
Расчет и конструирование многоскоростных станочных приводов
..pdfФедеральное агентство по образованию
Государственное образовательное учреждение высшего профессионального образования
«Пермский государственный технический университет»
В. К. Зальцберг, А. И. Лурье
РАСЧЕТ И КОНСТРУИРОВАНИЕ МНОГОСКОРОСТНЫХ СТАНОЧНЫХ ПРИВОДОВ
Рекомендовано Учебно-методическим объединением
по профессионально-педагогическому образованию для студентов специальности «Профессиональное обучение» (машиностроение и технология, оборудование, материаловедение и обработка материалов)
в качестве учебного пособия
Издательство Пермского государственного технического университета
2010
ÓÄÊ 621.9.06 Ç25
Рецензенты:
завкафедрой «Технология машиностроения» Пермского государственного технического университета д-р техн. наук, проф. В. Ф. Макаров;
проф. кафедры «Ремонт машин» Пермской государственной сельскохозяйственной
академии А. И. Горчаков
Зальцберг, В. К.
З25 Расчет и конструирование многоскоростных станочных приводов: учеб. пособие / В. К. Зальцберг, А. И. Лурье.— Пермь: Изд-во Перм. гос. техн. ун-та, 2010.— 116 с.
ISBN 978-5-398-00383-3
Представлены основы конструирования многоскоростных приводов главного движения и подачи. Изложены основные положения по кинематиче- скому расчету приводов, методы улучшения их кинематики.
Рассмотрены вопросы конструирования шпиндельных узлов и рациональной компоновки приводов, вопросы технологичности конструкции узлов станков.
Предназначено для студентов направления 150900 «Технологическое оборудование и автоматизация машиностроительных производств», выполняющих курсовые проекты по металлорежущим станкам, по расчету и конструированию станков.
ÓÄÊ 621.9.06
ISBN 978-5-398-00383-3 |
© ГОУ ВПО «Пермский |
|
государственный |
|
технический университет», 2010 |
ОБЩИЕ УКАЗАНИЯ ПО ПРОЕКТИРОВАНИЮ
Основные этапы проектирования металлорежущего станка
Создание каждой новой модели станка является результатом большого творческого труда коллективов конструкторов и исследователей.
В соответствии с ГОСТ 2.103–68* «Стадии разработки» основными этапами проектирования станков, принятыми в практике станкостроения, являются: техническое предложение, эскизный проект, технический проект, рабочая документация.
Техническое предложение. Его цель — обосновать целесообразность создания станка и дать исходные данные для его проектирования. Новый станок должен иметь более высокие технические характеристики по сравнению с существующими станками, обеспе- чить явные преимущества в случае его применения. Эти новые ка- чества могут быть разнообразны: повышенная точность и производительность станка, уменьшенные габариты, упрощенная конструкция, повышенная степень автоматизации и универсальность, возможность применения более высоких режимов обработки и др.
При составлении технической характеристики проектируемого станка, как правило, дается сводная таблица характеристик лучших станков данного типа. В техническом задании указываются основные конструктивные особенности будущего станка, разрабатывается ориентировочный вариант его кинематической и электрической схем, устанавливаются технические характеристики, которым должен отвечать новый станок.
Эскизный проект. При его разработке выбирается наиболее целесообразный вариант компоновки станка и его узлов, рассчитываются основные узлы, окончательно разрабатываются кинемати- ческая, электрическая и гидравлическая схемы станка. Стадия эскизного проектирования необходима для того, чтобы, не затрачивая времени на окончательную доработку проекта, выбрать оптимальный вариант конструкции на основе анализа нескольких конструкций однотипных узлов.
3
Технический проект. При выполнении технического проекта станка производится окончательное оформление конструкции станка. Разрабатываются сборочные чертежи всех узлов и спецификация к ним с указанием оригинальных, покупных и нормализованных деталей. Рассчитываются все узлы и детали. В техническом проекте стремятся к наибольшему применению стандартных и унифицированных узлов, деталей. Технический проект, как правило, детально обсуждается и после корректировки служит основой для рабочего проекта станка.
