
2890
.pdf
14.09.2003 |
технический университет |
УДК 621.9.047
РАСЧЕТ ЭЛЕКТРОДА-ИНСТРУМЕНТА НЕЖЕСТКОЙ КОНСТРУКЦИИ
М.Г. Поташников, С.В. Синегубова
Разработана методика проектирования электрода-инструмента (ЭИ) нежесткой конструкции, с учетом влияния геометрических характеристик рабочей поверхности ЭИ и детали на технологические параметры процесса электрохимической обработки (ЭХО)
В результате проведенных теоретических и экспериментальных исследований была разработана новая конструкция ЭИ нежесткой конструкции с изменяющейся по длине толщиной эластичной оболочки. Данная конструкция позволяет обеспечивать расчетный межэлектродный зазор (МЭЗ), при изменяющейся форме и площади поперечного сечения канала, на протяжении всего процесса обработки при значительном снижении избыточного давления внутри камеры, что повышает точность процесса обработки и позволяет увеличить ресурс работы инструмента.
Проектирование ЭИ и расчет технологических параметров процесса ЭХО каналов, произвольного контура с переменными по длине сечениями, катодами нежесткой конструкции предлагается проводить в следующей последовательности:
На основании выбранного способа обработки и исходных данных (материал заготовки, диаметр обрабатываемого канала, шероховатость поверхности до и после ЭХО, состав электролита) определяют МЭЗ. Поскольку в рассматриваемой схеме обработки МЭЗ в процессе анодного растворения не регулируется, следует выбирать такой размер зазора, при котором возможно достигнуть оптимальную скорость съема металла и точность формообразования /1/. Рекомендуемая величена МЭЗ:
so 0,3...1,0 мм.
1. Находят предельный ток, который может быть подан в рабочую зону:
I1 iF,
43

где i – удельный ток, зависит от материала и метода охлаждения катода;
F – площадь сечения токоподводов, через которые можно пропускать ток.
2. Находят длину рабочей части катода, которая зависит от предельной величины тока, подаваемого в рабочую зону:
Lp |
|
2I1 |
|
, |
(D |
ho ) J |
|
||
|
а пред |
где Ja пред – предельная плотность тока.
Предельная величина плотности тока Ja пред в приведенной
выше формуле должна обеспечивать требуемое качество поверхности, точность. Для большинства сплавов с увеличением плотности тока шероховатость поверхности снижается. По рассчитанной силе тока назначают источник питания и уточняют длину рабочей части катода. Длина рабочей части катода должна находиться в диапазоне 80...150 мм. Если расчетная длина катодных пластин находится вне указанного диапазона необходимо изменить материал катодных пластин и повторить расчет с пункта 2.
3. Рассчитывают скорость анодного растворения
U , s0
где — выход по току; — электрохимический эквивалент;
— удельная проводимость электролита; U — напряжение используемое на анодное растворение металла заготовки; — плотность обрабатываемого материала.
4. Рассчитывают время ЭХО
Lуч.об ,
прод .
где L у ч.об. — длина участка обработки; прод . — скорость
продольной подачи инструмента.
Скорость продольной подачи инструмента определяется как
|
|
U |
0 |
|
дет |
|
Lуч.обр |
, |
|
|
|
|
|
||||
прод . |
h0 2s0 |
|
|
|
|
|||
|
доп |
|
0 |
|
дет |
|
где дет — погрешность детали.
44
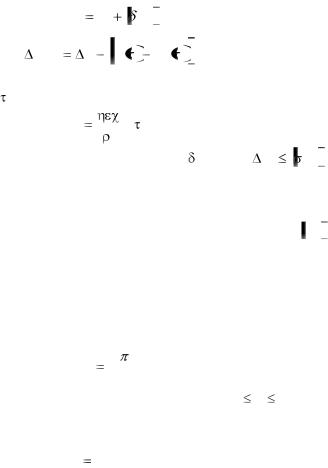
5. Рассчитать припуск на операцию, минимальный припуск рассчитывают в зависимости от допуска на деталь и глубины анодного растворения:
|
zmin |
|
y1 |
дет . |
|
|
6. Рассчитать точность обработки |
|
|
||||
|
дет |
0 y1 |
y2 |
, |
|
|
где y1 |
и y2 — съем металла в конце обработки на участках с |
|||||
зазорами s1 |
и s2; — время обработки. Съем металла в этом случае |
|||||
определяется по формуле y1 |
|
U |
. Рассчитанная погрешность |
|||
|
h 0 |
|||||
|
|
|
|
|
|
|
должна быть в пределах допуска на деталь [ |
дет], т.е. дет |
дет . |
Если рассчитанная величина находится за пределами допуска на деталь необходимо изменить МЭЗ или минимальный припуск и провести расчет точности повторно /2/.
