
m0935
.pdf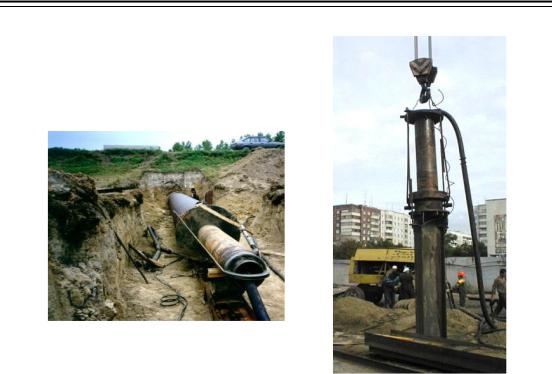
Б.Н. Смоляницкий, Ю.Н. Сырямин
Рис. 3. Сооружение пневмомолотом «Тайфун-740» бестраншейного перехода диаметром 1 м под автодорогой Новосибирск – Омск и свайного ограждения котлована
при строительстве станции метро «Березовая роща»
В основу конструирования таких пневмомолотов были заложены новые принципы, основанные на идее применения системы воздухораспределения с упругим клапаном, которая обеспечивает снятие противодавления в управляемой камере и устранение ее избыточного объема. Теоретически и экспериментально получены рациональные значения параметров, реализация которых в действующих образцах дала по сравнению с аналогами возрастание энергии удара (до 50 %) при снижении расхода воздуха (масса и размеры машины не изменялись). Приведенные индикаторные диаграммы пневмомолота «Тайфун» и наиболее известного аналога – пневмомолота М-200 иллюстрируют этот эффект (рис. 4).
61
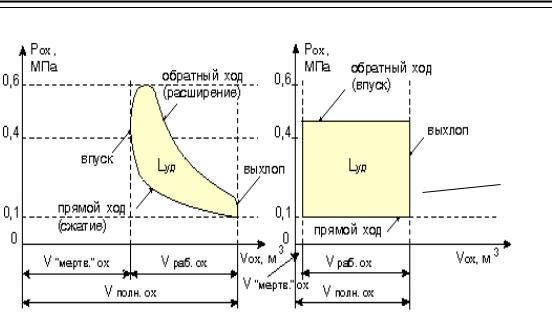
Системы машин на транспорте и в транспортном строительстве
а) |
|
б) |
|
|
|
Энергия
удара
Рис. 4. Индикаторные диаграммы (камера обратного хода ударника) пневмомолотов М-200 (а) и «Тайфун» (б)
На основе проведенных исследований разработан типоразмерный ряд пневмомолотов «Тайфун», больший из которых имеет массу ударника 1 500 кг. Новые разработки защищены патентами РФ. На предприятиях России работает более ста пневмомолотов. Осуществляется их экспорт в Литву, Польшу, Украину. За разработку пневмомолотов «Тайфун» авторы награждены золотыми медалями и дипломами отечественных и зарубежных выставок.
Проходка протяженных скважин – важнейшая составляющая многих технологий в строительстве и горном деле. Она используется при прокладке коммуникаций бестраншейным способом, в строительстве подземных сооружений без вскрытия породного массива, сооружении анкеров, изготовлении буронабивных свай, при проходке взрывных скважин и т.п. Процесс бурения является определяющим в подобного вида работах и значимые результаты, достигнутые в этой области, связаны в основном с бурением. Важным направлением повышения производительности бурения как в грунтах, так и в прочных горных породах является снижение энергоемкости процесса разрушения массива.
Механизм разрушения породы и энергоемкость процесса определяются удельной величиной нагрузки на забой скважины. Под ее воздействием может происходить либо усталостное, либо менее энергоемкое объемное разрушение с получением крупной фракции шлама. Поэтому определение условий получения объемного разрушения, установление обеспечивающих эти условия параметров инструмента и их сочетания с необходимым энергетическим воздействием является определяющей задачей повышения эффективности бурения.
