
Конструкционные материалы. Свариваемость и сварка
.pdfРучную электродуговую сварку алюминия и его сплавов можно осуществлять угольным или металлическим покрытым электродом. Сварку угольным электродом применяют для заварки брака отливок, сварки алюминиевых шин, иногда для сварки тонкого материала по отбортовке. При этом используют присадочный материал в виде прутков, покрытых флюсом. Сварку угольной дугой ведут на постоянном токе прямой полярности. В качестве электродов можно применять угольные или графитовые стержни разных диаметров. Режимы сварки стыковыхсоединенийизалюминияприведенывтабл. 10.3.
Таблица 1 0 . 3
Режимы сварки стыковых соединений из алюминия угольным и графитовым электродами
Толщина |
Ток, А |
|
Диаметр, мм |
|
||
присадочного |
угольного |
графитового |
||||
металла, |
мм |
|||||
|
прутка |
электрода |
электрода |
|||
|
|
|
||||
2–5 |
|
120–250 |
4–6 |
12,5 |
10,0 |
|
5–10 |
|
250–400 |
5–6 |
15 |
12,5 |
|
10–15 |
|
400–500 |
6–8 |
18 |
15 |
Чаще применяют дуговую сварку покрытыми металлическими электродами с нанесением на них покрытий из смеси хлористых
ифтористых солей. В качестве связующего используют раствор хлористого натрия в воде или раствор декстрина, также предложен водный раствор карбоксилметилцеллюлозы (КМЦ). Толщина слоя покрытия в зависимости от диаметра электродного стержня приведена ниже. Стержни электродов изготовляют из проволоки алюминия
иалюминиевых сплавов по ГОСТ 7871–75.
Толщина покрытия в зависимости от диаметра электродного стержня:
Диаметрэлектродногостержня, мм |
Толщинапокрытиянасторону, мм |
3,0 |
0,25–0,3 |
4,0 |
0,3–0,5 |
5,0 |
0,5–0,75 |
6 иболее |
0,75–1,6 |
211
Ниже представлены наиболее распространенные марки покрытых электродов для сварки алюминия и его сплавов производства России и других стран.
Некоторые покрытые электроды для сварки алюминия и его сплавов:
Электрод |
Составпроволоки |
ОЗА1 |
Техническийалюминий |
ОК96.10 (ESAB) |
Техническийалюминий |
ОЗА2 |
ЛитойсплавтипаАЛ4 |
ОК95.50 (ESAB) |
ЛитойсплавтипаАЛ4 |
МВТУ |
СплавытипаАМц |
АФ1 |
СплавытипаАМг, АМц |
ОК96.20 (ESAB) |
СплавытипаАМг, АМц |
А1Ф |
СплавытипаАМц, силумин |
Сварку производят на постоянном токе обратной полярности. В табл. 10.4 представлены режимы дуговой сварки покрытыми электродами. С течением времени при хранении электроды увлажняются, поэтому перед сваркой их необходимо подсушить при температуре 150–200 °С.
Таблица 1 0 . 4 Основные параметры режима сварки покрытыми электродами
Толщина |
Диаметр |
Ток, А |
Напряжение |
Ширинашва |
металла, мм |
электрода, мм |
|
вдуге, В |
|
4 |
4 |
180–200 |
26–30 |
8 |
6 |
5 |
280–300 |
28–32 |
10 |
8 |
6 |
300–320 |
30–34 |
14 |
10 |
6–7 |
320–380 |
30–34 |
16 |
12 |
8 |
350–450 |
32–36 |
20 |
Автоматическая электродуговая сварка по слою флюса
производится плавящимся электродом и используется для стыковых соединений металла толщиной не менее 4 мм. Питание дуги осуществляется постоянным током обратной полярности.
212
Для полуавтоматической сварки под слоем флюса применяют флюсы АН-А1, АН-А4, 48-АФ-1, МАТИ-1а, МАТИ-10 (табл. 10.5).
Таблица 1 0 . 5
Некоторые сварочные материалы для алюминия и его сплавов при сварке под флюсом
Маркаалюминия |
Маркасварочнойпроволоки |
Маркафлюса |
|
иалюминиевыхсплавов |
поГОСТ7871 |
||
|
|||
А99, А85, А7 |
Св-А97, Св-А85Т |
АН-А1, УФОК-А1 |
|
АМц |
Св-АМц |
||
|
|||
АМг1 |
Св-АМг3 |
АН-А1 |
|
АМг6 |
Св-АМг6 |
||
|
Для автоматической дуговой сварки алюминия применяют флюсы с пониженной электропроводностью. Например, состав керамического флюса ДА-64 следующий: 30–44 % криолита, 38–48 % хлористого калия, 15–19 % хлористого натрия, 3–3,5 % кварцевого песка. Флюс замешивают на водном растворе карбоксилметилцеллюлозы (10–14 % массы шихты), протирают через сито и прокаливают при 280–320 °С в течение 6 ч. Флюс должен храниться в герметично закрытой таре, а перед употреблением просушиваться при температуре 200–250 °С в течение 2 ч.
