
Расчет и конструирование многоскоростных станочных приводов
..pdf
|
|
|
|
|
|
|
|
|
|
|
|
Ò à á ë è ö à 1 7 |
||
|
|
|
Технологический анализ чертежа детали |
|
|
|
|
|||||||
|
|
|
|
|
|
|
|
|
|
|
|
|
|
|
|
|
|
|
|
|
Фактор технологического процесса |
|
|
|
|
||||
|
|
|
|
|
|
|
|
|
|
|
|
|
|
|
|
|
|
|
|
Êîí- |
Терми- |
|
|
|
|
|
|
|
|
|
|
Âèä çà- |
Âèä |
После- |
центра- |
ческая |
Âèä |
Метод |
Выбор |
Ðåæè- |
|
|
|
Квали- |
|
|
опера- |
äîâà- |
öèÿ è |
èëè |
оконча- |
Приме- |
|
|
|||||
Конструктивный признак де- |
готови- |
обеспе- |
техно- |
ìû îá- |
Оснаст- |
Обору- |
ôèêà- |
|||||||
тали, объем выпуска |
тельней |
öèè îá- |
òåëü- |
диффе- |
термо- |
òåëü- |
чения |
логиче- |
работ- |
няемый |
äîâà- |
öèÿ èñ- |
||
|
|
|
|
|
|
|
||||||||
|
|
работ- |
ность |
ренциа- |
õèìè- |
íîé îá- |
инстру- |
êà |
||||||
|
|
опера- |
точно- |
ñêèõ |
êè ðåçà- |
íèå |
полни- |
|||||||
|
|
öèè |
êè ðåçà- |
опера- |
öèÿ |
ческая |
работ- |
ñòè |
áàç |
íèåì |
ìåíò |
|
|
телей |
|
|
íèåì |
öèé |
опереа- |
îáðà- |
êè |
|
|
|
|||||
|
|
|
|
|
|
|
|
|
|
|||||
|
|
|
|
|
öèé |
ботка |
|
|
|
|
|
|
|
|
|
|
|
|
|
|
|
|
|
|
|
|
|
|
|
Материал |
|
+ |
– |
– |
– |
+ |
+ |
– |
– |
+ |
+ |
– |
– |
– |
Общая конфигурация |
+ |
+ |
+ |
+ |
– |
– |
– |
+ |
– |
+ |
+ |
+ |
– |
|
Порядок простановки раз- |
– |
– |
+ |
+ |
– |
– |
+ |
+ |
– |
– |
+ |
– |
– |
|
меров |
|
|
|
|
|
|
|
|
|
|
|
|
|
|
Точность: |
|
|
|
|
|
|
|
|
|
|
|
|
|
|
размеров поверхностей |
– |
+ |
+ |
+ |
– |
+ |
+ |
– |
+ |
+ |
– |
+ |
+ |
|
формы поверхностей |
– |
+ |
+ |
– |
+ |
+ |
– |
– |
– |
+ |
+ |
+ |
+ |
|
относительного |
распо- |
– |
– |
+ |
+ |
+ |
– |
– |
+ |
– |
– |
+ |
– |
+ |
ложения поверхностей |
|
|
|
|
|
|
|
|
|
|
|
|
|
|
Шероховатость |
поверх- |
– |
– |
– |
– |
– |
+ |
– |
– |
+ |
+ |
– |
– |
+ |
ностей |
|
|
|
|
|
|
|
|
|
|
|
|
|
|
|
|
|
|
|
|
|
|
|
|
|
|
|
|
|
81
82
Î ê î í ÷ à í è å ò à á ë . 1 7
|
|
|
|
|
Фактор технологического процесса |
|
|
|
|
||||
|
|
|
|
|
|
|
|
|
|
|
|
|
|
|
|
|
|
Êîí- |
Терми- |
|
|
|
|
|
|
|
|
|
Âèä çà- |
Âèä |
После- |
центра- |
ческая |
Âèä |
Метод |
Выбор |
Ðåæè- |
|
|
|
Квали- |
|
опера- |
äîâà- |
