
2421
.pdfактивированное состояние). Эти процессы связаны между собой, и массоперенос кислорода зависит от скорости потока кислорода и его давления. Вот почему окисление примесей в условиях конвертерного процесса при вдувании в расплав чистого кислорода резко интенсифицируется.
Рассматривая особенности процесса окисления углерода, можно выделить следующие его стадии:
1)поверхностное окисление углерода на границе расплав—газ с полным использованием кислорода. В этом случае повышение интенсивности подвода кислорода увеличивает скорость окисления углерода, но концентрация кислорода в расплаве остается примерно постоянной, кроме того, не обнаруживается внешних признаков окисления железа;
2)поверхностное окисление железа, что проявляется в образовании на поверхности расплава пленки окислов.
Концентрация |
кислорода |
в расплаве постепенно |
увеличивается, |
и наступает момент, когда она значительно |
|
превышает равновесную; |
|
3) интенсивное окисление углерода в объеме расплава, которое наступает за счет повышенной концентрации кислорода и образования зародышей газовой фазы с постепенным увеличением интенсивности выделения из расплава пузырьков СО (начало и интенсивное развитие процесса кипения). Это сопровождается турбулентным перемешиванием расплава с возможным вспениванием и развитием других побочных процессов (удаление неметаллических включений, водорода, азота и т. д.);
- заметное понижение скорости окисления углерода при малой концентрации его в расплаве; увеличение скорости окисления железа и общей окисленности расплава.
Установлено значительное влияние температуры на начало и продолжение процесса окисления углерода. Начало интенсивного окисления углерода соответствует достижению температуры1450–1500°С.
211

Образование внутри расплава новой фазы в виде пузырьков СО возможно в том случае, если суммарное внешнее давление в месте образования пузырька будет меньше или по крайней мере равно давлению окиси углерода в пузырьке:
РСО ≈ Рвн = Ратм + Feq hFe + шлqhшл |
2 |
, |
(8.14) |
|
r |
||||
|
|
|
||
где Ратм - атмосферное давление (или |
давление над |
|||
расплавом); |
|
шл hшл - |
||
FehFе соответственно плотности расплава и шлака; |
соответственно толщина слоя металлического и шлакового
расплавов; 2 - капиллярное давление; σ - поверхностное r
натяжение металлического расплава; r - радиус пузырька. Из уравнения (8.14) следует, что при очень малых
размерах пузырька давление Рвн будет значительно больше давления РСО и при прочих равных условиях образование СО и ее всплывание исключаются.
Для образования пузырьков СО, их роста до критических размеров и всплывания необходимы определенные условия, а именно, необходимо, чтобы большое количество частиц углерода и кислорода встретилось и соединилось и чтобы их накопилось в элементарном объеме столько, сколько требуется для зарождения пузырька, т. е. чтобы была достигнута определенная степень пересыщения ими расплава.
Величина пересыщения расплава молекулами новой фазы зависит от размера зародышей выделяющейся фазы и увеличивается с уменьшением радиуса зародышей.
Согласно данным расчетов при разных степенях пересыщения расплавов железа окисью углерода критический радиус пузырьков r составляет r ~ 5∙10-3 см.
Местами зарождения пузырьков могут быть «дырки», размер которых в жидком расплаве (10-8 см) соизмерим с
212
радиусом молекулы СО, различные включения, всегда присутствующие в реальных расплавах железа, и межфазные поверхности металл — шлак и металл —- под плавильной печи.
8.4 Раскисление
Раскисление – заключительная технологическая операция многих плавильных процессов. Для сталей и некоторых цветных сплавов этот процесс является последним звеном перед их разливкой и кристаллизацией, и от него зависит успех всего процесса плавки.
