
Экологически безопасные способы получения целлюлозы
..pdfлоза с числом Каппа 10–21 ед. легко отбеливается до белизны
86–88 %.
Для сульфатных и сульфитных целлюлоз характерно некоторое снижение или, в лучшем случае, неизменность механических характеристик в результате отбелки. У КЩ-целлюлоз при отбелке заметно возрастают все прочностные показатели. При этом прочность беленых КЩ-целлюлоз становится очень близкой к прочности беленых сульфатных целлюлоз.
Улучшение механических свойств КЩ-целлюлоз при отбелке происходит вследствие растворения части коротких волокон, снижения необычайно высокого содержания низкомолекулярных гемицеллюлоз и упорядочения микрофибриллярной структуры в клеточной стенке волокон.
Механические и бумагообразующие свойства целлюлоз.
По механическим свойствам небеленая КЩ-целлюлоза несколько уступает сульфатной целлюлозе, особенно из хвойных пород. Главным образом это относится к сопротивлению раздиранию (по данным финской фирмы «Kemi Oy», для лиственной КЩцеллюлозы оно ниже, чем для сульфатной, на 15–30 %, для хвойной – на 20–40 %) и в меньшей степени – к сопротивлению излому. Однако предварительная щелочная варка щепы до выхода примерно 65 % от массы абсолютно сухой древесины с последующей КЩ-варкой ее в пульсационном аппарате позволяет получить даже небеленую целлюлозу, очень близкую по прочности к сульфатной, а в случае березовой КЩ-целлюлозы даже существенно превзойти ее.
Показатели механической прочности целлюлозы в значительной степени формируются в процессе размола. Высокое содержание гемицеллюлоз в волокнах КЩ-целлюлозы способствует более легкому их набуханию до и в процессе размола в сравнении с соответствующей сульфатной целлюлозой. В результате уменьшается продолжительность размола до одинаковой степени помола и удельный расход электроэнергии на размол. Лучшая размалываемость способствует повышенному об-
61
разованию новой поверхности и появлению большого объема пор. При этом разрушение при размоле клеточных стенок набухших волокон КЩ-целлюлозы происходит настолько интенсивно, что первоначальная структура пор при увлажнении полотна после сушкиужене восстанавливается в должной степени.
В результате размола волокно КЩ-целлюлозы при сушке дает значительную усадку, лист получается более плотный,
сбольшой площадью межволоконных контактов, что требует большого усилия при разрыве. Однако большая площадь межволоконных контактов препятствует скольжению волокон в листе относительно друг друга. Вследствие этого уменьшается сопротивление раздиранию.
Более низкую прочность КЩ-целлюлозы также связывают
сменьшей упорядоченностью молекул клетчатки в фибриллах волокон, а также с большим разрушением водородных связей между фибриллами при удалении из клеточной стенки гемицеллюлоз и лигнина в процессе КЩ-варки.
Каталитическая КЩ-варка. Катализ – новое направле-
ние при совершенствовании и промышленной реализации КЩварки древесины. Для КЩ-делигнификации в разное время был предложен ряд катализаторов. Наиболее эффективными катализаторами КЩ-варки являются 1,10-фенантролин и 1,10-фенан- тролинат меди.
Вкачестве катализатора делигнификации при КЩ-варке 1,10-фенантролин был предложен еще в 1979 г. (исследователи С.А. Онохин, Э.И. Гермер, Ю.Г. Бутко). Этот катализатор ускоряет делигнификацию в условиях данного процесса в 1,5–3,0 раза при добавках его в количестве 0,1–0,5 % от массы абсолютно сухой древесины, при этом сохраняются или даже незначительно повышаются выход, вязкость и механические свойства получаемой целлюлозы.
Дальнейшие исследования показали, что каталитическое
действие 1,10-фенантролина |
обусловлено |
его координацией |
с небольшими количествами |
меди, всегда |
присутствующими |
в древесине (2–5 мг/кг). Сам 1,10-фенантролинат меди (II), бу-
62

дучи непосредственно добавлен в варочную систему в количестве 0,1–0,8 % от массы абсолютно сухой древесины, обеспечивает ускорение делигнификации в условиях КЩ-варки в пределах от 5–8 до 25–28 раз. Нижний предел указанного интервала относится к варке при высокой температуре (150–160 °С) и ограниченном массообмене, верхний предел – при относительно низкой температуре (90–100 °С) и интенсивном массообмене.