Рабочая документация. Разрабатываются рабочие чертежи узлов, оригинальных деталей и технические условия к ним. Эти чертежи содержат все данные для изготовления деталей и сборки узлов станка. Они являются техническим документом для проектирования соответствующих технологических процессов.
Отработка внешней формы узлов и станка производится с помощью эскизов, по которым выполняется макет в натуральную величи- ну. На макете окончательно утверждаются детали оформления, после чего вносятся коррективы в рабочие чертежи. По рабочему проекту изготавливается опытный образец станка для проведения испытаний. Выявленные при испытании неисправности устраняются и корректируются чертежи. По исправленным чертежам выпускается опытная серия для дополнительной проверки станка в изготовлении и эксплуатации. Во время испытаний опытной серии учитываются все недостатки, вносятся исправления в рабочие чертежи, и только после этого станок запускается в серийное производство.
Тема и объем курсового проекта
Темой курсового проекта является разработка конструкции универсального станка. Узлы, которые указаны в задании, проектируют подробно. Все остальные узлы и элементы кинематики заимствуются из существующих моделей станков [1]. При проектировании общего вида станка неразрабатываемые студентом узлы вычерчиваются по аналогии с существующими станками.
Курсовой проект состоит из графической части и расчетно-по- яснительной записки. Графическая часть курсового проекта выполняется на 4–5 листах формата А1. Примерный перечень чертежей:
кинематическая схема станка |
— 1 ëèñò; |
сборочный чертеж проектируемого узла |
— 1–2 листа; |
4
сборочный чертеж специального устройства — 1 лист; рабочие чертежи деталей — 1 лист. Расчетно-пояснительная записка объемом 30–50 страниц вы-
полняется на листах формата А4.
Этапы выполнения проекта
Работу над проектом рекомендуется выполнять в такой последовательности:
1.Обосновать техническую характеристику станка.
2.Выбрать и обосновать кинематическую схему станка.
3.Построить график частот вращения проектируемой коробки скоростей (подач).
4.Определить частные передаточные отношения постоянных
èгрупповых передач, рассчитать числа зубьев колес, диаметры шкивов.
5.Произвести расчеты на прочность зубчатых колес, валов.
6.Выполнить эскизную компоновку проектируемой коробки.
7.Сделать уточненный расчет валов, подобрать подшипники.
8.Вычертить кинематическую схему станка, структурную сетку и график частот вращения.
9.Вычертить развертку и поперечный разрез проектируемой коробки.
10.Разработать конструкцию специального устройства станка.
11.Выполнить рабочие чертежи деталей (по указанию руководителя проекта).
12.Разработать систему смазки станка.
13.Составить расчетно-пояснительную записку к проекту.
1. ОБОСНОВАНИЕ ТЕХНИЧЕСКОЙ ХАРАКТЕРИСТИКИ СТАНКА
Для сокращения затрат времени на выполнение курсового проекта и с учетом его учебного характера часть исходных данных для проектирования указана в задании на проект.
Используя эти данные, проектант должен:
а) сделать обзор конструктивных вариантов станков заданной группы, обосновать особенности проектируемого станка;
б) выбрать режимы обработки; в) рассчитать диапазон регулирования;
г) определить знаменатель ряда частот вращения (подач); д) выбрать стандартный ряд частот вращения (подач).
1.1. Обзор конструктивных вариантов станков заданной группы
Современный парк металлорежущих станков характеризуется большим разнообразием типов и моделей. Почти всегда любую деталь можно обработать на имеющихся станках. Поэтому вновь проектируемый станок должен иметь более высокие технические характеристики по сравнению с существующими и обеспечивать явные преимущества в случае его применения.
Проектант должен изучить и проанализировать технические данные и конструктивное оформление станков подобных проектируемому. Для обзора необходимо подобрать наилучшие образцы отдельных узлов, компоновок, систем управления, которые можно применить в проекте. Это позволит создать реальную и современную конструкцию проектируемого узла и станка в целом.
