
Конструкционные материалы. Свариваемость и сварка
.pdfлительные среды, способствующие минимальному угару легирующих элементов. У флюсов, применяемых для коррозионно-стойких сталей, необходимо контролировать углерод, содержание которого не должно быть выше 0,1–0,2 %. Наиболее широко для сварки коррозионных сталей применяются низкокремнистые флюсы АН-26, 48-ОФ-Ю и АНФ-14.
Флюсы для электродуговой и электрошлаковой сварки аустенитных сталей:
Маркафлюса |
Назначение |
АНФ-14; АНФ-16; |
Автоматическаяэлектродуговаясварка |
48-ОФ-10; К-8 |
аустенитно-ферритнымишвами |
|
Автоматическаяэлектродуговаясваркасталей |
АН-26 |
снебольшимзапасомаустенитности |
|
аустенитно-ферритнымишвами |
АНФ-5; ФЦК |
Автоматическая электродуговая сварка сталей |
с большим запасом аустенитности чисто |
|
|
аустенитными швами |
|
Автоматическаяэлектродуговаяиэлектрошлаковая |
48-ОФ-6 |
сваркасталейсбольшимзапасомаустенитности |
|
чистоаустенитнымишвами |
АНФ-1; АНФ-6; АНФ-7; |
Электрошлаковаясваркасталейсбольшимзапасом |
АН-29; АН-292 |
аустенитностичистоаустенитнымишвами |
Марки сварочных проволок для электродуговой сварки под флюсом и электрошлаковой сварки аустенитных сталей:
Маркастали |
Маркапроволоки |
|
Коррозионно-стойкиестали |
||
12Х18Н9, 08Х18Н10, 12Х18Н10Т, |
Св-01Х19Н9; Св-04Х19Н9; |
|
Св-06Х19Н9Т; Св-07Х18Н9ТЮ; |
||
12Х18Н9Типодобные |
||
Св-04Х19Н9С2; Св-05Х19Н9ФЗС2 |
||
|
||
12Х18Н10Т, 0Х18Н10Т, 08Х18Н12Т, |
Св-07Х19Н10Б; Св-05Х20Н9ФБС |
|
08Х18Н12Б, работающиепритемпера- |
||
турахвыше350 °С |
|
|
10Х17Н13МЗТ, 08Х×18Н12Биподоб- |
Св-08Х19Н10МЗБ; |
|
ные; 08Х18Н10, 12Х18Н10Т, 12Х18Н9Т |
Св-06Х20Н11МЗТБ; Св-08Х25Н13БТЮ |
181
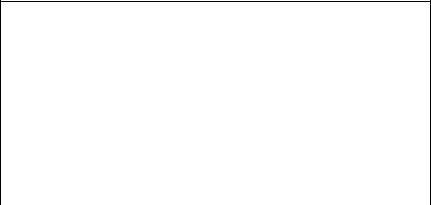
Жаропрочныестали
12×18Н9 саустенитно-ферритными |
Св-04Х19Н19 |
|
швами |
||
|
||
12×18Н9Б, 08×18Н12Тидр. |
Св-08Х18Н8Г2Б |
|
саустенитно-ферритнымишвами |
||
|
||
Х15Н35В4Т |
Св-06Х19Н10МЗТ |
|
Жаростойкиестали |
||
20×23Н13, 08×20Н14С2 иподобные |
Св-07Х25Н13 |
|
20×23Н18 иподобные, работающие |
Св-07Х25Н12Г2Т; Св-06Х25Н12ТЮ; |
|
притемпературах900–1100 °С |
Св-08Х25Н13БТЮ |
|
ХН35ВЮ, 20×25Н20С2 иподобные, |
|
|
работающиепритемпературах |
Св-08ХН50 |
|
до1200 °С |
|
Сварку жаростойких сталей аустенитно-ферритными проволоками типа 08Х25Н13БТЮ выполняют под низкокремнистыми флюсами АН-26, АНФ-14 и 48-ОФ-10. При сварке стабильноаустенитными проволоками и проволоками, содержащими легкоокисляющиеся элементы (алюминий, титан, бор и др.), применяют нейтральные фторидные флюсы АНФ-5, 48-ОФ-Ю. Для обеспечения стойкости к горячим трещинам аустенитных швов рекомендуют применять фторидный бористый флюс АНФ-22.
