
m0935
.pdf
В.А. Аксенов, А.С. Ильиных
рельсов по всем вышеуказанным направлениям с разработкой и внедрением полного комплекса технологической оснащенности данного процесса.
Формирование поперечного профиля рельсов
Перечень дефектов рельсов, удаляемых с применением технологии шлифования, достаточно обширен и включает в себя: волнообразные износы, механические повреждения, смятия и отслоения металла. При этом одной из главных целей шлифования является формирование поперечного профиля рельсов. Периодическая корректировка профиля шлифованием позволяет обеспечить наилучший контакт колеса с рельсом, равномерно распределить внутренние напряжения по поверхности рельса и тем самым продлить его эксплуатационный ресурс на 15…20 %.
Корректировка поперечного профиля рельсов осуществляется в соответствии с рядом ремонтных профилей, представленных в нормативнотехнической документации (выбирается наиболее подходящий профиль в зависимости от условий эксплуатации рельсов и их наработки). Как правило, при формировании выбранного ремонтного профиля происходит завышение съема металла от 15 до 30 %, что в дальнейшем значительно сокращает количество возможных технологических воздействий по шлифованию рельсов.
Более точный выбор ремонтного профиля может быть реализован на основе расчета его геометрических параметров с учетом фактической изношенности. Это позволит конкретизировать геометрию профиля под определенные условия эксплуатации пути и минимизировать съем металла с головки рельса.
Для решения этой задачи проведены исследования, устанавливающие взаимосвязь износа головки рельсов, геометрии их профиля, условий эксплуатации и наработки. Полученные результаты позволили определить степень и характер влияния различных факторов на изменение формы головки рельса и установить зависимость геометрических параметров поперечного профиля рельса от значений пропущенного тоннажа [4]:
R k T5 |
k T4 |
k T3 |
k T2 |
kT C, |
(1) |
|
i |
5 |
4 |
3 |
2 |
1 |
|
где k1, k2, k3, k4, k5 и С – коэффициенты полиномиального ряда, зависящие от условий эксплуатации; Т – значение пропущенного тоннажа, млн т брутто.
Полученное уравнение стало основой для формирования общей схемы ремонтного профиля, представленного на рис. 2, и создания математической модели расчета его геометрических характеристик [4].
Математическая модель расчета параметров ремонтного профиля представляет собой совокупность уравнений для расчета координат девяти точек, описывающих профиль головки рельса в системе координат XOY. В качестве примера в табл. 1 [4] приведены зависимости для расчета геометрических параметров координаты х6 точки 6 (см. рис. 2). Коэффициенты полиномиального
71
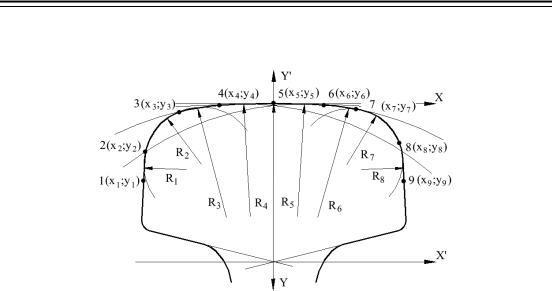
Технология транспортного машиностроения и ремонт подвижного состава
ряда, значения которых зависят от условий эксплуатации рельсов, представлены в табл. 2 [4].
|
Рис. 2. Обобщенная схема ремонтного профиля рельса типа Р65 |
|||
|
|
|
Таблица 1 |
|
|
Матрица расчета геометрических параметров ремонтного профиля |
|||
|
|
|
|
|
Коорди- |
Характеристика участка |
Уравнение или значение |
||
ната |
|
координаты |
|
|
|
|
|
||
|
Прямой участок пути |
x6 |
k2h2 k1h C |
|
|
Кривой участок пути: |
|
|
|
х6 |
Наружная рельсовая нить |
|
x6 k2h2 k1h C |
|
радиус более 650 м |
|
|
||
|
радиус менее 650 м |
x6 k4h4 |
k3h3 k2h2 k1h C |
|
|
|
|
|
|
|
Внутренняя рельсовая нить |
x6 k4h4 k3h3 k2h2 k1h C |
|
|
|
|
|
|
|
Примечание. h – разница высоты головки нового рельса Р65 и ремонтного профиля, мм.
