
Экологически безопасные способы получения целлюлозы
..pdfПревращение полисахаридов древесины при КЩ-варке, как и при щелочной, обусловлено в основном тремя реакциями:
1)нежелательной реакцией пилинга (отщепления) концевого редуцирующего звена полисахаридной цепи, содержащего восстанавливающую карбонильную СО-группу;
2)реакцией стабилизации этих концевых звеньев посредством их окисления до карбоксильных групп (реакция стоппинг), приводящей к прерыванию реакции пилинга;
3)реакцией гидролитической деструкции полисахаридной цепи в любом ее месте.
Особенности и проблемы кислородно-щелочной вар-
ки. Важнейшей особенностью КЩ-делигнификации древесины, исключающей возможность варить этим способом щепу нормальных размеров в варочной аппаратуре традиционных конструкций, является высокий градиент концентрации кислорода (ГКК) по толщине щепы, т.е. резкое снижение его концентрации в направлении от поверхности щепы к ее центру. Это явление возникает вследствие низкой растворимости кислорода в воде и водных растворах (13–18 ммоль/л в условиях варки) и его высокой реакционной способности при взаимодействии с лигнином древесины.
Данное явление приводит к тому, что, в то время как наружные слои нормальной по толщине щепы (3–5 мм) уже успели провариться до требуемой степени делигнификации, ее внутренние слои могут быть еще почти не проварены или проварены совершенно недостаточно. Когда же внутренние слои нормальной щепы достигнут требуемой степени делигнификации, значительная часть целлюлозы уже будет заметно переварена с соответствующими последствиями – пониженными выходом и особенно механическими свойствами.
Естественно, что чем более тонкий древесный материал берется для КЩ-варки, тем меньше сказывается отрицательное влияние ГКК. Однако даже при использовании для варки тонкой осиновой щепы толщиной 1,0–1,5 мм около 30 % целлюлозы
51
получается переваренной, с числом Каппа в 1,5–2,0 раза ниже, чем в среднем у древесного остатка.
Значение ГКК можно снизить не только за счет уменьшения толщины щепы, но и посредством увеличения концентрации кислорода в щелоке, что достигается:
–повышениемдавлениякислорода(обычнодо1,5–3,0 МПа);
–использованием принудительных мер увеличения массообмена (автоклавы с мешалкой, качающиеся автоклавы в лабораторной практике);
–насыщением щелока кислородом в системе его циркуляции (вне котла) с помощью различных аэрирующих устройств;
–повышением гидромодуля.
Для более или менее успешной реализации КЩ-варки (особенно одноступенчатой) необходимо использовать все перечисленные выше приемы.
В качестве сырья для одноступенчатой КЩ-варки могут использоваться обычная щепа, тонкая щепа, стружка толщиной около0,5 мм, опилки, образующиеся в качествеотходов лесопиления.
При варке обычной щепы выход нормальной целлюлозы с высокими показателями прочности составляет 50–52 % от массы абсолютно сухой древесины при содержании остаточного лигнина 2–3 %. Однако содержание непровара при этом составляет 14–16 % от массы абсолютно сухой древесины. Этот непровар собирается и доваривается в отдельных котлах.
Варка тонкой щепы позволяет получать целлюлозу с непроваром не более 2 % от массы абсолютно сухой древесины. Получать такую щепу можно на специальных рубительных машинах, позволяющих регулировать толщину щепы.
Недостатками при использовании для варки тонкой щепы или стружки являются меньшая степень заполнения котла древесиной, а также повышенный расход электроэнергии на их получение.
При рассмотрении различных видов щелочных агентов, используемых при КЩ-варке, отдается предпочтение карбонату
52
натрия. Его использование обеспечивает щелочность, достаточную для активной делигнификации (значение рН исходного щелока обычно равно 10,3–10,8). При этом карбонат натрия дешевле гидроксида натрия, который также может быть успешно использован для КЩ-варки, но в отличие от последнего карбонат натрия приводит к несколько меньшей деструкции целлюлозы и не требует ступени каустизации при регенерации основания из щелока.
Хорошие механические показатели получаются при использовании в качестве основания гидрокарбоната натрия. Однако в этом случае в схему регенерации необходимо вводить ступень абсорбции, так как бикарбонат получают насыщением растворов карбоната углекислым газом, в больших количествах образующимся как при КЩ-варке, так и при сжигании щелоков. Кроме того, более низкое значение рН растворов этого основания заметно замедляет делигнификацию.