Сварку под фторидными флюсами производят на постоянном токе обратной полярности, а под высокоосновными бесфтористыми флюсами – на постоянном токе прямой полярности. При этом для получения той же глубины проплавления, что и на углеродистых сталях, сварочный ток следует снизить на 10–30 %. Для снижения вероятности образования пор в швах флюсы для высоколегированных сталей необходимо прокаливать непосредственно перед сваркой при 500–900 °С в течение 1–2 ч. Остатки шлака и флюса на поверхности швов необходимо тщательно удалять.
Сварка под флюсом в сочетании с высоколегированными проволоками обеспечивает получение требуемых свойств сварных соединений (табл. 9.4).
182
Таблица 9 . 4
Механические свойства металла шва и сварного соединения аустенитных сталей при температуре 20 °С
Марка |
δ, |
Марка |
Сварка |
Испытуемый |
σт, |
σв, |
δ, |
|
металла |
мм |
проволоки |
образец |
МПа |
МПа |
% |
||
|
||||||||
|
|
Св-13Х25Н8; |
Электродуговая |
Металл |
|
|
|
|
20Х23Н8 |
|
подфлюсом |
665 |
797 |
5,9 |
|||
12 |
Св- |
АНФ-5 |
шва* |
|
|
|
||
ХН35ВТ |
|
|
|
|
||||
|
0Х15Н35ВЗБЗТ |
Тоже, подфлю- |
Металл |
463 |
654 |
24,7 |
||
|
|
|||||||
|
|
|
сомАНФ-17 |
шва** |
474 |
474 |
15,8 |
|
|
|
|
Электрошлако- |
|
|
|
|
|
|
|
|
вая, пластинча- |
|
|
|
|
|
ХН77ТЮР |
100 |
Св-08Н50 |
тымэлектро- |
Металлшва* |
587 |
762 |
18 |
|
|
|
|
дом, флюс |
|
|
|
|
|
|
|
|
АНФ-7 |
|
|
|
|
|
ХН78Т |
125 |
Св-08Н50 |
Тоже, под |
Металлшва |
288 |
638 |
17,4 |
|
флюсомАНФ-1 |
*Термообработка: аустенизация при 1080 °С 2 ч на воздухе и старение при 700 °С 16 ч.
**Термообработка: старение при 800 °С 10 ч.
Электрошлаковая сварка
Пониженная чувствительность к образованию горячих трещин при данном способе сварки позволяет получать аустенитные швы без трещин. Это объясняется особенностями электрошлаковой сварки: малой скоростью перемещения источника нагрева, характером кристаллизации металла сварочной ванны и отсутствием в стыковых соединениях больших угловых деформаций. Однако длительное пребывание металла при 1200–1250 °С, приводя к необратимым изменениям в его структуре, снижает прочностные и пластические свойства околошовной зоны. При сварке коррози- онно-стойких сталей перегрев стали в околошовной зоне может вызвать ножевую коррозию, поэтому следует производить термическую обработку сварных изделий (закалку или стабилизирующий отжиг).
183
Для электрошлаковой сварки коррозионно-стойких сталей используют флюсы АНФ-6, АНФ-7, АНФ-8, 48-ОФ-6, АНФ-14
идр., а для жаростойких сталей – флюсы АНФ-Ш, АНФ-7, АНФ-8
ивысокоосновный АН-292. При сварке жаростойких сталей двухфазным швом типа Х25Н13 можно применять низкокремнистые флюсы АНФ-14 и АН-26. Применение фторидных безокислительных флюсов, особенно при сварке жаропрочных сталей, не гарантирует угара легкоокисляющихся легирующих элементов (титана, марганца и др.) в результате проникновения кислорода воздуха через поверхность шлаковой ванны; это вызывает необходимость в некоторых случаях защищать поверхность шлаковой ванны путем обдува ее аргоном.
