
2558
.pdfкремния черный — для шлифования материалов с низким пределом прочности (чугуна, бронзы, латуни и др.).
Карбид бора (В4С) получают при плавке борной кислоты и нефтяного кокса; по твердости приближается к алмазу и выпускается в виде порошков и паст для доводки твердосплавного инструмента и обработки твердых минералов, таких, как рубин, корунд, кварц.
Алмазы, в основном искусственные, нормальной, повышенной и высокой прочности, являются самыми твердыми материалами и обладают самой высокой режущей способностью. Поэтому их применяют для высококачественной и производительной обработки твердых сплавов, твердых минералов, цветных металлов и их сплавов.
Кубический нитрид бора по своим свойствам почти не уступает алмазу, но используется для обработки черных металлов (железосодержащих), так как химически инертен к железу и углероду.
Абразивные материалы имеют высокие красностойкость и износостойкость. Инструменты из абразивных материалов позволяют обрабатывать детали со скоростью резания 15…100 м/с. Абразивные материалы используют главным образом для изготовления инструментов для окончательной обработки деталей, когда к ним предъявляют повышенные требования по точности и шероховатости обработанных поверхностей.
1.7. Выбор инструментальных материалов
Инструментальный материал (ИМ) оказывает большое влияние на производительность обработки, качество обработанной поверхности и на конструкцию самого инструмента, т. е. является важнейшей характеристикой режущего инструмента.
Трудности выбора ИМ помимо сложности процесса резания и явлений, его сопровождающих, объясняются еще двумя причинами. Во-первых, в отличие от многих других характеристик или параметров инструмента выбор марок затруднен, так как не имеется одного
21
какого-либо надежного и общего комплексного численного критерия, по которому можно было бы осуществлять выбор. Во-вторых, число возможных сочетаний различных факторов, условий работы инструмента, существенно влияющих на выбор ИМ, огромно. Очевидно, что дать рекомендации для каждых конкретных условий не представляется возможным.
Имеющиеся опытные данные, а также рекомендации по выбору ИМ в различных стандартах и нормативах позволяют с большим или меньшим основанием выбрать марку ИМ. При этом, однако, учитывается обычно от двух до пяти факторов, что для правильного выбора ИМ часто совершенно недостаточно.
Изложенная ниже методика выбора марок ИМ учитывает большее число факторов, что позволяет сделать выбор более обоснованным.
При выборе марок ИМ необходимо учитывать: обрабатываемый материал; состояние поверхности заготовки; режимы резания (соответственно t, S, v); характер резания (прерывистое, непрерывное); тип производства (массовое, серийное, единичное); жесткость технологической системы; требуемая надежность инструмента; технология перетачивания инструмента (способ, трудоемкость, оборудование, инструмент для перетачивания); технология изготовления инструмента (ковка, прокат, литье, вышлифовка и др.); размеры инструмента (режущей части); угол β заострения лезвия; форма (размеры) профиля инструмента.
Наибольшее влияние на выбор ИМ оказывает скорость реза-
ния.
Некоторые из условий и в зависимости от вида инструмента и техпроцесса могут трактоваться различно. Например, размеры спиральных сверл могут оказывать влияние на выбор ИМ: сверла из кобальтовых сталей диаметром менее 5 мм показывают невысокую стойкость из-за ухудшения теплоотвода при малой массе лезвия сверла. Кроме того, сверла и другие инструменты малого диаметра (метчики, протяжки) при малых размерах часто работают с предельными напряжениями, и поэтому предпочтение имеют марки ИМ бо-
22
лее прочные и менее хрупкие. Для других видов инструмента, например, цельных стальных червячных фрез, характерно использование относительно больших диаметров (60…200 мм и более). Здесь размер инструмента, как показывает практика, может существенно повлиять на балл карбидной неоднородности, что особенно опасно для более твердых и хрупких марок ИМ.
Вообще технологические свойства инструментальных материалов, особенно сталей, в технической литературе освещены недостаточно и мало систематизированы, что затрудняет их учет при выборе ИМ. В то же время они могут иметь не только существенное, но в ряде случаев решающее значение при выборе той или иной марки ИМ.
