
2558
.pdf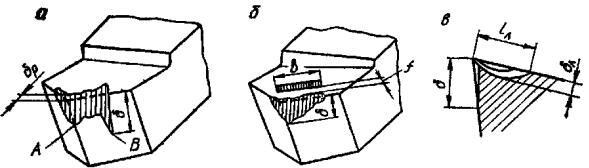
2.4.4. Изнашивание режущих инструментов
Виды износа. Поверхности инструмента, находящиеся в контакте с обрабатываемой деталью и стружкой, довольно быстро изнашиваются. Проработав несколько минут или в крайнем случае несколько сот минут, инструмент становится неработоспособным. Его снимают со станка и отправляют на переточку.
Инструменты изнашиваются или преимущественно по задней поверхности (рис. 8, а), или одновременно по задней и передней поверхностям (рис. 8, б). Износ по задней поверхности представляет собой площадку переменной ширины вдоль главной режущей кромки; он имеет наибольшую величину на переходной задней поверхности, в месте сопряжения главной задней поверхности со вспомогательной (А на рис. 8, а) или месте контактирования главной кромки с обрабатываемой поверхностью (В на рис, 8, а).
Рис. 8. Виды износа инструментов
Если инструмент изнашивается одновременно по задней и передней поверхностям, на последней образуется лунка износа длиной b и глубиной δ (рис. 8, б). В случае образования нароста лунка отстоит от главной кромки на расстоянии f. Если нароста нет, изношенный инструмент имеет вид, показанный на рис. 8, в. На кромках и поверхностях твердосплавного инструмента нередко появляются разрушения в виде выкрошиваний и сколов.
Преимущественно по задней поверхности инструменты изнашиваются при обработке чугунов, а также при обработке других ма-
51
териалов с малыми толщинами среза а и с низкими скоростями резания v. При обработке сталей и других вязких материалов имеется износ обоих видов, причем с увеличением а и v преимущественно изнашивается передняя поверхность.
Мера изношенности инструмента. За меру изношенности (показатель затупления) инструмента принимают линейный или массовый износ. Линейный износ задней поверхности количественно оценивается наибольшей шириной площадки износа δ (рис. 8), передней поверхности — наибольшей глубиной лунки износа δл.
Линейный износ в направлении, перпендикулярном к обработанной поверхности, характеризуется размерным износом δр (рис. 8, а), он связан с изменением размера обработанной детали в зависимости от затупления инструмента и служит для оценки его изношенности при чистовой размерной обработке.
Массовый износ m численно равен массе изношенной части инструмента. Для очень малых инструментальных вставок он определяется при их непосредственном взвешивании.
Физическая природа изнашивания инструментов. Физическая природа изнашивания инструментов настолько сложна, что до настоящего времени не вполне выяснена. Существующие гипотезы объясняют только отдельные стороны этого процесса.
По гипотезе абразивного изнашивания износ поверхностей инструмента является результатом царапания их твердыми частицами обрабатываемого материала. К таким относятся цементит, карбид кремния, интерметаллиды, фосфиды. Твердые частицы разрушающегося нароста, скользя по передней и задней поверхностям, также оказывают абразивное воздействие. Из-за абразивного изнашивания выходят из строя в основном инструменты из быстрорежущих и инструментальных сталей.
По гипотезе адгезионного изнашивания поверхности инструмента изнашиваются в результате адгезионного взаимодействия между материалами инструмента и обрабатываемой детали. В процессе резания контактные поверхности инструмента, стружки и обрабатываемой детали химически чисты. В условиях высоких кон-
52
тактных давлений и высоких температур между поверхностями возникают мостики схватывания как результат молекулярного взаимодействия. При относительном скольжении поверхностей мостики разрушаются с вырыванием частиц инструментального материала как менее прочного и более хрупкого во взаимодействующей паре. Чем выше циклическая прочность и ниже хрупкость инструментального материала, тем меньше адгезионный износ инструмента. Этим объясняется, например, иногда наблюдаемая более высокая износостойкость быстрорежущих сталей по сравнению с твердым сплавом при работе с низкими температурами резания.
