
1371
.pdf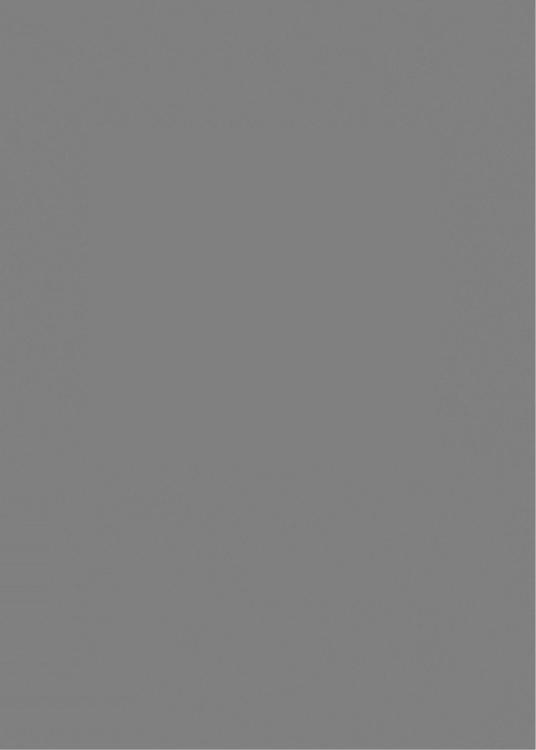
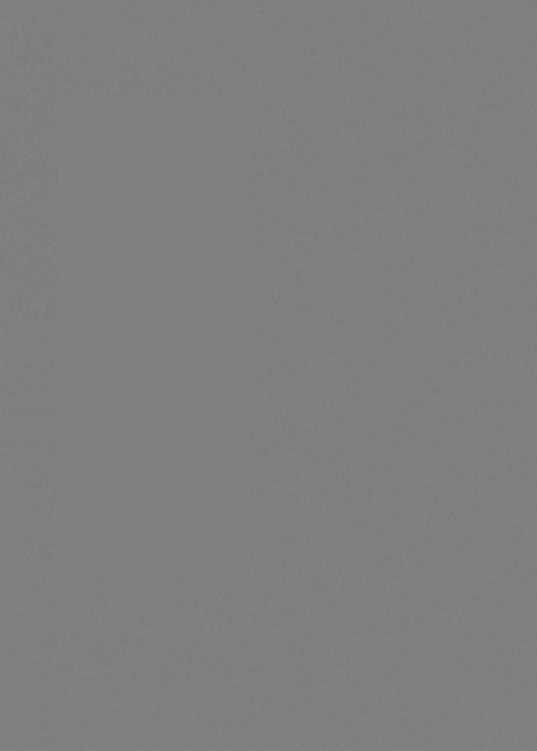
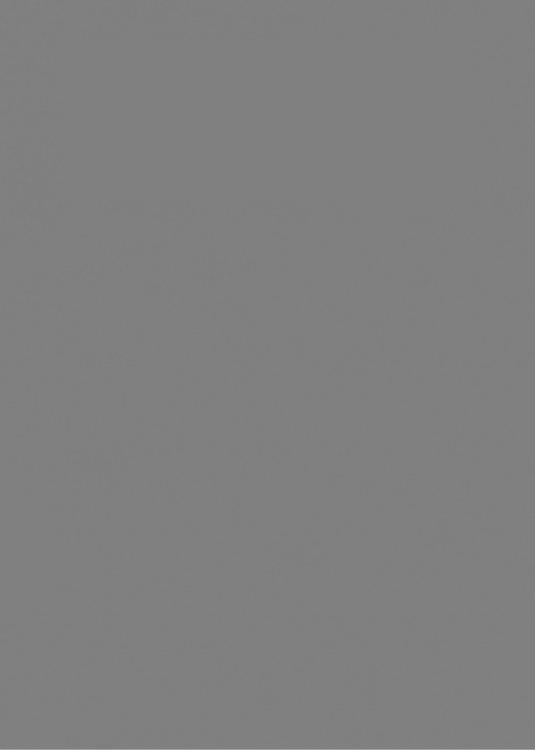
244 Л Макаллистер, У Лакман
Таблица |
5. Варианты |
элементов, армирующих |
проколотую |
|||
|
|
|
ткань |
в направлении Z [40] |
|
|
|
|
|
|
|
Общая площадь |
|
|
Элемент направления Z |
поперечного сечения |
||||
|
волокон, входящих |
|||||
|
|
|
|
|
в элемент (мкм3) |
|
8 графитовых нитей |
|
|
0,39 |
|||
10 графитовых |
нитей |
|
|
0,49 |
||
13 графитовых нитей |
(в виде пред* |
|
0!63 |
|||
13 графитовых |
нитей |
|
0,63 |
|||
|
варительно |
полимеризованного |
|
|
||
20 |
стержня) |
|
|
|
0,98 |
|
графитовых нитей |
|
|
||||
1 |
прядь |
(в |
виде предварительно |
|
0,46 |
|
2 |
полимеризованного стержня) |
|
0.92 |
|||
пряди |
|
|
|
|
||
|
Примечание, Диаметр всех указанных элементов от 0.89 до 1.4 мм. |
|||||
Таблица |
6. Характеристики заготовки из проколотой ткани |
|||||
|
|
|
в направлениях X, |
Y [40] |
|
|
|
Варианты укладки |
Плотность |
Объемная доля волокон *, % |
|||
|
заготовка. |
|
|
|||
|
|
|
|
г/см* |
X. Y |
Z |
|
|
|
|
|
||
GSGC-2 |
|
|
0,85 |
47,2 |
9,3 |
|
Торнел-50 |
|
|
0,92 |
50,8 |
8,9 |
|
8-ремнзный сатин |
||||||
WCA последовательно |
0,83 |
48.6 |
9,3 |
|||
повернута на 45° |
|
|
|
* В процентах от общего объема полуфабриката.
Таблица 7. Сопоставление характеристик ортогональной и проколотой заготовок [40]
|
Плотность |
Объемная доля волокон, % |
|
Т и п з а г о т о в к и |
заготовки. |
|
|
|
г/см* |
X. У |
Z |
Проколотая ткань |
0,9 |
50 |
9 |
Тонкое трехнаправлен- |
0.8 |
32 |
13 |
ное ортогональное пе- |
