
Плазменная обработка материалов
..pdfмаксимальна (в 3–4 раза выше, чем в аргоне), это значит, что только за счет увеличения анодного падения величина удельного теплового потока (определяющего в основном режим резки) в анодной области может быть увеличена в несколько раз.
Напряженность поля в водородной дуге также в 2–3 раза выше, чем в аргоновой. Благодаря более высокому значению напряженности поля при одном и том же токе в водородной дуге выделяется значительно большее количество тепла. Следовательно, в водородной дуге обеспечиваются наилучшие условия для преобразования электрической энергии в тепловую.
Теплопроводность водорода также значительно выше, чем у всех остальных газов (см. рис. 29), что обеспечивает максимальное использование тепловой энергии, выделившейся в дуге.
К тому же водород не дорог и не дефицитен. Несмотря на это, водород не нашел промышленного применения в качестве самостоятельного плазмообразующего газа. Стабильная работа обеспечивается только при больших значениях отношения величины диаметра сопла к величине тока, в результате чего не удалось добиться высоких скоростей резки.
Кроме того, как и при резке в кислороде, оказалось, что скорость при прочих равных условиях в одном водороде ниже, чем в смесях аргона с водородом или азота с водородом. Но даже при столь низких значениях скорости резки стабильность горения водородной дуги значительно ниже, чем дуги, горящей в смесях на основе водорода.
Лучшие характеристики достигаются при использовании ряда газовых смесей (например, водородсодержащие, кислородосодержащие).
Воздух. Экономично использовать плазмотроны, работающие на воздухе (смесь Н2-О2-N2). Проникающая способность воздушной плазмы более высокая, чем у азота, так как содержащийся в составе воздуха кислород обладает высоким теплосодержанием и, кроме того, он окисляет металл с выделением значительной тепловой энергии. При этом происходит заметное сокращение ширины реза и уменьшение скоса кромок.
Вода может быть использована в качестве плазмообразующей среды. Вода при высокой температуре столба дуги частично превращается в пар, а частично диссоциирует на водород и кислород. Энергетические параметры дуги позволяют отнести воду к водородсодержащим смесям, а качество резки указывает на то, что кислород активно
61
взаимодействует с выплавляемым металлом. При использовании воды наблюдается повышенный расход электрода (чаще используется угольный), что требует применения механизма подачи электрода. Воду используют также как добавку к основному плазмообразующему газу в небольших количествах; ее вводят в столб плазменной дуги в канале сопла или на его нижнем срезе.
4.3. ПЛАЗМОТРОНЫ ДЛЯ ПЛАЗМЕННОЙ РЕЗКИ
Установка для плазменной резки состоит из источника питания с аппаратурой управления процессом резки и плазмотрона, основными элементами которого являются электрод и сопло.
По назначению режущие плазмотроны подразделяются на машинные и ручные. Машинные плазмотроны работают от источников питания с напряжением холостого хода до 300 В при величине рабочего тока 250–500 А и выше.
Ручные плазмотроны для обеспечения безопасности работают при напряжении холостого хода источника не более 180 В, величине рабочего тока до 250 А и мощности дуги до 30 кВт. Толщина разрезаемого металла не превышает 40 мм при использовании в качестве плазмообразующей среды сжатого воздуха. Применяются ручные плазмотроны на монтажных работах, при утилизации металлических конструкций, при обработке отливок и при резке листового проката в малых объемах.
Наиболее широко применяются плазмотроны с дугой прямого действия.
По роду используемого тока наиболее распространены режущие плазмотроны постоянного тока, отличающиеся лучшей стабильностью горения дуги. Проведены исследования режущих плазмотронов на пульсирующем токе; исследуются также возможности применения переменного тока промышленной частоты.
По роду применяемой рабочей среды можно выделить три основных типа плазмотронов: с окислительным рабочим газом, с нейтральным рабочим газом и с использованием воды в качестве плазмообразующей среды. Из газов, нейтральных по отношению к рабочему электроду, наибольшее применение получили аргон, азот, водород и их смеси. Экономично использовать плазмотроны, работающие на воздухе. Интерес представляют плазмотроны, рабочей средой которых является вода.
62
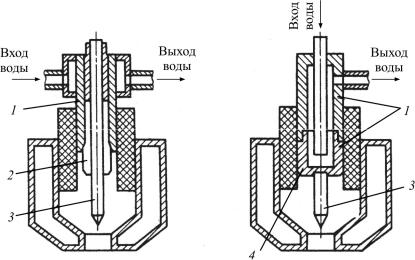
Электроды плазмотрона по типу и конструкции зависят от состава плазмообразующей среды, используемой при резке. Для работы в нейтральных плазмообразующих средах используются термокатоды – это катоды, имеющие высокую эмиссионную способность при нагреве до температуры ниже температуры плавления. Типичным примером такого катода является вольфрам и вольфрам с добавками, повышающими плотность тока термоэлектронной эмиссии (лантан, иттрий, торий).