7. Рассчитать шероховатость процесса, если R a
необходимо изменить время обработки или МЭЗ и провести повторный расчет шероховатости.
8. Рассчитать ширину катодных пластин и их количество, согласно следующей последовательности:
1.Назначить ширину катодной пластины В0=3 — 6 мм; 2.Рассчитать количество катодных пластин
mn |
|
1 |
|
|
D |
, |
|
|
|
|
|
||||||
|
|
2 B0 |
||||||
полученное значение округлить до целого и уточнить 3 B 6 |
||||||||
9. Рассчитать угол наклона катодных пластин относительно |
||||||||
продольной оси катода. |
|
|
|
|
|
|
|
|
α |
arctg |
2B |
|
|||||
Lр |
||||||||
|
|
|
|
|
В связи с тем, что процесс ведется без вращения инструмента или заготовки, пластины располагаются таким образом, чтобы отсутствовали участки с повторной обработкой за один проход катода.
На основании данной методики, был разработан алгоритм проектирования технологического процесса ЭХО каналов переменного сечения катодами нежесткой конструкции. Алгоритм позволяет составить оптимальную структуру технологического
45
процесса и спроектировать ЭИ оптимальной конструкции и геометрии на этапе конструкторско-технологической подготовки производства.
Литература:
1.Смоленцев В.П. Метод определения точности электрохимической обработки каналов переменного сечения катодами нежесткой конструкции / В.П. Смоленцев, М.Г. Поташников // Динамика технологических систем: Сб. тр. VI Междунар. науч.-техн. конф.: В 3 т. Ростов н/Д: ДГТУ, 2001. Т 1. С.
260-263.
2.Поташников М.Г. Моделирование процесса электрохимической обработки каналов произвольного контура с переменными по длине сечениями // Нетрадиционные технологии в машиностроении и приборостроении. Межвуз. сб. науч. тр. Воронеж: ВГТУ, 2001. Вып. 4. С. 102-107.
Получено |
Воронежский государственный |
20.11.2003 |
технический университет |
УДК 621. 92 |
|
ВЛИЯНИЕ ПАРАМЕТРОВ ПРОЦЕССА МИКРОРЕЗАНИЯ НА ИМПУЛЬС СИЛЫ МИКРОРЕЗАНИЯ
Ерѐмин М.Ю.
Динамические показатели в зоне контактирования абразивного инструмента с обрабатываемой поверхностью оказывают важное влияние на качество обработки неметаллических материалов. Поэтому для решения проблемы повышения качества шлифованных поверхностей хрупких высокопрочных материалов актуальным является исследование процессов, происходящих при алмазном дискретном микрорезании связанным зерном.
Для установления влияния параметров процесса микрорезания на динамические показатели в зоне контактирования абразивного зерна с обрабатываемой поверхностью проведены эксперименты по микрорезанию поликристаллических и аморфных материалов. Исследовали влияние режимов резания и геометрии микрорезца на
46
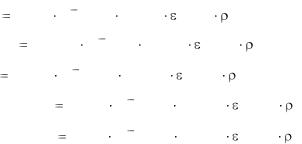
динамику процесса микрорезания. В экспериментах использовались алмазные инденторы с различными углами при вершине.
Микрорезание неметаллических хрупких материалов алмазным индентором показало, что увеличению скорости резания с 30 до 50 м /с вызывает снижение импульса силы микрорезания. При этом величина снижения импульса силы микрорезания во многом зависит от структуры и физико-механических свойств материала детали. Так, для поликора с ростом скорости резания импульс силы микрорезания снижается на 16,9 %, для керамики - на 12 %. Для поликристаллических ферритов 1000НТ1 и 2000МТ1 снижения величин импульса силы микрорезания соответственно составили 13,9 и 18,5 %, а для аморфного стекла - 41,5 %.
Глубину микрорезания t изменяли в диапазоне 5-100 мкм. Определено, что изменение глубины внедрения алмазного индентора в обрабатываемый материал вызывает значительное возрастание импульса силы микрорезания. Определено, что наибольшие значения импульса силы возникают при микрорезании поликора. Анализ следов микрореза показал, что значительные силовые нагрузки в зоне контакта резца и поликора способствуют возникновению большого градиента контактной температуры.
Статистическая обработка экспериментальных данных позволила получить степенные зависимости, отражающие влияние скорости резания VP, глубины микрорезания t, угла при вершине алмазного индентора и радиуса округления вершины
на показатель импульса силы микрорезания JC.