По гипотезе диффузионного изнашивания при температурах выше 800…850° С возникает процесс диффузионного переноса атомов инструментального материала в обрабатываемый. Высокая скорость этого процесса при резании объясняется высокой температурой резания и химической чистотой свежеобразованных поверхностей. Из твердого сплава первым диффундирует углерод, затем вольфрам, кобальт и титан, а из обрабатываемого металла в твердый сплав диффундирует железо. Разупрочненный поверхностный слой твердого сплава истирается стружкой и контактными поверхностями обрабатываемой детали.
По гипотезе окислительного изнашивания при резании с достаточно высокими температурами кислородом воздуха окисляются в первую очередь кобальт, а затем карбиды титана и вольфрама, входящие в состав инструментального материала. Механизм окислительного изнашивания твердосплавного инструмента включает образование и истирание окисных пленок, накопление окислов в порах поверхностного слоя и его разрушение. Возможность окислительного изнашивания объясняется тем, что в момент резания большая часть рабочей поверхности инструмента может взаимодействовать с окружающей средой. Установлено, что при резании сталей с относительно низкой схватываемостью окислительный износ при 600…900° С является преобладающим и определяет стойкость инструмента.
53
Вдействительности изнашивание инструмента происходит в результате одновременного протекания процессов абразивного истирания, адгезии, диффузионного растворения и окисления инструментального материала, а также вследствие его усталости, электрических явлений и др. Чрезвычайная сложность механизма изнашивания инструментов создает большие трудности при разработке математической модели изнашивания.
Во всех случаях наибольшее влияние на величину износа инструмента оказывает скорость резания, более слабое — подача и наименьшее — глубина резания. Такова же относительная сила влияния элементов режима резания на температуру резания. Эта закономерность подтверждает тот факт, что величина линейного износа прямо зависит от температуры резания.
Критерии износа. Инструмент считают окончательно затупившимся и отправляют на заточку, судя о затуплении по определенному признаку, который называют критерием износа. Свойство инструмента сохранять работоспособными свои режущие кромки и контактные поверхности называется стойкостью. Период времени резания между двумя заточками, в течение которого сохраняется работоспособность инструмента, носит название периода стойкости.
Влабораторных условиях и производственной деятельности используют два критерия износа: критерий оптимального износа и критерий технологического износа. При очень малом допустимом износе инструмент имеет малый период стойкости Т, но допускает большое число переточек i. При большом допустимом износе период стойкости оказывается большим, но число переточек значительно
сокращается. В обоих случаях суммарный период стойкости Тсум = iT сравнительно мал. Можно найти такую величину износа, при ко-
торой Тсум становится наибольшим. Этот износ δсум называют оптимальным.
Инструмент считают окончательно затупившимся и отправляют на заточку, когда износ его задней поверхности становится равным технологическому износу. Величину технологического износа устанавливают исходя из следующих признаков: 1) резко увеличи-
54
вается шероховатость обработанной поверхности по вине режущего инструмента; 2) резко изменяются размеры обработанных деталей вследствие износа инструмента; 3) частыми становятся его поломки; 4) возникают вибрации технологической системы; 5) имеет место наибольшее количество замен инструментов данного типа.
2.4.5. Расчет экономической эффективности режущих инструментов
Расчеты экономической эффективности проводятся на следующих этапах:
при подготовке создания новых инструментов (ожидаемый экономический эффект);
по окончании разработки нормативно-технической документации (гарантированный экономический эффект);
после внедрения (фактический экономический эффект). Ожидаемый экономический эффект служит основанием для
принятия решения о целесообразности создания нового инструмента. На основе гарантированного экономического эффекта, определяемого по годовому объему производства, принимается решение о целесообразности производства и внедрения нового инструмента. По фактическому экономическому эффекту оценивается окончательная эффективность новых инструментов.