öèÿ è |
èëè |
оконча- |
Приме- |
|
|
|||||
Конструктивный признак де- |
готови- |
обеспе- |
техно- |
ìû îá- |
Оснаст- |
Обору- |
ôèêà- |
||||||
тали, объем выпуска |
тельней |
öèè îá- |
òåëü- |
диффе- |
термо- |
òåëü- |
чения |
логиче- |
работ- |
няемый |
äîâà- |
öèÿ èñ- |
|
|
|
|
|
|
|
|
|||||||
|
работ- |
ность |
ренциа- |
õèìè- |
íîé îá- |
инстру- |
êà |
||||||
|
опера- |
точно- |
ñêèõ |
êè ðåçà- |
íèå |
полни- |
|||||||
|
öèè |
êè ðåçà- |
опера- |
öèÿ |
ческая |
работ- |
ñòè |
áàç |
íèåì |
ìåíò |
|
|
телей |
|
íèåì |
öèé |
опереа- |
îáðà- |
êè |
|
|
|
|||||
|
|
|
|
|
|
|
|
|
|||||
|
|
|
|
öèé |
ботка |
|
|
|
|
|
|
|
|
|
|
|
|
|
|
|
|
|
|
|
|
|
|
Структура поверхностно- |
+ |
– |
+ |
– |
+ |
+ |
– |
– |
+ |
+ |
– |
– |
+ |
ãî ñëîÿ |
|
|
|
|
|
|
|
|
|
|
|
|
|
Твердость поверхности |
– |
– |
+ |
– |
+ |
+ |
– |
– |
+ |
+ |
– |
+ |
– |
Герметичность стенок |
+ |
– |
– |
– |
– |
– |
– |
– |
– |
– |
– |
– |
– |
Магнитные и электриче- |
+ |
– |
– |
– |
+ |
– |
– |
– |
– |
– |
– |
– |
– |
ские свойства |
|
|
|
|
|
|
|
|
|
|
|
|
|
Покрытие |
– |
– |
+ |
+ |
+ |
+ |
– |
+ |
– |
– |
– |
– |
– |
Объем выпуска |
+ |
+ |
+ |
+ |
– |
– |
+ |
– |
– |
+ |
+ |
+ |
+ |
|
|
|
|
|
|
|
|
|
|
|
|
|
|
Примечание. Знак «+» означает сильное влияние конструктивного признака на фактор технологического процесса, знак «–» — слабое влияние конструктивного признака на фактор технологического процесса или отсутствие влияния.
Отработку конструкции на технологичность начинают с ее технологического анализа. При анализе учитывают большое число конструктивных признаков изделия (табл. 17). Последовательность анализа конструкции при выборе показателей технологичности показана на рис. 38.
Высокий уровень технологичности детали формируется, в ча- стности, за счет того, что конструктор предусматривает возможность использования при ее изготовлении типовых технологиче- ских решений. Например, стандартизация элементов конструкции — канавок для выхода инструмента, радиусов закругления, уклонов и тому подобных элементов — приводит к снижению затрат на подготовку соответствующего технологического инструмента и другой оснастки.
