
m0935
.pdf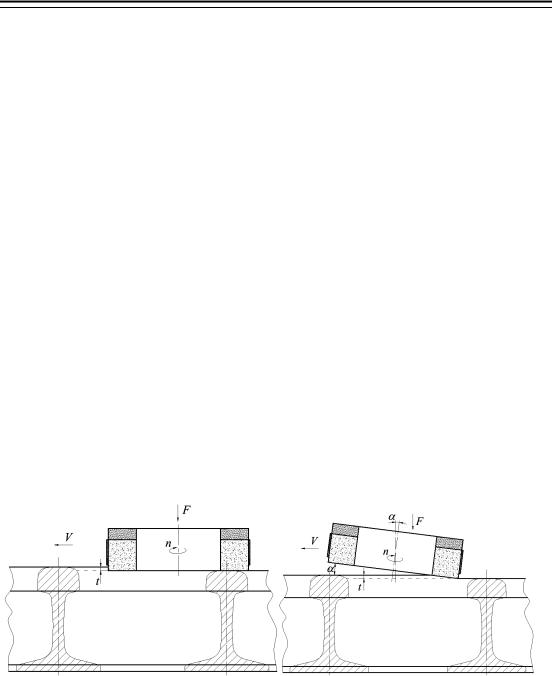
В.А. Аксенов, А.С. Ильиных
В связи с этим для процесса шлифования рельсов во всем мире до сих пор остается актуальным вопрос повышения производительности. Так, на железной дороге «Union Pacific» стремятся довести скорость выполнения работ по шлифованию рельсов до 12,8 км/ч за счет применения современного оборудования. На железной дороге «Burlington Northern», модернизируя рабочее оборудование фирмы «Loram», рассчитывают повысить скорость выполнения работ на 3,2 км/ч, тем самым увеличив ее до 8–9 км/ч. Фирмой «Pandrol Jacksons Technologies» ведутся работы по созданию рельсошлифовальных поездов с рабочей скоростью 16 км/ч и более [15].
Разработка нового высокопроизводительного технологического процесса шлифования рельсов в условиях железнодорожного пути применительно к российским условиям эксплуатации велась по трем направлениям.
Первое направление заключалось в устранении недостатка применяемой схемы шлифования (рис. 8, а), которая характеризуется невозможностью увеличения продольной подачи без снижения износостойкости инструмента. Известно, что производительность шлифования оценивают величиной удаляемого за проход припуска t с площади в единицу времени. При этом весьма важен показатель износостойкости шлифовального круга. Данные два критерия определяют эффективность шлифования.
Теоретический анализ процесса плоского шлифования показал, что абразивные зерна, обладающие меньшей потенциальной режущей способностью, проходят в теле металла больший путь, чем зерна, обладающие большей потенциальной режущей способностью [15].
а) |
б) |
Рис. 8. Схемы шлифования рельсов:
а – используемая схема шлифования; б – предлагаемая схема шлифования
Для устранения указанных недостатков предложена схема (см. рис. 8, б), отличие которой состоит в том, что абразивный круг устанавливается под углом к поверхности обрабатываемого рельса с раскрытием навстречу направлению движения рельсошлифовального поезда (угол атаки).
Новая схема шлифования позволяет реализовать равномерное распределение припуска между наибольшим числом абразивных зерен на рабочей по-
81

Технология транспортного машиностроения и ремонт подвижного состава
верхности круга, что позволяет существенно снизить износ инструмента и уровень ударных нагрузок, возникающих из-за неровности обрабатываемой поверхности рельса [15, 16].
Второе направление определялось тенденциями современного машиностроения. В настоящее время одним из наиболее перспективных направлений повышения эффективности процесса шлифования является повышение скорости вращения круга.
Эффективность применения высокоскоростного шлифования рассмотрена во многих работах, в которых на основании теоретических исследований доказывается, что увеличение скорости круга должно привести к пропорциональному уменьшению силы резания и шероховатости поверхности, увеличению съема металла на единицу силы резания. Уменьшение силы резания и шероховатости является следствием уменьшения размера удаляемых стружек при увеличении скорости круга. Если допустить, что удельная мощность шлифования постоянна, то станет очевидным, что наибольшие преимущества от применения высоких скоростей круга заключаются в пропорциональном увеличении интенсивности съема материала при тех же силах резания [15].
