
2558
.pdf
6 с эксцентриком пластина прижимается к базирующему уступу державки 2. Здесь для обеспечения самоторможения должна быть обеспечена высокая точность размерной цепи уступ — ось и эксцентрик — пластина.
Рис. 13. Формы пазов под пластину: а — паз под передним углом; б — схема переточки с пластиной в закрытом пазу;
в — открытый паз; г — полузакрытый паз; д — закрытый паз
На рис. 14, в показана самотормозящая конструкция, которая позволяет создавать большее усилие зажима. Зажим пластины 3 в конструкции на рис. 14, г осуществляется тягой 7, перемещаемой пружиной 8.
Рис. 14. Способы механического закрепления твердосплавных пластин с отверстием
В приведенных конструкциях действующие при резании силы улучшают закрепление пластин. В процессе резания пластина постепенно сминает опорную поверхность гнезда, что приводит, к образованию зазора, возникновению переменных нагрузок и поломок пластины. Поэтому в современных конструкциях опорная поверх-
61

ность гнезда защищается закаленной стальной или твердосплавной прокладкой 9 (рис. 14, а) такой же конфигурации, что и режущая пластина.
Форма передней и задней поверхностей резцов. Практикой применения резцов выработаны формы их передней и задней поверхностей. Различают плоскую (рис. 15, а) ломаную (рис. 15, б, в) и криволинейную (рис. 15, г) формы поверхности. Технология переточки передней и задней поверхностей обычно включает шлифование и доводку. С увеличением площади шлифуемой и доводимой задней поверхности резца из одного куска материала или с пластиной из быстрорежущей стали (рис. 15, а) технологичнее отделять только шлифуемую поверхность от доводимой путем введения ломаной задней поверхности под углом больше заданного на 2…4°. В этом случае трудоемкая операция доводки будет выполняться на небольшой площадке с углом α.
Рис. 15. Формы передней и задней поверхностей резцов: а — плоские передняя и задняя поверхности; б — задняя поверхность с двойным изломом; в — плоская передняя поверхность с фаской; г — криволинейная передняя поверхность с фаской
Резцы с пластинами твердого сплава при заточке требуют применения разных шлифовальных кругов и режимов для державки и пластины. В силу этого целесообразна форма, изображенная на рис.
62
15, б, где доводимая поверхность отделена от шлифуемой, а стальная поверхность державки — от твердосплавной пластины.
Передняя поверхность резца может выполняться в трех основных вариантах, если не учитывать специальных ее подточек для обеспечения стружколомания и стружкозавивания: плоской (рис. 15, а, б), плоской с фаской (рис. 15, в) и криволинейной с фаской (рис. 15, г). Резцы с плоской передней поверхностью применяют при обработке чугуна, при обработке стали с подачами s < 0,2 мм/об; такую поверхность имеют, в частности, фасонные резцы. Криволинейную переднюю поверхность с фаской имеют резцы для обработки стали, когда необходимо обеспечить стружкозавивание. Здесь, как и в плоской с фаской форме, важную роль при работе резца играет фаска шириной несколько меньше величины подачи, затачиваемая под углом γф. Создание специальной фаски укрепляет место сопряжения передней и задней поверхностей — режущую кромку и благоприятствует нагружению ее силой резания. Радиус r выемки передней поверхности выбирают в зависимости от подачи и назначения резца
r = (10…60) s.
Сочетание форм передней и задней поверхностей резца выбирают, исходя из условий его эксплуатации.
2.5.3. Расчет резцов на прочность и жесткость
Размеры поперечного сечения державки резца выбирают в зависимости от силы резания, материала державки, вылета резца и других факторов. Нормализованный размер поперечного сечения державок резцов выбирают по ГОСТ 9795-84, ГОСТ 18868-73,
ГОСТ 18869-73, ГОСТ 18871-73, ГОСТ 18877-73, ГОСТ 18878-73, ГОСТ 18879-73, ГОСТ 18880-73 и др.
Для определения минимальных размеров сечения державки резца из условия ее прочности необходимо приравнять действующий изгибающий момент максимальному моменту, допускаемому сечением державки, т.е.
63
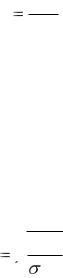
Мизг = М΄изг.
В свою очередь
Мизг = Pz·l;
М΄изг = σи.д·W,
где l – вылет резца в м (мм); σи.д – допускаемое напряжение на изгиб материала державки МПа (кгс/мм2), для державок из незакаленной углеродистой стали σи.д = 200…300 МПа (~20…30 кгс/мм2), для державок из углеродистой стали, подвергнутых термической обработке по режиму быстрорежущей стали, σи.д можно максимально увеличить в 2 раза, при прерывистом процессе снятия стружки и скоростном резании принимают σи.д = 100…150 МПа (~10…15
кгс/мм2); W – момент сопротивления сечения державки резца в м3 (мм3).
