
Конструкционные материалы. Свариваемость и сварка
.pdfНизколегированные стали обычно легируют медью в количестве 0,3 %. В таких пределах медь повышает коррозионную стойкость, особенно к атмосферной коррозии, несколько улучшая прочностные характеристики. Такая концентрация меди не сказывается отрицательно на свариваемости стали и не вызывает явления красноломкости, проявляющегося при большом ее содержании и требующего введения элементов-нейтрализаторов (например, никеля в соотношении 1 : 2 в сталях типа ХСНД).
По содержанию S и P эти стали можно отнести к качественным сталям. В последние годы расширяется производство и применение рафинированных сталей посредством электрошлакового, вакуумного переплава сталей, обработанных в ковше синтетическими шлаками с целью снижения содержания серы в их составе для повышения сопротивляемости образованию слоистых (ламинарных) трещин.
Введение в сталь различных легирующих элементов позволило создать серию марок сталей с достаточно высокой прочностью, хорошей свариваемостью и низким порогом хладноломкости. Упрочнение при легировании достигается вследствие повышения устойчивости аустенита и получения более дисперсных продуктов распада аустенита (феррито-карбидной смеси), а также за счет твердорастворного упрочнения. В зависимости от легирующих элементов различают марганцовистые (14Г, 19Г, 09Г2, 14Г2), кремнемарганцовистые (09Г2С, 10Г2С, 17Г1С), хромокремнемарганцовистые (10ХСНД, 15ХСНД) и другие стали.
Как правило, низколегированные стали поставляют в горячекатаном состоянии с феррито-перлитной структурой. Химический состав сталей и нормы механических свойств для проката различных видов и сечений определяются ГОСТ 19281–73, ГОСТ 19282–73, ГОСТ 6713–91 и ГОСТ 550–75. В табл. 1.1 приведены основные данные о составе и гарантируемых свойствах некоторых наиболее типичных низколегированных сталей.
11
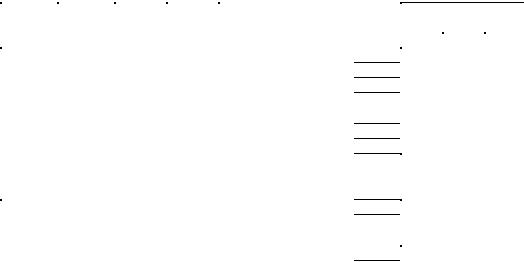
12
|
|
|
|
|
|
|
|
|
|
|
|
|
Таблица |
1 . 1 |
|||
|
Химический состав и механические свойства низколегированных сталей |
|
|
|
|
||||||||||||
|
|
|
|
|
|
|
|
|
|
|
|
|
|
|
|
||
Марка |
|
Содержаниехимическихэлементов, мас. % |
|
|
Механическиесвойства |
|
|||||||||||
|
|
|
|
|
|
|
|
|
|
δ, |
|
KCU, МДж/м2, |
|||||
|
|
|
|
|
|
|
|
σв, |
σт, |
|
|||||||
стали |
C |
|
Si |
Mn |
Cr |
Ni |
|
Cu |
|
|
приТ, °С |
|
|||||
|
|
МПа |
МПа |
% |
|
|
|
||||||||||
|
|
|
|
|
|
|
|
|
|
+20 |
|
–40 |
|
–70 |
|||
|
|
|
|
|
|
|
|
|
|
|
|
|
|
|
|||
09Г2 |
≤0,12 |
|
0,17–0,37 |
