
2890
.pdfэкономической |
целесообразности применяемых технических |
решений. |
|
Получено: |
Воронежский государственный |
22.12.2003 г. |
технический университет |
УДК 621.002.5: 378.1
МЕХАНИЗМ ФОРМИРОВАНИЯ ПОВЕРХНОСТНОГО СЛОЯ ПРИ ВОССТАНОВЛЕНИИ ДЕТАЛЕЙ ГАЗОПЛАМЕННЫМ МЕТОДОМ НАПЫЛЕНИЯ
В. М. Пачевский, Д. П. Бобров, Гунин В.И.
При газопламенном методе напыления подаваемый в горелку порошок разгоняется и ускоряется при движении в высокотемпературном потоке газа, истекающего с большой скоростью из сопла горелки. Частицы распыленного металла достигают поверхности в пластическом состоянии, с высокой скоростью соударяются с поверхностью основы и наслаиваются на нее, что приводит к образованию покрытия.
Свойства газотермического покрытия в значительной степени определяются особенностями взаимодействия напыляемого материала с высокотемпературным потоком и физико-химическими, физико-механическими и тепловыми процессами в зоне взаимодействия частиц с подложкой.
В процессе напыления частицы порошка разогреваются до температуры плавления или близкой к ней. Можно считать, что струя напыляемых частиц образует конус, вершина которого располагается на срезе сопла горелки. На поверхности основы напыляемые частицы образуют пятно распыла в форме круга. По его краям напыленные частицы слабее соединяются с материалом подложки. При многократном проходе на эти участки попадут другие частицы и в покрытии образуются поры. Для уменьшения пористости напыленного слоя перед горелкой устанавливают экран, который отсекает поток периферийных частиц. В результате покрытие формируется только частицами, движущимися в центральной зоне струи.
93

Соединение напыленного покрытия с основой осуществляется
восновном за счет механического сцепления напыляемых частиц с выступами и впадинами на поверхности основы, образованными предварительной обработкой. Механическое сцепление усиливается
врезультате сплавления или химического взаимодействия частиц с основой.
Движение частиц от среза сопла горелки до поверхности подложки происходит в среде, содержащей значительное количество воздуха, захваченного струей из атмосферы, независимо от соотношения расходов горючего газа и кислорода в газовом пламени. Следовательно, напыляемые частицы, движущиеся в газовой струе, непрерывно взаимодействуют с кислородом. Степень их окисления может быть значительной и зависит в основном от используемой для напыления аппаратуры и условий напыления. В результате этого каждая частица покрывается пленкой окислов, которая остается на границах частиц в покрытии. В напыленном материале соединение частиц, помимо механического сцепления, происходит и через окислы. В местах разрушения окисных пленок происходит сплавление металлических частиц. Химическое взаимодействие усиливается при повышении температуры в зоне контакта частицы с подложкой, которая определяется температурой частицы и подложки, а также их теплофизическими свойствами в момент контакта. Более высокая тепловая энергия соударяющихся с поверхностью частиц способствует увеличению прочности сцепления покрытия с подложкой. Для предотвращения окисления поверхности основы при напылении необходимо поддерживать
температуру 260—310 С.
При газопламенном нанесении порошковых материалов в случае, когда напыляемый материал и материал основы имеют решетки приблизительно одинакового размера, могут возникать физические связи, проявляющиеся в виде молекулярных связей. Это способствует повышению прочности сцепления покрытия с основой. На участках основы, поверхность которых имеет повышенную активность, характер соединения определяется диффузионными процессами.
Для получения хорошего сцепления напыленного покрытия с основным металлом частицы должны иметь достаточную скорость подлета к подложке. Увеличение скорости соударения частицы с подложкой приводит к повышению импульсного давления в зоне
94
соударения, что обеспечивает самоочищение подложки в зоне ее контакта с частицей.
Получено: 15.12.2003 |
Воронежский государственный |
|
технический университет |
УДК 621.8.004.6 |
|
ВЗАИМОСВЯЗЬ ПРЕДЕЛЬНЫХ ИЗНОСОВ ДЕТАЛЕЙ КРУПНОГАБАРИТНОГО ОБОРУДОВАНИЯ И ПАРАМЕТРОВ ИХ ВОССТАНОВЛЕНИЯ
ПЛАЗМЕННОЙ НАПЛАВКОЙ
К.т.н. Шевцов А.В., Кондратьев В.А., Гунин В.И.
