
Конструкционные материалы. Свариваемость и сварка
.pdfПри направлении растягивающих напряжений под углом к направлению роста кристаллов более вероятно образование трещины между осями кристаллов, чем по оси их встречи (рис. 9.9, б). Для дезориентации структуры в корне шва угловых соединений рекомендует делать зазор (рис. 9.9, г). Это приводит к уменьшению интенсивности теплоотвода, отсутствию концентратора напряжений и, соответственно, снижению вероятности образования горячей трещины по сравнению с соединением без зазора (рис. 9.9, в).
Уменьшение деформаций, возникающих в результате термического цикла сварки
Снижение силового фактора, возникающего в результате термического цикла сварки, уменьшение усадочных деформаций и жесткости закрепления свариваемых кромок достигается ограничением силы сварочного тока, заполнением разделки швами небольшого сечения и применением соответствующих конструкций разделок. Этому же способствует хорошая заделка кратера при обрыве дуги.
При сварке аустенитных сталей возможно образование холодных трещин в процессе остывания сварных швов в интервале температур 500–700 °С, а также при комнатной температуре спустя некоторое время после сварки. Причинами образования холодных трещин являются фазовые превращения, связанные с образованием σ-фазы и мартенсита. Холодные трещины имеют внутрикристаллитный характер, очагами их образования могут быть горячие трещины. Для уменьшения вероятности образования холодных трещин сварку рекомендуется производить после аустенизации основного металла, а упрочняющую термическую обработку проводить после сварки.
На свариваемость аустенитных сталей значительное влияние также оказывают их теплофизические свойства: низкий коэффициент теплопроводности, высокий коэффициент линейного расширения, высокое удельное электросопротивление.
Пониженный коэффициент теплопроводности при равных остальных условиях значительно изменяет распределение температур вшве и околошовной зоне (рис. 9.10), в результате одинаковые изо-
171
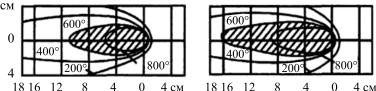
термы в высоколегированных сталях более развиты, чем в углеродистых. Низкий коэффициент теплопроводности приводит к увеличению глубины проплавления основного металла, а с учетом повышенного коэффициента теплового расширения возрастает и коробление изделий. Для уменьшения коробления изделий аустенитных сталей следует применять способы и режимы сварки, характеризующиеся максимальной концентрациейтепловойэнергии.
а б
Рис. 9.10. Температурныеполяприодинаковойпогоннойэнергии итолщинеметаллаприсваркеуглеродистой(а) иаустенитной(б) сталей
Более высокое удельное электросопротивление, примерно в пять раз выше чем у углеродистых сталей, обусловливает большой разогрев сварочной проволоки в вылете электрода или металлического стержня электрода для ручной дуговой сварки. При автоматической и полуавтоматической дуговой сварке следует уменьшать вылет электрода и повышать скорость его подачи. При ручной дуговой сварке уменьшают длину электродов и допустимую плотность сварочного тока.
9.4.3. Склонность к межкристаллитной коррозии при эксплуатации
Подавляющие большинство высоколегированных аустенитных сталей используются в качестве коррозионно-стойких материалов для работы в жидких и газообразных агрессивных средах. Основным требованием, которое предъявляется к сварным соединениям, является стойкость к различным видам корро-
172

зии. Аустенитные стали обладают хорошей коррозионной стойкостью к общей коррозии, но склонны к межкристаллитной коррозии при эксплуатации и коррозионному растрескиванию под напряжением.
Межкристаллитная коррозия может развиваться на трех участках сварного соединения: в металле шва, по линии сплавления (ножевая коррозия) и на определенном участке зоны термического влияния (рис. 9.11, 9.12). Механизм развития этих видов коррозии одинаков, однако причины возникновения названных видов межкристаллитной коррозии различны.
Межкристаллитная коррозия в металле шва возникает в результате выделения из аустенита под действием термического цикла сварки карбидов хрома, приводящих к обеднению хромом приграничных объемов зерен. Основными причинами этого являются повышенное содержание в металле шва углерода и отсутствие или недостаточное содержание титана или ниобия. Стойкость шва к межкристаллитной коррозии уменьшается в результате длительного воздействия нагрева при неблагоприятном термическом цикле сварки или эксплуатации изделия.
