
2890
.pdfВозрастая с ростом его толщины, остаточные напряжения могут приводить к отслоению покрытия, его растрескиванию или существенному снижению работоспособности. Опыт нанесения и эксплуатации газотермических покрытий показывает на многочисленные примеры отрицательного проявления остаточных растягивающих напряжений /12/.
Все основные факторы процесса ПНПМ можно представить в виде следующих основных групп /3, 10, 11/:
1)конструктивные и энергетические факторы, определяющие условия образования плазменной струи: конструкция плазмотрона; длина и диаметр канала сопла плазмотрона; сила тока и напряжение питания плазмотрона; вид плазмообразующего газа и его расход;
2)факторы, определяющие условия подачи порошка в плазменную струю: расход наплавляемого порошка; расход транспортирующего газа; угол подачи порошка и расстояние от места его ввода в плазменную струю до среза сопла плазмотрона;
3)факторы, определяющие условия наплавки: дистанция наплавки; угол наклона плазмотрона по отношению к наплавляемой поверхности; скорость относительного перемещения плазмотрона относительно детали; вид защитного газа и его расход;
4)факторы, определяющие свойства наплавляемого порошка: химический состав порошка; форма частиц порошка и их размеры; сыпучесть, влажность, теплопроводность, температура плавления порошка; температура предварительного подогрева порошка;
5)толщина покрытия.
Основными характеристиками восстановленных поверхностей деталей КТО, определяющими их работоспособность, являются адгезионная прочность, твердость и износостойкость нанесенного слоя материала /13/. По данным работ /1, 2, 4/ из всего многообразия факторов, определяющих свойства плазменных покрытий, на адгезионную прочность, твердость и износостойкость материала, нанесенного методом ПНПМ, наиболее значимое влияние оказывают мощность плазмотрона, расход наплавляемого порошка, дистанция наплавки и толщина покрытия.
Литература:
1. Кудинов В.В. Плазменные покрытия. М.: Наука, 1977.
184 с.
103
2. Нанесение покрытий плазмой / В.В. Кудинов, П.Ю. Пекшев, В.Е. Белащенко и др. М.: Наука, 1990. 408 с.
3.Барвинок В.А. Управление напряженным состоянием и свойства плазменных покрытий. М.: Машиностроение, 1990. 384 с.
4.Никитин М.Д., Кулик А.Я., Захаров Н.И. Теплозащитные и износостойкие покрытия деталей дизеля. Л.: Машиностроение, 1977. 168 с.
5.Хасуй А. Техника напыления. Пер. с японского. М.: Машиностроение, 1975. 288 с.
6.Кудинов В.В., Иванов В.М. Нанесение плазмой тугоплавких покрытий. М.: Машиностроение, 1981. 192 с.
7.Журавлев Г.И., Кирш М. К методике определения термоупругих напряжений в покрытиях. / Кн. Защитные высокотемпературные покрытия. Л., 48. Костиков В.И., Шестерин Ю.А. Плазменные покрытия. М.: Металлургия, 1978. 160 с.
8.Костиков В.И., Шестерин Ю.А. Плазменные покрытия. М.: Металлургия, 1978. 160 с.
9.Никитин М.Д., Кулик А.Я., Захаров И.И. Напряженное состояние плазменных покрытий // Физика и химия обработки материалов. 1978. № 2. С. 131 - 136.
10.Ворошилов Г.А. Исследование и оптимизация процесса плазменной металлизации внутренних цилиндрических поверхностей автомобильных корпусных деталей: Автореф. дис. канд. техн. наук. МАДИ, 1973. 22 с.
11.Дубасов Л.М., Кудинов В.В., Шоршоров Н.Х. Термическое взаимодействие частиц с подложкой при нанесении покрытий напылением // Физика и химия обработки материалов. 1971. № 6. С. 29 - 34.
12.Антошин Е.В. Газотермическое напыление покрытий. М.: Машиностроение, 1974. 96 с.
