
2558
.pdf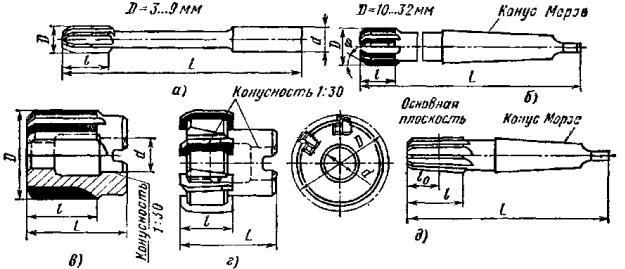
ного назначения. Для удобства введения развертки в отверстие служит участок А. Его наличие вызвано малыми глубинами резания, характерными для развертывания, и малыми углами в плане θ < 15°.
Рис. 2.4. Конструкции разверток:
а — машинная быстрорежущая с цилиндрическим хвостовиком; б — машинная твердосплавная с коническим хвостовиком;
в — насадная с режущей частью из твердого сплава; г — насадная с вставными быстрорежущими ножами; д — для отверстия
под коническую резьбу
У разверток для глухих отверстий этот участок может отсутствовать, так как он выполняется совместно с заборным конусом Б. Последний несет режущие элементы, выполняющие основную работу резания. Зуб на этом участке имеет геометрию режущей части с
углами γр и αр.
Участок В — калибрующий, выполняется цилиндрическим, а участок Г представляет собой обратный конус, чтобы обеспечить высокое качество обработанной поверхности при вынимании развертки из отверстия. На калибрующей части имеется передний γк и задний αк углы. Обычно αк = 0 для сохранения необходимого диаметра развертки при переточках. Это вызвано высокой точностью
81
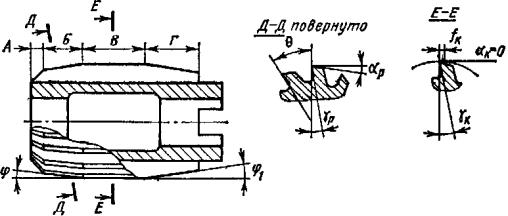
чистового развертывания (6...9 квалитет) и стремлением увеличить срок службы инструмента.
Рис. 25. Геометрические параметры цельной насадной развертки
У разверток с винтовым зубом угол подъема винтовой линии ω также характеризует геометрию. Следует отметить, что развертки могут иметь зубья как с правой, так и с левой винтовой линиями.
Зубья развертки чаще всего располагаются по окружности равномерно θ = 360º / z.
В ряде случаев делают угол θ переменным. Например, при
z = 10 угол θ изменяют в следующем порядке от зуба к зубу: 33°15', 34°32', 36°, 37°28', 38°45' и т. д. Это позволяет в ряде случаев повысить качество обработанной поверхности.
2.7. РАСЧЕТ И КОНСТРУИРОВАНИЕ ФРЕЗ
Фрезерование широко применяют в машиностроении и приборостроении для обработки различных поверхностей корпусных и призматических деталей, а также винтовых поверхностей деталей тел вращения. В машиностроении фрезерные станки составляют 10…20 % общего парка металлорежущих станков. Имеются производства, где фрезерные станки составляют до 50 % парка станков на
82
заводе. Метод фрезерования является высокопроизводительным, простым и в ряде случаев достаточно точным.
Фреза — многолезвийный вращающийся режущий инструмент, зубья которого последовательно вступают в контакт с обрабатываемой поверхностью в процессе резания. Относительно медленная подача производится движением обрабатываемой детали, закрепленной на столе фрезерного станка.
В зависимости от вида обрабатываемой поверхности равномерное движение подачи может быть прямолинейнопоступательным, вращательным или винтовым. Фрезерованием выполняют разнообразные операции, что обусловило значительное разнообразие типов, форм, конструкций и размеров фрез, используемых на универсальных фрезерных станках, так и специальных, проектируемых для обработки конкретных изделий.
Отклонения размеров деталей после обработки фрезерованием могут находиться в пределах 7…9-го квалитетов (ГОСТ 25347—82) при параметрах шероховатости до Rа = 1,25 мкм (ГОСТ 2789—73).
