
Конструкционные материалы. Свариваемость и сварка
.pdfОкончание табл. 7 . 6
1 |
2 |
3 |
4 |
5 |
6 |
7 |
8 |
9 |
10 |
|
|
АДС |
|
|
|
|
|
|
|
|
|
|
Проволока: |
|
|
|
|
|
|
|
|
|
|
Св-07Х25Н13 |
|
|
|
|
|
|
|
|
|
|
Флюс: АН-26 |
300 |
540 |
15 |
15 |
0,5 |
450 |
0,5 |
– |
|
|
АрДС |
|
|
|
|
|
|
|
|
|
|
Проволока: |
|
|
|
|
|
|
|
|
|
|
Св-04Х20Н5М6Б |
314 |
490 |
18 |
– |
0,9 |
490 |
0,5 |
– |
|
|
Св-07Х25Н13 |
300 |
540 |
15 |
15 |
0,5 |
540 |
0,5 |
– |
|
|
РДС |
|
|
|
|
|
|
|
|
|
|
Электроды: |
|
|
|
|
|
|
|
|
|
12X13 |
Э-12X13 (ЛМЗ-1) |
|
|
|
|
|
|
|
|
|
|
Э-06Х13Н(ЦЛ-41) |
|
|
|
|
|
|
|
|
|
|
ЦЛ-51 |
490 |
637 |
12 |
35 |
0,5 |
590 |
0,5 |
– |
|
12X13 |
Э-11X15Н25М6АГ2 |
363 |
588 |
13 |
15 |
0,4 |
590 |
0,5 |
– |
|
|
(ЭА-395/9) |
|
|
|
|
|
|
|
|
|
12X13 |
Э-10Х25Н13Г2 |
300 |
540 |
15 |
15 |
0,5 |
540 |
0,5 |
– |
|
(ЗиО-8, ЦЛ-25) |
||||||||||
|
|
|
|
|
|
|
|
|
||
|
Э-10Х25Н13Г2 |
300 |
540 |
15 |
15 |
0,5 |
540 |
0,5 |
– |
|
20X13 |
(ЗиО-8, ЦЛ-25) |
|||||||||
|
|
|
|
|
|
|
|
|||
|
ЦЛ-51 |
490 |
637 |
12 |
35 |
0,5 |
637 |
0,5 |
– |
|
|
АДС |
|
|
|
|
|
|
|
|
|
20X13 |
Проволока: |
|
|
|
|
|
|
|
|
|
Св-07Х25Н13 |
|
|
|
|
|
|
|
|
||
|
|
|
|
|
|
|
|
|
||
|
Флюс: АН-26 |
300 |
540 |
15 |
15 |
0,5 |
540 |
0,5 |
– |
|
|
РДС |
|
|
|
|
|
|
|
|
|
|
Электроды: |
|
|
|
|
|
|
|
|
|
|
Св-10Х18Н2 (АНВ-2) |
588 |
755 |
17 |
60 |
0,6 |
755 |
0,5 |
– |
|
|
АДС |
|
|
|
|
|
|
|
|
|
|
Проволока: |
|
|
|
|
|
|
|
|
|
14Х17Н2 |
Св-08Х18Н2ГТ, |
|
|
|
|
|
|
|
|
|
Св-08Х14ГНТ |
|
|
|
|
|
|
|
|
||
|
Флюс: АН-26с, ОФ-6, |
|
|
|
|
|
|
|
|
|
|
АНФ-6 |
588 |
755 |
20 |
45 |
0,7 |
755 |
0,5 |
– |
|
|
АрДС |
|
|
|
|
|
|
|
|
|
|
Проволока: |
|
|
|
|
|
|
|
|
|
|
Св-08Х18Н2ГТ, |
|
|
|
|
|
|
|
|
|
|
Св-08Х14ГНТ |
588 |
755 |
20 |
40 |
0,8 |
755 |
0,5 |
– |
141
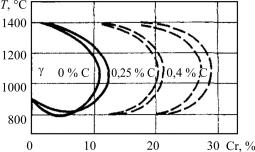
8. ВЫСОКОЛЕГИРОВАННЫЕ СТАЛИ ФЕРРИТНОГО КЛАССА
8.1.СОСТАВ И СВОЙСТВА СТАЛЕЙ
Кферритным сталям относят сплавы, содержащие более 12 % хрома, когда γ→α-превращение отсутствует. При содержании ~12 % Cr, в соответствии диаграммой Fe – Cr, у сплавов имеет ме-
сто замыкание области γ-твердых растворов. Точки А1 и А3 на диаграмме состояния сливаются. При дальнейшем увеличении содержания Cr сплавы не претерпевают превращений. Граница области γ-твердых растворов изменяется в зависимости от содержания С (рис. 8.1). Чистые железохромистые сплавы становятся однофазными ферритными при введении 13 % Cr. В присутствии С сплавы с большим содержанием Cr могут еще иметь γ→α-превращение. Перемещение границы γ-области в сторону больших концентраций Cr при введении С связано также с уменьшением растворенного Cr вследствие образования его стабильных карбидов. В связи с этим ферритные стали с обычным содержанием С легированы Cr в количестве не менее 16 %.