13.Анисимов В.И., Кудинов О.В., Украинцев Б.П. Ремонт и монтаж кузнечно-прессового оборудования: Справочное пособие. М.: Машиностроение, 1973. 624 с.
Получено: 15.12.2003 |
Воронежский государственный |
|
технический университет |
104
УДК 621.8.004.6
МАТЕМАТИЧЕСКОЕ ОПИСАНИЕ ВЗАИМОСВЯЗИ ВЕЛИЧИНЫ ИЗНОСА ДЕТАЛИ, ОСНОВНЫХ ХАРАКТЕРИСТИК НАПЛАВЛЯЕМОГО ПОРОШКА, ПРИМЕНЯЕМОГО ОБОРУДОВАНИЯ И ТЕХНОЛОГИЧЕСКИХ ПАРАМЕТРОВ ПЛАЗМЕННОЙ НАПЛАВКИ
К.т.н. Шевцов А.В.
При расчете предельных износов деталей крупногабаритного технологического оборудования (КТО), с учетом взаимосвязи степени их изношенности и технико-экономических параметров процесса плазменной наплавки порошковыми материалами (ПНПМ), возникает необходимость определения оптимальных значений технологических параметров данного процесса в зависимости от толщины покрытия. Данная задача может быть решена экспериментальным методом, а также методом математического моделирования.
Эмпирическая модель такого сложного процесса, как ПНПМ, будет наиболее точно отражать взаимосвязь его выбранных независимых факторов и целевых функций /1/. С другой стороны, такая модель применима лишь для тех диапазонов и условий осуществления процесса ПНПМ, для которых она была построена. В свою очередь, теоретическая модель рассматриваемого процесса обладает значительной универсальностью, позволяет определять оптимальные значения технологических параметров ПНПМ вне зависимости от конструктивных особенностей используемого оборудования и характеристик наплавляемого порошка. Основным недостатком теоретической модели сложного многофакторного процесса является ее невысокая точность /1/. Несмотря на это, теоретическая модель оптимальных значений технологических параметров процесса ПНПМ дополняет аналогичную эмпирическую модель, а также позволяет оценивать рациональные условия проведения соответствующего эксперимента.
Адгезионная прочность и износостойкость слоя материала, полученного методом ПНПМ, в значительной степени зависят от величины остаточных растягивающих напряжений, возникающих в
105
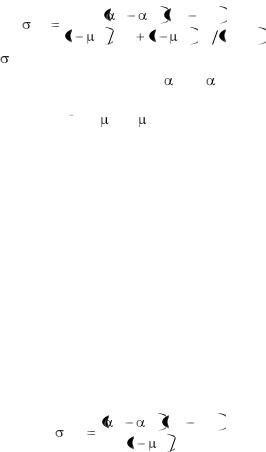
наплавленном слое /2, 3/. Величина таких напряжений определяется толщиной нанесенного слоя материала, интервалом температур охлаждения покрытия и механическими характеристиками материалов наплавленного слоя и детали /4, 5/:
|
|
|
|
П |
М |
ТП ТМ |
|
|
, |
(1) |
|
|
”– |
1 П |
ЕМ |
1 |
М h М |
ЕП h П |
|
||
|
|
|
|
|
||||||
|
|
|
|
|
|
|||||
где |
ОСТ |
- интегральные |
остаточные |
напряжения |
в |
|||||
|
|
|
|
|
|
|
|
|
|
|
наплавленном |
покрытии, |
МПа; |
|
П , |
М - |
|
коэффициенты |
термического расширения материалов покрытия и детали
соответственно, град 1 ; |
П |
, |
М |
- коэффициенты |
Пуассона |
материалов покрытия и детали соответственно; E П , EМ |
- модули |
упругости первого рода материалов покрытия и детали, МПа; TП ,ТМ - температуры наплавляемого покрытия и детали с покрытием после
охлаждения, град; |
hП ,hМ |
- толщина покрытия и детали |
|
соответственно, м. |
|
|
|
Известно, |
что |
эксплуатационные |
характеристики |
наплавленного порошкового покрытия в значительной степени зависят от степени оплавления частиц порошка и повышаются с ее ростом /6, 7/. С другой стороны, при увеличении степени оплавления частиц порошка возрастают растягивающие остаточные напряжения в наплавленном слое /8, 9/, что отрицательно сказывается на его прочностных и эксплуатационных характеристиках. Остаточные растягивающие напряжения также повышаются при увеличении толщины покрытия и в пределе приближаются к величине (см. формулу (1)
|
П |
М |
Т П Т М |
. |
(2) |
ОСТ |
|
|
|
||
1 |
|
Е П |
|
||
|
П |
|
Таким образом, остаточные растягивающие напряжения целесообразно выбрать в качестве комплексного параметра, характеризующего механические и триботехнические свойства плазменного покрытия.
