
Расчет и конструирование многоскоростных станочных приводов
..pdf
|
|
Ò à á ë è ö à 7 |
||
Грузоподъемность и быстроходность |
|
|||
подшипников основных исполнений |
|
|||
|
|
|
|
|
|
Условное |
Грузоподъ- |
Предельная |
|
Тип подшипника |
обозначе- |
частота вра- |
||
емность |
||||
|
íèå |
щения, мин–1 |
||
Шариковый |
|
|
|
|
радиальный сферический |
0000 |
1* |
1* |
|
сферический двухрядный |
1000 |
0,8 |
0,9 |
|
Роликовый |
|
|
|
|
с короткими цилиндрическими роликами |
2000 |
1,5 |
1 |
|
сферический двухрядный |
3000 |
2,0 |
0,7 |
|
Шариковый радиально-упорный |
36000 |
1,2 |
1 |
|
Роликовый конический: |
|
|
|
|
однорядный |
7000 |
2,0 |
0,7 |
|
двухрядный |
97000 |
3,8 |
0,6 |
|
четырехрядный |
77000 |
7,2 |
– |
|
Шариковый упорный |
8000 |
– |
0,3 |
*За единицу приняты радиальная грузоподъемность и предельная частота вращения радиальных однорядных подшипников 000, имеющих такие же радиальные размеры.
В схеме â применена установка радиальных или радиаль- но-упорных подшипников враспор. Вал зафиксирован в обоих направлениях. Для компенсации температурных удлинений и погрешностей линейных размеров между наружным кольцом и крышкой подшипника при сборке предусматривают осевой зазор à = 0,15…1 ìì, èëè à = 0,0015l, ãäå l — расстояние между опорами. Установка подшипников враспор отличается простотой и позволяет выполнить корпус со сквозной расточкой, без буртиков и специальных упоров.
Íà ðèñ. 21, à, á показаны фиксирующие опоры с применением шариковых радиальных подшипников; â, ã, ä, å — с применением шариковых радиально-упорных; æ, ç — роликовых радиаль- но-упорных подшипников; è — двухрядного роликового с внутренним дистанционным кольцом.
51
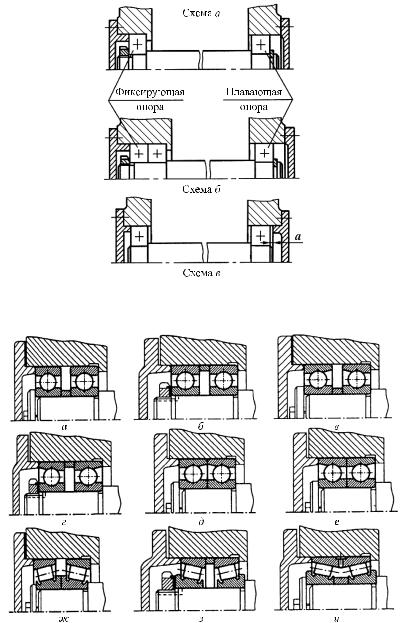
Рис. 20. Способы фиксирования валов
Рис. 21. Варианты фиксирующих опор
52

При сборке узла подшипники необходимо регулировать для получения минимального (примерно нулевого) зазора между телами качения и желобами колец. Регулирование следует выполнять при установившемся тепловом режиме.
Íà ðèñ. 21, à, â, æ показано регулирование подшипников осевым перемещением наружных колец путем подбора прокладок, прижимаемых крышками. Регулирование перемещением внутренних колец с помощью гаек показано на рис. 21, á, ã, ç.
Íà ðèñ. 21, ä, å, è показана установка подшипников с предварительным натягом. Предварительный натяг может быть создан сошлифовкой торцов соответствующих колец, установкой металли- ческих прокладок между кольцами, применением колец разной толщины. Указанные способы показаны на рис. 22. Применение предварительного натяга повышает жесткость опор, подшипники могут работать без дополнительного регулирования.
В станкостроении, особенно для шпиндельных опор, широко применяют радиально-упорные подшипники нерегулируемых типов с предварительным натягом.