Использование в качестве основания более дорогого карбоната калия повышает расходы на восполнение потерь основания, однако позволяет отработанный щелок использовать в качестве полноценного калийного удобрения. Также в качестве удобрения, но аммонийного, можно использовать щелок от кислородноаммониевой варки. Однако в этом случае в процессе варки образуются устойчивые к окислительной фрагментации конденсированные азотосодержащие структуры лигнина. Вследствие этого варка существенно замедляется, а получаемая целлюлоза имеет пониженные показатели прочности и выхода, темный цвет и трудно белится.
Одноступенчатая КЩ-варка. Для получения КЩ-цел-
люлозы с хорошими показателями выхода (55–57 и 57–60 % от массы абсолютно сухой древесины соответственно для хвойной и для лиственной древесины) и механической прочности одноступенчатую варку следует проводить в следующих условиях: древесный материал – стружка или щепа толщиной не более
1–2 мм; варочный щелок 10–12 г/л Na2CO3 (7,5–10,0 г/л NaOH),
53

давление кислорода при комнатной температуре 1,5–3,0 МПа, гидромодуль 15–30, температура 140–160 °С; использование приемов дополнительного усиления массообмена. Продолжительность варки составляет 3–6 ч.
Механические свойства целлюлозы, получаемой одноступенчатой КЩ-варкой, зависят от режима варки и интенсивности массообмена. При оптимальных условиях варки небеленая целлюлоза из лиственных пород древесины имеет следующие механические показатели: разрывную длину 9,5–11,5 км, сопротивление раздиранию 450–500 мН, продавливанию 350–550 кПа и излому 450–1800 ч. д. п.* (при 60 °ШР и отливке 75 г/м2).
Из приведенных данных видно, что целлюлозы, полученные одноступенчатой КЩ-варкой, уступают сульфатной целлюлозе по значениям сопротивления излому и немного – по сопротивлению раздиранию, заметно превосходя по разрывной длине.
Вкачестве аппаратурного оформления одноступенчатой КЩ-варки предлагается использовать как варочные котлы периодического, так и непрерывного действия (типа Камюр) при условии некоторой их модернизации. Котлы должны быть снабжены эффективными аэрирующими устройствами для насыщения циркулирующего щелока кислородом.
Двухступенчатые КЩ-варки. Наличие ГКК создает весьма большие трудности для практической реализации КЩ-варки, причем даже при использовании щепы толщиной 1–2 мм. Решить эту проблему возможнопутем проведения КЩ-варки вдве ступени.
Вэтом случае на 1-й ступени посредством натронной или содово-натронной варки нормальной щепы получают полуфабрикат повышенного выхода, который затем подвергают механическому размолу в дисковой мельнице с целью разделения щепы на волокна, а на 2-й ступени эту волокнистую массу доваривают КЩ-способом до получения целлюлозы требуемой степени делигнификации.
* ч. д. п. – число двойных перегибов.
54
Основные недостатки двухступенчатых КЩ-варок:
1.При получении на 1-й ступени варки полуфабрикатов сверхвысокого и высокого выхода (выше 70–80 %) их последующий размол заметно повреждает волокна. Вследствие этого КЩ-варка таких полуфабрикатов на 2-й ступени при повышенной температуре обычно приводит к снижению прочности и выхода целлюлозы.
2.При получении после 1-й ступени относительного невысокого выхода полуфабриката (50–65 %) в результате более глубокой делигнификации на 2-й ступени получается целлюлоза, близкая по прочности к сульфатной. Однако вследствие того, что значительная часть лигнина древесины удаляется на 1-й ступени посредством традиционных способов, существенно уступающих КЩ-делигнификации по селективности, окончательный выход целлюлозы очень мало превышает выход целлюлоз, получаемых традиционными способами. При этом исключается одно из важнейших экономических преимуществ КЩ-варки – повышенный выход целлюлозы. Кроме того, двухступенчатые КЩ-варки технологически и в аппаратурном оформлении сложнее одноступенчатых варок.
Другой вариант двухступенчатых КЩ-варок не предусматривает размол между ступенями и заключается том, что при варке щепы на 1-й ступени вследствие делигнификации и удаления из клеточных стенок волокон части гемицеллюлоз, пектинов и смол проницаемость древесного сырья для щелока и растворенного в нем кислорода существенно возрастает.
Примером такой двухступенчатой КЩ-варки является способ DODDEL, разработанный японской фирмой «Toyo Pulp Co. Ltd». Суть его в том, что обе ступени варки (1-я ступень – натронная варка с добавкой антрахинона в количестве 0,1 % от
массы абсолютно сухой древесины, 2-я ступень – КЩ-варка) с промежуточной диффузионной промывкой массы между ними проводятся в одном варочном аппарате типа Камюр. Варке подвергается нормальная щепа при гидромодуле 20 с повторным
55
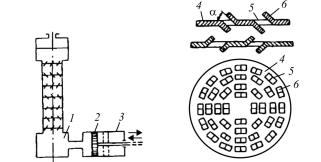
использованием части отработанного щелока кислородной ступени. Щелочь на КЩ-ступени вводится постепенно для поддержания постоянного значения рН. Предполагалось строительство работающей по этому способу опытно-промышленной установки производительностью 50 т/сутки целлюлозы.
