
2558
.pdf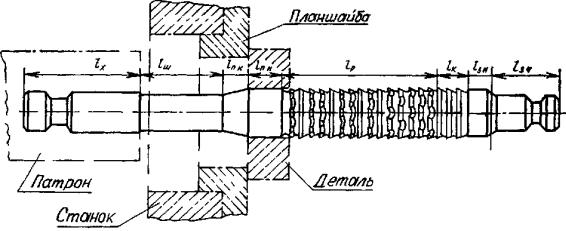
а) по форме обрабатываемых поверхностей: круглые, плоские и фасонные (шлицевые, многогранные, елочные и т. д.);
б) по схемам резания (одинарные и групповые, которые в свою очередь подразделяются на профильные, генераторные и комбинированные); в) по конструкции (цельные и сборные);
г) по режущему материалу (быстрорежущие и твердосплавные);
д) по способу размещения стружки (обычные и со свободным выходом стружки);
е) по способу формирования обработанной поверхности (режущие, уплотняющие, деформирующие и комбинированные, состоящие из режущей и уплотняющей частей).
2.9.2.Элементы конструкции
игеометрические параметры протяжек
Составные части внутренних протяжек показаны на примере круглой протяжки для обработки цилиндрического отверстия (рис.
42).
Рис. 42. Составные части протяжки
Рабочая часть, включающая режущую часть lр, выполняющую работу по удалению припуска, и калибрующую lк, окончательно формирующую размеры отверстия и качество обработанной поверхности, является основной частью протяжки. Она состоит из
111
зубьев остроконечной формы, имеющих переднюю поверхность 1, заднюю 2 и спинку 3 (см. рис. 41). Каждый зуб в отдельности представляет собой резец с присущими ему геометрическими параметрами: передним углом γ, задним утлом α, углом заострения β, углом резания δ, которые, как и у резца, задаются в нормальной секущей плоскости между соответствующими поверхностями зуба и координатными плоскостями: основной и плоскостью резания. Основная плоскость, перпендикулярная к вектору скорости резания, и плоскость резания взаимно перпендикулярны и перпендикулярны к плоскости чертежа. Для протяжек с прямыми зубьями, перпендикулярными к оси (рис. 41), плоскость чертежа является нормальной секущей плоскостью. У протяжек с наклонным зубом (плоские) или винтовым зубом (круглые) зубья имеют угол наклона главной режущей кромки λ между режущей кромкой и основной плоскостью.
Геометрические параметры калибрующих зубьев на рис. 41 обозначены индексом к. Шаг зубьев t, ширина задней поверхности зуба g, глубина h и форма R и r стружечной канавки, а также подъем на зуб sz являются основными элементами конструкции рабочей части протяжки. Они зависят от размеров и формы обработанной поверхности, припуска на обработку, принятой схемы резания, периода стойкости протяжки, обрабатываемого материала, заданного качества обработанной поверхности и других факторов. Параметры протяжки выбираются оптимальными по себестоимости обработки, т. е. такими, когда себестоимость обработки минимальная, что достигается при минимальной длине протяжки, высокой стойкости и большом количестве переточек.
Режущая часть протяжек групповой схемы резания дополнительно подразделяется на обдирочную, переходную и чистовую части. На обдирочной и переходной части зубья объединены в группы (секции) одинакового диаметра, а подъем задается на секцию зубьев, больший для обдирочных секций. Чистовые зубья имеют самый малый подъем, причем на каждый зуб. Такой принцип конструирования преследует цель удаления основного припуска минимальным числом зубьев с обеспечением требуемого качества обра-
112
ботанной детали чистовыми зубьями протяжки. Это позволяет сделать протяжку минимальной длины. Диаметр первого режущего зуба равен минимальному диаметру отверстия до протягивания, а диаметр последнего режущего зуба — диаметру калибрующих зубьев протяжки. Число зубьев зависит от припуска на обработку и подъема на зуб.
Зубья калибрующей части протяжки не имеют подъема на зуб. Их диаметр должен обеспечить максимально допустимый размер отверстия. Чем меньше шероховатость обработанной поверхности и выше ее точность, тем больше число калибрующих зубьев протяжки.
Передняя lпн и задняя lзн направляющие (рис. 42) служат для центрирования и направления протяжки по отверстию детали в момент начала и окончания работы. Форма и поперечные размеры передней направляющей соответствуют форме и минимальным размерам отверстия до обработки. Задняя направляющая чаще всего имеет форму окончательно обработанного отверстия с минимально допустимыми размерами.
