, а затем на основе выявленных закономерностей строят расчетные схемы. Применим такой подход и для изучения явления формирования микрорельефа поверхности, обрабатываемой деформирующим протягиванием.
Полагаем, что текущее значение Rz зависит от начальной Rzo , от максимального за всю историю процесса контактного давления (вызывающего смятие микровыступов) и, как показано выше, от работы сил трения Aтр ( вызывающей как дополнительное смятие
микронеровностей так и массоперенос их материала), то есть:
Rz Rzo ; qmax ; Атр ; материал заготовки .
Материал инструмента рассматривается как идеально жесткий, и по отношению к заготовке идеально гладкий, т.к. его
26
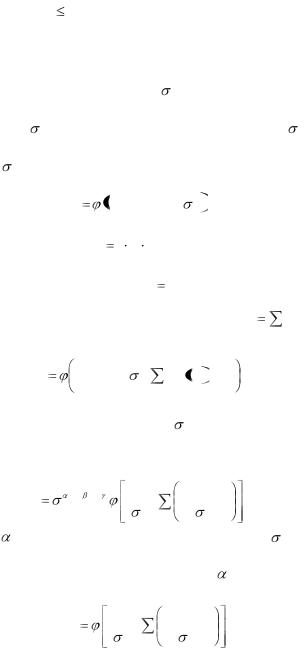
шероховатость Rz 0.4 мкм /7/. Взаимодействие инструмента с материалом заготовки при заданных технологических условиях определяется коэффициентом трения f (влияющим на Aтр ) и
степенью упрочнения материала микровыступов, т.е. возникающей в нем интенсивностью напряжений о . Из решения задачи теории пластичности о смятии клина и из экспериментальных данных /6/ известно, что о прямо пропорционально величине n . Из этих работ также известно, что при значительных степенях смятия
величина |
n |
остается |
постоянной и зависящей, в основном, от |
|
|
|
|
|
|
материала заготовки. Тогда можно записать, что |
|
|||
|
|
Rz |
Rzo ; qmax ; Атр ; n . |
(1) |
Рассмотрим поверхность заготовки единичной площади. Сила |
||||
трения на |
ней равна: |
Fтр 1 f q , где q есть текущее |
значение |
среднего контактного давления. Работа этой силы за один цикл
деформирующего протягивания Атр |
|
f q l , где l |
– длина пути трения. |
||||||||||||||
|
|
|
|
|
|
|
|
|
|
|
|
|
|
|
|
N |
|
Если обработка осуществляется за N циклов, то Атр |
fi qi li . |
||||||||||||||||
|
|
|
|
|
|
|
|
|
|
|
|
|
|
|
|
1 |
|
Тогда |
|
|
|
|
|
|
|
|
|
|
|
|
|
|
|
|
|
|
|
|
|
|
|
|
|
|
N |
|
|
|
|
|
|
|
|
|
Rz |
|
Rzo; qmax ; n ; |
|
fi ; |
qi ; qi ;li |
|
(2) |
|||||||||
|
|
|
|
|
|
|
|
|
1 |
|
|
|
|
|
|
|
|
В соответствии с принципами теории подобия выбираем |
|||||||||||||||||
новые независимые параметры: Rzo , |
n |
|
и do - внутренний диаметр |
||||||||||||||
заготовки. Причем Rz |
будем измерять в Rzo , а ширину контакта l - |
||||||||||||||||
в долях от |
do . |
Тогда, |
переходя |
к |
|
безразмерным |
величинам, |
||||||||||
|
|
|
|
|
|
|
|
qmax |
N |
|
|
qi |
|
li |
|
|
|
получаем |
R |
|
|
R |
|
d |
|
; |
f |
|
|
, где |
показатели |
||||
z |
n |
zo |
o |
i |
|
do |
|||||||||||
|
|
|
|
|
|
|
|
|
|||||||||
|
|
|
|
|
|
|
|
n |
1 |
|
|
n |
|
|
|
степеней , и
независимых параметров n , Rzo
выбираются такими, чтобы размерности правой и левой частей зависимости были одинаковыми, т.е., например, ==0;
=1.
