
2890
.pdfцепь. Для систем подачи и возврата это – общая подача, шаговая подача, число подаваемых шариков на оборот, направляющая системы подачи и направляющая втулка, встроенная система возврата, внешняя система возврата: через направляющую трубку или через канал гайки.
Особым достижением предприятия A.MANNESMANN следует считать разработанные системы охлаждения и уплотнения тягового устройства. Системы охлаждения выполнены адаптивными и позволяют исключить потери мощности посредством выборочного охлаждения участков винта при зонном росте температуры.
Высокая частота вращения винта и значительные передаваемые мощности при сложной контактной геометрии передачи не позволяют добиться абсолютного уплотнения элементов винта и гайки. Конструкторы фирмы решают эту сложную проблему путем создания смазывающе-уплотняющего слоя толщиной 3-5 мкм, которые позволяет компенсировать негативное воздействие микрочастиц, присутствующих на винте и разуплотняющих соединения.
Идеальное качество изготовления передач позволило решить сложную задачу для представленных механизмов – сочетание высокой осевой нагрузки и значительного крутящего момента без значимых потерь на трение. Выпускаемые варианты конструкций ранжированы по показателям жесткости и требуемого (передаваемого) крутящего момента. Оптимальный выбор типа устройства, подтверждаемый минимальными показателями холостого хода крутящего момента, дестабилизирующих вибраций и максимальным значением жесткости, обеспечивает высокие показатели надежности при экстремальной эксплуатации.
Сравнение конструкций A.MANNESMANN аналогичными конкурентными изделиями показывает явное превосходство новых разработок фирмы. Впервые решена комплексная задача достижения высокой безотказности и долговечности передач, практически с первых технологических переходов при изготовлении и посредством прогнозирования технологической наследственности при эксплуатации. Свободное владение технологиями в так называемой «микронной области» позволяет гарантировать, как минимум двойное увеличение показателей работоспособности По-сравнению с лучшими аналогами, и что важно стабильными по времени цикла.
63

В качестве примера можно привести высокотехнологичную передачу с двойной гайкой 40Х20. Она обладает типичной жесткостью 0,8-1,0 кН/мкм. Обеспечение таких показателей достигается максимальной общей погрешностью равной 15 мкм.
Получено: |
Воронежский государственный |
14.09.2003 |
технический университет |
УДК 621.78 |
|
ГИБКИЕ ТРУБОПРОВОДНЫЕ СОЕДИНЕНИЯ
Доктор техн. наук Осинцев А.Н., канд.техн.гаук Скачилов В.Н., Скуратов Б.И., доктор техн. наук Тибаев В.К.
Представлены конструкции сильфонных компенсаторов обладающих повышенной вибропоглощающей и демпфирующей способностью.
Для компенсации тепловых расширений трубопроводов двигателей летательных аппаратов (ДЛА), погрешностей изготовления и монтажа, угловых, поперечных и продольных взаимных перемещении стыкуемых элементов широко применяются гибкие металлические трубопроводы в виде сильфонных компенсаторов (СК). Они становятся единственно возможными гибкими соединениями в условиях воздействия высоких (550 C и более) температур, радиационного облучения, протекания внутри них криогенных жидкостей (с температурой до 22 К), а также длительного хранения.
Однако применение СК вносит ряд дополнительных требований [1], которые должны быть уточнены конструктором при проектировании трубопроводных коммуникаций ДЛА. Следует отметить, что установка СК сильно изменяет динамические характеристики трубопроводного пролета и приводит к возникновению проблемы обеспечения виброустойчивости и вибропрочности самого компенсатора, особенно его гофрированной оболочки-сильфона.
СК из-за низкой продольной и изгибной жесткости обладает плотным спектром низкочастотных продольных и изгибных колебании, однако не имеет достаточных вибропоглощающих свойств [2].
64
В последние годы были разработаны новые конструкции СК с высокой демпфирующей способностью, позволяющие снизить амплитуду резонансных колебаний до приемлемого уровня. С целью наиболее рационального использования СК возникла необходимость проведения их тщательного расчетного и экспериментального анализа, выявления достоинств и недостатков, а также разработки рекомендации по применению.
