
Экологически безопасные способы получения целлюлозы
..pdfдии пропитывают водным раствором реагентов (NaOH, Na2CO3, антрахинон) несколько часов при температуре 100 °С. Щелочь при этом расходуется только на нейтрализацию кислых групп
иомыление ацетильных групп. Затем водный раствор замещают водно-спиртовым раствором щелочи и антрахинона и быстро поднимают температуру. Концентрация спирта при варке 40–50 % (по массе), температура 160–180 °С для древесины хвойных пород и 140–170 °С для древесины лиственных пород
инедревесного сырья. После варки массу промывают при тем-
пературе 130 °С водным раствором щелочи (NaOH, Na2CO3). По сравнению с сульфатными варками выход целлюлозы выше, а расход щелочи ниже. Получаемые целлюлозы по качеству сопоставимы с сульфатными целлюлозами.
Применение спиртов в традиционных варочных процессах также давало хорошие результаты. Использование при натронной варке водно-этанольной смеси (50:50) усиливало делигнификацию древесины хвойных пород: получали целлюлозу более высокого выхода и большей белизны. В традиционной и модифицированной сульфатных варках введение 12 % метанола в варочный раствор улучшало делигнификацию. Вязкость целлюлоз повышалась, но механические характеристики и белимость сульфатной целлюлозы не улучшались. Использование при сульфатной варке этанола (10–30 мол. %) обеспечило повышение на 4 % выхода целлюлозы и на 30 % сокращение продолжительности варки
сминимальными изменениями свойств целлюлозы.
ВГермании для переработки всех видов волокнистого сырья разработан щелочно-сульфитный варочный процесс ASAM
сиспользованием метанола и антрахинона (рис. 8). Процесс позволяет получать целлюлозу с более высоким выходом, чем при сульфатной и сульфитной варках, с механическими свойствами, равными свойствам сульфатной целлюлозы. В 1990 г. ввели в эксплуатацию пилотную установку производительностью 3 т беленой целлюлозы в сутки на территории сульфитного завода
41
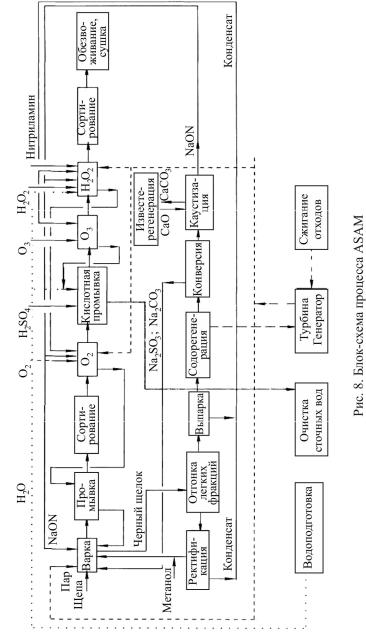
42
в Байенфурте. Установка включала оборудование для варки, промывки, сортирования волокна и оборудование для регенерации метанола и концентрирования щелока. Целлюлоза, отбеленная по схеме КЩО–К–О3–П, по качеству превосходила сульфатную. С 1994 г. маркетинговой проработкой процесса занима-
ется фирма «Voest-Alpine Industrieanlagenbau GmbH» вместе с фирмами, разработавшими и запатентовавшими схему регенерации химикатов.
Впроцессе используются стандартное оборудование и традиционные конструкционные материалы, за исключением варочного котла, рассчитанного на рабочее давление 1,1–1,4 МПа. Состав варочного раствора: 10–20%-ный метанол; 0,065–0,075 % от массы абсолютно сухой древесины антрахинона; 20–25 % от массы абсолютно сухой древесины общей щелочи, в том числе
15–20 % Na2SO3, 0–5 % NaOH и 0–5 % Na2CO3. При продолжи-
тельности варки 100–180 мин и температуре 175–185 °С выход целлюлозы на 2–5 % больше, чем при сульфатной варке, число Каппа 18–20 ед. для древесины хвойных пород и 8–10 ед. для древесины лиственных пород. При последующей делигнификации целлюлозы кислородом число Каппа снижается на 60 %.
Вцелом, эколого-экономическая оценка процесса показала возможность получения целлюлозы высокого качества при низких текущих затратах и низком уровне воздействия на окружающую среду с перспективой создания системы замкнутого водооборота.