|
|
|
Ò à á ë è ö à |
1 8 |
|||
Требования к технологичности конструкции детали |
|
||||||
|
|
|
|
|
|
|
|
|
|
Сфера проявления эффекта |
|
||||
Содержание требования |
|
|
Процес- |
Техниче- |
Ремонт |
||
ÊÏÏ |
ÒÏÏ |
ñû èç- |
ñêîå îá- |
èçäå- |
|||
|
|||||||
|
готов- |
служи- |
|||||
|
|
|
|
ëèÿ |
|||
|
|
|
ления |
вание |
|
||
|
|
|
|
|
|||
Конструкция детали должна состоять из стан- |
+ |
+ |
+ |
+ |
|
+ |
|
дартизированных и унифицированных элемен- |
|
|
|
|
|
|
|
тов или быть стандартизированной в целом |
|
|
|
|
|
|
|
Физико-химические и механические свойст- |
– |
+ |
+ |
+ |
|
+ |
|
ва материала детали, ее форма и размеры |
|
|
|
|
|
|
|
должны соответствовать требованиям техно- |
|
|
|
|
|
|
|
логии изготовления (включая процессы уп- |
|
|
|
|
|
|
|
рочнения, коррозионной защиты и пр.), хра- |
|
|
|
|
|
|
|
нения и транспортирования |
|
|
|
|
|
|
|
Требования точности размеров, формы и от- |
– |
+ |
+ |
– |
|
+ |
|
носительного расположения поверхностей |
|
|
|
|
|
|
|
должны быть экономически и конструктивно |
|
|
|
|
|
|
|
обоснованы |
|
|
|
|
|
|
|
Параметры баз (точность, шероховатость) де- |
– |
+ |
+ |
– |
|
+ |
|
тали должны обеспечивать достаточную точ- |
|
|
|
|
|
|
|
ность ее установки при обработке и контроле |
|
|
|
|
|
|
|
Конструкция детали должна обеспечивать |
– |
+ |
+ |
– |
|
– |
|
возможность применения типовых техноло- |
|
|
|
|
|
|
|
гических процессов ее изготовления |
|
|
|
|
|
|
Примечание. Знак «+» означает, что эффект проявляется, знак «–» — отсутствие эффекта.
83
Общие требования к технологичности конструкции деталей и сфера проявления эффекта при их выполнении приведена в табл. 18.
Технологичность конструкции станка — это совокупность свойств, заложенных в нем при проектировании и позволяющих получить наиболее рациональными способами станок с высокими эксплуатационными качествами при наименьших затратах труда, средств и материалов. Конструктор должен ясно представлять технологию изготовления любой детали или узла. На всех этапах конструирования металлорежущего станка, начиная с разработки кинематической схемы до составления рабочих чертежей, необходимо учитывать требования, способствующие повышению его технологичности. Эти требования можно разделить на две группы:
1.Требования эксплуатационной технологичности, связанные
ñповышением стабильности работы, точности, прочности, жесткости, надежности, с удобствами обслуживания и ремонта.
2.Требования производственной технологичности, связанные
ñпроизводственными показателями: себестоимостью, трудоемкостью, материалоемкостью, сроками освоения серийного выпуска и др.
Процесс производства станка складывается из трех основных этапов:
–производство заготовок (литье, штамповка, прессование);
–механическая обработка деталей и узлов;
–сборка (узловая и общая), включая контроль и испытания. Одну и ту же деталь можно выполнить в различных конструк-
тивных вариантах из разных заготовок. При этом детали могут обладать одинаковыми эксплуатационными свойствами, но технология их изготовления, трудоемкость и себестоимость различны.
Технологическая себестоимость конструкции зависит от масштабов производства. Следует сравнить между собой различные варианты конструктивных решений и выбрать наиболее технологичный для заданного объема производства. При этом следует иметь в виду, что иногда требования технологичности в индивидуальном и мелкосерийном производстве противоречат требованиям крупносерийного и массового производства.
84
6.2. Показатели оценки технологичности
Оценка технологичности производится по количественным
èкачественным показателям. Количественные показатели дают более полную оценку технологичности конструкции, чем качественные, но требуют громоздких расчетов. Вследствие ограниченного объема курсового проекта основные количественные показатели технологичности (трудоемкость, материалоемкость) не могут быть определены. Поэтому можно оценивать технологичность конструкции по дополнительным количественным показателям, часть которых можно определить по сборочным чертежам и спецификациям. К дополнительным показателям относятся:
–степень нормализации деталей — определяется как отношение количества нормативных, стандартных и покупных деталей к общему количеству деталей;
–степень унификации деталей — определяется как отношение количества деталей к количеству наименований деталей;
–степень унификации геометрических размеров — выражается количеством разновидностей этих размеров.