Известно, что опыты по промышленной реализации КЩ-варки подобного типа в котле Камюр проводились и в США фирмой «Wayerhauser». Однако результаты не удовлетворили разработчиков, так как возникли проблемы, связанные с неравномерным распределением кислорода по сечению и высоте варочного котла, а также с необходимостью иметь кислород в волокнистой массе в мелкодиспергированном виде.
КЩ-варка в пульсационном аппарате. Очень перспек-
тивное аппаратурное оформление процесса КЩ-варки, позволившее решить все основные проблемы, связанные с особенностями КЩ-варки щепы любой толщины, было предложено российскими специалистами во ВНИИБ. Это изобретение было запатентовано в пяти странах с развитой целлюлозно-бумажной промышленностью.
Пульсационный варочный аппарат является аппаратом непрерывного действия и представляет собой полую вертикальную колонну (рис. 10). По высоте колонны через определенные
Рис. 10. Схема пульсационного аппарата и неподвижной тарелки: 1 – пульсационный аппарат; 2 – поршень; 3 – пульсатор; 4 – тарелка; 5 – прямоугольное отверстие; 6 – направляющая лопасть
56
промежутки расположены неподвижныетарелки, перекрывающие все свободное сечение колонны и имеющие прямоугольные отверстия малого сечения, снабженные прямоугольными направляющими лопастями, а также цилиндрические патрубки (на рисунке не показаны) для перемещения щепы с тарелки на тарелку сверху вниз. Патрубки на соседних тарелках расположены напротив друг друга. Кислород подается в нижнюю часть колонны
идвижется снизу вверх, т. е. противотоком относительно направления перемещения щепы. В установившемся процессе аппарат целиком заполнен массой, которая пульсирует под действием пульсатора, соединенного с нижней частью колонны. При этом кислород диспергируется на мелкие пузырьки на каждой тарелке, проходя через ее отверстия вверх, этому способствует
ислой щепы, находящийся на ней. От пульсатора к жидкости, заполняющей колонну, постоянно передается возвратно-поступа- тельное движение в вертикальном направлении. Направляющие лопасти у малых отверстий тарелок добавляют к такому вертикальному возвратно-поступательному движению еще и вращательное движение, которое меняет свое направление на каждой
тарелке, поскольку лопасти на соседних тарелках направлены в противоположные стороны. Движение от жидкости передается щепе. В результате кислород диспергируется на каждой тарелке по всему поперечному сечению колонны, что создает весьма благоприятные условия для внешнего массообмена. Благодаря этому во всем объеме аппарата концентрация кислорода в щелоке оказывается близкой к равновесной.
Постоянное интенсивное пульсирующее гидродинамическое воздействие на щепу, трение щепок друг о друга приводит к отделению сварившихся волокон поверхностного слоя, делигнифицирующихся при КЩ-варке в первую очередь. При этом на щепе обнажается новая реакционная поверхность. Сварившиеся волокна проваливаются в те же отверстия, через которые снизу вверх движется кислород, непрерывно выводятся из аппарата с потоком циркулирующего щелока и отделяются от него в спе-
57
циальном выгрузочном устройстве. Частично сваренная щепа через патрубки, расположенные на краях тарелок, перемещается сверху вниз вплоть до полного превращения в сварившееся волокно. Требуемая степень делигнификации целлюлозы, при которой волокна отделяются от щепы, регулируется значениями факторов варки, из которых основным в данном случае является интенсивность пульсаций. Обычно этот показатель колеблется в интервале 1000–4000 мм/мин.
Основные значения факторов режима при КЩ-варке в пульсационном аппарате: давление 1,5–2,0 МПа; температура 140–150 °С; рН около 7,5; гидромодуль в реакционной зоне котла около 7,5 (но с учетом всего объема щелока, находящегося в системе циркуляции и принимающего участие в варке, – около 15); продолжительность варки 4–5 ч; расход кислорода 15–16 %; расход карбоната натрия 20–21 % (в ед. NaOH) от массы абсолютно сухой древесины. Система питания аппарата щепой такая же, как и в котлах Камюр. Щепа предварительно пропаривается, пропитывается варочным раствором; значение рН щелока в процессе варки поддерживается постоянным посредством периодической подачи в систему небольших объемов крепкого раствора щелочного агента.