Рис. 22. Способы создания предварительного натяга
Рис. 23. Радиально-упорные подшипники исполнений: à — 236000; á — 236000Ê; â — 336000; ã — 436000
53
Ò à á ë è ö à 8
Схемы комплектации и типы сдвоенных подшипников
Обозначение |
Óãîë |
Схема комплектации |
|
|
|
|
||
òèïà ïîä- |
контакта |
|
Примечание |
|
||||
шипников |
° |
|
подшипников |
|
|
|
|
|
|
|
|
|
|
|
|
||
236000 |
12 |
|
|
|
Наружные кольца обращены друг к дру- |
|||
246000 |
26 |
|
|
|
гу широкими торцами |
|
|
|
|
|
|
|
|
|
|
||
266000 |
36 |
Î |
|
|
|
|
|
|
|
|
|
|
|
|
|
||
236000Ê |
15 |
|
|
Комплект |
Внутренник |
кольца |
обращены |
äðóã |
|
|
|
|
|
|
|||
|
|
двусторонне- |
к другу узкими торцами |
|
||||
|
|
|
|
|
||||
336000 |
12 |
|
|
го осевого |
Наружные кольца обращены друг к дру- |
|||
|
|
|
||||||
346000 |
26 |
|
|
действия |
гу узкими торцами |
|
|
|
|
|
|
|
|
||||
|
|
|
|
|
|
|
||
366000 |
36 |
Õ |
|
|
|
|
|
|
|
|
|
|
|
|
|
||
336000Ê |
15 |
|
|
|
Внутренние |
кольца |
обращены |
äðóã |
|
|
|
к другу широкими торцами |
|
||||
|
|
|
|
|
|
|||
43600 |
12 |
|
|
|
Наружные кольца обращены друг к дру- |
|||
446000 |
26 |
|
|
Комплект од- |
гу разноименными торцами |
|
||
|
|
ностороннего |
|
|
|
|
||
466000 |
36 |
Ò |
|
|
|
|
|
|
|
осевого дей- |
|
|
|
|
|||
|
|
|
|
|
|
|||
|
|
|
|
|
|
|
|
|
436000Ê |
15 |
|
|
ствия |
Внутренние |
кольца |
обращены |
äðóã |
|
|
|
к другу разноименными торцами |
|
||||
|
|
|
|
|
|
Примером могут служить сдвоенные шариковые радиаль- но-упорные подшипники по ГОСТ 832–78, предназначенные для фиксации валов в радиальном и осевом направлениях (рис. 23 и табл. 8).
Одним из распространенных типов подшипников, применяемых для установки в шпиндельные узлы станков, являются радиальные двухрядные роликоподшипники типа 3182000 (рис. 24). Они обладают высокой несущей способностью, жесткостью и быстроходностью. Наличие конического отверстия у внутреннего кольца (конусность 1:12) позволяет тонко регулировать радиальный зазор в подшипнике осевым перемещением кольца относительно конической шейки шпинделя.
Иная модификация описанных подшипников — тип 4162000. Они отличаются тем, что гладкая (без буртов) дорожка качения выполнена на внутреннем кольце. Такое изменение конструкции позволяет уменьшить радиальные габариты шпиндельного узла.
54

На рис. 25 показаны специальные под- |
|
|
шипники, применяемые для шпиндельных |
|
|
узлов. Сдвоенные упорно-радиальные шари- |
|
|
коподшипники типа 178000 состоят из двух |
|
|
внутренних колец, двух комплектов шариков |
|
|
с сепараторами и имеют дистанционное |
|
|
кольцо, предназначенное для создания пред- |
Рис. 24. Подшипники |
|
варительного натяга, что облегчает сборку |
типов 3182000 |
|
è 4162000 |
||
шпиндельного узла. Направление восприни- |
||
|
маемых сил — осевое в обе стороны и радиальное. Несущая способность и жесткость этих подшипников
не меньше, чем обычных шариковых упорных, но они менее чувствительны к взаимному перекосу колец.