1,40–1,80 |
≤0,30 |
≤0,30 |
|
≤0,30 |
450 |
310 |
21 |
|
– |
|
0,30 |
|
– |
|
|
|
|
|
|
|
|
|
|
|
21 |
|
|
|
|
|
|
09Г2Д |
≤0,12 |
|
0,17–0,37 |
1,40–1,80 |
≤0,30 |
≤0,30 |
|
0,15–0,3 |
450 |
310 |
|
– |
|
0,30 |
|
– |
|
|
|
|
|
|
|
|
|
|
|
|
21 |
|
|
|
|
|
|
10Г2 |
0,07–0,15 |
|
0,17–0,37 |
1,20–1,60 |
≤0,30 |
≤0,30 |
|
≤0,30 |
425 |
265 |
|
– |
|
0,12 |
|
– |
|
|
|
|
|
|
|
|
|
|
|
|
21 |
|
|
|
|
|
|
14Г2 |
0,12–0,18 |
|
0,17–0,37 |
1,20–1,60 |
≤0,30 |
≤0,30 |
|
≤0,30 |
460 |
330 |
|
– |
|
0,30 |
|
– |
|
|
|
|
|
|
|
|
|
|
|
|
21 |
|
|
|
|
|
|
09Г2С |
≤0,12 |
|
0,50–0,80 |
1,30–1,70 |
≤0,30 |
≤0,30 |
|
≤0,30 |
480 |
330 |
|
0,6 |
|
0,35 |
|
0,3 |
|
|
|
|
|
|
|
|
|
|
|
|
21 |
|
|
|
|
|
|
09Г2СД |
≤0,12 |
|
0,50–0,80 |
1,30–1,70 |
≤0,30 |
≤0,30 |
|
0,15–0,3 |
480 |
330 |
|
0,6 |
|
0,35 |
|
0,3 |
|
|
|
|
|
|
|
|
|
|
|
|
21 |
|
|
|
|
|
|
10Г2С1 |
≤0,12 |
|
0,80–1,10 |
1,30–1,65 |
≤0,30 |
≤0,30 |
|
≤0,30 |
490 |
340 |
|
0,6 |
|
0,30 |
|
0,25 |
|
|
|
|
|
|
|
|
|
|
|
|
21 |
|
|
|
|
|
|
10Г2С1Д |
≤0,12 |
|
0,80–1,10 |
1,30–1,65 |
≤0,30 |
≤0,30 |
|
0,15–0,3 |
490 |
340 |
|
0,6 |
|
0,30 |
|
0,25 |
|
|
|
|
|
|
|
|
|
|
|
|
21 |
|
|
|
|
|
|
16ГС |
0,12–0,18 |
|
0,40–0,70 |
0,90–1,20 |
≤0,30 |
≤0,30 |
|
≤0,30 |
490 |
320 |
|
0,6 |
|
0,3 |
|
0,25 |
|
17ГС |
0,14–0,20 |
|
0,40–0,60 |
1,0–1,4 |
≤0,30 |
≤0,30 |
|
≤0,30 |
500 |
340 |
23 |
|
– |
|
0,35 |
|
– |
|
|
|
|
|
|
|
|
|
|
|
21 |
|
|
|
|
|
|
17Г1С |
0,15–0,20 |
|
0,40–0,60 |
1,15–1,60 |
≤0,30 |
≤0,30 |
|
≤0,30 |
490 |
355 |
|
– |
|
0,29 |
|
– |
|
|
|
|
|
|
|
|
|
|
|
|
22 |
|
|
|
|
|
|
14ХГС |
0,11–0,16 |
|
0,40–0,70 |
0,90–1,30 |
0,50–0,80 |
≤0,30 |
|
≤0,30 |
500 |
350 |
|
– |
|
0,35 |
|
– |
|
|
|
|
|
|
|
|
|
|
|
|
19 |
|
|
|
|
|
|
10ХСНД |
≤0,12 |
|
0,80–1,10 |
0,50–0,80 |
0,60–0,90 |
0,50–0,80 |
|
0,40–0,60 |
540 |
400 |
|
– |
|
0,4 |
|
0,3 |
|
15ХСНД |
0,12–0,18 |
|
0,40–0,70 |
0,40–0,70 |
0,60–0,90 |
0,30–0,60 |
|
0,20–0,40 |
500 |
350 |
21 |
|
– |
|
0,30 |
|
0,30 |
Примечания: 1. Указаны механические свойства при толщине проката до 20 мм. 2. Во всех сталях содержание P ≤ 0,035, S ≤ 0,040, N ≤ 0,008.
По сравнению с низкоуглеродистыми сталями низколегированные имеют предел текучести в 1,25–1,6 раза выше ипревосходят их по ударной вязкости, в особенности при отрицательных температурах. Так, для низколегированных сталей гарантируется ударная вязкость при температуре –40 °С, а для некоторых и при –70 °С (для углеродистых сталей ударная вязкость гарантируется только при –20 °С).