Комплексные исследования, проведенные в ИГД СО РАН под руководством чл.-кор. РАН В.Н. Опарина, позволили открыть явление знакопере-
62

Б.Н. Смоляницкий, Ю.Н. Сырямин
менной реакции горных пород на динамические воздействия [5–8]. Его сущность заключается в том, что при образовании полостей внутри массивов горных пород под действием взрыва, в окрестностях последних происходят колебательные смещения геоблоков относительно друг друга с их трансляционным и вращательным движением. Наличие этого эффекта свидетельствует о том, что значительная доля энергии взрыва и запасенной упругой энергии горных массивов расходуется не только на дробление горных пород в очаговой зоне, но и передается им в виде кинетической энергии. Используя это явление, В.Н. Опарин теоретически обосновал и экспериментально доказал существование в массивах горных пород нового типа нелинейных упругих волн [9]. Элементарными носителями этого типа волн являются геоблоки различного иерархического уровня за счет своего трансляционного и вращательного движения в результате импульсного воздействия определенного энергетического класса. Эта группа низкоскоростных волн (300–600 м/с и менее) получила название волн маятникового типа Uμ. Наиболее разрушительное действие на массивы горных пород связано именно с такими волнами. Это воздействие характеризуется энергетическим критерием, который удобно представить в безразмерном виде:
k |
W |
10 , |
(1) |
|
M 2 |
||||
|
|
|
где W – энергетическая характеристика для очаговой зоны разрушения; М – масса пород очаговой зоны их объемного разрушения; – скорость продоль-
ной волны для соответствующего типа пород объемом V (М = ρV, где ρ – плотность пород); θ и γ – коэффициенты с положительными значениями, лежащими в достаточно ограниченном диапазоне.
С целью повышения эффективности бурения скважин в прочных горных породах, например, при проходке взрывных скважин исследованы процессы разрушения геоматериалов импульсными нагрузками.
Эксперименты, проведенные недавним выпускником факультета канд. техн. наук В.В. Тимониным [10], показали, что этот критерий действует не только на макроуровне, но и на микроуровне при воздействии на образец породы механическим способом. Способ реализован инструментом погружной пневмоударной машины, применяемом при проходке протяженных скважин.
Характерные зависимости изменения энергоемкости процесса механического разрушения образца геоматериала от энергии единичного удара представлены на рис. 5. Образец имел форму пластины с размерами основания – 0,3 0,3 м при толщине 0,03 м.
63
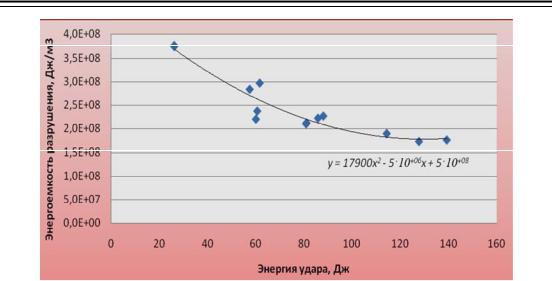
Системы машин на транспорте и в транспортном строительстве
Рис. 5. Зависимость энергоемкости процесса разрушения от энергии единичного удара
На рис. 6 приведены графики изменения энергетического критерия k от энергии единичного удара ударника (порода – гранит). При этом использовалась формула (1) в ее модифицированном к условиям эксперимента варианте:
k |
E0 |
10 , |
(2) |
|
V 2 |
||||
|
|
|
где – коэффициент импульсного воздействия на породный массив заданных энергетических классов; E0 – подводимая на разрушаемую поверхность энергия от породоразрушающего инструмента.
Значения ,V, для испытуемых геоматериалов определялись экспери-
ментально, E0 задавалось в определенном диапазоне.
Оказалось, что при 1 4 и 9 коэффициент принимает значение,
равное 1,5 ∙ 10–6. Это значение, полученное для испытуемых образцов, близко к прогнозному , полученному путем экстраполяции данных академика М.А. Садовского [11], касающихся мощного воздействия на породный массив подземных взрывов. При этом учитывалось, что испытуемые модели находились в свободном состоянии на поверхности земли и, следовательно, не испытывали существенных внутренних напряжений, обусловливаемых действием горного давления в глубине массива горных пород.
