
Конструкционные материалы. Свариваемость и сварка
.pdfОбразование горячих трещин
Склонность к горячим трещинам сварных швов высокопрочных сталей определяется следующими факторами:
–химическим составом металла шва, от которого зависит межкристаллитная прочность и пластичность в опасном температурном интервале хрупкости (ТИХ);
–величиной и скоростью нарастания растягивающих напряжений и, соответственно, деформаций;
–величиной первичных кристаллов;
–формой сварочной ванны (шва), от которой зависит направление роста столбчатых кристаллитов относительно направления растягивающих напряжений.
Элементами, способствующими образованию горячих трещин в сварном шве, являются прежде всего сера, затем углерод, фосфор, кремний, медь, никель (при 2,5–4,5 %), а также примеси
металлов с низкой температурой плавления (свинец, олово, цинк). Элементами, повышающими стойкость швов против трещин и нейтрализующими действие серы, являются марганец, титан, хром и особенно ванадий.
Измельчение и дезориентирование структуры металла шва, предупреждение развития грубой дендритной структуры с ликвационными зонами возможно за счет соответствующего легирования и приемов сварки, повышающих сопротивляемость сварных швов образованию горячих трещин.
При сварке листов встык наиболее опасными местами появления трещин являются начало и конец шва. Приварка технологических планок, частые прихваточные швы, заварка концевых участков шва в направлении от центра к краю свариваемых листов уменьшают опасность образования горячих трещин.
Снижение растягивающих напряжений при охлаждении шва в ТИХ и тем самым предупреждение горячих трещин может быть достигнуто путем уменьшения числа и сосредоточения швов при конструировании, выбора оптимальной формы разделки кромок, устранения излишней жесткости узлов и другими мерами. Эффек-
91
тивным средством является предварительный подогрев. Температура подогрева колеблетсяот 150 до500 °Св зависимостиот величиныСэкв (эквивалентного содержания углерода), конструкции, свариваемой толщины и др. Для снижения растягивающих напряжений в ТИХ сварку целесообразно выполнять методами, обеспечивающими наибольшую проплавляющую способность стали при наименьшей погонной энергии.
Образованию горячих трещин также способствует наличие концентраторов напряжений, поэтому применение остающихся подкладок, сварка в замок, швы с непроваром являются нежелательными. Наиболее предпочтительна сварка встык с полным проваром.
Образование холодных трещин
Рассматриваемая группа материалов относится к закаливающимся сталям. В сварных соединениях под действием термического цикла сварки могут образоваться хрупкие и малопластичные участки в зонах, нагреваемых выше точки Ас3. Распад аустенита при охлаждении в условиях сварочного термического цикла начинается при более низких температурах, при этом в структуре наряду с мартенситом остается нестабильный остаточный аустенит. Такие стали при повышенной концентрации водорода склонны к образованию холодных трещин.
В среднеуглеродистых мартенситно-бейнитных сталях наиболее часто холодные трещины образуются в швах и зоне термического влияния, свариваемых проволокой, состав которой близок к составу основного металла. Холодные трещины возникают как при температуре 250 °С и ниже, в интервале температур образования мартенсита, так и после полного остывания сварного изделия, спустя некоторое время после сварки (замедленное разрушение). Чем ниже температура распада аустенита, грубее структура мартенсита, выше уровень сварочных и структурных напряжений, тем вероятнее образование холодных и закалочных трещин. С увеличением толщины свариваемой стали вероятность образования трещин возрастает.
92
Образование холодных трещин при сварке закаливающихся сталей уменьшается в следующих случаях:
–при выборе способа и технологии сварки, обеспечивающих отсутствие грубодендритной структуры, закалочной структуры литого металла шва, минимальном перегреве ЗТВ и минимальных растягивающих напряжениях при остывании шва;
–при сварке с применением подогрева, уменьшающего вероятность образования закалочных структур;
–при снижении содержания водорода в сварных соединениях;
–при отпуске после сварки.
