
Экологически безопасные способы получения целлюлозы
..pdf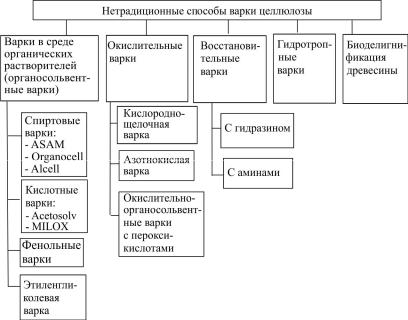
2. НЕТРАДИЦИОННЫЕ СПОСОБЫ ПРОИЗВОДСТВА ЦЕЛЛЮЛОЗЫ
2.1. КЛАССИФИКАЦИЯ НЕТРАДИЦИОННЫХ СПОСОБОВ ПРОИЗВОДСТВА ЦЕЛЛЮЛОЗЫ
Поиск наиболее эффективной экологической альтернативы традиционным способам получения целлюлозы привел к разработке большого числа различных способов варки. Классификация основных нетрадиционных экологически безопасных способов может быть представлена в виде схемы (рис. 6).
Рис. 6. Нетрадиционные способы варки целлюлозы
31
На схеме представлены нетрадиционные способы варки целлюлозы, имеющие практический интерес. Многие из них достигли стадии промышленной или полупромышленной реализации или стадии пилотных испытаний.
2.2. ОРГАНОСОЛЬВЕНТНЫЕ ВАРКИ ЦЕЛЛЮЛОЗЫ
2.2.1. Общие сведения о растворителях
Варки с органическими растворителями – органосольвентные варки (от англ. organic solvent – органический растворитель) – могут осуществляться без дополнительных химических реагентов со сравнительно простой схемой регенерации растворителя. Выделяемый органосольвентный лигнин отличается высокой реакционной способностью и может быть утилизирован в качестве углеродсодержащего сырья, фенолсодержащего сырья, связующего, сорбента и т.п. Эти особенности, а также возможность утилизации растительной биомассы разделением ее на отдельные компоненты для их последующей переработки (например, целлюлоза для производства бумаги или химической переработки, лигнин для получения продуктов, используемых в качестве жидкого топлива или для выделения индивидуальных соединений, и гемицеллюлозы в виде легко перерабатываемого раствора углеводов) привлекают внимание к органосольвентным технологиям.
Растворители, используемые для делигнификации растительного сырья, относятся к различным классам органических соединений (одноатомные и многоатомные спирты, фенолы, карбоновые кислоты, простые и сложные эфиры, кетоны, амины, сульфоксиды и др.) и существенно различаются по своим свойствам и характеру взаимодействия с компонентами древесины.
При выборе органического растворителя для варки следует учитывать не только технологичность процесса и свойства получаемой целлюлозы, но и наличие многотоннажного произ-
32
водства растворителя; возможность его получения из отходов древесины или побочных продуктов варки; наличие простой схемы регенерации растворителя; затраты на восполнение потерь растворителя при варке и промывке целлюлозы и в ходе его регенерации.
Растворитель не должен увеличивать коррозийную активность варочного раствора и чрезмерно повышать пожаро- и взрывоопасность производства. С экологической точки зрения растворитель должен подвергаться биологической деструкции и не быть токсичным. С учетом этих факторов к растворителям, наиболее пригодным для варки целлюлозы, относятся этанол, метанол, ацетон, уксусная и муравьиная кислоты, бутанол и этилцеллозольв (моноэтиловый эфир этиленгликоля). Фактически же наиболее проработаны варки с этанолом, метанолом, уксусной кислотой, муравьиной кислотой, фенолом и крезолами (метилфенолами). Следует отметить, что муравьиная кислота имеет высокую коррозионную активность, а регенерация ее затруднена.
Если рассматривать делигнификацию древесины органическими растворителями как физический процесс растворения лигнина в органическом растворителе, то одним из критериев активности органического растворителя по отношению к лигнину является мера полярности растворителя, которая характеризуется величиной диэлектрической проницаемости. Увеличение полярности органического растворителя способствует лучшей растворимости древесного лигнина при делигнификации древесины.
В сравнении с другими органическими растворителями, характеристики которых приведены в табл. 4, большой практический интерес для использования в качестве делигнифицирующего реагента представляет многоатомный спирт – этиленгликоль, имеющий высокую температуру кипения, высокую диэлектрическую проницаемость при незначительной молекулярной массе.
