
Плазменная обработка материалов
..pdfпостоянного тока электронная эмиссия с катода не должна зависеть от состава газовой среды, однако отмечено, что при использовании гелия в качестве защитного и плазмообразующего газа явление катодной очистки поверхности изделия не наблюдается, в то время как при использовании аргона катодная очистка имеет место. Отсюда можно сделать вывод, что автоэлектронная эмиссия не является основной причиной катодной очистки.
Вторичная электронная эмиссия. Бомбардировка положительны-
ми ионами может вызвать эмиссию электронов с поверхности твердого тела. Пороговая энергия положительных ионов, при которой появляется заметная эмиссия электронов, E0He+ = 380 эВ и E0Ar+ = 180 эВ. Более высокий выход е имеет место при бомбардировке окисленной поверхности. При бомбардировке нейтральными атомами также может наблюдаться эмиссия.
Эмиссия отрицательных ионов и нейтральных атомов. Падаю-
щий положительный ион может соединиться с электроном (е), вырванным с поверхности, образующийся при этом нейтральный атом может затем поглотиться поверхностью или отразиться от нее. Прямых данных об эмиссии нейтральных атомов нет, однако доказательством наличия этого процесса является наличие весьма низкой е эмиссии. Образование нейтральных атомов вероятнее всего происходит при низких значениях падающих ионов. Положительный ион, бомбардирующий поверхность, может захватывать два е и превращаться в отрицательный ион. Имеющиеся данные показывают, что выход отрицательных ионов весьма мал.
Отражение падающих ионов. Некоторые ионы, ударяющиеся о поверхность твердого тела, могут отражаться поверхностью с потерей энергии. Отражение по зеркальному углу наиболее вероятно, однако ионы обнаруживаются не только в этом направлении. Коэффициент отражения при бомбардировке поверхности разреженным газом достаточно высок при энергии падающих ионов не менее 50 эВ. Данные, полученные при бомбардировке поверхности ионами с энергией несколько сотен электрон-вольт, показывают, что коэффициент отражения значительно уменьшается при увеличении атомного веса иона. Например, коэффициент отражения ионов He+ на порядок выше, чем ионов Ar+ при величине энергии 600 эВ.
Распыление от падающих ионов. Атом или группа атомов могут вырываться из поверхностного слоя в результате ударения положи-
41
тельно заряженных ионов. Падающий ион вторгается в кристаллическую решетку поверхности металла, воздействуя на атомы или даже молекулы, которые, сталкиваясь друг с другом, приобретают скорость, достаточную для выхода из поверхностного слоя. Если имеется течение газа относительно поверхности, как в случае плазменной обработки, освобожденные атомы могут удаляться от поверхности с большой скоростью.
Газ, влага, адсорбированные поверхностью металла, другие загрязнения также могут распыляться под воздействием потока положительно заряженных ионов.
При изучении распыления адсорбированного газа при низкой (менее 10 эВ) энергии бомбардирующих ионов было обнаружено, что количество распыленных атомов одним ионом выражается зависимостью
S ≈ a (E – E0) при Е ≥ Е0;
где S – степень распыления; Е0 – пороговая энергия падающих ионов, выше которой процесс распыления имеет место; а – крутизна характеристики.
Существует попытка объяснить очистку поверхности металла резким вскипанием поверхности катода и сублимацией окислов (например, при сварке алюминия). Плотность тока в катодных пятнах, достигающая 106 А/см2, обусловливает высокие удельные тепловые потоки, достигающие значений 107 Вт/см2. Последние по величине превышают те тепловые потоки, которые могут быть отведены за счет теплопроводности материала катода, что вызывает эрозию поверхности за счет кипения и испарения. Достоверных данных о реальной температуре поверхности в зоне катодных пятен также пока нет из-за трудности ее измерения. Например, определение температуры путем спектроскопических исследований излучения пятна затрудняется интенсивным излучением из окружающей плазмы. Кроме того, следует напомнить, что при гелиевой атмосфере катодная очистка отсутствует, поэтому сублимация не является основной причиной очистки поверхности. Это подтверждается и тем, что при работе плазмотрона на прямой полярности очистки поверхности не происходит, хотя теплопередача в анод выше, чем в катод.