Для обеспечения более равноосной зернистой структуры металла шва и предупреждения чрезмерного развития зоны перегрева необходимо применять:
–специальную присадочную проволоку и флюсы;
–многослойную сварку;
–колебательныедвиженияэлектродапримногослойной сварке;
–импульсные режимы сварочного тока (при сварке небольших толщин);
–подбор оптимальных режимов сварки.
Метод сварки также влияет на склонность сварных соединений к образованию холодных замедленных трещин: чем более концентрированный источник тепла применяется при сварке, тем меньше эта склонность.
Для снижения растягивающих напряжений необходимо обеспечить при сварке изделий свободную усадку с помощью:
–рациональной конструкции;
–порядка наложения сварных швов;
–применения приспособлений, создающих сжимающие напряжения в сварных соединениях при охлаждении.
Снижение содержания водорода в металле шва обеспечивается:
–применением осушенных защитных газов;
–применением низководородистых электродов;
–прокаливанием их и флюсов перед сваркой.
93
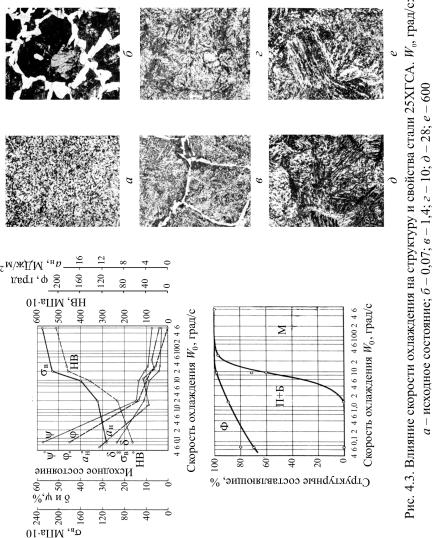
94
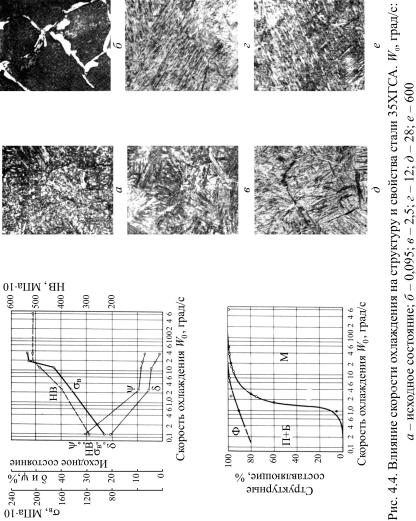
95
При сварке в защитных газах их влажность необходимо контролировать. Эквивалентное содержание углерода влияет на критическое содержание водорода в металле. Чем выше содержание углерода и другихэлементов, понижающих температуру мартенситного превращения, темприменьшемсодержанииводородаобразуютсятрещины.
В тех случаях, когда сварная конструкция применяется в термически упрочненном состоянии и последующая термическая обработка не проводится, при выборе оптимальных режимов сварки среднелегированных сталей необходимо не только создать условия для предотвращения образования горячих и холодных трещин, но и получить требуемый комплекс механических свойств сварного соединения. Определяющим фактором получения желаемой структуры исвойств металла шва и зоны термического влияния является скорость охлаждения сварного соединения. Для оценки структурных превращенийв сталипривоздействиитермическогосварочногоцикла можно воспользоваться термокинетическими (анизотермическими) диаграммами распада аустенита. На рис. 4.3 и 4.4 показано влияние скорости охлаждения сварного соединения на структурный состав, микроструктуру и механические свойства для сталей 25ХГСА
и35ХГСА соответственно.