64
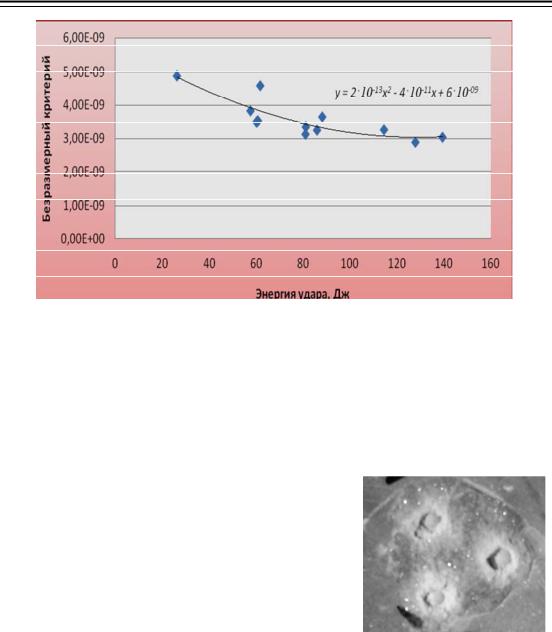
Б.Н. Смоляницкий, Ю.Н. Сырямин
Рис. 6. Зависимость критерия k от энергии единичного удара (инструмент – трехштыревой; расстояние между штырями 15, 20 и 25 мм; разрушаемая порода – гранит)
Таким образом, критерии катастрофического разрушения как массива в целом, так и его части, подвергаемой механическому воздействию, близки друг другу, а в зоне минимальной энергоемкости возникают геомеханические квазирезонансные явления, вызывающие максимальные объемы разрушения.
Это означает, что при ударном разрушении породного материала инструментом, оснащенным сферическими инденторами, существует пороговое значение энергии удара, обеспечивающее объемное разрушение материала с минимальной энергоемкостью, и критерий минимальной энергоемкости ударного разрушения горной породы.
Полученный результат является фундаментальной предпосылкой повышения эффективности динамического способа разрушения породного массива за счет согласования его свойств с параметрами машины ударного действия и породоразрушающего инструмента.
По результатам исследований разработаны и испытаны в натурных условиях рудников ООО «Евразруда» Горно-Шорского
филиала погружные пневмоударники и расширители скважин с новым штыревым породоразрушающим инструментом (рис. 8), обеспечившие увеличение на 50 % скорости бурения в сравнении с аналогами при достаточной стойкости инструмента.
65
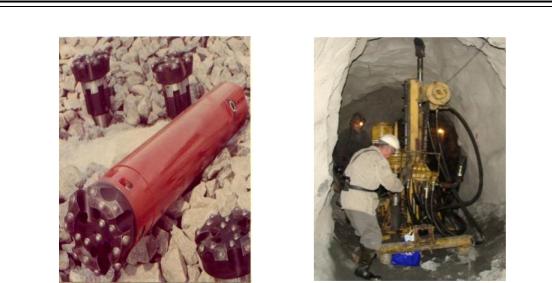
Системы машин на транспорте и в транспортном строительстве
а) |
б) |
Рис. 8. Вид: а – погружного пневмоударника П-110; б – бурового станка НКР-100
Известно, что бесстыковой железнодорожный путь имеет сложное на- пряженно-деформированное состояние, которое определяется не только воздействием сил от колес подвижного состава, но и воздействием сил, вызываемых изменениями температурного режима самих рельсов. Например, изменение температуры рельса Р65 на 1 °С изменяет продольную силу в нем на
41,5 кН [3].
При повышении температуры рельсовых плетей относительно темпера-
туры, при которой осуществлялось их крепление к шпалам, в них могут возникать сжимающие силы до 1 000 кН (зона Западной Сибири), создающие опасность выброса пути.
При понижении температуры плети возникает вероятность ее излома и появления опасного для прохода ходового колеса зазора, а при слабой затяжке клеммных и стыковых болтов может произойти разрыв стыка.