Рис. 8.1. Положение области γ в диаграмме состояния сплавов с различным содержанием углерода (схема)
142
С повышением содержания хрома в высокохромистых сталях возрастает их коррозионная стойкость и жаростойкость. Стали, содержащие 17–18 % хрома, обеспечивают возможность их эксплуатации в жидких средах средней агрессивности, поэтому они относятся к кислотостойким сталям (12X17, 08Х17Т, 08Х18Т1 и др.). Дальнейшее увеличение содержания хрома до 25–30 % придает им стойкость против газовой коррозии (жаростойкость) при температуре 1100 °С, поэтому эти стали относятся к жаростойким (15Х25Т, 15X28 и др.). Для серосодержащих сред (крепких щелоков сернистого натрия и др.) пригодны стали, содержащие не менее 25 % хрома.
Высокохромистые ферритные стали являются перспективным конструкционным материалом. По сопротивляемости коррозии ферритные стали не уступают хромоникелевым аустенитным сталям, значительно превосходят их по стойкости к коррозионному растрескиванию. Широкое применение ферритных сталей позволило бы решить проблему дефицита никеля путем замены ими распространенных в настоящее время аустенитных сталей (табл. 8.1 и 8.2).
Однако данные стали с обычным содержанием С и N обладают высокой чувствительностью к надрезу при нормальной температуре, что может привести к хрупкому разрушению конструкций как в процессе изготовления, так и при транспортировке и эксплуатации. Это затрудняет их применение для изготовления оборудования, работающего в условиях ударных и знакопеременных нагрузок. Такие ферритные стали используют, как правило, для изготовления внутренних устройств химических аппаратов, змеевиков пиролиза с незначительным внутренним давлением и т.п.
Резкое повышение пластичности и вязкости хромистых ферритных сталей возможно путем ограничения в их составе примесей внедрения. Для уменьшения примесей при выплавке ферритных сталей применяют вакуумные печи и последующую продувку расплава аргоном или аргонокислородной смесью. Новые хромистые ферритные стали с низким содержанием примесей внедрения (до 0,015–0,020 % всумме) отличаются высокой пластичностью иударной вязкостью. Среди них следует отметить стали ЭП882-ВИ и ЭП904-ВИ, которые начинаютприменятьвэнергетическоммашиностроении.
143
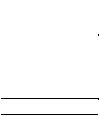
144
|
|
|
|
|
|
|
|
|
|
|
|
|
|
|
|
Таблица |
8 . 1 |
||
|
|
|
|
Химический состав высокохромистых ферритных сталей |
|
|
|
|
|||||||||||
|
|
Марка |
|
|
|
|
|
|
|
|
|
|
|
|
|
|
|
|
|
|
|
|
|
|
|
|
|
|
Содержаниеэлементов |
|
|
|
|
|
|
||||
|
|
стали |
|
|
|
|
|
|
|
|
|
|
|
|
|
|
|
|
|
|
C |
Si |
|
Mn |
S |
|
P |
Cr |
Ti |
Nb |
|
|
N2 |
Прочие |
|||||
|
|
08X17Т |
|
|
|
|
|
|
|
|
|
|
|
|
|
|
|
|
|
|
≤ 0,08 |
≤0,8 |
|
≤0,8 |
≤0,025 |
|
≤0,035 |
16–18 |
0,5–0,8 |
− |
|
|