Тогда
и do данной
Rz |
|
qmax |
N |
|
|
qi |
|
li |
|
|
|
; |
f |
|
|
. |
(3) |
||||
Rzo |
|
i |
|
do |
||||||
|
|
|
|
|
|
|
||||
|
n 1 |
|
|
n |
|
|
|
27

|
qmax |
|
N |
|
qi |
|
li |
|
Но величина |
уже входит в выражение |
f |
|
|
. |
|||
|
i |
|
||||||
|
|
|
|
|
do |
|||
|
n |
1 |
|
n |
|
Поэтому функциональную зависимость (3) можно представить как:
Rz |
N |
qi li |
|
fi |
|
|
|
. |
(4) |
Rzo |
|
|
||||
1 |
n do |
|
Таким образом, при принятых выше допущениях следует, что при обработке заготовок из различных материалов, экспериментальные данные должны соответствовать единой универсальной
зависимости (4): |
Rz |
, |
где |
|
|
Rzo |
|
||||
|
1 |
|
|
||
|
|
N |
|
||
|
|
|
|
fi qili , |
(5) |
|
|
|
n do |
||
|
|
|
1 |
|
есть безразмерный критерий подобия для процесса формирования микрорельефа при деформирующем протягивании.
|
Если при многоцикловой обработке li |
const , а за fi |
можно |
|||||||||||||||||||||
принять некоторое среднее значение |
f , то получаем: |
|
|
|||||||||||||||||||||
|
|
|
|
|
|
Rz |
|
|
|
f l |
|
qi |
|
|
1 |
|
qi . |
|
|
|
|
|||
|
|
|
|
|
|
Rzo |
|
|
do n |
|
1 |
|
|
|
|
|
|
|
||||||
|
|
|
|
|
|
|
|
|
|
|
|
n |
|
|
|
|
|
|
|
|||||
|
Если при этом обрабатываются |
заготовки из одного мате- |
||||||||||||||||||||||
риала, то |
|
|
|
|
|
|
|
|
|
|
|
|
|
|
|
|
|
|
|
|
|
|
||
|
|
|
|
|
|
|
|
|
|
Rz |
|
|
qi . |
|
|
|
|
|
|
|
|
|
(6) |
|
|
|
|
|
|
|
|
|
|
|
2 |
|
|
|
|
|
|
|
|
|
|
||||
|
|
|
|
|
|
|
|
|
Rzo |
|
|
|
|
|
|
|
|
|
|
|
|
|||
|
Если q выразить через технологическое усилие протягивания |
|||||||||||||||||||||||
Q |
/7/, а |
ширину |
контакта |
li |
через |
натяг |
на |
деформирующий |
||||||||||||||||
элемент |
ai , то |
критерий |
подобия |
рассчитывается |
как: |
|||||||||||||||||||
|
|
fi |
ai |
Q |
|
|
|
|
|
|
|
|
|
|
|
|
|
|
|
|
|
|
||
|
|
|
|
|
|
|
|
|
|
|
|
|
|
|
|
|
|
|
|
|
|
|||
|
|
fi |
|
i |
|
|
|
|
|
|
|
|
|
|
|
|
|
|
|
|
|
|
||
|
|
|
|
, |
|
где |
- |
угол |
конусности |
деформирующего |
||||||||||||||
1 |
|
d 2 |
|
|
||||||||||||||||||||
|
n |
|
|
|
|
|
|
|
|
|
|
|
|
|
|
|
|
|
|
|||||
|
|
o |
|
|
|
|
|
|
|
|
|
|
|
|
|
|
|
|
|
|
||||
элемента. Поскольку при деформирующем протягивании |
=4 |
- 5 , |
||||||||||||||||||||||
то принимая для стабильных условий обработки f |
const |
получаем |
||||||||||||||||||||||
простой технологический критерий подобия |
|
|
|
Qi ai |
. |
|
|
|||||||||||||||||
2 |
|
|
|
|
|
|||||||||||||||||||
|
|
|
|
|
|
|
|
|
|
|
|
|
|
|
|
|
|
|
d 2 |
|
|
|||
|
|
|
|
|
|
|
|
|
|
|
|
|
|
|
|
|
|
|
|
|
o n |
|
|
28

Для экспериментальной проверки предложенной модели были проведены многочисленные эксперименты по многоцикловому деформирующему протягиванию втулок из сталей: 10, Ст3, 45, Х18Н10Т, У8 и из меди инструментами из ВК15 и с покрытиями TiN и CrN. Все экспериментальные данные получали по методикам, изложенным в /7/. Кривая (см. рисунок) строилась для различных, безразмерных параметров. Как видно, выдвинутые теоретические положения удовлетворительно подтверждаются экспериментальными данными.