Назначением раскисления является доведение до минимума концентрации кислорода, остающегося в сплаве после окислительного рафинирования перевод его в форму включений (соединений), большая часть которых должна быть удалена из расплава до его разливки. Те включения (продукты раскисления), которые не успеют всплыть, должны иметь такую форму, свойства и расположение, чтобы вредное воздействие их было сведено к минимуму. В процессе приготовления определенной группы сплавов, например чугунов, не исключена возможность положительного влияния продуктов взаимодействия компонентов сплава с кислородом на структуру и свойства кристаллизующегося расплава.
Общие закономерности взаимодействия элементов с кислородом были рассмотрены выше (разд. 4). Критерием раскислительной способности того или иного элемента является активность кислорода в металле, которая находится в равновесии с определенной концентрацией (точнее определенной активностью) элемента раскислителя и с продуктами раскисления, образуемыми этим элементом и кислородом. Раскислительная способность различных элементов для стали представлена на рис.8.4.
213
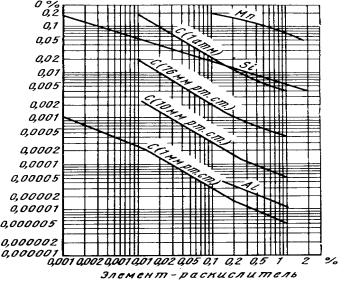
Рис. 8.4. Раскислительная способность некоторых элементов при 1600 оС
Установлено, что при одновременном использовании нескольких раскислителей раскислительная способность каждого из них может увеличиться. Такое явление объясняют тем, что в образующихся окислах более сложного химического строения силы межчастичного взаимодействия больше по сравнению с таковыми в более простых окислах. Примером этого является использование марганца и кремния. Известно, что марганец и кремний взаимно увеличивают раскислительную способность друг друга. Одновременное применение нескольких раскислителей (комплексное раскисление) улучшает и кинетику процесса, особенно при использовании элементов с разной температурой плавления (кипения), плотностью и т. п. При выборе раскислителей необходимо руководствоваться тем, что в конечном счете должны быть получены продукты раскисления, легко удаляемые из расплава. Этому условию отвечают
214
раскислители, которые дают с кислородом окислы, образующие затем друг с другом продукты с невысокой температурой плавления (лучше, если их температура плавления ниже температуры раскисляемого сплава) и плотностью, намного меньшей плотности сплава.
В табл. 8.1 приведены значения температур плавления и плотности некоторыхокислов. Видно, что только комплексные соединения типа силикатов имеют более низкую температуру плавления, чем сталь. В практике, которая согласуется с теорией, используют такую последовательность ввода раскислителей, которая обеспечивает образование вначале включении типа mFeO ∙ nМпО, а затем комплексных жидких или твердыхалюмосиликатныхвключений.
|
|
|
Таблица8.1 |
Температура плавленияиплотность(г/см3 ) некоторых |
|||
окисловиихсоединений |
|
||
Окисел |
|
Температ |
Плотн |
|
|
ура плавления |
ость |
|
|
в оС |
при |
|
|
|
20 оС |
1 |
|
2 |
3 |
FeO (точнее Fe0,9O) |
|
1369 |
5,8 |
МпО |
|
1785 |
5,5 |
SiO2. |
|
1760 |
2,2-2,6 |
А12О3 |
|
2050 |
4,0 |
Сг2О3 |
|
2280 |
5,0 |
ТiO2 |
|
1825 |
4,2 |
ZrO2. |
|
2700 |
5,75 |
Силикаты железа, |
|
1180-1380 |
4,0-5,8 |
содержащие < 40% SiO2. |
|
|
|
Силикаты железа, |
|
1380-1700 |
2,3-4,0 |
содержащие > 40% SiO2 |
|
|
|
|
215 |
|
Продолжение табл.8.1
1 |
2 |
3 |
Силикатымарганца, |
1210-1600 |
4,0-5,0 |
содержащие15-50%SiO2. |
|
|
Силикаты глинозема, |
1545 |
3,05 |
содержащие > 10 % А12О3 |
|
|
Процесс удаления продуктов раскисления, являющихся наиболее распространенным видом эндогенных включений, связан не только с их природой (свойствами), но и со многими побочными факторами (циркуляционными потоками металла, глубиной ванны или высотой ковша и т. д. ).