При использовании таблиц соответствий возможны случаи, когда ни одна марка не допускается и не рекомендуется для заданных условий. Это означает, что при данных условиях использование всех рассмотренных марок будет неэффективно, а стойкость инструмента низкая. В таком случае надо прежде всего изменить исходные данные, что практически требует либо изменения режимов резания, либо других условий эксплуатации или изготовления инструмента. Можно также увеличить число рассматриваемых марок или решать вопрос о применении ИМ другой группы, например, твердого сплава вместо быстрорежущей стали. Возможен случай, когда допускаемых марок несколько. При автоматизированном проектировании должен быть предусмотрен дополнительный критерий или даже несколько критериев, используемых последовательно, с помощью которых из числа допускаемых марок выбирается одна. Такими критериями могут быть дефицитность, например, пропорциональная содержанию в марке вольфрама, стоимость, хрупкая или пластическая прочность и др. При неавтоматизированном проектировании окончательный выбор марки ИМ из числа найденных возможных может быть также осуществим с учетом их физико-механических свойств.
В случаях, когда разрабатывается новый технологический процесс, новое оборудование или инструмент, необходимо решать вопрос о выборе группы инструментальных материалов. Хотя имеются
23
известные теоретические основы, в окончательных рекомендациях ориентируются на экспериментальные данные, опыт промышленности и, как правило, необходимы экономические расчеты вследствие существенной разницы в стоимости ИМ разных групп.
Выбор марок ИМ связан с различными видами инструментов, работающих по разным кинематическим схемам.
Во всех случаях при выборе марок ИМ используются справочные таблицы. В ряде задач помимо таблиц необходимо также использовать технико-экономические показатели.
2.РЕЖУЩИЕ ИНСТРУМЕНТЫ
2.1.Основные принципы работы и конструктивные
элементы режущих инструментов
Режущие инструменты применяют для образования требуемых формы и размеров поверхностей заготовок резанием, срезанием сравнительно тонких слоев материала (стружки). Несмотря на большое различие отдельных видов инструментов по назначению и конструкции, у них имеется много общего: условия работы, общие конструктивные элементы и способы их обоснования, принципы расчета. Основные определения и обозначения общих понятий по режущим инструментам и обработке резанием даны соответственно в ГОСТ 25751—83 и ГОСТ 25762—83.
У всех режущих инструментов имеются рабочая и крепежная части. Рабочая часть выполняет основное служебное назначение — резание, удаление излишнего слоя материала. Крепежная часть служит для установки, базирования и закрепления инструмента в рабочем положении на станке (технологическом оборудовании).
В рабочей части различают участок с режущими зубьями, предназначенный для снятия припуска, и участок с калибрующими зубьями, предназначенный для удаления оставшегося припуска после срезания его основной части режущими зубьями, и окончатель-
24
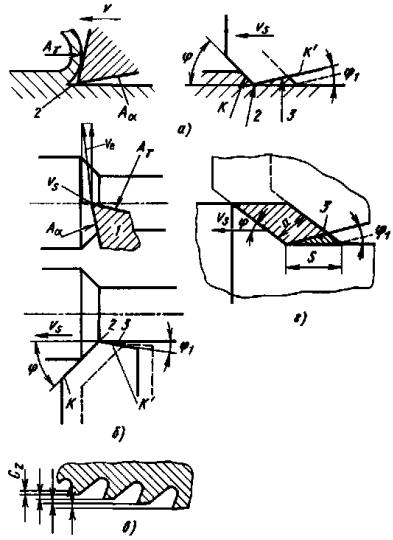
ного формирования обработанной поверхности заготовки; кроме них бывают участки с переходными и выглаживающими зубьями.
Срезание стружки осуществляется лезвиями 1 клинообразной формы, ограниченными передними Аγ и задними Аα поверхностями (рис. 1). Их пересечение образует режущую кромку К.
Рис. 1. Общие конструктивные элементы режущей части инструмента при прямолинейном (а) и вращательном (б) главном движении; подъем на зуб (в); сечение срезаемого слоя (г)
По числу лезвий (зубьев) могут быть инструменты одно- и многолезвийные (одно- и многозубые). На зубьях, как однолезвийных, так и многолезвийных инструментов имеются главная К и вспомогательная К' режущие кромки, их сопряжение образует вершину 2 лезвия. Различают зубья черновые, переходные, чистовые и калибрующие в зависимости от сечения срезаемых слоев.