2.7.1. Классификация фрез
Классификацию фрез проводят по следующим показателям.
По расположению зубьев относительно оси различают: фрезы цилиндрические с зубьями, расположенными на поверхности цилиндра (рис. 26, а), фрезы торцовые с зубьями, расположенными на торце цилиндра (рис. 26, б), фрезы угловые с зубьями, расположенными на конусе (рис. 26, в), фрезы фасонные с зубьями, расположенными на поверхности с фасонной образующей (рис. 26, г) (с выпуклым и вогнутым профилем). Некоторые типы фрез имеют зубья как на цилиндрической, так и на торцовой поверхности, например дисковые двух- и трехсторонние (рис. 26, д), концевые (рис. 26, е), шпоночные (рис. 26, ж, з).
По направлению зубьев фрезы могут быть прямозубыми (рис. 26, д), в которых направляющая линия передней поверхности лезвия прямолинейна и перпендикулярна направлению скорости главного
83
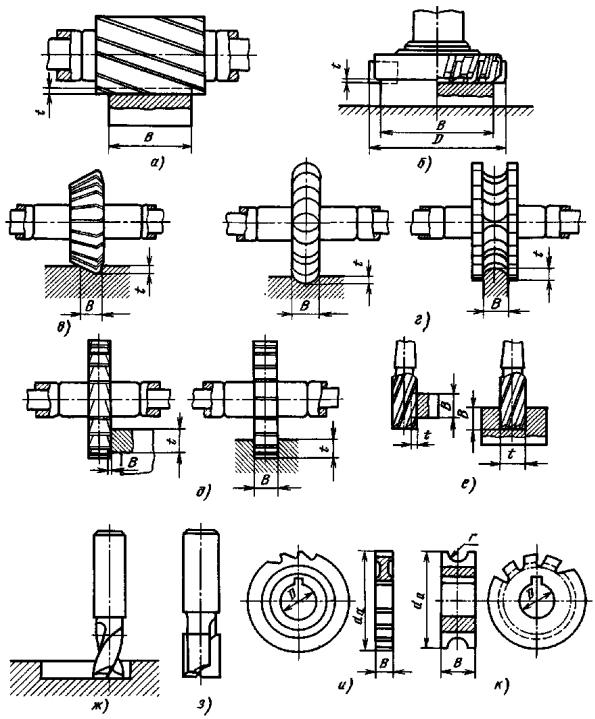
Рис. 26. Типы фрез и обрабатываемых поверхностей:
а— цилиндрическая; б — торцовая; в – угловая; г – фасонные;
д— дисковые двух- и трехсторонняя; е — концевые;
ж, з — шпоночные; и — с острозаточенными зубьями; к — с затылованными зубьями
84
движения резания (под направляющей линией передней поверхности понимают линию, по которой движется точка прямой, описывающей эту поверхность), косозубые (рис. 26, г), у которых направляющая линия передней поверхности лезвия прямолинейна и наклонена под углом к направлению скорости главного движения резания, с винтовым зубом (рис. 26, а), в которых направляющая линия передней поверхности является винтовой.
По конструкции фрезы могут быть, цельными, составными, например с припаянными или приклеенными режущими элементами, сборными, например оснащенными многогранными пластинами из твердого сплава; наборными, состоящими из нескольких отдельных стандартных или специальных фрез и предназначенные для одновременной обработки нескольких поверхностей.
По способу крепления на станке различают фрезы насадные с отверстием под оправку и концевые с коническим или цилиндрическим хвостовиком.
Фрезы цельные - зубья цельных фрез выполнены как одно целое с корпусом из быстрорежущей стали. Их делают насадными для закрепления на оправке станка (это наиболее распространенный тип фрез) и с цилиндрическим или коническим хвостовиками для непосредственного закрепления в гнезде шпинделя станка или патрона. Хвостовыми изготовляют преимущественно фрезы малого диаметра, которые нельзя выполнить насадными. Хвостовики делают из конструкционной стали и приваривают встык к рабочей части из быстрорежущей стали.