|
|
Рис. 1. Зависимость относи- |
|
||||
|
|
тельной |
|
шероховатости |
|
||
|
|
обработанной |
поверхности |
от |
|
||
|
|
безразмерных |
|
параметров |
|
||
|
|
технологического процесса (угол |
|
||||
|
|
конусности |
5о, |
смазка |
– |
|
|
|
|
сульфофрезол, натяг–0,2 мм на |
|
||||
|
|
проход) при протягивании втулок |
|
||||
|
|
из стали |
10, |
стали |
45, стали |
|
|
|
|
Х18Н10Т, стали У8 |
|
|
|
||
|
|
|
|
|
|
|
|
Таким |
образом, |
предложен |
теоретический |
метод |
определения величины шероховатости, учитывающий всю совокупность технологических факторов. Он может быть рекомендован как для дальнейших исследований механики поверхностного пластического деформирования, так и при проектировании технологических расчетов.
Литература:
1.Крагельский И. В. Основы расчетов на трение и износ. М.: Машиностроение, 1977. 526 с.
2.Хусу А. П., Витенберг Ю. Р., Пальмов В. А. Шероховатость поверхностей, теоретико-вероятностный подход. М.: Наука, 1975. 343 с.
3.Проскуряков Ю. Г. Технология упрочняюще-калибрующей и формообразующей обработки металлов. М.: Машиностроение, 1971. 208 с.
4.Макушок Е.М. Механика трения. Под ред. акад. В. П. Северденко. Минск, «Наука и техника», 1974. 254 с.
29
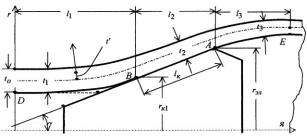
5.Седов Л. И. Методы подобия и размерности в механике. М.: Наука, 1972. 440 с.
6.Определение шероховатостей поверхности обрабатываемой детали при деформирующем протягивании / Балаганская Е. А., Цеханов Ю. А., Шейкин С. Е., Воронеж. гос. агр. ун-т.- Воронеж, 1997. Деп. В ВИНИТИ 29.09.97, N2930-В97.
7.Розенберг О. А. Механика взаимодействия инструмента с изделием при деформирующем протягивании. Киев, Наукова думка, 1981. 283 с.
8.Акаро В. Л. Контактное трение и изнашивание микрорельефа гравюр кузнечных штампов // Кузнечно-штамповочное производство, 1989,- №8,- С.13-16.
Получено |
Воронежский государственный |
14.11.2003 г. |
технический университет |
УДК 621.7.011 |
|
МАТЕМАТИЧЕСКИЙ АНАЛИЗ ЭНЕРГЕТИЧЕСКИХ ПАРАМЕТРОВ ОЧАГА ДЕФОРМАЦИИ ПРИ ДЕФОРМИРУЮЩЕМ ПРОТЯГИВАНИИ
Балаганская Е.А.
Предложена методика проведения анализа энергетических параметров очага деформирования при деформирующем протягивании трубных заготовок с небольшой толстостенностью, и даны пути снижения энергозатрат.
Для решения поставленной задачи была разработана математическая модель очага пластических деформаций при деформирующем протягивании (ДП) заготовок с небольшой толстостенностью, когда их напряженнодеформированное состояние можно описать с помощью моментной теории оболочек /1/. Схема очага деформации и соответствующие ей основные геометрические и кинематические параметры приведены на рис.1. Очаг состоит из трех зон: контактной (2-я зона) и двух внеконтактных (1-я и 3-я).
Рис.1. Расчетная схема очага пластических деформаций
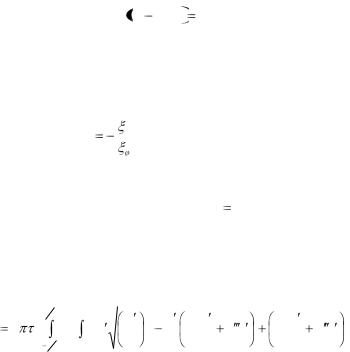
Полный функционал мощности W внешних и внутренних сил в соответствии с известными вариационными принципами теории
деформируемого твердого пластического тела /2/ равен: |
|
W QV3 min , |
(1) |
Q – сила протягивания, V3 - скорость течения материала в конце
очага деформации. Величина W равна сумме мощностей каждого из отдельных участков.
