
Плазменная обработка материалов
..pdf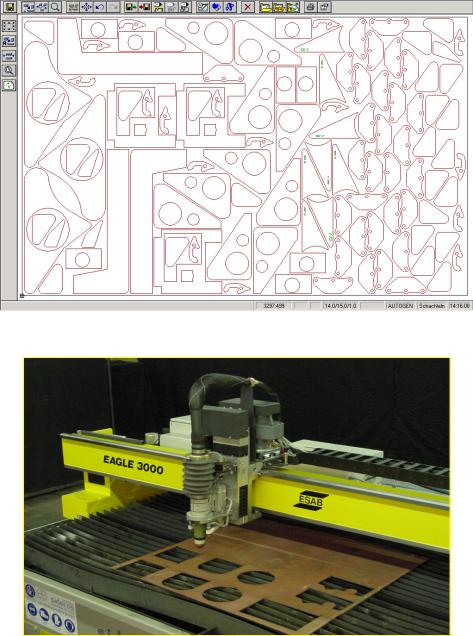
Рис. 40. Пример программного раскроя металла для плазменной резки
Рис. 41. Установка с ЧПУ для прецизионной плазменной резки
Высокая эффективность и производительность обеспечиваются высокоточной механикой, современным ЧПУ и модульным исполнением. Недостатком таких машин является высокая стоимость.
81
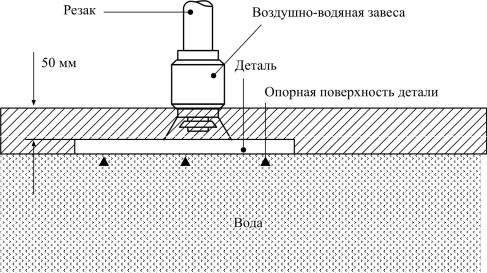
4.7. УСЛОВИЯ БЕЗОПАСНОСТИ ПРИ ПЛАЗМЕННОЙ РЕЗКЕ
ГОСТ 12221–79 определяет допустимое напряжение холостого хода источника питания для полуавтоматической плазменной резки не более 300 В, а для машинной – 500 В. Кроме того, дополнительно предусмотрено автоматическое отключение напряжения выпрямителя при обрыве дуги, а также защитная изоляция наружной поверхности металлического корпуса и соплового узла.
Процессы плазменной резки сопровождаются в разной степени газопылевыделениями, шумом и световым излучением. При резке на токах 150 А и выше металлов толщиной более 20 мм шум и газопылевыделения заметно возрастают. Для защиты плазморезчика в этих условиях следует применять защитные средства электросварщика, а при резке металлов толщиной свыше 40 мм – и шумозащитные наушники (уровень шума превышает 100 дБ). При работе в цеховых условиях обязательно использование на рабочем участке эффективной местной вытяжной и общеобменной цеховой вентиляции.
Ванна воды для опоры обрабатываемой детали и душирование вокруг горелки значительно улучшают условия труда. Плазменная резка под водой сводит до минимума проникновение тепла в обрабатываемую деталь и загрязнение окружающей среды (рис. 42).
Рис. 42. Схема резки над и под водой
82
Пыль и дым в значительной степени отбираются водой. Исходящий от дуги ультрафиолетовый свет также абсорбируются водой, отпадает необходимость в мерах защиты. Рез производится под водой на глубине 70–80 мм (50 мм, если режущий газ – кислород). При опускании горелки в начале каждой операции резания должно быть соблюдено условие, что сопло горелки подводится на выбранное определенное расстояние к поверхности обрабатываемой детали, чтобы можно было зажечь дугу.
При резке под водяным колоколом уровень воды в ванне снижается, чтобы только нижняя сторона детали находилась в воде (см. рис. 42). На горелке дополнительно смонтирован душ, с помощью которого создается водяная завеса вокруг режущего луча. Дым и пыль при этом способе эксплуатации связываются в воде, но уровень шума и величина ультрафиолетового излучения выше, чем при плазменной резке под водой.