Момент сопротивления прямоугольного сечения
W bh62 ,
где b и h соответственно ширина и высота державки резца в опасном сечении в м (мм).
Сторону b или диаметр d поперечного сечения державки резца можно определить по формулам:
при квадратном сечении (h = b)
b36 Pzl ,
и.д
где Pz – сила резания;
при прямоугольном сечении c h = 1,6 b (Прямоугольные сечения применяются с различными соотношениями h / b; чаще всего
64

h / b = 1,25 и 1,6 при b = 10…40 мм. Для чистовых и получистовых режимов рекомендуется h / b = 1,6, а для черновых режимов h / b =
= 1,25)
b |
3 |
|
6 Pzl |
|
; |
|
|
2,56 |
и.д |
||||
|
|
|
|
|
при круглом сечении
d310Pzl .
и.д
При расчете отрезных резцов на прочность учитывают, что опасным сечением отрезного резца является место перехода от головки резца к телу. Для резцов с наиболее часто встречающимся соотношением размеров сечения b / h ≈ 1 / 6 ширина опасного сечения
(рис. 16)
b |
3 |
|
6 Pzl |
|
= 3 |
|
|
Pzl |
|
. |
|
|
|
|
|
||||||
|
|
|
36 и.д |
6 |
и.д |
|
|
Рис. 16. Схема расчета поперечного сечения головки отрезного резца
65

Максимальная нагрузка, допускаемая прочностью резца при известных размерах сечения державки резца:
для резца прямоугольного сечения
|
bh2 |
|
P |
и.д |
; |
|
||
zдоп |
6l |
|
|
для резца круглого сечения
P |
d 2 |
и.д |
≈ d 2 |
и.д . |
||
zдоп |
32l |
|
10l |
|
||
|
|
Максимальная нагрузка, допускаемая жесткостью резца, определяется с учетом допустимой стрелы прогиба резца:
3 fEJ ,
Pzжёст l3
где f — допускаемая стрела прогиба резца [при предварительном точении f = 0,1·10-3 м (~ 0,1 мм), при окончательном точении
f = 0,05·10-3 м (~ 0,05 мм)]; Е — модуль упругости материала резца (для углеродистой стали Е = 1,9·105… …2,15·105 МПа); J — момент
инерции сечения державки (для прямоугольного сечения BH123 , для
круглого сечения 0,05 d4); l — расстояние от вершины резца до рассматриваемого (опасного) сечения (вылет резца), м (мм).
Необходимо, чтобы сила Рz была меньше максимально допус-
тимых нагрузок Рz доп и Рz жест (или равна им): Рz ≤ Рz доп; Рz ≤ Рz жест. При конструировании резца для заданного станка полученные
размеры державки (высоту) надо скорректировать с расстоянием от опорной поверхности резца в резцедержателе до линии центров этого станка.
Кроме размеров сечения державки, к габаритным размерам относится длина резцов L, устанавливаемая стандартами в зависимо-
66
сти от поперечного сечения державки (L = 100…500 мм). Величина L должна назначаться с учетом размера головки резца, вылета резца из резцедержателя, размера резцедержателя, числа зажимных винтов (резец должен крепиться не меньше чем двумя винтами) и расстояния между винтами; при выборе длины резца желательно учитывать и дальнейшее использование державки после, например, окончательного износа твердосплавной пластинки на данной технологической операции.
Выполнение рабочего чертежа. После расчета инструмента составляют его рабочий чертеж, на котором указывают все данные, необходимые для изготовления сконструированного инструмента. Чертеж должен удовлетворять всем требованиям ЕСКД.
2.5.4. Конструирование резцов с механическим креплением пластин
Применяют резцы с механическим креплением трех-, четырех-, пяти- и шестигранных пластин из твердого сплава, предназначенных для обработки заготовок из стали и чугуна. Рассмотрим один из вариантов конструкции головки резца (рис. 17). Резец имеет державку 1 с запрессованным в нее штифтом 2. На штифт свободно надевают многогранную пластину из твердого сплава 3, которую закрепляют между штифтом и задней опорной стенкой державки с помощью клина 4 и винта 5. Многогранные пластины не перетачивают. После изнашивания одной режущей кромки пластину поворачивают, и в работу вступает следующая режущая кромка. После изнашивания всех режущих кромок пластину заменяют новой.
Углы θ у резцов с многогранными пластинами такие же, как у цельных напайных резцов с той же рабочей высотой, а угол в плане может быть 45, 60 и 90°. Необходимых значений задних углов α и α1 достигают путем установки пластины под соответствующим отрицательным углом γy. Для обеспечения положительных значений переднего угла γ, а также для завивания и дробления стальной стружки вдоль каждой из режущих кромок предусмотрены выкружки, фор-
67
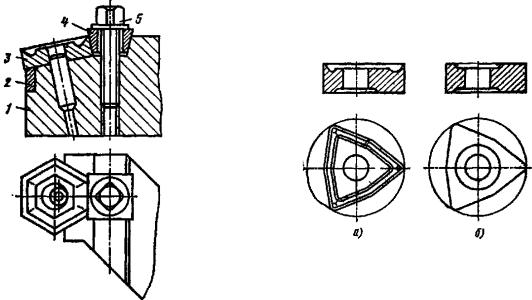
мируемые при прессовании многогранных пластин (форма I, рис. 18). Геометрические параметры режущей части резцов с многогранными пластинами формы I выбирают по справочным данным.