Электрошлаковую сварку можно выполнять проволокой диаметром 3 мм или пластинчатыми электродами толщиной 6–20 мм (табл. 9.5). Изделия большой толщины со швами небольшой протяженности целесообразнее сваривать пластинчатым электродом. Изготовлять пластинчатый электрод проще, чем проволоку, но сварка проволокой обеспечивает возможность изменения формы металлическойванныихарактеракристаллизациишва, чтоспособствует
Таблица 9 . 5
Типовой режим электрошлаковой сварки высоколегированных сталей
Толщина |
Электрод, |
Марка |
Глубина |
Скорость |
|
Напряже- |
Зазор, |
подачи |
Силатока, |
||||||
металла, |
мм |
флюса |
шлаковой |
электрода, |
А |
ние, В |
мм |
мм |
|
|
ванны, мм |
м/ч |
|
|
|
|
|
|
|
|
|
|
|
100 |
Проволока |
АНФ-7 |
25–35 |
330 |
600–800 |
40–42 |
28–32 |
|
Ø3 |
|
|
|
|
|
|
100 |
Пластина |
АНФ-7 |
15–20 |
2,4 |
1200–1300 |
24–26 |
28–32 |
|
10×100 |
|
|
|
|
|
|
200 |
Пластина |
АНФ-1 |
15–20 |
1,9 |
3500–4000 |
22–24 |
38–40 |
|
12×200 |
|
|
|
|
|
|
200 |
Пластина |
АНФ-6 |
15–20 |
1,9 |
1800–2000 |
26–28 |
38–40 |
|
12×200 |
|
|
|
|
|
|
184
получению швов без горячих трещин. Однако жесткость сварочной проволоки затрудняет длительную и надежную работу токоподводящихиподающихузлов сварочной аппаратуры.
Сварка в защитных газах
В качестве защитных используют инертные (аргон, гелий) и активные (углекислый газ, азот) газы, а также различные смеси инертных или активных газов и инертных с активными.
Сварку в защитных газах можно использовать для соединения материалов различной толщины (от десятых долей до десятков миллиметров). Применение защитных газов с различными теплофизическими свойствами и их смесей изменяет тепловую эффективность дуги и условия ввода тепла в свариваемые кромки и расширяет технологические возможности процесса сварки.
При сварке в инертных газах повышается стабильность дуги и снижается угар легирующих элементов. Заданный химический состав металла шва можно получить путем изменения состава сварочной (присадочной) проволоки и доли участия основного металла в образовании шва, когда составы основного и электродного металлов значительно различаются, или путем изменения характера металлургических взаимодействий за счет значительного изменения состава защитной атмосферы при сварке плавящимся электродом.
Сварка в среде защитных газов обеспечивает формирование швов в различных пространственных положениях, что позволяет применять этот способ вместо ручной дуговой сварки покрытыми электродами.
Сварку аустенитных сталей в инертных газах выполняют неплавящимся (вольфрамовым) или плавящимся электродом.
Сварку вольфрамовым электродом производят в аргоне по ГОСТ 10157–79 и гелии или их смесях, применяют обычно для материала толщиной до 5–7 мм. Однако в некоторых случаях, например при сварке неповоротных стыков труб, применяют и при большой толщине стенки (до 100 мм и более). Применять этот способ необходимо также для сварки корневых швов в разделке при изготовлении ответственных толстостенных изделий.
185
В зависимости от толщины и конструкции сварного соединения сварку вольфрамовым электродом производят с присадочным материалом или без него (табл. 9.6). Процесс осуществляют вручную с использованием специальных горелок или автоматически на постоянном токе прямой полярности. Исключение составляют стали и сплавы с повышенным содержанием алюминия, когда для разрушения поверхностной пленки окислов, богатой алюминием, следует использовать переменный ток.
Таблица 9 . 6 Примерные режимы аргонодуговой сварки вольфрамовым
электродом аустенитных сталей
δ, мм |
Типсоединения |
Силатока, |
А |
|
Расходаргона, |
Скорость |
|
л/мин |
сварки, м/ч |
||||
|
|
|
|
|
||
|
|
Ручнаясварка |
|
|
|
|
1 |
Сотбортовкой |
35–60 |
|
|
3,5–4 |
|
2 |
75–120 |
|
|
5–6 |
− |
|
3 |
|
100–140 |
|
|
6–7 |
|
1 |
Встыкбезразделки |
40–70 |
|
|
3,5–4 |
|
2 |
80–130 |
|
|
5–6 |
− |
|
3 |
кромоксприсадкой |
120–160 |
|
|
6–8 |
|
|
|
Автоматическаясварка |
|
|
|
|
1 |
Встыксприсадкой |
80–140 |
|
|
4 |
30–60 |
2 |
140–240 |
|
|
6–7 |
20–30 |
|
3 |
|
200–280 |
|
|
7–8 |
15–30 |
1 |
Встыкбезприсадки |
60–120 |
|
|
4 |
35–60 |
2 |
110–200 |
|
|
6–7 |
25–30 |
|
3 |
|
130–250 |
|
|
7–9 |
25–30 |
Сварку можно выполнять непрерывно горящей или импульсной дугой. Импульсная дуга уменьшает протяженность околошовной зоны и коробление свариваемых кромок, а также обеспечивает хорошее формирование шва на материале малой толщины. Особенности кристаллизации металлов сварочной ванны при этом способе сварки способствуют дезориентации структуры, что уменьшает вероятность образования горячих трещин, однако может способствовать образованию околошовных надрывов. Для улучшения защиты и формирова-
186
ния корня шва используют поддув газа, а при сварке корневых швов на металле повышенных толщин применяют и специальные расплавляемые вставки. При сварке вольфрамовым электродом в инертных газах погруженной дугой увеличение доли тепла, идущей на расплавление основного металла, позволяет без разделки кромок, за один проход сваривать металл повышенной толщины. Однако околошовнаязонарасширяетсяивозникает опасностьперегреваметалла.
