
Плазменная обработка материалов
..pdf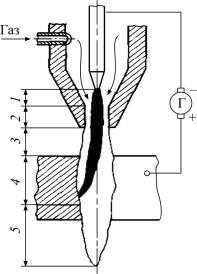
4.1.СУЩНОСТЬ ПРОЦЕССА ПЛАЗМЕННОЙ РЕЗКИ
Внастоящее время известен ряд методов плазменной резки, которые отличаются способом плазмообразования, используемой плазмообразующей средой, способом подачи плазмообразующего газа, материалом катода, полярностью тока, устройством плазмотрона, сопутствующими технологическими приемами.
|
Для резки могут использо- |
||
|
ваться сжатая дуга (прямого дей- |
||
|
ствия) и плазменная |
струя (кос- |
|
|
венного действия). В дуге прямого |
||
|
действия (рис. 25) в качестве ано- |
||
|
да применяется разрезаемый ме- |
||
|
талл, что позволяет использовать |
||
|
при резке высокую |
температуру |
|
|
анодного пятна. |
|
|
|
В этом случае |
разрезаемый |
|
|
металл является токоведущим эле- |
||
|
ментом и плазменная струя, исте- |
||
|
кающая из сопла плазмотрона, со- |
||
|
вмещена со столбом дуги по всей |
||
|
его длине, начиная от входного среза |
||
Рис. 25. Схема резки сжатой дугой |
канала сопла и заканчивая анодным |
||
прямого действия. Участки дуги: |
пятном на фронтальной поверхно- |
||
сти полости реза. В результате теп- |
|||
1 – закрытый; 2 – сжатый; 3 – откры- |
|||
тый; 4 – рабочий; 5 – факел плазмы; |
ловая энергия вводится в разрезае- |
||
Г – генератор тока |
мый металл струей плазмы, столбом |
||
|
дуги и тепловыделением в анодном |
пятне. Эффективный КПД при этом составляет 60–70 %. К недостатку дуги прямого действия можно отнести невозможность обработки материалов, не проводящих электрический ток.
Плазменная струя (рис. 26) возбуждается и горит между электродами, которые не связаны с обрабатываемым материалом. Катодом служит электрод плазмотрона, а в качестве анода используется его плазмообразующее сопло. Плазмообразующий газ и плазма лишь на коротком участке (от конца электрода до выходного среза канала сопла плазмотрона) контактируют со столбом дуги, а затем существуют независимо от него. При такой резке нагрев изделия в зоне обработки
51
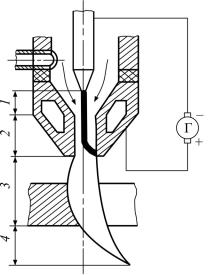
осуществляется только воздействием тепла плазменной струи. Вследствие этого температура и скорость истечения струи плазмы по мере удаления от среза сопла резко уменьшаются. КПД нагрева изделия не превышает 30–40 %. Плазменную струю используют при обработке не проводящих электрический ток материалов и для резки металлов небольшой толщины.
При резке сжатой дугой прямого действия имеется три источника тепла: пятно дуги, столб дуги и струя плазмы.
Каждый из них вносит свою долю тепла либо по всей высоте реза, либо на отдельных ее участках. При этом изменение формы фрон-
тальной поверхности реза по высоте отражает распределение количества вводимого тепла по высоте полости реза. При резке только плазменной струей форма фронтальной поверхности по высоте полости реза изменяется по экспоненциальному закону.
При резке же дугой прямого действия в верхней части фронтальной поверхности обычно имеется углубление (рис. 27, а), что свидетельствует о вводе тепла в данном месте за счет дополнительного действия анодного пятна. Измерения яркости дуги по высоте реза показывают, что частота расположения пятна в верхней части реза выше, чем в нижней (рис. 27, б). Верхнее предельное положение пятна ограничено верхней кромкой полости реза, а нижнее непрерывно меняется
впределах толщины листа, поэтому среднестатистическое положение пятна смещено к верхней части полости реза и проплавление здесь больше, чем в нижней части.