При разработке курсового проекта следует стремиться к увели- чению числа дополнительных количественных показателей технологичности, однако определить их количественные значения можно только после завершения проекта.
Качественными показателями технологичности являются такие, как технологичность кинематической схемы и общей компоновки станка, технологичность конструкции станка при сборке
èтехнологичность конструкции деталей.
Качественные показатели технологичности позволяют выявить преимущество какого-либо конструктивного решения по уровню его соответствия ряду требований, направленных на снижение себестоимости в заданных условиях производства. К этим требованиям относят:
1)упрощение кинематической схемы и уменьшение количества деталей в конструкции;
2)уменьшение механической обработки деталей и пригонки при сборке;
3)выполнение формы деталей в соответствии с теми способами получения заготовок и механической обработки, которые дают наименьшую себестоимость при заданных масштабах производства;
85
4) рациональное назначение точности обработки и шероховатости обработанных поверхностей.
Качественная оценка технологичности конструктивных решений производится на всех этапах проекта, начиная с разработки кинематической схемы.
6.3.Технологичность кинематической схемы
èобщей компоновки станка
Кинематическая схема станка является основанием для разработки конструкции станка и его узлов. Поэтому рациональная разработка кинематической схемы позволяет уменьшить трудоемкость и материалоемкость станка.
Лучшим из ряда вариантов кинематической схемы при равноценных эксплуатационных качествах является тот, который имеет меньшую длину кинематических цепей, т. е. содержит меньшее количество зубчатых колес, валов, рычагов, гидравлической и электрической аппаратуры и требует более простого оформления корпуса. Сокращение длины кинематических цепей достигается применением отдельных двигателей для каждой цепи, заменой нескольких зубчатых передач одной червячной, при передаче движения на большие расстояния — применением ременной или цепной передачи и т. д.
После выбора оптимального варианта кинематическая схема конструктивно разбивается на отдельные узлы. Эти узлы присоединяются к станине станка или один к другому. Взаимное расположение узлов и присоединительные связи между ними, выполненные по плоскости, цилиндрической или профильной поверхности, определяют общую компоновку станка.
Обеспечение заданной точности расположения узлов осуществляют методами взаимозаменяемости и методами компенсации.
При первом методе сборка станка производится из взаимозаменяемых деталей и узлов, независимо изготовленных с достаточно высокой точностью. Однако если точность взаимного расположения узлов очень высока, а масштаб производства небольшой, то метод взаимозаменяемости является экономически нецелесообразным. В этом случае применяют методы компенсации, при которых
86

требуемая точность взаимного расположения узлов обеспечивается пригонкой, подбором деталей, выверкой или дополнительной обработкой «по месту» при сборке.
От принятого метода обеспечения точности взаимного расположения узлов зависят тип и конструкция присоединительных связей. Поэтому станок разделяют на узлы с учетом предполагаемого метода обеспечения точности.
Конструкции коробок скоростей и подач различных станков, разрабатываемые в курсовых проектах, выполняются в виде отдельных узлов, присоединяемых к станине. Например, при установке передней (шпиндельной) бабки на станине токарного станка необходимо обеспечить параллельность оси вращения шпинделя направляющим станины в вертикальной и горизонтальной плоскостях.
В первом варианте (рис. 39, à) передняя бабка базируется на станине по горизонтальной плоскости I и плоскостям призмы II, III. Необходимая параллельность оси шпинделя и направляющих станины обеспечивается пригонкой поверхностей I, II, III корпуса бабки. Точная установка бабки в горизонтальной и вертикальной плоскостях затруднена, так как пригонка по поверхностям II и III изменяет положение корпуса бабки одновременно в обеих плоскостях.
Рис. 39. Варианты базирования шпиндельной бабки
87

Во втором варианте (рис. 39, á) базирование бабки производится по горизонтальной (Ià è Iá) и вертикальной плоскости П. Пригонка по одной плоскости не нарушает параллельности оси шпинделя
êнаправляющим станины в другой плоскости.