|
|
|
реплетенме |
|
|
|
В табл. 7 сопоставлены свойства 3-D ортогонального тка ного блока и блока из проколотой ткани. Обе заготовки были изготовлены из высокомодульной графитовой нити одной и той же ыаркн. Обнаруживается заметное различие структур
Многонаправленные углерод-углеродные композиты |
245 |
по объемному содержанию и распределению волокон. Блок из проколотой ткани имеет более высокое общее объемное со держание волокон и плотность.
Полученные результаты позволяют утверждать, что при менение проколотых тканей делает технологию изготовления многонаправленных блоков более разнообразной за счет воз
можности варьирования |
структуры |
ткани, типа и харак |
тера распределения нитей. |
Влияние |
некоторых из этих фак |
торов на свойства углерод-углеродных композитов будет рас смотрено в разд. 4.1.
2.4.4. Структуры из предварительно полимеризованных нитей. Рассмотренные в разд. 2.4.2 сухие многонаправленные армирующие каркасы изготавливают ткацким методом и на ткацком оборудовании. В технологии проколотых тканых структур (разд. 2.4.3) используют предварительно изготов
ленную ткань, |
вводя дополнительный технологический |
прием — прокол, |
а вместо некоторых элементов заготовки |
применяют предварительно полимеризованные нити. Много направленные структуры можно изготовить и без применения ткачества или других методов текстильной промышлености. Основными элементами для изготовления в этом случае яв ляются предварительно полимеризованные нити в виде прут ков, которые изготавливают методом пултрузии из высоко прочных углеродных волокон и фенольных связующих (34].
