
Конструкционные материалы. Свариваемость и сварка
.pdf4.ВЫСОКОПРОЧНЫЕ СТАЛИ
Кклассу высокопрочных сталей относятся низколегированные бейнитно-мартенситные и среднелегированные стали мартен- ситно-бейнитные с содержанием углерода от 0,12 до 0,45 %. Для большинства этих сталей характерно комплексное легирование (содержание легирующих элементов от 2,5 до 10 %), позволяющее получить стали с более высокими механическими свойствами. Необходимый комплекс служебных и технологических свойств
сталей с пределом текучести σ0,2 = 580…2000 МПа обеспечивается определенным легированием в сочетании с термической обработкой. Структура сталей формируется в процессе мартенситного и бейнитного превращений. Марки этих сталей изготавливают
восновном по техническим условиям.
Вданных сталях сочетаются высокие прочностные и пластические свойства с высокой стойкостью против перехода в хрупкое состояние. Это и определяет их широкое применение для конструкций, работающих при ударных и знакопеременных нагрузках, при низких и высоких температурах, при высоких давлениях, в агрессивных средах и т.п.
Высокопрочные стали применяются также для создания облегченных сварных конструкций. Однако не все эти стали имеют хорошую или удовлетворительную свариваемость: чем больше содержание легирующих элементов в стали, включая углерод, тем хуже свариваемость. Это связано с увеличением вероятности обра-
зования хрупкой структуры мартенсита в сварном соединении в результате термических циклов сварки.
Как правило, при содержании углерода более 0,3 % повышается склонность стали к перегреву, закалке, образованию холодных и горячих трещин в сварном соединении и образованию пор в сварном шве. Для предупреждения этих явлений необходимы усложняющие технологический процесс специальные приемы, поэтому
71
в ряде случаев при выборе марки высокопрочной стали для изготовления сварных конструкций более целесообразно выбрать менее прочную сталь, с меньшим содержанием углерода, но более технологичную при сварке, с учетом надежности и долговечности сварного соединения.
Все марки высокопрочных сталей можно разделить на три основные группы: низколегированные бейнитно-мартенситные стали, среднелегированные мартенситно-бейнитные стали и низкоуглеродистые мартенситные стали.
4.1. НИЗКОЛЕГИРОВАННЫЕ БЕЙНИТНО-МАРТЕНСИТНЫЕ СТАЛИ
4.1.1.Состав и свойства сталей
Книзколегированным бейнитно-мартенситным относят ста-
ли, имеющие предел текучести σ0,2 = 580…780 МПа. Данные стали выплавляют мартеновским, кислородно-конвекторным или индукционным способом. В ряде случаев осуществляется дополнительная обработка жидкого металла синтетическими шлаками, обдувкой аргоном или его электрошлаковый переплав, что позволяет ограничить содержание в стали вредных примесей. Основные марки низкоуглеродистых бейнитно-мартенситных сталей, их химический состав указаны в табл. 4.1.
Оптимальные механические свойства и достаточно высокая стойкость против хрупкого разрушения при отрицательных температурах приобретаются после термической обработки: закалки или нормализации и последующего высокого отпуска. Механические свойства сталей приведены в табл. 4.2.
Хорошее сочетание свойств имеют стали, содержащие 0,4–0,6 % молибдена и 0,002–0,006 % бора в сочетании с добавками других ле-
гирующих элементов. При соответствующей термической обработке обеспечивается получение стабильной бейнитной или мартенситной структурывлистовомпрокатедо100 мм. Куказаннымсталямотносятся
72
Таблица 4 . 1
|
|
Химический состав бейнитно-мартенситных сталей |
|
|
|
||||||||
|
|
|
|
|
|
|
|
|
|
|
|
|
|
Маркастали |
|
|
|
Содержаниехимическихэлементов, вес. % |
|
|
|
||||||
C |
Si |
