
m0935
.pdf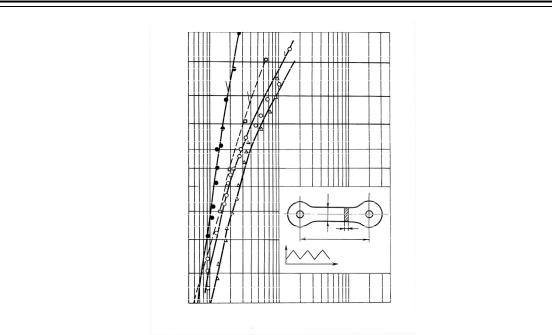
Н.М. Чернов, К.А. Медведев
Вероятность разрушения, %
95
1
90
4 3 2
80
70
60
50
40
30 |
|
20 |
|
|
|
|
|
20 |
|
132 |
5 |
|
|
||
|
max=500 МПа |
||
|
|
||
10 |
|
|
N |
|
|
|
|
5 |
|
|
|
105 |
106 |
|
107 |
|
Долговечность N, цикл. |
Рис. 6. Функции распределения долговечности при циклическом нагружении отдельно отлитых образцов из стали ВНЛ-3:
1 – ЛВМ; 2 – ЛВМКД; 3 – литье по выплавляемым моделям с высокотемпературной газостатической обработкой (ЛВМ ВГО); 4 – горячая штамповка – сталь ВНС-5
Таким образом, воздействие давления на кристаллизацию отливок из черных сплавов приводит к повышению прочности, пластичности, ударной вязкости и усталостной долговечности при циклических нагрузках без применения дорогостоящих модифицирующих добавок.
Предварительный анализ дефектов и износа быстроизнашиваемых деталей показал, что технологию литья по выплавляемым моделям с кристаллизацией под давлением с высоким экономическим эффектом можно применять для литья деталей путевых машин – подшипники скольжения из медных сплавов взамен заготовок из проката, композиционных подбоек (сталь – твердый сплав ВК8) путевых машин ВПР, композиционные литые ковши (сталь – стеллит) кюветонарезной машины вместо сварного с наплавкой твердым сплавом, деталей баровой цепи из стали 110Г13Л для щебнеочистительных машин, шаровой опоры и корпуса тележки электровоза, мотор-вагонных тормозных колодок из серого чугуна с высоким содержанием фосфора.
Библиографический список
1.Медведев К.А., Чернов Н.М. Литье по выплавляемым моделям с кристаллизацией под давлением коррозионно-стойких сталей // Литейное производство. 2006. № 1. С. 20–23.
2.Савинов Ю.П., Чернов Н.М., Медведев К.А. Технология изготовления композиционного режущего инструмента // Технология металлов. 2005. № 10. С. 23–27.
3.Пат. 53196 Российская Федерация, МПК В22Д 18/02. Устройство для литья с кристаллизацией под давлением / В.А. Аксенов, Н.М. Чернов, К.А. Медведев. № 2005137490/22; заявл. 01.12.05; опубл. 10.05.06, Бюл. № 13. 5 с.
121

Диагностика и неразрушающие методы контроля
НАПРАВЛЕНИЕ «ДИАГНОСТИКА И НЕРАЗРУШАЮЩИЕ МЕТОДЫ КОНТРОЛЯ»
УДК 620.179
В.В. Муравьев
Акустическая структуроскопия технических объектов железнодорожного транспорта
Становление научного направления в СГУПСе
Исследования и разработки новых приборов и методов в области акустической структуроскопии автор начал в 1976 г. на кафедре физики Новосибирского института инженеров железнодорожного транспорта. В это время науч- но-исследовательская группа (НИГ) физики в составе преп. Л.Я. Левитана, инженеров А.А. Лебедева и А.Н. Федорченко под руководством доцента А.В. Шарко занималась разработкой резонансного акустического метода для контроля твердости конструкционных углеродистых сталей.
Имея хорошую базовую подготовку в области физики металлов, методов их контроля и накопив опыт реальной работы по методам анализа структуры материалов в ОКБ при Новосибирском электровакуумном заводе, автор приступил к исследованиям влияния структурного состояния алюминиевых сплавов на скорость распространения ультразвуковых волн и установления закономерностей в их поведении при разных видах воздействия на материал.