ЛАБОРАТОРНАЯ РАБОТА № 4 ИССЛЕДОВАНИЕ ПРОЦЕССА ПЛАЗМЕННОЙ РЕЗКИ МЕТАЛЛОВ
С КОМБИНИРОВАННОЙ ПОДАЧЕЙ ГАЗОВ НА ОБРАТНОЙ ПОЛЯРНОСТИ
Цели работы:
1.Ознакомление с теоретическими и технологическими основами плазменной резки различных металлов и легированных сплавов.
2.Ознакомление с плазмотронами для плазменной резки.
3.Получение навыков практической работы с оборудованием для плазменной резки.
4.Изучение влияния режимов на энергетические и технологические характеристики плазменной резки металлов.
Методика проведения работы
Сущность процесса заключается в следующем (рис. 43). Плазменная резка производится с использованием активных окислительных сред (например, воздуха) на обратной полярности плазмотроном с использованием медного электрода, защищенного в зоне активного пятна дуги инертным газом. Электрод снабжен высокотемпературной вставкой, например из вольфрама.
83
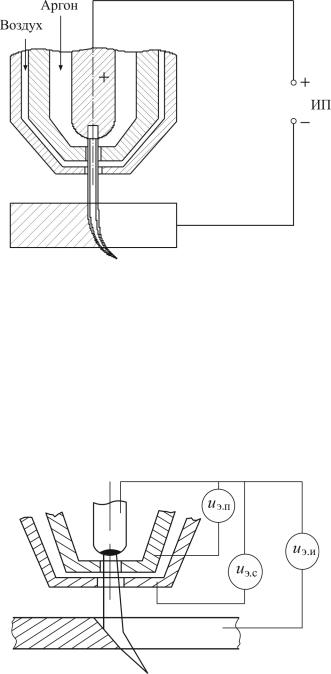
Рис. 43. Схема процесса плазменной резки на обратной полярности с комбинированной подачей газов
В работе измеряется тепловложение в плазмотрон при резке по методике, изложенной в лабораторной работе № 1, определяется распределение энергии в сжатой дуге и исследуется влияние параметров режима на качество и скорость резки.
Для определения суммарной мощности сжатой дуги и отдельных ее участков при проведении экспериментов фиксируются напряжения на различных участках дуги (рис. 44).
Рис. 44. Схемаизмерения падений напряжения научастках сжатойдуги приплазменнойрезке наобратной полярности скомбинированнойподачейгазов
84

Напряжение uэ.и – напряжение дуги; uэ.п – падение напряжения на участке электрод – плазмообразующее сопло, uэ.с – падение напряжения на участке электрод – стабилизирующее сопло
Схема установки для проведения исследований представлена на рис. 45.
Рис. 45. Схема установки для проведения исследований плазменной резки металлов с комбинированной подачей газов: 1 – электрод; 2 – плазмообразующее сопло; 3 – стабилизирующее сопло; 4 – ротаметр водяной; 5 – вентиль подачи воды; 6 – термометры для измерения температуры воды на входе и выходе
из плазмотрона; 7 – ротаметры газовые; 8 – манометры; 9 – баллон с аргоном; 10 – компрессор; 11 – источник питания; 12 – разрезаемый металл
На скорость и качество резки оказывают влияние геометрические параметры плазмотрона и технологические параметры резки, представленные ниже.
Для проведения исследований используется стенд для плазменной резки (рис. 46), скомпонованный на базе станка наплавочного У-653; плазмотроны для резки на обратной полярности с комбинированной подачей газов, сконструированные на кафедре сварочного производства и технологии конструкционных материалов Пермского национального исследовательского политехнического университета; источник питания
85
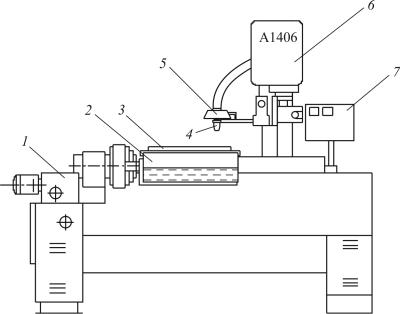
тока резки от установки плазменной резки типа УПР-201. Этот источник имеет высокую надежность и широко применяется для ручной резки металлов, обеспечивая безопасность работ. Основные технические характеристики источника: напряжение холостого хода их.х = 300 В, максимальный рабочий ток Iр = 200 А, период включения ПВ = 100 %.