Анализируя структуру расходов, возникающих при восстановлении работоспособности детали плазменной наплавкой порошковыми материалами (ПНПМ), можно сделать вывод, что они образуются суммированием следующего: затрат, являющихся функцией износа и связанных с нанесением слоя материала (затраты на наплавляемый порошок, электроэнергию, транспортирующий, плазмообразующий и защитный газы, трудовые расходы), восстанавливающего износ поверхностей; затрат, возникающих при проведении разборочно-сборочных работ, подготовке детали к восстановлению, ее последующей механической обработке и временном выводе машины из эксплуатации. С одной стороны, очевидно, что затраты, зависящие от величины износа детали, имеют минимальное значение при минимальном износе данной детали. Соответствующий период эксплуатации детали до восстановления также будет минимальным. Но, с другой стороны, высокая частота проведения разборочно-сборочных работ в итоге может вызвать недопустимо большие ремонтные расходы по прошествии некоторого количества циклов восстановления данной детали. Поэтому при определении предельных износов деталей крупногабаритного технологического оборудования (КТО) наряду со стоимостью и количеством циклов их восстановления необходимо учитывать величину периода эксплуатации данной группы деталей. При этом очевидно, что должно соблюдаться условие минимума суммарных затрат на восстановление деталей
95

при максимально возможном периоде их эксплуатации. В связи с этим, представляется целесообразным ввести параметр, равный отношению суммарных затрат на восстановление изделия (детали или машины) к периоду его эксплуатации. Данный параметр описывает взаимосвязь между технологическим процессом восстановления изношенного изделия и его степенью изношенности.
Очевидно, что, если для данной группы деталей значение указанного параметра будет минимально возможным, то на восстановление работоспособности этой группы деталей за некоторый, достаточно длительный период эксплуатации будет израсходовано минимально возможное количество средств. При этом восстановление работоспособности данного изделия будет наиболее выгодным экономически. Теоретическая минимизация отношения суммарных расходов на восстановление группы деталей к периоду их эксплуатации предполагает наличие математической модели данного параметра.
Пусть в данной машине имеется группа изнашивающихся и подлежащих периодическому восстановлению деталей. В общем случае межремонтные периоды данных деталей, соответствующие их предельно допустимым износам, будут различны, что неоправданно усложняет структуру ремонтного цикла машины /1, 2, 3/. С целью упрощения задачи моделирования удельной стоимости восстановления группы деталей возникает предложение рассматривать данную группу в качестве одной "обобщенной детали". Обобщенным износом U g назовем алгебраическую сумму
линейных износов деталей рассматриваемой группы:
n |
|
|
|
Ug |
U j |
, |
(1) |
j |
1 |
|
|
где U j - линейный износ |
j - |
й детали группы, мкм; |
n - |
количество деталей в группе.
Определенной величине обобщенного износа группы деталей соответствует определенное значение расходов, связанных с
износом. Так, для затрат на наплавляемый порошок Z• |
справедливо |
||||||||
следующее выражение: |
|
|
|
|
|
|
|
|
|
|
|
10 6 |
Ku Ug |
n |
|
|
|
|
|
Z |
|
C |
|
S |
|
, |
(2) |
||
• |
|
•j |
j |
||||||
|
|
Km g |
|
j |
|
|
|||
|
|
|
j 1 |
|
|
|
|
|
96

где - плотность наплавленного материала, кг/ м3 ; K u = 1,9 -
коэффициент, учитывающий величину снимаемого слоя материала при предварительной обработке поверхности; Km = 0,8 -
коэффициент использования наплавляемого порошка; CПj - стоимость порошка, наплавляемого на изношенную поверхность j -
й детали, р/кг; |
j - скорость изнашивания j - й детали, мкм/ч; |
S j - |
|
площадь изношенной поверхности j - ой детали, м2 ; |
|
||
|
|
n |
|
|
g |
j . |
(3) |
|
|
j 1 |
|
Затраты |
на электроэнергию ZЭЛ в зависимости |
от |
обобщенного износа группы деталей можно определить по следующей формуле:
|
|
C |
|
K |
|
U |
|
n |
|
J |
S |
|
|
|
|
ZЭЛ |
10 9 |
|
ЭЛ |
|
u |
|
g |
|
|
j |
|
j j |
|
, |
(4) |
|
K m g |
|
|
j |
1 |
|
q j |
||||||||
|
|
|
|
|
|
|
|
||||||||
где Cэл - |
стоимость |
электроэнергии, |
р/ кВт ч; |
- |
напряжение питания плазмотрона, В; J j - оптимальное значение тока плазмотрона при наплавке j - й детали, А; q j - оптимальное
значение расхода присадочного порошка при наплавке j - ой детали, кг/ч.