2.2.4. Уксусно-кислотные варки
Уксусная кислота, так же как метанол и этанол, относится к многотоннажным продуктам, широко используемым в промышленности. Она хорошо растворяет лигнин, а 50%-ную уксусную кислоту применяют в лабораторной практике в качестве растворителя при выделении лигноуглеводного комплекса из древесины. При взаимодействии лигнина с концентрированными растворами уксусной кислоты происходит гидролитическое
43
расщепление α- и β-эфирных связей, что и определяет возможность выделения лигнина. Расщепление эфирных связей сопровождается реакциями конденсации лигнина.
При делигнификации древесины лиственных пород при температуре 160–185 °С повышение концентрации уксусной кислоты с 50 до 75 % ускоряет делигнификацию и повышает выход целлюлозы, что объясняется уменьшением степени набухания полисахаридов и снижением их доступности и растворимости. Однако в целом снижение степени набухания клеточной стенки при повышении концентрации кислоты до 87,5 % затрудняет делигнификацию.
Исследования процесса делигнификации с уксусной кислотой проводились во многих странах. В Германии разработан процесс Acetosolv, заключающийся в делигнификации различных видов волокнистого сырья 93%-ной уксусной кислотой, содержащей 0,1–0,2 % НС1, при 110 °С (при атмосферном давлении) с последующей отбелкой озоном и пероксидом водорода (без промежуточной промывки). Отбелка озоном в уксусной кислоте более селективна, чем в воде. Пероксид водорода в уксусной кислоте образует перуксусную кислоту, являющуюся хорошим отбеливающим реагентом. Все это позволяет получать целлюлозу с белизной до 88–90 % без хлорсодержащих реагентов. Получается целлюлоза с механическими характеристиками, близкими к характеристикам сульфатной целлюлозы, за исключением сопротивления раздиранию. В 1989 г. создана пилотная установка производительностью 200 кг беленой целлюлозы в сутки, в которой сырье перерабатывалось в карусельном экстракторе с противоточным движением массы и растворов.
Поскольку использование минеральных кислот повышает коррозионную активность варочной среды, они были исключены из варочного раствора. Поэтому при некаталитической делигнификации древесины 50–87,5%-ными растворами уксусной кислоты температура повышается до 160–220 °С. Замена значи-
44
тельной части уксусной кислоты на этилацетат позволяет делигнифицировать с хорошими результатами древесину хвойных и лиственных пород при температуре 170–200 °С.
2.2.5. Варки с фенолами
Варки с фенолами – это типичные кислотные варки, в которых фенолы кроме функций органического растворителя исполняют роль нуклеофильного реагента, который взаимодействует с лигнином, препятствуя его конденсации. Потери фенолов компенсируют расщеплением выделяемого лигнина до низкомолекулярных фенолов в процессе пиролиза или гидрогенолиза (обработка водородом при повышенных давлениях и температурах с катализаторами).
В процессе, совместно разработанном «Баттеле-Женева» (Швейцария) и «Ринтекно Ой» (Финляндия), древесину хвойных или лиственных пород обрабатывают 40%-ным водным фенолом с каталитическим количеством НС1 при 100 °С в течение 4 ч и более. Получают целлюлозу, по свойствам соответствующую сульфитной, с низкой массовой долей остаточного лигнина. Отработанный варочный раствор при отстаивании расслаивается. От органического слоя отгоняют фенол, а остаток, содержащий лигнин и фенол, подвергают гидрогенолизу. Водный слой после выделения фенола с помощью толуола направляют на биохимическую переработку для утилизации содержащихся
внем углеводов.
ВЯпонии разрабатывались варианты фенольных варок без кислотных катализаторов, вызывающих коррозию оборудования. В качестве фенола использовался крезол. Было установлено, что древесина лиственных пород делигнифицируется в 70%-ных водных крезолах при температуре 185 °С, а хвойных – при более высоких температурах (до 200 °С). Добавка уксусной кислоты (10–40 % от массы абсолютно сухой древесины) снижала температуру варки на 15–20 °С. Из древесины ели и пихты получали
45
целлюлозу (выход 50,4–59,3 %, остаточный лигнин 2,3–7,9 %), по механическим свойствам соответствующую сульфатной целлюлозе, за исключением сопротивления раздиранию.