33
Процесс растворения лигнина в органическом растворителе можно рассматривать как результат диффузии молекулы растворителя в полимер, разрыва межмолекулярных водородных связей с образованием сольватного слоя между макромолекулами и набухания полимера в органическом растворителе. Когда набухание становится неограниченным, макромолекулы лигнина переходят в раствор. С увеличением молекулярной массы растворителя растворимость полимера ухудшается. В этом случае добиться более полного перехода лигнина в органический растворитель можно повышением температуры.
|
|
|
Таблица 4 |
|
Характеристики органических растворителей |
||||
|
|
|
|
|
Растворитель |
Диэлектрическая |
Температура |
Молекулярная |
|
проницаемость |
кипения, °С |
масса |
||
|
||||
Метиловый спирт |
32,6 |
64,5 |
32,04 |
|
Этиловый спирт |
24,3 |
78,3 |
46,1 |
|
Муравьиная кислота |
56,1 |
100,7 |
46,02 |
|
Уксусная кислота |
6,2 |
117,7 |
60,0 |
|
Этиленгликоль |
37,7 |
197,8 |
62,1 |
|
Фенол |
9,8 |
181,7 |
94,1 |
|
Крезолы |
– |
190–203 |
– |
|
Ацетон |
20,8 |
56,2 |
56,3 |
|
Диоксан |
2,2 |
101,3 |
88,1 |
Высокая температура кипения растворителя и малый мольный объем повышают его растворяющую способность по отношению к лигнину.
Растворимость лигнина зависит также от способности органического растворителя к образованию с лигнином водородных связей и характеризуется параметром Гильдебрандта (δ). Хорошие растворители лигнина должны иметь величину параметра Гильдебрандта порядка 40–46 кДж/моль, к числу таких растворителей относится диоксан (δ = 41,9 кДж/моль).
34
Делигнификация древесины органическими растворителями обусловлена не только возможностью перехода природного лигнина в органический растворитель, но и доступностью лигнина в растительной клетке.
Изменение доступности лигнина происходит при делигнификации в результате деструкции его макромолекул, разрыва связей с компонентами древесины и образования новых связей, в частности, в результате химического взаимодействия лигнина с органическим растворителем.
2.2.2. Водно-спиртовые варки
Метиловый и этиловый спирты относятся к многотоннажным растворителям, хорошо освоенным промышленностью.
Делигнификация водно-спиртовыми смесями имеет свои особенности. Варки проходят при неконтролируемом изменении значения рН варочной среды. Так, варка в 50%-ном этаноле начинается при рН ~ 6,5, а заканчивается при рН = 2,8…3,8. Высокие температуры приводят к быстрому повышению концентрации отщепляемых кислот в областях клеточной стенки, богатых гемицеллюлозами (P–S1 и S3). Основной реакцией деструкции лигнина является гидролитическое расщепление α-эфирной связи. Высокие температуры (около 195 °С) и низкие значения рН вызывают конденсацию лигнина. Основная фаза делигнификации начинается после удаления определенного количества гемицеллюлоз, сопровождающегося образованием в клеточной стенке макропор. Большая часть лигнина в варочном растворе находится в коллоидном состоянии и при охлаждении быстро агрегируется и осаждается на волокнах. Отложения лигнина на волокнах не удаляются промывкой водой или водноспиртовыми смесями, в этом случае требуются более сильные растворители (ацетон, 3–5%-ный NaOH и т. п.). Продолжительная делигнификация при высокой температуре и низком значении рН сопровождается деструкцией целлюлозы: получа-
35
ется темная масса с низкой вязкостью и большим количеством отходов сортирования (до 40 %). Все это делает водно-спиртовые варки малопригодными для производства целлюлозы, в особенности из древесины хвойных пород. Однако делигнификация значительно улучшается при интенсификации массообменных процессов ирегулировании рН среды, что делает возможным проведение ва- рочныхпроцессовсиспользованиемводно-спиртовыхсмесей.
Примером водно-спиртовых варок является процесс Alcell. В 1989 г. на территории сульфат-целлюлозного завода в г. Ньюкасле (Нью-Брансуик, Канада) начал работать демонстрационный завод, производящий 15 т целлюлозы в день из древесины североамериканских лиственных пород (обычно использовалась смесь, %: клена 50 ; березы 35 и тополя 15 ). Варки производились
всеми варочных котлах (экстракторах) периодического действия
в50%-ном (по массе) водном этаноле при 195 °С (рис. 7). Давление паров при этом было около 2,8 МПа, но с помощью азота
вкотлах поддерживали несколько большее давление.