Выдержка металла после раскисления и разливка его всегда сопровождаются повторным окислением. По этой причине металлические расплавы (например, сталь) после раскисления в плавильной печи подвергаются дополнительному раскислению путем ввода раскислителей в ковш при его заполнении или на желоб. При производстве сталей для этого используют главным образом алюминий, являющийся в этих условиях очень сильным раскислителем.
Большая степень чистоты от неметаллических включений может быть достигнута при раскислении, получившем название диффузионного (точнее экстракционного). В этом случае создаются условия массопереноса растворенного кислорода к поверхности соприкосновения металлического и шлакового расплавов с последующим переходом кислорода через границу металл — шлак и массопереноса кислорода от нижней поверхности шлака к верхней, где тем или иным методом поддерживается небольшая концентрация свободного кислорода.
Эффективным средством понижения содержания кислорода в расплавах является использование вакуума. В условиях вакуума изменяется (усиливается) раскислительная способность элементов и создаются благоприятные условия для дегазации и удаления неметаллических включений.
216
Однако при использовании вакуума для раскисления или для иных целей необходимо иметь в виду возможность взаимодействия жидкого металла с окислами огнеупорных материалов, в результате чего возникает переход кислорода из окислов огнеупорных материалов в металлический расплав.
Обычно основой большинства огнеупорных материалов являютсяокислыCaO, MgO, Fe2O3,Сг2О3, А12О3,SiO2.Условияих разложения подчиняются общим закономерностям, описанным выше. Иногда наряду с переходом в металл кислорода из огнеупоров происходит растворение элементов, входящих в окисел. Например, в условиях использования хромитовых или хромомагнезитовых высокоогнеупоров при плавке стали и чугуна в металлический расплав может перейти значительное количество хрома.
Раскислители должны удовлетворять следующим общим требованиям:
- при возможно малых концентрациях они должны обладать в условиях ведения раскисления большим сродством к кислороду;
-остающиеся после раскисления в сплаве в том или ином количестве раскислители не должны оказывать вредного влияния на свойства металла или сплава;
-окисел (окислы), образуемый (образуемые) раскислителем (раскислителями), должен в минимальной степени растворяться в раскисляемом металле или сплаве; лучше, если окисел, образующийся при раскислении, способен образовывать с другими окислами, которые присутствуют в сплаве, легкоплавкие нерастворимые соединения с плотностью, намного меньшей плотности раскисляемого сплава;
-нерациональные потери раскислителя в процессе раскисления должны быть минимальными;
-должны быть дешевыми и недефицитными.
Обычно для раскисления стали и других сплавов на основе железа используют углерод, марганец, кремний,
217
алюминий, титан, кальций и другие элементы. В табл. 8.2 приведены данные, характеризующие раскислительную способность этих элементов.
Медь и медные сплавы раскисляют углеродом, фосфором, цирконием, литием, кальцием и др.
|
|
Таблица 8.2 |
Раскислитель |
Равновесное содержание в % |
|
|
Кислорода |
Раскислителя |
|
при 0,1% |
при 0,01 % |
|
раскислителя |
кислрода |
Алюминий |
10-4 |
10-4 |
Титан |
10-3 |
10-3 |
Кремний |
0,02 |
0,27 |
Углерод |
0,02 |
0,23 |
Марганец |
0,20 |
2,00 |
8.5. Водород и азот в сталях. Дегазация расплавов
Водород и азот способны в небольших количествах растворяться в жидком железе, их растворимость в твердом металле гораздо ниже.
Резкое изменение растворимости этих газов в металлах, особенно при затвердевании (рис.8.5) является одной их причин их несплошности (пористости) и пониженной прочности.