Сварку ведут чаще расщепленным электродом. В конструкциях, работающих в коррозионных средах, после сварки необходимо тщательно удалять остатки флюса. Наиболее приемлемым типом сварного соединения для алюминия является стыковое соединение. Соединений внахлестку и тавровых избегают, так как возможно затекание шлака в зазоры, из которых его трудно удалить при промывке после сварки. Наличие шлака в зазоре может вызвать коррозию металла и остается в соединении в виде дефектов. В табл. 10.6 представлены рекомендуемые режимы автоматической дуговой сварки под слоем флюса стыковых двухсторонних швов алюминия и его сплавов (С7 по ГОСТ 14806).
213
Таблица 1 0 . 6 Рекомендуемые режимы автоматической сварки под слоем флюса
Толщина |
Диаметр |
Сварочный |
Напряжение |
Скорость |
Ширина |
Толщина |
свариваемого |
сварочной |
сварки, |
слоя |
слоя |
||
металла, мм |
проволоки, |
ток, А |
надуге, В |
м/ч |
флюса, |
флюса, |
|
мм |
|
|
|
мм |
мм |
6 |
1,2–1,4 |
170–180 |
28–30 |
25–26 |
24–26 |
6–10 |
8 |
1,4–1,6 |
190–210 |
30–32 |
20–22 |
24–26 |
8–10 |
12 |
2,5–2,7 |
350–370 |
38–40 |
16–18 |
32–34 |
10–12 |
20 |
3,0–3,2 |
450–480 |
38–42 |
12–14 |
46–50 |
12–14 |
Дуговую сварку в среде защитных газов широко используют для сварки алюминия и его сплавов. В качестве защитного газа применяют аргон чистотой не менее 99,9 % (по ГОСТ 10157–73: высший, первый и второй сорт) или смеси аргона с гелием. При сварке плавящимсяэлектродоминогдаприменяютаргонсдобавкойдо5 % О2.
Основным преимуществом процесса дуговой сварки вольфрамовым электродом в среде защитного газа является высокая устойчивость горения дуги. Благодаря этому процесс используется при сварке тонких листов.
Питание дуги осуществляется переменным током от источников с падающими внешними характеристиками. Сварку ведут ручным или автоматическим способом. Для ручной сварки используют вольфрамовые электроды и присадочную проволоку в зависимости от толщины свариваемого металла (табл. 10.7). Автоматическую сварку осуществляютбезподачиили сподачейприсадочнойпроволоки.
При ручной сварке тонких листов неплавящимся электродом без присадки (по отбортовке) или с присадкой в один проход горелку перемещают с наклоном «углом вперед». Угол наклона горелки кплоской поверхности детали около 60о. Присадочная проволока подаетсяпод возможно меньшим углом к плоской поверхности детали.
При механизированной или автоматической сварке неплавящимся электродом горелка располагается под прямым углом к поверхности детали, а присадочная проволока подается таким обра-
214
зом, чтобы конец проволоки опирался на край сварочной ванны; скорость подачи меняется от 4–6 до 30–40 м/ч в зависимости от толщины материала.
Таблица 1 0 . 7 Режимы ручной аргонодуговой сварки неплавящимся электродом
Условное |
Толщина |
Диаметр |
Диаметр |
Расход |
Сварочный |
Коли- |
|
обозначение |
сварочной |
||||||
швапо |
свариваемого |
вольфрамового |
проволоки, |
аргона, |
ток, А |
чество |
|
ГОСТ14806 |
металла, мм |
электрода, мм |
мм |
л/мин |
|
слоев |
|
|
|
|
|
|
|||
С1 |
1,5 |
1,0 |
1,0 |
5–6 |
60–90 |
1 |
|
2,0 |
3,0 |
2,0 |
5–6 |
80–110 |
1 |
||
|
|||||||
С7 |
3,0 |
4,0 |
3,0 |
7–8 |
100–130 |
2 |
|
С21 |
5,0–12,0 |
5,0 |
4,0–5,0 |
10–12 |
180–220 |
2–10 |
|
С21 |
12,0–30,0 |
6,0 |
6,0–8,0 |
12–14 |
240–260 |
2–5 |
|
8,0 |
400–450 |
||||||
|
|
|
|
|
|||
Т1 |
1,5–20 |
5,0–6,0 |
4,0 |
8–10 |
180–260 |
1–5 |
|
|
|
4,0 |
|
8–10 |
140–150 |
|
|
Н1, Н2 |
1,5–20,0 |
5,0 |
3,0–5,0 |
10–12 |
180–220 |
1–5 |
|
|
|
6,0 |
|
12–14 |
220–260 |
|
Для алюминиевых сплавов также используют сварку вольфрамовым электродом импульсной дугой. При этом можно сваривать алюминиевые сплавы толщиной от 0,2 мм и более. Для сварки алюминиевых сплавов импульсной дугой используют специализированные источники на переменном токе.