− |
|
− |
||||
|
|
15Х25Т |
|
|
|
|
|
|
|
|
|
|
|
|
|
|
|
|
|
|
≤ 0,15 |
≤1,0 |
|
≤0,8 |
≤0,025 |
|
≤0,035 |
24–27 |
0,5–0,9 |
− |
|
|
− |
|
− |
||||
|
|
08Х23С2Ю |
|
|
|
|
|
|
|
|
|
|
|
|
|
|
|
||
|
≤ 0,08 |
≤1,5–1,8 |
0,4–0,7 |
≤0,015 |
|
≤0,030 |
22–24 |
− |
− |
|
|
− |
1,1–1,5 Al |
||||||
|
|
ЭП882-ВИ |
|
|
|
|
|
|
|
|
|
|
|
|
|
|
|
|
|
|
≤0,015 |
≤0,5 |
|
≤0,5 |
≤0,02 |
|
≤0,015 |
16,5–18,5 |
− |
0,15–0,35 |
|
≤0,015 |
1,5–2,0 Mo |
||||||
|
|
ЭП904-ВИ |
|
|
|
|
|
|
|
|
|
|
|
|
|
|
|
|
|
|
≤0,012 |
≤0,3 |
|
≤0,5 |
≤0,02 |
|
≤0,025 |
16,0–18,5 |
− |
0,1–0,4 |
|
≤0,015 |
2,2–2,5 Al |
||||||
|
|
|
|
|
|
|
|
|
|
|
|
|
|
|
|
Таблица |
8 . 2 |
||
|
|
|
|
|
Назначение высокохромистых ферритных сталей |
|
|
|
|
||||||||||
|
|
|
|
|
|
|
|
|
|
|
|
|
|
|
|
|
|
||
|
|
Маркастали |
|
|
|
|
|
Примерыиспользования |
|
|
|
Температура |
|||||||
|
|
|
|
|
|
|
|
|
|
эксплуатации, °С |
|||||||||
|
|
|
|
|
|
|
|
|
|
|
|
|
|
|
|
|
|||
|
|
|
|
|
|
|
|
|
|
|
|
|
|
|
|
|
|
||
|
|
08Х17Т, |
|
|
|
|
|
|
|
|
|
|
|
|
|
700 |
|
||
|
|
15Х25Т, |
|
|
|
Деталивнутреннихустройствхимическихаппаратов |
|
|
1000 |
|
|||||||||
|
|
15X28 |
|
|
|
|
|
|
|
|
|
|
|
|
|
|
900 |
|
|
|
|
|
|
|
|
|
|
|
|||||||||||
|
|
Биметаллсплакирующимслоем |
|
Корпусы, днища, патрубкиидр. деталихимическихаппаратов |
|
|
450 |
|
|||||||||||
|
|
изсталей08Х17Ти15Х25Т |
|
|
|
|
|
|
|
|
|
|
|
|
|
|
|||
|
|
08Х23С2Ю |
|
|
|
Змеевикипиролизаацетонаиуксуснойкислоты |
|
|
1200 |
|
|||||||||
|
|
ЭП882-ВИ |
|
|
|
Заменительхромоникелевыхаустенитныхсталей |
|
|
400 |
|
|||||||||
|
|
ЭП904-ВИ |
|
|
Высокотемпературноеоборудование, работающеевусловиях |
|
|
1200 |
|
||||||||||
|
|
|
|
|
газовойкоррозии, втомчислевсеросодержащихсредах |
|
|
|
|||||||||||
|
|
|
|
|
|
|
|
|
|
|
|
||||||||
|
|
|
|
|
|
|
|
|
|
|
|
|
|
|
|
|
|
|
|
Сталь ЭП882-ВИ разработана в качестве заменителя хромоникелевых аустенитиых сталей марок 08Х18Н10Т, 12Х18Н20Т и др. для изготовления теплообменного оборудования химических производств, энергетического оборудования тепловых и атомных электростанций. Сталь не склонна к хлоридному коррозионному растрескиванию, питтинговой коррозии.
Сталь ЭП904-ВИ применяется для изготовления оборудования, работающего в условиях окисления при высоких температурах. Она отличается хорошей свариваемостью, высокой жаростойкостью до 1300 °С. Применение ее эффективно для элементов крепления поверхностей нагрева энергетических котлоагрегатов, особенно в случаяхработынавысокосернистомтопливе.
Всвязи с высокой хрупкостью при нормальной температуре
кхромистым ферритным сталям, произведенным в открытых печах, практически не предъявляют требований по ударной вязкости, а оговаривают в основном минимально допустимые значения прочностии пластичности (табл. 8.3).