Mn |
P, S |
Cr |
Ni |
Mo |
Al |
Cu |
V |
Nb |
Прочие |
||
|
|||||||||||||
13ХГМРБ |
0,1–0,16 |
0,17–0,37 |
0,9–0,12 |
≤ 0,035 |
0,9–0,13 |
≤ 0,03 |
0,3–0,4 |
0,02–0,08 |
< 0,3 |
– |
0,01–0,03 |
0,001– |
|
0,004 B |
|||||||||||||
|
|
|
|
|
|
|
|
|
|
|
|
|
|
14Х2ГМРБ |
0,1–0,16 |
0,17–0,37 |
0,9–0,12 |
≤ 0,035 |
1,1–1,5 |
≤ 0,03 |
0,3–0,4 |
0,02–0,08 |
< 0,3 |
– |
0,01–0,04 |
0,001– |
|
0,004 B |
|||||||||||||
|
|
|
|
|
|
|
|
|
|
|
|
|
|
12Г2СМФАЮ |
0,09–0,15 |
0,20–0,40 |
1,3–1,7 |
≤ 0,035 |
– |
≤ 0,03 |
0,15–0,25 |
0,05–0,10 |
< 0,3 |
0,07–0,15 |
– |
0,015– |
|
0,03 N2 |
|||||||||||||
|
|
|
|
|
|
|
|
|
|
|
|
||
12ГН2МФАЮ |
0,09–0,16 |
0,30–0,50 |
0,9–0,12 |
≤ 0,035 |
0,2–0,5 |
1,4–1,75 |
0,15–0,25 |
0,05–0,10 |
< 0,3 |
0,05–0,10 |
– |
0,02– |
|
0,03 N2 |
|||||||||||||
|
|
|
|
|
|
|
|
|
|
|
|
||
12ХГН2МБФАЮ |
0,09–0,16 |
0,30–0,50 |
0,9–0,13 |
≤ 0,005 |
0,5–0,9 |
1,4–1,7 |
0,3–0,4 |
0,05–0,10 |
0,5–1,0 |
0,05–0,10 |
0,02–0,06 |
0,02– |
|
0,03 N |
|||||||||||||
|
|
|
|
|
|
|
|
|
|
|
|
2 |
|
12ХГН2МФБДАЮ |
0,09–0,16 |
0,20–0,50 |
0,6–0,11 |
≤ 0,035 |
0,6–0,9 |
1,4–1,75 |
0,4–0,6 |
0,03–0,08 |
0,5–1,0 |
0,05–0,10 |
0,02–0,06 |
0,015– |
|
0,03 N |
|||||||||||||
|
|
|
|
|
|
|
|
|
|
|
|
2 |
|
12ХГН2МФДРА |
0,1–0,14 |
0,15–0,35 |
0,95–0,12 |
≤ 0,025 |
0,8–1,2 |
1,7–2,1 |
0,5–0,7 |
0,02–0,05 |
0,7–1,0 |
0,08–0,14 |
– |
B ≤ 0,004 |
73
Таблица 4 . 2 Механические свойства бейнитно-мартенситных сталей
Маркастали |
Толщина, |
σ0,2, |
σв, |
δ, |
KCU (*KCV), Дж/см2 при |
||
мм |
МПа |
МПа |
% |
–40 °С |
–70 °С |
||
|
|||||||
13ХГМРБ |
10–50 |
590 |
690 |
14 |
39 |
29 |
|
14Х2ГМРБ |
10–50 |
588 |
686 |
14 |
39 |
– |
|
12Г2СМФАЮ |
10–32 |
588 |
686 |
14 |
34 |
– |
|
12ГН2МФАЮ |
16–40 |
588 |
686 |
14 |
– |
29 |
|
12ХГН2МФБАЮ |
16–40 |
736 |
834 |
12 |
– |
29 |
|
12ХГН2МФБДАЮ |
20–40 |
785 |
883 |
15 |
– |
29 |
|
12ХГН2МФДРА |
4–20 |
980 |
1078 |
10 |
29 |
– |
стали марок 13ХГМРБ, 14Х2ГМРБ и др. Для сварных конструкций чаще всего применяются безникелевые стали с содержанием молибдена
0,15–0,5 %, бора 0,002–0,005 %. Например, сталь 12Г2СМФАЮ, обла-
дая высокими прочностными свойствами и достаточной пластичностью, несколькоуступаютстали14Х2ГМРБпохладостойкости.
Эффективно введение в высокопрочную низколегированную сталь небольших количеств азота (0,002–0,03 %) и нитридообразующих элементов – алюминия, ванадия и ниобия. Наличие мелкодисперсных нитридов в стали способствует уменьшению склонности к росту аустенитного зерна при сварке. По механическим свойствам и хладостойкости нитридосодержащие высокопрочные стали превосходят стали такого же химического состава, изготовленные по обычной технологии. На практике хорошо себя зарекомендовала нитридосодержащая высокопрочная сталь марки 12ГН2МФАЮ.
4.1.2. Свариваемость низкоуглеродистых бейнитно-мартенситных сталей
Основными показателями свариваемости низкоуглеродистых бейнитно-мартенситных сталей являются:
–сопротивляемость сварных соединений холодным трещинам;
–сопротивляемостьсварныхсоединенийхрупкомуразрушению;
74
– механические свойства зоны термического влияния, которые связаны с фазовыми превращениями и структурными изменениями в стали при сварке.
На основе этих показателей определяют технологические и конструктивные условия получения сварных соединений, удовлетворяющих эксплуатационным требованиям к сварной конструкции. Оценку характера структурных превращений в стали при воздействии термического сварочного цикла производят по термокинетическим (анизотермическим) диаграммам непрерывного распада аустенита. Обычно ориентируются по скорости охлаждения в диапазоне температур 600–500 °С (W6/5) и времени охлаждения от 800 до 500 °С.