Проведенный анализ конструкций СК, обладающих повышенной вибропоглощающей способностью, по способу реализации демпфирования позволяет классифицировать их на четыре основные группы:
1.Компенсаторы с многослойными гофрированными оболочками (сильфонами).
2.Компенсаторы с демпфирующими вкладышами во впадинах гофров по наружной поверхности силъфона.
3.Компенсаторы с выносными демпферами.
4.Компенсаторы с коаксиально расположенными демпферами.
Компенсаторы с многослойными гофрированными оболочками являются наиболее широко применяемыми гибкими соединениями в трубопроводных коммуникациях ДЛА. Варьируя количество слоев, высоту и количество гофров, радиусы вершин и впадин, можно добиться необходимой циклопрочности сильфона при обеспечении таких важных параметров, как давление потери устойчивости , величины компенсируемых перемещении и т.п.
На рис. 1 приведены зависимости декрементов колебаний δ для одно-, двух-, трех- и четырехслойных оболочек (n - количество слоев) от амплитуды колебаний Ар, полученные в НИЛ гибких трубопроводных систем УГАТУ.
65
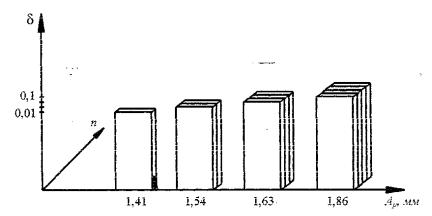
Рис.1 Зависимость декрементов колебаний гофрированных оболочек от амплитуды и числа слоев
Большой интерес представляют осредненные данные по декрементам колебаний (см. таблицу), полученные в СКТБ «Компенсатор» (г. Санкт-Петербург) для многослойных СК, состоящих из стальных гофрированных оболочек (С) со специальными демпфирующими покрытиями (Д) и перфорированными оболочками (П) между слоями. Однако такие компенсаторы очень трудоемки в изготовлении, а следовательно, дороги; кроме того, они имеют ограниченные пределы регулирования характеристик упругости и демпфирования.
Dy CK |
Структура СК |
δ |
|
|
|
100 мм |
С+С+С |
0,03 |
|
|
|
100 мм |
С+Д+П+С |
0,09 |
|
|
|
200 мм |
С+С+С+С |
0,003 |
|
|
|
200 мм |
С+Д+П+С |
0,1 |
|
|
|
200 мм |
С+П+Д+П+С |
0,05 |
|
|
|
200 мм |
С+Д+П+С+П+Д+С |
0,13 |
|
|
|
|
66 |
|

2. В компенсаторах с демпфирующими вкладышами 1 во впадинах гофров 2 (рис. 2) деформация стенок гофров передается на вкладыши из металлорезины («сойферит») или из резины, что обеспечивает демпфирование колебаний. Габариты таких компенсаторов и их масса минимальны. Однако данный тип СК не применим там, где амплитуды колебаний велики, так как у этих компенсаторов сравнительно невысокая степень демпфирования. Увеличение коэффициента рассеяния энергии Ψ происходит всего на 40 - 60% по сравнению с обычными СК.
В процессе деформирования гофров с демпфирующими вкладышами (см. рис. 2) возникает неблагоприятное распределение напряжении и деформации по профилю. Этого недостатка лишены СК с демпфирующими вкладышами /, выполненными в виде металлического кольца ( рис. 3). В сочетании с многослойной гофрированной оболочкой 2 такие СК, по мнению авторов, представляются перспективными.