1.2. Выбор режимов обработки
Режимы обработки, силы резания и эффективная мощность должны быть определены для всего диапазона обрабатываемых материалов и материалов инструмента, указанных в задании, исклю-
6
чая нереальные комбинации. Назначать режимы обработки следует по нормативам и справочникам режимов резания [12, 14]. Расчет режимов по эмпирическим формулам необязателен. Выбирая режимы обработки, следует обязательно указать принятые тип, геометрию и материал инструмента, обосновать поправочные коэффициенты.
При выборе режимов обработки необходимо учитывать особенности станков различных групп:
1.Для токарных станков при определении наибольшей скорости резания принимают:
а) глубину резания и подачу наименьшими; б) материал режущей части резца — твердый сплав;
в) стойкость наименьшую (например, Ò = 30 ìèí).
При определении наименьшей скорости резания глубину резания, подачу и стойкость инструмента принимают наибольшими.
Значение предельных скоростей резания определяют при работе без охлаждения. Для токарно-винторезных станков найденное значение наименьшей скорости резания следует сравнить со скоростями резания, используемыми при нарезании резьбы резцами.
Наибольшие значения сил резания определяют при наименьшей стойкости инструмента и при наибольших глубине резания и подаче.
Наибольшая эффективная мощность, потребная на резание, определяется по максимальной силе резания и соответствующей ей скорости резания.
2.Для сверлильных станков при определении наибольшей скорости резания диаметр сверла и подачу принимают наименьшими,
àпри расчете наименьшей скорости резания диаметр сверла и пода- чу принимают наибольшими.
Найденное значение минимальной скорости резания следует сравнить с допустимыми скоростями резания для выполнения других работ на станке: нарезания резьб машинными метчиками, зенкерования, развертывания и др.
Наибольшие значения осевой силы и момента резания при
сверлении определяются для максимального диаметра сверла и наибольшей подачи. При этих же условиях вычисляется наибольшая эффективная мощность, необходимая для сверления.
3. Для фрезерных станков при определении наибольшей скорости резания принимают:
7
а) материал режущей части фрезы — твердый сплав; б) диаметр фрезы минимальный; в) стойкость минимальную;
г) глубину резания и подачу на зуб фрезы минимальные; д) ширину фрезерования наименьшую, но с обеспечением рав-
номерного фрезерования.
При определении наименьшей скорости резания принимают: а) материал режущей части фрезы — быстрорежущую сталь; б) диаметр фрезы и стойкость наибольшие; в) глубину резания и подачу на зуб фрезы наибольшие; г) ширину фрезерования наибольшую.
Наибольшие значения окружной силы резания и эффективной мощности определяют при следующих условиях:
1.Материал режущей части фрезы при цилиндрическом фрезеровании — быстрорежущая сталь, при торцевом — твердый сплав.
2.Глубина резания и подача на зуб фрезы наибольшие.
3.Ширина фрезерования наибольшая.
4.Диаметр фрезы наибольший.
5.Стойкость фрезы наименьшая.
Следует иметь в виду, что при износе зубьев фрез до оптимальной величины сила фрезерования увеличивается при обработке вязких сталей на 75–90 %, при обработке сталей средней твердости и чугунов — на 20–40 %.
1.3. Расчет диапазона регулирования
Диапазоном регулирования называют отношение предельных частот вращения шпинделя.
По выбранным скоростям резания и диаметрам обработки (инструмента) подсчитываются предельные частоты вращения шпинделя.
Найденный диапазон регулирования является ориентировоч- ным и подлежит уточнению после выбора знаменателя ряда частот вращения. Диапазон регулирования может получиться слишком большим или слишком малым. В этих случаях не нужно повторять выбор режимов резания или корректировать их. Следует обратиться к литературным рекомендациям и к материалам анализа существующих моделей станков данной группы.