Сварку плавящимся электродом производят в инертных, а также активных газах или смеси газов (табл. 9.7). При сварке высоколегированных сталей, содержащих легкоокисляющиеся элементы (алюминий, титан и др.), следует использовать инертные газы, преимущественно аргон, и вести процесс на плотностях тока, обеспечивающих струйный перенос электродного металла. При струйном переносе дуга имеет высокую стабильность и практически исключается разбрызгивание металла, что важно для формирования швов в различных пространственных положениях и для ликвидации очагов коррозии, связанных с разбрызгиванием при сварке коррозионно-стойких и жаростойких сталей. Однако струйный перенос возможен на токах выше критического, при которых возможно образование прожогов при сварке тонколистового металла. Добавка в аргон до 3–5 % О2 и 15–20 % СО2 уменьшает критический ток, а создание при этом окислительной атмосферы в зоне дуги снижает вероятность образования пор, вызванных водородом. Однако при сварке в указанных смесях газов увеличивается угар легирующих элементов, а при добавке углекислого газа возможно науглероживание металла шва. Добавкой к аргону 5–10 % N можно повысить его содержание в металле шва. Азот является сильным аустенизатором, и таким образом можно изменить структуру металла шва. Для сварки аустенитных сталей применяют импульсно-дуговую сварку плавящимся электродом в аргоне и смесях аргона с кислородом и с углекислым газом, обеспечивающую соединение малых толщин и струйный перенос металла при прохождении импульса тока. Одновременно импульсно-дуговая сварка вызывает измельчение структуры шва и снижение перегрева околошовной зоны, что повышаетстойкостьсварногосоединениякобразованиютрещин.
187
Таблица 9 . 7
Ориентировочные режимы аргонодуговой сварки встык плавящимся электродом аустенитных сталей в нижнем положении
Толщина |
Подготовка |
Число |
Диаметр |
Сила |
Скорость |
Расход |
металла, |
сварочной |
тока, |
сварки, |
аргона, |
||
мм |
кромок |
слоев |
проволоки, мм |
А |
м/ч |
л/мин |
|
Автоматическаясварка |
|
|
|
||
2 |
Безразделки |
1 |
1 |
200–210 |
70 |
8–9 |
5 |
V-образнаяразделка |
1 |
1 |
260–275 |
44 |
8–9 |
|
подуглом50° |
|
|
|
|
|
10 |
V-образнаяразделка |
2 |
2 |
330–440 |
15–30 |
12–17 |
|
подуглом50° |
|
|
|
|
|
|
Полуавтоматическаясварка |
|
|
|
||
4 |
Безразделки |
1 |
1,0 − 1,6 |
160–300 |
− |
6–8 |
8 |
V-образнаяразделка |
2 |
1,6 − 2,0 |
240–360 |
− |
11–15 |
При сварке в углекислом газе низкоуглеродистых высоколегированных сталей с использованием низкоуглеродистых сварочных проволок при исходной концентрации углерода в проволоке менее 0,07 % содержание углерода в металле шва повышается до 0,08–0,12 %. Этого достаточно для резкого снижения стойкости металла шва к межкристаллитной коррозии. Однако науглероживание металла шва в некоторых случаях при энергичных карбидообразователях (титане, ниобии) может оказать благоприятное действие при сварке жаропрочных сталей за счет увеличения в структуре количества карбидной фазы.