Врезультате был разработан процесс Solvolysis Pulping,
вкотором для варки используют фракцию фенолов, получаемую пиролизом или гидрогенолизом лигнина. Это трехступенчатый варочный процесс, в котором сначала проводят варку в 80%-ном водном фенольном растворителе, а затем два раза экстрагируют сырье фенольным растворителем и промывают водой. В результате из древесины лиственных и хвойных пород получают целлюлозу с содержанием остаточного лигнина 5 %, которую отбеливают до белизны 88 % по схеме КЩО–Д–Щ–Д.
При отстаивании отработанный варочный раствор разделяется на два слоя – водный и органический. Из водного слоя выделяют углеводы, а из органического отгоняют низкомолекулярные фенолы. Остаток после отгонки подвергают пиролизу или гидрогенолизу. В качестве товарной продукции кроме целлюлозы получают лигнин, низкомолекулярные фенолы и углеводы. Степень превращения лигнина в фенолы невелика, и выделение из образующейся смеси индивидуальных фенолов все еще экономически нецелесообразно.
2.2.6. Варка с этиленгликолем
Этиленгликоль является эффективным делигнифицирующим древесину органическим растворителем.
Варка древесины в среде этиленгликоля может быть осуществлена в аппарате непрерывного действия Пандия (рис. 9). Производительность установки 150 т/сут. Варка ведется с непрямым обогревом при температуре 160–170 °С в течение 15–30 мин. Питатель для загрузки щепы в верхнюю варочную трубу устраивается по типу шнек-пресса.
46
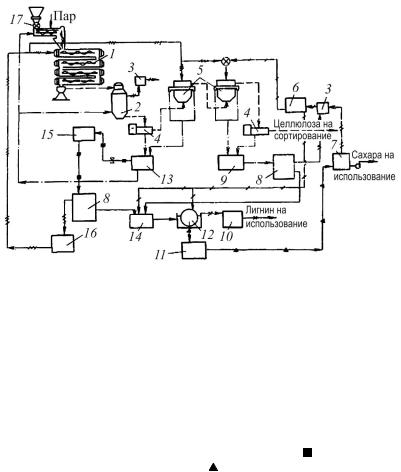
Рис. 9. Принципиальная технологическая схема получения целлюлозы путем варки древесины с этиленгликолем: 1 – варочный аппарат Пандия; 2 – выдувной резервуар, 3 – конденсатор; 4 – пресс; 5 – диффузор; 6 – сборник воды; 7 – испаритель; 8 – вакуум-дистилляторы; 9 – сборник разбавленного отработанного этиленгликоля; 10 – сборник лигнина; 11 – сборник раствора углеводов; 12 – вакуум-фильтр; 13 – сборник отработанного этиленгликоля; 14 – сборник сгустка (лигнин и углеводы); 15 – сборник этиленгликоля четырехкратного использования; 16 – сборник регенерированного этиленгликоля; 17 – дозатор; – – – масса, – · – отработанный этиленгликоль, –//– пары вскипания, –///– регенерированный этиленгликоль, –––– отработанный
этиленгликоль четырехкратный, |
– – водный раствор углеводов, |
–х– лигнин, |
–/– вода |
Щепа из бункера через лопастной расходомер попадает в приемную воронку и захватывается витками шнека. Из шнекпресса щепа попадает в диффузор и подается в пропиточную трубу со шнеком. Пропитка осуществляется смесью отработанного этиленгликоля и соляной кислоты. Варочный раствор подается во вторую варочную трубу.
47
Сваренная масса выводится из аппарата с помощью разгрузочного устройства в выдувной резервуар с «живым» дном, состоящим из ряда шнеков, откуда масса концентрацией 8–10 % подается на промывку в диффузор непрерывного действия Камюр. Продолжительность промывки 7–8 мин, производительность диффузора 100–500 т /сут.
Промывка целлюлозы осуществляется противотоком этиленгликолем, затем смесью этиленгликоля и воды и окончательно водой в трех последовательно работающих диффузорах. Промытая целлюлоза после сортирования поступает на отбелку по схеме Д–Щ–Д.
Отработанный щелок после отжима целлюлозы на прессах поступает в сборник и вновь используется на варку и промывку целлюлозы. После многократного использования отработанный этиленгликоль направляется на регенерацию в выпарной аппарат, где этиленгликоль отделяется от лигнина и углеводов. Регенерированный этиленгликоль возвращается в производство, а упаренный остаток разбавляется водой и поступает на центрифугирование, где выделяется практически чистый лигнин, углеводный остаток после упаривания направляется на биохимическую переработку.