Угол, образованный выкружкой, равен 20 или 25° в зависимости от размера пластины, что обеспечивает при закреплении пластины на державке под углом γу = - 10° передний угол γ, равный 10 или 15°. Радиусы при вершине выбирают минимальными (r =
= 0,4…1 мм).
|
|
Рис. 18. Многогранные пла- |
Рис. |
17. Резец с механи- стины из твердого сплава: |
|
ческим креплением неперета- |
а — форма I, б — форма II |
|
|
||
чиваемой |
многогранной пла- |
|
стины из твердого сплава |
|
Сочетание малого радиуса при вершине резца и большого переднего угла резца значительно уменьшает отжим заготовки и позволяет использовать эти резцы в условиях малой жесткости станка и заготовки.
Резцы с многогранными пластинами могут быть успешно использованы при обработке заготовок из чугуна, конструкционной и высоколегированной сталей. Пластины для резцов делают с выкружками (форма I) и плоскими без выкружек (форма II).
68
Пластины формы II целесообразно использовать в крупносерийном и массовом производстве при работе на полуавтоматах, автоматах и агрегатных станках. Для отвода сливной стружки и получения положительных передних углов на передней поверхности этих пластин образуют многогабаритные лунки доводочным чугунным диском с нанесенной на него пастой карбида бора или алмазными кругами.
Режимы резания при обработке заготовок выбирают в зависимости от размеров и формы пластин, применяемого оборудования и максимального сечения срезаемого слоя. Выбирают габаритные размеры пластин (при заданных режимах резания).
Для изготовления резцов общего назначения рекомендуются твердые сплавы следующих марок: Т5К10, Т14К8, Т30К4, ВК6, ВК6М, ВК8. При работе с большими нагрузками, для повышения долговечности державки со стороны задней поверхности резцы необходимо оснащать пластинами (подкладками) из твердого сплава ВК8.
Габаритные и конструктивные размеры сборных токарных резцов с механическим креплением многогранных твердосплавных пластин выбирают в зависимости от назначения и формы пластины по ГОСТ 20872—80, ГОСТ 20874-75* и ГОСТ 21151—75*, а техни-
ческие требования — по ГОСТ 21492—76*.
2.6. РАСЧЕТ И КОНСТРУИРОВАНИЕ ИНСТРУМЕНТОВ ДЛЯ ОБРАБОТКИ ОТВЕРСТИЙ
Сверление, зенкерование и развертывание являются технологическими способами обработки круглых отверстий различной степени точности и с различной шероховатостью образованных цилиндрических поверхностей.
69
2.6.1. Сверла
Сверление — основной технологический способ образования отверстий в сплошном металле обрабатываемых заготовок. Сверлением могут быть получены как сквозные отверстия в заготовке, так и глухие отверстия. При сверлении отверстий чаще всего используют стандартные сверла, имеющие два винтовых зуба, расположенных диаметрально друг относительно друга. Просверленные отверстия, как правило, не имеют абсолютно правильной цилиндрической формы. Их поперечные сечения имеют форму овала, а продольные
— небольшую конусность.
Диаметры просверленных отверстий всегда больше диаметра сверла, которым они просверлены. Разность диаметров сверла и просверленного им отверстия принято называть разбивкой отверстия. Она тем больше, чем больше диаметр сверла: для стандартных сверл диаметром dc = 10...20 мм разбивка составляет 0,15...0,25 мм. Причиной разбивки отверстий являются недостаточная точность заточки сверл и несоосность сверла и шпинделя сверлильного станка. Сверление отверстий без дальнейшей их обработки проводят в тех случаях, когда необходимая точность размеров лежит в пределах 12...14-го квалитета, параметр шероховатости Ra = 3,2…12,5. Наиболее часто сверлением получают отверстия для болтовых соединений, а также отверстия для нарезания в них внутренней крепежной резьбы.
Сверла по конструкции и назначению подразделяют на спиральные, центровочные и специальные. Наиболее распространенный для сверления и рассверливания инструмент - спиральное сверло (рис. 19, а), состоящее из рабочей части 6, шейки 2, хвостовика 4 и лапки 3.
В рабочей части 6 различают режущую 1 и направляющую 5 части с винтовыми канавками. Шейка 2 соединяет рабочую часть сверла с хвостовиком. Хвостовик 4 необходим для установки сверла в шпинделе станка. Лапка 3 служит упором при выбивании сверла из отверстия шпинделя.
70