Параметры режима резки:
Ток сжатой дуги Iд, А |
100; 150; 200 |
Расход аргона QAr, л/мин |
3,0; 5,0; 7,0 |
Расход воздуха QВ, л/мин |
20; 30; 40 |
Диаметр плазмообразующего сопла dп.с, мм |
2,5; 3,0; 3,5 |
Диаметр стабилизирующего сопла dс.с, мм |
2,8; 3,2; 3,5 |
Расстояние электрод – |
0,5; 1,0; |
плазмообразующее сопло hэ.с, мм |
|
Высота плазмообразующего сопла hп.с, мм |
2,5; 3,0; 3,5 |
Высота стабилизирующего сопла hс.с, мм |
2,5; 3,0; 3,5 |
Расстояние между соплами hп.с.с, мм |
1,0; 1,5; 2,0 |
Расстояние от торца плазмотрона до изделия hс.и, мм |
5; 10; 15 |
Рис. 46. Стенд для плазменной резки: 1 – манипулятор; 2 – бак с водой; 3 – разрезаемый металл; 4 – плазмотрон; 5 – воздухосборник системы вентиляции; 6 – каретка; 7 – блок управления
86

Резка выполняется на образцах из малоуглеродистой стали типа Ст. 3, низколегированных сталях: 16Г2АФ, 09Г2С, 10ХСНД, теплоустойчивой стали 15Х5М, нержавеющей стали Х18Н10Т, алюминиевых сплавов АМг6 и АМц, толщина образцов 10; 20; 30 мм.
Контролируется максимальная скорость реза, ширина реза и качество кромок. По результатам исследований определяется тепловложение в плазмотрон Pпл, полная мощность сжатой дуги Pд, мощность части столба дуги, расположенной внутри плазмотрона Pвн.
Рассчитывается погонная энергия реза для различных материалов и толщин по формуле
qп = Pд , vр
где νр – скорость резки.
Порядок выполнения работы
1.Включается пускатель системы управления установки для плазменной резки.
2.Открывается подача воды. Измеряется расход воды Qв через плазмотрон.
3.Измеряется начальная температура воды.
4.Устанавливается разрезаемый образец на решетку, расположенную над баком с водой.
5.Включением перемещения каретки устанавливается плазмотрон на начало реза, регулируется расстояние hс.и.
4.Включается компрессор и устанавливается заданный расход воздуха в стабилизирующее сопло Qв, включается подача и устанавливается расход аргона в плазмообразующее сопло QАr.
5.Включается вытяжная вентиляция воздухозаборника.
6.Включается пускатель источника питания сварочного тока, устанавливается сварочный ток Iд.
7.Возбуждается сжатая дуга и включается перемещение плазмотрона. При контроле сквозного прорезания металла, устанавливается максимальная скорость реза.
8.Измеряется напряжение на дуге и ее участках.
9.Измеряется температура воды на выходе из плазмотрона.
87
10.После окончания реза выключается перемещение плазмотрона, отключается источник питания, компрессор и подача аргона.
11.Измеряется ширина реза и оценивается качество кромок. Проводятся аналогичные измерения при изменении параметров
режима (см. лабораторную работу № 1), данные измерений заносятся
втаблицы.
12.Проводится расчет тепловой мощности, отведенной в плазмо-
трон Pпл.
13.Проводится расчет мощности сжатой дуги и части столба дуги,
расположенного внутри плазмотрона.
14.Рассчитывается погонная энергия реза для различных материалов и толщин.
15.Определяется относительное тепловложение в плазмотрон в зависимости от Pд, Рвн.
16.Оформляются выводы по выполненной работе.
Техника безопасности
1.Работа на стенде для плазменной резки производится под контролем ведущего преподавателя или учебного мастера.
2.Наблюдение за зоной резки в процессе работы производится через сварочный светофильтр.
3.Работа с образцами после резки производится после их полного остывания.
4.Резка производится при включенной вытяжной вентиляции.
5.После выполнения реза производится обязательное выключение источника питания и компрессора.