Рис. 25. Шпиндельные подшипники типов: à — 178000, á — 97000, â — 17000
Роликовые радиально-упорные двухрядные подшипники типа 97000 предназначены для восприятия комбинированных нагрузок — радиальных и двусторонних осевых. Величина допустимой радиальной нагрузки в 1,7 раза выше, чем у однорядных подшипников. Они изготовляются с заранее заданным зазором (предварительным натягом). Числа роликов в рядах подшипника отличаются на один, что способствует гашению резонансных вибраций шпинделя. Увеличенная ширина наружного кольца позволяет устанавливать подшипник без натяга, что облегчает его монтаж и демонтаж.
Конические роликоподшипники типа 17000 с широким наружным кольцом и встроенными пружинами предназначены для восприятия одновременно действующих радиальных и осевых нагрузок. Наличие пружин позволяет осуществлять постоянство предварительного натяга подшипника в собранном узле. Величина натяга
55

обеспечивается установкой нужного количества пружин. Увели- ченная ширина наружного кольца позволяет уменьшить величину возможного перекоса кольца в корпусе. Такие подшипники устанавливаются в задней опоре шпинделя в комбинации с одноили двухрядными подшипниками в передней опоре.
5.5. Компоновка коробок скоростей
Эскизную компоновку коробки рекомендуется выполнять
âмасштабе 1:1, предварительно определив типы опор валов и ориентировочно выбрав подшипники.
Развертка позволяет показать конструкцию коробки скоростей
âцелом. Все валы располагаются в одной плоскости. При этом решаются вопросы расположения групповых передач, определяются их осевые и радиальные габариты. Кроме того, необходимо показать конструкцию зубчатых колес, их фиксацию, конструкцию передвижных блоков, способы установки и регулирования подшипников. При выполнении чертежа следует продумать вопросы сборки отдельных элементов и коробки скоростей в целом.
Осевые габариты передач должны обеспечивать нейтральное положение передвижных зубчатых блоков при переключениях (рис. 26). Разность чисел зубьев соседних венцов тройного блока должна быть не менее четырех. Это условие можно обеспечить, увеличив сумму чисел зубьев групповой передачи, но увеличатся ее радиальные габариты. Можно разделить блок на двойной и одиноч- ную шестерню, усложнив управление, либо применить удлиненную конструкцию блока, что упрощает управление, но увеличивает осевые габариты передачи.
Рис. 26. Осевые габариты передач
56

Во избежание поломок колес толщина стенки между шпоноч- ным пазом и впадиной зуба должна быть больше двух модулей. Диаметр ступицы колес принимают равным 1,5…1,6 диаметра вала, длину — от 0,8 до 1,5 диаметра. Выточка в блоках зубчатых колес для выхода долбяка должна быть 5…7 мм.
Развертка коробки скоростей не дает представления о взаимном расположении валов в пространстве. Поэтому развертка коробки дополняется сверткой — поперечным разрезом, в котором показывается действительное взаимное расположение валов.
Ниже приведены некоторые рекомендации по проектированию свертки коробок скоростей металлорежущих станков.
Токарные станки. Исходной величиной при размещении валов в поперечном сечении коробки скоростей является высота центров. Для нахождения положения оси шпинделя проводят горизонтальную линию, от которой откладывают заданную высоту центров Í (ðèñ. 27).
Рис. 27. Свертка коробки скоростей
На этой высоте берут точку, представляющую собой ось шпинделя. Из этой точки радиусом начальной окружности Rí большего из колес, сидящих на шпинделе, описывают окружность. Этот радиус предопределяет высоту коробки скоростей Í1, которая должна быть не менее величины:
Í1 = Í + Rí + ñ,
57

ãäå ñ = (2,5 3)m — расстояние от начальной окружности большого колеса до верхней крышки коробки.
Высоту коробки не следует увеличивать без особых оснований, так как это приводит к удалению центра тяжести коробки от станины и создает условия для возникновения вибраций. Дальнейшее построение поперечного сечения коробки направляют вправо при условии, что органы управления будут размещены слева. Задача конструирования свертки состоит в том, чтобы валы и зубчатые колеса занимали наименьшее пространство. При этом совершенно не обязательно показывать на чертеже все зубчатые колеса, построение производится по передачам, находящимся в зацеплении.