Каталитическое ускорение делигнификации в 25–28 раз превышает в 5–10 раз ускорение любого из используемых сегодня способов делигнификации под действием самых активных катализаторов. Это принципиально новый результат, открывающий широкие перспективы совершенствования процессов делигнификации посредством катализа и, в частности, позволяющий реализовать в промышленных условиях КЩварку древесины.
На основе использования 1,10-фенантролината меди предложен новый КЩНП-процесс с исключительно низкими, по сравнению с обычной КЩ-варкой древесины, значениями параметров (табл. 5).
|
|
Таблица 5 |
Основные характеристки КЩ- и КЩНП-варки |
||
|
|
|
Параметр |
КЩ-варка |
КЩНП-варка |
Гидромодуль |
15–30 |
7–9 |
Концентрация массы, % |
3–6 |
10–13 |
Давление, МПа |
2–3 |
0,9–1,0 |
Расход*, кг/т воздушно- |
|
|
сухой целлюлозы: |
|
|
Na2CO3 (в ед. NaOH) |
220–340 |
150–200 |
кислород |
150–160 |
90–100 |
* Нижняя граница интервала – для лиственной, верхняя – для хвойной древесины.
По табл. 5 видно, что значения параметров КЩНП-про- цесса находятся на уровне значений аналогичных параметров
63
при КЩ-отбелке. Это позволяет предположить, что при использовании для КЩНП-процесса в качестве сырья не щепы, а предварительно разволокненных полуфабрикатов высокого выхода появляется возможность для промышленного производства КЩ-целлюлозы использовать оборудование, подобное тому, которое применяется для КЩ-отбелки, или иное оборудование, но более простой конструкции по сравнению с пульсационным котлом.
КЩНП-процесс рекомендуется вести до числа Каппа около 100 ед. и выше. Это связано с деструктирующим действием меди (II) и других металлов переходной валентности на полисахариды при КЩ-варке.
Ориентировочный расчет себестоимости КЩНП-целлю- лозы, выполненный с учетом затрат на получение волокнистой массы из щепы, но без учета стоимости катализатора, показал хорошую экономическую эффективность этого способа по сравнению с сульфатной варкой щепы – экономия составила 28–42 долл./т воздушно-сухой целлюлозы. Согласно расчетам ВНИИБ, удельный предотвращенный экономический ущерб от загрязнения окружающей среды при переходе от сульфатного способа варки к кислородно-щелочному составляет около 70 долл./т воздушно-сухой целлюлозы. Таким образом, суммарная удельная экономия (100–110 долл.) должна позволить решить многие проблемы, связанные со стоимостью относительно дорогих катализаторов и с их регенерацией. Согласно ориентировочным расчетам, затраты на оборудование, здания, строительно-монтажные работы при КЩНП-процессе должны быть ниже, чем при сульфатном.
Схемы производства КЩ-целлюлозы. Варианты кисло-
родно-щелочных варок имеют много общих черт и по технологической схеме производства сводятся к двум: кислороднощелочной варке с полной утилизацией отработанного щелока (метод окислительного аммонолиза и др.) и кислороднощелочной варке с регенерацией щелочного реагента (кислород- но-содовая варка).
64
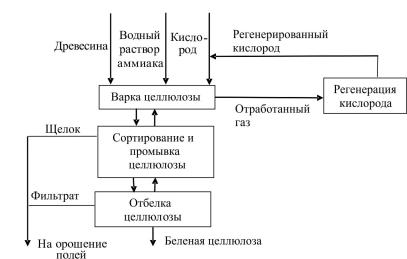
Метод окислительного аммонолиза, или кислороднощелочная варка в водном растворе аммиака (рис. 12), позволяет наряду с целлюлозой (выход 55–60 % из древесины лиственных пород, 52–55 % из хвойной древесины) получать второй товарный продукт – азотсодержащий отработанный щелок. Этот продукт можно использовать в качестве удобрения в виде смеси упаренного до 30 % щелока с древесной корой или без упаривания в жидком виде.