Вся полость реза может быть разбита на три участка по высоте (см. рис. 27, а). Первый верхний участок характеризуется тем, что плавление основного металла осуществляется в основном за счет теплоты, поступающей из столба дуги. Второй участок, расположенный
всредней части толщины листа, является основной областью рас-
52
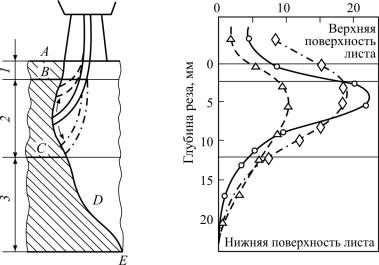
пространения пятна. На этом участке основной металл плавится за счет энергии столба дуги и энергии пятна. Добавлением энергии пятна объясняется некоторое выдвижение вперед этого участка по сравнению с первым. При прямой полярности пятно существует в основном вцентральнойчастифронтальнойповерхности иможетзанимать довольно широкую область, составляющую от 0,3 до 0,6 толщины разрезаемого листа. На третьем (нижнем) участке плавление металла по фронтальной поверхности осуществляется в основном за счет тепла, которое несет высокотемпературная плазменная струя. По мере уменьшения количества тепла, поступающего из высокотемпературной плазмы, форма фронтальной поверхности реза становится все более покатой.
а |
б |
Рис. 27. Поведение режущей дуги: а – схема перeмещений анодного пятна по фронтальной поверхности реза; б – яркость;
○–○Ar + 10 % H2; ◊–◊Ar; ∆–∆ N2;
Из рис. 27, б следует, что на ширину области распространения пятна по толщине листа оказывает влияние и вид плазмообразующей среды. При использовании азота область распространения пятна наиболее широкая.
Установлено, что характер перемещений анодного пятна внутри полости реза влияет на форму не только фронтальной поверхности, но и боковых стенок полости реза, т. е. на форму кромок вырезаемых деталей. Характер перемещения анодного пятна влияет и на поведение рас-
53
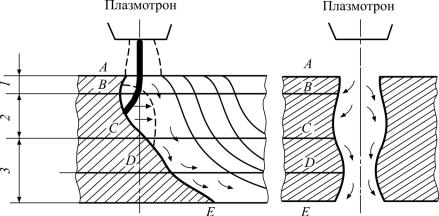
плавленного металла в полости реза. Несмотря на высокую скорость плазменного потока, в верхней части реза, т. е. в месте пятна, имеют место перемещения расплавленного металла, направленные из центральной области фронтальной поверхности в сторону линии затвердевания (рис. 28, а) . Перемещение расплавленного металла по боковой поверхности в верхней части полости реза, на участках 1 и 2 (показано стрелками), объясняется действием сил поверхностного натяжения, появляющихся вследствие большой разности температур в центральной части фронтальной поверхности и на участке затвердевания, где объем металла уменьшается (см. рис. 28, а).
а |
б |
Рис. 28. Схема полости реза и перемещения расплава под воздействием сил поверхностного натяжения: а – продольное; б – поперечное сечения
При этом, чем выше локальная плотность вводимого тепла, тем больше составляющая потока расплавленного металла, направленная к боковым стенкам реза. В связи с этим на участке ВС (см. рис. 28, а, б), являющемся областью существования пятна, расплавленный металл в большей степени перемещается в направлении поверхности затвердевания, чем на участке АВ. По мере перемещения к нижней части полости реза уменьшаются время пребывания анодного пятна и плотность тепла, вводимого из потока плазмы (участок СD). Поэтому снижается разность температур между центральной частью фронтальной поверхности и участком затвердевания на боковой поверхности. Это приводит к ослаблению сил поверхностного натяжения, в результате
54
чего на данном участке расплавленный металл большей частью стекает вниз. На участке ниже точки D происходит дальнейшее снижение плотности вводимого тепла и изменение угла наклона центральной части фронтальной поверхности полости реза в результате изменения направления потока газа, снова увеличивается составляющая потока расплавленного металла к боковым стенкам реза. В результате этого образуется поток расплавленного металла, направленный к линии затвердевания (см. рис. 28, а).