Ожидаемый и гарантируемый экономические эффекты отражают потенциальные возможности нового инструмента. Исходными данными для их расчета на единицу инструмента являются: для ожидаемого эффекта — проектные, нормативные и плановые показатели, а также экспериментальные оценки, справочные данные; для гарантированного эффекта — отчетные данные по трудовым и материальным затратам на изготовление, а также результаты испытаний и эксплуатации опытных образцов.
Фактический экономический эффект рассчитывают на основании отчетных данных.
55
Годовой экономический эффект представляет собой суммарную экономию всех производственных ресурсов (живого труда, материалов, капитальных вложений), которую получает народное хозяйство в результате производства и использования новых инструментов.
Экономический эффект от внедрения нового режущего инструмента может быть получен за счет повышения работоспособности инструмента, повышения производительности оборудования и труда рабочих, связанных с применением этого инструмента; улучшения качества обработки деталей (точности и шероховатости поверхности) и, как следствие, повышения их надежности и долговечности; снижения себестоимости и удельных капитальных вложений на единицу продукции.
2.5. РАСЧЕТ И КОНСТРУИРОВАНИЕ ТОКАРНЫХ РЕЗЦОВ
2.5.1. Классификация резцов
Токарная обработка отличается большим разнообразием обрабатываемых поверхностей и в силу этого значительной номенклатурой режущих инструментов — токарных резцов. На токарных станках выполняются различные стадии обработки поверхности; используемые при этом резцы называются черновыми, чистовыми, получистовыми. Геометрия режущей части этих резцов приспособлена к работе с большой или с малой глубиной резания.
Резцы, предназначенные для обработки наружных поверхностей, не имеют специального названия, а для обработки внутренних поверхностей называются расточными с добавлением названия, характеризующего вид выполняемой работы (рис. 9, а, б). По виду выполняемой работы различают резцы проходные — для обработки гладкой цилиндрической поверхности (внутренней или наружной) на «проход» (рис. 9, в) и упорные проходные — для обработки одновременно цилиндрической поверхности и торцовой плоскости
(рис. 9, г).
56

Рис. 9. Разновидности токарных резцов по назначению
Торцовые поверхности цилиндрических тел на токарных станках «подрезают» так называемыми подрезными резцами (рис. 9, д), которые работают с поперечной подачей к оси вращения или от оси вращения заготовки. Отрезку заготовки ведут отрезным резцом (рис. 9, ж), а образование канавок — канавочным или прорезным резцом (рис. 9, е). Резьбовые поверхности образуют резьбовыми резцами, фасонные — фасонными (рис. 9, з), фаски - фасочными, галтели — галтельными и т. д.
Все резцы, работающие с продольной подачей, могут в рабочем движении перемещаться справа налево — это правые резцы (рис. 10, б), и слева направо — левые резцы (рис. 10, а). У правых резцов главная режущая кромка находится со стороны большого пальца правой руки, положенной на резец сверху, у левых резцов главная режущая кромка при аналогичном положении левой руки находится также со стороны большого пальца.
Головка резца по отношению к его телу может быть отогнутой, изогнутой и оттянутой, а может совпадать по направлению с сечением тела. Тогда резцы называют прямыми (рис. 10, в), с отогнутой головкой (рис. 10, г), с оттянутой головкой (рис. 10, д) и с изогнутой головкой (рис. 10, е).
57

Рис. 10. Разновидности токарных резцов по направлению движения и подачи и по форме головки
Резцы одинакового назначения могут выполняться с державкой
— телом разного сечения: квадратного, прямоугольного, круглого, специального (рис. 11).