|
|
|
|
|
|
|
Таблица 2 |
|
|
Расчет и значение коэффициентов полиномиального ряда |
|
|
|||||
|
|
|
|
|
|
|
|
|
Коор- |
Характеристика |
Значение или уравнения расчета коэффициентов |
||||||
дината |
участка |
k1 |
k2 |
k3 |
k4 |
k5 |
С |
|
|
Прямой участок |
12,65 |
–5,1667 |
– |
– |
– |
16,429 |
|
|
пути |
|
||||||
|
|
|
|
|
|
|
|
|
|
Кривой участок |
|
|
|
|
|
|
|
|
пути: |
|
|
|
|
|
|
|
|
Наружная |
|
|
|
|
|
|
|
х6 |
рельсовая нить |
|
|
|
|
|
|
|
радиус более |
–1,085hв + |
0,403hв – |
|
|
|
0,683hв + |
|
|
|
– |
– |
– |
|
||||
|
650 м |
+ 35,41 |
–12,04 |
+ 0,683 |
|
|||
|
радиус менее |
–0,041hв – |
–0,024hв + |
0,011hв – |
–0,001hв + |
– |
0,057hв – |
|
|
650 м |
– 24,454 |
+ 17,254 |
– 3,856 |
+ 0,273 |
– 30,67 |
|
|
|
|
|
||||||
|
Внутренняя |
–0,338hв + |
0,204hв – |
0,055hв + |
0,007hв |
–0,0003hв + |
0,154hв + |
|
|
рельсовая нить |
+ 29,492 |
– 16,584 |
+ 4,506 |
– 0,585 |
+ 0,029 |
+ 7,864 |
|
Примечание. hв – возвышение наружного рельса в кривой, мм.
72
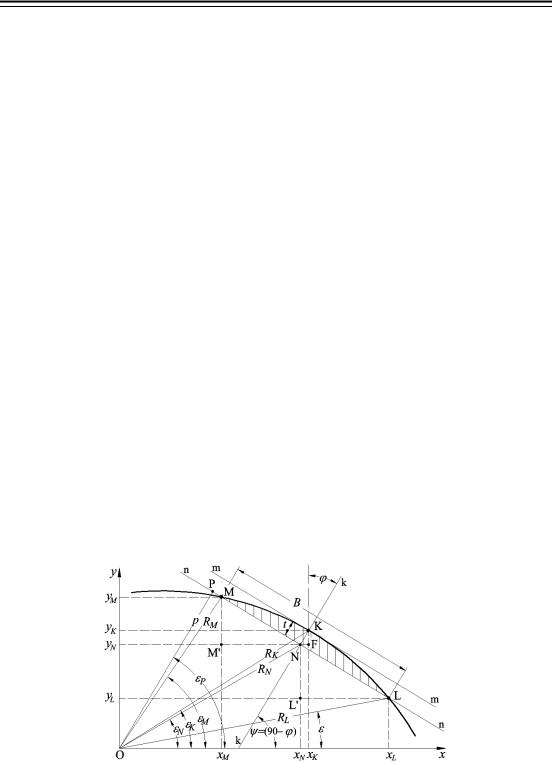
В.А. Аксенов, А.С. Ильиных
Воснову существующей технологии шлифования рельсов в России положена технология фирмы «Speno», при которой формирование поперечного профиля осуществляется несколькими шлифовальными кругами, работающими торцом круга. Существующие штатные настройки углов наклона этих кругов на рельсошлифовальном поезде не позволяют сформировать ремонтный профиль рельса, полученный по результатам расчета представленной модели.
Для обеспечения геометрической точности проектируемых ремонтных профилей разработана модель формообразования поперечного профиля рельса при его шлифовании торцами нескольких абразивных кругов [5].
Вкачестве исходных данных для реализации модели приняты геометрические параметры фактического поперечного профиля рельса, расчетная глубина резания и обрабатываемый участок головки рельса, определяемый углом наклона φ шлифовальной головки.