На рис. 4.1 приведены термокинетические диаграммы для некоторых низкоуглеродистых бейнитно-мартенситных сталей.
Так, например, для стали 14Х2ГМР оптимальным считается диапазон скоростей охлаждения W6/5 = 35…0,5 град/с, когда превращение аустенита происходит в мартенситной и бейнитной областях (рис. 4.1, а). При увеличении скорости охлаждения W6/5 > 18 град/с образуется низкоуглеродистый мартенсит с твердостью HV 3800 МПа. Уменьшение скорости охлаждения приводит к развитию бейнитного превращения, повышению температуры его начала и снижению твердости. При замедленных скоростях охлаждения (W6/5 ≈ 0,8 град/с) повышается температура бейнитного превращения и увеличиваются размеры ферритных игл.
По приведенным термокинетическим диаграммам хорошо видны отличия в фазовых превращениях при термических циклах сварки различных сталей.
Скорость охлаждения (рис. 4.1, в, 4.2) заметно влияет на величину временных напряжений в температурной области фазового γ→α-превращения (см. рис. 4.2). Различие в кинетике структурных превращений приводит также к изменению величины остаточных растягивающих напряжений в образцах. Например, с повышением скорости охлаждения W6/5 в интервале 0,6–50 град/с у стали 14ХГН2МДАФБ они уменьшаются от 240 до 150 МПа.
75
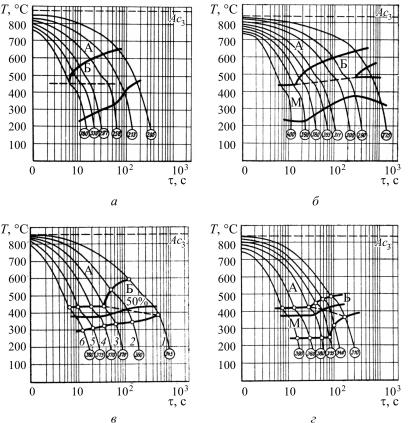
Рис. 4.1. Термокинетические диаграммы распада аустенита стали 14Х2ГМР (а), 12ГН2МФАЮ (б), 14ХГН2МДАФБ (в)
и12ХГН2МФБДАЮ (г): цифры в кружках обозначают твердость HV10; 1–6 – разные скорости охлаждения
76
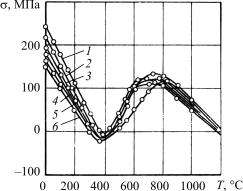
Рис. 4.2 Изменение временных напряжений при охлаждении защемленных образцов из стали 14ХГН2МДАФБ (нагрев-охлаждение)
Низколегированные бейнитно-мартенситные стали имеют ограниченное содержание С, Ni, Si, S и Р, поэтому образования горячих трещин в сварных швах можно избежать при соблюдении режимов сварки и правильном применении присадочных материалов.
Наиболее распространенным и опасным дефектом сварных соединений из низколегированных бейнитно-мартенситных сталей являются холодные трещины в зоне термического влияния и металле шва, возникающие в закаленной структуре под влиянием водорода
исварочных напряжений. При сварке многослойных швов могут образовываться поперечные трещины, пересекающие металл шва
иметалл околошовной зоны, а также внутренние продольные трещины металла корневых швов. В угловых и стыковых соединениях листового проката сталей толщиной более 12 мм возможно образование ламелярных трещин, располагающихся в основном металле параллельно границе сплавления. Они служат очагами разрушения сварных соединений.
Высокая сопротивляемость сварных соединений низкоуглеродистых легированных сталей образованию трещин обеспечивается в случае, когда содержание диффузионного водорода в на-
77
плавленном металле не превышает 3,5–4,0 мл/100г. Более высокая концентрация водорода приводит к снижению сопротивляемости соединений образованию холодных трещин.
Для предотвращения образования холодных трещин при сварке различных сталей рекомендуется скорости охлаждения зоны термического влияния в интервале температур минимальной устойчивости аустенита600–500 °Свыдерживатьв следующихдиапазонах:
1)W6/5 = 13…18 град/с – 14Х2ГМР, 13ХГМРБ, 14ХГ2САФД, 12ГН2МФАЮ;
2)W6/5 = 7…12 град/с – 14ХГНМДАФБРТ и 14ХГН2МДАФБ;
3)W6/5 = 4 … 6 град/с – 12ХГН2МФБДАЮ.
Для предотвращения образования холодных трещин при сварке металла большой толщины рекомендуется предварительный подогрев:
–при толщине более 20 мм до температуры 80–100 °С;
–при толщине более 40 мм до температуры 100–150 °С.