Рис. 11. Формы сечений тела резца
Преобладает прямоугольная форма сечения державки резцов, при которой врезание пластины меньше ослабляет державку. Державки с квадратной формой сечения лучше сопротивляются деформированиям сложного изгиба и применяются для расточных и авто- матно-револьверных резцов и в других случаях, когда расстояние от линий центров станка до опорной поверхности резца недостаточно велико. Державку с круглой формой сечения применяют для расточных, резьбовых, токарно-затыловочных и других резцов, так как она позволяет осуществлять поворот резца и изменять углы его заточки.
58
2.5.2.Стандартные режущие элементы резцов
идругих инструментов
Установлены стандартные формы и основные размеры пластин для резцов и других металлорежущих инструментов. ГОСТ 2209—69 распространяется на перетачиваемые пластины из твердого сплава для режущего инструмента, а ГОСТ 2379—77 — на пластины из быстрорежущей стали для резцов.
Широко применяется механическое крепление пластин. В России действует ряд стандартов на твердосплавные механически закрепляемые пластины. Последние классифицируются по семи параметрам, которые условно обозначаются цифрами или буквами:
по форме: трехгранные с углом 60° (01 или Т), с углом 80° (02 или F), квадратная (03 или S), ромбические с углом 60° (04 или G), с углом 80° (05 или С), с углом 84° (06 или И), параллелограммные с углом 84° (07 или W), с углом 55° (08 или К), прямоугольная с радиусной режущей кромкой (09 или L), пятигранная (10 или Р), шестигранная (11 или Н), круглая (12 или R);
по величине заднего угла: α = 0 (1 или N), α = 7° (2 или С), α = 11° (3 или Р);
по степени точности: нормальная (1 или U), повышенная (2 или М), высокая (3 или G), особо точная (4 или С). Пластины нормальной и повышенной точности шлифуются по опорным поверхностям и ленточке, но пластины повышенной точности шлифуются с более жестким допуском на диаметр вписанной окружности d; две другие степени обеспечиваются шлифованием также и боковых поверхностей;
по конструктивным особенностям: без отверстия и канавки (1 или N), с отверстием, но без канавки (3 или А), с отверстием и канавкой с одной стороны (4 или М) и др. (всего 6 вариантов).
по размерам отдельных элементов: длина режущей кромки l, толщина пластины s, радиус при вершине, увеличенный в 10 раз. Таким образом, форма, геометрия, степень точности и т. д. квадратной пластины из сплава Т15К6 с углом α = 7°, повышенной степени
59

точности, без отверстия и канавки, с длиной режущей кромки l = 27 мм, толщиной 7 мм, с радиусом при вершине 1,6 мм может быть обозначена по ГОСТ 19042—73 цифрами
03221-270716 Т15К6 ГОСТ 19052-73
или буквами и цифрами
SCMN 270716 Т15К6 ГОСТ 19052-73.
Разнообразие форм и конструктивных элементов пластин, предусмотренное стандартом, позволяет подобрать нужный вариант пластин для данного типа инструмента (резец, фреза и т. п.) и конкретных условий его работы. Конструктивные варианты некоторых пластин приведены на рис. 12.
Рис. 12. Формы твердосплавных механически закрепляемых пластин
Крепление режущих элементов резца. Режущие пластины соединяют с головкой резца пайкой, сваркой или механическим способом. В первых двух случаях на головке резца предварительно фрезеруется паз той или иной формы: открытый, полузакрытый, закрытый (рис. 13). Однако твердосплавные пластины при напайке подвергаются действию перепада температур, что вызывает появление микротрещин и выход резцов из строя. Лучшим вариантом закрепления пластин является их механическое крепление.
На рис. 14 приведены некоторые схемы закрепления твердосплавных пластин с отверстием. Стальной штифт 1 запрессован в державку (рис. 14, а), и на него надевается пластина 5. Двусторонний клин 4 при ввинчивании винта 5 прижимает пластину к штифту и таким образом закрепляет ее. Более удачной, за счет уменьшения числа стыков, является конструкция на рис. 14, б, где поворотом оси
60