Один из типов структур, изготавливаемых из этих прут ков, представляет собоой 4-D конструкцию в виде правиль ного тетраэдра, каждый пруток которой составляет угол 70,5° с каждым из остальных трех. Если воспользоваться рис. 7, эту структуру можно представить с помощью диагоналей, проходящих через вершины Т, U, V, W элементарного блока.
Полимеризованные пучки нитей (прутки) для производ ства 4-D структур имеют диаметр от 1,0 до 1,8 мм и шести угольное поперечное сечение для достижения максимальной плотности упаковки. Показано, что вследствие высокой эф фективности упаковки объем волокон в 4-D четырехгранных структурах достигает 75 % [32].
Для сборки 4-D структур из прутков применяют оборудо вание, обеспечивающее строгое соответствие теоретической геЪметрической схеме [32]. Тип применяемого оборудования не описан. Готовые 4-D структуры, по-видимому, представ ляют собой блок, собранный из прутков, образованных графи товыми волокнами, в соответствии с заданной геометрической схемой. До введения матрицы подобные блоки не обладают целостностью.
246 |
|
Л. Макаллистер, У. Лакман. |
|
|
|
|
|
|
|
||
2.4.5. |
Намоточные структуры из подэлементов. Нетекстиль |
||||||||||
ный способ изготовления многонаправленных цилиндриче |
|||||||||||
ских структур |
описан в работе [41]. Готовый армирующий |
||||||||||
|
|
|
|
каркас |
имеет |
нити |
в |
||||
|
|
|
|
окружном, |
радиальном |
||||||
|
|
|
|
и осевом направлениях |
|||||||
|
|
|
|
(рис. |
|
18). |
Согласно |
||||
|
|
|
|
этому |
способу, |
ради |
|||||
|
|
|
|
альная |
арматура |
пред |
|||||
|
|
|
|
ставляет собой |
предва |
||||||
|
|
|
|
рительно |
изготовлен |
||||||
|
|
|
|
ные |
композитные |
под |
|||||
|
|
|
|
элементы |
из |
графито |
|||||
|
|
|
|
вых |
нитей |
на |
феноль |
||||
|
|
|
|
ных |
связующих. |
|
Со |
||||
|
|
|
|
бранные вместе на |
ци |
||||||
|
|
|
|
линдрической |
|
оправке |
|||||
|
|
|
|
радиальные подэлемен |
|||||||
|
|
|
|
ты образуют |
решетку с |
||||||
|
|
|
|
пазами |
в |
окружном и |
|||||
|
|
|
|
осевом |
направлениях. |
||||||
|
|
|
|
Далее в эти пазы за |
|||||||
|
|
|
|
матывают |
|
предвари |
|||||
|
|
|
|
тельно |
из |
пропитанные |
|||||
|
|
|
|
ленты |
однонаправ |
||||||
|
|
|
|
ленных |
высокомодуль |
||||||
|
|
|
|
ных |
графитовых |
воло |
|||||
|
|
|
|
кон. |
При |
этом |
окруж |
||||
Рис. 18. Схема трехнаправленного (3-D) |
ные |
слои |
чередуются с |
||||||||
осевыми. |
В |
|
качестве |
||||||||
цилиндрического |
армирующего |
каркаса |
|
||||||||
[41]; 1 — осевые; |
2 — радиальные, 3 — ок |
связующего |
на |
всех |
|||||||
ружные |
элементы арматуры. |
этапах |
|
изготовления |
|||||||
смолы. После |
завершения |
намотки |
применяют фенольные |
||||||||
полуфабрикат |
подверга |
ется отверждению для получения 3-D графитофенольного цилиндра, пригодного для дальнейшей переработки в угле- род-углеродный композит.
Для получения разного объемного содержания волокон в окружном и осевом направлениях изменяют размеры и фор му радиальных элементов.