6.При включении резки высоковольтным высокочастотным разрядом не допускается касание плазмотрона.
Контрольные вопросы
1.Сущность процесса плазменной резки металлов.
2.Особенности взаимодействия сжатой дуги с материалом при плазменной резке.
3.Разновидности плазменной резки металлов.
4.Плазмообразующие среды для плазменной резки.
5.Особенности устройства плазмотронов для плазменной резки.
88
6.Основные режимные параметры плазменной резки.
7.Характерные дефекты плазменной резки металлов.
8.Что такое пленкозащитные катоды?
9.Особенности источников питания для плазменной резки?
10.Для каких толщин возможно применение плазменной резки металлов?
11.Как распределяется энергия в сжатой дуге при плазменной
резке?
12.Какие режимные параметры оказывают наибольшее влияние на скорость резки?
13.Что характеризует погонная энергия резки?
14.Недостатки ВПР.
15.Особенности плазменной резки металлов на обратной полярности.
Список литературы
1.Эсибян Э.М. Воздушно-плазменная резка: состояние и перспективы // Автоматическая сварка. – 2000. – № 12. – С. 6–20.
2.Варгафтик Н.Б. Справочник по теплофизическим свойствам газов и жидкостей. – М.: Физматгиз, 1963. – 708 с.
3.Лакомский В.И. Оксидные катоды электрической дуги. – Запорожье: Интернал, 1997. – 192 с.
4.Исследование и оптимизация электроплазменной резки металлов / Ю.Я. Киселев [и др.]. – Кишинев: Штиинца, 1981. – 112 с.
5.Васильев К.В. Плазменно-дуговая резка. – М.: Машинострое-
ние, 1974. – 111 с.
6.Эсибян Э.М. Плазменно-дуговая аппарутура. – Киев: Техника,
1971. – 162 с.
7.Щицын Ю.Д., Тыткин Ю.М. Плазменная обработка металлов на обратной полярности // Сварка и контроль – 2004: сб. докл. всерос. науч.- техн. конф. / Перм. гос. техн. ун-т. – Пермь, 2004. – Т. 1. – С. 280–288.
8.Щицын Ю.Д., Щицын В.Ю. Расширение возможностей плазменной резки металлов // Вестник ПГТУ. Механика и технология материалов и конструкций. – Пермь, 2004. – № 8. – С. 62–66.
89
5. ПЛАЗМЕННАЯ СВАРКА ПРОНИКАЮЩЕЙ ДУГОЙ
Возможность управления параметрами сжатой дуги в широких пределах позволяет использовать различные технологии плазменной сварки, помогающие получать сварные швы с различной геометрией поперечного сечения.
Повышение производительности дуговых способов сварки и увеличение глубины проплавления требуют увеличения мощности дуги, что приводит к значительному росту силового воздействия на расплавленный металл. В результате этого жидкий металл в сварочной ванне деформируется и оттесняется в ее хвостовую часть. Это ведет к появлению подрезов, «бугристости» поверхности шва, газовых пор и полостей в металле шва, прожогам и другим дефектам. Для увеличения глубины проплавления и повышения скорости сварки без нарушения стабильности формирования шва необходимо снизить мощность силового воздействия дуги на жидкую ванну, не изменяя величины силового воздействия на фронт плавления. Этого можно достичь сбросом части потока сжатой дуги через отверстие в корне шва («замочную скважину») – переходом на режимы сварки проникающей дугой.
Автоматическая плазменная сварка проникающей дугой обеспечивает получение бездефектных сварных швов при высокой производительности. Этот способ сварки имеет целый ряд преимуществ перед другими способами дуговой сварки:
1.Обеспечивается полное проплавление свариваемого металла за один проход, сварные швы имеют в поперечном сечении узкую клиновидную форму. Внутренние дефекты сварного шва отсутствуют. Металл шва имеет химический состав и механические характеристики, близкие
косновному металлу.
2.Не требуется разделки кромок для стыковой сварки и механическая обработки швов после сварки вследствие высокого качества корневой и лицевой частей сварочного шва.
3.Снижаются затраты на проектирование и изготовление подкладных приспособлений.
90