Рис. 12. Принципиальная технологическая схема получения целлюлозы путем кислородно-щелочной варки с полной утилизацией отработанного щелока
Отработанный щелок, полученный после варки методом окислительного аммонолиза, содержащий около 0,5 % азота, в течение ряда лет применялся в качестве азотного удобрения Биологическим институтом ЛГУ им. А.А. Жданова на дерновоподзолистых почвах с различными сельскохозяйственными культурами: ячменем, райграссом, овсом, кукурузой, овсяницей тростниковидной. Установлено, что внесение щелока в рекомендуемых дозах вызывает увеличение урожайности и повыше-
65
ние содержания белка в растениеводческой продукции. Агрономическая эффективность отработанного щелока при использовании в эквивалентных дозах аналогична стандартным азотным удобрениям – сульфату аммония и аммиачной селитре.
При отбелке данного вида целлюлозы кислородом и перекисью водорода в присутствии поташа (K2СО3) или гидроксида калия можно и фильтраты отбелки применять вместе с отработанным щелоком окислительного аммонолиза.
Таким образом, при окислительном аммонолизе появляется реальная возможность создания безотходного производства целлюлозы с получением из древесины полезных продуктов, пользующихся неограниченным спросом. Кроме того, применение этого способа позволяет избежать загрязнения атмосферы, поскольку все газообразные продукты реакции проходят двухступенчатую очистку с целью регенерации кислорода. Регенерированный кислород вновь направляется на варку, а органические примеси (следы аммиака и оксид углерода) окисляются до углекислого газа, азота и воды. После абсорбирования диоксида углерода раствором поташа можно получать товарный продукт – твердую углекислоту в количестве 150–250 кг на 1 т воз- душно-сухой целлюлозы.
Биологически окисляемая часть щелока, полученного традиционными методами, представляет собой углеводы и продукты их превращения, в то время как при окислительном аммонолизе происходит глубокая окислительная деструкция лигнина с образованием алифатических кислот, легко утилизируемых биологическими методами. Отработанный щелок окислительного аммонолиза содержит на 1 т целлюлозы меньше трудноокисляемых веществ (в 3–4 раза) и фенолов (в 5–10 раз) по сравнению с сульфатным и сульфитным щелоками.
Метод окислительного аммонолиза наряду со значительным снижением токсичности стоков, полным отсутствием газовых выбросов, рациональным использованием растительного сырья позволяет существенно снизить капиталоемкость производст-
66
ва за счет исключения цехов регенерации химикатов: выпарного, содорегенерационного, каустизации и регенерации извести.
Азот отработанного щелока после окислительного аммонолиза также является полноценной заменой азота, добавляемого в виде питательных солей для биологической очистки стоков. Это дает возможность сократить расход питательных азотсодержащих солей на очистных сооружениях. В этом случае обеспечивается биологическая очистка стоков без сброса избыточного азота в водоемы.
Газы, удаляемые из варочного котла и содержащие избыток О2, а также СО, СО2 и летучие органические соединения, направляются в систему регенерации кислорода, где последние вместе с СО каталитически окисляются до СО2 и воды. Далее углекислый газ отделяется от кислорода абсорбцией. Кислород возвращается на варку, а углекислый газ выделяется в десорбере, затем сжижается и направляется на использование, например для получения твердой углекислоты.
В процессе кислородно-содовой варки с регенерацией щелочного реагента (рис. 13) регенерация основания из щелока после КЩ-варки может быть осуществлена по упрощенной схеме регенерации сульфатных щелоков с получением содового плава, но без последующей его каустизации при использовании для варки карбоната или бикарбоната натрия. При этом отсутствует необходимость в регенерации извести. Полученный варочный раствор содержит в основном углекислый натрий. Вследствие этого потери щелочи в производстве целесообразно возмещать кальцинированной содой.
Концентрирование щелока можно проводить либо путем его упаривания, либо с помощью мембранных методов. Щелок кислородно-щелочной варки имеет в расчете на 1 кг сухого вещества более низкую теплотворную способность (на 20–30 %), чем сульфатный щелок, однако при его сжигании отпадает необходимость проведения реакции восстановления сульфата до сульфида. Вместо СРК можно применять более простую по кон-
67
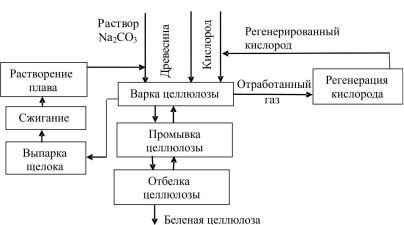
струкции и эксплуатации печь циклонного типа. Процесс сжигания ведут с использованием дополнительного топлива в окислительной среде. Возможно и «мокрое сжигание» щелока.