Известно, что наплавленное порошковое покрытие минимально возможной толщины (0,2 мм) имеет наилучшие прочностные и эксплуатационные характеристики в том случае, если оно было сформировано из полностью проплавленных частиц
106
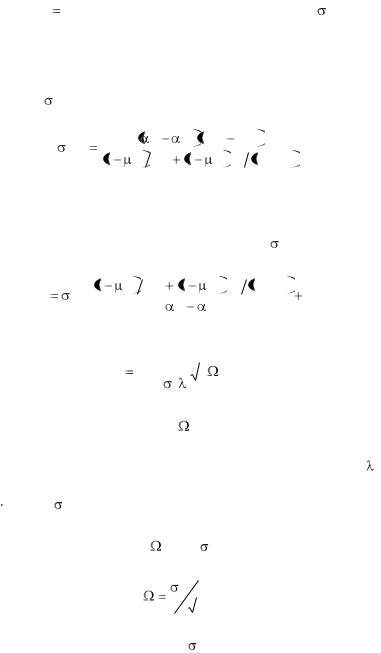
порошка ( TП ТПЛ ) /6, 10/. При этом величина ОСТ имеет
оптимальное значение относительно прочностных и эксплуатационных характеристик наплавленного слоя для данных условий осуществления процесса ПНПМ. Вышесказанное выступает в качестве граничных условий расчета величины остаточных
напряжений |
0 |
|
в покрытии, соответствующей его максимально |
||||||||
ОСТ |
|||||||||||
|
|
|
|
|
|
|
|
|
|||
возможным значениям эксплуатационных характеристик: |
|
||||||||||
|
|
0 |
|
|
П |
М |
ТПЛ |
ТМ |
, |
(3) |
|
|
|
ОСТ |
1 |
П ЕП |
1 |
|
h П 0,2ЕП |
||||
|
|
|
|
|
|||||||
|
|
|
|
П |
|
|
где TПЛ - температура плавления материала покрытия, град С. Приравнивая выражения (1) и (3), получаем уравнение для
расчета |
температуры |
наплавляемого |
покрытия |
T |
0 |
, |
которой |
|||||||||||||||||
|
|
|
|
|
|
|
|
|
|
|
|
|
|
|
|
|
|
|
П |
|
|
|
|
|
соответствует значение остаточных напряжений |
0 |
|
|
|
|
|
|
|
||||||||||||||||
ОСТ , возникающих |
||||||||||||||||||||||||
в наплавленном слое толщиной hП |
после его охлаждения |
|
|
|
|
|||||||||||||||||||
|
T0 |
0 |
|
1 |
П |
ЕМ |
|
1 |
|
|
|
|
М h М ЕП h П |
|
Т |
|
. |
|
|
(4) |
||||
|
ОСТ |
|
|
|
|
|
|
|
|
|
|
|
|
|
|
М |
|
|
||||||
|
П |
|
|
|
|
|
|
|
|
|
|
|
|
|
|
|
|
|
|
|
||||
|
|
|
|
|
|
|
|
П |
|
|
|
|
М |
|
|
|
|
|
|
|
|
|
|
|
По данным работы /6/, температура наплавляемого материала |
||||||||||||||||||||||||
определяется с использованием следующей зависимости: |
|
|
|
|
||||||||||||||||||||
|
|
|
|
|
|
|
|
NТ |
|
|
|
|
|
|
|
|
|
|
|
|
|
|
|
|
|
|
|
|
TП |
0,09 |
|
|
|
q |
|