4.2.ПЛАЗМООБРАЗУЮЩИЕ СРЕДЫ ДЛЯ РЕЗКИ
Втехнике плазменной резки применяются две системы стабилизации и обжатия столба дуги – осевая и вихревая.
При осевой (или аксиальной) системе газ подается вдоль продольной оси электрода, охлаждает его и выходит через канал сопла, обжимая в нем и за его пределами столб дуги. В плазмотроне с осевой системой стабилизации электрод участвует в формировании дуги и поэтому имеет форму стержня с заострением на конце, чтобы обеспечить точное совпадение оси столба дуги с осью канала сопла, а также равномерность толщины газовой оболочки, обжимающей столб дуги в канале сопла. В связи с этим требования к соосности электрода и канала сопла очень высокие. Это является недостатком осевой системы стабилизации.
При вихревой (тангенциальной) системе стабилизации газ поступает в дуговую камеру по каналам, продольные оси которых расположены по касательным к окружности поперечного сечения дуговой камеры, или по каналам винтообразной формы. Вследствие этого газ
вкамере движется по спирали, охватывая столб дуги вихревым потоком. При этом катодное пятно и столб дуги автоматически и точно фиксируются в точке пересечения оси канала сопла с поверхностью катода, что позволяет применять электроды с плоской или другой формой рабочей поверхности. Возрастает стойкость сопла за счет обеспечения равномерности толщины газовой оболочки, обжимающей столб дуги в камере и в канале сопла.
Качественный состав плазмообразующей среды существенно влияет на основные технологические показатели процесса, и в первую очередь скорость и качество резки.
55
Состав среды определяет при заданной геометрии сопла и данном токе напряженность поля столба дуги как внутри, так и вне сопла, и, следовательно, за счет изменения состава среды можно в широких пределах регулировать количество тепловой энергии, выделяющейся в дуге.
Состав плазмообразующей среды сильно влияет на максимально допустимое значение I/d, что позволяет регулировать плотность тока в дуге, величину теплового потока в полости реза и, в конечном итоге, ширину реза и скорость резки.
Теплопроводность плазмообразующей среды определяет эффективность передачи разрезаемому листу выделенной в дуге тепловой энергии.
Плазмообразующая среда, взаимодействуя с выплавляемым металлом, дает возможность изменять его вязкость, величину поверхностного натяжения, химический состав. В результате изменения состава среды можно создавать наиболее благоприятные условия удаления расплавленного металла из полости реза, предотвращая образование наплывов на нижних кромках разрезаемого листа или делая их легко удаляемыми.
Следует также учитывать в некоторых случаях добавку тепловой энергии за счет химического взаимодействия плазмообразующей среды с разрезаемым металлом. Дополнительный вклад химической реакции в общий тепловой баланс может достигать величины, соизмеримой с электрической мощностью дуги.
Состав плазмообразующей среды сильно влияет на физико-хими- ческие процессы на стенках реза; от состава среды зависит насыщение стенок реза различными газами, а также глубина газонасыщеного слоя.
Выбор плазмообразующей среды определяется природой разрезаемых металлов и толщиной листов. Чем выше теплопроводность материала и больше толщина листа, тем более жесткие требования предъявляются к составу плазмообразующей среды и тем более сужается диапазон смесей, которые могут использоваться.
При выборе плазмообразующей среды необходимо также учитывать себестоимость процесса и дефицитность применяемых материалов.
