
Расчет и конструирование многоскоростных станочных приводов
..pdfÎ ê î í ÷ à í è å ò à á ë . 1 3
Тип подшипника |
Условия |
|
Класс точности подшипника |
||||
работы подшипника |
5 |
4 |
2 |
||||
|
|||||||
|
|
|
|
||||
Радиально-упорные с кони- |
Регулирование |
çà ñ÷åò |
Js5 |
Js4 |
– |
||
ческими роликами |
смещения |
наружного |
|
|
|
||
|
кольца |
|
|
|
|
|
|
|
Фиксированное |
наруж- |
K5 |
K4 |
– |
||
|
ное кольцо |
|
|
|
|
|
|
|
Сосредоточенная нагруз- |
M5 |
M4 |
– |
|||
|
ка на внутреннем кольце |
|
|
|
|||
Упорно-радиальные |
|
– |
|
– |
K5 |
K4 |
|
Упорные |
|
– |
|
H7 |
H7 |
– |
5.8.Смазка шпиндельных узлов
Âшпиндельных узлах станков применяются различные способы смазки. Выбор способа смазки зависит от быстроходности подшипников. Быстроходность оценивают с помощью скоростного параметра d·nmax ìì·1/ìèí (d — диаметр отверстия подшипника, nmax — предельная частота его вращения). Рекомендуемые способы смазки представлены в табл. 14.
Смазка погружением является простой, но пригодна только для тихоходных шпинделей. Смазочная камера должна вмещать достаточный объем масла, а его уровень должен достигать центра нижнего тела качения подшипника. Основной недостаток смазки погружением — относительно высокое тепловыделение в опорах, невозможность теплоотвода смазкой.
Òà á ë è ö à 1 4
Способы смазки шпиндельных подшипников
Скоростной параметр d·nmax ìì·1/ìèí |
Способ смазки |
55000–80000 |
Погружением |
225000–320000 |
Разбрызгиванием |
420000–600000 |
Циркуляционный |
280000–400000 |
Капельный |
550000–800000 |
Масляным туманом |
750000–1000000 |
Впрыскиванием |
71
Смазка разбрызгиванием осуществляется с помощью вращающейся шестерни или специальной крыльчатки, которая подает масло на подшипники шпинделя. Для нормальной работы системы смазки частота вращения шпинделя должна быть достаточно большой. Недостатком смазки разбрызгиванием является то, что масло в подшипник поступает загрязненным продуктами износа шестерен. Поэтому такая смазка в основном используется в станках для черновой обработки.
Циркуляционная система смазки применяется для шпиндельных узлов, работающих при напряженных режимах. С ее помощью можно обеспечить расход смазки через подшипник, необходимый по условиям теплоотвода. Охлаждение смазки может происходить естественным путем (в баке-отстойнике) или с помощью установки для искусственного охлаждения. В большинстве станков система циркуляционной смазки общая для шпинделя и коробки скоростей. Иногда устанавливают автономную систему циркуляционной смазки для подшипников шпинделя. Это усложняет систему, но позволяет применять смазки, оптимальные для данного режима работы шпиндельного узла. Раздельные системы циркуляционной смазки применяют для высокоскоростных шпиндельных узлов, в частности для смазки конических роликоподшипников, работающих при скоростном параметре d·nmax 200000 мм·1/мин. Необходимо обращать внимание на правильное расположение мест подвода смазки. Поскольку радиально-упорные подшипники производят насосное действие, смазку следует подавать в зону всасывания. В вертикальных шпиндельных узлах смазка должна подаваться в высшую точку и протекать через все подшипники шпинделя. При выходе из нижнего подшипника смазка должна поступать в ванну с хорошим уплотнением, откуда она либо отсасывается малым насосом, либо поступает в масляный бак.
При капельной смазке дозировка объема поступающего в подшипник масла осуществляется с помощью игольчатых и фитильных масленок. Пневматические капельные масленки позволяют настраивать подачу масла от 1 до 100 г в час. Тепловыделение подшипников при такой смазке невелико и поэтому ее широко применяют для смазки шпиндельных узлов с несколькими подшипниками. Вязкость масла выбирают исходя из условий работы подшипников, независи-
72
мо от требований к смазке других устройств коробки скоростей. При капельной смазке следует предусматривать уплотнения подшипников шпинделя и со стороны привода, чтобы исключить попадание в подшипники шпинделя смазки из коробки скоростей.
Смазка впрыскиванием используется для подшипников, работающих в особо напряженных условиях (высокие частоты вращения и температуры). Масло подается в подшипник через три-четыре сопла, расположенных по окружности подшипника, в зазор между сепаратором и кольцом подшипника под давлением до 0,4 МПа. Таким способом преодолевается воздушный барьер, создаваемый быстровращающимися частями подшипника.
Для высокоскоростных шпиндельных узлов, в первую очередь для шлифовальных головок внутришлифовальных станков, применяют смазку масляным туманом.
Вязкость масла для смазки шпиндельных узлов выбирают в зависимости от условий работы узла и системы смазки (табл. 15).