Определение фактического поперечного профиля головки рельса осуществляется при помощи рельсового профилометра, позволяющего производить измерения в полярной системе координат. При этом измеренный профиль рельса представляется массивом точек с координатами (Ri; εi), а геометрию профиля можно описать уравнением [5]
R f ( ), |
(2) |
где R – радиус-вектор измеряемой точки профиля, мм; ε – полярный угол в измеряемой точке, град.
Основной задачей создания рассматриваемой модели является определение ширины дорожки шлифования на обрабатываемом участке профиля рельса (рис. 3). Для этого необходимо знать, в какой именно точке головки рельса произойдет контакт со шлифовальным кругом, т.е. необходимо определить координаты точки K с учетом угла наклона φ шлифовальной головки.
Рис. 3. Схема к определению ширины дорожки шлифования
Торцевую поверхность шлифовального круга представим прямой m–m, касательной к профилю рельса в точке К. С учетом того что искомые коорди-
73
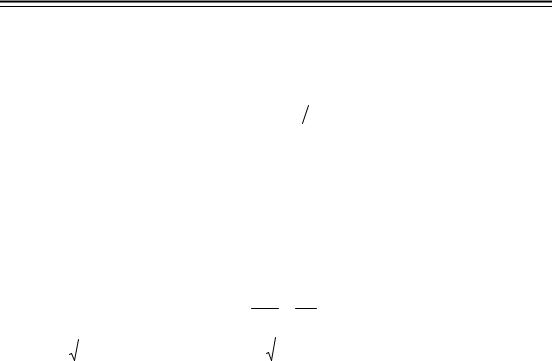
Технология транспортного машиностроения и ремонт подвижного состава
наты одновременно принадлежат касательной и профилю рельса, их значения определяются совместным решением нормального уравнения прямой m–m с уравнениями параметризации координат точки К, полученных в соответствии с выражением (2) [5]:
xK cos yK sin (xK |
cos K )cos( K ) 0, |
||
|
|
f ( K )cos K , |
(3) |
xK |
|||
|
|
f ( K )sin K . |
|
yK |
|
При работе шлифовальный круг врезается в поверхность рельса на заданную глубину резания t, которую можно определить по нормали к обрабатываемой поверхности, отложив из точки K отрезок KN, равный значению t.
Проведем через точку N прямую, параллельную касательной m–m. Секущая прямая n–n пересекает границы профиля в точках M и L. Расстояние между этими точками определяет ширину дорожки шлифования B:
|
|
|
|
|
B MN NL, |
(4) |
||||
|
|
|
|
|
|
|
|
|
|
. |
|
|
|
|
|
|
|
xL xN 2 yN |
yL 2 |
||
где |
|
|
xN xM 2 yM yN 2 |
|||||||
|
|
; |
|
NL |
||||||
MN |
Таким образом, задача определения ширины дорожки шлифования сводится к нахождению координат точек М и L, которые одновременно принадлежат секущей n–n и профилю рельса, т.е. значения координат точек M и L можно определить совместным решением нормального уравнения прямой n–n с уравнениями параметризации координат этих точек [5]:
для точки M
xM cos yM sin RN cos( N ) 0,
xM f ( M )cos M ,
|
f ( M )sin M ; |
yM |
|
для точки L |
(5) |
xL cos yL sin RN cos( N ) 0,xL f ( L )cos L,
yL f ( L )sin L.
Совокупность данных о ширине дорожки шлифования, зависящей от глубины резания на каждом отдельном участке профиля, дает возможность определения и назначения последовательности формирования ремонтного профиля рельса. Для построения модели формирования ремонтного профиля рельса рассмотрим его участок совместно с фактическим профилем, описываемым уравнением (2) (рис. 4).