Конструктивно электроды из вольфрама выполняются двумя способами: в виде прутка, который фиксируется цанговым зажимом, закрепленным в электродном узле плазмотрона (рис. 30, а), и в виде медной державки с заделанным в нее стержнем вольфрама, закрепленным в электродном узле (рис. 30, б).
а |
б |
Рис. 30. Плазмотроны с вольфрамовым катодом
Последняя конструкция предпочтительней, так как позволяет получать более высокие плотности тока на катоде благодаря лучшим условиям теплоотвода. Она также более экономична с точки зрения расхода вольфрама, поскольку при эксплуатации вольфрамового прутка его часть, находящаяся в цанговом зажиме, не используется.
В качестве материала для электродов, работающих в кислородсодержащих средах, используются гафний и цирконий, так как его соединения обладают высокими эмиссионными свойствами, устойчивы тер-
63

мически к колебаниям токового и газового режимов, а также условий охлаждения (табл. 4).
Таблица 4 Свойства материалов, применяемых для изготовления катодов
Металл |
Температура плавления, К |
Работа выхода, эВ |
|||
Металл |
Нитрид |
Оксид |
|||
|
|
||||
Вольфрам |
3650 |
– |
1742 |
(торированный) 2,63 |
|
Цирконий |
2125 |
3255 |
2950 |
(оксид) 5,8; (нитрид) 2,92 |
|
Гафний |
2488 |
3580 |
3063 |
(оксид) 3,53; (нитрид) – |
Теплофизические константы гафния и циркония и его соединений существенно ниже соответствующих теплофизических констант вольфрама: теплопроводность в 3–4 раза, а температура плавления – в 2 раза. В связи с этим для улучшения теплоотвода от активной катодной вставки из гафния ее помещают заподлицо в медную державку. Исходя из необходимости обеспечения максимального ресурса работы таких катодов создается и конструкция медной державки: в частности, диаметр ее торцовой части не может быть меньше определенной величины для заданного тока дуги. Объясняется это тем, что величина допустимого теплового потока, проходящего через материал активной вставки, зависит от радиуса медной державки. Стабилизация дуги – вихревая (тангенциальная). При нарушении четкой вихревой подачи плазмообразующего газа катодное пятно вместе со столбом дуги будет смещаться от центра катодной вставки, что приводит к нестабильному горению сжатой дуги, двойному дугообразованию и выходу плазматрона из строя.
Технология изготовления электрода должна обеспечивать гарантированный тепловой и электрический контакт между медью и гафнием по всей поверхности активной вставки в течение всего времени ее работы. Наиболее полно этим требованиям отвечает метод совместной холодной штамповки активной вставки и медной державки (рис. 31, а).
Для предотвращения расплавления стенок медной державки под воздействием теплового потока столба дуги и для повышения ресурса работы электрода между активной гафниевой вставкой и медной державкой делается алюминиевая прокладка толщиной 0,05–0,15 мм.
64
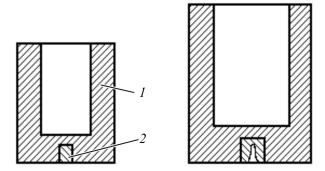
а |
б |
Рис. 31. Схема катода с активной вставкой: а – обойма 1 с впрессованной вставкой 2; б – и кратер на катодной вставке
Катод работает следующим образом. При подаче напряжения на электрод и возбуждении сжатой дуги на поверхности торца катодной вставки (в зоне привязки катодного пятна) материал катода расплавляется. Вследствие взаимодействия расплавленного металла с кислородом
иазотом воздуха образуются тугоплавкие оксиды и нитриды в виде пленки золотистого цвета, эта пленка защищает материал катодной вставки от дальнейшего разрушения. Эта особенность циркония и гафния образовывать пленки оксидов при высоких температурах позволила назвать такие катоды «пленочными».