25
Для осуществления процесса резания лезвие инструмента перемещается относительно обрабатываемой поверхности заготовки, совершая главное движение Dr резания со скоростью v, необходимое для удаления поверхностного слоя материала заготовки — срезания стружки. Кроме того, инструмент совершает движение подачи Ds со скоростью vs, меньшей скорости v. Это движение предназначено для того, чтобы распространить отделение слоя материала на всю обрабатываемую поверхность. В процессе обработки данного участка поверхности заготовки главное движение осуществляется непрерывно.
Движение же подачи может быть непрерывным и прерывистым. Главное движение Dr со скоростью v, движение подачи Ds со скоростью vs создают суммарное результирующее движение резания De со скоростью ve.
При периодическом движении подачи, например при строгании и долблении, в процессе данного рабочего хода инструмента скорость подачи vs = 0, а результирующее движение резания создается только главным движением (ve = v). Главное движение и движение подачи может совершать заготовка относительно инструмента или инструмент относительно заготовки; они могут быть прямолинейно-поступательными (рис. 1, а) или вращательными
(рис. 1, б).
В зависимости от вида главного движения Dr создается конструкция инструмента: при вращательном главном движении инструмент имеет форму тела вращения с зубьями по периферии, торцу. Если вращательное главное движение сообщается заготовке, то инструмент может быть более простой формы и иметь даже один режущий элемент, например резец, совершающий движение подачи Ds параллельно, перпендикулярно или наклонно относительно оси главного вращательного движения (оси обрабатываемой поверхности заготовки).
Движение подачи Ds — прямолинейное поступательное или вращательное движение режущего инструмента или заготовки, скорость которого меньше скорости главного движения резания, пред-
26
назначенное для того, чтобы распространить отделение слоя материала на всю обрабатываемую поверхность. Движение подачи может быть продольным и поперечным. При применении многих инструментов движение подачи образуется кинематикой станка, но есть многозубые инструменты, при применении которых поперечное смещение траекторий, образуемых лезвиями инструмента в их главном движении для снятия всего припуска, осуществляется не механизмами станка, а соответствующим смещением лезвий в конструкции инструмента относительно его базовых поверхностей.
Лезвия последующих зубьев этих инструментов в процессе главного движения перемещаются не по одной и той же траектории, а по траекториям, смещенным относительно траекторий предыдущих зубьев. Это смещение траекторий последующих режущих кромок многозубого инструмента необходимо для снятия всего припуска. Оно обеспечивается не движением, осуществляемым инструментом или заготовкой (как указано выше), не кинематикой и механизмами станка, а конструктивным исполнением инструмента, и по сути своей соответствует подаче на зуб.
В отличие от подачи на зуб назовем это смещение конструктивным обеспечением срезания припуска. Изменение положения режущих кромок последующих зубьев определяет толщину срезаемых слоев материала и применяется в многолезвийных инструментах (протяжках, метчиках и др. ) Величину этого смещения (подъема) обозначим Сz.
Применение конструктивного обеспечения срезания припуска позволяет за один рабочий ход инструмента осуществить обработку и формообразование поверхности детали, в том числе и сложной, обеспечивает повышение производительности процесса и точность обработанных поверхностей, упрощает конструкцию (кинематику) станка (необходимо только одно главное движение).
27
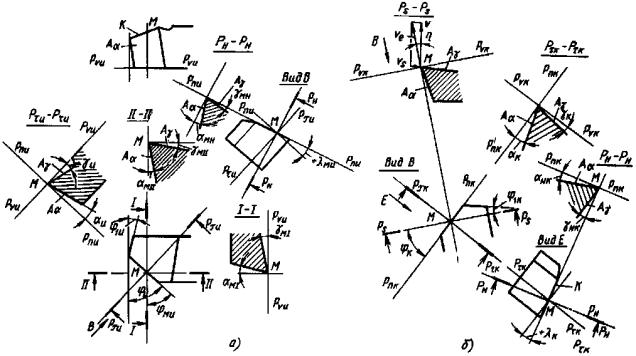
2.2. Геометрические параметры рабочей части
Слой материала заготовки отделяет лезвие инструмента, режущая кромка которого образуется пересечением передней и задней поверхностей, а положение этих поверхностей зависит от геометрических параметров инструмента. Геометрические параметры в зависимости от целей их применения рассматривают в системах координат инструментальной (и), статической (с) и кинематической (к). Их обозначают индексами, указанными в скобках.