74
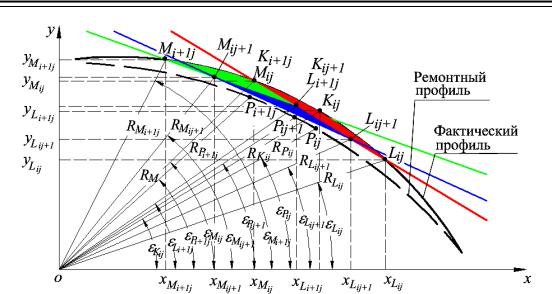
В.А. Аксенов, А.С. Ильиных
Рис. 4. Схема формообразования поперечного профиля рельса
Начальной точкой для формирования профиля примем точку фактического профиля рельса, координаты которой совпадают с координатами какой-либо точки ремонтного профиля. Предположим, что в соответствии с полученными координатами контакт первого шлифовального круга с поверхностью рельса произойдет в точке Kij. Для этой точки определяется требуемое значение угла наклона шлифовальной головки. С учетом полученного значения глубины резания tрасч для данной точки определяются координаты точек Mij и Lij и значения ширины дорожки шлифования. Для последующего абразивного круга точкой контакта с рельсом будет являться точка Mij. Сравнение координат ремонтного профиля с фактическим профилем осуществляется по периметру профиля i и по глубине j, которые в конечном итоге определяют необходимое количество проходов рельсошлифовального поезда.
Представленная модель формообразования поперечного профиля рельсов шлифованием несколькими инструментами, работающими по схеме плоского шлифования торцом круга, учитывающая технологическое наследование после обработки каждым абразивным кругом, позволяет повысить точность формообразования головки рельса, минимизировать количество проходов рельсошлифовального поезда и производить нормирование выполняемых операций.
Качество обработанной поверхности
Как уже было отмечено, шлифование рельсов осуществляется несколькими абразивными инструментами (на рельсошлифовальных поездах типа РШП-16 – 8 кругов на одну рельсовую нить, РШП-48 – 24 круга, РШП-112 – 56 кругов). С учетом того что условия работы шлифовальных кругов различны, проблема обеспечения требуемых параметров качества по всей поверхности головки рельса до настоящего времени остается нерешенной.
75

Технология транспортного машиностроения и ремонт подвижного состава
Исследованиями в этой области установлено, что первостепенную роль в зарождении и дальнейшем развитии усталостных трещин в головке рельсов играют параметры качества поверхности. При обработке шлифованием формируется качественно новый уровень физико-механических свойств поверхности, который в значительной степени влияет на усталостную прочность, износостойкость и общую долговечность рельсов. Основными параметрами качества поверхности, которые регламентируются нормативно-технической документацией по шлифованию рельсов, являются шероховатость и наличие прижогов на обработанной поверхности. В совокупности эти параметры определяют физическое состояние поверхности рельса после механической обработки.
Определение истинного влияния режимов шлифования рельсов на формирование шероховатости обработанной поверхности осуществлялось на основе экспериментальных данных. Зависимость шероховатости Rz от исследуемых факторов представлена линейным уравнением регрессии [6, 7]:
Rz 193t 34dз 0,15Sп 0,44vср 16, |
(6) |
где t – глубина резания, мм; dз – средний диаметр абразивного зерна шлифовального круга, мм; Sп – рабочая скорость рельсошлифовального поезда (продольная минутная подача), м/мин; vср – средняя скорость движения зерен, расположенных на разном расстоянии от оси вращения круга, м/с.
Формирование математических моделей и последующий анализ температурных полей применительно к процессу абразивной обработки базировались на анализе реальной физической картины взаимодействия поверхности обрабатываемого рельса с источниками теплообразования и фактических данных о свойствах материала, коэффициентах теплоотдачи и т.д. [8].
Выбор и обоснование метода расчета температурных полей в материале проводились исходя из положения, что источник теплоты является внешним, а
его распространение в твердом теле подчиняется уравнению Фурье [9]: |
|
|||||||||||||||||||||||||||||
|
dT |
|
d |
|
|
dT |
|
d |
|
|
dT |
|
d |
|
dT |
|
|
dT |
|
dT |
|
dT |
|
|||||||
с |
|
|
|
|
|
|
|
|
|
|
|
|
|
|
|
|
|
|
|
c V |
x |
|
V |
y |
|
V |
z |
|
. |
(7) |
|
|
|
|
|
|
|
|
|
|
|||||||||||||||||||||
|
d |
|
dx |
|
dx |
|
|
|
|
|
|
|
dz |
|
dz |
|
dx |
dy |
|
|
|
|||||||||
|
|
|
|
dy |
|
dy |
|
|
|
|
|
|
dz |
|
Шероховатость поверхности и температура в зоне резания формируют остаточные напряжения в обработанной поверхности, которые в значительной степени определяют ее эксплуатационные свойства.