Хвостовик lх, шейка lш, переходной конус lпк и задняя замковая часть lзч (рис. 42) являются присоединительной частью прок тяжки. За хвостовик, закрепленный в тяговом патроне станка, протяжку протягивают через обрабатываемое отверстие. Размеры и форма хвостовика зависят от диаметра протяжки и зажимного патрона. Переходный конус облегчает ввод протяжки в отверстие. Длины переходного конуса и шейки выбираются такими, чтобы при положении детали, как показано на рис. 42, обеспечить возможность соединения хвостовика протяжки с патроном протяжного станка. Размеры поперечного сечения шейки должны быть меньше опасного сечения на рабочей части, чтобы в случае разрушения протяжки по присоединительной части ее можно было восстановить.
Задней замковой частью протяжку соединяют с кареткой обратного хода станка для возврата протяжки в исходное положение. Делается это только у протяжек, работающих по автоматическому или полуавтоматическому циклу.
113
Разновидностью внутренних протяжек являются прошивки, которые в отличие от протяжек работают не на растяжение, а на сжатие, их проталкивают через отверстие. Во избежание продольного изгиба прошивки делают короче протяжек, поэтому для полного удаления припуска выпускается комплект прошивок из нескольких штук. Кроме того, у прошивок нет присоединительной части.
2.9.3. Расчет и конструирование протяжек
Материалом для протяжек служит легированная сталь ХВГ или быстрорежущие стали Р9К5, Р6М5, Р9 и Р18. При применении быстрорежущих сталей используют сварную конструкцию, причем хвостовик выполняют из стали 45Х и стали других марок. Протяжки, оснащенные пластинами из твердого сплава, не получили широкого распространения из-за сложности изготовления. Протяжки из быстрорежущей стали диаметром 50 мм и более допускается изготовлять цельными или с механическим креплением хвостовика.
В зависимости от типа патрона, применяемого доя крепления протяжки на станке, хвостовик протяжки выполняют различной конструкции. Хвостовики для круглых и шпоночных протяжек могут быть выполнены по ГОСТ 4042-70* и ГОСТ 4044—70*. В нормалях приводятся конструкции хвостовиков других типов. Технические требования к протяжкам для шлицевых отверстий приведены в ГОСТ 6767—79, для цилиндрических отверстий — в ГОСТ 9126— 76*, для шпоночных протяжек — в ГОСТ 16491—80Е, для гранных отверстий — в ГОСТ 16492—70*.
У рабочей и задней направляющей частей должна быть HRC
62…65.
Поверхности и все сопряжения радиусов впадины зуба должны быть плавными, без уступов и других дефектов заточки.
Параметры шероховатости должны быть следующие: задних и передних поверхностей всех зубьев Rz ≤ 1,6 мкм, поверхностей спинок зубьев, радиусов впадин, стружкоделительных канавок и вы-
114
кружек Rz ≤ 6,3 мкм, поверхностей передней и задней направляющих Ra ≤ 0,63 мкм, поверхностей хвостовика Ra ≤ 1,25 мкм.
На шейке хвостовика каждой протяжки должна быть четко нанесена следующая маркировка: обозначение протяжки (номер или код детали, для которой предназначен инструмент или др.); диаметр и обозначение поля допуска отверстия; порядковый номер протяжки
вкомплекте; пределы длин протягиваемых заготовок; марка стали протягиваемых заготовок; номинальная величина переднего угла; марка стали рабочей части протяжки; товарный знак (символ) пред- приятия-изготовителя.
Методика расчета и конструирования наиболее распространенных типов протяжек описана в литературе.
Порядок расчета круглой протяжки.
1.Определяют припуск на диаметр отверстия под протягива-
ние.
2.Определяют подъем на зуб на сторону sx по нормативам режимов резания для протягивания.
Между режущими и калибрующими зубьями делают несколько (два — четыре) зачищающих зубьев с постоянно убывающим подъемом на зуб.
3.Профиль, размеры зуба и впадины между зубьями выбирают
взависимости от сечения металла, снимаемого одним режущим зубом протяжки.
Шаг калибрующих зубьев tк круглых протяжек принимаем равным 0,6…0,8 шага режущих зубьев (для остальных типов протяжек
tк = t). Для получения лучшего качества обработанной поверхности шаг режущих зубьев протяжки делается переменным: от t + (0,2…1) до t - (0,2…1 мм). Фаска f на калибрующих зубьях плавно увеличивается от первого зуба к последнему с 0,2 до 0,6 мм.