Обозначим для срединной поверхности заготовки через K отношение скорости осевой деформации к скорости окружной
деформации: |
K |
zo |
. |
|
(2) |
|
|
||||
|
|
o |
|
|
|
В пределах каждого участка эта величина |
имеет свое |
||||
постоянное значение: K1 , K 2 , K3 . Геометрию срединной |
|||||
поверхности |
внеконтактных зон r |
f (z) опишем |
с помощью |
полиномов четвертой степени, которые учитывают граничные условия, как всего процесса, так и условия кинематического сопряжения на границах участков /1/. Согласно этой работе полная мощность пластических деформаций в пределах каждого участка определяется выражением (рис.1):
|
t |
l |
|
|
|
|
2 |
|
|
|
|
2 |
|
|
||
|
2 |
|
|
|
r |
|
r |
|
r |
|
|
r |
|
|
|
|
W 4 |
|
dt |
V |
r |
|
K |
r t |
K |
r t dz . |
(3) |
||||||
s |
|
|
|
|
|
|||||||||||
|
1 |
z |
|
|
r |
|
r |
|
r |
|
r |
|
||||
|
t 2 |
0 |
|
|
|
|
|
|
|
|||||||
Изменение скорости осевого течения Vz и толщины стенки |
||||||||||||||||
заготовки t |
определяется из условия несжимаемости и условия |
|||||||||||||||
неразрывности деформаций. |
|
|
|
|
|
|
|
|
|
Пять независимых параметров: K1 , K 2 , K3 , l1 , l3 - являются
варьируемыми параметрами, которые должны обеспечить в рассматриваемой модели минимум полной мощности.
Основные выражения для каждого участка имеют вид: 1-й участок внеконтактных деформаций DB :
31

|
|
|
|
|
|
|
|
|
|
|
|
|
|
|
|
|
|
|
|
|
|
|
|
|
|
|
|
|
|
|
K l1 |
r |
dz |
|
|
|
|
|
|
|
|
|
K |
|
l1 |
r |
dz |
|
|||||
|
|
|
|
|
|
|
|
|
|
|
|
|
|
|
|
|
|
|
|
|
|
|
|
|
|
|
|
|
|
|
1 |
|
|
|
|
|
|
|
|
|
|
|
|
|
|
|
1 |
1 |
|
|
r |
|
|
r rср |
3 tg |
|
|
z |
2 |
|
|
|
|
tg |
z |
4 |
, Vz |
|
|
|
|
Vzo e |
0 r |
|
|
, t1к |
to e |
|
0 |
|
; |
||||||||||||||||||||||||||
|
|
|
|
|
|
|
|
|
|
|
|
|
|
|
|
|
|
|
|
|
|
|
|
|
|
|
|
|
|
|
|||||||||||||||||||||||
4 l |
|
|
|
|
|
|
|
|
8l 3 |
|
|
|
|
|
|
|
|
|
|
|
|
|
|
|
|
||||||||||||||||||||||||||||
|
|
1 |
|
|
|
|
|
|
|
|
1 |
|
|
|
|
|
|
|
|
|
|
|
|
|
|
|
|
|
|
|
|
|
|
|
|
|
|
|
|
|
|
|
|
|
|
|
|
|
|
||||
|
2-й |
|
|
контактный |
|
|
|
|
|
участок |
|
|
|
ВА: |
|
|
|
|
r |
|
r |
|
|
|
5 |
tg |
l , |
||||||||||||||||||||||||||
|
|
|
|
|
|
|
|
|
|
|
|
|
|
|
|
||||||||||||||||||||||||||||||||||||||
|
|
|
|
|
|
|
|
|
|
|
|
|
|
|
|
|
|
|
|
|
|
|
|
|
|
|
|
|
|
|
|
|
|
|
|
|
|
|
|
|
|
к |
|
|
ср |
|
8 |
|
|
|
1 |
||
|
|
|
|
|
|
|
|
|
|
|
|
|
|
|
|
|
|
|
|
|
|
|
|
|
|
|
|
|
|
|
|
|
|
|
|
|
|
|
|
|
|
|
|
|
|
|
|
|
|