4.2.3.Технология сварки мартенситно-бейнитных сталей
Сварка покрытыми электродами
Для дуговой сварки среднеуглеродистых мартенситнобейнитных сталей применяют различные электроды в зависимости от прочности и пластичности свариваемой стали, а также условий эксплуатации сварных конструкций (табл. 4.15). Для сварки сталей высокой и средней прочности при толщинах более 2,0 мм рекомендуются электроды типа Э100, ВИ10-6 (Св-18ХМА) и типа Э85, НИАТ-ЗМ (Св-08А) (ГОСТ 9467–75). Для получения соединений с высокой стойкостью к образованию холодных трещин, а также швов с высокими пластическими свойствами и малой чувствитель-
96
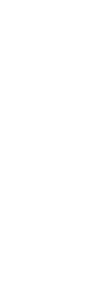
ностью к концентраторам напряжений рекомендуется применять электроды со стержнем, обеспечивающим аустенитную структуру шва. Эти электроды обеспечивают высокую работоспособность конструкций в условиях динамических и ударных нагрузок при прочности металла шва 600 МПа. Аустенитные электроды применяются для соединений, не подвергающихся термической обработке после сварки.
Таблица 4 . 1 5
Электроды для дуговой сварки конструкционных сталей и механические свойства металла шва
|
|
|
|
|
|
|
|
|
|
|
|
|
|
|
|
|
|
|
|
|
Электрод |
|
Механические |
|
Марка |
|
|
|
|
|
Термическая |
|
свойства, неменее |
||||||||||||||||
|
|
|
|
|
|
|
||||||||||||||||||
стали |
|
|
|
|
|
|
обработка |
Тип |
ГОСТ |
σв, |
KCU, |
|||||||||||||
|
|
|
|
|
|
|
|
|
|
|
|
|
|
|
|
|
|
|
|
|
МПа |
Дж/см2 |
||
25ХГСА |
|
|
|
|
|
Закалка |
|
иотпуск |
|
|
|
|
|
Э70 |
9467–75 |
700 |
60 |
|||||||
30ХГСА |
|
|
|
|
|
после |
|
сварки |
|
|
|
|
|
Э85 |
9467–75 |
800 |
50 |
|||||||
|
|
|
|
|
наσв ≤ |
900 МПа |
||||||||||||||||||
25ХГСА |
|
|
|
|
|
Закалка |
|
иотпуск |
|
|
|
|
|
Э85 |
|
|
|
|||||||
30ХГСА |
|
|
|
|
|
после |
|
сварки |
|
|
|
|
|
9467–75 |
800 |
50 |
||||||||
|
|
|
|
|
наσв ≥ |
900 МПа |
|
|
|
|
||||||||||||||
25ХГСА |
|
|
|
Сваркавупрочнен- |
|
|
|
Э-10Х20Н9Г6С |
10052–75 |
600 |
90 |
|||||||||||||
|
|
|
ном |
состоянии |
без |
|||||||||||||||||||
|
|
|
|
|
|
|
|
|||||||||||||||||
|
|
|
|
|
|
|
|
|||||||||||||||||
|
|
|
|
|
|
|
|
|
|
|
|
|
|
|
|
|
|
|
|
|
|
|
|
|
30ХГСА |
последующей |
терми- |
|
Э-11X15Н25М6АГ2 |
10052–75 |
600 |
90 |
|||||||||||||||||
|
|
|
|
|
|
|
||||||||||||||||||
|
|
|
|
ческойобработки |
|
|
|
|
||||||||||||||||
12Х2НВФА |
|
|
|
|
|
Закалка |
|
иотпуск |
|
|
|
Э85 |
|
0,90 σв |
60 |
|||||||||
|
|
|
|
|
|
|
|
|
|
|
|
|
|
|
|
|
основного |
|
||||||
23Х2НВФ |
|
|
|
|
|
после |
|
сварки |
|
|
|
|
|
|
Э100 |
9467–75 |
50 |
|||||||
|
|
|
|
|
наσв ≥ |
|
|
1000 |
|
МПа |
|
|
|
|
|
|
металла |
|
||||||
|
|
|
|
|
|
|
|
|
|
|||||||||||||||
12Х2НВФА |
|
|
|
Сваркавупрочнен- |
|
|
Э85 |
9467–75 |
900 |
60 |
||||||||||||||
|
|
|
ном |
состоянии |
без |