Сборные фрезы более экономичны. Корпуса таких фрез делают из конструкционных сталей, обычно стали 40Х, а ножи (зубья) из режущих материалов или конструкционных сталей с напаянными, приклеенными или механически закрепленными режущими пластинками. Ножи крепятся в пазах корпусов клиньями, штифтами, винтами и другими способами.
Для повышения производительности фрезы всех разновидностей оснащают твердыми сплавами. Однако следует иметь в виду, что из-за повышенной хрупкости твердого сплава и ударной нагруз-
85
ки при входе и выходе зуба из резания не все твердосплавные фрезы одинаково работоспособны. Фрезы с жесткими корпусами, такие, как торцовые, успешно работают при фрезеровании любых конструкционных материалов. Другие разновидности твердосплавных фрез с недостаточной жесткостью корпусов, особенно отрезные и дисковые, хорошо зарекомендовали себя при обработке чугуна и цветных металлов, где усилия резания сравнительно небольшие. Обработка стали такими фрезами также производится, но при тщательной отладке операции, заключающейся в обеспечении надлежащей жесткости станка, приспособления, детали, достаточной плавности подачи стола станка, равномерности вращения его шпинделя, выбора наиболее подходящих марок твердого сплава и оптимизации параметров инструмента.
Наиболее рациональным способом крепления пластинок твердого сплава является механическое крепление, устраняющее дефекты напайки пластин. Самыми прогрессивными среди них следует считать конструкции с механическим креплением неперетачиваемых многогранных пластинок твердого сплава, используемых для сборных конструкций резцов.
Широкое применение получили сборные фрезы с ножами или резцами, в гнездах которых пластинки твердого сплава напаиваются или приклеиваются. Основное их преимущество по сравнению с фрезами, оснащенными неперетачиваемыми пластинками, состоит в том, что конструкция — повышенной жесткости и позволяет разместить больше режущих зубьев. Конструктивное оформление основных типов таких фрез такое же, как и с быстрорежущими пластинчатыми ножами, только поперечное сечение ножей несколько больше.
Отличаются от быстрорежущих торцовые фрезы для обработки стали. В связи с большими силами резания ножи выпускают с крупным сечением, наподобие токарных резцов, и закрепляют в корпусе различного рода клиньями.
У фрез малых размеров, которые не могут быть сделаны сборными, а также у относительно крупных концевых, цилиндрических
86
и торцовых фрез с винтовыми пластинками твердого сплава, пластинки напаиваются или наклеиваются непосредственно на корпуса.
Мелкоразмерные твердосплавные фрезы делают целиком из твердого сплава или в виде твердосплавных коронок с зубьями, которые напаиваются на хвостовые державки.
По конструкции зубьев фрезы могут быть с острозаточенными (рис. 26, и) и затылованными (рис. 26, к) зубьями. Затылование — процесс образования задней поверхности инструмента по некоторой кривой (обычно спираль Архимеда) для получения задних углов. У острозаточенных фрез задние углы получают заточкой. Фрезы работают с малыми подачами на зуб, поэтому их изнашивание происходит по задней поверхности, и затачивать их целесообразно по задней поверхности. Однако такую заточку не всегда возможно и не всегда целесообразно выполнять. Форма производящей поверхности может быть сложной, исключающей возможность заточки задней поверхности зуба шлифовальным кругом. Нецелесообразно производить заточку задней поверхности у фрез с точным профилем, например у червячных зуборезных и шлицевых, потому что в этом случае нужно вновь обеспечить требуемую точность профиля и шага зубьев. Для приведенных случаев целесообразнее применять затылованные зубья, заточка которых производится по передней поверхности, что обеспечивает ее простоту.