Таблица 8 . 3 Механические свойства ферритных сталей
|
σ0,2, МПа |
σв, МПа |
δ5, % |
ψ, % |
KCU, |
Маркастали |
МДж/м2 |
||||
|
|
|
неменее |
|
|
08Х17Т(лист) |
– |
440 |
18 |
– |
– |
08X17Т(трубы) |
– |
372 |
17 |
– |
– |
15Х25Т(лист) |
– |
440 |
14 |
– |
0,2 |
15Х25Т(трубы) |
– |
441–461 |
17 |
– |
– |
08Х23С2Ю(трубы) |
– |
490 |
10 |
6 |
– |
ЭП882-ВИ(лист) |
274 |
440 |
30 |
– |
0,6 |
ЭП882-ВИ(трубы) |
245 |
372 |
22 |
– |
– |
ЭП904-ВИ(лист) |
323 |
440 |
440 |
– |
0,6 |
Хрупкость ферритных сталей обычно связывают с грубозернистой структурой, обусловленной интенсивным ростом зерна даже в процессе охлаждения заготовок после прокатки. Для измель-
145
чения структуры сталь легируют титаном, образующим мелкодисперсные карбиды, устойчивые к коагуляции и диссоциации при высоких температурах. Располагаясь на границах зерен, карбиды могут уменьшить рост зерна при нагреве. Наиболее распространенные в настоящее время хромистые ферритные стали марок
08Х17Т и 15Х25Т содержат до 0,80 и 0,90 % Ті.
Для измельчения грубозернистой структуры прокатку листов из сталей 08Х17Т, 15Х25Т и 25Х28НА завершают при пониженных температурах до 820–850 °С. Низкотемпературная прокатка способствует повышению ударной вязкости указанных сталей до 0,8 МДж/м2 и пластичности δ5 до 25 %. С учетом этих возможностей в ГОСТ 7350–77 внесены требования по минимально допустимым значениям ударной вязкости KCU стали 15X25 до 0,2 МДж/м2. Ударная вязкость стали 15Х25Т, произведенной по модернизированной технологии прокатки листов, достигает 0,8 МДж/м2, стали 08Х23С2Ю – не превышает 0,1 МДж/м2. Это связано прежде всего с тем, что значения температуры перехода сталей в хрупкое состояние существенно отличаются. Для стали 15Х25Т температура перехода в хрупкое состояние находится на уровне 10 °С, для стали 08Х23С2Ю – на уровне 100 °С.
8.2. СВАРИВАЕМОСТЬ ФЕРРИТНЫХ СТАЛЕЙ
Основным недостатком высокохромистых ферритных сталей является их неудовлетворительная свариваемость, связанная с резким охрупчиванием сварных соединений в зоне термического влияния. Под воздействием термического цикла сварки в металле околошовной зоны происходит чрезмерный рост зерен феррита, перенасыщение твердого раствора С и N, диссоциация карбонитридов хрома, резко снижаются ударная вязкость и пластичность, возникает склонность к межкристаллитной коррозии (рис. 8.2).
В зоне термического влияния можно выделить три области опасных температур, в диапазонах которых происходит охрупчи-
146
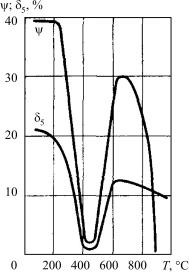
вание и появление склонности к межкристаллитной коррозии ферритных сталей при сварке:
1)от температуры конца кристаллизации TS до 1000 °С происходит интенсивный рост зерна;
2)от 850 до 550 °С наблюдается выделение σ-фазы (сигматизация);
3)от 550 до 400 °С проявляется 475-градусная хрупкость.
Рис. 8.2. Влияние температуры нагрева на пластичность стали 15X25T: δ5 – относительное удлинение;
ψ – относительное сужение
Рост зерна и связанная с этим хрупкость металла околошовной зоны ферритных сталей, возникающие под влиянием кратковременного воздействия термического цикла сварки, не устраняются последующей термической обработкой сварных соединений. Склонность к межкристаллитной коррозии может восстанавливаться отпуском после сварки при температуре 700–740 °С с быстрым охлаждением.