|||||||||||||||||||
|
|
|
|
|
|
|
|
|||||||||||||||||
|
|
|
|
|
|
|
|
|
|
|
|
|
|
|
|
|
|
|
|
|
|
|
|
|
23Х2НВФ |
|
|
|
последующей |
терми- |
|
Э-10Х20Н9Г6С, |
10052–75 |
600 |
90 |
||||||||||||||
|
|
|
|
ческойобработки |
|
|
|
|
Э-1IX15Н25М6АГ2 |
|||||||||||||||
|
|
|
|
|
|
|||||||||||||||||||
|
|
|
|
|
|
|
|
|
|
|||||||||||||||
30ХГСНА |
|
Закалкаиотпускпо- |
|
Э85, Э100, |
|
900 |
50 |
|||||||||||||||||
|
|
|
|
слесваркинаσв = |
9467–75 |
|||||||||||||||||||
|
|
|
|
|
|
|
||||||||||||||||||
|
= |
(1600 ± 1800) МПа |
Э150 |
|
1400 |
40 |
||||||||||||||||||
|
|
Сваркавупрочнен- |
Э-10Х20Н9Г6С, |
|
|
|
||||||||||||||||||
30ХГСНА |
|
|
номсостояниибез |
Э-11X15Н25М6АГ2 |
10052–75 |
600 |
90 |
|||||||||||||||||
|
последующейтерми- |
Э-06Х19Н11Г2М2 |
|
|
|
|||||||||||||||||||
|
|
|
|
ческойобработки |
|
|
|
|
97
Сварка в защитных газах
При выборе присадочного материала (электродной проволоки) для дуговой сварки в среде защитных газов следует руководствоваться табл. 4.16:
–первый слой выполняют без присадки с полным проваром кромок стыка и обратным формированием;
–второй – с поперечными низкочастотными колебаниями электрода и механической подачей присадочной проволоки.
–возможен и третий слой с поперечными колебаниями электрода без присадочной проволоки со стороны обратного формирования на небольшом режиме для обеспечения плавного перехода от шва к основному металлу.
Высокое качество сварных соединений толщиной 3–5 мм достигается при аргонодуговой сварке неплавящимся электродом. Для увеличения проплавляющей способности дуги при аргонодуговой сварке сталей применяют активирующие флюсы. Применение активирующих флюсов повышает проплавляющую способность дуги
в1,5–2 раза, что обеспечивает увеличение производительности процесса, повышение качества, возможность исключения разделки кромок и многопроходной сварки при толщинах 8–10 мм.
Для сварки сталей рекомендуется применять флюс, представляющий смесь компонентов (SiO2, NaF, TiO2, Ti, Сr2O3). Эффективно
применение активирующих флюсов при аргонодуговой сварке неплавящимся электродом среднеуглеродистых сталей, подвергнутых электрошлаковому и электронно-лучевому переплавам. При сварке этих сталей для обеспечения заданного провара требуется увеличение сварочного тока по сравнению с металлом открытой выплавки. Активирующие флюсы рекомендуется применять преимущественно при сварке механизированным способом для получения равномерной глубины проплавления. В этом случае рекомендуется применять неплавящийся электрод из наиболее стойких марок активированного вольфрама ВТ15 или СВИ-1. Для обеспечения плавного перехода от шва к основному металлу при выполнении поверхностных слоев шва применяют сочетание активирующих флюсов и поперечных низкочастотных колебаний электрода.