Таким образом, можно сделать вывод, что катодная очистка поверхности изделий представляет собой совокупность целого ряда про-
42
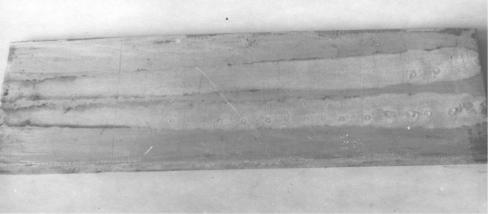
цессов, основной причиной которых является бомбардировка положительно заряженными ионами. Катодная очистка имеет место при всех дуговых способах сварки, когда изделие является катодом.
3.2. ВЛИЯНИЕ ТЕХНОЛОГИЧЕСКИХ ПАРАМЕТРОВ НА ПРОЦЕСС КАТОДНОЙ ОЧИСТКИ
Основными параметрами плазменной обработки металлов на обратной полярности являются: ток сжатой дуги Jд, А; расход плазмообразующего газа Qп, л/мин (Ar); расход защитного газа Qз, л/мин (Ar); диаметр плазмообразующего сопла dс, мм; скорость движения плазмотрона vсв, м/ч; расстояние от среза сопла плазмотрона до изделия H, мм.
Перечисленные параметры должны оказывать влияние на эффективность катодной очистки.
Качество катодной очистки можно контролировать по нескольким параметрам: ширине зоны катодной очистки Во (рис. 20), сопротивлению поверхностного слоя до и после очистки (например, мостом постоянного тока МО-62), растекаемости припоя, химическому составу поверхностного слоя (например, рентгеновским микроанализатором МАР-2).
Рис. 20. Изменение ширины зоны катодной очистки при уменьшении скорости движения плазмотрона
43
ЛАБОРАТОРНАЯ РАБОТА № 3 ИССЛЕДОВАНИЕ КАТОДНОЙ ОЧИСТКИ ОБРАБАТЫВАЕМОЙ ПОВЕРХНОСТИ СЖАТОЙ ДУГОЙ ОБРАТНОЙ ПОЛЯРНОСТИ
Цели работы:
1.Изучить процессы, протекающие при катодной очистке рабочей зоны при плазменной сварке на обратной полярности и при подготовке изделий под пайку.
2.Ознакомиться с оборудованием и технологией плазменной сварки на обратной полярности.
3.Исследовать влияние параметров режима обработки на эффективность катодной очистки металлических поверхностей.
4.Выявить особенности сварки алюминия и его сплавов.
Методика проведения экспериментов
Основными параметрами плазменной обработки металлов на обратной полярности являются:
Jд, А – ток сжатой дуги;
Qп, л/мин – расход плазмообразующего газа (Ar); dс, мм – диаметр плазмообразующего сопла; Qз, л/мин – расход защитного газа (Ar);
vсв, м/ч – скорость движения плазмотрона;
H, мм – расстояние от среза сопла плазмотрона до изделия. Исследования проводятся на образцах из различных материалов
(табл. 1). Образцы имеют следующие размеры: толщина 5–15 мм; ширина – 80 мм; длина 250 мм.
|
|
Таблица 1 |
|
|
Исследуемые материалы |
|
|
|
|
|
|
№ |
Группа материалов |
Металл- |
|
п/п |
представитель |
||
|
|||
1 |
Алюминиевые сплавы |
АМг6; АМц; Д16Т |
|
2 |
Высоколегированные коррозионно-стойкие стали |
12Х18Н10Т |
|
3 |
Высоколегированные жаропрочные стали |
09Х16Н4Б |
|
4 |
Сплавы на никелевой основе |
ХН67ВМТЮ |
|
5 |
Бронза |
БрХ08 |
|
6 |
Титановые сплавы |
ОТ4 |
44
Исследования выполняются на стенде для плазменной обработки материалов, скомплектованном на базе станка наплавочного.
Вкачестве рабочего инструмента используется плазмотрон для сварки на обратной полярности, сконструированный на кафедре сварочного производства и технологии конструкционных материалов Пермского национальногоисследовательского политехнического университета.
Для питания сварочного тока используется выпрямитель типа ВДУ-505, имеющий падающую внешнюю вольт-амперную характеристику и плавное регулирование сварочного тока.