Температуру предварительного подогрева можно снизить до 80–100 °С, если незамедлительно после сварки производить нагрев сварных соединений до температуры в интервале 150–200 °С (отдых). Времянагреваназначаетсяизрасчета1,5–2 минна1 ммтолщины соединения.
При температуре окружающего воздуха менее 0 °С температура предварительного подогрева повышается на 20–50 °С. Подогрев сварных соединений наиболее эффективен, если его осуществлять равномерно по всей длине с двух сторон от разделки кромок на расстоянии не менее 100 мм. В табл. 4.3 и 4.4 приведены рекомендуемые температура предварительного подогрева и погонная энергия сварки сталей 14Х2ГМР и 12ХГН2МФБДАЮ соответственно.
Предварительный подогрев замедляет скорость остывания при температуре ниже 300 °С и способствует более полному удалению водорода из наплавленного металла. При этом возрастает стойкость соединений против образования холодных трещин.
78

Таблица 4 . 3 Рекомендуемые температура предварительного подогрева и погонная энергия сварки стали 14Х2ГМР
Форма |
Темпе- |
|
|
Погоннаяэнергияq/v, кДж/см, притолщинеметаллаδ, мм |
|
|
||||||
поперечного |
ратура |
|
|
|
|
|||||||
сечения |
подогрева |
|
|
|
|
|
|
|
|
|
|
|
6 |
8 |
10 |
16 |
20 |
25 |
30 |
36 |
|
40 |
50 |
||
кромок |
Т, °С |
|
|
|
|
|
|
|
|
|
|
|
|
20 |
≤ 10 |
≤ 16 |
≤ 23 |
≤ 33 |
≤ 40 |
– |
– |
– |
|
– |
– |
|
100 |
≤ 9 |
≤ 15 |
≤ 20 |
≤ 30 |
≤ 35 |
– |
– |
– |
|
– |
– |
|
|
|
|
|
|
|
|
|
|
|
|
|
|
20 |
6,3–13,3 |
8,3–16,2 |
11,6–19,5 |
16,2–24,1 |
17,9–32,4 |
22,9–38,3 |
– |
– |
|
– |
– |
|
100 |
– |
– |
– |
13,3–25,0 |
18,7–30,0 |
20,0–37,4 |
21,6–47,8 |
– |
|
– |
– |
|
150 |
– |
– |
– |
– |
13,3–23,7 |
15,8–29,1 |
18,7–36,6 |
20,0–41,0 |
25,8–49,9 |
26,2–51,1 |
|
|
|
|
|
|
|
|
|
|
|
|
|
|
79
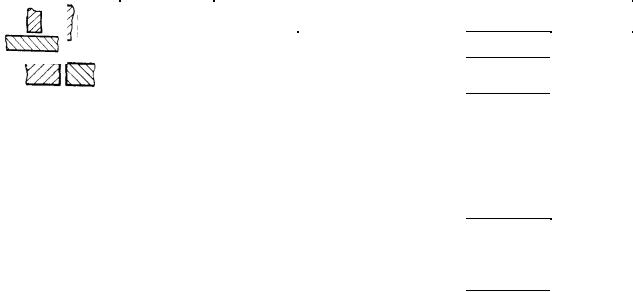
80
Таблица 4 . 4
Рекомендуемые температура предварительного подогрева и погонная энергия сварки стали 12ХГН2МФБДАЮ
Формапоперечного |
Температура |
|
Погоннаяэнергияq/v, кДж/см, притолщинеметаллаδ, мм |
|
||||
сечениякромок |
подогреваТ, °С |
|
|
|
|
|
|
|
16 |
|
20 |
24 |
30 |
|
40 |
||
|
|
|
|
|||||
|
|
|
|
|
|
− |
|
|
|
20 |
15–34 |
|
20–42 |
− |
|
− |
|
|
100 |
12–25 |
|
15–30 |
− |
− |
|
− |
|
|
|
|
|
|
|
|
|
|
20 |
17–35 |
|
20–44 |
− |
− |
|
− |
|
100 |
13–28 |
|
15–34 |
16–42 |
17–48 |
|
18–62 |
|
150 |
− |
|
− |
12–33 |
14–45 |
|
12–50 |
|
|
|
|
|
|
|
|
|
|
20 |
17–35 |
|
20–42 |
− |
− |
|
− |
|
100 |
13–28 |
|
14–34 |
19–38 |
21–48 |
|
25–60 |
|
150 |
− |
|
− |
14–32 |
18–39 |
|
20–50 |
|
|
|
|
|
|
|
|
|
|
20 |
20–43 |
|
26–47 |
− |
− |
|
− |
|
100 |
15–34 |
|
19–43 |
23–47 |
27–60 |
|
30–70 |
|
150 |
− |
|
− |
18–42 |
21–50 |
|
22–60 |
|
|
|
|
|
|
|
|
|