Для |
затрат |
на |
|
защитный, |
|
|
|
|
плазмообразующий |
и |
||||||||||||||||
транспортирующий газ (аргон) ZГ |
|
|
и заработную плату ZЗ были |
|||||||||||||||||||||||
получены следующие выражения: |
|
|
|
|
|
|
|
|
|
|
|
|
|
|
|
|
|
|
||||||||
|
ZГ |
10 6 |
|
C |
Г |
Q K |
u |
U |
g |
|
n |
|
S |
j |
j |
, |
(5) |
|||||||||
|
|
|
|
|
|
|
|
|
|
|
|
|
|
|
|
|||||||||||
|
|
|
|
|
|
K m |
|
g |
|
|
|
|
j |
1 |
|
|
q j |
|
|
|||||||
|
|
|
|
|
|
|
|
|
|
|
|
|
|
|
|
|
|
|
||||||||
|
ZЗ |
10 6 |
|
|
C |
З |
K |
u |
U |
g |
|
n |
|
S |
j |
|
j |
, |
(6) |
|||||||
|
|
|
|
|
|
|
|
|
|
|
|
|
|
|
||||||||||||
|
|
|
|
|
|
K m |
|
|
g |
|
|
|
|
j |
1 |
|
q j |
|
|
|||||||
|
|
|
|
|
|
|
|
|
|
|
|
|
|
|
|
|
|
|
||||||||
где CГ - стоимость |
аргона, |
|
р/л; |
|
|
СЗ - |
почасовая тарифная |
|||||||||||||||||||
ставка, р/ч; Q - расход аргона, л/ч. |
|
|
|
|
|
|
|
|
|
|
|
|
|
|
|
|
|
|
||||||||
Таким |
образом, |
затраты |
|
Z Ug |
|
|
|
на |
|
восстановление деталей |
методом ПНПМ определяются с использованием следующего выражения:
97
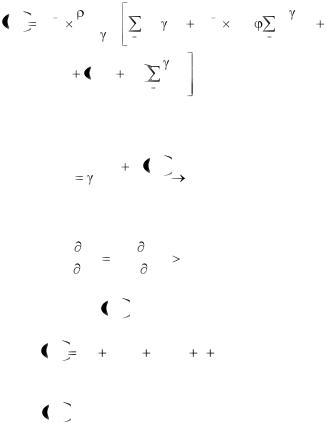
|
|
|
K |
U |
|
n |
|
|
|
|
|
n |
J |
S |
|
Z U |
|
10 6 |
u |
|
g |
|
C |
S |
10 3 |
C |
|
|
j j j |
||
g |
|
|
|
|
ЭЛ |
|
|
|
|||||||
|
|
Km |
|
|
|
|
Пj |
j j |
|
|
|
q j |
|||
|
|
|
g |
|
j 1 |
|
|
|
|
j 1 |
|
||||
|
|
|
|
|
|
|
n |
jSj |
|
|
|
|
|
|
|
|
|
|
C |
Q |
C |
|
|
, |
|
|
|
(7) |
|||
|
|
|
З |
|
|
|
|
|
|||||||
|
|
|
Г |
|
|
|
|
q j |
|
|
|
|
|
|
|
|
|
|
|
|
|
|
j 1 |
|
|
|
|
|
|
||
С учетом выражения (7) отношение Cg |
суммарных расходов |
на восстановление группы деталей к периоду их эксплуатации можно представить в виде:
Cg |
|
|
|
Zc |
Z Ug |
|
|
min . |
|
(8) |
||
|
g |
|
Ug |
|
|
|
|
|||||
Оптимальный |
обобщенный |
|
|
износ |
группы |
деталей |
||||||
определяется из условий: |
|
|
|
|
|
|
|
|
|
|
|
|
|
C |
g |
0 и |
|
2 C |
g |
|
0 . |
|
(9) |
||
|
|
|
|
|
|
|||||||
|
|
|
|
|
|
|
|
|
||||
|
U |
g |
|
U2 |
|
|
||||||
|
|
|
|
|
|
|
|
|||||
|
|
|
|
|
g |
|
|
|
|
Сцелью упрощения математической формулировки
выражения (8) |
функция |
|
Z Ug |
|
может быть представлена в виде |
|||||||
полиномиального уравнения: |
|
|
|
|
|
|
|
|
||||
|
Z U |
g |
Z |
0 |
Z U |
g |
Z |
U2 |
... Z |
Uk , |
(10) |
|
|
|
|
1 |
|
2 |
g |
k |
g |
|
|||
где Z0 , Z1 , Z2 ,..., Zk - параметры аппроксимации; k - порядок |
||||||||||||
аппроксимирующего уравнения. |
|
|
|
|
|
|
|
|||||
Функция |
Z Ug |
может |
быть |
получена любым |
методом |
построения аппроксимирующих функций с учетом того, что нарастание износов U j (j = 1, 2, 3, ..., n) всех деталей группы
происходит одновременно.