Рис. 9.11. Примеры межкристаллитной коррозии сварных соединений: а – однопроходный шов; б – многопроходный шов; в – коррозия по линии сплавления
173
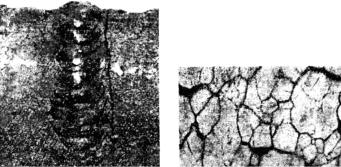
а |
б |
Рис. 9.12. Межкристаллитная коррозия в зоне термического влияния: а – внешний вид разрушения; б – микроструктура
Межкристаллитная коррозия в основном металле по линии сплавления (ножевая коррозия) поражает узкую полоску стали, которая в результате термического цикла сварки нагревается до температур выше 1250 °С. Этому виду коррозии могут подвергаться стали, стабилизированные титаном и ниобием. При нагреве таких сталей выше 1250 °С карбиды титана и ниобия растворяются в аустените. Повторное тепловое воздействие на этот металл критических температур 500–800 °С (например, при многослойной сварке) приведет к сохранению титана и ниобия в твердом растворе и выделению по границам зерен карбидов хрома.
Межкристаллитная коррозия в зоне термического влияния на некотором расстоянии от шва вызвана действием термического цикла сварки. По обе стороны от шва располагаются участки основного металла, которые в результате сварки нагреваются до критических температур 850–450 °С, вызывающих выделение по границам зерен избыточных фаз (например, Cr23C6). Если содержание хрома в пограничных краях зерен аустенита ниже порога химической устойчивости (≈ 12 %), то агрессивный реагент растворяет обедненный хромом металл и развивается межкристаллитная коррозия (рис. 9.13).
174
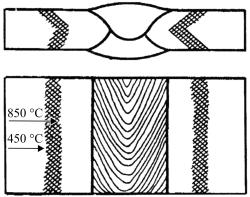
Рис. 9.13. Схема межкристаллитной коррозии в зоне термического влияния
Для снижения склонности аустенитных сталей к межкристаллитной коррозии в шве и зоне термического влияния следует:
1)снизить содержание углерода до пределов его растворимости в аустените (0,02–0,03 %);
2)дополнительно легировать металл шва более энергичными, чем хром, карбидообразующими элементами (стабилизация титаном, ниобием, танталом, ванадием и др.);
3)после сварки проводить стабилизирующий отжиг при температурах 850–900 °С в течение 2–3 ч или аустенизацию закалкой
стемператур 1050–1100 °С;
4)создать в структуре металла шва аустенитно-ферритную структуру путем дополнительного легирования хромом, кремнием, молибденом, алюминием и др.
Аустенитно-ферритные швы со сплошной структурой и извилистыми очертаниями границ зерен имеют повышенную стойкость к межкристаллитной коррозии по сравнению с аустенитными. Возрастание протяженности границ зерен вследствие измельчения зерен увеличивает площадь поверхности, на которой выделяются карбиды. Выделяющиеся карбиды более дисперсны, и местное обеднение объема зерна хромом происходит на меньшую
175
глубину. Кроме того, процессы диффузии в феррите происходят значительно быстрее, что ускоряет выравнивание концентрации хрома в обедненных приграничных и центральных участках зерен. Однако высокое содержание в структуре феррита (до 20–25 %) может понизить стойкость металла к общей коррозии.
Общая коррозия, т.е. растворение металла в коррозионной среде, может развиваться в металле шва, на различных участках или в околошовной зоне в целом, и в основном металле. В некоторых случаях наблюдается равномерная общая коррозия основного металла и сварного соединения.
Имеется еще один вид коррозионного разрушения – коррозионное растрескивание, возникающее под совместным действием растягивающих напряжений и агрессивной среды. Развивается как межкристаллитное, так и транскристаллитное разрушение. Снижение остаточных сварочных напряжений – одна из основных мер борьбы с этим видом коррозионного разрушения.
9.5. СВАРКА АУСТЕНИТНЫХ СТАЛЕЙ
Газовая сварка
Газовая сварка приводит к образованию большой зоны разогрева, значительному перегреву расплавленного металла и замедленному охлаждению сварного соединения. В сварных соединениях образуются большие коробления, также при этом происходит значительный угар легирующих элементов, поэтому газовая сварка наименее благоприятна, особенно для сварки кислотостойких сталей, в которых может развиваться значительная межкристаллитная коррозия. Газовая сварка может использоваться для сварки жаропрочных и жаростойких сталей толщиной 1–2 мм. Сварка обычно ведется нормальным пламенем с мощностью пламени 70–75 л/ч на 1 мм толщины. Процесс следует вести с возможно большей скоростью левым способом, мундштук держать под углом 45° к поверхности.
176
Ручная дуговая сварка
При выборе электродов для сварки высоколегированных аустенитных сталей необходимо учитывать тип сварного соединения, пространственное положение при сварке с учетом изменения глубины проплавления основного металла и количества наплавленного металла. Применяемые электроды должны обеспечить необходимое содержание в металле шва феррита для предупреждения образования горячих трещин и получения необходимой жаропрочности и коррозионной стойкости швов. Чаще всего применяют электроды с фтористокальциевым (основным) покрытием, уменьшающим угар легирующих элементов. Примеры применяемых электродов представлены в табл. 9.1.