2.7.2.Элементы конструкции
игеометрические параметры фрез
Элементы конструкции. Фрезы разных типов — это разновидности двух базовых конструкций: торцовой и цилиндрической. Поэтому схемы работы фрез сводятся к цилиндрическому (рис. 27, а) и торцовому (рис. 27, б) фрезерованию, а все фрезы имеют сходные элементы конструкции: тело 1, у сборных конструкций его называют корпусом, зубья 2, стружечные канавки 3 (рис. 27, а) и присоединительную часть для закрепления на станке и передачи крутящего момента в виде отверстия со шпоночной канавкой у насадных фрез
87
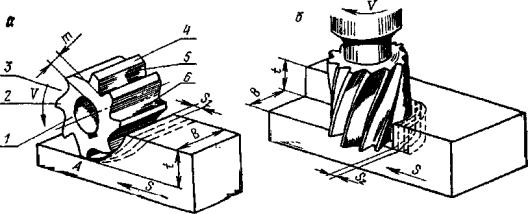
или в виде цилиндрического или конического хвостовика у концевых фрез. У торцовых фрез средних размеров крутящий момент передается шпоночным пазом на торце, а у крупных сборных конструкций — другими жесткими элементами. На каждом зубе фрезы различают переднюю поверхность 5, заднюю поверхность 4 и спинку зуба 5 (рис. 27, а).
Рис. 27. Фрезерование цилиндрической (а) и торцовой (б) фрезами
Для повышения плавности работы и повышения стойкости зубья фрез делают винтовыми.
Форма зубьев фрез разного назначения различна. Все они, за исключением фасонных, делаются с остроконечным зубом трех разновидностей: трапецеидальным, параболическим и усиленным, которые характеризуются параметрами, показанными на рис. 28.
Зубья трапецеидальной формы (рис. 28, а) наиболее, простые, но не прочные, для тяжелых работ непригодны, делаются только у фрез с мелким зубом, предназначенных для чистового фрезерования, при торцовом шаге зубьев t < 10 мм и отношении диаметра фрезы к числу зубьев D / z < 3.
Параболический зуб (рис. 28, в) представляет собой балку равного сопротивления изгибу и является наиболее рациональным для тяжело нагруженных фрез с t ≥ 10 мм и D / z ≥ 3, применяемых для чернового фрезерования.
88

Рис. 28. Формы остроконечных зубьев:
а — трапецеидальный; б — усиленный; в — параболический
Заменив параболу ломаной линией, образуют усиленный зуб, (рис. 28, б), который по прочности мало уступает параболическомy и получил более широкое распространение, так как его проще изготовить. С усиленным зубом делают фрезы для черновых работ и все фрезы, оснащенные пластинками твердого сплава.
Переточки остроконечных зубьев после затупления выполняют по наиболее изношенной, задней поверхности.
Зубья фасонных фрез делают в большинстве случаев затылованными, с криволинейной задней поверхностью, очерченной по гребню А участком АС кривой Архимеда (рис. 29).
При образовании задней поверхности на токарнозатыловочном станке по схеме рис. 29 фреза 1 равномерно вращается по стрелке v, а резец 2 с профилем изделия, обрабатываемого фрезой, равномерно подается кулачком 3 в радиальном направлении S. За один оборот кулачка с рабочим участком θр по спирали Архимеда фреза повернется на угловой шаг ε. Таким образом, в процессе затылования режущий контур Е΄АЕ резца постоянно лежит в радиальной плоскости фрезы. Поэтому профиль зуба фрезы в любом радиальном сечении одинаковый, соответствует профилю затыловочного резца, чего нельзя достичь при линейчатой форме задней поверхности зуба, выполненной по одной из схем рис. 28. В результате появляется возможность переточку зубьев фрезы после затупления упростить и производить по передней радиальной плоскости, а не
89

Рис. 29. Схема радиального затылования зуба фрезы
по фасонной задней поверхности. Это — единственное преимущество затылованного зуба. Во всех остальных отношениях он хуже: малое число переточек, больше шероховатость обработанной поверхности профиля детали и ниже стойкость фрез из-за неблагоприятной геометрии зуба. Поэтому в случае большого потребления одинаковых фасонных фрез их делают с остроконечным зубом и идут на дополнительные затраты по изготовлению специальных приспособлений для переточки фрез по задней поверхности.
Толщина тела фрезы m (см. рис. 27) выбирается минимальной по прочности.
Диаметр посадочного отверстия желательно иметь возможно большим с целью увеличения жесткости оправки, что позволит увеличить производительность фрезерования за счет увеличения подач, не опасаясь при этом вибраций.
Наружный диаметр фрез предпочтительно меньший, так как меньше крутящие моменты и больше производительность обработки за счет сокращения времени врезания. Однако это не всегда воз-
90