Большое колесо, сидящее на шпинделе, соединяют с малым, сидящим на предшпиндельном валу, и находят положение оси предшпиндельного вала. На этом валу вычерчивается наибольшее зуб- чатое колесо, которое сцепляется с малым колесом следующего вала. Аналогичное построение продолжается до тех пор, пока не определятся координаты оси входного вала коробки скоростей.
Следует отметить, что не всегда сразу удается получить наиболее рациональное расположение валов относительно друг друга. При проектировании свертки коробки скоростей следует учитывать следующее:
На величину деформации шпинделя и реакцию в опорах влияет положение приводной шестерни, сцепленной с зубчатым колесом шпинделя (рис. 28). В положении I результирующая сила R,
Рис. 28. Влияние положения приводной шестерни на реакции в опорах и прогиб шпинделя
58

которая определяет величины опорных реакций в переднем и заднем подшипниках, получается как сумма силы резания Ð и силы на шестерне Q.
В положении II результирующая сила получается как разность силы резания и силы на шестерне. С точки зрения действующей силы в передней опоре положение шестерни в случае II выгоднее, так как возникающая реакция меньше. Однако с точки зрения прогиба конца шпинделя схема I более благоприятна, так как деформация конца шпинделя в этом случае меньше. Поэтому схема I чаще применяется в точных станках, а схема II — в станках для черновой обработки.
Большое значение имеет положение промежуточ- ных валов. Вариант, показанный на рис. 29 слева,
предпочтительнее, так как промежуточная шестерня втягивается в зону зацепления и жесткость системы возрастает. При угле равном 80…90°, происходит частичная компенсация радиальных и тангенциальных сил.
Необходимо стремиться получить наименьшие размеры поперечного сечения коробки. Наиболее нагруженные валы следует располагать ближе к основанию коробки, особенно в тех случаях, когда они имеют высокие частоты вращения. Низкое расположение нагруженных валов по отношению к основанию коробки снижает центр тяжести самой коробки и делает ее более устойчивой.
Для увеличения жесткости корпуса коробки скоростей желательно предусматривать дополнительные поперечные стенки. При наличии таких стенок первые валы можно сделать короткими.
При проектировании свертки необходимо учесть размещение фрикционных муфт, тормозов, механизмов переключения зубчатых колес, устройств системы смазки и т. д.
Сверлильные станки. В вертикально-сверлильных станках коробки скоростей обычно располагаются на верхней части стани-
59
ны. Для обеспечения необходимого вылета шпинделя валы располагают в одной вертикальной плоскости. При таком расположении валов образуется естественная развертка коробки.
Некоторые модели вертикально-сверлильных станков (серия Н) имеют компоновку, при которой коробка скоростей крепится к вертикальным направляющим станины. Свертка таких коробок подобна сверткам токарных станков, но следует обратить внимание на расположение фланцевого электродвигателя.
Проектирование свертки следует начинать с большего колеса на шпинделе станка, сохраняя последовательность, принятую для токарных станков.
Фрезерные станки. Коробки скоростей во фрезерных станках размещают в станине станка, и валы коробки обычно располагают в одну линию по вертикали.
После согласования с руководителем эскизной компоновки
коробки производится уточненный расчет наиболее нагруженного (предшпиндельного) вала на сложное сопротивление.
5.6. Проектирование шпиндельных узлов
Шпиндель — наиболее ответственная деталь станка, последнее звено коробки скоростей, несущее заготовку или инструмент. От него во многом зависит точность обработки, что заставляет предъявлять к шпинделю целый ряд дополнительных требований. Расчет и конструктивное оформление шпинделей имеют специфику по сравнению с обычными валами [10].
Работоспособность металлорежущих станков и точность обработки заготовок во многом определяются точностью вращения шпинделей, статической и динамической жесткостью шпиндельного узла, предельно допустимой частотой вращения, диапазоном регулирования, несущей способностью и долговечностью подшипников.
Точность вращения шпинделей зависит от точности подшипников, точности изготовления сопряженных с подшипниками деталей, от качества монтажа, качества регулировки подшипников (величины зазора, натяга) и от частоты вращения шпинделя, при которой производится обработка изделия.
Для обычных двухопорных шпиндельных узлов соотношение между биениями внутренних колец подшипников и биением цен-
60