Третье направление определялось тем, что конструкция рабочего оборудования существующих рельсошлифовальных поездов не может обеспечить эффективность выполнения работ на всем диапазоне возможных условий шлифования профиля рельсов.
Шкала токовой нагрузки на рельсошлифовальных поездах ограничена значениями 18 и 28 А, которые определяют рабочий диапазон нагрузки электродвигателя. При выходе значений силы тока за рамки указанных границ происходит автоматическое отключение шлифовальных электродвигателей, а система управления работой рельсошлифовального поезда выводит их из работы как неисправные.
В настоящее время шлифование рельсов осуществляется торцешлифовальными кругами на бакелитовой связке с рабочей скоростью 47 м/с. Как уже было отмечено, повышение рабочей скорости круга до 100 м/с с одновременным увеличением продольной подачи позволяет увеличить производительность шлифования рельсов в два раза. Одним из основных факторов, ограничивающих повышение скорости резания, является прочность шлифовального круга, которая должна обеспечить его безопасную работу.
Для экспериментов использовались абразивные круги для скоростного шлифования, изготовленные в соответствии с результатами исследований по увеличению прочностных характеристик кругов [17–20].
Комплексное исследование показателей процесса плоского шлифования торцом круга по трем вышеуказанным направлениям позволило разработать технологию высокопроизводительного шлифования рельсов в условиях желез-
82

В.А. Аксенов, А.С. Ильиных
нодорожного пути, позволяющего по результатам лабораторных исследований повысить производительность шлифования в 2…2,5 раза [21].
Результаты лабораторных исследований новой технологии шлифования представлены в табл. 5.
Таблица 5
Основные условия и результаты исследований новой технологии шлифования (усредненные значения)
Диаметр |
Угол про- |
|
|
Частота вра- |
Контролируемые параметры |
||
|
|
|
Шерохова- |
Износ |
|||
Глубина |
|
щения шли- |
|
||||
шлифо- |
дольного |
резания, |
Скорость, |
фовального |
Температу- |
тость обрабо- |
шлифо- |
вального |
наклона |
мм |
км/ч |
круга, |
ра в зоне |
танной по- |
вального |
круга, мм |
круга, град |
|
резания, ºС |
верхности, |
круга, |
||
|
|
|
|
об/мин |
|
мкм |
мм/ч |
|
|
|
|
|
|
||
|
|
|
Новая схема шлифования |
|
|
||
250 |
1,5 |
0,3 |
15 |
7 000 |
450 |
40 |
5 |
|
|
Традиционная схема шлифования |
|
|
|||
250 |
0 |
0,3 |
8 |
3 600 |
600 |
80 |
8 |
Полученные результаты исследований положены в основу создания опытного образца рабочего оборудования рельсошлифовального поезда для проведения опытно-промышленных испытаний технологии. В ходе модернизации на рабочем оборудовании реализована возможность обеспечения угла атаки шлифовального круга 1,5°, а также изменения частоты его вращения в диапазоне 3 600–6 000 об/мин с увеличением мощности привода шлифовальной головки с 15 до 25 кВт. Конструктивные особенности РШП-16К позволили технологически увеличить рабочую скорость до 12 км/ч, что превышает штатную рабочую скорость поезда в два раза [22].
В ходе испытаний отработаны основные режимы шлифования и определены оптимальные параметры технологического процесса скоростного шлифования. Изменение схемы шлифования позволило увеличить съем металла без изменений интенсивности износа инструмента и качества шлифования. Реализация преимуществ, полученных при увеличении скорости шлифовального круга, позволила резко повысить эффективность процесса.
По результатам испытаний произведена корректировка конструкции рабочего оборудования и технологической документации, на основании которой проведена модернизация рельсошлифовального поезда РШП-16К под разработанную высокопроизводительную технологию шлифования рельсов в условиях железнодорожного пути [23].