|
|
||
|
|
|
|
l |
|
|
|
|
|
|
|
K |
1 |
l |
l |
2 |
|
|
|
|
|
|
K2 |
|
|
|
|
|
l |
|
|
|
|
K 1 |
l |
|
l |
21 |
|
|
|
|
K2 1 |
|
|||||||||
|
|
|
|
|
|
|
|
|
|
|
|
|
1 |
|
|
|
|
|
|
|
|
|
|
|
|
|
|
|
|
|
|
|
|
|
1 |
1 |
|
|
|
|
|
|
|
|
|||||||||
|
|
1 |
|
r |
dz |
|
|
|
|
|
|
|
|
|
|
|
r |
|
dz |
|
|
|
|
|
|
|
|
|
|
|
|
|
1 |
r |
dz |
|
|
|
|
|
|
r |
dz |
|
|
|
|
||||||
|
|
|
|
|
|
|
|
|
|
|
|
|
|
|
|
|
|
r |
|
|
|
|
|
|
|
|
|
|
|
|
|
|
|
|
|
|
|
|
|
|
r |
|
|
|
|
||||||||
Vz 2 |
Vo e 0 r |
|
|
|
|
|
|
|
e l1 |
|
|
|
|
|
|
|
|
|
, tк 2 |
to e 0 r |
|
|
|
|
|
e |
|
l1 |
|
|
|
|
|
|
|
||||||||||||||||||
|
|
|
|
|
|
|
|
|
|
|
|
|
|
|
|
|
|
|
|
|
|
|
|
|
|
|
|
|
|
; |
|||||||||||||||||||||||
|
3-й внеконтактный участок АЕ: |
|
|
|
|
|
|
|
|
|
|
|
|
|
|
|
|
|
|
|
|
|
|
|
|||||||||||||||||||||||||||||
r |
r |
|
tg |
|
|
|
|
tg |
|
z3 |
|
|
tg |
|
z |
4 |
, |
|
|
|
|
|
|
|
|
|
|
|
|
|
|
|
|
|
|
|
|
|
|
|
|
|
|||||||||||
|
|
|
|
|
|
2l 2 |
|
|
8l 3 |
|
|
|
|
|
|
|
|
|
|
|
|
|
|
|
|
|
|
|
|
|
|
|
|
|
|
||||||||||||||||||
3 |
ср3 |
|
|
|
|
|
|
|
|
3 |
|
|
|
|
|
3 |
|
|
|
|
|
|
|
|
|
|
|
|
|
|
|
|
|
|
|
|
|
|
|
|
|
|
|||||||||||
|
|
|
|
|
|
|
|
|
|
3 |
|
|
|
|
|
3 |
|
|
|
|
|
|
|
|
|
|
|
|
|
|
|
|
|
|
|
|
|
|
|
|
|
|
|
|
|
|
|
||||||
|
|
|
|
|
|
K l1 |
r |
dz |
|
K2 l1 l2 |
r |
|
dz |
|
K3 l1 l2 l3 |
r |
dz |
|
|
|
|
|
|
|
|
|
|
|
|
|
|
|
|
|
|
||||||||||||||||||
|
|
|
|
|
|
|
|
|
|
|
|
|
|
|
|
|
|
|
|
|
|
|
|
|
|
|
|
|
|
||||||||||||||||||||||||
|
|
|
|
|
1 |
|
|
r |
|
|
|
|
|
|
|
|
r |
|
|
|
|
|
|
|
|
|
r |
|
|
|
|
|
|
|
|
|
|
|
|
|
|
|
|
|
|
|
|||||||
Vz 3 |
Vo e |
|
|
|
|
|
|
e |
|
|
|
|
|
|
|
|
|
|
e |
|
|
|
|
, |
|
|
|
|
|
|
|
|
|
|
|
|
|
|
|
|
|||||||||||||
|
|
|
0 |
|
|
|
|
|
l1 |
|
|
|
|
|
l1 |
l2 |
|
|
|
|
|
|
|
|
|
|
|
|
|
|
|
|
|
|
|||||||||||||||||||
|
|
|
|
|
|
|
|
|
|
|
|
|
|
|
|
|
|
|
|
|
|
|
|
|
|
|
|
|
|
|
|
|
|
|
|
|
|
|
|
|
|||||||||||||
|
|
|
|
|
|
|
|
l |
|
|
|
|
|
|
|
|
|
|
|
|
l1 |
|
l |
2 |
|
|
|
|
|
|
|
l |
l |
2 |
l |
3 |
|
|
|
|
|
|
|
|
|
|
|
|
|
|
|
||
|
|
|
|
|
|
|
|
|
|
|
|
|
|
|
|
|
|
|
|
|
|
|
|
|
|
|
|
1 |
|
|
|
|
|
|
|
|
|
|
|
|
|
|
|
|
|
||||||||
|
|
|
|
K 1 |
1 |
r |
dz |
K2 1 |
|
|
|
|
r |
dz |
K3 1 |
|
|
|
|
r |
dz |
|
|
|
|
|
|
|
|
|
|
|
|||||||||||||||||||||
|
|
|
|
|
|
|
|
|
|
|
|
|
|
|
|
|
|
|
|
|
|
|
|
|
|
|
|
||||||||||||||||||||||||||
|
|
|
|
|
|
|
|
|
|
|
|
|
|
|
|
|
|
|
|
|
|
|
|||||||||||||||||||||||||||||||
|
|
|
|
|
1 |
|
|
|
|
r |