Материал катодной вставки под действием дуги испаряется, а поверхность вставки в зоне действия катодного пятна имеет температуру, не превышающую точку кипения расплава (для двуоксида циркония 4583 К). В интервале температур от точки плавления до точки кипения дуговой разряд может существовать беспрепятственно, так как электропроводность оксидной пленки высокая. Однако неравномерное распределение тепловой нагрузки в зоне действия катодного пятна приводит к неравномерному испарению металла на рабочей поверхности вставки. Поверхность катода в этой зоне приобретает вид кратера (рис. 31, б). Кроме естественного износа путем испарения унос металла вставки из кратера происходит во время последующих возбуждений сжатой дуги. При возбуждении дуги пленка частично отслаивается, расплавляется
ииспаряется. При этом происходит разбрызгивание материала пленки
ициркония. По мере роста числа включений износ вставки увеличивается и она, после определенного числа включений, становится непригодной для дальнейшего использования. Продолжительность работы
65
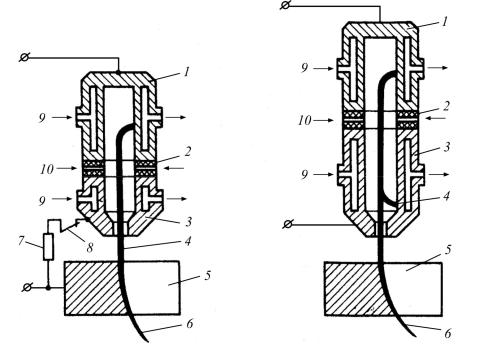
катодной вставки задается количеством включений сжатой дуги. Ресурс электрода при силе тока 200–300 А и диаметре сопла 3 мм составляет 1,5–3 ч суммарного времени горения дуги.
С целью повышения стойкости электрода и расширения технологических возможностей плазменной резки были разработаны плазмотроны с полым медным электродом. Режущие плазмотроны с полым медным электродом могут быть прямого и косвенного действия (рис. 32). Они состоят из полого внутреннего электрода, завихрителя
исоплового электрода. Завихритель расположен между электродом
исоплом и изготовляется из изолирующего материала или из меди с изолирующими прокладками. У плазмотронов для дуги косвенного действия сопловый электрод удлинен.
а |
б |
Рис. 32. Принципиальные схемы плазмотронов с медными полыми электродами: а – с дугой прямого действия; б – с дугой косвенного действия: 1 – полый внутреннийэлектрод; 2 – завихритель; 3 – сопловая часть; 4 – дуга; 5 – металл; 6 – струя плазмы; 7 – балластное сопротивление; 8 – контактор; 9 – подача охлаждающей воды;
10 – подача воздуха
66
Отличительной особенностью полых электродов является интенсивное перемещение опорного пятна дуги по сильно охлаждаемой поверхности электрода, которое осуществляется под действием газового циклона, создаваемого тангенциальными отверстиями в завихрителе иналичием соленоида на внешней поверхностиплазмотрона. При этомобеспечивается стабильное положение столба дуги по оси полости электрода и не допускается локальный нагрев электрода и сопла. Интенсивное наружное охлаждение обеспечивает длительный срокслужбыэлектродов.
Полыеэлектродыимеютневысокуютемпературунагрева(420–470 К), и в качестве рабочего газа может быть использован сжатый воздух. В отличие от плазмотронов с гафниевым или циркониевым катодом плазмотрон с полым электродом имеет увеличенный ресурс работы (примерно 40 ч), а также обладает более высокими мощностью и производительностью.
К недостаткам плазмотронов с полым электродом можно отнести необходимость использования источников питания сварочного тока с напряжением холостого хода Ux.x ≈ 500 В. Рабочее напряжение при резке составляет порядка Uд ≈ 300 В. Плазмотроны с полым электродом из-за наличия соленоида имеют повышенные габариты и массу. Это усложняет оборудование, снижает условия электробезопасности работ, при этом исключается возможность использования этогоспособа дляручнойрезкиметаллов.
Сопло наряду с катодом является основным элементом плазмотрона. К главным характеристикам сопла относятся диаметр отверстия, его высота, геометрия теплоотводящей поверхности. Диаметр и высота отверстия полностью определяют технологические возможности плазмотрона (толщину разрезаемых листов, скорость и качество резки), эффективность использования электрической мощности дуги, надежность работы плазмотрона (рис. 33). Геометрия сопла связана с остальными параметрами: током, составом и расходом плазмообразующей среды, природой разрезаемого металла, толщиной листов, скоростью резки и т.д. Оптимизация конструктивного оформления сопла позволяет достичь максимальной концентрации режущего участка столба сжатой дуги при высоком ресурсе работы катода и сопла (см. рис. 33).
Исходным размерным параметром является диаметр канала сопла dс, который выбирается из оптимальной плотности тока. Последняя равна 40–70 А/мм2 для Iд = 100…300 А в плазмотронах с водяным охлаждением и соответственно 40–45 А/мм2 для Iд ≤ 150 А в плазмотронах с воздушным охлаждением.
67

Рис. 33. Конструктивные параметры плазмообразующего сопла плазмотрона для резки: 1 – электрод; 2 – сопло; 3 – разрезаемый металл; rс = (0,9…2,2) dс, rэ = (0,9…1,2) dс, dэ = (4…5) dс,
hк.с = (3,5…4,5) dс, lс = (1,5…2,0) dс, δ = (0,2…0,4) dс
Экспериментальное исследование влияния высоты канала сопла на технологические характеристики резки (скорость и качество) и надежность работы плазмотрона показало, что чем длиннее канал, тем больше скорость и выше качество резки, но тем ниже надежность работы плазмотрона.