dП a , |
|
|
|
|
|
|
|
(5) |
|||||
|
|
|
|
|
p |
|
|
|
|
|
|
|
|
|
|
|
||||||||
|
|
|
|
|
|
|
|
|
|
|
|
|
|
|
|
|
|
|
|
|
|
|
|
|
где NТ |
- тепловая мощность плазмотрона, Вт; |
|
q |
- |
расход |
|||||||||||||||||||
наплавляемого |
порошка, кг/с; |
|
|
- |
радиус |
рассеяния |
частиц |
|||||||||||||||||
порошка, м; dП - |
диаметр частицы порошка, м; а - |
коэффициент |
||||||||||||||||||||||
температуропроводности |
наплавленного материала, |
|
м2 / с ; |
- |
||||||||||||||||||||
коэффициент |
теплопроводности |
|
|
|
|
наплавленного |
|
|
материала, |
|||||||||||||||
Вт /(м град) ; |
2 |
- дисперсия массового распределения частиц на |
||||||||||||||||||||||
|
|
p |
|
|
|
|
|
|
|
|
|
|
|
|
|
|
|
|
|
|
|
|
|
|
основе. |
|
|
|
|
|
|
|
|
|
|
|
|
|
|
|
|
|
|
|
|
|
|
|
|
Между |
параметрами |
|
|
и |
|
|
|
|
2 |
существует |
взаимосвязь, |
|||||||||||||
|
|
|
|
|
|
p |
||||||||||||||||||
|
|
|
|
|
|
|
|
|
|
|
|
|
|
|
|
|
|
|
|
|
|
|
|
|
описываемая следующей аналитической зависимостью /6/ |
|
|
|
|||||||||||||||||||||
|
|
|
|
|
|
|
|
|
p |
|
|
|
. |
|
|
|
|
|
|
|
|
|
(6) |
|
|
|
|
|
|
|
|
|
|
|
|
2 |
|
|
|
|
|
|
|
|
|
||||
В |
свою |
очередь, |
из |
практики |
известно, |
что |
радиус |
|
пятна |
|||||||||||||||
наплавки RПН связан с параметром |
2 |
|
следующим соотношением |
|||||||||||||||||||||
|
p |
107
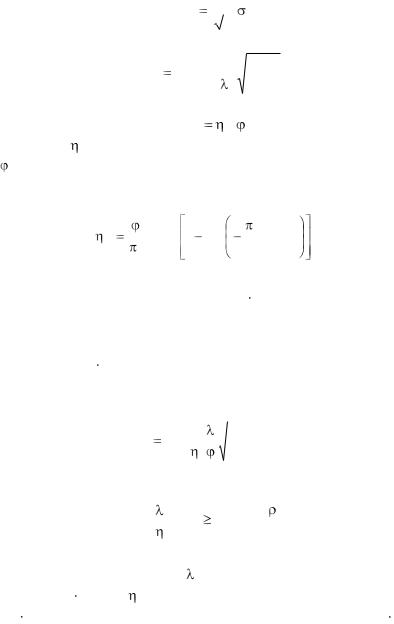
R ПН |
1,73 |
p . |
(7) |
||||
|
|
|
|
|
|||
|
|
|
|
|
|||
2 |
|
|
|||||
|
|
|
|
|
С учетом (6) и (7), выражение (5) принимает вид
|
|
TП |
0,1448 |
|
NТ |
|
qdП a |
. |
(8) |
||
|
|
|
|
|
|
R |
П Н |
||||
|
|
|
|
|
|
|
|
|
|
||
Тепловая мощность дуги определяется как |
|
||||||||||
|
|
|
NТ |
П I |
, |
|
|
(9) |
|||
где |
П |
- КПД |
плазмотрона; |
|
I |
- ток |
плазмотрона, А; |
||||
|
|
|
|
|
|
|
|
|
|
|
- напряжение дуги плазмотрона, В.