Реализация разработанной технологии позволила увеличить точность формообразования, обеспечить требуемую шероховатость обработанных участков головки рельсов, тем самым повысив качество их профилирования, и сформировать повышенные эксплуатационные свойства рельсов. В целом комплексное внедрение результатов исследований позволило в значительной сте-
83

Технология транспортного машиностроения и ремонт подвижного состава
пени повысить эффективность технологии шлифования рельсов в условиях железнодорожного пути [24].
Многолетние исследования в области совершенствования технологии шлифования рельсов позволили получить следующие результаты:
1.Обоснованы и разработаны научно-методические основы высокопроизводительной технологии шлифования рельсов в условиях железнодорожного пути, позволившие сформировать технические и технологические решения, внедрение которых вносит значительный вклад в развитие железнодорожной отрасли за счет повышения эффективности эксплуатации, содержания и ремонта железнодорожного пути.
2.Разработан комплекс математических моделей процесса шлифования рельсов, учитывающих особенности обработки в условиях железнодорожного пути, заключающиеся в упругой подвеске шлифовальных головок и большой протяженности обрабатываемой поверхности.
3.Разработана модель формообразования поперечного профиля головки рельса несколькими инструментами, работающими по схеме плоского шлифования торцом круга, учитывающая технологическое наследование после обработки каждым абразивным кругом.
4.Выявлены закономерности изменения эксплуатационных свойств головки рельса после шлифования по критериям циклической трещиностойкости, контактно-усталостной прочности и износостойкости в зависимости от параметров качества поверхности.
Библиографический список
1.Нормативно-техническая документация: Технические указания по шлифованию рельсов / ОАО «РЖД». М., 2004. 39 с.
2.Аксенов В.А., Ильиных А.С. Оценка эффективности технологического процесса шлифования рельсов в пути // Изв. вузов. Машиностроение. 2007. № 1. С. 49–57.
3.Ильиных А.С. Особенности современной ресурсосберегающей технологии шлифования рельсов в пути // Политранспортные системы: М-лы VII Всерос. науч.-техн. конф. Красноярск. Новосибирск: Изд-во СГУПСа, 2010. С. 249–253.
4.Юркова Е.О. Повышение производительности технологического процесса восстановления служебных свойств рельсов шлифованием за счет оптимизации выбора ремонтных профилей: Дис. … канд. техн. наук. Новосибирск, 2001. 138 с.
5.Ильиных А.С. Научно-методические основы высокопроизводительной технологии шлифования рельсов в условиях железнодорожного пути // Вестник СГТУ. 2013. № 1. С. 82–88.
6.Ильиных А.С. Возможности управления уровнем эксплуатационных свойств рельсов на основе формирования требуемых параметров качества поверхности: Дис. … канд. техн. наук. Новосибирск, 2005. 140 с.
7.Ильиных А.С. Формирование качества поверхности при плоском шлифовании торцом круга // Технология машиностроения. 2011. № 4. С. 19–22.
8.Кузьменя А.А. Повышение эффективности технологических процессов шлифования рельсов в пути: Дис. … канд. техн. наук. Новосибирск, 2000. 137 с.
84

В.А. Аксенов, А.С. Ильиных
9.Аксенов В.А., Ильиных А.С. Теплофизический анализ процесса плоского шлифования рельсов торцом круга // Вестник Южно-Урал. гос. ун-та. Сер. Машиностроение. 2012. № 33. С. 96–100.
10.Дмитриева О.В. Возможность повышения долговечности рельсов за счет рациональных режимов и условий шлифования их в пути: Дис. … канд. техн. наук. Новосибирск, 2003. 130 с.
11.Тихомирова Л.Б., Дмитриева О.В. Формирование остаточных напряжений за счет регулирования режимов шлифования рельсов // Современные технологии железнодорожному транспорту: М-лы науч.-практ. конф. Хабаровск, 2003. С. 120–122.
12.Турутин Б.Б. Совершенствование технологической системы обеспечения требуемого уровня эксплуатационных свойств рельсов в пути: Дис. … канд. техн. наук. Новосибирск, 2003. 135 с.