Реологические процессы в рельсах протекают достаточно медленно, и при резких изменениях температуры возможна потеря устойчивости пути. Наблюдения [3] показали, что независимо от длины рельсовых плетей и от способа разрядки напряжений максимальные дополнительные напряжения от неравномерного их распределения вдоль плети составляют около 35∙103 кН/м2. Очевидно, что перераспределение напряжений сжатия (релаксацию) можно выполнить только ударным методом. Это объясняется тем, что рельс является своего рода стержнем малой жесткости и статически приложенными усилиями его реально можно только растягивать.
Для эффективного воздействия на рельс целесообразна ударная система с неторцевым соударением и передачей энергии удара рельсу через зажимной механизм, т.е. близкая по своей сути динамической системе ударных машин со сквозным осевым каналом.
66

Б.Н. Смоляницкий, Ю.Н. Сырямин
Эксперименты показали, что волны деформаций, возникшие в контактном сечении рельса, распространяются по нему одновременно в обе стороны от места возникновения. Причем по направлению удара в плети распространяется волна напряжений сжатия (деформаций), а в противоположную сторону – волна напряжений растяжения.
Установлено, что для прохождения по плети (на расстояние до 150 м) ударного импульса энергия удара, достаточная для перераспределения напряжений, должна быть не менее 1 500 Дж. Если плеть вывесить на роликоопоры либо установить на антифрикционные подкладки, протяженность рабочей зоны увеличивается примерно в два раза. Исследования показали, что ударное воздействие приводит к снижению напряжений в рельсовой плети в среднем на 60 %. При рассмотрении изменения напряженно-деформированного состояния рельсовой плети при прохождении по ней ударного импульса без учета и с учетом сил трения установлено, что энергия импульса уменьшается на величину работы сил трения. Теоретически установлена длина участка, на котором происходит затухание ударной волны. Определяющее значение при этом имеют величины погонного сопротивления, погонного веса рельса и скорости распространения продольной ударной волны.
Важно, что смещения поперечных сечений от воздействия ударного импульса распределяются равномерно.
По результатам исследований разработан технологический процесс релаксации напряжений в рельсах бесстыкового пути и устройство ударного действия для его реализации, способное обеспечить передачу рельсу энергии удара в любом его поперечном сечении (решения защищены авторскими свидетельствами на изобретения).
Таким образом, осуществляемые в рамках научно-образовательного центра реальные разработки сотрудников выпускающей кафедры и выпускников, работающих в ИГД СО РАН, позволяют внедрить на производстве конкурентоспособные новые технологические процессы, экономящие трудовые и материальные ресурсы.
Мы с уверенностью смотрим в будущее, потому что основополагающие принципы совместной работы, которые заложены предыдущими поколениями, восприняты и взяты на вооружение молодыми учениками-коллегами, ставшими квалифицированными специалистами.
Библиографический список
1.Гербер А.Р., Сырямин Ю.Н., Смоляницкий Б.Н. Применение пневмоударных машин для лечения земляного полотна железных дорог // Применение пневмоударных машин для лечения земляного полотна железных дорог: Сб. науч. тр. Новосибирск: Изд-во СГУПСа, 2001.
С. 45–62.
2.Крицкий М.Я., Сырямин Ю.Н., Смоляницкий Б.Н., Скоркин Н.Ф. Комплекс мобильных машин и механизмов для упрочнения и армирования грунтов // Опыт строительства и реконст-
67

Системы машин на транспорте и в транспортном строительстве
рукции зданий и сооружений на слабых грунтах: Сб. тр. Междунар. науч.-практ. конф. Архангельск, 2003. С. 73–78.