Оценка остаточных напряжений основывается на модели, предложенной профессором А.Ю. Албагачиевым. Согласно предложенной модели суммарные остаточные напряжения определяются из выражения [10, 11]:
сум сил темп стр, |
(8) |
где σсил – силовые остаточные напряжения; σтемп – температурные остаточные напряжения; σстр – остаточные напряжения от структурно-фазовых превращений.
76
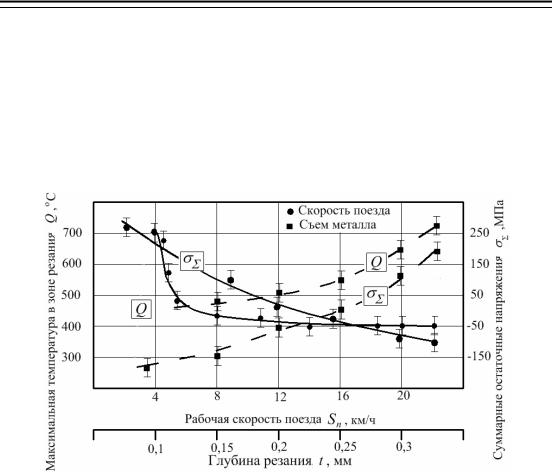
В.А. Аксенов, А.С. Ильиных
Рассмотрев на основе представленных моделей формирования параметров качества поверхности возможность увеличения производительности шлифования рельсов, можно сделать следующий вывод: наиболее благоприятным направлением повышения эффективности профильного шлифования рельсов является увеличение рабочей скорости поезда, так как это приводит к снижению теплового воздействия на рельс при обработке и уменьшению остаточных напряжений в поверхностном слое (рис. 5). С увеличением глубины резания наблюдается обратный эффект.
Рис. 5. Влияние режимов шлифования рельсов на температуру в зоне резания и остаточные напряжения в поверхностном слое
Представленные модели позволили выявить закономерность формирования шероховатости обработанной поверхности с учетом силового и температурного воздействия, а также ее взаимосвязь с параметрами технологического процесса, позволяющую реализовать управление качеством поверхности при шлифовании рельсов [5, 7, 10, 11].
Эксплуатационная стойкость рельсов
Эксплуатационные свойства рельсов характеризуются противодействием образованию и развитию трещин, контактно-усталостных дефектов и износу, возникновение которых в значительной степени определяется качеством поверхности после шлифования.
Определение эксплуатационных свойств поверхности катания рельсов после шлифования осуществлялось по критерию трещиностойкости, усталостной прочности и износостойкости. Исследования проводились на специально разработанных установках. Схемы и условия проведения исследований представлены в табл. 3 [12–14].