Теплофизический анализ работы различных материалов и практика резки показывают, что наилучшим материалом для сопла является медь. Исследования показали, что допустимое значение теплового потока на внутреннюю поверхность канала сопла можно увеличить почти в полтора раза, если покрыть эту поверхность вольфрамом. Однако при этом высоту канала сопла приходится уменьшать в сравнении с высотой медного сопла в связи с увеличением вероятности двойного дугообразования.
Вероятность двойного дугообразования в этом случае увеличивается вследствие повышения температуры на внутренней поверхности со-
68
пла, что приводит к уменьшению потенциала пробоя слоя между столбом дуги и стенками канала. Кроме того, увеличение температуры приводит к уменьшению анодного падения напряжения. И наконец, величина катодногопадениянапряжениянавольфрамесущественнониже, чемнамеди.
4.4.РАЗНОВИДНОСТИ ПЛАЗМЕННОЙ РЕЗКИ
Внастоящее время известны и находят промышленное применение несколько разновидностей плазменной резки металлов. Среди них: резка с использованием инертных газов в качестве плазмообразующей среды, воздушно-плазменная резка плазмотронами с термохимическими
(пленочными) катодами, воздушно-плазменная резка плазмотронами с полым электродом, резка плазмотронами с комбинированной подачей инертного (для защиты вольфрамового электрода) и окислительного (режущего) газов. Известны способы резки плазмой, стабилизированной водой, воздушно-водяной плазмой, узкоструйной плазмой. Для резки неэлектропроводных материалов применяется резка косвенной сжатой дугой (плазменной струей).
Наибольший объем применения приходится на воздушноплазменную резку на прямой полярности с использованием пленочных (термохимических) катодов. Воздушно-плазменная резка (ВПР) явилась следствием развития резки металлов инертной азотной плазмой и резки азотно-кислородной смесью. Было установлено, что добавки кислорода к азоту до 25 % позволяют повысить скорость резки (более чем на 50 %) за счет экзотермических реакций. Дальнейшее повышение содержания кислорода (до 100 %) повышает скорость резки всего на 10–15 %. Воздух, как плазмообразующий режущий газ, представляет собой природную смесь 78 % азота и 21 % кислорода и, наряду с очевидными экономическими преимуществами (в сравнении с инертными к вольфраму газами), обладает высокими теплофизическими показателями, поэтому применение воздуха в качестве плазмообразующей среды стало очевидным. Воздушно-плазменная резка (ВПР) характеризуется сложными явлениями преобразования электрической энергии источника тока в тепловую энергию сжатой дуги (рис. 34).
Столб дуги интенсивно сжимается в формирующей камере плазмотрона, обеспечивает сквозное проплавление разрезаемого металла и выдувает расплав из полости реза. Наличие кислорода в воздухе при резке сталей дает дополнительный тепловой эффект за счет экзотермической реакции окисления железа.
69
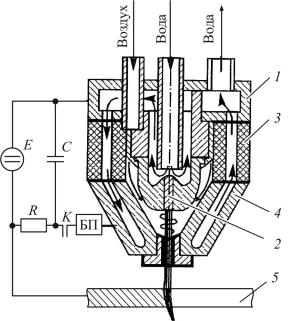
Рис. 34. Схема воздушно-плазменной резки:
1 – катодный узел плазмотрона; 2 – катод с накидной гайкойзавихрителем; 3 – изоляционный корпус плазмотрона;
4 – сопловой узел; 5 – разрезаемое изделие
Возможность применения ВПР была предопределена разработкой термохимических (пленочных) катодов, стойких в агрессивной окислительной среде. Механизм работы термохимических катодов обусловлен возникновением при взаимодействии циркония (гафния) с воздухом в процессе горения дуги тугоплавкой пленки из нитрида и диоксида циркония (гафния) на торце активной вставки, запрессованной в медную обойму. Образующаяся на торце вставки пленка приобретает высокие эмиссионные свойства и, благодаря этому, а также высоким значениям температуры плавления и кипения, обеспечивает устойчивое существование воздушно-плазменной дуги на катодном опорном пятне.
ВПР имеет высокую тепловую эффективность и обеспечивает высокую скорость резки углеродистых сталей, цветных металлов и сплавов, при экономичности процесса.
Однако ВПР имеет существенный недостаток. При обрыве дуги пленка быстро остывает, дает усадку и растрескивается, а при последующих включениях дуги из-за термоудара частично или полностью скалывается. В результате ресурс работы термохимического катода определя-
70