13.Щелоков С.В. Повышение эксплуатационных свойств рельсов в пути на основе разработки комбинированного технологического процесса шлифования с использованием высокоэнергетического воздействия: Дис. … канд. техн. наук. Новосибирск, 2005. 130 с.
14.Ильиных А.С. Влияние процесса шлифования на уровень эксплуатационных свойств рельсов // Научное обозрение. 2006. № 2. С. 88–91.
15.Ильиных А.С. Скоростное шлифование рельсов в пути // Мир транспорта. 2011.
№3 (36). С. 56–61.
16.Шаламов В.А. Повышение производительности технологии шлифования рельсов в пути торцом круга: Дис. … канд. техн. наук. Новосибирск, 2000. 130 с.
17.Филиппов И.А. Повышение эффективности процесса шлифования рельсов в пути за счет улучшения эксплуатационных показателей абразивного инструмента: Дис. … канд. техн. наук. Новосибирск, 2002. 137 с.
18.Фефелов В.Н. Повышение эксплуатационных свойств поверхности катания рельсов за счет оптимизации режимов шлифования и параметров абразивного инструмента: Дис. … канд. техн. наук. Новосибирск, 2006. 126 с.
19.Ильиных А.С. Разработка абразивного инструмента для скоростного шлифования
рельсов // Технология машиностроения. 2013. № 3. С. 26–30.
20. Пат. 59472 Российская Федерация, МПК B 24 D 5/02. Шлифовальный круг / В.А. Аксенов, А.С. Ильиных, С.В. Щелоков. № 2006133526/22; заявл. 19.09.2006; опубл. 27.12.2006, Бюл. № 36.
21.Пат. 2391458 Российская Федерация, МПК E 01 B 31/13, 31/17. Способ обработки поверхности головки рельса / В.А. Аксенов, А.С. Ильиных, С.В. Щелоков. № 2008149876/11; заявл. 18.12.2008; опубл. 10.06.2010, Бюл. № 11.
22.Пат. 84856 Российская Федерация, МПК E 01 B 31/17. Устройство для шлифования
длинномерных изделий / В.А. Аксенов, А.С. Ильиных, А.Д. Абрамов, В.В. Банул.
№2009104978/22; заявл. 13.02.2009; опубл. 20.07.2009, Бюл. № 22.
23.Ильиных А.С. Модернизация рабочего оборудования рельсошлифовального поезда // Строительные и дорожные машины. 2013. №2. С. 12–18.
24.Шаламова О.А., Фефелов В.Н., Ильиных А.С. Снижение эксплуатационных расходов предприятий железнодорожного транспорта на основе оптимизации технологических процессов // Вестн. Вост.-Укр. нац. ун-та им. В. Даля. 2005. № 8 (90). С. 220–223.
85

Технология транспортного машиностроения и ремонт подвижного состава
УДК 621.96
В.А. Каргин, А.Д. Абрамов
Математическое моделирование низкочастотных линейных электромагнитных двигателей
Одним из показателей эффективности виброударных машин является уровень энергии единичного удара, отнесенной к массе машины. Для существующих ручных машин он составляет 1–2 Дж/кг, что зачастую недостаточно даже для начала пластического течения материала. Вместе с тем проведенный нами анализ показал, что для реализации ряда виброударных технологий он должен составлять 10–15 Дж/кг, что нелегко получить обычными путями.
Одним из путей решения рассматриваемой задачи может быть использование в качестве привода линейного электромагнитного двигателя (ЛЭМД) возвратно-поступательного движения, обладающего способностью к значительным перегрузкам при работе в повторно-кратковременном режиме. При этом якорь электромагнита выполняет роль бойка, а сам двигатель превращается в электромагнитную машину ударного действия.
К задачам расчета ЛЭМД относится определение следующих геометрических и электрических параметров: длины и диаметра бойка; длины, внутреннего и наружного диаметров катушки; сечения и числа витков.
По способу преобразования электрической энергии в механическую работу электромагнитные машины ударного действия представляют собой специфический класс электрических машин. Это позволяет использовать для анализа динамики линейных электромагнитных двигателей общие положения теории электрических машин.