77
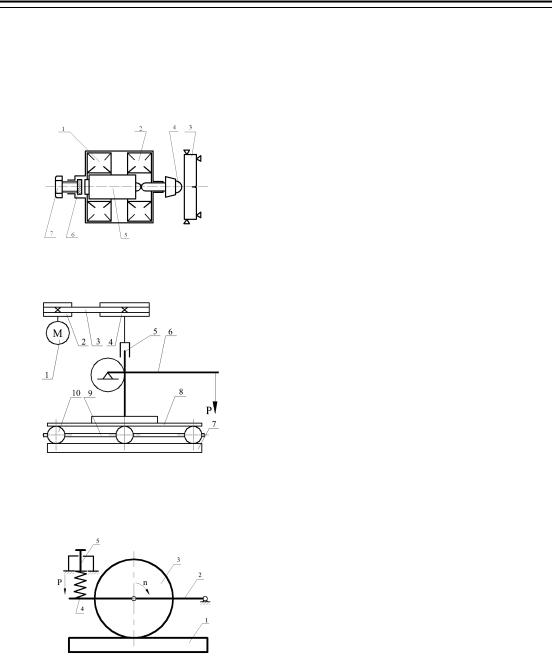
Технология транспортного машиностроения и ремонт подвижного состава
|
|
|
|
|
Таблица 3 |
|
|
Испытания по оценке эксплуатационных свойств обработанной поверхности |
|||
|
|
|
головки рельсов |
|
|
|
|
|
|
|
|
Вид |
|
Условия проведе- |
|
|
|
испы- |
Схема проведения испытаний |
Цель испытаний |
Критерии оценки |
||
таний |
|
ния испытаний |
|
|
|
|
|
|
|
||
|
|
|
|
|
|
|
|
|
Испытание образ- |
Оценка пределов |
Количество циклов |
|
|
|
цов из рельсовой |
циклической тре- |
до начала развития |
циклическая-Ударно |
трещиностойкость |
|
стали по принципу |
щиностойкости, |
трещины, скорость |
|
«пульсирующий |
определение кине- |
роста усталостной |
||
|
|
|
|||
|
|
|
контакт» со схемой |
тики зарождения и |
трещины, количест- |
|
|
|
нагружения «трех- |
распространения |
во циклов до полно- |
|
|
|
точечный изгиб» |
усталостных тре- |
го разрушения об- |
|
|
|
|
щин шлифованной |
разца |
|
|
1 – катушка прямого хода; 2 – ка- |
|
поверхности |
|
|
|
|
|
|
|
|
|
тушка обратного хода; 3 – образец, |
|
|
|
|
|
4 – индентор; 5 – боек; 6 – аморти- |
|
|
|
|
|
затор; 7 – подвижный упор |
|
|
|
|
|
|
Испытание образ- |
Определение преде- |
Количество питтин- |
|
|
|
цов из рельсовой |
лов контактной вы- |
гов, ширина и глу- |
|
|
|
стали методом об- |
носливости, оценка |
бина дорожки ката- |
|
|
|
катки шариками по |
кинетики развития |
ния в зависимости от |
усталостная-Контактно |
прочность |
|
схеме качения без |
питтингов на шли- |
количества циклов |
|
проскальзывания с |
фованной поверхно- |
нагружения. Весовая |
||
|
|
|
|||
|
|
|
созданием значи- |
сти |
и металлографиче- |
|
|
|
тельной контактной |
|
ская оценка |
|
|
|
нагрузки, с сохра- |
|
|
|
|
|
нением постоянно- |
|
|
|
|
|
го пятна контакта |
|
|
|
|
1 – электродвигатель; 2 – шкив |
|
|
|
|
|
ведущий; 3 – ремень; 4 – шкив |
|
|
|
|
|
ведомый; 5 – шпиндель; 6 – нагру- |
|
|
|
|
|
зочное устройство; 7 – образец; |
|
|
|
|
|
8 – обойма; 9 – сепаратор; |
|
|
|
|
|
10 – индентор |
|
|
|
|
|
|
Испытание образ- |
Определение сопро- |
Объемный износ |
|
|
|
цов из рельсовой |
тивления шлифо- |
образцов, их дефор- |
Износостойкость |
1 – образец; 2 – рычаг; |
стали в условиях |
ванной поверхности |