98

Таблица 4 . 1 6
Присадочные материалы и механические свойства сварных соединений при дуговой сварке неплавящимся электродом в защитных газах
|
|
Всредеинертных |
Вуглекислом |
σв, МПа |
KCU, |
||
Марка |
Термическая |
газов |
газе |
Дж/см2 |
|||
стали |
обработка |
|
|
|
|
|
|
Марка |
ГОСТ |
Марка |
неменее |
|
|||
|
|
проволоки |
илиТУ |
ГОСТ2246–70 |
|
||
|
|
|
|
||||
25XГСА |
Закалкаиотпуск |
Св-18ХМА |
ГОСТ2246–70 |
Св-18ХМА, |
0,9 σв основного |
50 |
|
после сварки |
Св-18ХГС |
металла |
|||||
|
|
|
|
||||
30ХГСА |
Сваркавтермическиоб- |
Св-18ХГС |
ГОСТ2246–70 |
Св-08ГСМТ |
0,9 σв основного |
40 |
|
12Х2НВФА |
Св-18ХМА |
ГОСТ2246–70 |
Св-08ГСМТ |
||||
|
работанномсостояниибез |
|
|
|
металла |
|
|
23Х2НВФА |
Св-18ХМА |
ГОСТ2246–70 |
Св-08ГСМТ |
|
|||
|
|
||||||
|
последующейтермиче- |
|
|
|
|
|
|
|
Св-08Х21Н10Г6, |
|
|
|
|
||
23Х2НВФА |
скойобработки |
Св-08Х20Н9Г7Т, |
ГОСТ2246–70 |
Св-08Х20Н9Г7Т |
600 |
90 |
|
|
|
Св-10Х16Н25АМ6 |
|
|
|
|
|
|
|
|
|
|
|
|
|
12Х2НВФА |
Закалка+ отпуск |
Св-18ХМА |
ГОСТ2246–70 |
Св-08ГСМТ |
0,9 σв основного |
60 |
|
|
послесварки |
|
|
||||
23Х2НВФА |
металла |
40 |
|||||
|
|
|
|||||
|
Закалка+ отпуск |
|
ЧМТУЦНИИЧМ |
|
0,9 σв основного |
|
|
30Х2ГСНВМА |
послесваркина |
Св-20Х2ГСНВМ |
– |
– |
|||
582–61 |
металла |
||||||
|
σв = (1700 ± 100) МПа |
|
|
|
|||
|
|
|
|
|
|
||
|
Закалка+ отпуск |
|
ЧМТУЦНИИЧМ |
|
(0,9…0,95) σв |
|
|
42Х2ГСНМА |
послесваркина |
Св-20ХСНВФАВД |
– |
основного |
– |
||
|
σв = (2000 ± 100) МПа |
|
1–91–67 |
|
металла |
|
|
|
|
|
|
|
99
Сварные соединения, выполненные электродами типа Э70–Э150, после сварки подвергаются высокому отпуску при 600–650 °С в течение 2 ч, не позднее чем через 30 мин. Затем производится окончательнаятермическаяобработкапорежимуосновногометалла.
Ряд ответственных конструкций из термически упрочненных среднеуглеродистых мартенситно-бейнитных сталей сваривают проволокой Св-08Х20Н9Г7Т в углекислом газе как в автоматическом, так и полуавтоматическом режиме. Прочность металла шва достигает 600 МПа и представляет конструктивную равноценность сварного соединения основному металлу при высокой их надежности. Последующая термическая обработка сварного соединения при этом не проводится.
Сварка под флюсом
Автоматическая сварка под флюсом рекомендуется для прямолинейных и кольцевых (диаметром 80 мм и выше) соединений изделий с толщиной свариваемого металла свыше 4 мм. Не рекомендуется при сварке применять подкладные кольца и замковые соединения, так как они снижают надежность конструкции при эксплуатации. Вместо подкладных колец первый слой целесообразно выполнять аргонодуговой сваркой на весу.
Электродную проволоку и флюс для сварки среднелегированных мартенситно-бейнитных сталей выбирают в соответствии с табл. 4.17. Для предотвращения пористости и наводораживания швов флюсы перед сваркой необходимо прокаливать, чтобы их влажность не превышала 0,1 % для стекловидных флюсов и 0,05 % для пемзовидных. Это достигается нагревом стекловидных флюсов до 350–400 °С, а пемзовидных до 400–500 °С с выдержкой 2–3 ч. Максимальная температура нагрева под прокалку применяемых флюсов не должна превышать 650–700 °С во избежание окисления компонентов флюса и его спекания.
В случае сварки жестких узлов проволоками типа Св-18ХМА, Св-18ХГС, Св-08ГСМТ, а также соединений сталей 30ХГСА, 30ХГСНА, 40ХГСН3МА и др. большой толщины применяют подогрев 150–300 °С. Непосредственно после сварки во всех случаях не-
100