8
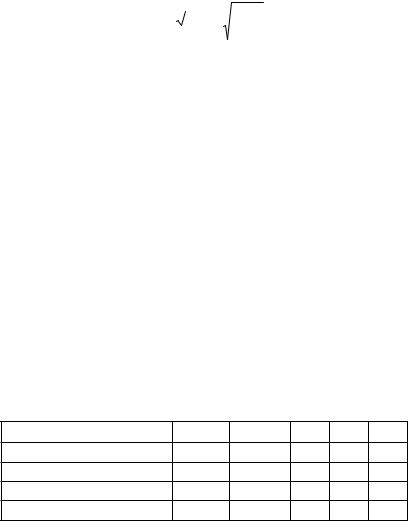
1.4. Определение знаменателя ряда частот вращения (подач)
Знаменатель ряда частот вращения определяют по формуле
|
Z 1 |
|
|
níàèá |
|
|
|
R Z 1 |
, |
||||
|
níàèì |
|||||
|
|
|
|
|
ãäå z — число скоростей (подач); R — диапазон регулирования. Расчетную величину знаменателя следует округлить до стан-
дартного значения. Отраслевой стандарт ОСТ 2 Н11-1–72 рекомендует для универсальных станков в основном применять знаменатели 1,26; 1,41; 1,58, а ГОСТ 8032–84 — «Предпочтительные числа и ряды предпочтительных чисел» — допускает применение приближенных предпочтительных чисел, значения которых равны 1,25; 1,4 и 1,6 (прил. 1).
При выборе знаменателя ряда следует учитывать величину Rãð.íàèá (см. с. 15) и дополнительные условия проектирования, указанные в задании. Так, применение двухскоростного электродвигателя ограничи- вает возможные значения знаменателя, применение перебора позволяет принимать большие значения знаменателя и т. д. Окончательно принять знаменатель ряда, диапазон регулирования и мощность привода следует после сравнения рассчитанных параметров с рекомендациями литературы и с характеристиками аналогичных станков.
Результаты сравнения и принятые параметры необходимо представить в виде табл. 1 и согласовать с руководителем проекта.
Ò à á ë è ö à 1
Технические характеристики станка
Значения параметров |
níàèá, 1/ìèí níàèì, 1/ìèí |
R |
|
N, êÂò |
Расчетное (заданное)
Рекомендуемое (ссылки)
Существующих моделей cтанков
Принятое
Частоты вращения следует принять из стандартного ряда (см. прил. 1).
9
2. КИНЕМАТИЧЕСКИЙ РАСЧЕТ КОРОБОК СКОРОСТЕЙ
Задачами кинематического расчета являются:
–выбор порядка расположения постоянных и множительных передач (варианта кинематической схемы);
–выбор последовательности переключения множительных передач;
–определение частных передаточных отношений;
–расчет чисел зубьев шестерен и диаметров шкивов.
Для удобства и облегчения кинематического расчета коробок скоростей и подач широко применяют графоаналитический метод, достоинством которого является большая наглядность, облегчающая сравнение вариантов [11]. Метод основан на последовательном построении графиков двух видов: структурной сетки и графика частот вращения. Первый график используется для выявления вариантов (последовательностей) переключения передач и определения относительных величин их передаточных отношений. С помощью второго графика устанавливаются абсолютные величины этих отношений, а также конкретные частоты вращения.
2.1. Закономерности ступенчатого регулирования
На выходе многоскоростного привода требуется получить геометрический ряд частот вращения. Рассмотрим, как должны изменяться передаточные отношения в таком приводе на примере коробки скоростей, кинематическая схема которой приведена на рис. 1.
Предположим, что для изменения частот вращения шпинделя, которые образуют геометрический ряд, в первую очередь будем переключать блок Б2, во вторую — блок Б1, в третью — блок Б3. Запишем уравнения кинематического баланса для всех частот вращения шпинделя, имея в виду, что для получения níàèì необходимо в каждой группе передач использовать наименьшее передаточное отношение, а для níàèá — наибольшее:
10