КПД плазменной горелки можно вычислить с использованием следующей аналитической зависимости /10/:
|
|
|
|
|
Cp QП |
|
1 |
exp |
|
|
d Д a П lД |
|
, |
|
(10) |
|||||||||||
|
|
П |
d д a П U |
|
|
Cp QП |
|
|||||||||||||||||||
|
|
|
|
|
|
|
|
|
|
|
|
|
|
|||||||||||||
|
|
|
|
|
|
|
|
|
|
|
|
|
|
|
|
|||||||||||
где U - напряжение источника питания, В; |
Cp |
- теплоемкость |
||||||||||||||||||||||||
плазмообразующего |
|
газа |
|
|
|
Дж /(кг |
град) ; |
QП |
- |
расход |
||||||||||||||||
плазмообразующего газа, кг/с; |
|
|
dД - |
|
диаметр дугового |
канала |
||||||||||||||||||||
плазмотрона, м; |
a П - коэффициент полной теплоотдачи от плазмы к |
|||||||||||||||||||||||||
каналу, Вт /(м2 |
град) |
; l |
Д |
- длина дуги, м. |
|
|
|
|
|
|||||||||||||||||
|
|
|
|
|
|
|
|
|
|
|
|
|
|
|
|
|
|
|
|
|
|
|
|
|
|
|
Объединяя (8) |
и (9) и приравнивая (8) к значению |
T0 для |
||||||||||||||||||||||||
|
|
|
|
|
|
|
|
|
|
|
|
|
|
|
|
|
|
|
|
|
|
|
|
|
|
П |
оптимального тока плазмотрона, получаем |
|
|
|
|
|
|||||||||||||||||||||
|
|
|
|
|
|
|
|
|
|
|
|
T0 |
|
|
|
|
|
|
|
|
|
|
|
|
|
|
|
|
|
|
|
|
|
|
|
|
|
|
|
|
|
R |
П Н |
|
|
|
|
|
|
|
|||
|
|
|
|
|
I |
|
6,91 |
|
|
П |
|
|
|
|
. |
|
|
|
|
(11) |
||||||
|
|
|
|
|
|
|
|
|
|
|
|
|
|
|
|
|
||||||||||
|
|
|
|
|
|
|
|
|
|
|
|
|
П |
|
|
|
qdП a |
|
|
|
|
|
||||
При нагреве частицы порошка в потоке плазмы условие ее |
||||||||||||||||||||||||||
полного проплавления имеет вид /11/: |
|
|
|
|
|
|
|
|
|
|||||||||||||||||
|
|
|
|
|
T |
2 |
2 |
|
|
|
|
|
|
|
d2 |
Т2 |
|
C2 |
|
|
|
|
|
|||
|
|
|
|
|
Г |
Г |
L |
|
|
|
|
|
|
• |
ПЛ |
|
|
L |
, |
|
|
|
(12) |
|||
|
|
|
|
|
V |
|
min |
|
|
|
4Nu2 |
|
|
|
||||||||||||
|
|
|
|
|
Г |
|
|
|
|
|
|
|
|
|||||||||||||
|
|
|
|
|
Г |
|
|
|
|
|
|
|
|
|
|
|
|
|
|
|
|
|
||||
где VГ |
- скорость плазмообразующего |
газа, м/с; |
TГ - |
|||||||||||||||||||||||
температура плазмы, град; |
|
|
|
Г |
- коэффициент |
теплопроводности |
||||||||||||||||||||
газа, Вт /(м град) ; |
Г |
-коэффициент динамической вязкости газа, |
||||||||||||||||||||||||
Па с ; |
CL - теплоемкость наплавляемого материала, |
Дж /(кг |
град) ; |
|||||||||||||||||||||||
Lmin - |
наименьшая длина траектории частицы порошка, за время |
108
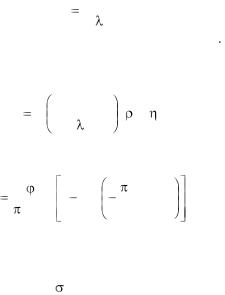
прохождения которой последняя расплавится, м; Nu - критерий Нуссельта /6/:
|
|
Nu |
a p d |
П |
, |
(13) |
|
|
|
|
|||
|
|
|
|
|||
где a |
p |