При поддержке завкафедрой «Физика» К.Л. Комарова формируется научное направление «Диагностика и неразрушающие методы контроля», целью которого становятся фундаментальные исследования, разработка приборов и методов диагностирования объектов железнодорожного транспорта, металлургии, машиностроения и теплоэнергетики, в частности, методологии оценки микроструктуры, механических свойств, напряженно-деформированного состояния металлических объектов повышенной опасности неразрушающими методами, оценка их состояния и остаточного ресурса. Устанавливаются научные связи с НовосибНИАТ (ведущий научный сотрудник А.С. Бедарев), СибНИА (начальник сектора В.Н. Чаплыгин, старший научный сотрудник Г.В. Серегин), НЭТИ (завкафедрой Л.И. Тушинский).
Выполнен цикл работ по исследованию структур сплавов и их связи с акустическими и механическими свойствами, в том числе с циклической долговечностью. По результатам исследований дислокационной структуры при статических и циклических испытаниях алюминиевых сплавов, конструкционных сталей и сплавов получены первые авторские свидетельства на способы определения предела ограниченной выносливости материалов и опубликована
122

В.В. Муравьев
серия статей в журналах «Физика металлов и металловедение», «Металловедение и термическая обработка металлов», «Дефектоскопия» [1–5].
В 1984 г. на базе НИГ организована ОНИЛ «Физические методы контроля качества и надежности металла деталей и узлов подвижного состава» ЦВ МПС. Научным руководителем назначен завкафедрой К.Л. Комаров. В ОНИЛ разрабатываются приборы для контроля структурного и напряженного состояния, твердости и механических свойств металла узлов и деталей тележек, колесных пар вагонов, рельсов, трубопроводов.
Организаторские способности К.Л. Комарова проявились при обеспечении конструкторской доработки и производства разработанного в ОНИЛ структуроскопа ИСП-12. Серия таких структуроскопов была изготовлена на базе ОКБм при НПО «Союз» в количестве более ста штук. Приборы, прошедшие сертификацию в Дальстандарте, внедрили в вагонные депо, дистанции пути для контроля сварных стыков рельсов, на предприятия теплоэнергетики для контроля трубопроводов ТЭЦ. Разработан новый структуроскоп ИСП-24, с возможностью неразрушающего контроля механических характеристик сталей и сплавов.
Найдены новые физические закономерности в поведении скорости ультразвука при накоплении усталостной поврежденности циклически нагруженного металла и высокоэнергетических воздействиях на металл, что дало возможность заявить о новом подходе к оценке состояния металлов и сплавов и позиционировать его как метод для обнаружения начальной подготовительной стадии образования микротрещин. В проведении исследований неоценимую помощь оказал В.Н. Чаплыгин. Разработанный метод контроля оказался чувствительным к структурным преобразованиям при изготовлении и эксплуатации транспортных и теплоэнергетических металлов, колесных пар, колец подшипников, рельсов, изделий из алюминиевых сплавов и др. Это нашло отражение в опубликованных статьях и монографии [6–7].
Усиливаются научные связи с ИФПМ СО РАН, создается академическая лаборатория акустики. Открывается аспирантура по материаловедению на транспорте и методам контроля и диагностики в машиностроении, появляются аспиранты: А.Г. Васильев, З.И. Ермолаева, Р.Р. Рамазанов, Е.В. Бояркин, А.Н. Курбатов, Е.М. Сухарев, А.Л. Бобров, М.В. Муравьев, С.А. Бехер, К.В. Власов, докторанты: Г.В. Серегин, А.Н. Смирнов, С.Б. Теодорович. В вузе открывается диссертационный совет по названным специальностям, успешно работавший до 2008 г. (председатель К.Л. Комаров, зам. председателя В.В. Муравьев, ученый секретарь С.И. Герасимов).
