
2558
.pdf
Элементы рабочей части и геометрические параметры спирального сверла показаны на рис. 19, б. Сверло имеет две главные режущие кромки 11, образованные пересечением передних 10 и задних 7 поверхностей и выполняющие основную работу резания; поперечную режущую кромку 12 (перемычку) и две вспомогательные режущие кромки 9. На цилиндрической части сверла вдоль винтовой канавки расположены две узкие ленточки 8, обеспечивающие направление сверла при резании.
Рис. 19. Части, элементы и углы спирального сверла
Геометрические параметры сверла определяют условия его работы. Передний угол γ измеряют в главной секущей плоскости II - II, перпендикулярной к главной режущей кромке. Задний угол α измеряют в плоскости I - I, параллельной оси сверла. Передний и задний углы в различных точках главной режущей кромки различны. У наружной поверхности сверла угол γ наибольший, а угол α наименьший; ближе к оси — наоборот. Угол при вершине сверла 2θ измеряют между главными режущими кромками; его значение раз-
71

лично в зависимости от обрабатываемого материала. Угол наклона поперечной режущей кромки ψ измеряют между проекциями главной и поперечной режущих кромок на плоскость, перпендикулярную к оси сверла. Угол наклона винтовой канавки ω измеряют по наружному диаметру. С увеличением угла ω увеличивается передний угол γ ; при этом облегчается процесс резания и улучшается выход стружки. Рекомендуемые геометрические параметры сверла приведены в справочной литературе.
Силы резания. В процессе резания сверло испытывает сопротивление со стороны обрабатываемого материала. Равнодействующую сил сопротивления, приложенную в некоторой точке А режущей кромки, можно разложить на три составляющие силы Рx, Рy и Рz
(рис. 20).
Рис. 20. Силы, действующие на сверло
Составляющая Рx направлена вдоль оси сверла. В этом же направлении действует сила Рп на поперечную режущую кромку. Суммарная всех указанных сил, действующих на сверло вдоль оси х, называется осевой силой. Радиальные силы Рy, равные по величине, но направленные противоположно, взаимно уравновешиваются.
72