Известно, что для машин переменного тока мощность связана с электромагнитными нагрузками и главными геометрическими размерами следующим соотношением:
(1)
где Ω – обобщенный коэффициент, учитывающий частоту питающей сети; DC – диаметр расточки статора; AS – линейная токовая нагрузка, определяемая величиной потребляемого тока, отнесенной к длине машины; Bδ – индукция в рабочем воздушном зазоре; А – длина машины (статора).
Как видно из (1), увеличение мощности (или энергии единичного удара) при заданных размерах двигателя может быть достигнуто увеличением AS и Bδ. Но так как величина Bδ имеет некоторое предельное значение, определяемое свойствами ферромагнитного материала, то увеличение энергии удара при D2C A = const может происходить только за счет роста AS. При этом частота питающей сети должна быть снижена таким образом, чтобы среднее за период
86
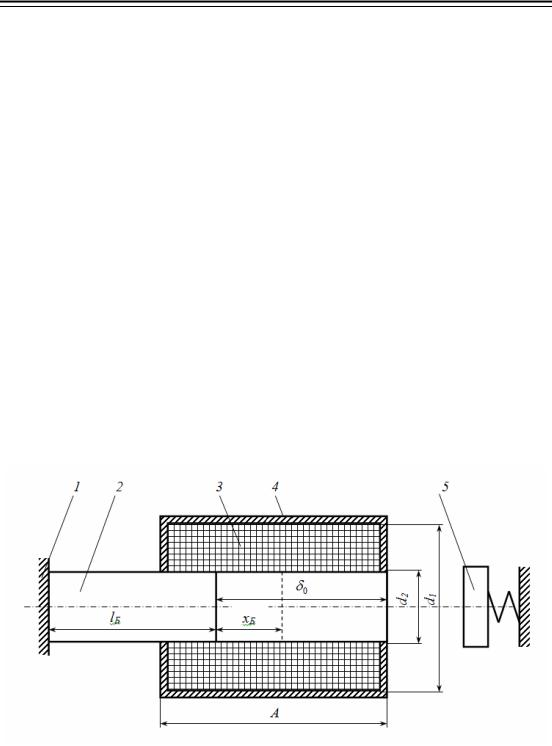
В.А. Каргин, А.Д. Абрамов
значение тока, определяющее нагрев машины и нагрузку на сеть, оставалось неизменным.
Необходимость повысить примерно на порядок удельную энергию удара требует точно такого же снижения частоты ударов. Очевидно, что машины ударного действия, частота ударов которых примерно на порядок ниже, чем частота питающей сети, следует считать низкочастотными.
Увеличение энергии удара неизбежно приведет к качественным изменениям в работе приводного двигателя за счет роста электромагнитных нагрузок и их импульсного характера, обусловленного рассогласованием между частотой питающего напряжения и частотой ударов. Указанные особенности должны быть учтены при проектировании электромагнитных низкочастотных машин ударного действия.
Основными требованиями, определяющими выбор конструкции двигателя, являются его способность к перегрузкам и устойчивость работы при пониженном напряжении. Линейный электромагнитный двигатель, непосредственно преобразующий электроэнергию в возвратно-поступательное движение бойка, отвечает этим требованиям в наибольшей степени. При его использовании существенно повышается надежность двигателя, поскольку он имеет только одну движущуюся деталь – якорь (боек).
Силовая часть привода, конструктивная схема которого приведена на рис. 1, представляет собой цилиндрическую катушку со стальным сердечником и магнитопроводом, сечение которого равно сечению бойка.
Рис. 1. Схема силовой части привода:
1 – неподвижный ограничитель; 2 – боек; 3 – силовая катушка; 4 – наружный магнитопровод; 5 – подвижный ограничитель вылета бойка
87
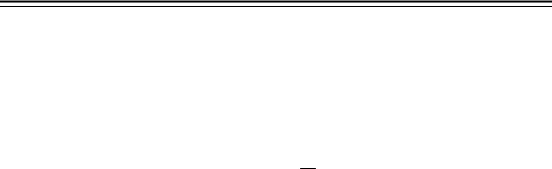
Технология транспортного машиностроения и ремонт подвижного состава
В начале рабочего цикла боек фиксирован относительно ограничителя, начальный воздушный зазор δ0 = const. Динамика такой электромагнитной системы описывается (без учета сил сопротивления движению бойка) известными уравнениями движения якоря и электрического равновесия:
|
|
1 |
|
dL |
|
2 |
|
|
mБхБ |
|
|
|
|
i |
|
; |
(2) |
2 |
|
dx |
|
|||||
|
|
|
|
Б |
|
|
|
|
di u irw L dt ,
где mБ – масса бойка; хБ = δ0 – перемещение бойка; L – мгновенное значение индуктивности; i, u – мгновенные значения тока и напряжения соответственно; rw – активное сопротивление катушки.