Ò à á ë è ö à 1 5
Выбор вязкости масел для смазки шпиндельных узлов
|
Скоростной параметр d·nmax ìì·1/ìèí |
|
||
Типы станков |
для подшипников |
для подшипников |
Вязкость, сСт |
|
сверхточных и осо- |
легкой и средней се- |
|||
|
|
|||
|
бо легких серий |
ðèè |
|
|
Токарные станки, |
80000 |
55000 |
24–55 |
|
токарные автоматы |
80000 |
55000 |
17–32 |
|
|
|
|||
|
240000 |
170000 |
12–23 |
|
|
|
|||
Расточные |
80000 |
55000 |
34–55 |
|
|
80000 |
55000 |
17–32 |
|
|
|
|||
Фрезерные и свер- |
160000 |
110000 |
17–32 |
|
лильные |
160000 |
110000 |
12–23 |
|
|
|
|||
Шлифовальные |
240000 |
170000 |
12–23 |
|
|
240000 |
170000 |
6–10 |
|
|
|
Если система смазки шпиндельного узла общая с приводом, то вязкость масла принимается большей. Так, при смазке погружением используют масло вязкостью 25–45 сСт, при смазке разбрызгиванием — 20–30 сСт при 50 °С.
73
В шпиндельных узлах с относительно низкими частотами вращения применяют консистентные смазки. Они особенно удобны для автономных шпиндельных узлов и вертикальных узлов. В первом случае можно не применять громоздкую систему гибких шлангов для подвода и отвода смазки к перемещающемуся шпиндельному узлу, во втором — существенно облегчается проблема уплотнения шпиндельного узла. В некоторых случаях консистентные смазки применяют с целью защиты подшипников шпинделя от влаги и загрязнений.
5.9. Уплотнения шпиндельных узлов
Уплотнения шпиндельных узлов защищают подшипники шпинделя от проникновения грязи, пыли и влаги, а также препятствуют вытеканию смазки. Для станков, работающих с обильным охлаждением зоны резания, а также с ее высокой запыленностью, ка- чество уплотнений является решающим фактором, определяющим долговечность шпиндельных узлов [3, 16].
Для быстроходных шпинделей широко применяют бесконтактные уплотнения, поскольку применение контактных уплотнений всегда связано с изнашиванием деталей, со значительным тепловыделением. Преимуществом бесконтактных уплотнений (лабиринтных, канавочных) является их способность работать при неограни- ченном пределе окружной скорости вала и при отсутствии механи- ческих потерь.
Достаточно эффективными являются лабиринтные уплотнения (табл. 16). Уплотняющее действие лабиринтного устройства основано на создании малого зазора сложной извилистой формы между вращающимися и неподвижными деталями.
Насосный эффект, характерный для лабиринтных уплотнений, может приводить к снижению давления воздуха в корпусе опоры, что вызывает запыление подшипника при остановках шпинделя. Поэтому в шпиндельных узлах, работающих в загрязненных условиях, лабиринты заполняют консистентной смазкой. Обеспечение малых зазоров требует тщательного центрирования деталей уплотнения. Лабиринтные уплотнения часто применяют в комбинации с уплотнениями других типов.
74

Разновидностью бесконтактных уплотнений являются канавочные (щелевые) уплотнения, щели концентрических проточек которых заполняют консистентной смазкой. Образуемый затвор препятствует вытеканию масла и ограничивает проникновение влаги и грязи извне. Температура разжижения смазки, заполняющей щели, должна быть выше рабочей температуры узла. Для лучшего удержания смазки канавки делают в крышке корпуса и на валу.
Ò à á ë è ö à 1 6
Размеры лабиринтных уплотнений
Находят широкое применение резиновые армированные манжеты для валов по ГОСТ 8752–79 (в ред. 1997 г.), которые надежно уплотняют узлы при окружных скоростях до 10 м/с (рис. 35).
Для предотвращения вытекания смазки из подшипникового узла эластичная кромка манжеты направляется внутрь узла к подшипнику. Для исключения осевого перемещения манжеты в посадоч- ном отверстии ставят эксцентричное упорное кольцо. При установке манжеты рядом с коническим подшипником в отверстии под подшипник необходимо предусмотреть канавки для отвода масла, нагнетаемого подшипником.
75
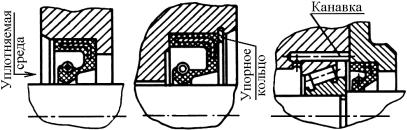
Рис. 35. Манжетные уплотнения
Для уплотнения узлов станков применяют также маслооткачи- вающие канавки, маслоотражательные кольца и комбинированные уплотнения.
5.10. Разработка системы смазки станка
Повышение быстроходности и надежности станков требует совершенствования систем смазки. Основное назначение системы смазки сводится к уменьшению потерь на трение, повышению износостойкости трущихся поверхностей и обеспечению нормально допустимой рабочей температуры. Правильно спроектированная система смазки способствует длительному сохранению первона- чальной точности станка в течение срока его эксплуатации.