4.Геометрические параметры режущих и калибрующих зубьев, число стружкоразделительных канавок и их размеры выбираем по справочной литературе.
115
5.Определяем максимальное число одновременно работающих
зубьев.
6.Определяем размеры режущих зубьев. Диаметр первого зуба принимается равным диаметру передней направляющей части. Диа-
метр каждого последующего зуба увеличиваем на 2sz. На последних трех зачищающих зубьях, предшествующих калибрующим зубьям, подъем на зуб постепенно уменьшаем по данным п. 2.
7.Определяем диаметр калибрующих зубьев Dк = Dmax ± δ, где Dmax — максимальный диаметр обработанного отверстия; δ — изменение диаметра отверстия после протягивания; при увеличении диаметра отверстия берется знак «—», а при уменьшении — знак
«+»;
δопределяем для каждого материала и толщины стенок протягиваемой заготовки опытным путем. В большинстве случаев при протягивании заготовок из стали увеличение диаметра отверстия 0,005…0,01 мм; при протягивании заготовок из вязких сталей уменьшение достигает 0,01 мм. При обработке отверстий с большими полями допусков (11...17 квалитеты) диаметр калибрующих
зубьев выбирается как Dк = Dmax – (0,01…0,015) мм. Вычисленные размеры зубьев сводят в таблицу, помещаемую в рабочем чертеже протяжки. Предельные отклонения диаметров режущих зубьев не должны превышать —0,01 мм, а калибрующих зубьев —0,005 мм.
8.Число режущих зубьев подсчитывают по формуле и затем уточняют по таблице размеров зубьев:
zp = (А/2sz) + (2…3), |
|
где А — припуск на протягивание. |
|
9. Число калибрующих зубьев зависит от типа протяжки: |
|
Протяжка: |
zк |
цилиндрическая для отверстий квалитетов 7 и 8 ....………. 7—8 цилиндрическая для отверстий квалитетов 11—17 …......... 5—6 шлицевая, острошлицевая, эвольвентная ...........…………….. 5
шпоночная, прямоугольная ..................……………………….. 4
116
предварительная (из комплекта) всех типов .........…...…… 2—4
10.Длину протяжки от торца хвостовика до первого зуба принимают в зависимости от размеров патрона, толщины опорной плиты, приспособления для закрепления заготовки, зазора между ними, длины заготовки и других элементов.
11.Выбираем конструктивные размеры хвостовой части протяжки по ГОСТ 4044—70*.
12.Определяем общую длину протяжки.
Если общая длина протяжки превышает наибольшую длину хода станка, то делают комплект протяжек. Общее число режущих зубьев делят на принятое число проходов. Диаметр первого режущего зуба протяжки данного прохода принимают равным диаметру калибрующих зубьев протяжки предыдущего прохода.
13.Определяем максимально допустимую силу резания с учетом свойств материалов заготовки и протяжки, размеров протяжки и других условий резания.
Если полученная сила Pz max превышает тяговую силу станка, приведенную в его паспортных данных, необходимо увеличить шаг зубьев или уменьшить подъем на зуб sz.
14.Проверяем конструкцию протяжки на прочность. Рассчитаем конструкцию на разрыв во впадине первого зуба.
Напряжение в опасном сечении не должно превышать допустимого напряжения. Проведем аналогичный расчет для сечения хвостовика. Рассчитаем хвостовик на смятие. По результатам расчетов выбираем материалы режущей части протяжки и ее хвостовика.
15.Предельные отклонения на основные элементы протяжки и другие технические требования выбираем по ГОСТ 9126—76*.
16.Центровые отверстия выполняем по ГОСТ 14034—74*.
17.Выполняем рабочий чертеж протяжки с указанием основных технических требований.
117
2.10.ЗУБОРЕЗНЫЕ ИНСТРУМЕНТЫ
2.10.1.Способы нарезания зубчатых изделий
Зубчатые изделия широко используются в конструкциях машин и приборов. К ним относятся зубчатые колеса и шлицевые валы с различной формой зуба, звездочки цепных передач и другие, подобные изделия. Нарезание зубьев таких изделий производят двумя основными методами: методом копирования и методом обкатки или огибания.