Уравнения (2) нелинейны и не допускают точного аналитического решения, а погрешности приближенных решений определяются выбором удачной аппроксимации функции L = L(xБ). Для рассматриваемого класса электромагнитных двигателей аппроксимирующие функции принимают сложный вид, что затрудняет даже приближенное аналитическое решение. Кроме того, при этом не решается и задача синтеза двигателя, поскольку его конструктивные параметры должны быть определены предварительно. Вместе с тем проведенные нами исследования электромагнитных двигателей [1] показали, что при увеличенных электромагнитных нагрузках, составляющих Im = 300 A; Вδ = 2 Тл, протекающие в них электрические и механические процессы имеют явно выраженный синусоидальный характер, что возможно только при условии
dL |
const, |
(3) |
|
||
dx |
|
когда индуктивность L = L(t) также изменяется по синусоидальному закону. Такое допущение позволяет вести расчет двигателя в квазистационарном
режиме с использованием метода эквивалентных синусоид, суть которого заключается в том, что фактическая кривая тока заменяется синусоидой, площадь которой равна площади реальной кривой.
Так как уравнение электрического состояния приводится к виду
u ir L |
di |
, |
(4) |
w |
dt |
|
то расчет высоконагруженных ЛЭМД можно вести с использованием методов расчета статических электрических машин и трансформаторов.
Прежде всего необходимо рассчитать геометрические и кинематические (перемещение, скорость и ускорение) параметры бойка, определяющие уровень энергии единичного удара. В том случае, если имеется прототип, т.е. ЛЭМД, обладающий удовлетворительными характеристиками, но не отвечающий требованиям по энергии единичного удара, расчет проектируемого двигателя можно вести с использованием методов теории подобия.
88

В.А. Каргин, А.Д. Абрамов
В настоящее время при расчетах методом подобия для механически подобных систем используется отношение коэффициентов подобия
FCtC |
1, |
(5) |
|
||
mС C |
|
где FC – коэффициент подобия силы, приложенной к бойку; tС – коэффициент подобия времени протекания процесса; mC и δС – коэффициенты подобия массы и хода якоря соответственно.
Но для высоконагруженных электромагнитных машин коэффициент подобия времени tС ≠ 1, так как в связи с большой величиной ЭДС самоиндукции период действия тока не равен полупериоду напряжения сети, а рассчитать его практически невозможно. Кроме того, он будет различным для каждого проектируемого электромагнитного двигателя. Поэтому в целях уменьшения погрешности расчетов следует исключить явно входящее в расчетные зависимости время.
Исходным параметром является отношение энергий единичного удара прототипа 1 и модели 2 (проектируемого ЛЭМД):
T |
|
T1 |
. |
(6) |
|
||||
С |
|
T |
|
|
|
2 |
|
|
При определении массы бойка mБ принимаются во внимание геометрические соотношения. Если изменить линейный размер l в lC раз, то площадь будет изменяться в lC2 раз, объем в lC3 раз. На основании геометрического подобия двух машин можно определить значения степеней коэффициентов подобия основных геометрических параметров этих машин, определяемых размерами бойка.