Механические свойства низколегированных сталей сильно зависят от толщины проката. Так, гарантируемые значения предела текучести стали 09Г2С следующим образом убывают с увеличением сечения проката:
Толщина проката, мм |
4 |
5–9 |
10–20 |
21–32 |
33–60 |
61–80 |
более 80 |
σт, МПа (не менее) |
350 |
350 |
330 |
310 |
290 |
280 |
270 |
Иногда низколегированные стали применяют в нормализованном состоянии. Нормализация приводит к большей стабильности механических свойств, улучшению характеристик пластичности, ударной вязкости и хладостойкости по сравнению с горячекатаным состоянием. При этом прочностные характеристики практически не изменяются.
Низколегированные стали могут подвергаться термическому улучшению (закалке с высоким отпуском). Термическая обработка низколегированных сталей отличается от термообработки низкоуглеродистых сталей тем, что, как правило, закалка стали проводится не с прокатного нагрева, а со специального. В процессе охлаждения стали из аустенитного состояния протекают промежуточное и мартенситное превращения. После закалки обязательно проводят высокий отпуск. В результате такой обработки сталь имеет дисперсную сорбитную структуру.
Гарантируемые механические свойства листового проката после термического улучшения приведены в табл. 1.2.
13

Таблица 1 . 2
Механические свойства (не менее) низколегированных сталей после термического улучшения
Марка |
Толщина |
σв, |
σт, |
δ, % |
KCU, МДж/м2, при Т, °С |
||
стали |
проката, мм |
МПа |
МПа |
–40 |
–70 |
||
|
|||||||
14Г2 |
10–32 |
540 |
400 |
18 |
0,4 |
0,3 |
|
10Г2С1 |
10–40 |
540 |
400 |
19 |
0,5 |
0,3 |
|
09Г2С |
10–32 |
500 |
370 |
19 |
0,5 |
0,3 |
|
15Г2СФ |
33–60 |
460 |
320 |
21 |
0,5 |
0,3 |
|
10–32 |
600 |
450 |
17 |
0,4 |
0,3 |
Термическое упрочнение позволяет дополнительно на 20–50 % увеличить уровень показателей прочности, повысить уровень ударной вязкости в 1,5–2 раза и обеспечить высокую сопротивляемость низколегированныхсталейхрупкому разрушению.
1.2. СВАРИВАЕМОСТЬ НИЗКОЛЕГИРОВАННЫХ СТАЛЕЙ
Рассматриваемые стали обладают хорошей свариваемостью. Технология сварки низколегированных сталей должна обеспечивать определенный комплекс требований, основными из которых являются равнопрочность сварного соединения с основным металлом и отсутствие дефектов в сварном шве. Для обеспечения равнопрочности механические свойства сварного соединения должны быть не ниже нижнего предела механических свойств основного металла. Кроме этого сварное соединение должно обладать хорошей пластичностью (не переходить в хрупкое состояние). В некоторых случаях конкретные условия работы конструкций допускают снижение отдельных показателей механических свойств сварного соединения, а для ответственных изделий к сварному соединению, наоборот, предъявляют дополнительные требования.
14
Влияние легирующих элементов на свариваемость
Легирующие элементы оказывают существенное влияние на свариваемость низколегированных сталей. Наиболее распространенные легирующие элементы, такие как Mn и Cr, уменьшают диффузионную подвижность углерода, как следствие, увеличивают временной уровень перехода аустенита в феррит, перлит и бейнит
ипонижают температурный интервал γ→α-превращения. При этом Mn упрочняет феррит и способствует процессу карбидообразования, Cr существенно уменьшает критическую скорость охлаждения, подавляет перлитное превращение, расширяет область промежуточных превращений на диаграмме, поэтому при общепринятых режимах сварки в околошовном участке возрастает вероятность образования мартенсита и понижается сопротивляемость сварных соединений образованию холодных трещин.
Таким образом, увеличение содержания легирующих элементов, повышающих закаливаемость, снижает сопротивление сварных соединений образованию холодных трещин. Элементы, упрочняющие твердый раствор, способствуют, как правило, снижению ударной вязкости металла на участках перегрева и полной перекристаллизации в зоне термического влияния сварных соединений.