Смесь этиленгликоля и воды от промывки целлюлозы направляется на вакуум-дистилляцию в выпарной аппарат. После выпарки вода поступает на промывку целлюлозы, а этиленгликоль – на варку целлюлозы.
Целлюлоза, полученная из хвойной древесины варкой в среде этиленгликоля, имеет выход 51,6 % от абсолютно сухой древесины, степень делигнификации 29 ед. и показатели прочности на уровне соответствующих показателей хвойной бисульфитной целлюлозы.
Полупромышленные испытания и проведенные техникоэкономические расчеты показывают целесообразность использования этиленгликоля для варки целлюлозы при реконструкции
48
действующих предприятий малой мощности, в частности старых сульфитно-целлюлозных заводов.
2.3. ОКИСЛИТЕЛЬНЫЕ СПОСОБЫ ПОЛУЧЕНИЯ ЦЕЛЛЮЛОЗЫ
2.3.1. Кислородно-щелочной способ
Кислородно-щелочной (КЩ) способ получения целлюлозы – один из наиболее перспективных и потому хорошо разработанных бессернистых способов.
Кислородно-щелочная варка проходит в водной среде. Активными делигнифицирующими агентами при КЩ-варке являются молекулярный кислород и щелочь (Na2CO3, NaHCO3, NaOH, NH4OH и др.). Это обеспечивает высокую экологичность данного способа – полное отсутствие токсичных и дурнопахнущих соединений как в стоках, так и в газовых выбросах.
КЩ-варка имеет следующие достоинства:
1.Выход целлюлозы на 6–8 % от массы абсолютно сухой древесины выше, чем при традиционных способах варки.
2.Белизна после варки лиственной древесины вдвое превосходит белизну сульфатной целлюлозы, достигая 60–70 % (у хвойной – около 40 %) при значительно более легкой белимости целлюлозы, полученной КЩ-способом.
3.При производстве целлюлозы по КЩ-способу реализуется упрощенная система регенерации основания: каустизация щелоков не требуется при использовании в качестве основания
Na2CO3, NaHCO3, NH4OH; сжигание отработанных щелоков может осуществляться не в сложных содорегенерационных котлоагрегатах (СРК), а в более простых агрегатах, например в топках циклонного типа (возможно и «мокрое сжигание» щелока).
Экономические расчеты показали, что производство целлюлозы КЩ-способом не уступает по рентабельности сульфатному способу или даже несколько превосходит его.
49
Краткие сведения о процессах и реакциях, составляю-
щих сущность варки. По сравнению с другими окислительнощелочными варками, проходящими в водной среде, КЩ-варка наиболее изучена.
Одним из наиболее важных параметров КЩ-варки является значение рН щелока. От него зависят не только селективность варки, ее скорость, но и направление реакций фрагментации макромолекул лигнина.
При высоких температурах КЩ-варки (140–160 °С) и рН > 7,0…7,2 окислительная фрагментация лигнина происходит относительно быстро, при рН ниже указанных значений этот процесс значительно замедляется.
Оптимальным значением рН на протяжении основной части КЩ-варки является 7,5, так как при этом значении хорошая селективность делигнификации сочетается с достаточно высокой скоростью процесса. Хорошие результаты могут быть получены в диапазоне рН = 7,5…8,5.
В процессе КЩ-варки, в первую очередь, в щелок переходит лигнин, наиболее доступный действию щелока и растворенного внем кислорода. Лигнин более труднодоступных областей также претерпевает окислительную фрагментацию уже на самой ранней стадии варки, но, по-видимому, преимущественно под действием немолекулярного кислорода, а производных от негочастиц.
К моменту завершения начальной стадии варочного процесса (по достижении степени делигнификации 20–30 %) фактически весь лигнин уже разделен в твердой фазе на фрагменты с молекулярной массой (ММ) 550–4400 с преобладанием фрагментов с ММ, равной 1100–2200. Их переход в щелок происходит на последующей стадии варки, частично с незначительным снижением ММ за счет разрушения преимущественно концевых структур.
Таким образом, начальная стадия в процессе делигнификации играет определяющую роль и существенно влияет на результаты КЩ-варки в целом.
50