3.Грищенко В.А., Коломеец Р.Г., Сырямин Ю.Н., Смоляницкий Б.Н. Технические средства для ввода рельсовых плетей бесстыкового пути в расчетный режим эксплуатации // Повышение эффективности работы пути с бесстыковыми плетями и длинными рельсами в условиях Сибири и Казахстана: Межвузовский сб. науч. тр. Новосибирск, 1987. С. 11–18
4.Смоляницкий Б.Н., Червов В.В., Трубицын В.В., Вебер И.Э., Тищенко И.В. Новые пневмоударные машины «Тайфун» для выполнения специальных строительных работ // Механизация строительства. 1997. № 18. С. 50–62.
5.Курленя М.В., Опарин В.Н. Проблемы нелинейной геомеханики. Ч. I // Физикотехнические проблемы разработки полезных ископаемых. 1999. № 3. С. 12–27.
6.Курленя М.В., Опарин В.Н. Проблемы нелинейной геомеханики Ч. II // Физикотехнические проблемы разработки полезных ископаемых. 2000. № 4. С. 3–27.
7.Курленя М.В., Опарин В.Н. , Ревуженко А.Ф., Шемякин Е.И. О некоторых особенностях реакции горных пород на взрывные воздействия в ближней зоне // ДАН СССР. 1987. Т. 273. № 1. С. 265–268.
8.Курленя М.В., Адушкин В.В., Опарин В.Н. и др. Знакопеременная реакция горных пород на динамическое воздействие // ДАН СССР. 1992. Т. 323. № 2. С. 363–366.
9.Методы и измерительные приборы для моделирования и натурных исследований нелинейных деформационно-волновых процессов в блочных массивах горных пород / В.Н. Опарин и др. Новосибирск: Изд-во СО РАН, 2007. 320 с.
10.Тимонин В.В. Оценка процесса разрушения горных пород при динамическом вдавливании группы инденторов с точки зрения нелинейной геомеханики // Геодинамика и напряженное состояние недр Земли: Сб. тр. конф. Новосибирск: ИГД СО РАН, 2007. С. 186–190.
11.Курленя М.В., Опарин В.Н., Востриков В.И. О геомеханических условиях возникновения квазирезонансов в геоматериалах и блочных средах // Физико-технические проблемы разработки полезных ископаемых. 1998. № 5. С. 6–16.
НАПРАВЛЕНИЕ «ТЕХНОЛОГИЯ ТРАНСПОРТНОГО МАШИНОСТРОЕНИЯ И РЕМОНТ ПОДВИЖНОГО СОСТАВА»
УДК 691.795.2
В.А. Аксенов, А.С. Ильиных
Повышение эффективности технологии шлифования рельсов в условиях железнодорожного пути
Российские железные дороги – одна из крупнейших железнодорожных магистралей мира, являющаяся ключевым звеном транспортной системы нашей страны.
68
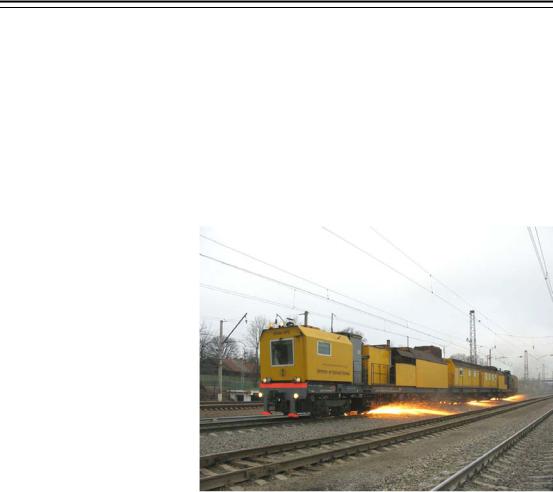
В.А. Аксенов, А.С. Ильиных
Наиболее дорогостоящим и ответственным элементом железнодорожного пути, состояние которого в первую очередь определяет бесперебойное и надежное движение поездов, являются рельсы. Общая масса рельсовой стали, вложенной в транспортную сеть страны, составляет более 50 млн т. Для поддержания рельсового хозяйства в исправном состоянии ежегодно требуется более 3 млн т новых рельсов. В современных условиях эксплуатации железных дорог с ростом скоростей движения и грузонапряженности потребность в новых рельсах с каждым годом только возрастает, поэтому задача продления жизненного цикла рельсов имеет огромное значение для путевого хозяйства
железнодорожной отрасли. |
|
|||
Наиболее |
перспек- |
|
||
тивным |
направлением в |
|
||
решении |
данной |
задачи |
|
|
является технология шли- |
|
|||
фования рельсов с приме- |
|
|||
нением рельсошлифоваль- |
|
|||
ных поездов (рис. 1), по- |
|
|||
зволяющая |
производить |
|
||
механическую |
обработку |
|
||
головки рельса без его де- |
|
|||
монтажа в условиях же- |
|
|||
лезнодорожного пути. |
|
|||
В России технология |
|
|||
обработки рельсов с при- |
Рис. 1. Общий вид рельсошлифовального поезда |
|||
менением схемы плоского |