Водород, оставшийся в растворе в твердом металле, вызывает снижение технологических и механических свойств: падает пластичность металла, в нем возникают микротрещины (флокены). Особенно опасен водород в сплавах, которые содержат элементы, образующие прочные гидриды (титан, цирконий, ниобий). Гидридные фазы вызывают охрупчивание сталей и других сплавов.
218
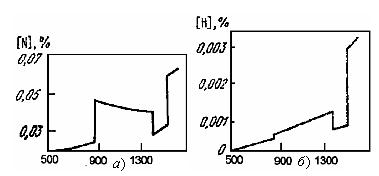
Т, С |
Т, С |
Рис. 8.5. Зависимость растворимости азота (а)и водорода(б) в железе от температуры
Азот, оставшийся в твердом металле, может вызывать газовую пористость и нередко является причиной резкого снижения пластичности, особенно при образовании хрупких нитридных фаз (хром, ванадий, ниобий и др.). Вместе с тем, азот может оказывать и положительное влияние на свойства сталей, т.к. он способствует получению выгодной аустенитной структуры, а также вызывает упрочнение поверхности стальных деталей при их нитроцементации.
Основным источником водорода в любых плавках является влага сырых материалов и воздуха, продукты горения топлива. Азот попадает в сталь главным образом из воздуха. В большинстве случаев в процессе выплавки стали приходится уменьшать количество растворенного газа, т.е. проводить дегазацию расплава.
Растворение газов в железе (абсорбция) сопровождается обычно изменением молекулярного состояния газа:
1 |
Н |
|
[H] |
КН = |
a[H] |
|
f[H][H] |
, |
(8.15) |
||
2 |
2( ) |
Р1/2 |
Р1/2 |
|
|||||||
|
|
|
|
|
|
||||||
|
|
|
|
|
Н2 |
|
Н2 |
|
|
219

|
1 |
N |
|
[N] |
|
|
КN = |
|
a[N] |
|
f[N][N] |
, |
(8.16) |
||||
|
2 |
2( ) |
|
|
|
Р1/2 |
Р1/2 |
|
|||||||||
|
|
|
|
|
|
|
|
|
|
||||||||
|
|
|
|
|
|
|
|
|
|
N2 |
|
|
N2 |
|
|
||
где |
a[H] , a[N] |
- активности газов, |
f[H ] , f[N] |
-коэффициенты |
|||||||||||||
активности, РН2 |
и |
РN2 - парциальные давления газов, [H] и |
|||||||||||||||
[N] – равновесные концентрации газов в металле. |
|||||||||||||||||
|
|
Из (8.15) и (8.16) получаем |
|
|
|
|
|
|
|||||||||
|
|
[H] = КН |
|
|
|
[N] = КN |
|
; |
|
(8.17) |
|||||||
|
|
РН2 |
; |
|
РN2 |
|
Величина константы равновесия в (8.17) численно равна растворимости газа в металле при его парциальном давлении в газовой фазе Р=1 ат.
Для изменения энергии Гиббса при растворении Н2 и N2 известны следующие соотношения:
Gо |
= 30400 + 32,70 Т, |
[H] |
|
Gо |
= 12120 + 20,27 Т. |
[N ] |
|
Из этих выражений видно, что оба процесса эндотермичны, и по принципу Ле-Шателье при повышении температуры растворимость газов возрастает, причем для водорода быстрее, чем для азота. Для чистого железа зависимость растворимостей от температуры можно выразить
уравнениями: |
|
|
|
||
1g[%H] = - |
1590 |
1,71 ; |
1g[%N] = - |
850 |
0,905. |
|
Т |
|
Т |
Следует иметь в виду, что излишний перегрев металла увеличивает его газонасыщенность. Это проявляется особенно сильно в электродуговых печах. В области электрической дуги создаются очень высокие температуры, при которых возможна частичная диссоциация молекул Н2 и N2 на атомы, легко абсорбируемые расплавленным металлом.
Условие дегазации, которое можно получить из уравнения изотермы заключается в том, что
220