Уменьшению угара легирующих элементов способствует и поддержание короткой дуги без поперечных колебаний электрода. Это снижает вероятность появления дефектов на поверхности основного металла в результате попадания на него брызг.
Тип покрытия электрода диктует необходимость применения постоянного тока обратной полярности (при переменном или постоянном токе прямой полярности дуга неустойчива).
Величину сварочного тока выбирают так, чтобы отношение его к диаметру электрода не превышало 25–30 А/мм. В потолочном и вертикальном положениях сварочный ток уменьшают на 10–30 % по сравнению с током, выбранным для нижнего положения сварки.
Сварку покрытыми электродами рекомендуется выполнять ниточными швами, и для повышения стойкости к горячим трещинам применять электроды диаметром 3 мм. Во всех случаях следует обеспечивать минимальное проплавление основного металла. Электроды перед сваркой должны быть прокалены при 250–400 °С в течение 1–1,5 ч для уменьшения вероятности образования в швах пор, вызываемых водородом, и трещин.
Некоторые данные о режимах для ручной дуговой сварки приведены в табл. 9.2, а свойствах сварных соединений – в табл. 9.3.
177

Таблица 9 . 1
Некоторые марки электродов для сварки высоколегированных аустенитных сталей
Маркастали |
Марка |
Типэлектродов |
Структура |
|
наплавленного |
||||
электродов |
поГОСТ10052–75 |
|||
|
|
|
металла |
|
|
Коррозионно- |
стойкиестали |
|
|
08Н18Н10,08Х18Н10Т, |
ЦЛ-11, ОЗЛ-7, |
Э-04Х20Н9, |
Аустенитно- |
|
ОЗЛ-8, ОЗЛ-22, |
Э-07Х20Н9, |
ферритная |
||
12Х18Н10Т, 08Х18Н12Т, |
ОЗЛ-36 |
Э-08Х19Н10Г2Б |
с2,5–7 % α-фазы |
|
08Х18Н12Б, 08Х22Н6Ти |
||||
|
|
Аустенитно- |
||
подобные, работающиев |
ОЗЛ-7, |
|
||
Э-08Х20Н9Г2Б |
ферритная |
|||
агрессивныхсредах |
АНВ-13 |
|||
|
с5,0–10 % α-фазы |
|||
|
|
|
||
Работающиепри |
|
|
Аустенитно- |
|
Л-38М |
Э-02Х19Н9Б |
ферритная |
||
температурахдо600 °С |
||||
|
|
с3,0–5,0 % α-фазы |
||
|
|
|
||
10Х17Н13М2Т, |
СЛ-28, |
Э-8Х19Н10Г2МБ, |
Аустенитно- |
|
10Х17Н13МЗТ, |
ОЗЛ-20, |
ферритная |
||
Э-09Х19Н10Г2М2Б |
||||
08Х18Н12Б, |
ОЗЛ-41 |
|
с4,0–5,0 % α-фазы |
|
08Х2IH6M2T иподоб- |
|
|
Аустенитно- |
|
ные, работающиепри |
НЖ-13 |
Э-09Х19Н10Г2М2Б |
ферритная |
|
температурахдо700 °С |
|
|
с4,0–8,0 % α-фазы |
|
|
Жаропрочные |
стали |
|
|
12Х18Н9,12Х18Н10Т, |
|
ЭА-1М2, |
Аустенитно- |
|
08Х18Н12Т, работающие |
ЦТ-15, |
|||
Э-08Х16Н8М2, |
ферритная |
|||
притемпературахдо |
ЦТ-26 |
|||
Э-08Н17Н8М2 |
с2,0–4,0 % феррита |
|||
800 °С |
|
|||
|
|
|
||
10Х23Н18 иподобные, |
|
|
Аустенитно- |
|
ОЗЛ-4, |
|
ферритнаяссодер- |
||
работающиепритемпе- |
Э-10Х25Н13Г2 |
|||
ратурахвыше850 °С |
ОЗЛ-6 |
|
жаниемферрита |
|
|
|
неменее2,5 % |
||
|
|
|
||
|
Жаростойкие |
стали |
|
|
Х20Н14С2, 20Х20Н14С2, |
|
|
Аустенитно- |
|
20Х25Н20С2, работаю- |
ОЗЛ-6, |
|
||
Э-12Х24Н14С2 |
ферритная |
|||
щиепритемпературах |
ОЗЛ-31М |
|||
|
с3–10 % α-фазы |
|||
900–1100 °С |
|
|
||
|
|
|
||
20Х25Н20С2, |
|
|
|
|
4Х18Н25С2, работающие |
ОЗЛ-5, |
Э-28Х24Н16Г6 |
Аустенитно- |
|
притемпературахдо |
ОЗЛ-9-1 |
карбидная |
||
|
||||
1050 °С |
|
|
|
178
Таблица 9 . 2
Ориентировочные режимы ручной дуговой сварки аустенитных сталей
Толщина |
Электрод |
Силасварочноготока(А) |
||||
материала, |
приположениисварки |
|||||
|
|
|||||
мм |
Диаметр, мм |
Длина, мм |
нижнем |