|
|
|
|
|
|
|
|
|
|
|
|
|
r |
|
|
|
|
|
|
|
|
|
r |
|
|
|
|
|
|
|
|
|
|
|
|
|
||||||
t3 |
to e |
|
|
|
|
|
|
|
e |
|
|
|
|
|
|
l1 |
|
|
e |
|
|
|
|
l1 l2 |
|
. |
|
|
|
|
|
|
|
|
|
|
|
||||||||||||||||
|
|
|
0 |
|
|
|
|
|
|
|
|
|
|
|
|
|
|
|
|
|
|
|
|
|
|
|
|
|
|
|
|
|
|
|
|||||||||||||||||||
|
|
|
|
|
|
|
|
|
|
|
|
|
|
|
|
|
|
|
|
|
|
|
|
|
|
|
|
|
|
|
|
|
|
|
|
|
|
|
|
|
|
|
|
||||||||||
|
Расчет по разработанной модели осуществлялся с помощью |
||||||||||||||||||||||||||||||||||||||||||||||||||||
метода последовательных приближений. |
|
|
|
|
|
|
|
|
|
|
|
|
|
|
|
|
|
|
|
||||||||||||||||||||||||||||||||||
|
По окончании итерационного |
процесса |
рассчитывали силу |
||||||||||||||||||||||||||||||||||||||||||||||||||
трения |
по |
известной |
|
/4/ |
|
|
зависимости: |
|
|
Fтр |
|
|
|
|
Q f |
|
|
|
|
|
и |
||||||||||||||||||||||||||||||||
|
|
|
|
|
|
|
|
|
|
|
|
|
|
|
|
|
|||||||||||||||||||||||||||||||||||||
|
|
|
|
|
|
f |
cos |
|
|
sin |
|||||||||||||||||||||||||||||||||||||||||||
|
|
|
|
|
|
|
|
|
|
|
|
|
|
|
|
|
|
|
|
|
|
|
|
|
|
|
|
|
|
|
|
|
|
|
|
|
|
|
|
|
|
|
|
|
|||||||||
среднее |
|
|
|
|
|
|
|
контактное |
|
|
|
|
|
|
|
касательное |
|
|
|
|
напряжение: |
||||||||||||||||||||||||||||||||
|
Q f cos |
|
|
|
|
|
|
|
|
|
|
|
|
|
|
|
|
|
|
|
|
|
|
|
|
|
|
, |
|
|
|
где |
|
|
f – |
коэффициент |
|||||||||||||||||
n |
|
|
|
|
|
|
|
|
rк1 |
|
rэ |
l2 |
|
|
f cos |
|
|
|
sin |
|
|
|
|
|
|||||||||||||||||||||||||||||
|
|
|
|
|
|
|
|
|
|
|
|
|
|
|
|
|
|
|
|
|
|
|
|
|
|
|
|
|
|
|
|
|
|
|
|
|
|||||||||||||||||
|
|
|
|
|
|
|
|
|
|
|
|
|
|
|
|
|
|
|
|
|
|
|
|
|
|
|
|
|
|
|
|
|
|
|
|
|
|
|
|
|
|
|
|
|
|
|
|
|
|
|
|
|
|
трения, |
а |
|
|
|
|
|
- |
|
|
угол |
|
|
наклона |
образующей |
|
рабочего |
конуса |
||||||||||||||||||||||||||||||||||||
инструмента. |
|
|
|
|
|
|
|
|
|
|
|
|
|
|
|
|
|
|
|
|
|
|
|
|
|
|
|
|
|
|
|
|
|
|
|
|
|
|
|
|
|
|
|
|
|
|
|||||||
|
После этого осуществляется итерация по минимизации более |
||||||||||||||||||||||||||||||||||||||||||||||||||||
полного |
функционала |
|
с |
|
фиксированными |
внешней |
|
силой |
|
|
Q |
и |
заданными силами трения по заданной площади контакта, протяженностью lк . По результатам последней итерации
определяются искомые основные и производные параметры: l1 , l3 ,
K1 , K2 , K3 , l2 , lк , W1 , W2 , W3 , Wтр , W .
Разработанная модель дала возможность проанализировать энергетику процесса. Общая мощность, затраченная на
32