Строение сварного соединения низколегированных сталей
Механические и эксплуатационные характеристики сварного соединения напрямую зависят от формирующейся структуры и уровнявременныхиостаточныхнапряжений.
Сварное соединение при сварке плавлением имеет два ярко выраженных участка: закристаллизовавшийся металл шва и зону термического влияния в основном металле, отличающихся макро-
имикроструктурой, химическим составом, механическими свойствами по сравнению с основным металлом. Характерные признаки зон связаны с фазовыми и структурными превращениями, которые претерпевает при сварке металл в каждой зоне.
Металл шва (или сварной шов) характеризуется литой макроструктурой металла. Свойства сварного шва зависят от химического состава металла, термического цикла сварки и последующей
15
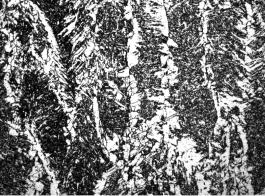
термической обработки. Химический состав металла шва определяется долей участия в образовании шва основного и электродного металлов, а также взаимодействием между металлом
ишлаком и газовой фазой. При сварке низколегированных сталей состав металла шва незначительно отличается от состава основного металла.
Свойства металла шва определяются структурой, формирующейся в процессе охлаждения закристаллизованного металла. В сварных швах низколегированных сталей формируется ферритоперлитная структура. При относительно высокой скорости охлаждения с высоких температур в металле шва возможно выделение феррита в виде ориентированных пластин внутри зерна, имеющих четко выраженную игольчатую форму (видманштеттова структура). Возможны случаи одновременного образования сетки феррита
ивидманштеттового феррита (рис. 1.1). При непрерывном охлаждении количество ферритной фазы не достигает равновесного значения и в результате распада оставшейся части аустенита образуется перлит – квазиэвтектоид с содержанием углерода менее 0,8 %. Такой перлит характеризуется повышенной долей ферритной составляющей (см. рис. 1.1).
Рис. 1.1. Микроструктура металлашвастали09Г2С, сваренногоэлектродомспроволокойСв-08ГС(×200)
16
Повышенные скорости охлаждения металла шва способствуют изменению количества и строения перлитной фазы вплоть до образования закалочных структур. При этом прочность металла шва повышается, однако снижаются пластические свойства и ударная вязкость. Для предупреждения образования закалочных структур при повышенных скоростях охлаждения содержание углерода
вметалле шва должно быть меньше. Возможное снижение прочности металла шва из-за сниженного содержания углерода компенсируется легированием металла шва марганцем и кремнием через проволоку, покрытие или флюс марганцем.
Скорость охлаждения металла шва определяется толщиной свариваемого металла, конструкцией сварного соединения, режимом сварки и начальной температурой изделия. Влияние скорости охлаждения в наибольшей степени проявляется при дуговой сварке однослойных угловых швов и последнего слоя многослойных угловых и стыковых швов при наложении их на холодные, предварительно сваренные швы.
Металл многослойных швов, кроме последних слоев, подвергающийся действию повторного термического цикла сварки, имеет более благоприятную мелкозернистую структуру, поэтому он обладает более низкой критической температурой перехода
вхрупкое состояние.
Зона термического влияния (ЗТВ) представляет собой участок основного металла, испытывающий нагрев от сварочного источника тепла от температуры ниже температуры кристаллизации и до температуры окружающего воздуха среды. В результате такого нагрева в зоне термического влияния протекают фазовые и структурные превращения в твердом металле. Механические свойства зоны термического влияния будут зависеть от исходной структуры металла, термического цикла сварки и предыдущей и последующей термической обработки.
Для низколегированных сталей, претерпевающих при термическом цикле сварки полиморфное превращение, в зоне термического влияния выделяется несколько характерных участков.
17
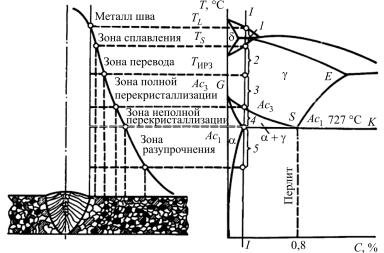
Деление зоны термического влияния на участки происходит в основном по характерной максимальной температуре, на которую нагревается данный участок при сварке в соответствии с диаграммой Fe – Fe3C (рис. 1.2): 1 – зона сплавления, 2 – зона перегрева, 3 – зона полной перекристаллизации (нормализации), 4 – зона неполной перекристаллизации, 5 – зона разупрочнения.