Расширение технологических возможностей при сварке металла больших толщин достигается за счет использования способа дуговой сварки вольфрамовым электродом погруженной дугой. Способ позволяет сваривать за один проход материал толщиной до 20 мм. При этом используют специальные вольфрамовые электроды с добавками иттрия и тантала и сварочные горелки с улучшенной защитой зоны сварки.
Алюминиевые сплавы подвергают трехфазной дуговой сварке вольфрамовыми электродами. Возможности регулирования теп-
215
ловложения при трехфазной дуговой сварке позволяют использовать ее для металла разных толщин. При трехфазной сварке за один проход успешно сваривают металл толщиной свыше 30 мм.
Сварку плавящимся электродом в защитном газе исполь-
зуют для материала толщиной более 3 мм, сварку ведут в чистом аргоне либо в смеси аргона и гелия (до 70 %). Для питания дуги при сварке плавящимся электродом применяют источники постоянного тока с жесткой внешней вольт-амперной характеристикой. Сварку ведут на токе обратной полярности, что обеспечивает надежное разрушение окисной пленки за счет катодного распыления и нормальное формирование швов. Сварку можно выполнять в полуавтоматическом или автоматическом режиме на подкладках с формирующей канавкой. Преимуществом процесса сварки плавящимся электродом является высокая производительность, возрастающая с увеличением толщины металла. Ориентировочные режимы сварки плавящимся электродом для сплавов типа АМг представлены в табл. 10.8.
Таблица 1 0 . 8
Режимы полуавтоматической дуговой сварки плавящимся электродом
Толщина, |
Диаметрсварочной |
Скоростьсварки, |
Сварочный |
Напряжение |
мм |
проволоки, мм |
мм/мин |
ток, А |
надуге, В |
1,6 |
1,0 |
450–600 |
70–100 |
17–18 |
3,0 |
1,2 |
500–700 |
105–120 |
17–20 |
6 |
1,2 |
450–600 |
120–140 |
20–24 |
10 |
1,6 |
550–700 |
240–300 |
29–32 |
Полуавтоматическая сварка плавящимся электродом возможна в различных пространственных положениях и позволяет заменить менее совершенный процесс сварки алюминиевых сплавов покрытыми электродами; при этом рекомендуются полуавтоматы с механизмом подачи тянущего типа. Импульсно-дуговая сварка плавящимся электродом расширяет возможность сварки
216
алюминиевых сплавов при различных пространственных положениях. При этом улучшается формирование швов, регулируется время пребывания металла сварочной ванны в расплавленном состоянии, а значит, и протекание металлургических реакций.
При плазменной сварке (сжатой дуге) концентрация энер-
гии в пятне нагрева высокая, что делает этот вид сварки перспективным для соединения алюминиевых сплавов. Преимуществом плазменной сварки является высокая скорость, значительное сокращение зоны термического влияния, стабильность процесса, благодаря чему не требуется контроль и поддержание постоянства длины дуги, что облегчает выполнение ручной сварки. При плазменной сварке, в связи с глубоким проплавлением, резко увеличивается доля основного металла в формировании шва. Однако при этом необходимо соблюдать точность сборки деталей под сварку и ведения горелки по стыку. Для алюминиевых сплавов необходимо применятьплазменнуюсварку спитаниемдугипеременным током.
С помощью слаботочной сжатой дуги (микроплазмы) можно сваривать алюминиевые сплавы толщиной 0,2–1,5 мм при силе тока 10–100 А. При микроплазменной сварке применяют аргон чистотой не менее 99,98 %; в качестве защитного газа используют гелий чистотой 99,95 %. Гелий, защищая сварочную ванну от атмосферы, затрудняет развитие фронта ионизации в радиальном направлении и, дополнительно сжимая дугу, делает ее пространственно устойчивой. Сварочные горелки рассчитаны на применение лантанированных вольфрамовых электродов диаметром 0,8–1,5 мм.
217
11.ТИТАН И ТИТАНОВЫЕ СПЛАВЫ
11.1.ОСНОВНЫЕ СВОЙСТВА ТИТАНА
Титан широко распространен в земной коре, где его содержится около 0,6 %, по распространенности он занимает четвертое место после алюминия, железа и магния. Однако промышленный способ его извлечения был разработан лишь в 40-х гг. XX в. Благодаря прогрессу в области самолето- и ракетостроения производство титана и его сплавов интенсивно развивалось. Рост производства титана объясняется сочетанием таких ценных свойств, как малая плотность, высокая удельная прочность (σв/γ), коррозионная стойкость, технологичность при обработке давлением и свариваемость, хладостойкость, высокая стойкость против солнечной радиации, немагнитность и ряд других ценных физико-механичес- ких характеристик.