- коэффициент теплоотдачи газа, Вт /(м2 |
град) . |
|||
|
|
|
|
|
|
Используя (12), получаем уравнение для расчета оптимального значения дистанции наплавки L
|
|
|
|
1 |
|
|
d П Т |
ПЛ СL |
2 |
|
|
|
|
||
|
L |
|
|
|
VГ |
|
. |
|
(14) |
||||||
|
4 |
|
|
Nu |
Г Т |
|
|
Г |
|
||||||
|
|
|
|
|
Г |
|
|
|
|
|
|
||||
Температура плазмообразующего газа определяется в |
|||||||||||||||
соответствии с зависимостью /10/: |
|
|
|
|
|
|
|
||||||||
TГ |
|
|
I |
|
1 |
exp |
|
|
d Д a |
П l |
Д |
. |
(15) |
||
|
|
d Д a П |
|
|
|
Cp QП |
|
||||||||
|
|
|
|
|
|
|
|
|
|
|
Алгоритм практического применения приведенных выше зависимостей оптимальных значений технологических параметров процесса ПНПМ состоит из следующих этапов:
1) расчет параметра толщины покрытия;
0 |
по формуле (3) в зависимости от |
|
ОСТ |
||
|
2)расчет параметра TП0 по формуле (4);
3)определение КПД плазменной горелки с использованием уравнения (10);
4)расчет оптимального значения тока плазмотрона по формуле (11);
5)расчет температуры плазмообразующего газа с использованием уравнения (15);
6)определение оптимального значения дистанции наплавки по формуле (14).
Литература:
1.Хартман К. и др. Планирование эксперимента в исследовании технологических процессов. Пер. с нем. / Под ред. к.
т. н. Э.К. Лецкого. М.: Мир, 1977. 552 с.
2.Барвинок В.А. Управление напряженным состоянием и свойства плазменных покрытий. М.: Машиностроение, 1990. 384 с.
3.Кудинов В.В., Иванов В.М. Нанесение плазмой тугоплавких покрытий. М.: Машиностроение, 1981. 192 с.
109
4.Журавлев Г.И., Кирш М. К методике определения термоупругих напряжений в покрытиях. / Кн. Защитные высокотемпературные покрытия. Л., 1972. с. 315 - 321.
5.Никитин М.Д., Кулик А.Я., Захаров Н.И. Теплозащитные и износостойкие покрытия деталей дизеля. Л.: Машиностроение, 1977. 168 с.
6. Нанесение покрытий плазмой / В.В. Кудинов, П.Ю. Пекшев, В.Е. Белащенко и др. М.: Наука, 1990. 408 с.
7.Николаев А.В. / Кн. Плазменные процессы в металлургии
итехнологии неорганических материалов. М.: Наука, 1973. С. 20 - 32.
8.Александров А.В., Потапов В.Д., Державин В.П. Сопротивление материалов. М.: Высш. шк., 1995. 560 с.
9.Ляхович Л.С. Текстура и остаточные напряжения в боридных покрытиях // Физико-химическая механика материалов.
1973. № 3. С. 18 - 22.
10.Костиков В.И., Шестерин Ю.А. Плазменные покрытия. М.: Металлургия, 1978. 160 с.
11.Юшков В.И., Борисов Ю.С., Гершензон С.М. // ФХОМ. 1975. № 4. С. 20 - 22.