147
Худшей свариваемостью обладают ферритные стали, не содержащие карбидообразующих элементов или с недостаточным их содержанием. Для повышения стойкости ферритных сталей к межкристаллитной коррозии в них вводят преимущественно титан (реже ниобий) для связывания углерода в карбиды и карбонитриды в количестве Ti/C > 5. При этом для гарантии необходимое количество титана в стали значительно превышают. Чрезмерно высокое содержание карбидообразующих элементов в высокохромистых ферритных сталях также отрицательно влияет при сварке на ударную вязкость металла околошовной зоны, как и их недостаточность. Связано это с возможностью образования эвтектики, обогащенной титаном вблизи линии сплавления, а также выделения ферритотитанидов.
Улучшение свариваемости высокохромистых ферритных сталей достигается снижением суммарного содержания в них углерода и азота. Установлено, что в сталях, содержащих 25 % хрома, с суммарным содержанием углерода и азота до 0,198 % резко снижается температура перехода в хрупкое состояние и после воздействия термического цикла сварки находится в интервале отрицательных температур. При этом обеспечивается также стойкость к межкристаллитной коррозии.
Улучшение свариваемости низкоуглеродистых ферритных сталей достигнуто также комплексным легированием титаном
(0,3–0,5 %), ванадием (0,2–0,4 %) и азотом (0,03–0,04 %). Совме-
стное легирование титаном, ванадием и азотом более эффективно, чем легирование каждым элементом в отдельности. На основе комплексного легирования разработана удовлетворительно сваривающаяся сталь марки 04Х19АФТ. Положительное влияние азота в данном случае объясняется тем, что при нагреве до температуры 1100 °С карбиды и карбонитриды ванадия растворяются в железе, а азот переходит в твердый раствор, что приводит к расширению двухфазной (α + γ) области и в структуре стали появляется аустенитная составляющая.
148
Охрупчивание высокохромистых ферритных сталей в интервале температур 400–500 °С (475-градусная хрупкость) изучалась многими исследователями, однако причина этого явления до сих пор является предметом дискуссии, так как все гипотезы, связанные с образованием и обособлением в феррите различных дисперсных фаз, а также с внутрифазовыми процессами без выделения избыточных фаз, не имеют исчерпывающих экспериментальных доказательств.
Некоторые исследователи считают, что 475-градусная хрупкость является латентной стадией образования σ-фазы, при которой происходит «внутрифазовый наклеп», связанный с появлением напряжений.
Это противоречит тому, что 475-градусная хрупкость характеризуется метастабильным состоянием и не сопровождается изменением параметров кристаллической решетки феррита.
Известно, что решающее значение в проявлении склонности к 475-градусной хрупкости ферритных сталей имеет концентрация хрома, с увеличением которой склонность возрастает. Дополнительное легирование стали молибденом и алюминием не оказывает влияния на 475-градусную хрупкость сталей, содержащих 17 % хрома, иускоряетпроявлениехрупкостиу сталей, содержащих25 % хрома.
Отрицательное влияние хрупкости при 475 °С может быть устранено нагревом при более высоких температурах. На рис. 8.3 представлено влияние температуры «закалки» на ударную вязкость и относительное удлинение образцов из стали 15X25, охрупченной после нагрева в течение 0,5 ч при 475 °С. В соответствии с этими данными нагрев при 750–760 °С практически полностью восстанавливает исходный уровень пластичности и вязкости стали. Более высокие температуры нагрева значительно менее эффективны, так как способствуют росту ферритного зерна, что особенно заметно при 1000 °С. Хрупкость при 475 °С сменится на хладноломкость при нормальной температуре вследствие формирования грубозернистой структуры.
149

Рис. 8.3. Влияние температуры «закалки» на пластичность (δ5 – 1) и ударную вязкость (KCU – 2) стали 15X25T, охрупченной после нагрева при 475 °С
Усовершенствованная технология производства – прокатка при пониженных температурах – не улучшает свариваемости сталей. Под воздействием термического цикла сварки и других операций, связанных с высокотемпературным нагревом, пластичность ферритных сталей с исходной мелкозернистой структурой резко снижается, приобретается весьма высокая склонность к хрупкому разрушению.
Крупнозернистый металл швов, а также металл в зоне термического влияния более склонен к образованию трещин, чем мелкозернистый. Образование трещин в сварных соединениях ферритных сталей не имеет ничего общего с замедленным разрушением, характерным для сварных соединений закаливающихся сталей. Радикальной мерой предотвращения трещин является предварительный и сопутствующий подогрев.
В целях максимального ограничения роста зерен при сварке предпочтительны методы с сосредоточенными источниками тепло-
150