Модель (8) позволяет определять величину обобщенного износа Ugopt рассматриваемой группы деталей, оптимальную как из
условия максимальной экономической эффективности восстановления этих деталей, так и из условия выбора оптимальных методов и режимов их восстановления. Определенное таким
образом оптимальное значение обобщенного износа Ugopt позволяет
рассчитать величину периода эксплуатации рассматриваемой группы деталей до восстановления, оптимальное значение износа каждой детали, а также определить параметры технологических
98

процессов восстановления деталей группы. Так, период эксплуатации Т данной группы деталей следует рассчитывать как
T Ugopt g . При этом учитывая, что изнашивание деталей группы
происходит одновременно, и отношение износа любой детали группы к износу обобщенной детали равно отношению соответствующих скоростей изнашивания, для оптимального износа
Uoj pt j - й детали можно получить следующую формулу:
U j |
j |
Ug . |
(11) |
|
|||
opt |
|
opt |
|
g
Оптимальному износу детали Uoj pt , в свою очередь, можно
поставить в соответствие оптимальные значения параметров технологического процесса ее восстановления.
Таким образом, на основании общей структуры восстановительного цикла машины, оптимальность которой доказана на практике, разработана комплексная модель взаимосвязи технико-экономических параметров технологического процесса восстановления группы деталей машины и их степени изношенности. С использованием данной модели разработана методика оптимизации указанной взаимосвязи, позволяющая найти значения предельных износов деталей, минимизирующие расходы на восстановление работоспособности этих деталей с применением метода ПНПМ, а также оптимальные параметры процесса ПНПМ.
Литература:
1.Пекелис Г.Д., Гельберг Б.Т. Технология ремонта металлорежущих станков. М.: Машиностроение. 1976. 320 с.
2.Проников А.С. Надежность машин. М.: Машиностроение,
1978. 592 с.
3.Рыков В.Н. Организация капитального ремонта машин. М.: Машиностроение, 1988. 112 с.
Получено: 15.12.2003 |
Воронежский государственный |
|
технический университет |
99
УДК 621.791.92
ДОСТОИНСТВА И НЕДОСТАТКИ ПЛАЗМЕННОЙ НАПЛАВКИ ПОРОШКОВЫМИ МАТЕРИАЛАМИ.
ФАКТОРЫ, ВЛИЯЮЩИЕ НА СВОЙСТВА ПЛАЗМЕННЫХ ПОКРЫТИЙ
К.т.н. Шевцов А.В., Кондратьев В.А., Гунин В.И.
Среди широко используемых методов восстановления деталей крупногабаритного технологического оборудования (КТО) одним из наиболее перспективных является метод плазменной наплавки порошковыми материалами (ПНПМ). Применение ПНПМ позволяет: восстанавливать широкую номенклатуру деталей КТО, имеющих плоские, цилиндрические, конические поверхности и поверхности сложной формы; полностью автоматизировать технологический процесс наращивания поверхности; осуществлять нанесение покрытий заданного химического состава и применять тугоплавкие материалы; восстанавливать локальный участок поверхности детали; осуществлять восстановление деталей КТО с любыми величинами износа, встречающимися на практике. Данный реновационный метод обладает также высокой производительностью.
Основным недостатком метода ПНПМ следует считать оплавление поверхности детали в процессе наращивания слоя материала /1, 2/. Оплавление поверхности сопровождается значительным нагревом самой детали, что неизбежно приводит к ее последующему короблению. Поэтому метод ПНПМ нельзя рекомендовать для восстановления тонкостенных деталей и деталей небольших размеров. При восстановлении крупногабаритных деталей методом ПНПМ оплавление наращиваемых поверхностей не приводит к недопустимому нагреву таких деталей вследствие их значительной массы.