Смазывать следует все трущиеся пары станков — направляющие, подшипники, передачи, шарнирные соединения и т. д. Система смазки должна обеспечивать подвод необходимого количества смазочного материала к трущимся парам, его распределение по всем рабочим поверхностям, очистку масла. Она должна содержать контрольно-регулирующие и уплотняющие устройства.
Описание системы смазки в пояснительной записке должно включать:
–обоснование принятой системы смазки;
–расчеты, связанные с определением количества необходимой смазки и производительности насоса;
–обоснование выбора насоса и регулирующей аппаратуры;
–схему смазки станка.
6. ТЕХНОЛОГИЧНОСТЬ КОНСТРУКЦИЙ УЗЛОВ СТАНКОВ
6.1. Общие сведения
Технологичность конструкции изделия (ТКИ) определена ГОСТ 14.205–83 (в ред. 1989 г.) как совокупность свойств конструкции изделия, определяющих ее приспособленность к достижению оптимальных затрат при производстве, техническом обслуживании и ремонте для заданных показателей качества, объема выпуска и условий выполнения работ.
Обеспечение технологичности изделий — важная функция подготовки производства, включающая комплекс мероприятий по управлению технологичностью и совершенствованию условий выполнения работ. ТКИ является динамически изменяющимся качеством, так как связана с большим количеством внешних по отношению к изделию переменных факторов, например, с объемом выпуска, состоянием технологической базы производящих и эксплуатирующих предприятий, организацией производства и т. п. [8, 17].
Технологичность конструкции специфицируемого изделия рассматривают относительно всего изделия, учитывая технологич- ность составных частей, сборочных единиц, требований техниче- ских условий по проведению испытаний, монтажу вне предпри- ятия-изготовителя, техническому обслуживанию и ремонту.
Виды технологичности по областям проявления, факторы, определяющие требования к технологичности, и виды оценок представлены на рис. 36.
Главными факторами, определяющими требования к технологичности конструкции изделия, являются: вид изделия, объем выпуска и тип производства. Вид изделия определяет главные конструктивные и технологические признаки, обуславливающие основные требования к технологичности конструкции; объем выпуска
èтип производства определяют степень технологического оснащения, механизации и автоматизации технологических процессов
èспециализации производства, влияющих на обеспечение технологичности изделий.
77

Рис. 36. Виды технологичности
Оценка ТКИ может быть двух видов: качественной и количественной.
Качественная оценка характеризует технологичность конструкции обобщенно на основании опыта исполнителя-разработчика. Например, такая оценка может быть сделана в отношении принципиальной возможности формообразования поверхности, в отношении возможности применения нормализованного обрабатывающего или контрольного инструмента, возможности достижения заданной твердости поверхности термической обработкой и др. Качественная сравнительная оценка вариантов конструкции применяется, когда осуществляется выбор лучшего конструктивного решения, но не требуется определения степени различия технологич- ности сравниваемых вариантов.
Количественная оценка ТКИ выражается системой показателей, численное значение которых характеризует степень удовлетворения требований к технологичности конструкции.
78
Качественная оценка при сравнении вариантов конструкции в процессе проектирования изделия предшествует количественной и определяет целесообразность последней, которая создает предпосылки для планомерного улучшения технологичности изделий.
Сравнение вариантов конструкции и отработку на технологич- ность осуществляют по базовым показателям. Базовый показатель ТКИ — это показатель, принятый за исходный при оценке технологичности. Технологичной считается конструкция, значения показателей технологичности которой соответствуют базовым показателям или превосходят их. Под отработкой конструкции на технологичность понимают комплекс мероприятий по обеспечению необходимого уровня технологичности конструкции изделия по установленным показателям.
Номенклатуру показателей технологичности, методику определения, а также их базовые значения указывают в техническом задании на разработку изделия. Номенклатура показателей зависит от стадии разработки. Количество показателей должно быть минимальным, но достаточным для оценки технологичности.
Уровень технологичности конструкции изделия представляет собой показатель технологичности, выражаемый отношением зна- чения показателя технологичности данного изделия к значению соответствующего базового показателя технологичности.
В соответствии с ГОСТ 14.201–83 (в ред. 1989 г.) отработка конструкции изделия на технологичность является неотъемлемой составной частью комплекса работ по обеспечению технологичности. Отработка конструкции изделия на технологичность производится совместно разработчиками конструкторской и технологиче- ской документации, предприятиями-изготовителями изделия и представителями заказчика. Ответственными исполнителями отработки конструкции на технологичность являются разработчики конструкторской документации.
Показатели технологичности при совместной работе конструкторов и технологов играют роль единого критерия в оценке технологичности [8]. На рис. 37 приведена классификация показателей ТКИ. Рекомендуемый перечень показателей в зависимости от вида изделия и стадии разработки конструкторской документации приведен в прил. 1 ГОСТ 14.201.
79

Рис. 37. Классификация показателей технологичности
Рис. 38. Анализ конструкции изделия при выборе показателей технологичности. Нумерация соответствует приведенной на рис. 34
80