Рис. 1.2. Строениесварногосоединения низколегированныхсталей
Первый участок ЗТВ – зона сплавления, где основной металл нагревается в интервале температур начала TL и конца TS кристаллизации. Этот участок примыкает непосредственно к металлу шва и находится в двухфазном твердожидком состоянии. Здесь происходит сплавление наплавленного и основного металла. Участок имеет сравнительно небольшую ширину и отличается по химическому составу от соседних участков основного металла. Эти изменения вызваны диффузионными процессами. Направление диффузии элемента определяется коэффициентом распределения в твердой и жидкой фазах, а также содержанием элемента в основном металле и сварочной ванне. В зависимости от соотношения этих величин диффузия
18
элемента может происходить из основного металла в шов или из металла шва в основной металл. При сварке сталей низкоуглеродистой проволокой элементы перемещаются из основного металла в шов. Участок металла, примыкающий к металлу шва, обедняется этими элементами. Например, при соблюдении указанных условий наблюдается заметная диффузия углерода из основного металла в сварочную ванну. При этом максимальная концентрация углерода в жидкой ванне в месте контакта твердой и жидкой фаз повышается, а на участке основного металла понижается.
Свойства зоны сплавления в ряде случаев оказывают резкое влияние на свойства сварного соединения. Ширина зоны сплавления зависит от характера источника нагрева, состава свариваемого и электродного металлов и ряда других факторов.
Второй участок ЗТВ – зона перегрева, или участок крупного зерна. В него входит металл, который нагревался от температуры конца кристаллизации TS до температуры начала интенсивного роста зерна TИРЗ. Обычно температура начала интенсивного роста зерна составляет 1200–1050 оС и зависит от химического состава стали и предшествующего способа обработки. При нагреве металл претерпевает α→γ-превращение и приобретает, соответственно, аустенитную структуру. По мере перегрева металла выше температуры Ас3 аустенитное зерно растет и даже при незначительной продолжительности пребывания при высоких температурах успевает вырасти до значительных размеров. Таким образом, данный участок характеризуется несколькими рядами крупных зерен, постепенно уменьшающихся в размере по мере удаления от шва.
При охлаждении происходит γ→α-превращение. Это превращение вследствие некоторого переохлаждения происходит при более низких температурах, чем при нагреве, и при более крупном исходном зерне аустенита после полного охлаждения образуется крупнозернистая структура. Тип структуры, образующейся на участке перегрева, зависит от характера термического цикла сварки и состава металла. Так, в некоторых случаях на этом участке формируется видманштеттова структура (рис. 1.3). В результате быст-
19
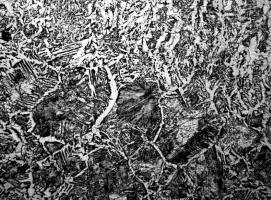
рого охлаждения на данном участке могут появляться структуры закалки: феррито-мартенситная, феррито-мартенситно-бейнитная, феррито-бейнитная.
Рис. 1.3. Микроструктура зоны сплавления и зоны перегрева, сталь 09Г2С (×200)
Третий участок ЗТВ – участок полной перекристаллизации,
или участок нормализации. Он включает металл, нагретый от температуры начала интенсивного роста зерна TИРЗ до температуры конца α→γ-превращенияАс3. Наэтомучасткепри нагревеметалл, какв зоне перегрева, приобретает аустенитную структуру. Однако этот участок отличаетсяотпредыдущегоболеемелкозернистымстроением.
В низколегированных сталях на участке нормализации образуется мелкозернистая структура (рис. 1.4), характеризующаяся в целом достаточно высоким комплексом механических свойств (прочностью, пластичностью, вязкостью).
Четвертый участок ЗТВ– зона неполной перекристаллизации,
включает в себя металл, нагретый в интервале температур концаАс3 иначала Ас1 α→γ-превращения. Металл участка подвергается только частичной перекристаллизации– превращение в γ-фазу претерпевают перлитные структуры, а ферритные зерна (α-фаза) остаются практически неизменными, поэтому указанный участок называется участком
20