В 90-х гг. в России организуется система сертификации персонала по неразрушающему контролю, в СГУПСе создается уполномоченный орган по сертификации персонала в области неразрушающего контроля объектов ж.-д. транспорта «Транссиб», он аккредитуется Госстандартом и МПС и является
123

Диагностика и неразрушающие методы контроля
третьим подобным органом в России. При кафедре электротехники, диагностики и сертификации организован научный сертификационно-диагностический центр (НСДЦ), включающий ОНИЛ «Физические методы контроля качества металлов и сплавов», НИЛ метрологии и стандартизации, центр «Транссиб». НСДЦ обеспечивает для железных дорог разработку, изготовление и планомерные поставки акустических диагностических комплексов, их ремонт и поверку; обучение, повышение квалификации и сертификацию специалистов по неразрушающему контролю объектов железнодорожного транспорта в вагонном, локомотивном и путевом хозяйствах; экспертизу разрушений деталей и конструкций на железнодорожном транспорте. НСДЦ работает в тесной связи с предприятиями железнодорожного транспорта, отраслевыми и академическими НИИ, заводами Сибирского региона. Результаты исследований и разработок изложены в монографиях и статьях [7–12].
Активная позиция главного технолога ЦВ МПС В.Б. Харитонова по переоснащению парка дефектоскопов и введению системы сертификации персонала на ремонтных предприятиях ЦВ позволила в период 1985–2000 гг. разработать на новых физических принципах структуроскопы и существенно уменьшить число разрушившихся в эксплуатации узлов и деталей грузовых вагонов.
Ст. науч. сотрудник НСДЦ И.И. Козятник разработал структуроскоп УДС–СИН для контроля натяга внутренних колец подшипников и тензометрическую станцию со съемными тензодатчиками. Доц. Б.В. Глухов разработал стенд для тарировки этого прибора, документацию к которому подготовил преп. А.Н. Курбатов и обеспечил его сертификацию и ввод в реестр средств, допускаемых к применению на ж.-д. транспорте. После этого ст. науч. сотрудник И.И. Козятник организовал производство приборов и планомерные поставки в вагонные депо.
Диагностирование литых деталей методом акустической эмиссии
К концу 90-х гг. на сети железных дорог России сложилось критическое положение с литыми элементами тележек грузовых вагонов, вызванное острой нехваткой новых деталей из-за снижения их выпуска вследствие резкого падения производства на металлургических заводах. Нехватка боковых рам и надрессорных балок тележек модели 18-100 с нормативным сроком службы 30 лет вынуждает МПС принять решение о продлении срока службы по результатам индивидуальных испытаний каждой детали с истекшим сроком эксплуатации.
При обсуждении в ЦВ для обнаружения усталостных трещин было предложено использовать метод акустической эмиссии (АЭ), который в то время был неплохо проработан. Начать работу планировалось на двух приборах АФ-15 разработки ВНИИНК, которые имелись в ОНИЛ. Было сформировано техническое задание. Сложность заключалась в том, что практически не было реализации АЭ на литых изделиях. Так как затухание акустических волн в ли-
124

В.В. Муравьев
том металле велико, требовалась многоканальная быстродействующая система. Вначале к экспериментам и разработке аппаратуры пытались привлечь из СибНИА группу, занимавшуюся ранее обеспечением прочностных экспериментов, но ознакомившись с проблемой члены этой группы отказались от участия в проекте.
По рекомендации В.Н. Чаплыгина к разработке АЭ системы в 1994 г. была привлечена ст. науч. сотрудник Л.Н. Степанова из СибНИА, имевшая опыт создания многоканальных тензометрических систем. Правильность выбора подтвердили дальнейшие исследования АЭ метода, проведенные в СГУПСе совместно с СибНИА в период 1994–2006 гг., позволившие разработать методику и автоматизированные АЭ стенды для диагностирования боковых рам и надрессорных балок, а также при поддержке В.А. Гапановича (в то время зам. начальника ЗСЖД) других объектов железнодорожного транспорта, таких как: котел цистерны для перевозки нефтебензиновых продуктов и сжиженного газа, тяговый хомут автосцепного устройства, карданный вал и крестовина электровоза ЧС-2, серповидная подвеска электропоезда, колесная пара вагона и локомотива, кольца подшипников всех типоразмеров, звеньевые рельсы на мостах и сварные стыки на рельсосварочных предприятиях, элементы металлических железнодорожных мостов.