вертикальном |
потолочном |
|
До2,0 |
2 |
150–200 |
30–50 |
− |
− |
|
2,5–3,0 |
3 |
225–250 |
70–100 |
50–80 |
45–75 |
|
3,0–8,0 |
3–4 |
250–300 |
85–140 |
75–130 |
65–120 |
|
8,0–12,0 |
4–5 |
300–400 |
85–160 |
75–150 |
65–130 |
|
|
|
|
|
|
Таблица 9 . 3 |
|
Типичные механические свойства металла шва |
|||||||
|
при комнатной температуре |
|
|
||||
|
|
|
|
|
|
|
|
Маркаэлектрода |
σт, МПа |
|
σв, МПа |
|
δ, % |
|
Ударнаявяз- |
|
|
|
кость, Дж/см2 |
||||
|
Коррозионно-стойкиестали |
|
|
||||
ЦЛ-11 |
360 |
|
600 |
|
24 |
|
70 |
ОЗЛ-7 |
400 |
|
640 |
|
25 |
|
100 |
Л-38М |
300 |
|
600 |
|
30 |
|
90 |
Л-40М |
350 |
|
600 |
|
24 |
|
70 |
СЛ-28 |
– |
|
600 |
|
38 |
|
120 |
НЖ-13 |
450 |
|
600 |
|
26 |
|
100 |
|
|
Жаростойкиестали |
|
|
|
||
ОЗЛ-5 |
350 |
|
600 |
|
25 |
|
60 |
ОЗЛ-6 |
350 |
|
570 |
|
33 |
|
100 |
ОЗЛ-9-1 |
500 |
|
650 |
|
12 |
|
50 |
Сварка под флюсом
Сварка под флюсом является одним из основных процессов сварки высоколегированных сталей толщиной 3–50 мм при производстве химической и нефтехимической аппаратуры. Основным преимуществом этого способа перед ручной дуговой сваркой покрытыми электродами является стабильность состава и свойств металла по всей длине шва при сварке как с разделкой, так и без разделки кромок. Это обеспечивается возможностью получения шва
179
любой длины без кратеров, образующихся при смене электродов, равномерностью плавления электродной проволоки и основного металла по длине шва и более надежной защитой зоны сварки от окисления легирующих компонентов кислородом воздуха.
Хорошее формирование поверхности швов с мелкой чешуйчатостью и плавным переходом к основному металлу, отсутствие брызг на поверхности изделия заметно повышают коррозионную стойкость сварных соединений. Уменьшается трудоемкость подготовительных работ, так как разделку кромок производят на металле толщиной свыше 12 мм (при ручной сварке – на металле толщиной 3–5 мм). Возможна сварка с повышенным зазором и без разделки кромок стали толщиной до 30–40 мм. Уменьшение потерь на угар, разбрызгивание и огарки электродов на 10–20 % снижает расход дорогостоящей сварочной проволоки.
Техника и режимы сварки аустенитных сталей имеют ряд особенностей по сравнению со сваркой обычных низколегированных сталей. Для предупреждения перегрева металла и связанного с этим укрупнения структуры, возможности появления трещин
иснижения эксплуатационных свойств сварного соединения рекомендуется выполнять сварку швами небольшого сечения. Это обусловливает применение сварочных проволок диаметром 2–3 мм, а с учетом высокого электросопротивления аустенитных сталей – необходимость уменьшения вылета электрода в 1,5–2 раза. Аустенитные сварочные проволоки в процессе изготовления сильно наклепываются и имеют высокую жесткость, что затрудняет работу правильных, подающих и токоподводящих узлов сварочных установок, снижая срок их службы.
Шов легируют через флюс или проволоку. Последний способ более предпочтителен, так как обеспечивает повышенную стабильность состава металла шва. Для сварки под флюсом аустенитных сталей и сплавов используют сварочные проволоки, выпускаемые по ГОСТ 2246–70 и по ведомственным техническим условиям,
инизкокремнистые фторидные и высокоосновные бесфтористые флюсы, создающие в зоне сварки безокислительные или малоокис-
180