Окислительная атмосфера, создаваемая в дуге за счет диссоциации углекислого газа, вызывает повышенное (до 50 %) выгорание титана и алюминия. Несколько меньше выгорают марганец, кремний и другие легирующие элементы, а хром не окисляется. Поэтому при сварке коррозионно-стойких сталей в углекислом газе применяют сварочные проволоки, содержащие раскисляющие и карбидообразующие элементы (алюминий, титан и ниобий). Другим недостатком сварки в углекислом газе является большое разбрызгивание металла (потери достигают 10–12 %) и образование на
188
поверхности шва плотных пленок окислов, прочно сцепленных
сметаллом. Это может резко снизить коррозионную стойкость и жаростойкость сварного соединения. Для уменьшения возможности налипания брызг на основной металл следует применять специальные эмульсии, наносимые на кромки перед сваркой, а для борьбы
сокисной пленкой эффективна подача в дугу небольшого количества фторидного флюса типа АНФ-5. Применение импульсной сварки также позволяет несколько снизить разбрызгивание. Сварка плавящимся электродом в углекислом газе производится на полуавтоматах и автоматах (табл. 9.8).
Таблица 9 . 8
Ориентировочные режимы дуговой сварки аустенитных сталей без разделки кромок плавящимся электродом в углекислом газе
δ, мм |
Шов |
D |
, |
Вылет |
I, А |
U, В |
v , |
Расход |
пр |
электрода, |
св |
CO2, |
|||||
|
|
мм |
мм |
|
|
м/ч |
л/мин |
|
|
|
|
|
|
|
|
||
1 |
Односторонний |
1 |
|
– |
80 |
16 |
80 |
10–12 |
3 |
Односторонний |
2 |
|
15 |
230–240 |
24–28 |
45 −50 |
12–15 |
|
|
2 |
|
15 |
250–260 |
28–30 |
30 |
12–15 |
6 |
Двусторонний |
3 |
|
15 |
350–360 |
30–32 |
30 |
12–15 |
|
|
2 |
|
15–20 |
380–400 |
30–32 |
− |
− |
8 |
Двусторонний |
3 |
|
20–25 |
430–450 |
33–35 |
− |
− |
2 |
|
15–20 |
420–440 |
30–32 |
30 |
12 |
||
|
|
|
||||||
10 |
Двусторонний |
3 |
|
25–30 |
530–560 |
34–36 |
− |
− |
Сварочные проволоки, созданные для сварки в углекислом газе высоколегированных аустенитных сталей, обеспечивают требуемую коррозионную стойкость и механические свойства за счет повышенного содержания титана, ниобия и элементов ферритизаторов – кремния, алюминия, хрома. Например, для сварки сталей типа 12Х18Н10Т используют проволоки Св-07Х18Н9ТЮ, Св-08Х20Н9С2БТЮ, для сталей типа 12Х18Н12Т– проволоку Св-08Х25Н13БТЮ, а для хромоникельмолибденовых сталей – проволоки Св-06Х19Н10МЗТ иСв-06Х20Н11МЗТБ.
189
10. АЛЮМИНИЙ И ЕГО СПЛАВЫ
Алюминиевые сплавы используют в сварных конструкциях различного назначения. Основными достоинствами их как конструкционных материалов являются малая плотность, высокая удельная прочность, высокая коррозионная стойкость. Чистый алюминий ввиду низкой прочности используют для изготовления конструкций в отдельных случаях в химической, пищевой и электротехнической промышленности. Алюминий высокой чистоты применяют в отраслях новой техники, в том числе при производстве полупроводников. В качестве конструкционных материалов в основном используют полуфабрикаты из алюминиевых сплавов. По показателям отношения прочности и текучести к плотности высокопрочные алюминиевые сплавы значительно превосходят чугун, низкоуглеродистые и низколегированные стали, чистый титан
иуступают лишь высоколегированным сталям повышенной прочности и сплавам титана.
Алюминий – легкий металл серебристо-светлого цвета с плотностью 2,7 г/см3 и температурой плавления 660 °С, имеет гранецентрированную кубическую решетку (ГЦК). Обладает высокой тепло-
иэлектропроводностью. Химически активен, но образующаяся
плотная пленка оксида алюминия Al2O3 предохраняет его от коррозии, поэтому алюминий коррозионностоек к влаге, в растворах азотной и других кислот. Коррозионная стойкость алюминия тем выше, чем он чище (не содержит примесей); то же самое относится к электропроводности алюминия. Хотя электропроводность алюминия составляет не более 60 % от электропроводности меди, но провода из алюминия при той же пропускной способности в два раза легче.
Алюминий высокой чистоты маркируется А99 (99,999 % Al), А8, А7, А6, А5, А0 (содержание алюминия от 99,85 % до 99 %).
Механические свойства: предел прочности 150 МПа, относительное удлинение 50 %, модуль упругости 7000 МПа.
190