Л.Н. Степанова, организовав группу инженеров электронщиков и программистов (С.И. Кабанов, Е.Ю. Лебедев, В.Л. Кожемякин, А.Е. Ельцов, М.В. Геращенко, А.Е. Кареев и др.), сумела обеспечить не только разработку многоканальных быстродействующих АЭ систем, но и организацию прочностных экспериментов. Исследования и разработки описаны в двух монографиях и многочисленных статьях [13–16]. Получены патенты на способы и устройства с использованием метода АЭ [17–20].
Метод АЭ характерен тем, что требует создания в диагностируемом изделии напряженно-деформированного состояния, соответственно необходима разработка нагружающих стендов. Участвовали в расчетах НДС деталей доц. С.П. Васильев, Б.В. Глухов, профессора В.П. Кутовой, С.И. Герасимов, Н.В. Мокин, сотрудники СибНИА В.Я. Ковалев, В.В. Ивлиев, В.А. Беспалов. Профессор Н.В. Мокин разработал первые нагружающие стенды. Корректная работа руководителей организаций К.Л. Комарова, В.М. Круглова, А.Н. Серьезнова, В.П. Тырина по взаимодействию коллективов и финансовому обеспечению позволила выполнить в срок НИОКР, изготовление и поставки диагностических стендов в ремонтные депо железных дорог России.
По приказу зам. министра МПС по локомотивному и вагонному хозяйствам В.Н. Пустового назначены сравнительные испытания разработанных АЭ стендов, в которых приняли участие специалисты ООО «Интерюнис» с системой A-Line и сотрудники ВНИИЖТа. Испытания стендов и феррозондовых и вихретоковых дефектоскопов относительно магнитопорошкового метода в ва-
125
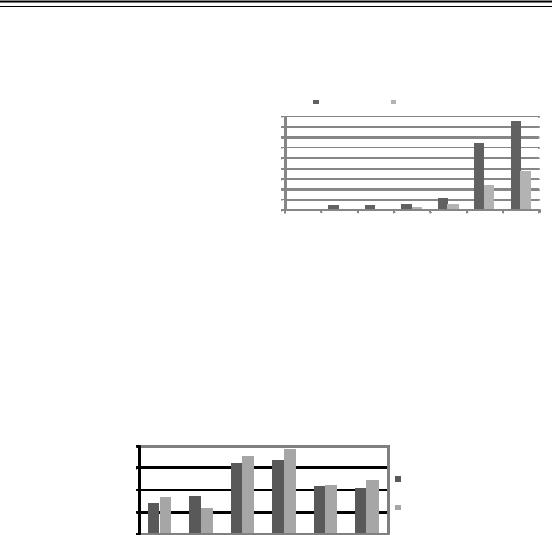
Диагностика и неразрушающие методы контроля
гонном ремонтном депо Нижнеудинск (2001 г.) показали их значительно более высокую вероятность обнаружения дефектов (85 % – СЦАД-16 и 74 % – A-Line) по сравнению с феррозондовым (42 %) и особенно вихретоковым (35 %) методами.
С начала внедрения в 1998 |
|
|
Боковаярама |
|
Надрессорная балка |
|
|
|||
|
|
|
|
|
|
|
|
|
|
|
г. АЭ метода усилиями СГУПСа |
4000 |
|
|
|
|
|
|
|
|
|
в вагонных депо Кемерово и Ин- |
3000 |
|
|
|
|
|
|
|
|
|
ская (ЗСЖД), Тосно (ОктЖД) |
2000 |
|
|
|
|
|
|
|
|
|
растет число испытанных дета- |
1000 |
|
|
|
|
|
|
|
|
|
лей до 2004 г. (рис. 1). К 2005 г. |
0 |
|
|
|
|
|
|
|
|
|
|
1998 |
г. |
г. |
|
г. 20 1 г. |
г. |
г. |
2004 |
г. |
|
завершено оснащение 104 голов- |
|
1999 |
2000 |
2001 |
2002 |
2003 |
|
|||
|
|
|
|
|
|
|
|
|
|
|
ных вагонных ремонтных депо |
Рис. 1. Рост числа испытанных деталей стендами |
АЭ стендами СЦАД и A-Line. Руководил поставками оборудо-
вания доц. В.Н. Шкляр, обеспечивали пусконаладочные работы Е.В. Бояркин, А.Л. Бобров, М.В. Муравьев, С.А. Бехер, К.В. Власов, А.Н. Курбатов, сотрудники СибНИА). Вместе с освоением стендов увеличивается их производительность, которая для систем СЦАД и систем A-Line за 2005–2010 гг. представлена на рис. 2.