В связи с этим метод ПНПМ нашел широкое распространение на промышленных предприятиях. Однако, несмотря на широкое применение метода ПНПМ, недостаточно полно разработаны научно обоснованные рекомендации по получению наплавленных слоев определенного порошкового материала заданной толщины, имеющих максимально возможную износостойкость и достаточную
100
адгезионную прочность, что особенно актуально для восстановленных деталей КТО.
Разработка рекомендаций по применению метода ПНПМ для восстановления деталей КТО непосредственно связана с поиском оптимальных условий осуществления данного процесса. Для успешного решения задачи оптимизации процесса ПНПМ особое значение имеет рациональный выбор целевых функций и факторов оптимизации.
Впроцессе формирования покрытий методом ПНПМ можно выделить два основных этапа: нагрев, ускорение и перенос частиц наплавляемого материала к наплавляемой поверхности (основе); осаждение частиц на поверхности и формирование наплавленного слоя и системы покрытие - основа /3/. При плазменной наплавке порошковыми материалами нагрев и перенос частиц совмещены во времени. Параллельно с нагревом и ускорением частиц на первом этапе формирования покрытия развиваются процессы их взаимодействия с окружающей средой, приводящие к окислению, газонасыщению и частичной дислокации материала наплавляемых частиц. Следовательно, на данном этапе закладывается уровень прочностных и эксплуатационных характеристик покрытий, поскольку на этом этапе, с одной стороны, частицы накапливают запас тепловой и кинетической энергии, а с другой, происходит металлургический передел наплавляемого материала в материал, из которого формируется покрытие /1, 2, 4, 5/.
На втором этапе формирования покрытия можно выделить две стадии. На первой стадии на контактных поверхностях осаждаемых частиц и основы (ранее наплавленного слоя) развиваются процессы образования соединения частиц с основой. На второй стадии в процессе кристаллизации частиц и охлаждения наплавленного слоя
вобразующейся системе покрытие - основа протекают процессы объемного взаимодействия и формируются остаточные напряжения. Сцепление между частицами, а также основой и покрытием может происходить за счет механического зацепления, физического и химического взаимодействия /1, 2, 6/.
Вработах /1, 6, 11/, где достаточно обстоятельно рассмотрены физико-химические процессы, возникающие при взаимодействии наплавляемой частицы с основой, показано, что адгезионная прочность плазменно-порошковых покрытий является сложной функцией температуры в контакте частица - основа, длительности
101
удара и затвердевания частицы, давления, развивающегося при ударе. Регулировать длительность удара и давление, развивающееся при ударе, в условиях высокотемпературной наплавки затруднительно /3/. В связи с этим важнейшим комплексным фактором, определяющим эксплуатационные свойства плазменнопорошковых покрытий, становится термическая активация контакта напыляемой частицы и основы.
Термическую активацию наплавляемой поверхности для достижения химического взаимодействия с наплавляемым материалом можно осуществить предварительным подогревом данной поверхности, применением термореагирующих материалов, нагревом наплавляемых частиц путем изменения: скорости плазменной струи, состава и температуры плазмообразующего газа, дистанции наплавки и скорости перемещения плазмотрона относительно наплавляемой поверхности /3/. Способ термической активации основы заслуживает особого внимания, так как позволяет управлять эксплуатационными свойствами покрытий посредством контролируемых изменений параметров технологического процесса их получения. Недостатками, присущими термической активации, являются: возможность окисления восстанавливаемой поверхности при подогреве без защитной атмосферы; возникновение в покрытии значительных кристаллизационных растягивающих напряжений в результате оплавления и расплавления основы из легкоплавких сплавов при подогреве наплавляемой поверхности.
Следует отметить, что одной из причин сравнительно низкой прочности плазменных покрытий является формирование в наплавленном материале больших остаточных растягивающих напряжений /8, 9/. Возникновение таких напряжений обусловлено различием температуры частиц и основы, их коэффициентами термического расширения, усадкой при кристаллизации частиц, жесткостью системы покрытие - основа, деформацией и наклепом частиц при ударе о наплавляемую поверхность и т. д. Таким образом, остаточные напряжения в наплавленном слое материала являются также результатом действия термического и кинематического факторов процесса ПНПМ. Процесс термической активации, повышая прочность сцепления наплавленного слоя с основой, вместе с тем оказывает существенное влияние на уровень остаточных растягивающих напряжений. Уровень этих напряжений не остается постоянным в процессе наращивания слоя материала.
102