
Расчет и конструирование многоскоростных станочных приводов
..pdf
Ò à á ë è ö à |
2 0 |
Элементы конструкции отливок |
|
|
91 |
Примеры рекомендуемого и не рекомендуемого исполнения некоторых конструктивных элементов отливок приведены в табл. 20.
Повышению технологичности способствуют выравнивание толщины стенок отливки, устранение местных скоплений металла, исключение из конструкции тонкостенных ребер, глубоких впадин и щелей.
6.5. Кованые и горячештампованные детали
Ковка и горячая штамповка применяются для изготовления стальных заготовок. Свободная ковка находит применение в единичном и мелкосерийном производстве, особенно при изготовлении крупных деталей. Детали, изготовленные свободной ковкой, должны иметь простые формы, очерченные плоскостями или цилиндрическими поверхностями, без уклонов и конусности.
Горячая штамповка применяется в серийном и крупносерийном производстве. Конфигурация деталей, штампованных на молотах или прессах в штампах, должна обеспечивать легкую выемку поковки из штампа. Плоскость разъема штампа желательно располагать по направлению двух наибольших габаритных размеров.
Для облегчения наладки штампов поверхности, прилегающие к разъему, должны иметь угол с плоскостью разъема, близкий к прямому. Все поверхности, перпендикулярные к плоскости разъема, должны иметь штамповочные уклоны, величина которых выбирается в пределах 5–12 градусов в зависимости от габаритов детали.
В конструкциях горячештампованных деталей следует избегать резкой разницы в сечениях, тонких стенок, высоких ребер и бобышек, так как это приводит к трудностям при штамповке и незаполнению формы.
6.6. Технологичность деталей при обработке резанием
Сокращение объема механической обработки является средством, значительно повышающим технологичность деталей [13]. Конструктивное оформление деталей, подлежащих обработке резанием, связано с видом заготовок. При изготовлении деталей из проката имеет место увеличенный объем срезаемого металла, так как
92

обрабатываются не только рабочие, но и свободные поверхности деталей. Снижение трудоемкости обработки достигается сокращением перепадов между диаметрами деталей (рис. 42).
Рис. 42. Примеры сокращения трудоемкости обработки
Из-за наличия заплечика (рис. 42, à) увеличивается диаметр D заготовки и повышается объем снимаемой стружки, составляющий 135 % объема готовой детали. В конструкции валика без заплечика и с уменьшенным перепадом диаметров ступенек (рис. 42, á) объем снимаемой стружки сокращается в три раза. На рис. 42, â показано дальнейшее сокращение объема обработки, достигнутое при изготовлении валика из калиброванного прутка.
Еще пример сокращения трудоемкости обработки путем изготовления шпильки из калиброванного проката показан на рис. 43, à. Конструкция гайки с кольцевым выступом (рис. 43, á) нетехнологич- на. Гайки без выступа можно изготовлять из шестигранного прутка.
Рис. 43. Крепежные детали, изготовленные из проката
В серийном производстве снижение объема обработки достигается уменьшением веса заготовок. Следует применять заготовки, близкие по форме и размерам к готовым деталям, оставляя без механической обработки все свободные поверхности.
При конструировании деталей, подлежащих механической обработке, необходимо обеспечить возможность обработки поверхностей с применением типовых технологических процессов. В кон-
93
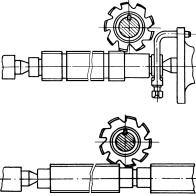
струкции деталей не следует предусматривать элементы, препятствующие свободному доступу инструментов к месту обработки или контроля.
Конструкция детали должна обеспечивать возможность обработки с одной установки всех поверхностей, связанных между собой условиями параллельности, соосности или перпендикулярности. Для этого необходимо предусматривать удобные и единые базы для установки и закрепления деталей, например в деталях типа валов — центровые отверстия.
Конструктивная форма деталей при серийном производстве должна, по возможности, обеспечивать одновременную обработку нескольких деталей.
На деталях, подвергаемых круглому шлифованию, необходимо предусматривать канавки для выхода шлифовального круга.