Выбор плазмообразующей среды влияет на характеристики оборудования. В первую очередь состав плазмообразующей среды определяет конструкцию плазмотрона. В прямой зависимости от состава среды находится материал катода. В инертных или нейтральных смесях применяется нерасходуемый катод. В химически активных средах
56
катод рассчитан либо на относительно частую замену, либо на непрерывную подачу. От состава плазмообразующей среды зависит не только материал катода, но и способ его крепления в плазмотроне, а также интенсивность его охлаждения, что, в свою очередь, определяет конструкцию катодного узла.
В зависимости от состава среды изменяется величина тепловых потоков в сопла плазмотрона при прочих равных условиях и, следовательно, конструкция системы охлаждения сопел.
Как показали исследования, от состава плазмообразующей среды зависит величина частоты и амплитуда колебаний в кривой напряжения на дуге, от которых зависит устойчивость системы дуга – источник питания.
Состав и расход плазмообразующего газа полностью определяют циклограмму формирования рабочей дуги и, следовательно, схему управления установкой.
Таким образом, технологические возможности процесса и характеристики основных узлов оборудования во многом определяются плазмообразующей средой.
Исследования показали, что однокомпонентные плазмообразующие среды нецелесообразно использовать при плазменной резке. Справедливость этого положения подтверждается при рассмотрении основных газов с точки зрения возможности использования их при плазменной резке.
Аргон. Нецелесообразность применения аргона как самостоятельного плазмообразующего газа объясняется его плохими энергетическими характеристиками. В данном случае под энергетическими характеристиками понимается способность среды преобразовывать электрическую энергию в тепловую и передавать ее разрезаемому металлу.
Аргон также имеет наиболее низкую теплопроводность по сравнения со всеми плазмообразующими средами, вследствие чего тепло, выделяющееся в аргоновой дуге, используется плохо (рис. 29, а).
Проникающая способность дуги наиболее низкая из всех газовых сред, что снижает скорость и прорезающую способность дуги при заданных параметрах тока и геометрии плазмотрона.
Аргоновая дуга характеризуется наиболее низкой напряженностью поля (рис. 29, б), в результате чего при одном и том же токе в дуге выделяется наименьшее количество тепла.
57
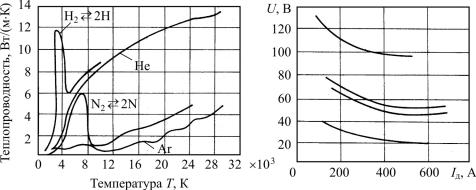
а |
б |
Рис. 29. Зависимость теплопроводности газов: а – от температуры; б – от напряжения на дуге в различных газах
Максимально допустимое значение I/d в аргоне намного меньше, чем в других средах.
В какой-то степени можно было компенсировать плохие электрические и теплофизические характеристики аргона значительным повышением его расхода. Увеличение расхода позволило бы повысить максимально допустимый ток для заданного диаметра сопла, а кроме того, с увеличением расхода газа повысилась бы проникающая способность дуги. Но аргон один из наиболее дефицитных и дорогих газов, вследствие чего работа при высоком расходе экономически нецелесообразна.
Азот. Азот – единственный газ, который можно применять самостоятельно в качестве плазмообразующей среды при резке. Это объясняется следующим. Теплопроводность и теплоемкость азота при высоких температурах довольно высоки. Благодаря этому в азотной дуге можно обеспечить достаточно эффективное преобразование электрической энергии в тепловую и передачу последней разрезаемому металлу. В результате скорость резки при использовании азота в несколько раз выше, чем при использовании аргона. Как и при использовании других плазмообразующих смесей, содержащих двухатомные газы, проникающая способность азотной дуги значительно выше, чем аргоновой дуги, что обеспечивает возможность резки листов больших толщин.
Технологические исследования показали, что в азоте обеспечивается достаточно высокое качество резки нержавеющих сталей, особенно
58
малых толщин. Качество резки алюминиевых сплавов и сплавов на медной основе хуже, чем при резке в водородсодержащих смесях, но лучше, чем в аргоне.