мация. Весовая и |
|
трения скольжения |
изнашиванию |
металлографическая |
|||
|
|
|
|
|
оценка |
|
|
3 – индентор; 4 – рычаг; |
|
|
|
|
|
5 – механизм прижатия индентора |
|
|
|
|
|
к образцу с усилием Р |
|
|
|
Анализ результатов испытаний на циклическую трещиностойкость показал, что увеличение микронеровностей после шлифования приводит к снижению циклической трещиностойкости. При этом грубое шлифование (Rz = 80 мкм) может снизить трещиностойкость рельсов на 70…80 %, что можно считать результатом влияния остаточных растягивающих напряжений, воз-
78
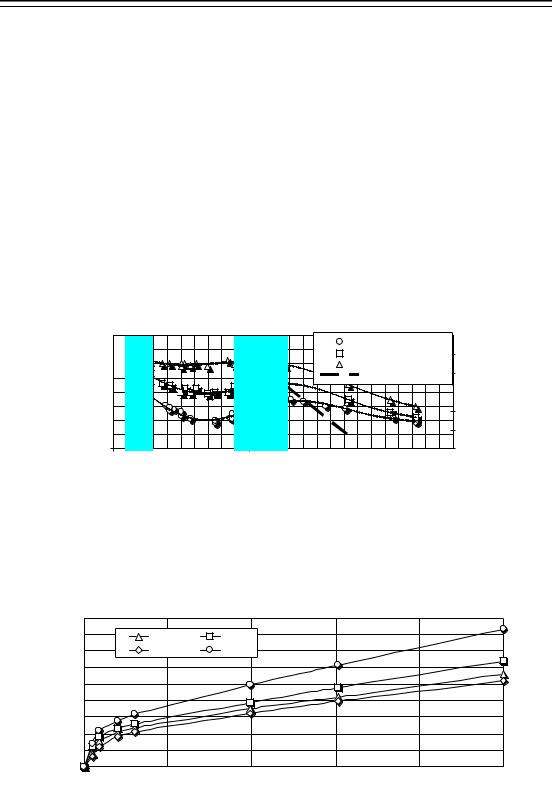
В.А. Аксенов, А.С. Ильиных
никающих в поверхности вследствие сильного местного нагрева и повышенной шероховатости [6].
Отмечено, что при определенных режимах шлифования наклеп, формирующийся в процессе механической обработки, в определенной степени нейтрализует действие концентраторов напряжений от полученных микронеровностей, тем самым увеличивая параметры трещиностойкости. Так, размах коэффициента интенсивности напряжений, соответствующий скорости роста усталостной трещины (10–7 м/цикл) для шероховатости Rz = 40 мкм, на 10 % выше значения, соответствующего шероховатости Rz = 20 мкм [6].
Сделанные выводы также подтверждаются результатами испытаний на контактно-усталостную прочность (рис. 6), которые показали, что большое влияние на стойкость к разрушению оказывает поверхностная твердость обрабатываемой поверхности. На графике отмечены две области, в которых значения шероховатости обеспечивают повышенную усталостную прочность обработанной поверхности рельсов [14].
|
5 |
Число циклов до |
разрушения N ∙10 |
3,1 2,9 2,7
2,5 |
2,3 |
2,1 |
1,9
1,7
1,5
0 |
20 |
40 |
|
НВ 340 |
|
520 |
|
|
|
|
|
|
|
НВ 400 |
|
470 |
НВ |
|
НВ 460 |
|
|
|
|
Линейный (НВ) |
420 |
Твердость |
|
|
|
|
370 |
|
|
|
|
|
|
|
|
|
320 |
|
|
|
|
270 |
|
|
|
|
220 |
|
60 |
80 |
100 |
|
Шероховатость поверхности Rz, мкм
Рис. 6. Влияние шероховатости на усталостную прочность рельсов
Весовая оценка испытаний на износостойкость (рис. 7) показала, что снижение шероховатости на 20 мкм позволяет увеличить износостойкость на 22…24 % за счет повышения сжимающих остаточных напряжений и увеличения микротвердости поверхностного слоя [13].