Для поликора, стела, керамики, ферритов 1000 НТ и 2000 МТ соответственно получены следующие результаты:
Jcпол |
1,4794 Vp 1,3161 |
t1,0100 |
1,2935 0,2091 , |
|
(1) |
||||||
Jcстекло |
54,7174 |
Vp 3,147 |
t1,4575 1,3122 |
0,2054 , |
(2) |
||||||
Jкер |
2,0589 |
V |
1,4145 |
t0,9926 |
1,2723 |
0,2022 , |
|
(3) |
|||
|
c |
|
|
p |
|
|
|
|
|
|
|
J |
фер.1000 |
НТ1 |
0,7926 |
V |
1,1828 |
t 0,9396 |
1,2829 |
0,2129 , |
(4) |
||
|
c |
|
|
|
|
p |
|
|
|
|
|
J |
фер.2000 |
МТ1 |
1,6383 |
V |
1,4198 |
t 0,9941 |
1,2375 |
0,2177 . |
(5) |
||
|
c |
|
|
|
|
p |
|
|
|
|
|
Анализ экспериментальных данных показывает, что структура материала оказывает существенное влияниена показатель импульса силы микрорезания, но в рамках близких структур (ферриты 1000 НТ1
47

и 2000 МТ1) закономерности очень близки и отличаются друг от друга незначительно.
Получено: 15.12.2003 |
Воронежский аграрный университет |
УДК 621. 92
ДИНАМИЧЕСКИЕ ПОКАЗАТЕЛИ ПРОЦЕССА ШЛИФОВАНИЯ
Ерѐмин М.Ю.
Считается, что отношение сил РУ / РZ является наиболее стабильным показателем процесса резания при шлифовании. С уменьшением этого отношения повышается доля затрат энергии на разрушение материала и соответственно снижаются затраты энергии на трение и в целом на работу разрушения.
В этом плане представляются важными полученные соотношения между составляющими сил микрорезания, которые при дальнейших расчѐтах взяты за основу
Основываясь на экспериментальных данных А.А. Сагарда, получил подтверждение, что при микрорезании единичным алмазным зерном ( = 40 мкм) Стали 45 и твѐрдого сплава ВК6 по
мере внедрения сферической |
части |
зерна отношение РУ / РZ |
|
уменьшается. Это отношение зависит от угла заострения |
и равно |
||
Рz / Py |
1 1,8 1 |
. |
(1) |
При прерывистом шлифовании силы микрорезания могут быть в одних случаях больше, а в других меньше сил микрорезания обычного шлифования. Чтобы избежать ошибок при выборе приоритетного направления в моделировании процессов микрорезания, мы предпочтителен путь, основанный на поиске взаимосвязей сил резания и импульса сил микрорезания. Для этих целей были проведены серии опытов и использованы ранее полученные данные, которые показывают взаимосвязи сил резания
48
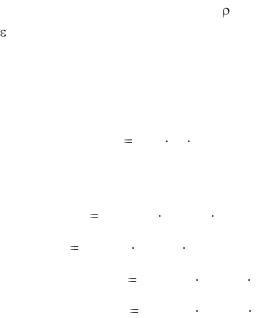
(на примере составляющей РZ и импульса сил микрорезания JС при разных глубинах шлифования (микрорезания), присущие различным материалам.
Микрорезание и шлифование проводилось при скорости VP = 40 м/с, радиус округления индентора = 2,5 мкм, угол при вершине = 1200; круг АС4 125/100 М08 100. Устанавливая зависимости, исходили из соображения, что степенная функция наиболее близко описывает процесс резания и микрорезания и их взаимосвязи. Введение коэффициента АКМ позволяет учитывать изменяющиеся условия обработки. Поэтому использовали
зависимость |
|
P |
A |
км |
tb Jc |
|
, |
(2) |
|
|
z |
|
c(мi) |
|
|
||
где АКМ, b, с – коэффициенты модели; JС(Мi) – импульс силы |
||||||||
микрорезания исследуемого материала. |
|
|
|
|||||
Рстеклоz |
775,4693 |
t 0,6868 |
J с0,1592 ; |
(3) |
||||
Ркерz |
210,512 |
t0,3163 Jс0,1000 ; |
(4) |
|||||
Рферz .1000 НТ1 |
120,2335 t 0,4921 Jс0,1000 ; |
(5) |
||||||
Рферz .2000 МТ1 |
131,7698 t 0,5198 Jс0,1000 . |
(6) |
Для расчѐта коэффициентов модели по экспериментальным данным использован метод наименьших квадратов. Использование данных методами Симплекс, Квазиньютон, Хука-Дживса, а также совместного решения методами Розенброк и Квазиньютон показали, что для исследуемых материалов наиболее близки к физикохимическим процессам, протекающим при разрушении хрупких неметаллических материалов алмазным микрорезцом, математические модели 3 – 6, которые представлены соответственно для стекла, керамики, ферритов 1000 НТ1 и 2000 МТ1.