Рис.2 Компенсатор с демпфирующим вкладышем из металлорезины: 1 – вкладыш; 2 – впадина гофра
Рис.3. Компенсатор с металлическим демпфирующим вкладышем: 1 – вкладыш; 2 – гофрированная оболочка
67

3. Компенсаторы с выносными демпферами 1 (рис.4) рационально использовать в тех случаях, когда их габариты не имеют принципиального значения. Статическая и динамическая нагрузки, воспринимаемые фланцами 2 компенсатора, передаются через шток 3 и расположенный на нем грибовидный элемент 4 на демпфирующие элементы 5 из металлорезины. Корпус демпфера 1
Рисунок 4 - Компенсатор с выносным демпфером:
1 – корпус демпфера; 2 – фланец; 3 - шток; 4 – грибовидный элемент; 5 – демпфирующий элемент; 6 - тяга
и грибовидный элемент 4 спрофилированы таким образом, что поперечные, продольные, угловые перемещения фланцев воспринимаются демпфирующими элементами 5. Корпус демпфера 1 с помощью тяги 6 связан со вторым фланцем компенсатора. Основным преимуществом таких компенсаторов является возможность варьирования в больших пределах их упругодемпферных характеристик, а недостатками - большие габариты и масса.
4. Компенсаторы с коаксиально расположенными относительно сильфона 1 демпферами 2 (рис. 5) могут иметь демпфирующие элементы, расположенные как внутри, так и снаружи сильфона. Принцип работы таких компенсаторов аналогичен изложенному в пункте 3. Преимуществом их конструкции является возможность достаточно широкого
68

варьирования упругодемпферных характеристик, а также небольшие габариты и масса.
Рисунок 5 - Компенсатор с коаксиально расположенным демпфером: 1 – сильфон; 2 - демпфер
Каждый из рассмотренных выше типов компенсаторов имеет свои преимущества и недостатки, поэтому выбор конкретной конструкции зависит от требовании технического задания.
Литература:
1.Старцев Н.И. Трубопроводы газотурбинных двигателей. М.: Машиностроение, 1976.
2.Итбаев В.К. Исследование диссипативных свойств гофрированных оболочек с жидкостью при вынужденных колебаниях. Вестник УГАТУ. 2001, № 1.
Получено: |
Воронежский государственный |
15.12.2003 |
технический университет |
.
69
УДК 621.78
ИССЛЕДОВАНИЕ КОНСТРУКТИВНОЙ ПРОЧНОСТИ СТАЛИ 12Х18Н10
А.Н. Семичев, А.Н. Осинцев, А.Н. Скребова
Хромникелевые стали аустенитного класса типа 18-8 обладают целым рядом несомненных достоинств. Они высокотехнологичны при получении изделий методами обработки металлов давлением (ОМД) и сваркой, экологически чисты, коррозионностойки, немагнитны, сохраняют достаточную пластичность вплоть до криогенных температур. Однако круг упрочняющих обработок этих сталей как правило ограничивается пластической деформацией, позволяющей сочетать эффекты наклепа с возможным переходом неустойчивого аустенита в мартенсит деформации. Эффективность такого упрочнения во многом может определяться исходной структурой стали перед пластическим деформированием.
В работе исследовалась сталь 12Х18Н10 после различных видов термической обработки (Т.О.) с последующей пластической деформацией путем одноосного растяжения на 20%. Температура нагрева при Т.О. была 1150 0С, что гарантировало максимальное растворение карбидной фазы в аустените. Выбранные виды термообработки (отжиг, нормализация, закалка в воду) не меняли фазовый состав стали, но ввиду разной скорости охлаждения могли повлиять на количество, размер и местовыделение карбидов хрома типа М23С6, уровень термических напряжений и концентрацию точечных дефектов. Анализ полученных результатов подтверждает эти предположения.
Во всех случаях после термообработки наблюдалась однотипная аустенитная структура с карбидными включениями, число и размеры которых уменьшались с ростом скорости охлаждения, но влияние режимов термообработок на механические свойства неоднозначно (табл. 1).
Так наибольшие значения прочностных характеристик (ζb и ζ0,2) имели образцы охлажденные с повышенными скоростями, при этом нормализация, сохраняя возможность протекания диффузионных процессов, приводила к некоторому увеличению
70
карбидных выделений, что повышало значение предела прочности ζb и снижало относительное сужение ψ, а соответственно давало незначительный уровень истинного разрушающего напряжения Sк, по сравнению с закалкой и даже отпуском. Пластичность стали 12Х18Н10 сохранялась на высоком уровне: относительное удлинение δ находилось в интервале 51-53%, а ψ – 69-74%. После всех видов термообработок условный предел текучести (ζ0,2) оставался весьма низким: 239-253 МПа, что с одной стороны говорит о невысокой конструктивной прочности, характеризуемой показателем надежности материала в виде отношения ζ0,2/ ζb, которое находилось вблизи значения 0,4, но с другой стороны дает перспективу как эффективного деформационного упрочнения за счет наклепа, так и успешного использования структурного состояния после такой обработки заготовок для формоизменяющих операций ОМД.