3.Уплотнение многонаправленных структур
3.1.ОБЩИЕ ЗАМЕЧАНИЯ
Переработку полуфабриката с многонаправленной струк турой в предельно плотный композит можно осуществить
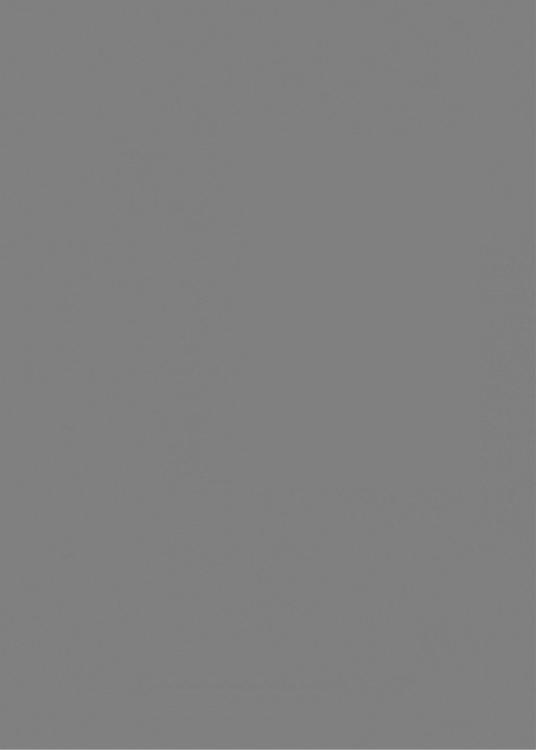
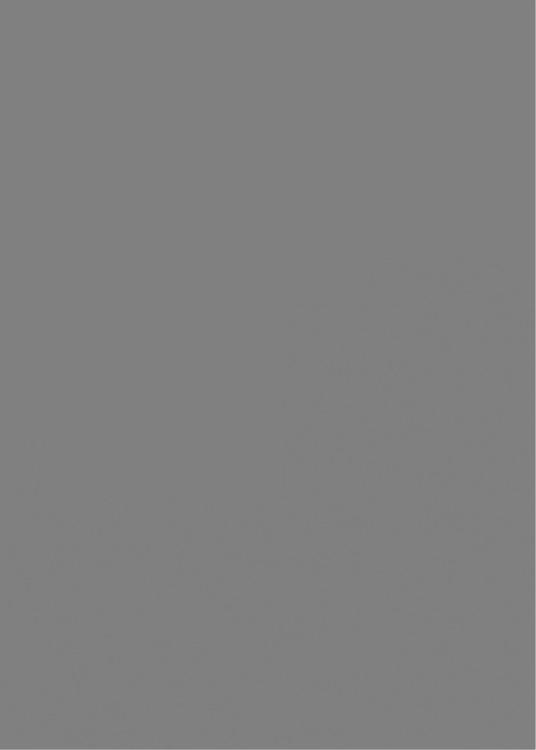
Многонаправленные углерод-углеродные композиты |
249 |
3.2.МЕТОДЫ ПРОПИТКИ ЖИДКОСТЬЮ
3.2.1.Выбор пропитывающего вещества. Число органиче ских соединений, которые можно использовать для пропитки армируюшего каркаса почти не ограничено. Однако, если при нять во внимание все требования, касающиеся технологии и свойств готового материала, выбор ограничится относительно небольшим рядом соединений.
Выбирая полимерную матрицу для пропитки, последую щего уплотнения каркаса и перевода его в углерод-углерод- пый композит, учитывают следующие характеристики мат рицы и продукта ее пиролиза: (а) вязкость; (Ь) выход кокса;
Таблица 8. Характеристики каменноугольного пека
Температура размягчения, °С |
|
94-107 |
Вязкость при температуре 250 °С, мПа-с |
|
30—50 |
Нерастворимые бензолом вещества, % |
|
24 -28 |
Нерастворимые хинолином вещества, % |
|
2 - 7 |
Коксовое число |
|
52 -62 |
Плотность, г/см3 |
|
1,28—1,31 |
Содержание серы, % |
|
0,1—0,6 |
Зольность, % |
|
0,2—0,5 |
Таблица 9. Характеристики фенольной смолы |
||
Плотность, г/см3 |
|
1,08-1,09 |
Содержание твердых веществ, % |
|
6 0 -62 |
Вязкость при температуре 25°С, мПа-с |
|
120—200 |
Показатель преломления |
165 °С, с |
1,518—1,525 |
Время отверждения при температуре |
85—105 |
|
Содержание свободного формальдегида, |
% |
0 -0 ,5 |
Содержание свободного фенола, % |
|
11,5-13,5 |
Содержание микропримесей (Na, К, Li, Fe), |
< 5 каждого, |
|
частей на миллион |
|
< 10 общее |
(с) микроструктуру кокса; (d) кристаллическую структуру кокса. Все эти характеристики зависят от давления и темпе ратуры, развивающихся в процессе получения углерод-угле- родных композитов.