Титан – металл серебристо-белого цвета, имеющий малую плотность(γ = 4,505 г/см3). Температураплавлениятитана(1668 ± 4) °С в зависимости от степени его чистоты. Титан обладает полиморфизмом, имеет две полиморфные модификации: 1) низкотемпературную (рис. 11.1, а) – α-титан (плотность 4,505 г/см3) с гексагональной плотноупакованной кристаллической решеткой с периодами а = 0,2951 нм и с = 0,4684 нм; 2) высокотемпературную (рис. 11.1, б) – β-титан (плотность 4,32 г/см3), имеющую объемно-центрированную кубическую решетку, период которой а = 0,3282 нм. Температура полиморфногопревращенияα ↔ β составляет882 °С.
Механические свойства титана существенно зависят от чистоты металла, т.е. от количества примесей. Различают примеси внедрения: кислород, азот, углерод, водород – и примеси замещения, к которым относятся железо и кремний. Примеси повышают прочность, но одновременно резко снижают пластичность, причем наиболее сильное отрицательное действие оказывают примеси вне-
218
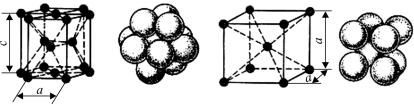
дрения – газы. При содержании 0,03 % Н, 0,2 % N или 0,7 % О титан полностью теряет способность к пластическому деформированию и хрупко разрушается.
а |
б |
Рис. 11.1. Кристаллографические решетки чистого титана:
а – α-Ti; б – β-Ti
Технически чистый титан изготовляют двух марок: ВТ1-00, ВТ1-0. Титан марки ВТ1-00, содержащий не более 0,05–0,1 % примесей, имеет предел прочности σв = 300 МПа, относительное удлинение δ = 65 %. Для технического титана ВТ1-0 с суммарным содержанием примесей 0,8 % предел прочности σв = 650 МПа, а относительное удлинение δ = 20 %.
Недостатком титана является низкий модуль нормальной упругости (Е = 112 000 МПа), почти в два раза меньший, чем у железа
иникеля, что затрудняет изготовление жестких конструкций. Для повышения жесткости приходится увеличивать толщину деталей
иих массу.
Титан имеет низкую теплопроводность, относится к числу химически активных металлов, со многими элементами периодической системы способен взаимодействовать и образовывать твердые растворы и интерметаллиды с особыми механическими, химическими и физическими свойствами.
Несмотря на химическую активность, титан при нормальной температуре обладает высокой коррозионной стойкостью – выше, чем у железа, алюминия и даже нержавеющих сталей. Это обусловлено образованием на его поверхности стойкой пассивной пленки
219
TiO2, прочно связанной с основным металлом и исключающей его непосредственный контакт с агрессивной средой. Толщина оксидной пленки, образующейся на титане после длительного пребывания на воздухе, обычно достигает 5–6 нм. Благодаря оксидной пленке титан и его сплавы не корродируют в атмосфере воздуха, холодной и кипящей пресной воде, в морской воде, устойчивы к коррозии под напряжением, а также в кислотах органического происхождения. Титан не стоек в плавиковой кислоте и в концентрированных серной и азотной кислотах. При нагреве выше 500 °С титан становится очень активным элементом. Он либо растворяет почти все соприкасающиеся и ним вещества, либо образует с ними химические соединения.
Одним из важных преимуществ титановых сплавов перед алюминиевыми, магниевыми сплавами, нержавеющими и теплостойкими сталями является жаропрочность, которая в условиях практического применениякомпенсируетразницу вплотности.
Интервал температур применения титана и его сплавов – от криогенных (близких к абсолютному нулю) до 600 °С. При понижении температуры от комнатной до криогенных прочностные свойства титана растут при сохранении высокого уровня пластичности (табл. 11.1).
Таблица 1 1 . 1 Механические свойства титана ВТ1-0 при криогенных температурах
Температура, К |
σв, МПа |
σ0,2, МПа |
δ, % |
ψ, % |
293 |
520 |
400 |
24 |
59 |
77 |
990 |
750 |
44 |
68 |
20 |
1280 |
900 |
29 |
64 |
4,2 |
1210 |
870 |
35 |
58 |
По удельной прочности в интервале температур 300–600 °С сплавы титана не имеют себе равных; при температуре ниже 300 °С они уступают алюминиевым сплавам, а выше 600 °С – сплавам на основе железа и никеля.
220