шлифования торцом круга получила распространение в середине 1980-х гг., с появлением на Горьковской
железной дороге рельсошлифовального поезда URR-112 производства швейцарской фирмы «Speno». Однако становление профильного шлифования на отечественных железных дорогах как самостоятельной операции по восстановлению служебных свойств рельсов произошло только в 1994 г. в соответствии с приказом МПС № 12Ц и разработкой единой нормативно-технической документации на профильное шлифование рельсов, которая является основным регламентирующим документом до настоящего времени [1]. Его основой стала технология фирмы «Speno» и опыт эксплуатации рельсошлифовальных поездов, полученный на европейских железных дорогах. Учитывая несоответствие российских и европейских стандартов на рельсы, технология была адаптирована к местным условиям эксплуатации, но ожидаемого эффекта не последовало. Это объясняется отсутствием в нормативной документации каких-либо рекомендаций по назначению режимов шлифования для определенных условий об-
69

Технология транспортного машиностроения и ремонт подвижного состава
работки рельсов, что отражается на производительности, качестве обработки и на эффективности операции в целом.
Определяющим фактором эффективности технологии шлифования рельсов является производительность обработки при условии обеспечения требуемых эксплуатационных свойств рельсов с минимальными затратами, т.е. повышение эффективности рассматриваемой технологии может быть обеспечено за счет комплексного решения следующих задач [2]:
–увеличение производительности рельсошлифовальных поездов,
–обеспечение геометрической точности профиля головки рельса,
–обеспечение требуемых параметров качества поверхности,
–улучшение эксплуатационных характеристик абразивного инструмента,
–оптимизация технологических воздействий.
Решение вышеуказанных задач затруднялось отсутствием научнометодической базы, описывающей процесс шлифования рельсов.
Вопросу шлифования рельсов была посвящена единственная монография, изданная в Германии в 1992 г. под редакцией Хайнца Функе, в которой описаны общие вопросы профилирования рельсов с применением рельсошлифовальных поездов. Развитием теории шлифования рельсов занимались и в России, но все проводимые исследования были направлены в большей степени на организационно-технические мероприятия и устройство железнодорожного пути. С позиции технологии машиностроения этот процесс рассматривался в единичных случаях, а исследования, направленные на повышение эффективности процесса шлифования рельсов, практически не проводились.
Кроме того, принципиальные отличия схем шлифования рельсов в условиях железнодорожного пути и в стационарных условиях не позволяли использовать уже разработанные теоретические модели и полученные эмпирические зависимости для оценки процесса рельсошлифования. К этим принципиальным отличиям относятся [3]:
–силовое замыкание кинематической цепи «абразивный круг – обрабатываемая поверхность»;
–значительные различия условий резания каждого отдельно работающего шлифовального круга в зависимости от угла его наклона;
–изменения физико-механических свойств поверхности по периметру рельсов.
Специфика рельсошлифования потребовала разработки комплекса моделей, описывающих процесс шлифования рельсов на основе сочетания теоретических и экспериментальных исследований.
Начиная с 1996 г. коллектив кафедры «Технология транспортного машиностроения и эксплуатация машин» при поддержке службы пути ЗападноСибирской железной дороги приступил к исследованию процесса шлифования
70