Пульсационный варочный аппарат с высокой эффективностью может быть использован и для кислородной ступени двухступенчатой варки. После 1-й (щелочной) ступени (расход Na2O 7–12 % от массы абсолютно сухой древесины, гидромодуль 5, температура 160 °С, время 20–90 мин) продолжительность кислородной варки сокращалась на 30–40 % и существенно повышались механические свойства КЩ-целлюлозы, вплотную приближаясь или становясь равными соответствующим показателям сульфатной целлюлозы. Однако в этом случае незначительно снижалась белизна и на 3–5 % от массы абсолютно сухой древесины уменьшался выход КЩ-целлюлозы, оставаясь тем не менее на 2–5 % выше, чем у сульфатной.
В 1988 г. на Сясьском ЦБК была построена и успешно работала в течение 9 лет пилотная установка непрерывной
58
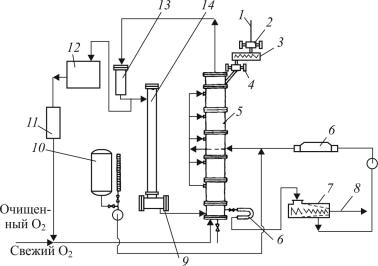
КЩ-варки с расчетной производительностью 100 кг/сут, основой которой являлся пульсационный аппарат (рис. 11). В 1997 г. она была законсервирована из-за отсутствия финансирования для продолжения работ в этом направлении.
Рис. 11. Схема полузаводской установки для кислородно-щелочной варки в пульсационном аппарате: 1 – щепа; 2 – питатель низкого давления; 3 – пропарочная камера; 4 – питатель высокого давления; 5 – варочный аппарат; 6 – теплообменники; 7 – разгружатель целлюлозы; 8 – целлюлоза на промывку; 9 – пульсатор; 10 – бак варочного щелока; 11 – компрессор; 12 – установка очистки газов;
13 – конденсатор; 14 – пульсационная камера
Удельная производительность пульсационного варочного котла, рассчитанная исходя из параметров пилотной установки (внутренний диаметр 0,2 м; высота 8,5 м), равна 0,39 т/м3 в сутки. Это значение существенно ниже аналогичного показателя для котлов Камюр, не имеющих промывной зоны (1,18 т/м3 в сутки), из-за значительно более высокого гидромодуля КЩварки по сравнению с сульфатной. Однако котлы Камюр с диф-
59
фузионной промывкой массы в котле имеют удельную производительность 0,47 т/м3 в сутки, близкую к значению для пульсационного котла.
Белимость и отбелка целлюлоз. Белизна небеленой хвойной КЩ-целлюлозы (30–45 %) в 1,3–1,5 раза выше белизны сульфатной целлюлозы (23–28 %). Белизна лиственной КЩцеллюлозы превышает белизну сульфатной фактически в два раза (при числе Каппа 10–20 ед. ее белизна достигает 60–70 %). Причем как для хвойной, так и для лиственной небеленой КЩцеллюлозы белизна увеличивается практически пропорционально снижению числа Каппа. Белимость КЩ-целлюлозы высокая, при этом лиственная целлюлоза белится значительно легче хвойной. Исключение составляет только КЩ-целлюлоза, полученная на аммониевом основании, которая имеет белизну, близкую к сульфатной, и белится почти так же трудно, как сульфатная, из-за наличия в остаточном лигнине конденсированных азотсодержащих соединений.
Осиновую КЩ-целлюлозу с числом Каппа 15–20 ед. можно отбелить до уровня полубеленой целлюлозы в одну ступень пероксидом водорода при его расходе 2 % от массы абсолютно сухой целлюлозы. При отбелке по схеме Д–П (расход активного хлора 2 % от массы абсолютно сухой целлюлозы) белизна целлюлозы составляет 87 % при химических потерях волокна всего около 2 % от массы абсолютно сухой целлюлозы. Березовая ки- слородно-бикарбонатная целлюлоза в три ступени (Д–П–Д) отбеливается до белизны 88–92 % с выходом 54 % от массы абсолютно сухой древесины.
Высокая избирательность КЩ-делигнификации и устойчивость небеленых КЩ-целлюлоз к окислительным обработкам при отбелке (СlO2, Н2О2, О3) способствуют тому, что выход беленых КЩ-целлюлоз на 2–5 % от массы абсолютно сухой древесины выше выхода сульфатных целлюлоз, аналогичных по белизне и породе использованной древесины.
По схеме Д–Щ–Д с расходом диоксида хлора 1,5–3 % от массы абсолютно сухой целлюлозы лиственная КЩ-целлю-
60