В расчетах для определения осевой силы Ро (Н) и крутящего момента Мк (Н·м) используют эмпирические формулы:
P |
С |
p |
D x p s y p K |
p |
; |
о |
|
|
|
М |
к |
С |
м |
D xм s yм К |
м |
, |
|
|
|
|
где Ср и См — постоянные коэффициенты, характеризующие обрабатываемый материал и условия резания; D – наружный диаметр сверла, мм; s - подача сверла (мм/об); хр, ур, хм, ум — показатели степеней; Кр и Км — поправочные коэффициенты на измененные условия резания. Коэффициенты и показатели степеней приведены в справочниках.
Осевая сила и крутящий момент являются исходными для расчета сверла и узлов станка на прочность, а также для определения эффективной мощности. Эффективная мощность (кВт), затрачиваемая на резание при сверлении,
Ме = Mкn / (60·103).
2.6.2. Расчет и конструирование сверл
По форме и конструкции сверла разделяют на спиральные, с прямыми канавками, перовые, для глубинного сверления, кольцевые, центровочные, с канавками для подвода смазочноохлаждающей жидкости, с многогранными пластинами. Сверла выполняют с цилиндрическим, коническим и четырехгранным хвостовиками. Основные размеры сверл стандартизованы. Геометрические параметры режущей части сверл (ω, γ и 2θ) в зависимости от материалов заготовки и сверла можно выбрать для сверл диаметром свыше 10 мм из инструментальной стали по табл. 9, для сверл, оснащенных пластинами из твердого сплава, — по табл. 10.
73
Угол наклона поперечной режущей кромки ψ для сверл диаметром до 12 мм принимают 50°, для сверл диаметром свыше 12 мм
— 55°. Задний угол α различен в различных точках кромки. У стандартных спиральных сверл в наиболее удаленной от оси сверла точке α = 8…15°, в ближайшей к оси точке α = 20…26°. У сверл, оснащенных пластинами из твердого сплава, задний угол α соответственно равен 4…6° и 16…20°. Меньшие из приведенных значений углов относятся к большим диаметрам сверл, большие значения — к малым диаметрам сверл. Формы и размеры заточки режущих кромок, перемычек и ленточек сверл приведены в нормативах.
Таблица 9 Рекомендуемые углы наклона винтовой канавки ω
и углы при вершине 2θ спиральных сверл диаметром свыше 10 мм из инструментальной стали
Материал заготовки |
ω |
2θ |
||
|
|
|||
градусы |
||||
|
|
|||
|
|
|
||
Сталь с ζв, МПа (кгс/мм2) |
|
|
||
до 500 (до 50) |
35 |
116 |
||
500…700 |
(~ 50…70) |
30 |
116…118 |
|
700…1000 |
(~ 70…100) |
25 |
120 |
|
1000…1400 (~ 100…140) |
20 |
125 |
||
коррозионно-стойкая |
25 |
120 |
||
Чугун серый |
|
25…30 |
116…120 |
|
Медь красная |
|
35…45 |
125 |
|
|
25…30 |
130 |
||
Медные отливки и латунь |
||||
|
|
|||
Бронза с НВ: |
|
15…20 |
135 |
|
100 и выше |
|
|||
|
8…12 |
125 |
||
< 100 |
|
|||
|
|
|
||
Алюминиевые сплавы литейные |
35…45 |
130…140 |
||
Алюминиевые сплавы деформируемые |
45 |
140 |
||
Пластмассы, эбонит, бакелит |
8…12 |
60…100 |
||
|
|
|
|
74
Технические требования к изготовлению спиральных сверл приведены в ГОСТ 2034 — 80Е и СТ СЭВ 566 — 77.
Хвостовики сверл с коническим хвостовиком имеют конус Морзе, выполняемый по СТ СЭВ 147 — 75.
Порядок расчета и конструирования спирального сверла из быстрорежущей стали с коническим хвостовиком для обработки сквозного отверстия.
Таблица 10 Рекомендуемые передние углы γ и углы при вершине 2θ сверл, оснащенных пластинами из твердых сплавов
Материал заготовки |
γ |
|
2θ |
|
|
|
|
|
градусы |
||
|
|
||
|
|
|
|
Сталь: |
|
|
|
конструкционная, углеродистая |
|
|
|
и легированная |
0…4 |
|
116…118 |
инструментальная |
— 3 |
|
116…118 |
марганцовистая твердая |
0 |
|
116…118 |
литая |
— 3 |
|
116…118 |
термически обработанная |
— 3 |
|
130…135 |
Чугун с НВ: |
|
|
|
≤ 200 |
6 |
|
116…118 |
> 200 |
0 |
|
116…118 |
Бронза, латунь, алюминий |
4…6 |
|
116…118 |
Баббит |
4…6 |
|
140 |
Пластмассы |
0…2 |
|
60…100 |
|
|
|
|
1.Определяем диаметр сверла. По ГОСТ 19257—73.
2.Определяем режим резания по нормативам.
3.Определяем осевую силу.
4.Момент сил сопротивления резанию (крутящий момент).
5.Определяем номер конуса Морзе хвостовика. С расчетом момента трения между хвостовиком и втулкой.
75
6.Определяем длину сверла. Общая длина сверла, длины рабочей части, хвостовика и шейки могут быть приняты по ГОСТ
10903—77 или ГОСТ 4010—77.
7.Определяем геометрические и конструктивные параметры режущей части сверла. По нормативам находим форму заточки, угол наклона винтовой канавки, углы между режущими кромками, задний угол, угол наклона поперечной кромки, размеры подточки, шаг винтовой канавки.
8.Определяем толщину dc сердцевины сверла в зависимости от диаметра сверла и утолщение сердцевины по направлению к хвостовику.
9.Обратная конусность сверла (уменьшение диаметра по направлению к хвостовику) на 100 мм длины рабочей части должна находиться в пределах:
D, мм ......... |
До 6 |
Св.6 |
Св. 18 |
Обратная конусность, мм |
....0,03—0,08 |
0,04—0,10 |
0,05—0,12 |
10. Определяем ширину ленточки f0 и высоту затылка по спин-
ке К.
11.Определяем ширину пера.
12.Геометрические элементы профиля фрезы для фрезерования канавки сверла определяют графическим или аналитическим способом.
13.По найденным размерам строим профиль канавочной фре-
зы.
14.Устанавливаем основные технические требования и допуски на размеры сверла (по СТ СЭВ 566—77 и ГОСТ 885—77).
Предельные отклонения диаметров сверла (ГОСТ 885—77). Допуск на общую длину и длину рабочей части сверла равен удвоенному допуску по квалитету 14 с симметричным расположением предельных отклонений по ГОСТ 25347—82. Предельные отклонения размеров конуса хвостовика устанавливаются по ГОСТ 2848— 75 (степень точности АТ8). Радиальное биение рабочей части сверла относительно оси хвостовика не должно превышать 0,15 мм. Предельные отклонения на углы 2θ; 2θ0, угол наклона винтовой канав-
76