Примеры выполнения конструктивных элементов деталей, рекомендуемые варианты и их технологические преимущества показаны в табл. 21.
При фрезеровании шлицевых валов для закрепления поводка и выхода фрезы следует предусматривать гладкую часть (рис. 44). При этом необходимо удлинять заготовку вала или фрезеровать двойную заготовку с последующей разрезкой.
Выбор диаметра для центрирования в шлицевом соединении зависит от термообработки соединяемых деталей, так как в закаленной детали центрирующий диа-
|
метр необходимо шлифовать. |
|||
|
Крышки, закрывающие от- |
|||
|
верстия в корпусе под подшип- |
|||
|
íèêè, |
обычно |
центрируют по |
|
|
диаметру отверстия. Однако ес- |
|||
|
ли крышки предназначены для |
|||
|
осевой фиксации деталей, то це- |
|||
|
лесообразно |
применять пло- |
||
|
ñêèé |
фрезерованный |
объеди- |
|
|
ненный фланец (рис. 45). |
|||
|
Торцы зубьев передвижных |
|||
|
блоков со стороны входа в заце- |
|||
Рис. 44. Примеры фрезерования |
пление с парным зубчатым ко- |
|||
шлицевых валов |
лесом |
должны быть |
скошены |
94

95

Рис. 45. Применение объединенного фланца
и закруглены. Это облегчает попадание зуба одного колеса во впадину другого при переключениях и снижает вероятность их повреждения.
При простановке размеров нужно увязывать обрабатываемые поверхности с обрабатываемыми, а необрабатываемые — с необрабатываемыми. Исключение составляют базовые размеры, которые связывают базовые необработанные поверхности с базами механи- ческой обработки.
6.7. Технологичность конструкций при сборке
Сборка — сложный и ответственный процесс в цикле производства станков. Трудоемкость сборочных и монтажных работ составляет от 20 до 50 % общей трудоемкости. Условиями производительной и качественной сборки являются:
1)разделение станка на самостоятельные узлы, сборку, контроль и испытание которых можно выполнять параллельно;
2)уменьшение количества деталей в сборочном узле за счет выбора наиболее простой и рациональной схемы узла, за счет объединения нескольких деталей в одну технологичную;
3)уменьшение и исключение пригоночных работ при сборке путем увеличения числа взаимозаменяемых деталей и узлов или введения компенсаторов (регулировка);
4)удобство и доступность сборки, регулировки и разборки;
5)применение простых и производительных приемов сборки, удобный подход монтажного инструмента, возможность применения механизированного инструмента.
96

Особое внимание следует обращать на устранение пригоноч- ных работ, доделки деталей в процессе сборки. Пригонка требует применения слесарных операций или дополнительной станочной обработки, снижает качество сборки и лишает конструкцию взаимозаменяемости.
Технологичность сборки зависит от правильного выбора соответствующих конструктивных элементов на собираемых деталях
èузлах. Например, заходные фаски облегчают сборку. При подвижных и переходных посадках цилиндрических деталей достаточ- но сделать фаску на одной из деталей. Фаску на валу легче обработать, поэтому она предпочтительнее.
При последовательной установке нескольких деталей с натягом следует избегать посадки по одному диаметру. Необходимость перемещать детали через посадочную поверхность усложняет монтаж
èвызывает опасность повреждения поверхностей. В таких случаях целесообразно применять ступенчатые детали с последовательно возрастающим диаметром ступеней. При монтаже по двум посадоч- ным ступеням необходимо обеспечить правильную последовательность сборки, выдерживая определенную длину деталей (рис. 46).
Рис. 46. Сборка деталей с натягом
Если при сборке между торцами деталей остается зазор m, то вследствие возможного перекоса монтаж становится затруднительным. Следует также избегать одновременного входа вала в отверстия. Правильным является положение, когда вал входит в меньшее отверстие на расстояние n = 2…3 мм, достаточное для его направления.