|
|
|
|
|
|
|
Таблица 1 |
|
|
|
Свойства стали после термообработки |
|
|
||||
Вид |
ζ0,2, |
ζb, |
Sк, |
δ, % |
ψ, % |
ζ0,2/ ζb |
|
ζb/ ζ0,2 |
Т.О. |
МПа |
МПа |
МПа |
|
||||
|
|
|
|
|
||||
Отжиг |
239 |
618 |
1800 |
52 |
74 |
0,39 |
|
2,6 |
Норма- |
250 |
642 |
1577 |
51 |
69 |
0,39 |
|
2,6 |
лизация |
|
|||||||
|
|
|
|
|
|
|
|
|
Закалка |
253 |
623 |
1908 |
53 |
74 |
0,40 |
|
2,5 |
Вне зависимости от вида проведенной термообработки последующая пластическая деформация растяжением на 20% (табл.2) приводила к заметному, на 15-20% росту ζb и значительному (более чем в два раза) повышению условного предела текучести при хорошем уровне относительного сужения (ψ=67-69%), что давало хорошее значение характеристики надежности близкое к 0,9. Однако способность стали к равномерной деформации снизилось (δ упало до 35-32%).
В выбранных условиях эксперимента наилучшим режимом предварительной обработки, дающим структуру с оптимальным набором механических свойств, следует считать нормализацию стали 12Х18Н10 с последующей пластической деформацией. Это вероятно связано с тем, что формирование механических свойств определяется не только составом фаз и их морфологией, но и
71

одновременно действующими несколькими механизмами торможения дислокаций, обеспечивающих как упрочнение, так и условия вязкого течения, гарантирующего повышенную надежность материала.
Таблица 2 Свойства стали после термической обработки и пластической
деформации
Вид |
ζ0,2, |
ζb, |
Sк, |
δ, % |
ψ, % |
ζ0,2/ ζb |
ζb/ ζ0,2 |
|
обработки |
МПа |
МПа |
МПа |
|||||
|
|
|
|
|||||
Отжиг + |
629 |
730 |
1655 |
32 |
67 |
0,86 |
1,2 |
|
εпл |
||||||||
|
|
|
|
|
|
|
||
Норма- |
|
|
|
|
|
|
|
|
лизация + |
662 |
762 |
1845 |
34 |
69 |
0,86 |
1,2 |
|
εпл |
|
|
|
|
|
|
|
|
Закалка + |
645 |
750 |
1820 |
35 |
69 |
0,86 |
1,2 |
|
εпл |
||||||||
|
|
|
|
|
|
|
Важным показателем конструктивной прочности материала является его сопротивление наиболее опасным – циклическим нагрузкам. Одним из параметров, дающих экспресс-заключение о циклической стабильности структуры, является отношение предела прочности к условному пределу текучести.
Из данных, приведенных в табл. 1 и 2, видно, что любая из предложенных термических обработок создавала циклически упрочняемую структуру ((ζb/ ζ0,2) >1,4), характерную для пластичных материалов, в то время как последующая пластическая деформация переводила сталь 12Х18Н10 в разряд циклически стабильных материалов (1,4 (ζb/ ζ0,2) 1,2), что дает хорошие гарантии на ее использование при заготовлении деталей, работающих в усталостном режиме.
Анализ изломов образцов и машинных диаграмм показал, что во всех случаях разрушение носило явно вязкий характер (поверхность излома матовая, излом волокнистый, скорость распространения трещины мала). Тем не менее установлено отличие в механизмах второго этапа разрушения – (распространение трещины) при различных технологиях предварительной обработки стали. Так образцы с максимальными значениями Sк, которые обрабатывались по схеме Т.О.+εпл, имели ―двухчашечный‖ вид изломов, соответствующий схеме распространения трещины с
72