Масса бойка цилиндрической формы
m |
|
d |
2 |
l |
|
, |
(7) |
|
Б |
|
|||||
4 |
|
|
|||||
Б |
|
|
|
Б |
|
|
где – удельный вес материала бойка; dБ = d2 – диаметр бойка; lБ – длина бойка. Отсюда коэффициент подобия массы бойка
mБС lС3 . |
(8) |
Аналогичным образом находятся и остальные коэффициенты подобия. Кинетическая энергия бойка
Т |
m 2 |
|
|
Б Б |
. |
(9) |
|
|
|||
2 |
|
|
Скорость бойка υБ в момент его соударения с инструментом ограничивается по условию механической прочности и принимается равной скорости бойка оригинала, т.е. υБС = 1. Коэффициент ее подобия
Т |
С |
m |
2 |
l3 . |
(10) |
|
БС |
БС |
С |
|
89
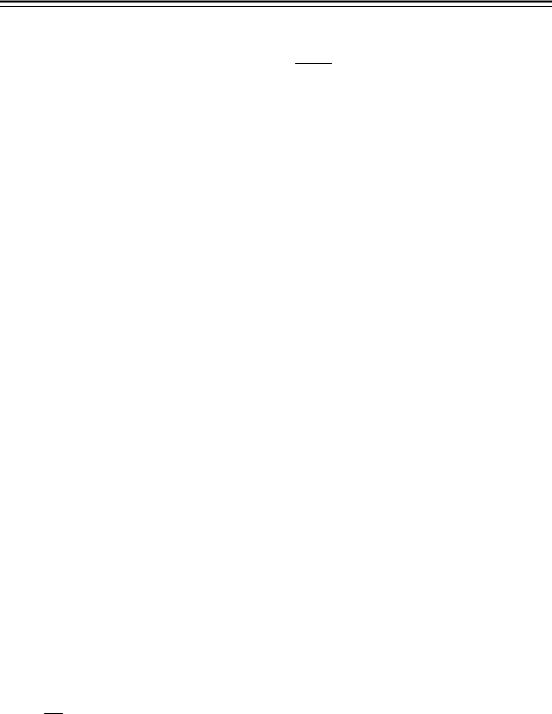
Технология транспортного машиностроения и ремонт подвижного состава
Для силы тяги электромагнита
F |
В2S |
Б , |
(11) |
|
2 О
где SБ – площадь сечения бойка; µО – магнитная проницаемость воздуха. Коэффициент подобия силы тяги
F |
В2 l2 |
l2 |
, |
(12) |
|
С С |
|||||
2 ОС |
|||||
С |
С |
|
|
где μОС – коэффициент подобия магнитной проницаемости воздуха (μОС = 1). Приведенная в (12) величина индукции в воздушном зазоре определяется
ферромагнитными свойствами материала и не может превышать величины его насыщения. Для стали 45, из которой изготовлен боек, она составляет Вδ = 1,95 Тл и остается неизменной для всех подобных ЛЭМД. При определении размеров катушки и магнитопровода следует ввести поправки на радиальную и аксиальную толщины каркаса.
Дальнейшие расчеты не могут быть выполнены традиционными методами подобия. Действительно, для того чтобы рассчитать наружный диаметр катушки, с изменением которого меняется индуктивность L, надо знать число витков катушки и сечение обмоточного провода. Если известны габаритные размеры катушки, то приближенное число витков может быть найдено. Обратная задача, даже решаемая последовательными приближениями, неоднозначна и может быть решена только после выбора критерия, оптимизирующего соотношения между рассчитываемыми параметрами.
В качестве такого критерия предлагается ввести понятие коэффициента электромагнитного подобия, который характеризует электромагнитные нагрузки подобных ЛЭМД. Он должен определять плотность энергии, т.е. энергию, приходящуюся на единицу объема машины, и являться аналогом машинной постоянной электрических машин вращательного действия.
Исходя из сказанного этот коэффициент можно представить в виде
К |
|
|
1 |
|
const, |
(13) |
эм |
|
|
||||
|
|
В А |
|
|||
|
|
|
|
S |
|
где Кэм – электромагнитная постоянная машины; АS – линейная токовая нагрузка, определяемая количеством витков w, током I и длиной катушки А
Iw
( АS А ).
Если допустить, что у оригинала 1 и модели 2 напряжение питающей сети неизменно, т.е.
U |
1 |
U |
2 |
w A2 |
const, |
(14) |
|
|
|
1 |
1 |
|
|
то для проектируемой машины количество витков определится из выражения
90