Фиксирование деталей от осевого смещения может осуществляться гайками, позволяющими отрегулировать положение детали на валу. Это удобно при сборке, но требует нарезания резьбы на валу. Фиксацию установочными кольцами со стопорными винтами
97
следует применять при небольших осевых нагрузках в направлении кольца. Для фиксации деталей на валах и в отверстиях широко применяют стандартные наружные и внутренние концентрические и эксцентрические кольца.
Для исключения проворота деталей при передаче крутящих моментов применяют шпоночные соединения. Следует избегать применения длинных призматических шпонок, требующих пригонки при сборке. Их желательно заменять двумя сегментными, не требующими пригонки. Нежелательно применять шпоночные соединения с валом закаленных зубчатых колес, кулачковых муфт и других деталей, так как термообработка вызывает коробление их пазов и отверстий. В шлицевых отверстиях деформации от термообработки распределяются равномернее.
При передаче больших крутящих моментов применяют шлицевые соединения. Они обладают рядом преимуществ по сравнению со шпоночными. При одинаковом диаметре вала передают больший крутящий момент, обеспечивают улучшение центрирования, не требуют съемных деталей.
Центрирование шлицевых сопряжений возможно по наружному или внутреннему диаметру, а также по ширине шлицов. Наиболее технологично центрирование по наружному диаметру. Вал шлифуют, что не представляет затруднений, а отверстие протягивают. Центрирование по внутреннему диаметру следует применять только в случаях, когда закалена наружная деталь, отверстие которой необходимо шлифовать. Посадка по нецентрирующим элементам должна быть с зазором.
Следует избегать установки на один вал неподвижных и передвижных деталей (назначать посадки с натягом и с зазором). Это требует применения ступенчатой конструкции валов и увеличивает объем механической обработки.
Монтаж валов на подшипниках качения, фиксация и регулирование подшипников рассмотрены выше, в разделе «выбор и регулирование подшипников». Подшипники монтируют и демонтируют с приложением усилия только к закрепленному кольцу (внутреннему при посадке с натягом на вал и наружному при посадке с натягом в корпус). Воздействовать на другое кольцо нельзя, так как в этом случае усилие передается через тела качения и беговые дорожки, которые при этом могут быть повреждены.
98
Высоту упорных буртиков и других элементов, фиксирующих подшипники в осевом направлении, определяют с учетом условий демонтажа подшипников. Высота упорного буртика должна быть меньше толщины кольца на величину, достаточную для упора демонтажной втулки или лап съемника непосредственно в кольцо подшипника.
Для получения правильного зацепления в конической передаче необходимо обеспечить совпадение вершин начальных конусов колес, т. е. выдержать с достаточной точностью размеры в корпусе передачи и зазоры в зацеплении колес. Обеспечение этой точности за счет механической обработки значительно усложняет и удорожает производство. Поэтому во всех конструкциях следует предусматривать элементы, позволяющие регулировать зазор в зацеплении. Регулирование зацепления производится после регулирования подшипников и не должно нарушать их регулировку (должно быть по возможности автономным). Наибольшее распространение получили следующие способы регулирования зазоров в конических передачах:
1)осевое перемещение колеса по валу при помощи регулировочных гаек;
2)осевое перемещение стакана с подшипниками прижимными
èрегулировочными винтами;
3)установка регулировочных колец или полуколец под фланец стакана или под опорный торец колеса;
4)подгонка или набор по толщине компенсаторных колец. Первый и второй способы технологичны по условиям сборки
èрегулировки, но отличаются трудоемкостью изготовления самих устройств для регулирования зазора. Третий способ требует частичной разборки узла при регулировании. При четвертом способе регулирования необходимо предварительное измерение зазора между торцами колеса и сопрягаемой детали, для чего необходима предварительная сборка.
Правильное взаимное положение деталей в червячной передаче лучше обеспечивать за счет их точной механической обработки, так как регулирование пятна контакта трудоемко и неудобно. Если механической обработкой трудно обеспечить правильное зацепление, то в конструкции узла следует предусмотреть возможность осевого перемещения червячного колеса.