Производительность
1200 |
|
|
900 |
A-Line |
|
600 |
||
|
||
300 |
СЦАД |
|
|
0 2005г. 2006г. 2007г. 2008г. 202009г. 2010г.
Рис. 2. Производительность систем АЭ контроля A-Line и СЦАД по годам
До 2008 г. наблюдается ежегодный рост числа диагностированных боковых рам и надрессорных балок при продлении срока службы по всем ремонтным депо ОАО «РЖД» (рис. 3, а, в). Анализ результатов эксплуатации АЭ стендов в этот период дает устойчивую тенденцию к снижению числа бракуемых деталей (рис. 3, б, г).
С 2009 г. ОАО «РЖД» принимает решение снизить объемы АЭ контроля по продлению срока службы боковых рам и применять АЭ контроль только для инвентарных надрессорных балок и после сходов тележек (см. рис. 3, а, в). В этот же период наблюдается рост числа забракованных боковых рам (см. рис. 3, б), что связано с вводом в отдельных ремонтных депо АЭ контроля при проведении ТО-3 для разработанных новых боковых рам коробчатого сечения после двухлетнего пробега, у которых из-за неотработанной техноло-
126
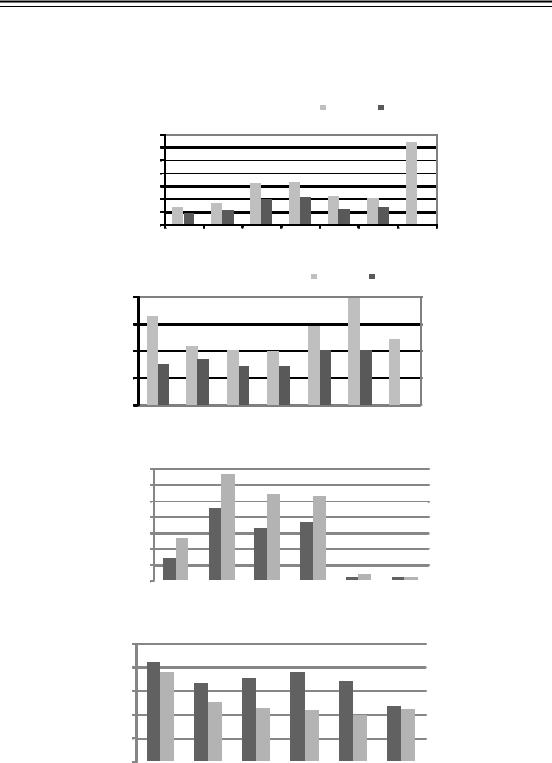
В.В. Муравьев
гии низкое качество литья. По результатам АЭ диагностики к 2013 г. продлен срок службы более чем 800 000 боковым рамам и более чем 200 000 надрессорным балкам с 30 лет до 38 лет полезного использования (рис. 4).
а)
Всего проверено, |
A-Line СЦАД |
боковых рам |
СЦАД и |
|
A-Line |
120000
80000
40000
0
2005 2006 2007 2008 2009 2010 2011
2005г. 2006г. 2007г. 2008г. 2009г. 2010г. 2011г.
б)
% брака боковых рам |
A-Line СЦАД |
|
16 |
СЦАД и |
|
12 |
||
A-Line |
||
8 |
|
4
0 202005г. 2006г. 2007г. 2008г. 2009г. 2010г. 2011г.
в)
Всего проверено,надрессорныхбалок
СЦАД
A-Line
30000
20000
10000
0 2005 г. 2006г. 2007г. 2008г. 2009 г. 2010 г.
г)
%брака надрессорныхбалок
25
СЦАД
A-Line
20
15
10
5
0 2005г. 2006г. 2007г. 20088 г. 2009г. 2010г.