В инструментальной системе координат (инструментальные геометрические параметры, рис. 2, а) определяют геометрические элементы инструмента. Эту систему применяют для изготовления и контроля инструмента. Обычно геометрические параметры рассматривают относительно базы установки инструмента при изготовлении, контроле и эксплуатации.
Рис. 2. Геометрические параметры:
а — инструментальные; б — кинематические
28
Встатической системе координат рассматривают статические геометрические параметры в системе, ориентированной относительно направления скорости главного движения резания. Эти параметры применяют для учета изменения геометрических параметров после установки инструмента на станке.
Вкинематической системе координат рассматривают кинематические геометрические параметры (рис. 2, б) в условиях процесса эксплуатации инструмента — в процессе резания. Значения этих па-
раметров определяют относительно вектора скорости ve результирующего движения; они определяют кинематику резания.
При определении геометрических параметров необходимы
плоскости: основная Pv, проведенная через рассматриваемую точку режущей кромки перпендикулярно скорости главного v или резуль-
тирующего ve движения резания в этой точке; резания Рn, касательная к профилю режущей кромки в рассматриваемой точке и перпен-
дикулярная основной плоскости; главная секущая Рη, перпендикулярная линии пересечения основной плоскости Pv и плоскости резания Рn; нормальная секущая Рн, перпендикулярная режущей кромке
врассматриваемой точке; секущая плоскость схода стружки Pc, проходящая через направления схода стружки и скорости резания в рас-
сматриваемой точке режущей кромки; рабочая Ps, в которой расположены направления (векторы) скоростей главного движения реза-
ния Dr и движения подачи Ds.
При криволинейной форме режущей кромки, передней и задней поверхностей учитываются плоскости (линии), касательные к ним в рассматриваемой точке режущей кромки.
Положение основной плоскости в инструментальной системе координат зависит от конструкции инструмента. У токарных и строгальных резцов прямоугольного поперечного сечения она совпадает с основной установочной базой резца; у инструментов с главным вращательным движением проходит через ось инструмента.
Основными геометрическими элементами лезвия являются: передний угол γ — угол в секущей плоскости между передней поверхностью лезвия Аγ и основной плоскостью Рv; главный задний угол α
29
— угол в секущей плоскости между задней поверхностью Аα лезвия
иплоскостью резания Рn; угол в плане
θ— угол в основной плоскости между плоскостью резания и рабочей плоскостью, т. е. угол между проекцией режущей кромки (касательной к режущей кромке в рассматриваемой точке) на основную плоскость и вектором скорости подачи; вспомогательный угол
в плане θ1 — угол между проекцией вспомогательной режущей кромки на основную плоскость и вектором, обратным направлению скорости подачи; угол наклона режущей кромки λ — угол в плоскости резания между режущей кромкой и основной плоскостью.
В зависимости от координатной системы, в которой они измеряются, различают инструментальные, статические и кинематические углы; углы передний и задний измеряют в главной секущей плоскости или в других плоскостях, обозначаемых соответствующими индексами.
У некоторых инструментов различие в величинах инструментальных, статических и кинематических геометрических параметров незначительно, но у некоторых это различие большое, и его необходимо учитывать при назначении инструментальных геометрических параметров. Их пересчитывают с учетом угла скорости резания η — угла в рабочей плоскости между направлениями скоростей резуль-
тирующего движения резания ve и главного движения v резания; угла подачи μ — угла между направлениями скоростей движения по-
дачи vs и главного движения v резания, а также с учетом параметров установки инструмента — угла установки и положения рассматриваемой точки режущей кромки относительно оси заготовки или инструмента при вращательном главном движении.
Задний угол α необходим для возможности перемещения лезвия по образованной им поверхности заготовки, для уменьшения контакта задней поверхности лезвия и образованной поверхности заготовки и возникающих между ними сил трения. С увеличением α интенсивность изнашивания лезвия по задней поверхности уменьшается и увеличивается стойкость инструмента. Однако при увеличении α уменьшаются угол заострения β и прочность лезвия.
30