ПРИЛОЖЕНИЯ
Приложение 1
Ò à á ë è ö à Ï 1 . 1
Предпочтительные числа частот вращения (ГОСТ 8032–84)
Обозначение ряда
R40 |
R20 |
R10 |
R |
20 |
|
R5 |
R |
20 |
|
R |
10 |
|
|
|
|
||||||||||
|
|
|
3 |
|
|
5 |
|
3 |
|
|||
|
Значения знаменателя ряда |
|
|
|
||||||||
1,06 |
1,12 |
1,25 |
1,40 |
1,60 |
1,78 |
2 |
|
|||||
10,0 |
10,0 |
10,0 |
|
|
|
10,0 |
10,0 |
|
|
|
||
10,6 |
|
|
|
|
|
|
|
|
|
|
|
|
11,2 |
11,2 |
|
11,2 |
|
|
|
|
|
|
|
||
11,8 |
|
|
|
|
|
|
|
|
|
|
|
|
12,5 |
12,5 |
12,5 |
|
|
|
|
|
|
|
|
|
|
13,2 |
|
|
|
|
|
|
|
|
|
|
|
|
14,0 |
14,0 |
|
|
|
|
|
|
|
|
|
|
|
15,0 |
|
|
|
|
|
|
|
|
|
|
|
|
6,0 |
16,0 |
16,0 |
16,0 |
16,0 |
|
|
|
16,0 |
||||
17,0 |
|
|
|
|
|
|
|
|
|
|
|
|
18,0 |
18,0 |
|
|
|
|
|
18,0 |
|
|
|
||
19,0 |
|
|
|
|
|
|
|
|
|
|
|
|
20,0 |
20,0 |
20,0 |
|
|
|
|
|
|
|
|
|
|
21,2 |
|
|
|
|
|
|
|
|
|
|
|
|
22,4 |
22,4 |
|
22,4 |
|
|
|
|
|
|
|
||
23,6 |
|
|
|
|
|
|
|
|
|
|
|
|
25,0 |
25,0 |
25,0 |
|
|
|
25,0 |
|
|
|
|
|
|
26,5 |
|
|
|
|
|
|
|
|
|
|
|
|
28,0 |
28,0 |
|
|
|
|
|
|
|
|
|
|
|
Обозначение ряда
R40 |
R20 |
R10 |
R |
20 |
|
R5 |
R |
20 |
|
R |
10 |
|
|
|
|
||||||||||
|
|
|
3 |
|
|
5 |
|
3 |
|
|||
|
Значения знаменателя ряда |
|
|
|
||||||||
1,06 |
1,12 |
1,25 |
1,40 |
1,60 |
1,78 |
2 |
|
|||||
30,0 |
|
|
|
|
|
|
|
|
|
|
|
|
31,5 |
31,5 |
31,5 |
31,5 |
|
31,5 |
31,5 |
||||||
33,5 |
|
|
|
|
|
|
|
|
|
|
|
|
35,5 |
35,5 |
|
|
|
|
|
|
|
|
|
|
|
37,5 |
|
|
|
|
|
|
|
|
|
|
|
|
40,0 |
40,0 |
40,0 |
|
|
|
40,0 |
|
|
|
|
|
|
42,5 |
|
|
|
|
|
|
|
|
|
|
|
|
45,0 |
45,0 |
|
45,0 |
|
|
|
|
|
|
|
||
47,5 |
|
|
|
|
|
|
|
|
|
|
|
|
50,0 |
50,0 |
50,0 |
|
|
|
|
|
|
|
|
|
|
53,0 |
|
|
|
|
|
|
|
|
|
|
|
|
56,0 |
56,0 |
|
|
|
|
|
56,0 |
|
|
|
||
60,0 |
|
|
|
|
|
|
|
|
|
|
|
|
63,0 |
63,0 |
63,0 |
63,0 |
63,0 |
|
|
|
63,0 |
||||
67,0 |
|
|
|
|
|
|
|
|
|
|
|
|
71,0 |
71,0 |
|
|
|
|
|
|
|
|
|
|
|
75,0 |
|
|
|
|
|
|
|
|
|
|
|
|
80,0 |
80,0 |
80,0 |
|
|
|
|
|
|
|
|
|
|
85,0 |
|
|
|
|
|
|
|
|
|
|
|
|
100