Варку проводили в три ступени (1-я ступень – варка, 2-я
и3-я ступени – экстрагирование). В варочный котел загружали около 10 т предварительно пропаренной щепы и паром вытесняли из котла воздух. Затем в котел к жидкой фазе после удаления лигнина добавляли щелочь для связывания органических кислот
инаправляли ее на перегонку. В дистилляционной колонне отбиралась спиртовая фракция и фракция с летучими маслами и фурфуролом. Кубовый остаток с углеводами и солями органических кислот (в основном уксусной) упаривали. Полученный концентрат предлагался для использования в качестве кормов для скота или топлива либодляпроизводства этанолаифурфурола.
Небеленая целлюлоза имеет оптимальные механические характеристики при сравнительно высоких числах Каппа (20–30 ед.). Однако она хорошо делигнифицируется кислородом с уменьшением числа Каппа на 70 %. Вязкость при этом практически не меняется. Для сульфатной целлюлозы такой уровень кислородной делигнификации снизил бы вязкость в два раза. После добелки по
36
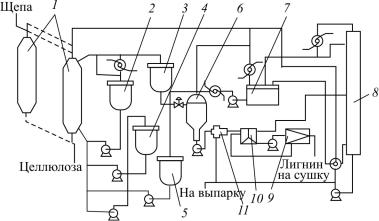
Рис. 7. Блок-схема процессаAlcell: 1 – варочный котел (экстрактор); 2, 3, 4, 5, 7 – сборники растворов 2, 1 и3-йступеней, свежегораствора и регенерированного растворителя соответственно; 6 – испаритель; 8 – дистилляционная колонна; 9 – центрифуга;
10 – осадитель; 11 – смеситель
схеме Д–Щ–Д белизна целлюлозы составляет 90 %. Возможна отбелка такой целлюлозы ибез хлорсодержащих соединений.
При сравнении свойства полученной целлюлозы оказались сопоставимы со свойствами сульфатной лиственной целлюлозы, полученной в промышленных условиях, и даже превосходили их. Так, для органосольвентного и сульфатного образцов целлюлозы разрывная длина оставляла 7,47 и 7,40 км, сопротивление раздиранию – 7,20 и 6,75 мНм2/г и продавливанию – 5,08 и 5,18 кПам2/г соответственно. Производимую на демонстрационном заводе органосольвентную целлюлозу использовали для производства бумагиспокрытием.
На основании положительного опыта работы демонстрационного завода была запланирована организация завода беленой органосольвентной целлюлозы с суточной производительностью около 300 т. В 1997 г. на одном из сульфит-целлюлоз- ных заводов в Атолвилле (Нью-Брансуик, Канада) должно было
37
начаться производство органосольвентной целлюлозы по методу Alcell, активного лигнина и фурфурола. Однако по ряду причин проект не был завершен. Права на процесс были в 1997 г. приобретены одной канадской фирмой с целью распространения этой технологии в регионах с ограниченной лесосырьевой базой, так как она позволяет перерабатывать с хорошими результатами древесину лиственных пород, в том числе быстро растущих (эвкалипт и т. п.), и недревесное сырье.
Дальнейшее развитие водно-спиртовых варок связывают сприменением различных катализаторов. Наиболее интересные результаты получены при использовании солей Са и Mg. Так, всерии варок с 80%-ным метанолом, содержащим катализатор, при 190–220 °С за 15–55 мин получают целлюлозу с очень высоким выходом. После отбелки высокий выход сохранялся (54–57 % для хвойных и 57–62 % для лиственных пород), при мягком размоле беленой целлюлозы достигались механические характеристики, сопоставимые с характеристиками сульфатной целлюлозы или дажепревосходящиеих.
2.2.3. Щелочные водно-спиртовые варки
При щелочных водно-спиртовых варках кроме регенерации растворителя требуется и регенерация щелочи. Однако возможность эффективной делигнификации древесины хвойных пород и получения целлюлозы высокого качества вызывают интерес к этим варкам.