Вкачестве защитного иплазмообразующего газаиспользуется аргон.
Порядок проведения работы
1. Подготавливается стенд плазменной обработки к работе: а) включается пускатель системы управления стенда; б) включается пускатель источника питания сварочного тока;
в) включается система подачи охлаждающей воды и система подачи газа; устанавливается необходимый расход, контролируемый соответствующими ротаметрами.
2.На рабочий стол укладывается испытываемый образец.
3.Устанавливаются требуемые параметры режима (табл. 3), включается сварочный ток и механизм перемещения плазмотрона.
|
|
Таблица 3 |
|
|
Параметры режимов процесса катодной очистки |
||
|
|
|
|
№ |
Параметры |
Диапазон |
|
п/п |
изменения |
||
|
|||
1 |
Сварочный ток Iсв, А |
50–200 |
|
2 |
Диаметр плазмообразующего сопла dс, мм |
3–6 |
|
3 |
Расход плазмообразующего газа, Аr, Qп, л/мин |
2–8 |
|
4 |
Расход защитного газа, Ar, Qз, л/мин |
2–9 |
|
5 |
Скорость перемещения плазмотрона vсв, м/ч |
5–80 |
|
6 |
Расстояние от среза сопла до изделия h, мм |
5–20 |
Наблюдается явление катодной очистки. После остывания образца производится определение ширины зоны катодной очистки.
Исследования проводятся последовательно по каждому параметру режима при поддержании остальных параметров постоянными. Подплавление поверхности образцов не допускается. Для исключения влияния предварительного подогрева на ширину зоны катодной очист-
45
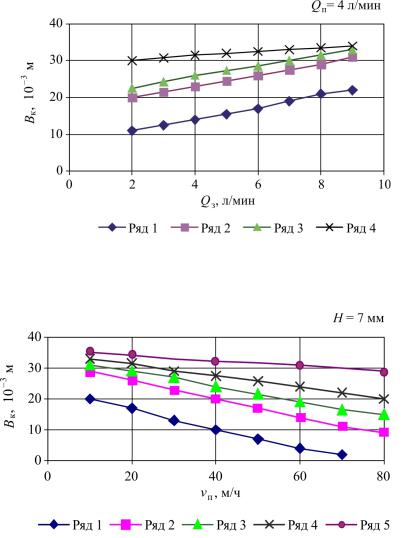
ки выполнение повторных проходов допускается только после охлаждения образца.
Измеряется ширина зоны катодной очистки, результаты исследований заносятся в таблицы. По полученным результатам строятся графики зависимостей ширины зоны катодной очистки от изменения параметров режима обработки (рис. 21–24).
Рис. 21. Влияние расхода защитного газа на ширину зоны катодной очистки:
ряд 1 – Iсв = 60 А; ряд 2 – Iсв = 100 А; ряд 3 – Iсв = 150 А; ряд 4 – Iсв = 200 А; ряд 5 – Iсв = 300 А; при vсв, = 16 м/ч, Qп = 4 л/мин, dс = 6 мм и h = 7 мм
Рис. 22. Влияние скорости сварки на ширину зоны катодной очистки. Обозначения и условия см. на рис. 21 при Qз, = 5 л/мин
46
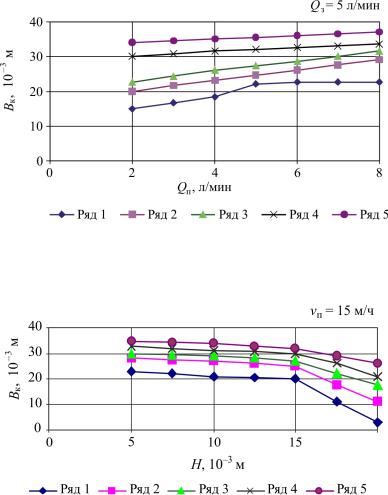
Рис. 23. Влияние расхода плазмообразующего газа на ширину зоны катодной очистки. Обозначения и условия см. на рис. 21 при Qз = 5 л/мин
Рис. 24. Влияние расстояния от среза сопла до изделия на ширину зоны катодной очистки. Обозначения и условия см. на рис. 21 при Qз = 5 л/мин
Проводится анализ полученных результатов, выявляются параметры режима, оказывающие наибольшее влияние, составляются выводы по проведенным исследованиям. Для сокращения числа экспериментов и возможности математической обработки полученных результатов рекомендуется использовать методику планирования эксперимента.