ки. Предельные отклонения размеров подточки режущей части сверла. У рабочей части сверла HRС 62…65, у лапки хвостовика сверла HRC 30…45.
15. Выполняем рабочий чертеж. Рабочий чертеж должен иметь три проекции (винтовые линии при черчении заменяют прямыми линиями). Форма заточки сверла с геометрическими параметрами режущей части, центровое отверстие, а также профиль канавочной фрезы вычерчивают отдельно в большом масштабе. На чертеже также указывают основные технические требования к сверлу.
2.6.3. Зенкеры
Зенкерование — технологический способ обработки предварительно просверленных отверстий диаметром dc или отверстий, изготовленных литьем и штамповкой с целью получения более точных по форме и размеру, чем при сверлении, цилиндрических отверстий (10...11-го квалитета точности) с шероховатостью Rа = 1,25…3,2, диаметром dз > dc. Зенкеруют сквозные и глухие отверстия (рис. 21).
Рис. 21. Зенкеры различного назначения:
а - для растачивания цилиндрических отверстий; б - для обработки цилиндрических углублений под головки винтов; в - для зенкерования конических углублений (зенковка); г - для обработки торцовых поверхностей (цековка)
Элементы конструкции хвостового зенкера для обработки цилиндрических отверстий показаны на рис. 22.
77
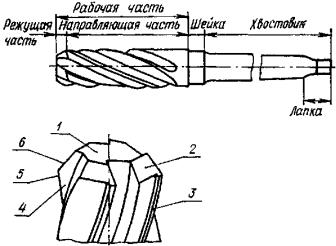
Рис. 22. Элементы конструкции цилиндрического зенкера: 1 — сердцевина; 2 — задняя поверхность; 3 — ленточка; 4 — передняя поверхность; 5—вспомогательная режущая кромка; 6 — главная режущая кромка
Стандартные зенкеры имеют от трех до восьми зубьев. Наиболее часто на практике встречаются зенкеры с тремя винтовыми зубьями, смещенными на 120° друг относительно друга. Через точки главных режущих кромок трех зубьев, лежащих в плоскости вращения, перпендикулярной геометрической оси зенкера, можно провести концентрические окружности. Это геометрическое свойство трехзубых зенкеров обеспечивает их самоцентрирование и получение после зенкерования отверстий более правильной цилиндрической формы и с более точным размером диаметра, чем это достигается двухзубыми сверлами.
Рабочая часть зенкера включает режущие и калибрующие элементы. Режущие элементы ограничены главным углом в плане θ, измеряемым между направлением подачи и главной режущей кромкой (рис. 23). В пределах вспомогательного угла в плане θ1 находится калибрующая часть, близкая по форме к цилиндру, поскольку зенкер, подобно сверлу, шлифуется при изготовлении с небольшой обратной конусностью. Геометрия рабочей части зенкера для цилиндрических отверстий определяется углами γ и α в точке х главной режущей кромки, а также углами α1 и ω.
78

Рис. 23. Геометрические параметры хвостового зенкера
Передний угол γх в точке главной режущей кромки определяется в плоскости, перпендикулярной проекции главной режущей кромки на диаметральную плоскость, проходящую через вершину зуба зенкера.
Главный задний угол αх, как и у сверла, определяется между касательными в точке х к задней поверхности и к винтовой траектории движения точки х при вращении зенкера и его осевом перемещении по подаче. Вспомогательный задний угол на калибрующей части обычно близок нулю. Угол наклона винтовой канавки ω не требует особых пояснений.
2.6.4. Развертки
Развертывание — технологический способ завершающей обработки просверленных и зенкерованных отверстий с целью получения точных по форме и диаметру цилиндрических отверстий (6...9- го квалитета точности) с малой шероховатостью (Rа = 0,32…1,25 мкм).
Развертываются отверстия развертками, имеющими четное число (z ≥ 4) расположенных диаметрально друг против друга зубьев. Число зубьев развертки зависит от диаметра:
79

z p 1,5d p
2...4 ,
где dp — диаметр развертки, мм. Наличие на развертках большого числа зубьев обеспечивает устойчивое их центрирование в обрабатываемых отверстиях. Поскольку каждым зубом развертки срезается слой металла малой толщины az < 0,04 мм, а также благодаря применению смазывающе-охлаждающей жидкости, развертыванием можно достигнуть высокой точности размера диаметра обработанных отверстий и малой шероховатости их стенок.
Развертки используют для чистовой обработки точных отверстий в материалах, обычно не прошедших упрочняющей термической обработки. Обработка ведется на станках сверлильнорасточной и токарной групп, а также автоматических линиях. Разверткой могут обрабатываться цилиндрические и конические, как глухие, так и сквозные отверстия. Помимо машинных, имеются ручные развертки. Некоторые конструкции разверток показаны на рис. 24.
Развертки небольшого диаметра (рис. 24, а) выполняются с цилиндрическим хвостовиком, а при диаметре более 10 мм — с коническим (рис. 24, б). Те и другие развертки изготовляются быстрорежущими — целиком, или с вставными ножами (рис. 2.4, б, в). Развертки по рис. 24, г выполняются диаметром до 100 мм. Здесь на ножах и в корпусе имеются рифления, что позволяет переставлять ножи и закреплять их клиньями на новом, большем диаметре, а также перетачивать на необходимый диаметр и таким образом более рационально использовать и режущие ножи, и корпус, меняя ножи. Подобную конструкцию имеют и развертки с твердосплавными ножами.
Кроме цилиндрических отверстий, развертками обрабатывают конические поверхности под резьбу, конусы Морзе, метрические конусы, отверстия под конические штифты (рис. 24, д).
Геометрию разверток рассмотрим на примере цельной насадной машинной развертки для сквозных отверстий (рис. 25). По длине рабочей части развертки можно выделить участки А — Г различ-
80