Получено: 15.12.2003 |
Воронежский государственный |
|
технический университет |
РАЗДЕЛ 3. ОБЩИЕ ВОПРОСЫ МАШИНОСТРОЕНИЯ
УДК 681.2
ПРОЕКТИРОВАНИЕ АРХИТЕКТУРЫ ПРОГРАММНОЙ СИСТЕМЫ, ИСПОЛЬЗУЕМОЙ ДЛЯ ТЕХНОЛОГИЧЕСКОЙ ПОДГОТОВКИ МАШИНОСТРОИТЕЛЬНОГО ПРОИЗВОДСТВА
Муранов В.А, Селезнева Т.А.
При построении автоматизированной системы технологической подготовки производства (АСТПП) в рамках автоматизированной системы управления предприятием (АСУП) обе системы должны быть, прежде всего, адекватно описаны. При
110

этом должны быть построены полные и непротиворечивые их функциональные и информационные модели. АСУП относится к категории наиболее сложных информационных систем (ИС). Опыт проектирования ИС показывает, что это логически сложная, трудоемкая и длительная по времени работа, требующая высокой квалификации участвующих в ней специалистов. Однако часто проектирование ИС выполняется в основном на интуитивном уровне с применением неформализованных методов, основанных на искусстве, практическом опыте, экспертных оценках и дорогостоящих экспериментальных проверках качества функционирования ИС. Кроме того, в процессе создания и функционирования ИС информационные потребности пользователей могут изменяться или уточняться, что еще более усложняет разработку и сопровождение таких систем.
Более того, ручная разработка обычно порождала следующие проблемы:
неадекватная спецификация требований;
неспособность обнаруживать ошибки в проектных
решениях; |
|
|
|
низкое |
качество |
документации, |
снижающее |
эксплуатационные качества;
затяжной цикл и неудовлетворительные результаты тестирования и другие.
С появлением программно-технологических средств специального класса - CASE-средств, реализующих CASEтехнологию создания и сопровождения ИС ситуация изменилась. Отметим, что в настоящее время термин CASE (Computer Aided Software Engineering) используется в широком смысле. Первоначальное значение термина CASE ограничивалось вопросами автоматизации разработки только лишь программного обеспечения (ПО). Но в настоящее время оно приобрело новый смысл, охватывающий процесс разработки сложных ИС в целом. Под термином CASE-средства понимаются программные средства, поддерживающие процессы создания и сопровождения ИС, включая анализ и формулировку требований, проектирование прикладного ПО (приложений) и баз данных, генерацию кода, тестирование, документирование, обеспечение качества, конфигурационное управление и управление проектом, а также другие процессы.
111
CASE-средства вместе с системным ПО и техническими средствами образуют полную среду разработки ИС.
Автоматизация самого процесса разработки тем более необходима, что современные крупные проекты АСУП характеризуются, как правило, следующими особенностями:
сложность описания (достаточно большое количество функций, процессов, элементов данных и сложные взаимосвязи между ними), требующая тщательного моделирования и анализа данных и процессов;
наличие совокупности тесно взаимодействующих компонентов (подсистем), имеющих свои локальные задачи и цели функционирования;
отсутствие прямых аналогов, ограничивающее возможность использования каких-либо типовых проектных решений и прикладных систем;
необходимость интеграции существующих и вновь разрабатываемых приложений;
функционирование в неоднородной среде на нескольких аппаратных платформах;
разобщенность и разнородность отдельных групп разработчиков по уровню квалификации и сложившимся традициям использования тех или иных инструментальных средств;
существенная временная протяженность проекта, обусловленная, с одной стороны, ограниченными возможностями коллектива разработчиков, и, с другой стороны, масштабами организации-заказчика и различной степенью готовности отдельных ее подразделений к внедрению ИС.
Методологии, технологии и инструментальные средства проектирования CASE составляют основу проекта любой ИС, в том числе и АСУП, частью которой является АСТПП. Методология реализуется через конкретные технологии и поддерживающие их стандарты, методики и инструментальные средства, которые обеспечивают выполнение процессов ЖЦ.
Технология проектирования определяется как совокупность многих подсистем, которые связаны основными составляющими, в том числе есть три таких:
применение пошаговой процедуры, определяющей последовательность технологических операций проектирования;
112