Рис. 3. Результаты АЭ контроля боковых рам и надрессорных балок по продлению срока службы (а, в) и выявление бракованных деталей по годам (б, г) с использованием систем СЦАД и A-Line
127
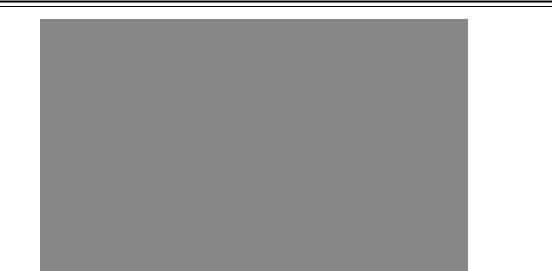
Диагностика и неразрушающие методы контроля
Рис. 4. Продление срока службы литых деталей вагонов (по данным ЦДРВ ОАО «РЖД»)
За год на каждой установке АЭ контроля в разных депо испытывается от 600 до 2000 боковых рам. Особо следует отметить, что ни одна из деталей с продленным сроком службы после АЭ контроля не отказала в процессе эксплуатации. По данным ЦДРВ ОАО «РЖД», внедрение работ по продлению срока службы литых деталей тележек грузовых вагонов позволило сэкономить ОАО «РЖД» к 2010 г. более 12 млрд р.
Диагностирование ответственных деталей железнодорожного транспорта методом акустической эмиссии
Диагностирование котлов цистерн. В период 1994–1999 гг. проводились исследования возможности АЭ контроля котлов железнодорожных цистерн. Исследовали варианты нагружения котла избыточным давлением изнутри воздухом и водой (участвовали сотрудники СибНИА, Е.В. Бояркин, А.Л. Бобров, С.А. Бехер, К.В. Власов). Устанавливали на поверхность котла 16 преобразователей акустической эмиссии (ПАЭ), из которых 8 настраивали для выявления сквозных дефектов с учетом коэффициента затухания и 8 ПАЭ для обнаружения дискретной АЭ от развивающихся трещин. Технологию отрабатывали в СибНИА. Гидроиспытания нефтеналивных и газовых цистерн совместно с АЭ методом проводили на Алтайвагонзаводе. Использование метода АЭ в процессе гидроиспытаний позволило выявлять наряду со сквозными дефектами зарождающиеся и значительные несквозные дефекты. Выявляли трещины в зоне сливного отверстия, вблизи опор на лежнях, сварных швах нижнего пояса, дефекты некачественной сварки в виде врезки и усиления днища.
Тормозные цилиндры локомотивов, эксплуатируемые при давлениях свыше 10 атм., являются ответственными элементами системы безопасности движения. Разработанный метод АЭ контроля позволил надежно выявлять сквозные и несквозные дефекты, растущие изнутри трещины, внутреннюю
128

В.В. Муравьев
коррозию (участвовали Е.В. Бояркин, А.Л. Бобров, С.А. Бехер, К.В. Власов, сотрудники СибНИА).
Карданный вал тягового двигателя электровоза ЧС-2 подвержен дей-
ствию значительных вращающих моментов, которые вызывают большие касательные силы в местах их приложения; вал воспринимает, кроме того, вес деталей якоря. Часто меняющаяся нагрузка с мгновенными толчками в период пуска и торможения, ударная нагрузка при выходе движущей колесной пары из состояний боксования, динамические воздействия от неровностей пути, значительные перегрузки в период выхода из строя одного из тяговых двигателей создают особенно тяжелые условия для работы валов.
Задачей АЭ диагностирования было обеспечить повышение надежности контроля карданного вала ЧС-2 и оценить срок службы детали. Решение поставленной задачи осуществлялось с использованием системы СЦАД 16.02 и специально разработанного нагружающего устройства с обеспечением крутящего момента (участвовали сотрудники СибНИА, Е.В. Бояркин, А.Л. Бобров, С.А. Бехер, К.В. Власов).
Выступы крестовины привода карданного вала передают крутящий момент от двигателя и редуктора к ведомым шестерням и работают на срез. Появляющиеся в крестовине в местах высоких напряжений растущие трещины обнаруживаются АЭ методом.