Получено: 15.12.2003 |
Воронежский аграрный университет |
УДК 621.002.5
ОБОСНОВАНИЕ ЦЕЛЕСООБРАЗНОСТИ ПРИМЕНЕНИЯ
49
ТЕХНОЛОГИЧЕСКОГО ОБОРУДОВАНИЯ
С.Н.Яценко
Встатье с теоретических позиций представлен один из методов рационального выбора технологического оборудования, основывающийся на едином критерии экономической эффективности - минимуме затрат живого и овеществленного общественного труда на достижение заданных результатов производственного процесса.
Вусловиях современного машиностроительного производства нередко складывается ситуация, когда какое-либо изделие может быть изготовлено несколькими взаимозаменяемыми средствами или методами. Такие средства и методы могут иметь различные характеристики: производительность, стоимость, мощность, требования к производственным условиям, качественно обеспечивая одинаковые конечные результаты. Так, например, выполнение конкретного технологического процесса обработки партии валов может осуществляться с применением различного металлорежущего оборудования. Возможно применение универсальных токарных, токарно-револьверных станков, токарных автоматов. Именно в таких случаях возникает необходимость обоснования целесообразности применения той или иной модели технологического оборудования.
При этом методы выбора экономически эффективного оборудования должны соответствовать решаемым задачам, обусловленным уровнями и этапами технической подготовки производства. На уровне рабочего места задача рационального выбора технологического оборудования заключается в отборе из возможного ряда взаимозаменяемого оборудования одной модели, которая обеспечивала бы выполнение требуемой технологической операции с минимальными затратами. На уровне более крупного структурного подразделения (участка, цеха) задача выбора оборудования сводится к определению оптимального комплекта технологического оборудования, которым оснащается это подразделение.
Однако методы отбора технологического оборудования всегда должны удовлетворять одному условию. Несмотря на уровень и этап технической подготовки производства, они должны базироваться на едином критерии экономической эффективности – минимуме затрат
50
живого и овеществленного общественного труда на достижение заданных результатов производственного процесса. Важно, чтобы создание и использование каждого нового конструкторскотехнологического решения, каждой единицы оборудования приводило не только к перераспределению количества труда между различными производственными сферами, а к его общей экономии.
Единство критерия экономической эффективности дает возможность согласования методов выбора технологического оборудования на разных уровнях и этапах технической подготовки производства. В основу такого согласования может быть положена система, базирующаяся на разработке комплекта документации, регламентирующей использование технологического оборудования в различных производственных условиях с целью достижения высокого уровня экономической эффективности производства /1/. Подобная документация иллюстрировала бы возможные экономически эффективные области использования технологического оборудования.
Разработка подобной системы складывается из двух стадий. Во-первых, необходимо построить ряды взаимозаменяемого оборудования для изготовления технологически однотипных групп изделий и определить области экономически эффективного использования оборудования, включенного в ряды. Эти действия выполняются с целью создания эталонов экономически эффективных областей использования технологического оборудования. Во-вторых, требуется разработать систему применения эталонов в процессе подготовки производства внутри структурного подразделения (участка, цеха, машиностроительного предприятия).
Необходимо учесть, что на первом этапе разработки системы важно провести анализ экономической эффективности использования всего ряда моделей взаимозаменяемого оборудования, которое можно в принципе применить для выполнения заданной работы, а не ограничиваться только анализом использования новой модели взамен устаревшей. Только в этом случае можно обеспечить максимальную объективность результатов выбора оборудования. Кроме того, необходимо определить границы, разделяющие области экономически эффективного использования оборудования. Область экономически эффективного использования технологического оборудования представляет собой интервал
51
изменения объема производства продукции, ограниченный минимальными и максимальными его значениями, в котором применение данного способа или средства обеспечивает по сравнению с другими способами или средствами относительно меньшие затраты /2/.
Определение областей экономически эффективного использования оборудования может осуществляться в следующем порядке:
-соединение типовых объектов производства (полуфабрикатов, деталей, сборочных единиц) в технологически однородные группы;
-выбор типовых технологических процессов для изготовления технологически однородных групп объектов;
-построение рядов потенциально возможного взаимозаменяемого технологического оборудования для каждой операции типового технологического процесса;
-определение границ областей экономически эффективного использования той или иной модели оборудования из построенного ряда;
-построение схемы выбора оборудования.
Схема выбора оборудования обычно представляет собой систематизированное выражение типового маршрутного технологического процесса изготовления определенной технологически однородной группы изделий. Схемы выбора оборудования должны периодически обновляться и дополняться с учетом изменений, вызванных научно-техническим прогрессом.
Литература:
1.Градов А.П. Технический уровень производства предприятия. Методы анализа и количественной оценки. Л.: ЛПИ. 1973. 93 с.
2.Экономика машиностроения. Под ред. Иванова Н.А., Мечковского Г.И. М.: Высш. школа. 1976. 423 с.
Получено: |
Воронежский государственный |
18.12.2003 |
технический университет |
52