Âтретьем варианте (рис. 39, â) требуемая параллельность в горизонтальной плоскости обеспечивается регулировкой. С этой целью
êоснованию передней бабки крепят две планки 1, в боковые отверстия которых ввинчены регулировочные винты 2 с контргайками. Параллельность в вертикальной плоскости обеспечивается пригонкой.
Четвертый вариант (рис. 39, ã) отличается тем, что регулировка бабки в горизонтальной плоскости производится ее поворотом с помощью пары регулировочных болтов с контргайками относительно оси пальца, запрессованного в станине.
По жесткости два первых варианта являются равноценными, но второй менее трудоемкий. Третий и четвертый варианты более экономичны при выверке, но имеют меньшую жесткость стыков.
Рис. 40. Варианты соединения корпусных деталей
Подвижные соединения корпусных деталей с помощью направляющих должны обеспечивать надежный контакт поверхностей. Более технологичным является такое соединение, в котором контактирующая поверхность не имеет ступеней. Так, в направляющих типа «ласточкин хвост» очень трудно достигнуть плотного прилегания поверхностей по плоскости À (рис. 40). Конструкция будет технологич- ной, если между этими поверхностями предусмотреть зазор.
6.4. Технологичность отливок
Значительное количество деталей станков изготовляется методами литья. Это различные корпусные коробчатые детали открытого и закрытого типов и мелкие детали (крышки, фланцы, шкивы, маховики, рычаги и др.).
88

Конструкция отливки должна обеспечивать беспрепятственное удаление модели из формы без применения отъемных частей моделей.
Поверхность разъема моделей следует выполнять по плоскости, положение которой должно обеспечивать удобную формовку.
Для свободного удаления модели без повреждений формы необходимо предусматривать литейные уклоны в пределах 0,5–3° на плоскостях, перпендикулярных к плоскости разъема.
В корпусных деталях соседние поверхности, подлежащие обработке, следует располагать на одном уровне, выше смежных черновых поверхностей (объединять в один прилив). Высота приливов не должна превышать толщины стенки. Толщина стенок отливки должна быть по возможности равномерной. Это обеспечивает благоприятные условия охлаждения отливки, предотвращает появление внутренних напряжений, коробления и трещин. При литье в песчаные формы толщину стенок отливок определяют по графикам (рис. 41) в зависимости от приведенного габаритного размера детали N:
N 2L B H , 3
ãäå L, Â, Í — соответственно длина, ширина и высота отливки в метрах.
Толщина внутренних стенок назначается на 20 % меньше наружных из-за замедленного отвода тепла.
Рис. 41. Графики для определения толщины стенок отливок: à — из серого чугуна; á — из углеродистой стали
89
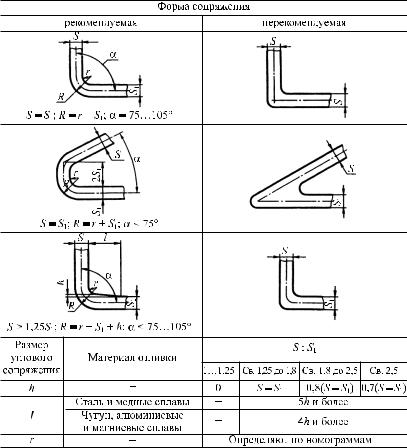
Во избежание образования усадочных раковин и трещин стен- |
ки различной толщины 1 è 2 следует соединять плавным переход- |
ным участком длиной l = 4(1 – 2). Сопряжения стенок в углах де- |
тали должны иметь плавные переходы. Рекомендуемые для приме- |
нения в конструкциях форма и размеры угловых сопряжений литых |
деталей приведены в табл. 19. |
Ò à á ë è ö à 1 9 |
Форма и размеры угловых сопряжений литых деталей |
90 |