Серповидные подвески электропоездов, являющиеся одними из основ-
ных конструктивных элементов электропоездов, поддерживают электродвигатель, препятствуют его выпадению на пути во время движения. Разработанные в локомотивном депо нагружающие устройства с ручным механическим и электрическим приводом, создающими сжимающую нагрузку до 9 тс, позволили на основе АЭ методики выявлять трещины в подвесках (участвовали сотрудники СибНИА, Е.В. Бояркин, А.Л. Бобров, С.А. Бехер, К.В. Власов).
Диагностирование колец подшипников. На этапе отработки методики АЭ контроля колец подшипников использовали разрывную машину и АЭ систему СЦАД 16.02 (участвовали С.А. Бехер, М.В. Муравьев, Е.В. Бояркин, А.Л. Бобров, К.В. Власов). Разработанная в результате экспериментов методика и специализированное нагружающее устройство позволили надежно выявлять АЭ методом начальные микро- и макротрещины в кольцах подшипников любых типорамеров в цеховых условиях вагонных и локомотивных депо.
Диагностирование пролетных балок металлических железнодорожных мостов. Метод АЭ совместно с тензометрией с 2001 г. используется для поиска трещин продольных несущих балок железнодорожного моста через р. Обь в Новосибирске (участвовали С.А. Бехер, М.В. Муравьев, Е.В. Бояркин, А.Л. Бобров, К.В. Власов). Регистрация сигналов и деформаций пролетных балок осуществлялась шестнадцатью ПАЭ и четырьмя тензопреобразователями в процессе прохождения пассажирских поездов. Установлена возможность регист-
129

Диагностика и неразрушающие методы контроля
рации различных типов источников акустической эмиссии: усталостные трещины различной протяженности, ориентации и раскрытия, непровары, поры, трещины в сварных швах и зоне термического влияния. Выявляются новые трещины, находящиеся на ранней стадии роста. Разработаны технические требования для непрерывного мониторинга технического состояния ответственных элементов мостовых конструкций. К.В. Власов, используя дисперсионные кривые, показал, что в обшивке котлов и продольных балках формируются волны Лэмба, переносящие информативные сигналы АЭ.
Диагностирование рельсов на мостах в эксплуатации. Проведены необходимые исследования при разработке методики АЭ диагностирования звеньевых рельсов, уложенных на мосту, под нагрузкой проходящего поезда. Исследования возможностей АЭ диагностирования рельсов проводились на рельсах, установленных на железнодорожном мосту в Новосибирске через р. Обь (участвовали М.В. Муравьев, С.А. Бехер, Е.В. Бояркин, А.Л. Бобров, К.В. Власов). Диагностирование осуществлялось с помощью АЭ системы СЦАД 16.03 с использованием 16 ПАЭ. При исследованиях использовались информативные параметры и линейная методика определения местоположения источников сигналов АЭ по вычислению разности времен прихода на ПАЭ, расположенных в ряд.
Предварительные эксперименты, проведенные с использованием имитатора сигналов АЭ, показали, что наиболее оптимальным положением ПАЭ как с точки зрения максимальной амплитуды сигнала в зоне растяжения, так и технологичности, а также защиты преобразователя акустической эмиссии от возможных повреждений со стороны проходящего поезда является подошва рельса. Одной из основных проблем при АЭ диагностировании являлся выбор информативных браковочных критериев. При испытаниях за основу были взяты стандартные критерии по плотности сигналов и их амплитуде, были дополнительно исследованы энергетические критерии оценки степени дефектности рельсов.
Общее количество зарегистрированных сигналов намного превышает количество локализованных сигналов, т.е. подтвержденных всеми ПАЭ. Это объясняется тем, что невозможно полностью избавиться от акустического шума, принимаемого ПАЭ во время прохода поезда по рельсу. В этот период локализовать «полезный» сигнал АЭ не представлялось возможным. Поэтому все локализованные сигналы от источников АЭ были выявлены до захода поезда на диагностируемый рельс.
Данной работой обоснована достаточность уровня напряженно-деформи- рованного состояния для АЭ контроля, создаваемого весом проходящего поезда. Изучен характер акустических и электромагнитных шумов и найдены способы борьбы с ними. Впоследствии были показаны особенности возникновения деформаций в пролетных строениях моста при прохождении поезда [21].
130