47
Техника безопасности
1.Работа на стенде для плазменной обработки металлов производится под контролем ведущего преподавателя или учебного мастера.
2.Наблюдение за зоной обработки плазменной дугой производится через сварочный светофильтр.
3.Измерение зоны катодной очистки производится после остывания образцов.
4.Работа проводится при включенной вытяжной вентиляции.
5.Регулировка скорости перемещения плазмотрона сменными шестернями привода производится при выключенном пускателе стенда.
Контрольные вопросы
1.Особенности сварки алюминиевых и магниевых сплавов.
2.Способы подготовки поверхностей изделий под сварку и пайку.
3.Механизм процесса катодного распыления.
4.Вторичная электронная эмиссия.
5.Эмиссия отрицательных ионов и нейтральных атомов.
6.Отражение падающих ионов.
7.Распыление от падающих ионов.
8.При каких способах сварки имеет место катодная очистка поверхности изделия?
9.Какие параметры режима обработки плазменной дугой влияют на мощность катодной очистки?
10.Какими параметрами можно оценить качество катоднойочистки?
11.Какие материалыможноподвергать процессу катоднойочистки?
12.Почему при использовании гелия в качестве защитного и плазмообразующего газа не наблюдается явление катодной очистки?
13.Почему происходит сужение зоны катодной очистки при расплавлении металла?
Список литературы
1.Предупреждение образования окалины и методы очистки деталей. – М.: Машиностроение, 1984. – 164 с.
2.Рабкин Д.М., Фурсов В.А. О процессе катодного распыления
в сварочной дуге // Физика и химия обработки металлов. – 1973. –
№ 8. – С. 28–30.
48
3. Pattee H.E., Anno J.N., Ranadall M.D. Theoretical and experimentax stady of catodic cleaning With the plasma arc // Welding Journall. – 1968. –
Vol. 47, № 4. – P. 181–192.
4. Щицын Ю.Д., Тыткин Ю.М. Исследование способа катодной очистки для подготовки деталей под пайку // Сварка в машиностроении:
сб. науч. тр. – М.: Знание, 1995. – С. 95–99.
49
4. ПЛАЗМЕННАЯ РЕЗКА МЕТАЛЛОВ
Плазменная резка на сегодняшний день является одним из наиболее освоенных направлений плазменной обработки металлов. Плазменная резка находит все более широкое применение в различных отраслях промышленности. Это обусловливается возможностью ее использования для резки практически всех металлов и их сплавов, высокой производительностью и точностью, отсутствием грата на кромках деталей, низкой стоимостью погонного метра реза, взрывобезопасностью.
В настоящее время накоплен опыт использования различных видов плазменной резки и средств ее технологического оснащения в виде стационарных машин с программным управлением, переносных машин, поточных линий и различных средств механизации вспомогательных и транспортных операций. Создаются гибкие автоматизированные производственные системы на базе плазморежущих машин с программным управлением.
Плазменно-дуговая резка и необходимое для ее выполнения оборудование впервые были разработаны и исследованы во ВНИИАвтогенмаш в 1956–1957 гг. одновременно с аналогичными разработками в США, Англии и ФРГ. Также вопросами разработки и практического внедрения плазменной резки занимались ВНИИЭСО, ЦНИИТС, НИКИМТ, ИЭС им. Е.О. Патона.
Плазменной резке поддаются все металлы. В отличие от кислородной резки, при которой около 70 % тепловой энергии создается при горении, в процессе плазменной резки энергия, необходимая для расплавления металла, создается электрическим способом. Сущность способа состоит в локальном интенсивном расплавлении разрезаемого металла в полости реза теплотой, генерируемой сжатой дугой (температура плазмы может достигать 20 000–30 000 °С), и интенсивном удалении расплава из полости высокоскоростным плазменным потоком, вытекающим из канала сопла плазмотрона. Плотность энергии в формирующих соплах режущих плазмотронов достигает 106 Вт/см2. Скорость плазмы в струе, истекающей из сопла режущего плазмотрона, может превышать 2–3 км/с.
50