При методе копирования режущая кромка инструмента копирует размеры и форму впадины между зубьями обрабатываемой детали. Вырезание материала из впадины детали производится по принципу фрезерования, долбления или протягивания, в зависимости от типа инструмента. При этом обрабатываются или все впадины одновременно, или поочередно каждая из них с последующим поворотом детали на угловой шаг зубьев при переходе к обработке новой впадины.
В отличие от метода копирования метод обкатки основан на использовании принципа работы зацепления, одной деталью которого является режущий инструмент, а второй (сопряженной) — нарезаемое изделие. Профиль зубьев инструмента представляет собой огибающую положений обрабатываемой впадины в процессе взаимной обкатки. Поэтому он совершенно не похож на профиль впадины обрабатываемой детали. Его размеры совпадают с размерами нарезаемой впадины только по начальным поверхностям, по которым происходит взаимное обкатывание без скольжения детали и инструмента.
Обработка зубчатых деталей обкаточными инструментами производится на специальных зубообрабатывающих станках, где, помимо движений взаимной обкатки, режущему инструменту сообщается движение резания. Оно может быть вращательным (фрезерование) и прямолинейным (строгание и долбление).
118
Многие инструменты для нарезания зубчатых колес имеют свои прототипы среди ранее рассмотренных инструментов: резцов, фрез, протяжек.
Из всех зубчатых изделий наибольшее распространение получили зубчатые колеса эвольвентного профиля, на примере которых будут рассмотрены вопросы зубообработки и применяемые при этом инструменты.
2.10.2. Зуборезные инструменты, работающие по методу копирования
Инструменты для нарезания цилиндрических колес. Дисковые
ипальцевые модульные фрезы являются фасонными фрезами с присущими им параметрами конструкции и геометрии (рис. 43). Дисковые фрезы делают с затылованным зубом, а пальцевые — с остроконечным. Профиль зуба фрез эвольвентный и строится по точкам.
Форма и размеры межзубной впадины колес зависят не только от модуля, но и от числа зубьев колеса, так как кривизна эвольвенты определяется диаметром основной окружности. Поэтому для колеса каждого модуля и каждого числа зубьев нужна своя фреза. С целью сокращения количества фрез их комплектуют в наборы, состоящие из 8, 15 или 26 штук для каждого модуля. Отдельную фрезу, входящую в набор, используют для обработки нескольких колес с числом зубьев в определенном интервале. Профиль фрезы точно соответствует профилю впадины колеса с меньшим числом зубьев в интервале. Колеса с другими числами зубьев этого интервала будут нарезаны с некоторыми погрешностями.
Дисковые и пальцевые фрезы используются в единичном и мелкосерийном производстве для нарезания прямозубых, косозубых
ишевронных колес наружного зацепления. Фрезерование зубьев производят на универсально-фрезерных станках в центрах делительных приспособлений. Чаще используют дисковые модульные фрезы, допускающие большие подачи. Пальцевые модульные фрезы применяют только для нарезания крупномодульных колес, а также
119
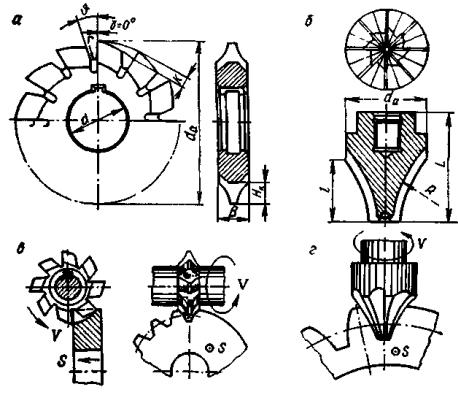
колес, которые нельзя нарезать дисковыми фрезами, а именно шевронных колес и блочных шестерен. Для повышения экономичности фрезы крупных модулей делают сборными.
Рис. 43. Модульные фрезы: а — дисковая; б — пальцевая; в, г — соответствующие им схемы фрезерования
Головки для контурного зубодолбления (рис. 44) —это очень сложные, высокопроизводительные инструменты, предназначенные для одновременного долбления всех впадин одного определенного колеса на специальных станках в условиях крупносерийного и массового производства. Режущими в головке являются фасонные стержневые резцы с присущими им геометрическими параметрами и с профилем впадины нарезаемого колеса. Перед началом каждого рабочего хода сводящее кольцо перемещает резцы к центру, т. е. осуществляет радиальную подачу резцов. Для устранения трения задних поверхностей резцов об обработанную поверхность при обратном ходе резцы отводятся от детали разводящим кольцом.
120