В Германии был разработан водно-метанольный щелочной варочный процесс Organocell. В 1988 г. на территории бумажной фабрики в Мюнхене стала работать полупромышленная установка производительностью 5 т беленой целлюлозы в день. На этой установке щепа подавалась в пропиточную камеру, откуда после обработки паром или варочным раствором поступала в камеру предгидролиза, где 30 мин при температуре 150 °С обрабатывалась 50%-ным водным метанолом, после
38
чего подавалась на двухступенчатую варку в варочный котел непрерывного действия. На 1-й ступени варка проводилась 20–50 мин при 190 °С в 50%-ном метаноле (давление до 3,0 МПа) при рН = 4…5. На 2-й ступени водно-метанольная смесь разбавлялась до 30%-ной концентрации метанола раствором NaOH (18–22 % NaOH от массы абсолютно сухой древесины) и варилась 40 мин при 170 °С. Затем масса поступала в зону диффузионной промывки, где противотоком при 115 °С в течение 3–6 ч промывалась холодным варочным раствором. Из котла целлюлоза поступала на сортирование и отбелку по схеме КЩО–Д–П.
Использование антрахинона (0,1 % от массы абсолютно сухой древесины) позволило проводить варку в одну ступень в 25–30%-ном водном метаноле с NaOH (17–22 % от массы абсолютно сухой древесины) при температуре 155–170 °С за 60–120 мин без проведения предгидролиза.
Система регенерации растворителя состояла из восьми последовательно соединенных выпарных аппаратов, куда подавались щелока 1-й и 2-й ступеней. На выходе получали 65%-ный метанол, а кубовый остаток из последнего аппарата (примерно 25%-ный метанол) перегоняли в дистилляционной колонне с получением 95%-ного метанола. Отходы направляли на городской завод по переработке отходов из-за нецелесообразности строительства печи для регенерации щелочи.
Установка работала круглосуточно десятидневными циклами в течение нескольких лет. Полученная целлюлоза имела лучшие механические свойства, чем у сульфитной целлюлозы, но несколько уступала сульфатной и использовалась в производстве бумаги с покрытием.
Успешный опыт эксплуатации установки позволил перейти к промышленной реализации процесса Organocell на суль- фит-целлюлозном заводе в Кельхайме. В 1992 г. был построен завод для ежегодного производства из древесины ели 150 тыс. т беленой целлюлозы, по качеству сопоставимой с сульфатной
39
целлюлозой и даже ее превосходящей. Целлюлоза предназначалась для изготовления высококачественной бумаги для печати, бумаги с покрытием, а также для бумаги санитарно-гигиени- ческого назначения. Варочный котел с башней предварительной пропитки был первым большим аппаратом такого типа, созданным в Германии (высота с питателем 60 м, общий объем 660 м, внутренний диаметр 2,4 м в верхней части и 5,5 м в нижней). Варка из двухступенчатой была упрощена до одноступенчатой при температуре 165 °С с антрахиноном. После котла масса направлялась на диффузионную промывку, затем на сортирование
иотбелку. Небеленую целлюлозу сначала делигнифицировали кислородом, а затем, после кислотной промывки, добеливали в две ступени пероксидом водорода. Для повышения белизны целлюлозы предусматривалась возможность дополнительной добелки по схеме Д–Щ–Д с использованием тех же башен отбелки. Беленую целлюлозу далее очищали и сушили. Черный щелок из котла подавался в пленочные испарители, где сбрасывалось давление, и щелок концентрировался. Метанол иконденсаты направлялись на перегонку. Эффективность регенерации метанола из щелока составляла 99,95 %.
Упаренный щелок сжигался в присутствии достаточного количества кислорода. Термический КПД котлоагрегата был значительно выше 80 % (на сульфат-целлюлозных заводах 65–67 %). Эффективность регенерации всех соединений натрия выше 90 %. Очистные сооружения на 30–50 % меньше типовых. Проработав несколько месяцев по новой технологии, компания «Bayerische Zellstoff GmbH» в 1993 г. прекратила выпуск целлюлозы и освоение нового процесса из-за возникших технических затруднений
ипадения цен на целлюлозу.
ВФинляндии разрабатывается новый щелочной варочный процесс, в котором для улучшения делигнификации используют этанол и антрахинон. Процесс предназначен для переработки любого вида волокнистого сырья и включает три стадии: пропитку, делигнификацию и промывку щелочью. Сырье на 1-й ста-
40