г |
4,5 |
|
|
|
|
|
G , |
4 |
Rz40 |
Rz60 |
|
|
|
, |
3,5 |
Rz20 |
Rz80 |
|
|
|
образцов |
|
|
|
|||
3 |
|
|
|
|
|
|
2,5 |
|
|
|
|
|
|
износ |
2 |
|
|
|
|
|
1,5 |
|
|
|
|
|
|
Весовой |
|
|
|
|
|
|
1 |
|
|
|
|
|
|
0,5 |
|
|
|
|
|
|
0 |
|
|
|
|
|
|
|
|
|
|
|
|
|
|
0 |
10 |
20 |
30 |
40 |
50 |
|
|
|
Количество циклов нагружения N ∙105 |
|
|
Рис. 7. Влияние шероховатости на износостойкость поверхности рельсов
79
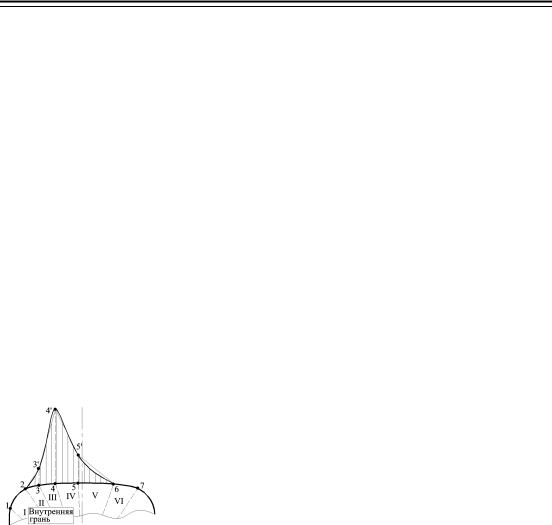
Технология транспортного машиностроения и ремонт подвижного состава
Проведенные исследования по оценке эксплуатационных свойств отшлифованной поверхности рельсов показали, что для обеспечения повышенной эксплуатационной стойкости рельсов необходимо формировать шероховатость поверхности при шлифовании с учетом их исходной твердости и условий эксплуатации. На основе работ М.Х. Ахметзянова, М.А. Фришмана, Е.П. Бондаренко и других ученых, в которых определяются напряженные состояния головки рельса в процессе работы с учетом вида нагружения в зависимости от кривизны участка пути и его расположения, определены значения шероховатости поверхности, обеспечивающие повышенные эксплуатационные свойства рельсов. В качестве примера в табл. 4 представлены значения требуемой шероховатости участков головки рельса, лежащего на внутренней нити кривого участка пути радиусом более 500 м [5].
Таблица 4
Требуемая шероховатость участков головки рельса, лежащего на внутренней нити кривого участка пути радиусом более 500 м
|
Участки профи- |
|
Рекомендуемая |
||||
Условная схема нагрузки |
ля и их границы |
Характерный вид |
шероховатость на участке |
||||
по углам накло- |
профиля Rz, мкм, |
||||||
разрушения |
|||||||
на рельс |
на шлифоваль- |
на участке профиля |
при твердости участка НВ |
||||
|
ных головок φ, |
|
|
|
|
||
|
|
340–400 |
400–460 |
> 460 |
|||
|
|
град |
|
||||
|
I |
–60…–15 |
– |
35…40 |
35…40 |
35…40 |
|
|
II |
–15…–10 |
Износ |
16…20 |
16…20 |
16…20 |
|
|
III |
–10…–5 |
Образование попе- |
64…68 |
54…58 |
44…48 |
|
|
IV |
–5…–1,5 |
речных трещин |
64…68 |
54…58 |
44…48 |
|
|
V |
–1,5…8 |
Контактно- |
54…58 |
48…54 |
40…44 |
|
|
усталостное |
||||||
|
|
|
|
|
|
||
|
VI |
8…20 |
– |
35…40 |
35…40 |
35…40 |
|
|
|
|
|
|
|
|
Таким образом, установлены закономерности изменения эксплуатационных свойств отшлифованных участков головки рельса по критериям циклической трещиностойкости, контактно-усталостной прочности и износостойкости. Это позволило предложить и обосновать методы обеспечения повышенных эксплуатационных свойств рельсов за счет формирования требуемой шероховатости на отдельных участках головки рельса, воспринимающих различные виды нагружения в процессе эксплуатации.
Производительность рельсошлифовальных поездов
Применение технологии шлифования рельсов в условиях железнодорожного пути усложняется необходимостью закрытия целых перегонов для движения поездов (организация технологических окон). Это приводит к значительным убыткам, связанным с ограничением пропускной способности участков пути, задержкой движения и снижением скорости перевозок. Уменьшение этих издержек может быть обеспечено за счет повышения производительности рельсошлифовальных поездов, позволяющей сократить продолжительность окон.
80