Рис. 13. Принципиальная технологическая схема получения целлюлозы путем кислородно-содовой варки с регенерацией щелочного реагента
В отработанном щелоке после кислородно-содовой варки содержится большое количество карбоновых кислот, которые до регенерации могут быть биохимически переработаны с получением до 70 кг белковых кормовых дрожжей на 1 т целлюлозы.
При получении целлюлозы кислородно-щелочными методами трудно создать энергетически замкнутую систему. Однако в самом варочном аппарате за счет экзотермических окислительных реакций выделяется значительное количество тепла – 1,1–1,5 Гкал/т целлюлозы. Это тепло можно использовать для поддержания необходимой температуры в варочном аппарате, что снизит расход тепловой энергии на варку до 0,2–0,3 Гкал/т целлюлозы.
68
2.3.2. Азотнокислый способ
Получение целлюлозы азотнокислым способом известно с XIX века. Когда появились кислотоупорные стали, стойкие
крастворам азотной кислоты различной концентрации, внимание
кэтим варкам значительно возросло. Некоторые из многочисленных вариантов данного способа варки реализованы в промышленности (например, варка буковой древесины в 1940-х годах в Германии на заводе «Вольфен»; небольшие заводы для получе-
ния целлюлозы для химической переработки есть в Японии и США). Исследованиями по разработке различных вариантов азотнокислой варки, по изучению особенностей делигнификации древесины, поведения лигнина и полисахаридов под действием азотнокислых растворов занимались во Франции, США, СССР.
Азотнокислую варку нельзя однозначно отнести к окислительным способам делигнификации, так как в зависимости от концентрации используемой кислоты и температуры в этом процессе более или менее значительную роль играют реакции нитрования лигнина. Известные варианты азотнокислой варки подразделяются в зависимости от концентрации используемой азотной кислоты на три группы: варки с концентрированной кислотой (40–50 %), кислотой средней (12–15 %) и низкой (3–8 %) концентрации. Чем более разбавленная кислота используется в процессе, тем выше роль окислительных реакций.
Нитрирующим агентом является не собственно HNO3, а катион нитроний (NO2+), образующийся при варке. Реакции нитрования ведут к фрагментации лигнина или раскрытию его ароматических ядер.
На окислительный характер превращения лигнина при азотнокислой делигнификации указывает увеличение содержания в лигнине карбоксильных групп и деметоксилирование его; на реакции нитрования – появление в его составе азота; на реакции фрагментации – разрушение связей между фенилпропановыми единицами лигнина с образованием растворимых даже
69
в водной среде низкомолекулярных фрагментов, а также увеличение содержания фенольных гидроксилов.
Хвойная древесина варится значительно труднее. Многие однолетние растения варятся легче лиственных пород.
Более низкую скорость делигнификации хвойной древесины связывают с отсутствием в ней широких сосудов, которые имеются у лиственных пород или однолетних растений. Возможной причиной является также различная реакционная способность гваяцил-, сирингил- и α-оксиарилпропановых структур в реакциях нитрования.
Азотная кислота является сильной кислотой. Поэтому ее воздействие на углеводную часть древесины в условиях варки носит главным образом гидролитический характер, приводя к существенному гидролизу гемицеллюлоз. В щелоках кроме сахаров и образовавшихся из них оксикарбоновых кислот содержатся также фурфурол и его производные, образующиеся в результате дегидратации сахаров, продукты превращения этих соединений в кислой среде.
Азотная кислота очень плохо впитывается в древесину. Поэтому при этом способе варки желательно применять стружку, тонкую щепу (до 2 мм), измельченные отходы лесопиления или однолетние растения. При использовании обычной щепы необходимо интенсифицировать процесс пропитки путем пропарки, вакуумизации и т. д.
Азотнокислая варка не может быть одноступенчатой: при относительно низкой температуре (меньше 100 °С), характерной для обработки сырья азотной кислотой, значительная часть лигнина даже после фрагментации остается в древесном остатке. Для его удаления применяют обработку слабыми растворами щелочей после тщательной многоступенчатой отмывки азотной кислоты.
Серьезным недостатком этого способа варки является выделение газообразных токсичных оксидов азота, а иногда и цианистого водорода. Улавливание этих соединений с превращением их в азотную и азотистую кислоты, используемые в процессе,
70