Термореактивные фенольные и фурфуриловые смолы и пек из каменноугольной смолы или нефти являются двумя обычно применяемыми видами исходных материалов. Харак теристики типичных пека и смолы, применяемых для уплот нения углерод-углеродных композитов, приведены в табл. 8 и 9.
3.2.1.1. Термореактивные смолы. Применение термореак тивных смол обусловлено их хорошей пропитывающей
250 |
Л Макаллистер, У. Лакман |
способностью и наличием обширной технологической базы благодаря их широкому использованию в производстве пласт масс. Большинство термореактивных смол полимеризуются при сравнительно низких температурах (<250 °С) с образо ванием сильно сшитого неплавкого полимера — аморфного твердого тела. При пиролизе эти смолы образуют стекловид ный углерод, который не графитизируется при нагреве вплоть до 3000 °С [28, 25]. Выход кокса у термореактивных смол,
Таблица 10. Характеристики угля из термореактивных смол (37]
|
|
|
|
|
Характеристики дифракции |
||
|
|
|
|
Выход |
рентгеновских лучей угля |
||
|
Смола |
|
при 2700°С |
|
|||
|
|
угля. %* |
|
|
|
||
|
|
|
|
|
V А |
d002‘ |
^ |
Фенольная, отвержденная |
ос- |
57 |
68 |
3,43 |
|
||
нованием |
|
кис- |
56 |
132 |
3,40 |
||
Фенольная, отвержденная |
|||||||
лотой (литьевая) |
|
60 |
75 |
3,44 |
|||
Полиимидная |
фурфуриловых |
||||||
На |
основе |
63 |
75 |
3,41 |
|
||
эфиров |
|
|
73 |
40 |
3,45 |
||
Полибензимидазоловая |
|
||||||
Полифениленовая |
|
71 |
54 |
3,44 |
|||
Бисфенолформальдегидная |
65 |
83 |
3,43 |
||||
Сажа |
без термообработки |
при |
— |
17 |
3,63 |
||
Сажа, |
термообработанная |
— |
247 |
3.41 |
|
||
температуре 2700°С |
|
|
|
3,36 |
|||
Натуральный графит |
|
|
|
||||
* Определен методом термогравиметрии со скоростью нагрева до температуры 800вС, |
|||||||
5°С/мин. |
кристаллитов |
натурального графита, |
по-видимому, |
составляет |
тысячи |
||
** Lc для |
|||||||
ангстрем—величину, слишком |
большую |
для измерения методами |
расширения |
линии |
|||
па приборах, использованных для исследования образцов остальных материалов |
|
которые образуют необходимые циклические структуры, кон денсируются и легко превращаются в углерод, составляет от 50 до 56 % по массе [35]. Установлено, что некоторые смолы дают более высокий выход кокса, до 73 % по массе при тем пературе до 800 °С [37]. В табл. 10 содержатся данные по выходу кокса и рентгенодифракционные данные получаемого продукта для ряда термореактивных смол; данные по ди фракции рентгеновских лучей для углеродной сажи и при родного графита приведены для сопоставления. На рис. 21 показаны обобщенные зависимости некоторых характеристик фурфуриловой смолы и каменноугольного пека от темпера туры обработки. Как видно, термореактивные смолы дают менее плотный и менее графитизированный кокс, чем к.ямен-