Широкое применение азота в качестве плазмообразующего газа при плазменной резке ограничивается тем, что даже чистый азот взаимодействует с вольфрамом при высоких температурах, образуя нитриды. Еще более сложно использование технического азота, содержащего 1–2 % кислорода. При температурах около 600 °С кислород начинает взаимодействовать с вольфрамом, образуя ряд более или менее летучих окислов (WO3, W2O3, W2O5). В результате, особенно в техническом азоте, вольфрамовый катод быстро сгорает, если величина тока превышает
500 А (табл. 3).
Используя очень чистый азот, например спектрально чистый, можно несколько поднять допустимые значения тока, но спектрально чистый азот не намного дешевле аргона. Таким образом, азот в отличие от аргона можно применять в качестве самостоятельного плазмообразующего газа при резке. Однако из-за низкой производительности и невысокой прорезающей способности области использования его весьма ограничены: механизированная резка листов небольшой толщины (преимущественно нержавеющих сталей) и ручная резка.
Таблица 3 Изменение длины и веса вольфрамового электрода за 1 ч работы
Сила тока, А |
Потеря в весе, г |
Уменьшение длины, мм |
200 |
0,13 |
0,4 |
250 |
0,16 |
0,6 |
300 |
0,17 |
0,7 |
350 |
0,22 |
0,8 |
400 |
0,34 |
1,1 |
Гелий. Использование гелия в качестве плазмообразующей среды значительно целесообразнее, чем использование аргона. В гелиевой дуге более высокая напряженность поля, поэтому при одной и той же силе тока обеспечивается больший запас тепловой энергии в дуге. Анодное падение напряжения также более высокое, что способствует увеличению удельных тепловых потоков в анодной области. Оба фактора приводят к тому, что скорость резки и прорезающая способность гелиевой дуги более высокие, чем аргоновой, и приближаются по параметрам к азотной дуге.
59
Хорошие результаты дает использование для резки аргонно-гелие- вых смесей. Однако необходимо помнить об очень высокой стоимости и дефицитности гелия.
Возможной областью применения гелия в качестве плазмообразующего газа (и смеси с аргоном) является резка таких сплавов, для которых с точки зрения металлургии наличие водорода и азота в зоне реза недопустимо.
Кислород. При использовании кислорода нельзя пренебрегать химическим взаимодействием плазмообразующей среды с разрезаемым металлом. При горении металлов в кислороде выделяется довольно большое количество тепла, которое может складываться с тепловой мощностью дуги. При добавлении кислорода в плазмообразующий газ азот и неизменном общем расходе газа скорость резки малоуглеродистых сталей постепенно увеличивается. Поскольку теплофизические параметры кислорода и азота весьма близки (теплоемкость и теплопроводность), то такое увеличение скорости может быть объяснено только химическим взаимодействием кислорода со сталью. Скорость резки линейно увеличивается с увеличением содержания кислорода
всмеси. Это значит, что наличие азота в смеси фактически не влияет на процесс горения железа. В то же время при газовой кислородной резке наличие примесей в кислороде существенно снижает скорость резки, а при содержании примесей свыше 30 % процесс резки невозможен. Такое различие во влиянии примесей при плазменной резке
вкислороде и обычной кислородной резке может быть объяснено тем, что необходимая для устойчивого горения температура на поверхности фронта горения поддерживается при плазменной резке за счет тепла электрической дуги.
Применение кислорода при плазменной резке сталей, несомненно, целесообразно, так как оно дает возможность получить высокие скорости резки на малых токах при небольшой ширине реза. Качество резки при этом не уступает качеству обычной кислородной резки. В то же время в качестве самостоятельной плазмообразующей среды кислород
не может быть использован из-за крайне низкой стойкости катода. К тому же скорость резки в чистом кислороде ниже, чем в смеси азота с кислородом.
Водород. Наилучшим газом для плазменной резки как процесса локального выплавления металла является водород. В водороде по сравнению со всеми рассмотренными газами величина анодного напряжения
60